第三章 粉末材料的成形与固结
粉末冶金基础知识(三篇)

粉末冶金基础知识(一)粉末的化学成分及性能尺寸小于1mm的离散颗粒的集合体通常称为粉末,其计量单位一般是以微米(m)或纳米(nm)。
1.粉末的化学成分常用的金属粉末有铁、铜、铝等及其合金的粉末,要求其杂质和气体含量不超过1%~2%,否则会影响制品的质量。
2.粉末的物理性能⑴粒度及粒度分布粉料中能分开并独立存在的最小实体为单颗粒。
实际的粉末往往是团聚了的颗粒,即二次颗粒。
实际的粉末颗粒体中不同尺寸所占的百分比即为粒度分布。
⑵颗粒形状即粉末颗粒的外观几何形状。
常见的有球状、柱状、针状、板状和片状等,可以通过显微镜的观察确定。
⑶比表面积即单位质量粉末的总表面积,可通过实际测定。
比表面积大小影响着粉末的表面能、表面吸附及凝聚等表面特性。
3.粉末的工艺性能粉末的工艺性能包括流动性、填充特性、压缩性及成形性等。
⑴填充特性指在没有外界条件下,粉末自由堆积时的松紧程度。
常以松装密度或堆积密度表示。
粉末的填充特性与颗粒的大小、形状及表面性质有关。
⑵流动性指粉末的流动能力,常用50克粉末从标准漏斗流出所需的时间表示。
流动性受颗粒粘附作用的影响。
⑶压缩性表示粉末在压制过程中被压紧的能力,用规定的单位压力下所达到的压坯密度表示,在标准模具中,规定的润滑条件下测定。
影响粉末压缩性的因素有颗粒的塑性或显微硬度,塑性金属粉末比硬、脆材料的压缩性好;颗粒的形状和结构也影响粉末的压缩性。
⑷成形性指粉末压制后,压坯保持既定形状的能力,用粉末能够成形的最小单位压制压力表示,或用压坯的强度来衡量。
成形性受颗粒形状和结构的影响。
(二)粉末冶金的机理1.压制的机理压制就是在外力作用下,将模具或其它容器中的粉末紧密压实成预定形状和尺寸压坯的工艺过程。
钢模冷压成形过程如图7.1.2所示。
粉末装入阴模,通过上下模冲对其施压。
在压缩过程中,随着粉末的移动和变形,较大的空隙被填充,颗粒表面的氧化膜破碎,颗粒间接触面积增大,使原子间产生吸引力且颗粒间的机械楔合作用增强,从而形成具有一定密度和强度的压坯。
第三章粉末冶金
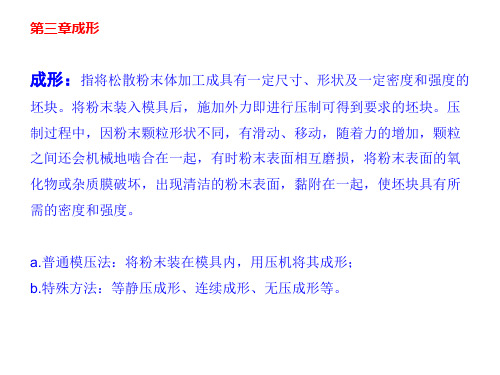
第三章成形 d.弹性后效
加载(或卸载)后经过一段时间应变才增加(或减小)到一定数值的 现象。压制过程中,当卸掉压制力并把坯块从模具内取出后,由于弹性 内应力的作用,坯块发生弹性膨胀,这种现象称为弹性后效。
a.粉末颗粒发生位移,填充孔隙,施加压力,密度增加很快; b.密度达到一定值后,粉末体出现一定压缩阻力,由于位移大大减少, 而变形尚未开始,压力增加,但密度增加很少; c.当压力超过粉末颗粒的临界应力时,粉末颗粒开始变形,使坯块密度 继续增大。
图3-10坯块密度的变化规律
第三章成形
(5)压制压力与坯块相对密度的关系 相对密度指物质的密度与参考物质的密度在各自规定的条件下之比,
第三章成形
退火温度: T退 (0.5 ~ 0.6)T熔
退火气氛: a.还原性气氛(氢、离解氨、转化天然气或煤气) b.惰性气氛 c.真空退火
第三章成形
(2)混合 a.混合:将两种或两种以上不同成分的粉末混合 b. 将相同成分而粒度不同的粉末混合(合批) 混合方法:机械法(干混、湿混)和化学法 机械法:干混用于生产铁基制品;湿混用于生产硬质合金。混料设备有
a.普通模压法:将粉末装在模具内,用压机将其成形; b.特殊方法:等静压成形、连续成形、无压成形等。
第三章成形
1.成形前原料准备 (1)退火
将金属缓慢加热到一定温度,保持足够时间,然后以适宜速度冷却(通 常是缓慢冷却,有时是控制冷却)的一种金属热处理工艺。
金属粉末退火的目的: a.氧化物还原,降低碳和其它杂质的含量,提高粉末的纯度; b.消除粉末的加工硬化,稳定粉末的晶体结构; c.防止超细粉末自燃,将其表面钝化。 加工产品退火的目的: a.降低硬度,改善切削加工性; b.消除残余应力,稳定尺寸,减少变形与裂纹倾向; c.细化晶粒,调整组织,消除组织缺陷。
第3章成形

压制过程中的力分析—侧压力
• 侧压力与压制压力关系
由广义虎克定律
x
1 E
[ x
v(
y
z )]
0
P侧
v 1 v
P
P
--侧压系数
P侧 0 f () P
• 侧压系数与压坯密度的关系?
压制过程中的力分析—侧压力
压制过程中的力分析—外摩擦力
成形前原料准备—造粒
金属粉末的压制过程
• 模压成形3个工步
金属粉末的压制过程
• 4种送粉方式
金属粉末的压制过程
金属粉末的压制过程
金属粉末的压制过程
金属粉末的压制过程
• 粉末颗粒变形与位移
金属粉末的压制过程
• 压模压制是将置于压模内的松散粉末施加一定的压力后,成 为具有一定尺寸、形状和一定密度、强度的压坯。
P摩擦 P
• 外摩擦力(摩擦压力损失)与压制压力的关系
8 H
P模底 Pe D
实验证明 常数
• 摩擦压力损失与压坯尺寸的关系
压制过程中的力分析—外摩擦力
• 摩擦力对压制过程及压坯质量的影响 1、压制压力损失 2、压制压力不均匀 3、阻碍粉体的运动
压制过程中的力分析—脱模压力
粉末冶金原理
主讲教师:施钢 班级:09材料 2011年9月19日 厦门理工学院
第3章011.09.19
3.2 金属粉末的压制过程
3.3 压制压力与压坯密度的关系
3.4 压制过程中力的分析
2011.09.21
3.5 压坯密度及其分布
3.6 成形剂
3.7 压制废品分析
材料制备技术-粉末冶金
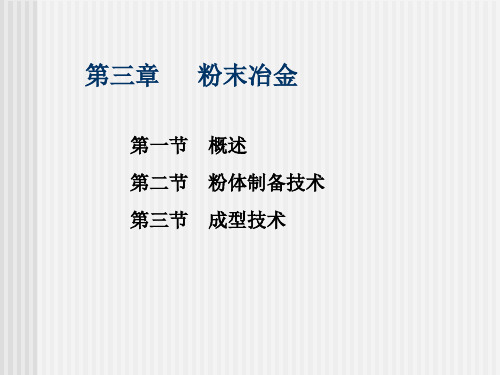
热模锻优势:
① 粉末冶金制件精度比精锻高;
① 可制造大型零件;
② 粉末锻造节省材料、重量控制精 ② 锻件力学性能比烧结粉
确、可无非边锻造,也能制造形状较 末冶金零件高,但与粉末
复杂制件;
锻造件相当;
③ 粉末锻造只需一副成形模具和一 ③ 可制造形状复杂程度较
副锻模;热锻需两副以上锻模、一副 高的制品。
挤压(extrusion)、轧制(rolling)、拉拔(drawing)、 冲压(punching)、锻造(forging)
PM(Powder Metallurgy) 粉末冶金法 制粉(powder making)压型(pressing) 烧结(sintering)
粉末冶金特点及与其他成形工艺的比较
现代粉末冶金发展的三个重要标志:
• 1909年制造电灯钨丝的技术成功(W粉成形、烧结、锻打、 拉丝);1923年硬质合金研制成功。 • 20世纪30年代,多孔含油轴承成功;相继发展铁基机械零件 • 向新材料、新工艺发展:20世纪40年代,金属陶瓷、弥散强 化材料(如烧结铝);60年代末~70年代初,粉末高速钢、粉 末高温合金,粉末锻造技术已能生产高强度零件。
4) 成型性 Formation ability
定义:粉末压制后,压坯保持既定形状的能力 用压坯强度 表示
意义: 压坯加工能力,加工形状复杂零件的可能性 影响因素:颗粒之间的啮合与间隙
a 不规则颗粒,颗粒间连接力强, 成型性好 b 颗粒越小,成型性越好;
与压缩性影响后果相反,必须综合考虑
2.2 粉末制备方法
3) 压缩性 Compressive ability
(1) 定义: 粉末被压紧的能力,表示方法是:在恒定压 力下(30t/inch2)粉末压坯的密度
第三章 粉末成形技术-1

materials.
School of Materials Science and Engineering
(一)合批和混合的目的
1. 不同成分混合均匀;
2. 消除运输过程中产生的偏析或生产过程中不同 批号粉末之间的性能差异 3. 混入合金元素 4. 调整松装密度和流动性
5. 混e and Engineering
1.装粉要求:保证各高度(料腔)处装填系数相同! 2. 基本方法: (1)手工装粉—重量法
要求:
☆ 保证粉料重量在允许误差范围内; ☆ 装料均匀,尤注意边角处的充填;
☆ 不能过分振动阴模,防止比重轻的组元上浮产
生偏析 ☆ 多台阶压坯,要严格控制各料腔的装填高度。
School of Materials Science and Engineering
(2)自动装粉—容量法
装于料仓中的粉末,通过送料器自动地送入阴模模腔中。
自动装料是自动压制的一个重要的工艺步骤! 常用的装料方式有: 落入(下)法、吸入法、多余装料法、超满装料法、 零腔装料法、不满装料法 (图)
School of Materials Science and Engineering
V--制品的体积(由制品图算出),m3; d--制品要求密度,kg/m3; K--重量损失系数。
称料方法有两种: (1)重量法;(2)容量法。 (二)装料(粉) 将所称量的粉末装入模具中时,要求粉末在模腔内分布均匀、 平整,以保证压坯各部分压缩比一致。
School of Materials Science and Engineering
常用分级方法:筛分分级:
旋风分级、离心分级、沉降分级等。 粉末的粒度及粒度组成不同,影响压制和烧结工艺,且 对产品的最终性能也有重要影响! 采用细颗粒粉末制成的产品,其强度较粗颗粒的高韧性 也好。
第三章 粉末材料的成形与固结
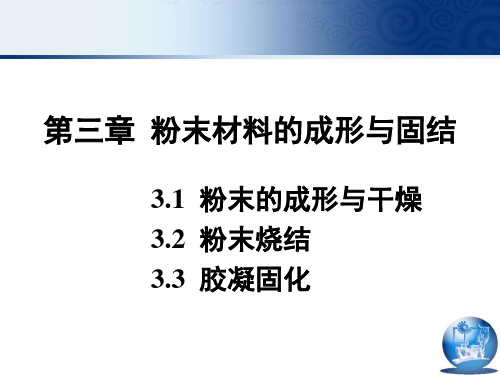
• 按粉料成形时的状态,分类:
模压成形
压力成形
等静压成形
……
挤压成形
成形
增塑成形
注射成形
……
注浆成形
料浆成形
热压铸成形
流延成形
……
颗粒密度
• 粉末材料的理论密度,通常不能代表粉末 颗粒的实际密度,因颗粒几乎总是有孔; • 孔与颗粒外表面相通,称开孔或半开口 (一端相通); • 颗粒内不与外表面相通的潜孔称闭孔;
成形方法
模压成形 温压成形 等静压成形 软模成形 高能成形 挤压成形 扎膜成形 注射成形 车坯成形
压力成形
增塑成形
注浆成形 热压铸成形 流延法成形 压力渗滤工艺与离心成形 凝胶铸模成形 直接凝固成形
浆料成形
压力成形-(1)模压成形
步骤:
原料准备(粉末退火、混合、筛分、 制粒、添加润滑剂和成形剂) 装模 加压 保压 脱模
原料准备
• 粉末退火:使氧化物还原、降低碳及其 它杂质、提高粉末纯度。 • 退火温度:(0.5-0.6)Tm
• 粉末混合:两种或两种以上不同成分的粉 末混合均匀的过程。 • 合批:将成分相同而粒度不同的粉末进行 混合。 • 混合方法:机械法(球磨机、振动搅拌机、 V型混合器……)、化学法 • 机械法:干混、湿混(水、酒精、汽油、 丙酮)
(3)
(2) (1) 200 400 600 800 1000 1200 1400 1600
P /MPa
热压Mg2Si块体的Heckel图
Kawakita(川北公夫)方程
3500 3000
P/C /MPa
P 1 P C ab a
Experimental results Best fit to formula (2)
粉末材料成形

加润滑剂
1
粉末还原退火
粉末还原退火:
指金属粉末在还原性气氛、惰性气氛或真空保护条
件下,加热到一定温度并保持一定时间后缓冷。
退火工艺:
退火温度: 退火时间:
0.5~0.6 Tm(金属熔点) 1h
1
粉末还原退火
退火的目的:
1) 提高粉末的纯度 2) 消除加工硬化,稳定晶体结构 3) 表面钝化
成形前原料准备 模压成形
4.1.3
特殊成形
4.1.3
特殊成形
粉末模压成形是当前粉末冶金生产中的主流成形方法,它
技术成熟,工艺简单,成本较低,适合大批量生产。
但是压机的能力与压模的设计限制了模压成形制品的尺寸
与形状,传统的模压成形法所生产的粉末冶金制品一般尺 寸较小,单重较轻,形状也较简单。
用于硬质合金生产及比重差大的多种金属粉混料。
混料常用设备:
球磨机,V性混料器、桶型混料器、锥型混料器等
3
粉末混合
混合方法: 机械混合法 化学混合法
3
粉末混合
将粉末和添加金属的盐溶液均匀混合,然后
化学混合法:
经沉淀、干燥、还原等处理得到均匀混合物。
如:生产W-Ni-Cu粉
钨粉
硝酸镍
硝酸铜或氯化铜
填充孔隙,使粉末体的体 积减小,粉末颗粒迅速达 到最紧密的堆积。
1
单向压制
侧压力:
粉末体在压模内受力后力图向各个方向 流动,于是引起垂直于压模壁的压力。
摩擦力:
侧压力使压模内靠近模壁的外层粉末 与模壁之间产生摩擦力。
使压坯高度方向存在明显的压力降。 压坯各个部分的密度分布不均匀。
1
单向压制
材料成型:粉末成型

2、硬质合金
6
五、粉末冶金制品的结构工艺性(详见表4.2) 1、壁厚不能过薄 2、沿压制方向的横截面变化时,不能逐渐增大
不合理
合理
7
3、阶梯圆柱体每级直径之差不宜大于3mm,每级的长度与直径之比应小于3,上下底面之差也不能 悬殊太大,否则不易压实
不合理
合理
8
4、应避免与压制方向垂直的或斜交的沟槽、孔腔以及网纹花
零件成形方法:
1、材料成形法——进入工艺过程物料初始重量近似等于加 工后最终重量。如铸造、压力加工、粉末冶金、注塑成 形等,这些方法多用于毛坯制造,但也可直接成形零件。
2、材料去除法——零件的最终几何形状局限在毛坯的初始 几何形状范围内,零件形状的改变是通过去除一部分材 料,减少一部分重量来实现的。如切削与磨削,电火花 加工、电解加工等特种加工等。
b.连续式: 网带传送式烧结炉
4
4、后处理: (1)浸渗:利用烧结件的多孔性的毛细现象,浸入各种液体 (2)表面冷挤压 (3)切削加工 (4)热处理 (5)表面保护处理
5
五、粉末冶金成型的应用 1、机械制造中常用的粉末冶金材料 (1)粉末冶金减摩材料 (2)粉末冶金铁基结构材料 (3)粉末冶金摩擦材料
26
构造三维模型 模型近似处理
切片处理
激光
喷射源
固化树脂 切割箔材 烧结粉末
喷粘结剂 喷热熔材料
三维产品(样品/模具)
表面处理
27
图6-1 快速成型过程
设计
设计
铸造 锻压 焊接
模具
去
模具
毛坯 (大于工件)
除
半成品
加 工
a)
半成品 工件
样品
图6-2 传统加工与快速成型比较
- 1、下载文档前请自行甄别文档内容的完整性,平台不提供额外的编辑、内容补充、找答案等附加服务。
- 2、"仅部分预览"的文档,不可在线预览部分如存在完整性等问题,可反馈申请退款(可完整预览的文档不适用该条件!)。
- 3、如文档侵犯您的权益,请联系客服反馈,我们会尽快为您处理(人工客服工作时间:9:00-18:30)。
• 按粉料成形时的状态,分类:
模压成形
压力成形
等静压成形
……
挤压成形
成形
增塑成形
注射成形
……
注浆成形
料浆成形
热压铸成形
流延成形
……
颗粒密度
• 粉末材料的理论密度,通常不能代表粉末 颗粒的实际密度,因颗粒几乎总是有孔; • 孔与颗粒外表面相通,称开孔或半开口 (一端相通); • 颗粒内不与外表面相通的潜孔称闭孔;
板后,以粉末锥的高度衡量流动性,粉末锥
的底角称为安息角,也可作为流动性的量度。
锥愈高或安息角愈大,则表示粉末的流动
性愈差,反之则流动性愈好。
规律:
等轴状(对称性好)粉末、粗颗粒粉末 的流动性好; 粒度组成中,极细粉末占的比例愈大, 流动性愈差,但是,粒度组成向偏粗的 方向增大时,流动性变化不明显。
粉末压制理论的一些理论公式和经验公式
序号 1 2 提出时间 1923 1930 著者姓名 汪克尔 L. F. Athy 艾西 M. Balshin 巴尔申 公 β =k1-k2lgP θ =θ 0e-β P 式 注 解 k1, k2—系数 P—压制压力,β —相对密度 θ —压力 P 时的空隙率 θ 0—无压力时的空隙率 β —压缩系数 Pmax—相应于压至最紧密状态(β =1)时的单位压力 L—压制因素 m—系数 β —相对体积 d 压—压坯密度 d 松—粉末松装密度 C—粉末体积减少率 a、b—系数 A、κ —系数
• 真密度:颗粒质量用除去开孔和闭孔的颗粒体积除 得的商值。真密度实际就是粉末的固体密度。 • 有效密度:颗粒质量用包括闭孔在内的颗粒体积去 除得到的。用比重瓶法测得的密度接近这种密度, 故又称为比重瓶密度。 • 表观密度:颗粒质量用包括开孔和闭孔在内的颗粒 体积除得的密度值。 • 堆积密度:粉体材料在自然堆积状态下单位体积的 质量。自然状态下的体积,是指既含颗粒内部的孔 隙,又含颗粒之间空隙在内的总体积。
碎化
应变硬化
脆性粉末 点接触应力>断裂强度→断裂 塑性粉末 点接触应力>屈服强度 →塑性变形 →加工硬化 →脆化→断裂
压坯密度与压制压力的关系
在压制过程中,随着压力的增加,粉体的密 度增加、气孔率降低。 对压力与密度或气孔率的关系进行了大量的研 究,试图在压力与相对密度之间推导出定量的数 学公式。目前已经提出的压制压力与压坯密度的 定量公式(包括理论公式和经验公式)有几十种 之多。
3
1938
dP LP dβ lg P max lg P L ( β 1) lg P max lg P m lgβ
4 5 6 7 8 9 10 11
1948 1956 1961 1962 1962 1963 1963 1964~ 1980
Smith 史密斯 川北公夫 R. W. Heckel 黑克尔 尼古拉耶夫 米尔逊 库宁 尤尔钦科 平井西夫 黄培云
3、压缩性
代表粉末在压制过程中被压紧的能力。 在标准的模具中在规定的润滑条件下加以测 定,用规定的单位压力下粉末所达到的压坯密 度表示。通常也可以用压坯密度随压制压力变 化的曲线图表示。 压缩比:松装粉末的高度与成型坯体高度之
比。
4、成形性
成形性是指粉末压制后,压坯保持既 定形状的能力,用粉末得以成形的最小单 位压制压力表示,或者用压坯的强度来衡 量。 压制性:是压缩性和成形性的总称。
规律:
成形性好的粉末,往往压缩性差; 相反,压缩性好的粉末,成形性差。例
如松装密度高的粉末,压缩性虽好,但
成形性差;细粉末的成形性好,而压缩 性却较差。
粉末在压力下的运动行为
成型工艺主要有: 刚性模具中粉末的压制(模压)
弹性封套中粉末的等静压
粉末板条滚压以及粉末挤压等
压制过程的三个阶段:
第一阶段:首先粉末颗粒发生位移(滑动 与转动)与重排,颗粒间的架桥现象被部分消 除且颗粒间的接触程度增加;
3.5 3.0 2.5 2.0 1.5 1.0 0
Experimental results Linear fit:Y=A+B*X (1) A=0.7780 B=0.00383 R=0.9406 (2) A=1.4793 B=6.7825E-4 R=0.9455 (3) A=-3.7910 B=0.00493 R=0.8920
d 压=d 松+κ P1/3 C=(abP)/(1+bP) ln(1-D)-1=κ P+A P=σ sCDln[D/(1-D)]
12
1973
巴尔申 查哈良 马奴卡
σ s—金属粉末的屈服强度 C—系数 lg(P+κ )≈-lgβ +lgPk Pk—金属最大压制密度时的临界压力;κ 、n—系数 d=dmax-(κ 0/d)e-aP dmax—压力无限大时的极限密度 a、κ 0—系数 dε /dt=[(β /φ )tkfβ -1](df/dt)+[(K/φ )tk-1fβ ′ f—外力,ε —应变 -1 ]f φ 、β 、K—系数 lgln[(dm-do)d]/[(dm-d)d0]=nlgP-lgM dm—致密金属密度 mlgln[(dm-do)d]/[(dm-d)d0]=lgP-lgM d0—压坯原始密度 d—压坯密度, P—压制压力 M—相当于压制模树 n—相当于硬化指数的倒数 m—相当于硬化指数 a 2 P=3 P0ρ (Δ ρ /θ 0) P0—初始接触应力 ρ —相对密度 θ 0—(1-ρ ) a=[ρ 2(ρ -ρ 0)]/θ 0
2500 2000 1500 1000 500 0 0 200 400 600 800 1000 1200 1400 1600
P /MPa
热压Mg2Si块体的Kawakita图
压制过程中力的分析
总压力 P 净压力 P净
压力损失 P损失
侧压力 P侧
模壁摩擦力 P摩
内摩擦力 P内摩
弹性力 P弹
P侧 P 总
第三章 粉末材料的成形与固结
3.1 粉末的成形与干燥 3.2 粉末烧结 3.3 胶凝固化
3.1 粉末的成形与干燥
成形的理论基础 • 粉末的工艺性能 • 粉末在压力下的运动行为 • 成形方法
•
• 成型:是说工件、产品经过加工后具有 某种特定的、所需要的形状;把东西按 标准尺寸或规格完成的过程。
• 成形:将松散的粉体加工成具有一定尺 寸、形状以及一定密度和强度的坯块。
(a) 装配图
(b) 流速漏斗 松装密度测定装置一
(c) 量杯
(1) 漏斗 (2) 阻尼箱
(3) 阻尼隔板
(4) 量杯 (5) 支架
松装密度测定装置二
• 松装密度取决于颗粒间的粘附力、相对 滑动的阻力以及粉末体孔隙被小颗粒填 充的程度。
2、流动性 50克粉末从标准的流速漏斗流出所 需的时间,单位为s/50克,其倒数是 单位时间内流出粉末的质量,俗称为 流速。
(3)
(2) (1) 200 400 600 800 1000 1200 1400 1600
P /MPa
热压Mg2Si块体的Heckel图
Kawakita(川北公夫)方程
3500 3000
P/C /MPa
P 1 P C ab a
Experimental results Best fit to formula (2)
粉末的工艺性能
包括: 1、松装密度、振实密度
2、流动性
3、压缩性
4、成形性
另外,工艺性能也主要取决于粉末的生产 方法和粉末的处理工艺(球磨、退火、加润 滑剂、制粒等)。
1、松装密度与振实密度
不同粉末装满一定容积的质量是不同的,因此规定 用松装密度或振实密度来描述粉末的这种容积性质。
松装密度:粉末试样自然填充规定的容器时, 单位容器内粉末的质量,单位为g/cm3。 (国标GB1478-84,GB5060-85) 振实密度:将粉末装于振动容器中,在规定条 件下,经过振动后测得的粉末密度。 (国标GB5162-85)
通常为了提高堆积密度,常在较大的均一颗粒之间加 入较小的颗粒。当小颗粒粉末量增加时,粉体的松装密度 先增加然后降低。
5.4 5.2
¬ cm3 È £ à ¶ ×Ü É ° Ë
5.0 4.8 4.6 4.4 4.2 0 20 40 60 ¸ ¿ Ï Å Á £ £ ¬ % 80 100
细颗粒(-325目)对不锈钢粗颗粒(-100+150目)松装密度的影响
粉末成形的理论基础 粉体的堆积与排列
理想球形颗粒的堆积类型、堆积密度和配位数
排列 简单立方 体心立方 面心立方 六方密堆 堆积密度% 52 68 74 74 配位数 6 8 12 12
将大小均匀的球形颗粒粉末倒入容器 时,即使颗粒进行面心立方或密排六方排 列,堆积密度也较低, 即小于74%。通过 振动可以提高堆积密度,但是,即使采用 最仔细的振动方式,最高的振实密度也仅 能达到62.8%,并且平均配位数也低于12。
• 脱模压力:使压坯由模中脱出所需的压力。
它与压制压力、粉末性能、压坯密度和尺寸、 压模和润滑剂有关。
• 弹性后效:在压制过程中,当除去压制压力
并把压坯压出压模之后,由于内应力的作用, 压坯会发生弹性膨胀。
• 压坯强度:表征压坯抵抗破坏的能力,即颗粒 间的粘结强度; • 影响因素:颗粒间的结合强度、颗粒表面的粗 糙度、颗粒形状、颗粒表面洁净程度、压制压 力、颗粒的塑性、成形剂
第二阶段:颗粒发生弹塑性变形,塑性变 形的大小取决于粉末材料的延性。但是,同样 的延性材料在一样的压力下,并不一定得到相 同的坯体密度,还与粉末的压缩性能有关; 弹性变形 颗粒间的接触应力≤材料弹性极限 塑性变形 颗粒接触应力≥材料的屈服强度 点接触处局部→面接触处局部→整体 断裂
第三阶段:颗粒断裂。不论是原本脆性的 粉体如陶瓷粉末、还是在压制过程中产生加工 硬化的脆化粉体,都将随着施加压力的增加发 生脆性断裂形成较小的碎块。