车床《主轴刚度校核》
材料力学课程设计-车床主轴设计
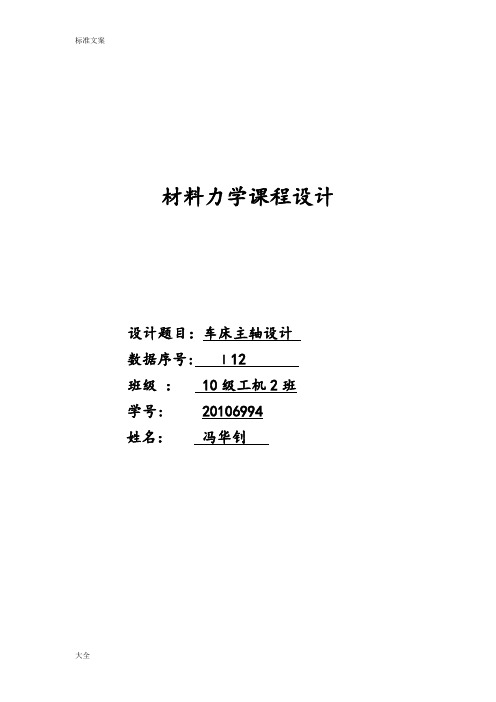
材料力学课程设计设计题目:车床主轴设计数据序号: Ⅰ12 班级: 10级工机2班学号: 20106994姓名:冯华钊目录一、材料力学课程设计的目的二、材料力学课程设计的任务和要求三、设计题目四、对主轴静定情况校核1.根据第三强度理论校核2.根据刚度进行校核3.疲劳强度校核五、对主轴超静定情况校核1.根据第三强度理论校核2.根据刚度进行校核3.疲劳强度校核六、循环计算程序七、课程设计总结一、设计目的材料力学课程设计的目的是在于系统的学习材料力学之后,能结合工程中的实际问题,运用材料力学设计的基本原理和计算方法,独立计算工程中的典型零部件,已达到综合运用材料力学的知识解决工程实际问题的能力。
同时,可以使我们将材料力学的理论和现代的计算方法及手段融为一体。
即从整体上掌握了基本理论和现代的计算方法,又提高了分析问题,解决问题的能力;即把以前学到的知识综合的运用,又为以后的学习打下了基础,并初步掌握工程中的设计思想和设计方法,对实际工作能力有所提高。
1.使我们的材料力学知识系统化,完整化。
2.在系统的全面的复习的基础上,运用材料力学的知识解决工程中的实际问题。
3.由于选题力求结合专业实际,因而课程设计可以把材料力学的知识和专业需要结合起来。
4.综合运用以前所学的各门课程知识,是相关学科知识有机的联系起来。
5.初步了解和掌握工程实践中的设计思想和方法,为以后打下基础。
二、设计的任务和要求1.画出受力分析计算简图和内力图2.列出理论依据和导出的计算公式3.独立编制计算机程序,通过计算机给出计算结果4.完成设计说明书。
三、设计题目车床主轴设计---某车床主轴尺寸及受力情况如图1所示。
在A、B、C三个支座的中间支座B处,轴承与轴承座之间有间隙δ,正常工作时,B处轴承不起支撑作用,此时轴处于A、C两支座下的静定状态。
当B截面处弯曲变形大于间隙δ时,轴处于A、B、C三支座下的静不定状态。
轴截面E处装有斜齿轮,其法向压力角为α,螺旋角为β,工作处的切削力有Fx、Fy、Fz(在进行强度、刚度计算时,可以不计轴向力Fx的影响,而以弯曲、扭转变形为主)。
机床主轴系统综合静刚度测定实验指导书07级
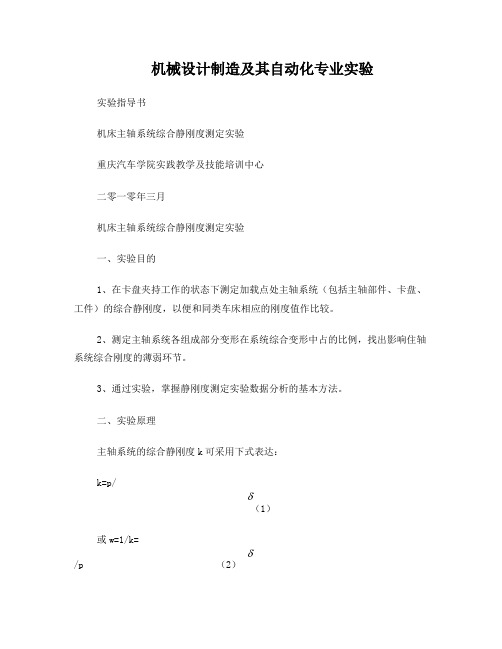
机械设计制造及其自动化专业实验实验指导书机床主轴系统综合静刚度测定实验重庆汽车学院实践教学及技能培训中心二零一零年三月机床主轴系统综合静刚度测定实验一、实验目的1、在卡盘夹持工作的状态下测定加载点处主轴系统(包括主轴部件、卡盘、工件)的综合静刚度,以便和同类车床相应的刚度值作比较。
2、测定主轴系统各组成部分变形在系统综合变形中占的比例,找出影响住轴系统综合刚度的薄弱环节。
3、通过实验,掌握静刚度测定实验数据分析的基本方法。
二、实验原理主轴系统的综合静刚度k可采用下式表达:k=p/(1)或w=1/k=/p (2)式中 w—主轴系统的综合静刚度。
(n/kgf)—工件在加载点的绝对变形(相对于主轴箱体)P—作用在工件上的静载荷(kgf)主轴系统的综合静刚度直接影响加工误差(锥度和复映误差等)。
静刚度过弱也是引起振动的重要原因。
因此对主轴系统进行综合刚度的考核时很有必要的。
但是主轴系统的综合静刚度仅反映主轴系统各组成部分在静载时的综合变形,不能用于分析各部分变形对综合刚度的影响程度。
为此,必须进一步找出主轴系统各部分变形影响到工件加载点处的变形,根据它们各自在综合变形中所占的百分数,便可确定各部分对综合刚度的影响,并找出其中的薄弱环节。
本次实验对象是车床,车削主要是在卡盘夹持的状态下工作。
这时,车床主轴系统由主轴部件(主轴与轴承)、卡盘、工件三部分组成。
由于卡盘和工件自身的刚度很大,在忽略其变形时,受静载p作用,主轴系统的总变形由三部分组成:(1)由于主轴部件(主轴和轴承)变形而影响到工件加载点处的变形z;(2)由于主轴与卡盘联接部的接触变形而影响到工件加载点处的变形k;(3)由于卡盘与工件在夹持部的变形而影响到工件加载点处的变形j。
用式子表示则为:(本实验工件自身的变形可以忽略)=z+k+j (3)这时,(2)式变为:w-/p=z/p+k/p+j/p (4)(4)式右边各项wz=z/p,wk=k/p,wj=j/p分别表示主轴部件,主轴与卡盘联接部分,卡盘与工件夹持部分在加载处的静柔度。
CA6150车床主轴箱设计(有全套图纸)(可编辑)
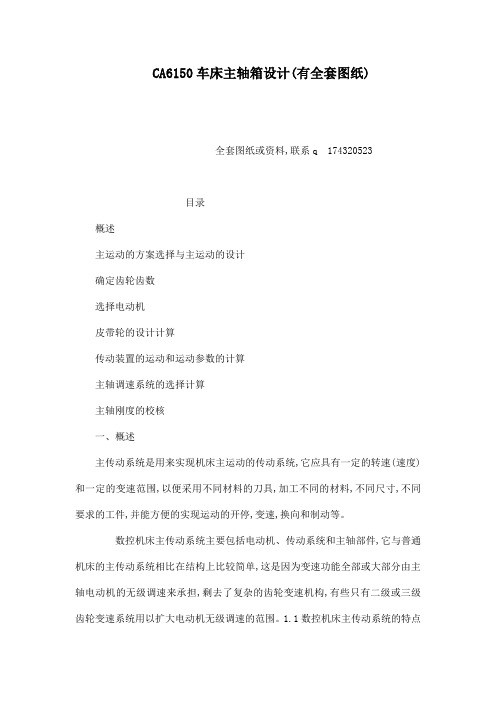
CA6150车床主轴箱设计(有全套图纸)全套图纸或资料,联系q 174320523目录概述主运动的方案选择与主运动的设计确定齿轮齿数选择电动机皮带轮的设计计算传动装置的运动和运动参数的计算主轴调速系统的选择计算主轴刚度的校核一、概述主传动系统是用来实现机床主运动的传动系统,它应具有一定的转速(速度)和一定的变速范围,以便采用不同材料的刀具,加工不同的材料,不同尺寸,不同要求的工件,并能方便的实现运动的开停,变速,换向和制动等。
数控机床主传动系统主要包括电动机、传动系统和主轴部件,它与普通机床的主传动系统相比在结构上比较简单,这是因为变速功能全部或大部分由主轴电动机的无级调速来承担,剩去了复杂的齿轮变速机构,有些只有二级或三级齿轮变速系统用以扩大电动机无级调速的范围。
1.1数控机床主传动系统的特点与普通机床比较,数控机床主传动系统具有下列特点。
转速高、功率大。
它能使数控机床进行大功率切削和高速切削,实现高效率加工。
变速范围宽。
数控机床的主传动系统有较宽的调速范围,一般Ra100,以保证加工时能选用合理的切削用量,从而获得最佳的生产率、加工精度和表面质量。
主轴变速迅速可靠,数控机床的变速是按照控制指令自动进行的,因此变速机构必须适应自动操作的要求。
由于直流和交流主轴电动机的调速系统日趋完善,所以不仅能够方便地实现宽范围无级变速,而且减少了中间传递环节,提高了变速控制的可靠性。
主轴组件的耐磨性高,使传动系统具有良好的精度保持性。
凡有机械摩擦的部位,如轴承、锥孔等都有足够的硬度,轴承处还有良好的润滑。
1.2 主传动系统的设计要求①主轴具有一定的转速和足够的转速范围、转速级数,能够实现运动的开停、变速、换向和制动,以满足机床的运动要求。
②主电机具有足够的功率,全部机构和元件具有足够的强度和刚度,以满足机床的动力要求。
③主传动的有关结构,特别是主轴组件要有足够高的精度、抗震性,热变形和噪声要小,传动效率高,以满足机床的工作性能要求。
车床主轴箱课程设计机床主轴箱有全套CAD图纸

目录1、参数的表述2、体育设计3、传动件的估算和校核计算4、展开图的设计5、摘要一.参数制定1、确定公比φ。
已知Z = 12级(采用集中传输)nmax =1800 nmin=40Rn =φz-1所以算出来φ≈1.41。
2.确定电机功率n。
根据ф 320和ф 400车床的设计参数,采用插补方法:已知最大旋转直径为ф 360。
切割深度ap(t)为3.75毫米,进给速度f (s)为0.375毫米/转,切割速度V为95米/分钟。
计算:主(垂直)切削力:FZ = 1900ap0.75n=1900 X 3.75 X0.3750.75牛顿≈3414.4北纬切割功率:N切割= FZV/61200千瓦= 5.3千瓦主电机的估计功率:N= N cut/η total= N切割/0.8千瓦=5.3/0.8千瓦=6.6千瓦因为N的取值必须根据Y系列中国产电机的额定功率来选择,所以选择7.5 KW。
第二,体育运动的设计1.列出结构式12=2[3] 3[1] 2[6]因为:如果换向摩擦离合器安装在I轴上,为了减小轴向尺寸,第一个传动组的传动副数不宜多,2个为好。
在机床设计中,由于所需的R较大,最终展开组选择2比较合适。
由于I 轴装有摩擦离合器,结构上要求齿轮的根圆大于离合器的直径。
2.画出结构网络。
3.绘制速度图。
1)主电机的选择电动机功率n: 7.5kw电机速度nd:因为nmax =1800r/min,按N=7.5 KW,因为电机转速nd应接近或适宜于主轴的最大转速,以免采用过大的增速或过小的减速传动。
因此,电机初步确定为Y132m-4,电机转速为1440r/min。
2)恒速传动在变速传动系统中,采用定比传动,主要考虑传动、结构和性能的要求,以满足不同用户的要求。
为了减缓中间两个齿轮组的速度,减小齿轮箱的径向尺寸,在ⅰ-ⅱ轴之间增加了一对减速传动齿轮。
3)分配减速比。
① 12步减速:40 56 80 12 112 160 224 315 450630900 1250 1800(转/分钟)②确定ⅳ档和ⅴ档之间的最小减速传动比:由于齿轮的极限传动比限定为imax=1/4,为了提高主轴的稳定性,最后一个换挡的减速比为1/4。
卧式车床主轴箱设计

卧式车床主轴箱设计摘要金属切削机床在国民经济现代化建设中起着重大的作用。
机床技术水平的高低已成为衡量一个国家工业现代化水平的重要标志之一。
机床工业是机械制造业的“装备部”,对国民经济的发展起着重大作用。
本论文设计的主轴箱的变速级数是12级,传动比为1.41,转速从31.5r/min 到1440r/min,加工工件的最大直径为400mm,。
论文对箱体内结构进行方案设计,并对传动方案、传动路线进行了分析,离合器、带轮、润滑系统、密封装置等进行了设计、计算及校核。
本设计的主要内容包括:1.运动设计:确定主轴的转速、拟定合理结构式、结构网和转速图、确定齿轮的齿数、皮带轮的设计计算以及实际转速和标准速偏差的校核等。
2.动力设计:估算各传动轴的转速、估算各轴的直径、选择电动机、齿轮强度验算、主轴刚度的校核、轴承寿命的验算、选择离合器。
3.结构设计:确定各传动组件的空间布置。
关键词:主轴箱,齿轮,摩擦式离合器HORIZONTAL LATHE SPINDLE BOX DESIGNABSTRACTMetal-cutting machine tool in the modernization of the national economy plays an important role. The level of machine technology has become the measure of a country's level of industrial modernization of one of the important symbols. Machine tool industry is the machinery manufacturing industry, "the Ministry of Equipment," the development of the national economy played a major role.In this paper, the design of the spindle box is a series of 12 speed, 1.41 gear ratio, speed from 31.5r/min to 1440r/min, the maximum workpiece diameter of 400mm,. Papers箱体内structure of the program design, and program transmission, transmission line analysis, clutch, pulley, lubrication systems, such as a seal design, calculation and checking.The main elements of the design include: 1. Campaign Design: to determine the speed of the spindle to draw up a reasonable-structured, the structure of network and the speed map to determine the number of teeth of gears, pulleys, as well as the design and calculation of the actual speed and standard deviation of the check, such as speed. 2. Dynamic Design: to estimate the speed of the shaft, to estimate the diameter of the axis, select the motor, gear strength check, the check spindle rigidity, bearing life of the check, select the clutch. 3. Structural Design: To determine the spatial arrangement of drive components.KEY WORDS: Main spindle box,Gear,Friction clutch assembly目录前言 (1)第1章设计分析 (2)1.1机床主要技术参数 (2)1.1.1尺寸参数: (2)1.1.2运动参数: (2)1.1.3动力参数: (2)1.2确定结构方案 (2)1.3主传动系统运动设计 (3)1.3.1拟订结构式 (3)1.3.2绘制转速图 (3)1.3.3确定齿轮齿数 (3)1.3.4验算主轴转速误差: (3)1.4估算传动件参数,确定其结构尺寸 (4)1.4.1确定传动件计算转速 (4)1.4.2确定主轴支承轴颈直径 (4)1.4.3估算传动轴直径 (5)1.4.4估算传动齿模数 (5)1.4.5离合器的选择与计算 (5)1.4.6普通V带的选择与计算 (7)1.5结构设计 (8)1.5.1带轮设计 (8)1.5.2主轴换向与制动机构设计 (9)1.5.3齿轮块设计 (9)1.5.4轴承的选择 (10)1.5.5主轴组件 (10)1.5.6润滑系统设计 (10)1.5.7密封装置设计 (10)1.6传动件验算 (10)1.6.1轴的强度验算 (10)1.6.2验算花键键侧压应力 (12)1.6.3滚动轴承验算 (12)1.6.4直齿圆柱齿轮的强度计算 (13)第2章主轴箱设计 (15)2.1运动设计 (15)2.1.1已知条件 (15)2.1.2结构分析式 (15)2.1.3绘制转速图 (16)2.1.4绘制传动系统图 (19)2.2动力设计 (19)2.2.1确定各轴转速 (19)2.2.3各传动组齿轮模数的确定和校核 (22)2.3齿轮强度校核 (23)2.3.1校核a传动组齿轮 (24)2.3.2校核b传动组齿轮 (25)2.3.3校核c传动组齿轮 (26)2.4主轴挠度的校核 (27)2.4.1确定各轴最小直径 (27)2.4.2轴的校核 (27)2.5主轴最佳跨距的确定 (28)2.5.1选择轴颈直径,轴承型号和最佳跨距 (28)2.5.2求轴承刚度 (28)2.6各传动轴支承处轴承的选择 (29)2.7主轴刚度的校核 (29)2.7.1主轴图 (30)2.7.2计算跨距 (30)结论 (32)谢辞 (33)参考文献 (34)前言随着机械的行业的发展,机床设计越来越向高精度的方向发展,但是在机床发展的同时,普通机床依然有这不可忽视的优点,例如低价格,加工种类多,对操作人员的技术要求低,缺点是加工的精度不高,效率不高,本书是设计12级普通车床,车床在机械行业中是举足轻重的角色,它可以加工外圆,螺纹等等,在本书的设计中参考了大量的前人的经验,对设计中出现的力学问题加以计算和解释,也对前人的观点加以考论和论证。
轴的扭转刚度校核

图12-4
3、钢丝软轴(挠性轴)
它不受任何空间的限制,可以将扭转或旋 转运动灵活地传到任何所需的位置,常用于医 疗设备、操纵机构、仪表等机械中。
图12-5
二、按照承受载荷不同分类
转轴:既承受扭矩又承 受弯矩(常见) 转动 根据承受载荷不同分类 受弯矩 心轴:只承受扭矩不承 固定 无弯矩 传动轴:只承受扭矩而
轴有不同的分类方法,也有不同类型的轴。 常用的分类方法有两类: 1)根据轴线的形状 不同分类;2)根据承受载荷不同分类。
光轴 根据需要可制成空心轴 直轴 阶梯轴 按轴线形状分类 旋转运动变为直线运动 曲轴:通过连杆可以把 可以穿过 钢丝软轴:具有挠性, 曲路传递运动或动力
三、轴的设计内容及应考虑的主要问题 与其它零件一样,轴的设计包括两个方面的 内容: 1 )轴的结构设计:即根据轴上零件的安装、定 位及轴的制造工艺等方面的要求,合理确定轴的 结构形状和尺寸。 2)轴的工作能力设计:即从强度、刚度和振 动稳定性等方面来保证轴具有足够的工作能力和 可靠性。对于不同机械的轴的工作能力的要求是 不同的,必须针对不同的要求进行。但是强度要 求是任何轴都必须满足的基本要求。
合金钢:对于要求强度较高、尺寸较小或有其 它特殊要求的轴,可以采用合金钢材料。耐磨 性要求较高的可以采用 20Cr、20CrMnTi 等低 碳合金钢;要求较高的轴可以使用40Cr(或用 3 5 SiMn、40MnB 代 替 ) 、 4 0 CrNi( 或 用 38SiMnMo代替)等进行热处理。 合金钢比碳素钢机械强度高,热处理性 能好。但对应力集中敏感性高,价格也较高。 设计时应特别注意从结构上避免和降低应力集 中,提高表面质量等。
所以,轴的设计程序是:先根据扭转强度 (或扭转刚度)条件,初步确定轴的最小直径; 然后,根据轴上零件的相互关系和定位要求, 以及轴的加工、装配工艺性等,合理地拟订轴 的结构形状和尺寸;在此基础上,再对较为重 要的轴进行强度校核。只有在需要时,才进行 轴的刚度或振动稳定性校核。 因而,轴的设计区别于其它零件设计过程 的显著特点是:必须先进行结构设计,然后才 能进行工作能力的核算。
主轴刚度校核

主轴刚度校核通常只作刚度验算1.弯曲变形验算(1)端部桡度y≤[y]≤0.0002ll—跨距,前后车轴间的轴向距离(2)前支承处倾角θb≤[θ]≤0.001rad(3)小齿轮处倾角θ≤[θ]≤0.001rad2.扭转变形验算改变角φ≤1°支承简化与受力分析tmax=955⨯104⨯n⨯η=(n∙mm)njn--电机功率;η--机械效率取(0.75~0.85);nj--主轴计算转速fc'=2⨯tmax=(n),其中d=0.5⨯dmax=dff'=0.35⨯fc'=(n)fp'=0.5⨯fc'=(n)由f=a+0.4⨯dmaxf'作用在主轴端部的作用力afz=p=2⨯tmax=(n),其中df—齿轮分度圆直径df分解成水平面受力图:fp;fz1=fz×cosθ;m=ff×d/2分解成垂直面受到力图:fc;fz2=fz×sinθ(注意各力和力矩的方向,和公式示图相反加负号)ⅰ刚性车轴、弹性主轴(指导书p34)由传动力fz引起的变形:主轴端部桡度:y=-p⋅a⋅b.c(l+a)=(1-1)6e⋅i⋅lp⋅a⋅b(b-a)=(2-1)大齿轮处倾角:θ1=3e⋅i⋅lp⋅a⋅b⋅(2a+b)=(3-1)前车轴处倾角:θ2=-6e⋅i⋅l由切削力fp(fc)引起的变形:p⋅c2(l+c)=(1-2)主轴端部桡度:y=3e⋅ip⋅c(l2-3a2)=(2-2)6e⋅i⋅lp⋅c⋅l=(3-2)前车轴处倾角:θ2=3e⋅i小齿轮处倾角:θ1=-由切削力矩m引起的变形:m⋅c(2l+3c)=(1-3)6e⋅i⋅lm(l2-2a2)=(2-3)小齿轮处倾角:θ1=-6e⋅i⋅lm⋅l=(3-3)前支承处倾角:θ2=3e⋅i主轴端部桡度:y=PR320横截面惯性矩i=π⋅d464⨯(1-d0d)4=d—主轴平均值直径;do—主轴内孔直径材料弹性模量:e=2.1×105(mpa)ⅱ刚性主轴、弹性车轴由传动力fz引起的变形:主轴端部桡度:y=p(l+c)⨯(l-b)pbc-=(1-4)cb⨯l2ca⨯l2p(l-b)p⨯b-=(2-4)22cb⨯lca⨯l小齿轮和前车轴处倾角:θ1=θ2=由切削力fp(fc)引起的变形:主轴端部桡度:y=pcpc(1+)2+⨯()2=(1-5)cblcal p(l+c)p⨯c+=.(2-5)22cb⨯lca⨯l小齿轮和前车轴处倾角:θ1=θ2=由切削力矩m引起的变形:主轴端部桡度:y=m(l+c)m⨯c+=(1-6)cb⨯l2ca⨯l2 mm+=(2-6)22cb⨯lca⨯l小齿轮和前车轴处倾角:θ1=θ2=轴承刚度:ca=ra/∆0=;cb=rb/∆0=ra---后端的车轴反力;rb---前端车轴反力;δ0---轴承径向加速度量f3182100系列双列向心短圆柱滚子轴承:∆0=0.062⨯r0.815=(μm)d0.8950.077q0.9圆锥滚子轴承:∆0=⨯0.8=(μm)cosαl0滚动体上的载荷:q=5fr=(n)izcosαfr--轴承的径向载荷;d--轴承的孔径;α--轴承的接触角;z--每列于中翻转体数;i--翻转体列数;l0—滚子长度因此水平方向:y=y11+y12+y13+y14+y15+y16=θ1=θ21+θ22+θ23+θ24+θ25+θ26=θ2=θ31+θ32+θ33+θ24+θ25+θ26=y=y11+y12+y14+y15=θ1=θ21+θ22+θ24+θ25=θ2=θ31+θ32+θ24+θ25=综上所述y=y221+y2=(---)2=(---)2=(---)φ=tmax⨯lg⨯i⨯180抗炎抖横截面惯性矩i=132π(d4-d4环流模量g=8.1⨯104(mpa)l—主轴端部到大齿轮处的受扭长度d—主轴平均直径;do—主轴内孔直径。
CA6140车床主轴箱的设计18级公比1.26

目录一、设计目的 (1)二、设计步骤 (1)1.运动设计 (1)1.1已知条件 (1)1.2结构式分析 (1)1.3 绘制转速图 (2)1.4 绘制传动系统图 (5)2.动力设计 (5)2.1确定各轴转速 (5)2.2带传动设计 (6)2.3各传动组齿轮模数的确定和校核 (7)3.齿轮强度校核 (9)3.1 校核 a 组传动组齿轮 (9)3.2 校核 b 组传动组齿轮 (10)3.3 校核 c 组传动组齿轮 (11)4.主轴挠度的校核 (13)4.1确定各轴的最小直径 (13)4.2轴的校核 (14)5.主轴最佳跨距的确定 (14)5.1 选择轴颈直径,轴承型号和最佳跨距 (14)5.2 求轴承刚度 (14)6.各传动轴支承处轴承的选择 (15)7.主轴刚度的校核 (15)7.1 主轴图 (15)7.2 计算跨距 (16)三、总结 (17)四、参考文献 (18)一、设计目的通过机床主运动机械变速传动系统得结构设计,在拟定传动和变速的结构方案过程中,得到设计构思、方案分析、结构工艺性、机械制图、零件计算、编写技术文件和查阅技术资料等方面的综合训练,树立正确的设计思想,掌握基本的设计方法,并具有初步的结构分析、结构设计和计算能力。
二、设计步骤1.运动设计1.1 已知条件[1]确定转速范围:主轴最小转速 n min =37.5r / min 。
[2]确定公比:1.26[3]转速级数: z 181.2 结构分析式⑴18 3 2 3⑵18 3 3 2[3]18 2 33从电动机到主轴主要为降速传动,若使传动副较多的传动组放在较接近电动机处可使小尺寸零件多些,大尺寸零件少些,节省材料,也就是满足传动副前多后少的原则,因此取 18 2 3 3方案。
在降速传动中,防止齿轮直径过大而使径1向尺寸常限制最小传动比i min;在升速时为防止产生过大的噪音和震动常限制最大转速比 i max2 。
在主传动链任一传动组的最大变速范围 R max i max i min 8 ~ 10 。
- 1、下载文档前请自行甄别文档内容的完整性,平台不提供额外的编辑、内容补充、找答案等附加服务。
- 2、"仅部分预览"的文档,不可在线预览部分如存在完整性等问题,可反馈申请退款(可完整预览的文档不适用该条件!)。
- 3、如文档侵犯您的权益,请联系客服反馈,我们会尽快为您处理(人工客服工作时间:9:00-18:30)。
主轴校核
通常只作刚度验算(P110) 1. 弯曲变形验算
(1)端部桡度y ≤[Y] ≤0.0002L L —跨距,前后支承间的轴向距离 (2)前支承处倾角θB ≤[θ] ≤0.001rad (3) 大齿轮处倾角θ≤[θ] ≤0.001rad 2.扭转变形验算 扭转角φ≤1°
支承简化与受力分析
)(109554max mm N n N T j
∙=⨯⨯
⨯=η
(P115) N--电机功率; η--机械效率取(0.75~0.85); nj--主轴计算转速
)(2'max
N d
T F c =⨯=
, 其中=⨯=max 5.0D d )('35.0'N F F c f =⨯= )('5.0'N F F c p =⨯=
由'4.0max
F a
D a F ⨯+=
作用在主轴端部的作用力
)(2max
N d T P F f
z =⨯=
= , 其中d f —齿轮分度圆直径 分解成水平面受力图:Fp ; Fz 1=Fz ×cos θ; M=F f ×d/2 分解成垂直面受力图:Fc ; Fz 2=Fz ×sin θ
Ⅰ刚性支承、弹性主轴 (指导书P78,表5-22) 由传动力Fz 引起的变形:
主轴端部桡度:=-⋅⋅⋅⋅-
=)(6.a l L I E c
b a P y (1-1)
大齿轮处倾角:=-⋅⋅⋅⋅=)(31a b L
I E b
a P θ (2-1)
前支承处倾角:=⋅⋅+⋅⋅⋅-=L
I E b a b a P 6)
2(2θ (3-1)
由切削力Fp(Fc)引起的变形:
主轴端部桡度:=+⋅⋅⋅=
)(32
c L L
I E c P y (1-2) 大齿轮处倾角:=-⋅⋅⋅-=)3(6221a L L I E c
P θ (2-2)
前支承处倾角:=⋅⋅⋅=I E L
c P 32θ (3-2)
由切削力矩M 引起的变形:
主轴端部桡度:=+⋅⋅⋅=)32(6c L L
I E c
M y (1-3)
大齿轮处倾角:=-⋅⋅-=)2(6221a L L I E M
θ (2-3)
前支承处倾角:=⋅⋅=I E L
M 32θ (3-3)
抗弯截面惯性矩=-
⨯⋅=
44
)1(64
0d
d d I π d —主轴平均直径;do —主轴内孔直径
材料弹性模量:E=2.1×105(MPa )
(注意各力和力矩的方向,和公式示图相反加负号)
Ⅱ刚性主轴、弹性支承(指导书P111,表6-23)
由传动力Fz 引起的变形: 主轴端部桡度:=⨯-⨯-⨯+=
2
2)()(l C Pbc
l C b l c l P y A B (1-4)
大齿轮和前支承处倾角:=⨯⨯-⨯-==2
22)(1l
C b
P l C b l P A B θθ (2-4) 由切削力Fp(Fc)引起的变形: 主轴端部桡度:=⨯++=
22)()1(l
c
C P L C C P y A B (1-5) 大齿轮和前支承处倾角:.)(2
221=⨯⨯+⨯+==l
C c
P l C c l P A B θθ (2-5) 由切削力矩M 引起的变形: 主轴端部桡度:=⨯⨯+⨯+=
2
2B C )(l
C c M l c l M y A (1-6) 大齿轮和前支承处倾角:=⨯+⨯=
=2
221l
C M
l C M A B θθ (2-6) 轴承刚度: =∆==∆=00/;/B B A A R C R C
R A ---后端支承反力; R B ---前端支承反力; Δ0---轴承径向位移量
3182100系列双列向心短圆柱滚子轴承:=⨯=∆815.0895
.00062.0d
F
r (μm)
圆锥滚子轴承:=⨯=∆8.009
.00cos 077.0l Q α (μm)
滚动体上的载荷:==
α
cos 5iZ Fr
Q (N )
Fr--轴承的径向载荷; d--轴承的孔径; α--轴承的接触角; Z--每列中滚动体数; i--滚动体列数; l 0—滚子长度
因此水平方向:
=+++++=161514131211y y y y y y y
=+++++=2625242322211θθθθθθθ
=+++++=2625243332312θθθθθθθ
垂直方向:
=+++=15141211y y y y y
=+++=252422211θθθθθ
=+++=252432312θθθθθ
综上所述
L y y y 0002.0)(2
221<---=+=
001.0)(22211<---=+=θϑθ
001.0)(22212<---=+=θϑθ
合格∴
扭转校核
π
180
max ⨯⨯⨯=
ΦI G L T = L —主轴端部到大齿轮处的受扭长度
抗扭截面惯性矩()
=-=
40432
1
d d I π d —主轴平均直径;
do —主轴内孔直径 切变模量 4101.8⨯=G (MPa )。