配料计算
3-配料计算

其中0.5603为CaCO3转化为CaO的转化系数。 ②配方中的MgO只能由滑石引入,因此引入质量为1.3的 MgO需要的滑石质量为:
滑石的质量=1.3/0.317=4.10 ③配方中的SiO2由高岭土和滑石同时引入,所以,需引入的 高岭土质量为:
2019/12/19
④工业纯A12O3的引入质量为: ⑤引入原料的总质量为:
在配方计算时,原料有氧化物(如MgO),也有碳酸盐(如 MgCO3)以及其它化合物。其计算标准一般根据所用原料化学 分子式计算最为简便。只要把主成分按摩尔数计算配入坯料 中去即可。对于用铅类氧化物配料.如果用PbO配料,则 PbO为1摩尔,如果用Pb3O4时,PbO就是3摩尔。
2019/12/19
例如配置(Ba0.85Ca0.15 ) TiO3 ,采用BaCO3 , CaCO3 ,TiO2原 料进行配料,按以上所述的计算法, 列入表1-2-1进行计算。
2019/12/19
对于陶瓷的配方,除了主成分外,还有添加物。这些添加 物有的是为了调整性能,有的是为了调整工艺参数。其用量是 根据试验研究的结果和实际生产经验来确定的。配方时,可按 质量百分比组成表示,也可采用外加方式表示。
在配料时,每次配料都不可能完全相同,如果原料有所变 更,有可能出现不同情况。因此,每一次配料都应标明原料的 产地、批量、配料日期和人员,以便当制品性能发生变化时进 行查考和分析。如果有条件,每批原料应作化学分析,尤其是 微量杂质,这在陶瓷研制和生产中也很重要。
2019/12/19
⑴由坯料的实验公式计算
在陶瓷配方中,常常遇到这样的化学分子Ca(Ti0.54Zr0.46)O3, (Ba0.85Sr0.15)TiO3,Pb0.9325Mg0.0675 ,(Zr0.44Ti0.56)O3等等这种分子式,实质 上与ABO3相似,其特点是A位置上和B位置上各元素右下角系数的 和等于1。例如(Ca0.85Ba0.15 ) TiO3可以看成是CaTiO3中有15%摩尔的 Ca被Ba取代了。从上面的情形来看,“ABO3”型化合物中,A或B 都能为其它元素所取代,从而能达到改性的目的,而且这种取代 能形成固溶体及化合物。这种取代能形成固溶体及化合物。这种 取代是任意的,而是有条件的。
(12全)生料配料计算
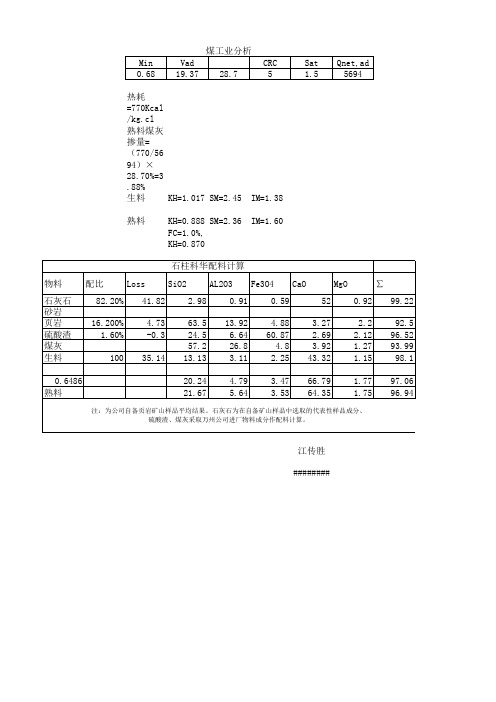
江传胜 ########
灰分 30.90% ########
Qnet,ad 设计热耗 煤灰掺量 5207 800 4.74746
铜梁中联配料计算
物料(干基) 配比 石灰石 86.00% 石英砂 5.00% 砂岩 4.000% 钢渣 5.00% 煤灰 Loss
40.12 2.66 4.24 4.35
煤工业分析 Min 0.68 Vad 19.37 28.7 CRC 5 Sat 1.5 Qnet,ad 5694
热耗=770Kcal/kg.cl 熟料煤灰掺量=(770/5694)×28.70%=3.88% 生料 KH=1.017 SM=2.45 IM=1.38 熟料 KH=0.888 SM=2.36 FC=1.0%,KH=0.870 IM=1.60
物料 石灰石 砂岩 页岩 硫酸渣 煤灰 生料 0.6486 熟料
石柱科华配料计算 配比 Loss SiO2 AL2O3 Fe3O4 CaO 82.20% 41.82 2.98 0.91 0.59 16.200% 1.60% 100 4.73 -0.3 35.14 63.5 24.5 57.2 13.13 20.24 21.67 13.92 6.64 26.8 3.11 4.79 5.64 4.88 60.87 4.8 2.25 3.47 3.53
进厂煤
进厂Mar 10.9
Mad 1.27Aad 3源自.9Vad 21.00Fad 46.81
S,ad 1.47
Qnet,ad 5207
∑ 98.58 99.22983 96.04029 93.13478 93.89
98.2386
97.28925
98.6279 1.44182
灼烧生料 20.09867 3.817092 3.171672 68.40188 1.79993
配料计算方法
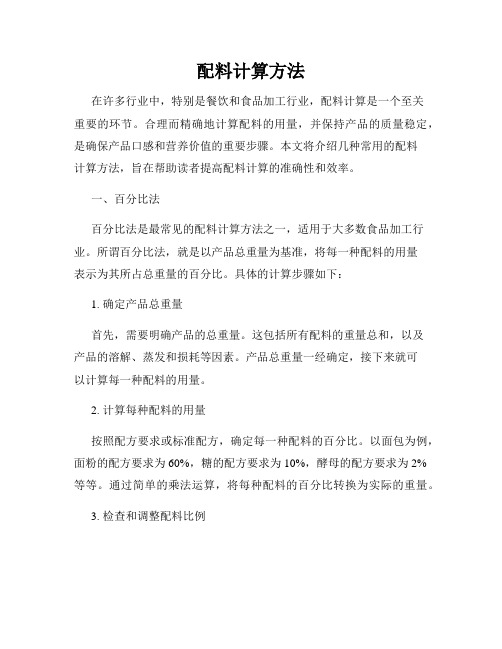
配料计算方法在许多行业中,特别是餐饮和食品加工行业,配料计算是一个至关重要的环节。
合理而精确地计算配料的用量,并保持产品的质量稳定,是确保产品口感和营养价值的重要步骤。
本文将介绍几种常用的配料计算方法,旨在帮助读者提高配料计算的准确性和效率。
一、百分比法百分比法是最常见的配料计算方法之一,适用于大多数食品加工行业。
所谓百分比法,就是以产品总重量为基准,将每一种配料的用量表示为其所占总重量的百分比。
具体的计算步骤如下:1. 确定产品总重量首先,需要明确产品的总重量。
这包括所有配料的重量总和,以及产品的溶解、蒸发和损耗等因素。
产品总重量一经确定,接下来就可以计算每一种配料的用量。
2. 计算每种配料的用量按照配方要求或标准配方,确定每一种配料的百分比。
以面包为例,面粉的配方要求为60%,糖的配方要求为10%,酵母的配方要求为2%等等。
通过简单的乘法运算,将每种配料的百分比转换为实际的重量。
3. 检查和调整配料比例完成计算后,应该对所有配料的用量进行检查,确保其总和等于产品总重量。
如果发现偏差,需要进行适当的调整。
此外,还应该根据实际经验和产品要求,对各种配料的用量进行优化和改进。
二、配方表法配方表法是一种常用的配料计算方法,特别适用于多种产品的加工场所。
配方表是一个记录了每种配料名称和用量的表格,通过参考配方表,工作人员可以准确地投入所需的配料。
1. 设计配方表首先,需要设计一个配方表,列出产品所使用的所有配料及其用量。
配方表的设计应该清晰明了,包括配料名称、用量单位和所占百分比等信息。
可以使用Excel等软件制作配方表,方便后续计算和记录。
2. 参考配方表进行计算在加工过程中,根据需要的产品种类和数量,参考配方表中的配料用量进行计算。
只需输入所需产品的总重量,配方表会自动计算出每种配料的实际用量。
这样,就可以准确地投入所需的配料,确保产品质量的稳定性。
三、成本法成本法是一种以经济成本为基础的配料计算方法。
配料计算方法

配料计算学习资料一.配料计算的基本过程1•了解炉料的化学成分。
2•确定目标铁水成分。
3•初步确定生铁、废钢、回炉料、铁沫的加入量4.根据配比计算C、Si、Mn、P、S、Cu、Cr当前配料含量8•计算添加缺少的合金(增碳剂、硅铁、锰铁等等)二.各种炉料的参考成分如果有化验单,则必须以化验单为准。
如果没有则按以下数值估算。
说明:1.以上都是平时常见数据,配料需要及时了解各种材料化验单并替换上述数。
2.表格内空格都按没有计。
3•回炉料和铁沫成分就是该产品实际控制的化学成分(应该和作业基准书相同)三.确定配料目标值配料目标就是工艺要求的化学成分,但是要区分原铁水和孕育后。
四.确定生铁、废钢、回炉、铁沫加入量按工艺文件和配料单确定加入量。
五.计算定好的配料各种合金成分举例:配料 Q10生铁 30%,废钢 30%,回炉 40% (C3.6、Si2.6,、Mn0.6)含碳量=0.3*4.3+0.3*0.2+0.4*3.6=2.88含硅量=0.3*0.8+0.3*0.2+0.4*2.6=1.34含锰量=0.3*0.3+0.3*0.4+0.4*0.6=0.45说明:上述公式中0.3和0.4分别表示30%和40%,今后以此类推如果配料还有铁沫一项,就增加一项铁沫的我们用的合金含量都是假设的,今后需要多看材料的化验单并按化验单计六。
计算需要添加合金的含量举例:目标含量是C3.85 Si1.6 Mn0.6按第五项举例的结果计算合金量增碳剂:(3.85-2.88)/0.8 =1.2%硅铁:(1.6-1.34)/0.7 =0.37%锰铁:(0.6-0.45) /0.6 =0.25%说明:公式中0.8、0.7、0.6分别表示增碳剂、硅铁、锰铁含量是80%、70%、60% 我们用的合金含量都是假设的,今后需要多看材料的化验单并按化验单计计算结果是百分数,具体加多少乘上铁水量就行了。
比如出1000公斤铁水,那么增碳剂加入量是1.2%*1000=1.2*1000/100=12公斤计算的时候注意百分号中的100,需要除以100 简便计算方法:出1000公斤铁水,加入合金增加值。
配料及填充率计算

配料及填充率计算一、配料计算配料计算是确定制作食品所需的原料数量和比例。
它涉及到确定每种原料的重量或体积,以确保食品产品的质量和口感的一致性。
1.配料计算的目的:-确保产品的质量和口感一致性,保持产品品质的稳定性;-控制生产成本,降低原料和材料的浪费;-符合法规要求,确保配料的准确性和食品安全性。
2.配料计算的方法:配料计算可以通过以下几种方法进行:-固定比例法:根据食品配方中每种原料的推荐比例确定所需原料的重量或体积;-以目标产量为基础的计算:根据生产所需的食品产品的目标数量,按比例计算所需原料的重量或体积;-标准配方法:根据已有的标准配方,按比例计算所需原料的重量或体积。
3.配料计算的注意事项:在进行配料计算时,需要注意以下几点:-精确度:计算配料时需要精确到小数点后几位,以确保配料的准确性;-考虑损耗:在计算配料时,需要考虑原料在加工过程中的损耗情况,以确保最终产品的质量和成本效益。
填充率计算是确定食品产品包装容器的填充率,即所填充物体在容器内的百分比。
它涉及到确定适当的填充物体积,以确保产品的安全性和包装的完整性。
1.填充率计算的目的:-确保食品产品的安全性,在运输和储存过程中,避免因装载不足或过度装载导致包装容器受损或食品产品受污染;-符合法规要求,确保填充物的准确性和包装的完整性。
2.填充率计算的方法:填充率计算可以通过以下几种方法进行:-体积法:根据包装容器的内部体积和填充物的体积,计算填充率;-重量法:根据包装容器的重量和填充物的重量,计算填充率;-高度法:根据填充物的高度和容器的高度,计算填充率。
3.填充率计算的注意事项:在进行填充率计算时,需要注意以下几点:-容器形状:不同形状的容器可能会影响填充率的计算结果,需要根据实际情况进行调整;-填充物体积:填充物的体积应该与容器的内部体积相匹配,以确保产品的安全性和包装的完整性;-法规要求:根据食品包装的法规要求,确定填充物的准确性和包装的完整性。
1配料计算

1.炉料成分的配定原则配料过程中,炉料化学成分的配定主要考虑钢种规格成分、冶炼方法、元素特性及工艺的具体要求等。
具体为:(1)碳的配定。
炉料中碳的配定主要考虑钢种规格成分、熔化期碳的烧损及氧化期的脱碳量,还应考虑还原期补加合金和造渣制度对钢液的增碳。
熔化期碳元素的烧损与助熔方式有关,可根据实际生产的具体条件,总结固有规律,一般波动在0.60%左右。
氧化期的脱碳量应根据工艺的具体要求而定,对于新炉时的第一炉,脱碳量应大于0.40%。
不氧化法碳的配定应保证全熔碳位于钢种规格要求的下限附近。
(2)硅的配定。
在一般情况下,氧化法冶炼钢铁料的硅主要是由生铁和废钢带入,全熔后的硅不应大于0.30%,以免延缓熔池的沸腾时间。
返吹法冶炼为了提高合金元素的收得率,根据工艺要求可配入硅废钢或硅铁,但也不宜超过1.0%以上,对于特殊情况也可不配。
(3)锰的配定。
用氧化法冶炼的钢种,如锰的规格含量较高,配料时一般不予以考虑;如锰的规格含量较低,配料时应严格控制,尽量避免炼钢工进行脱锰操作。
对于一些用途重要的钢种,为了使钢中的非金属夹杂物能够充分上浮,熔清后钢液中的锰含量不应低于0.20%,但也不宜过高,以免影响熔池的沸腾及脱磷。
由于不氧化法或返吹法冶炼脱锰操作困难,因此配锰量不得超过钢种规格的中限。
高速钢中锰影响钢的晶粒度,配入量应越低越好。
(4)铬的配定。
用氧化法冶炼的钢种,钢中的铬含量应尽可能的低。
冶炼高铬钢时,配铬量不氧化法按出钢量的中下限控制,返吹法则低于下限。
(5)镍、钼元素的配定。
钢中镍、钼含量较高时,镍、钼含量按钢种规格的中下限配入,并同炉料一起装炉。
冶炼无镍钢时,钢铁料中的镍含量应低于该钢种规定的残余成分。
高速钢中的镍对硬度有害无利,因此要求残余含量越低越好。
(6)钨的配定。
钨是弱还原剂,在钢的冶炼过程中,因用氧方式的不同而有不同的损失。
矿石法冶炼,任何钢种均不人为配钨,且要求残余钨越低越好。
不氧化法和返吹法冶炼时,应按钢种规格含量的中下限配入,并同炉料一起装炉。
配料计算方法

配料计算的方法烧结过程是一个非常复杂的氧化还原过程,氧的得失很难确定,原料成分的波动和水分的大小均会对最终结果产生影响,而要精确进行烧结配料的理论计算,在烧结生产中显得尤为麻烦,并且要占用大量的时间,所以,现场配料计算一般多采用简易计算方法,即:反推算法。
所谓反推算法是先假定一个配料比,并根据各种原料的水分、烧损、化学成分等原始数据,计算出烧结矿的化学成分,当计算结果符合生产要求,即可按此料比进行组织生产,如果不否,再重新进行调整计算,直至满足生产要求为止。
如果在实际生产中,所计算的配比和实际有误差,可分析其产生误差的原因,并再次进行调整计算。
生产中如何确定配料比,也是大家所关心的一个问题,实际上配料比的确定常常是根据炼铁生产对烧结矿的质量指标的要求和原料供应状况以及原料成分等,并结合生产成本进行合理的搭配,反复计算,得出最终使用的配料比。
在进行反推算法计算时,首先要了解有关配料方面需要掌握的一些术语。
烧损:物料的烧损是指(干料)在烧结状态的高温下(1200—14000C)灼烧后失去重量对于物料试样重量的百分比。
烧残:物料的残存量即物料经过烧结,排出水分和烧损后的残存物量。
水分:烧结原料的水分含量是指原料中物理水含量的百分数,即一定的原料(100g—200g)加热至1500C,恒温1h,已蒸发的水分重量占试样重量的百分比。
化学成分:原料的化学成分是指某元素或化合物含量占该种干原料试样重量的百分比。
具体计算公式烧残量=干料配比×(1—烧损)进入配合料中的TFe=该种原料含TFe 量×该种原料配比进入配合料中的SiO2=该种原料含SiO2量×该种原料配比进入配合料中的CaO=该种原料含CaO量×该种原料配比进入配合料中的MgO=该种原料含MgO量×该种原料配比进入配合料中的Mn=该种原料含Mn量×该种原料配比烧结矿的化学成分烧结矿TFe=各种原料带入的TFe之和÷总的烧残量烧结矿SiO2=各种原料带入的SiO2之和÷总的烧残量烧结矿CaO=各种原料带入的CaO之和÷总的烧残量烧结矿MgO=各种原料带入的MgO之和÷总的烧残量烧结矿Mn=各种原料带入的Mn之和÷总的烧残量如果还有其他指标要求,其计算公式同上。
高碳锰铁配料计算

高碳锰铁配料计算1、计算依据:1.1入炉锰矿平均成分:%Mn Fe P S Cao SiO2 MgO AI2O343 6 0.07 0.05 3 9 1 41.2锰矿元素分配:%1.3焦碳成分:固定碳:82%、灰分:15%、挥发分:3%、焦碳利用率:90%、炉口烧损:10%、水分:10%、焦碳灰分中含SiO2 : 50%、Cao : 3%、MgO : 2%1.4以100Kg干基锰矿做为计算基础。
2、合金成分的预算每100Kg锰矿可得:Mn = 43X0.62 = 26.66KgFe = 6X0.95 = 5.7KgP = 0.07 >0.90 = 0.063KgMn+ Fe+ P = 26.66+5.7+0.063 = 32.423Kg(Mn+ Fe+ P)合金名的百分比为:[100 - (6.5+1.5+1.0 ) ]% =91.0%所以合金总量=32.423/0.9仁35.63Kg预计合金成份:Mn = 26.66/35.63 = 74.8%Fe = 5.7/35.63 = 16%P = 0.063/35.63 = 0.18%C = 6.5%Si = 1.5%其它=1%3、焦碳配入量计算:3.1锰矿中锰的高价氧化物受热分解成Mn3O4 ,Mn3O4还原成MnO需Mn 3O4 + C = 3MnO + CO43 >12 / 165 = 3.12kg3.2还原进入高碳锰铁和挥发的锰需碳量:MnO + C = Mn + CO43 >0.62+0.1) 12/55 = 6.75kg3.3氧化铁还原需碳量:FeO + C = Fe + CO6 >0.95 >2 / 56 = 1.22kg3.4五氧化二磷还原需碳量:P2O5 + 5C = 2P + 5CO0.07 >(0.9+0.02) 5沟2/(2 B1)= 0.062kg 3.5二氧化硅还原需碳量:SiO2 + 2C = Si + 2CO9 X28/60 >4% >2 >2/28 = 0.144kg3.6高碳锰铁渗碳量:35.63 >.065 = 2.316kg3.7总需碳量:3.12+6.75+1.22+0.062+0.144+2.316=13.612 kg焦碳的固定碳为82%,利用率为90%,需干焦碳为:13.612/( 0.82 >.90)= 18.44kg4、配料比:锰矿:100kg (干),焦碳18.44kg (干,固定碳82% )。
- 1、下载文档前请自行甄别文档内容的完整性,平台不提供额外的编辑、内容补充、找答案等附加服务。
- 2、"仅部分预览"的文档,不可在线预览部分如存在完整性等问题,可反馈申请退款(可完整预览的文档不适用该条件!)。
- 3、如文档侵犯您的权益,请联系客服反馈,我们会尽快为您处理(人工客服工作时间:9:00-18:30)。
配料计算
3.原、燃料资源
3.1油页岩尾渣(石灰质原料)
油页岩干馏后尾渣平均化学成分(%)见表。
尾渣粒度小于100微米,密度1.0t/m3,
3.2硅质原料
本项目拟采用当地的砂岩作为硅质原料。
砂岩资源丰富,预计砂岩矿石储量在8000万吨以上。
砂岩采用民采民运,汽车运输进厂,运输距离12公里。
根据业主提供的资料,砂岩矿石的化学成分(%)见表。
砂岩矿石的化学成分 (%)
当地砂岩的SiO2含量高,质量满足本项目生产优质水泥熟料的技术要求。
3.3铝质校正原料
本项目用电厂的干排粉煤灰作为铝质校正原料,汽车运输进厂,运距10 km。
电厂粉煤灰的化学成分(%)见表。
粉煤灰的化学成分 (%)
上述粉煤灰Al2O3含量质量基本满足本项目的技术要求。
3.4铁质校正原料
本项目采用当地的硫酸渣作为铁质校正原料,汽车运输进厂,运距20km,有充足的供料保证。
根据提供的资料,硫酸渣的化学成分(%)见表。
硫酸渣的化学成分 (%)
上述硫酸渣的Fe2O3含量较高,质量基本满足本项目的技术要求。
3.5燃料用煤
本项目熟料煅烧用煤采用无烟煤,由汽车运输进厂,能满足供应。
煤的工业分析(%)及煤灰化学成分(%)分别见表。
无烟煤的工业分析 (%)
煤灰化学成分 (%)
煤的挥发份和含硫量较低,灰份适中,低位发热量较低,煤质基本满足本项目的煅烧技术要求。
3.6调凝剂
水泥生产所需调凝剂拟采用的脱硫石膏,汽车运输进厂。
根据业主提供的资料,进厂的脱硫石膏平均化学成分(%)见表。
脱硫石膏化学成分报告 (%)
SO3含量较高,碱含量较低,质量优良且品位稳定,满足本项目水泥生产需要。
3.7炉渣
炉渣化学成分报告 (%)
熟料热耗的选择:
熟料热耗选择3050kj/kg熟料。
1).原燃料化学成分表(%)
2).煤的工业分析:
原煤水分:10%
3其他:
1).地形地貌
本项目所选厂址处于港区内,地势平坦。
2).气象条件
年平均气温: 21.1℃
年平均相对湿度:78%
年平均雾日:21.4天
年平均降水量:1464mm
潮汐:属于不规则半日潮,一天两涨两落,潮流平均流速0.08米/秒;
年主导风向:东南偏东。
5~11月为台风季节,主要集中在7~9
月。
年平均风速:2~5m/s
最大风速:19.3m/s
年平均雷暴日数:41.8天
地震烈度:Ⅶ度
2.2设计内容:
3.1设计范围 :从油页岩尾渣储存至水泥出厂整条生产线。
3.2工作内容
3.2.1工艺初步设计
3.2.2工艺设备表(标明各设备用水、用气量等)
3.2.3工艺流程图
3.2.4工艺计算书(包括物料量、气体量等计算,各种辅机规格的计算)。
2.3配料计算
配料计算的依据是物料平衡。
化学反应的物料平衡是:反应物的量应等于生成物的量。
计算时必须采用统一标准。
生料配料计算方法繁多,有代数法、图解法、尝试误差法(包括递减试凑法)、矿物组成法、最小二乘法等。
尝试误差法计算方法很多,但原理都相同。
其中一种方法是:先按假定的原料配合比计算熟料组成,若计算不符合要求,则要求重新调整原料配比,再进行计算,重复至符合为止,另一种方法是从熟料化学成分中依次递减假定配合比的原料成分,试凑至符合要求为止(又称递减试凑法)]4[。
本设计配料计算采用的是尝试误差法第一种计算方法,并结合计算机计算原料配合比。
该设计要求熟料的三个率值分别为:KH=0.9±0.02,SM=2.75±0.1,IM=1.59±
0.1。
取KH=0.9,SM=2.70,IM=1.59,单位熟料热耗为3050kj/kg 。
(1)计算煤灰掺入量:
100kg 熟料中的煤灰掺入量:
ad net Q s Aad q G ,100..a =
=%41.2230810
100100
64.223050=⨯⨯⨯
式中 Ga -熟料中煤灰掺入量(%);
q -单位熟料热耗(kj /kg 熟料) Q net,ad -煤的热值(kj /kg )
A ad -煤的空气干燥基灰分含量(%)
S -煤灰沉落率(%),可选100%;
(2)根据熟料率值估算熟料化学成分 已知:KH=0.9,SM=2.70,IM=1.59,则:
%247.335
.165.2)1)(18.2(e 32=++++=
∑
IM SM IM KH O F
∑=++-==+===%
8826.66)(%7075.22)(%
1632.5.23232323223232SiO O Al O Fe Ca O Fe O Al SM SiO O Fe IM O Al
(3)累加试凑法计算生料成分
(4)熟料的化学成分如下表:
9078
.08.235.0-65.1-2
3
232==SiO O Fe O Al CaO KH
7462
.232322
=+=O Fe O Al SIO SM IM=
547.13
23
2=O Fe O Al
所得结果符合要求,可按此配比生产,考虑到生产波动,可按KH=0.91,SM=2.70,IM=1.55。
可得干原料的配合比为:尾渣84.54%,砂岩13.49%,硫酸渣0.46%,粉煤灰1.51%。
(5)计算湿原料的配合比:
原料中的水分:尾渣:1% 砂岩:4% 硫酸渣:13% 粉煤灰:8% 则湿原料配合比为:
湿尾渣=84.54/(100-1)×100%=85.39% 湿砂岩=13.49/(100-4)×100%=14.05%
湿硫酸渣=0.46/(100-13)×100%=0.53% 湿粉煤灰=1.51/(100-8)×100%=1.64% 85.39%+14.05%+0.53%+1.64%=101.61% 将质量配比换算为百分比: 湿尾渣=85.39/101.61=84.04% 湿砂岩=14.05/101.61=13.83% 湿硫酸渣=0.53/101.61=0.52% 湿粉煤灰=1.64/101.61=1.61%
(6)计算熟料矿物组成:
C 3S=3.8SiO2(3KH -2)=3.8×22.603%×(3×0.9078-2)=62.13%
C2S=8.6SiO2(1-KH)=8.6X22.603%×(1-0.9078)=17.92%
C3A=2.65(Al2O3-0.64Fe2O3)=2.65×(4.9985%-0.64×3.2321%)=7.76%
C4AF=3.04×Fe2O3=3.04×3.2321%=9.83%
C3S+C2S=62.13%+17.92%=89.05%
C3A+C4AF=7.76%+9.83%=17.59%
液相量:1338℃L=6.1Fe2O3=6.1×3.2312%=19.72%
1450℃
L=3Al2O3+2.25Fe2O3+MgO+R2O=3×4.9985%+2.25×3.2321%+1.7364%+0=24.00%。