压铸模具设计详细标准
压铸模技术要求规笵
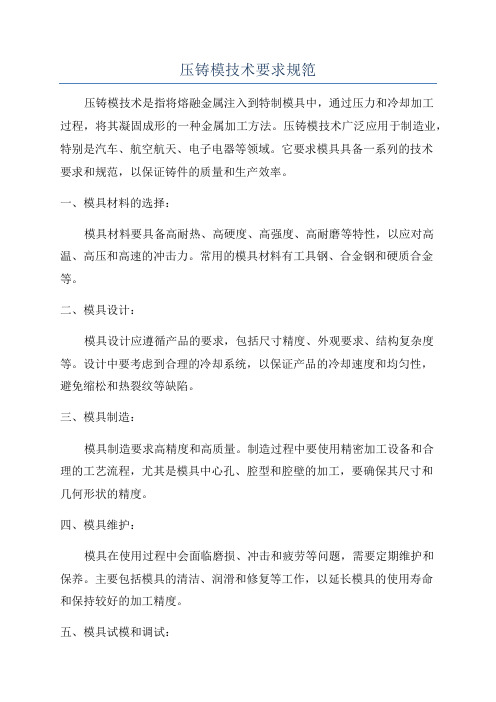
压铸模技术要求规笵压铸模技术是指将熔融金属注入到特制模具中,通过压力和冷却加工过程,将其凝固成形的一种金属加工方法。
压铸模技术广泛应用于制造业,特别是汽车、航空航天、电子电器等领域。
它要求模具具备一系列的技术要求和规范,以保证铸件的质量和生产效率。
一、模具材料的选择:模具材料要具备高耐热、高硬度、高强度、高耐磨等特性,以应对高温、高压和高速的冲击力。
常用的模具材料有工具钢、合金钢和硬质合金等。
二、模具设计:模具设计应遵循产品的要求,包括尺寸精度、外观要求、结构复杂度等。
设计中要考虑到合理的冷却系统,以保证产品的冷却速度和均匀性,避免缩松和热裂纹等缺陷。
三、模具制造:模具制造要求高精度和高质量。
制造过程中要使用精密加工设备和合理的工艺流程,尤其是模具中心孔、腔型和腔壁的加工,要确保其尺寸和几何形状的精度。
四、模具维护:模具在使用过程中会面临磨损、冲击和疲劳等问题,需要定期维护和保养。
主要包括模具的清洁、润滑和修复等工作,以延长模具的使用寿命和保持较好的加工精度。
五、模具试模和调试:模具制造完成后,需要进行试模和调试工作。
通过试模可以检验模具的结构和尺寸是否满足要求,是否有漏料、开裂等问题。
调试过程中需根据试模结果进行调整,以确保铸件的质量和尺寸精度。
六、模具应用:模具在使用中要对材料性能、温度、压力等参数进行合理控制,以避免过渡应力、热裂纹和变形等问题。
模具应用过程中,操作人员需要按照操作规程进行操作,并保持模具的清洁和正常维护。
七、模具质量管理:模具的质量管理是整个生产过程的重要环节。
要建立相应的质量管理体系,制定操作规程和质量标准,监控和控制每一个生产环节,确保产品的质量和生产效率。
总之,压铸模技术要求规范的模具材料选择、合理的模具设计、高精度的模具制造、定期的模具维护、严格的模具试模和调试工作、合理的模具应用和质量管理。
只有严格按照这些要求进行操作和管理,才能保证压铸模技术的高质量和高效率。
压铸模具技术标准及要求
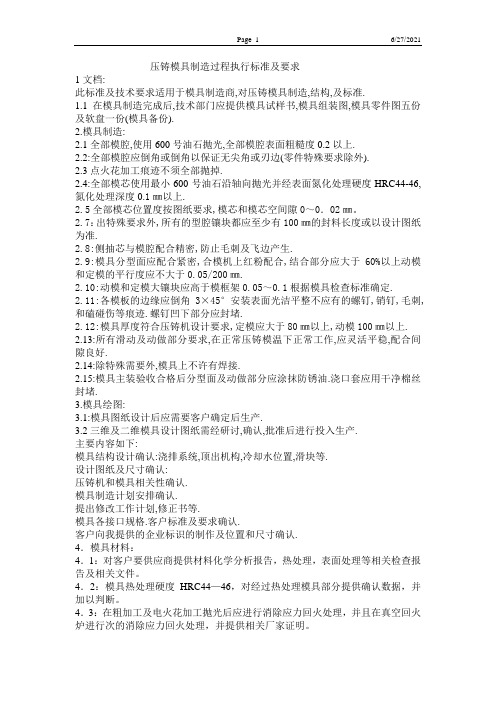
压铸模具制造过程执行标准及要求1文档:此标准及技术要求适用于模具制造商,对压铸模具制造,结构,及标准.1.1在模具制造完成后,技术部门应提供模具试样书,模具组装图,模具零件图五份及软盘一份(模具备份).2.模具制造:2.1全部模腔,使用600号油石抛光,全部模腔表面粗糙度0.2以上.2.2:全部模腔应倒角或倒角以保证无尖角或刃边(零件特殊要求除外).2.3点火花加工痕迹不须全部抛掉.2.4:全部模芯使用最小600号油石沿轴向抛光并经表面氮化处理硬度HRC44-46,氮化处理深度0.1㎜以上.2.5全部模芯位置度按图纸要求,模芯和模芯空间隙0~0.02㎜。
2.7:出特殊要求外,所有的型腔镶块都应至少有100㎜的封料长度或以设计图纸为准.2.8:侧抽芯与模腔配合精密,防止毛刺及飞边产生.2.9:模具分型面应配合紧密,合模机上红粉配合,结合部分应大于60%以上动模和定模的平行度应不大于0.05/200㎜.2.10:动模和定模大镶块应高于模框架0.05~0.1根据模具检查标准确定.2.11:各模板的边缘应倒角3×45°安装表面光洁平整不应有的螺钉,销钉,毛刺,和磕碰伤等痕迹.螺钉凹下部分应封堵.2.12:模具厚度符合压铸机设计要求,定模应大于80㎜以上,动模100㎜以上. 2.13:所有滑动及动做部分要求,在正常压铸模温下正常工作,应灵活平稳,配合间隙良好.2.14:除特殊需要外,模具上不许有焊接.2.15:模具主装验收合格后分型面及动做部分应涂抹防锈油.浇口套应用干净棉丝封堵.3.模具绘图:3.1:模具图纸设计后应需要客户确定后生产.3.2三维及二维模具设计图纸需经研讨,确认,批准后进行投入生产.主要内容如下:模具结构设计确认:浇排系统,顶出机构,冷却水位置,滑块等.设计图纸及尺寸确认:压铸机和模具相关性确认.模具制造计划安排确认.提出修改工作计划,修正书等.模具各接口规格.客户标准及要求确认.客户向我提供的企业标识的制作及位置和尺寸确认.4.模具材料:4.1:对客户要供应商提供材料化学分析报告,热处理,表面处理等相关检查报告及相关文件。
压铸模具设计规范
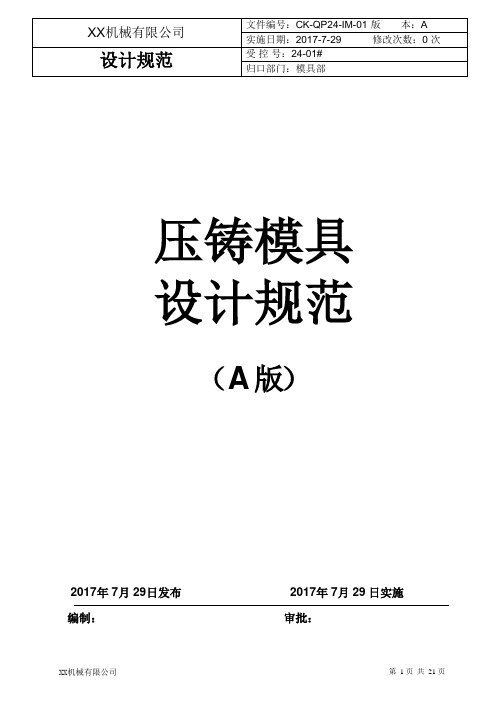
压铸模具设计规范(A 版)2017 年 7 月 29 日发布2017 年 7 月 29 日实施编制:审批:01. 目录一:模芯1.1模芯尺寸1.1.1模芯边距尺寸机型(T)160T 280T400T 500T-630T800T 1250T1600T三面(mm)55 60 70 80 100 120 140料筒面(mm)60 65 80 90 110 130 160 1.1.2模芯底面厚度尺寸机型(T)160T 280T400T500T-630T800T 1250T 1600T定模芯(mm)50 55 60 65 70 80 85动模芯(mm) 55 60 70 80 85 100 105敞开式滑块(mm)55 60 70 80 85 100 105 1.2模芯定位设计1.2.1模芯四角精定位斜度:动定模配合处单边 5°,与模框干涉处也要做斜度,单边 1.5°。
侧面转角圆角在 R8 以上。
定位的平面要避空 0.1mm,所有 R 角都要避空。
总高度最少 8mm。
1.2.2模芯周围一圈定位的斜度也做成 5°,平面不避空。
插入附件1.3,模芯冷却系统设计1.3.1:冷却水应设于流道附近、水管之间距保持 40mm-60mm,单独的孤岛处(凸起的)、大面积凹坑的侧边,产品最后凝固的厚壁处;1.3.2:环形冷却水的螺纹接口为 ZG1/4,冷却水管ø8-ø10mm,距离侧壁为 15mm 左右,距离顶面为 20~30mm,距离顶杆孔或销子孔至少 5mm;1.3.3:环形冷却水管经过的地方有高出平面的凸台或圆柱时应当采用隔水片的方式进行冷却,每一个环形最多允许有 6 个隔水片,隔水片孔与成型部位的距离参照点冷却;1.3.4:点冷却的水管直径为ø15.3mm-23mm 螺纹接口一般为 ZG3/8,距离侧壁为 15mm 左右,产品特殊厚壁可做到 6mm 左右,距离顶面为 15~25mm。
压铸模具标准
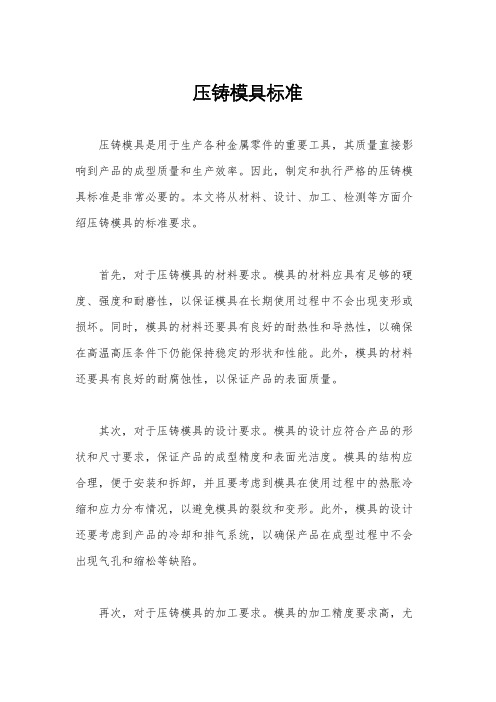
压铸模具标准压铸模具是用于生产各种金属零件的重要工具,其质量直接影响到产品的成型质量和生产效率。
因此,制定和执行严格的压铸模具标准是非常必要的。
本文将从材料、设计、加工、检测等方面介绍压铸模具的标准要求。
首先,对于压铸模具的材料要求。
模具的材料应具有足够的硬度、强度和耐磨性,以保证模具在长期使用过程中不会出现变形或损坏。
同时,模具的材料还要具有良好的耐热性和导热性,以确保在高温高压条件下仍能保持稳定的形状和性能。
此外,模具的材料还要具有良好的耐腐蚀性,以保证产品的表面质量。
其次,对于压铸模具的设计要求。
模具的设计应符合产品的形状和尺寸要求,保证产品的成型精度和表面光洁度。
模具的结构应合理,便于安装和拆卸,并且要考虑到模具在使用过程中的热胀冷缩和应力分布情况,以避免模具的裂纹和变形。
此外,模具的设计还要考虑到产品的冷却和排气系统,以确保产品在成型过程中不会出现气孔和缩松等缺陷。
再次,对于压铸模具的加工要求。
模具的加工精度要求高,尤其是对于模具的芯部和腔部,其加工精度和表面粗糙度都会直接影响到产品的质量。
因此,模具的加工过程需要采用先进的加工设备和工艺,以保证模具的尺寸和形状精度。
同时,模具的表面还需要进行表面处理,以提高其耐磨性和耐腐蚀性。
最后,对于压铸模具的检测要求。
模具在使用过程中需要进行定期的检测和维护,以确保其性能和精度。
模具的检测主要包括外观检查、尺寸检测、材料分析和磨损分析等内容,以发现模具的损坏和磨损情况,并及时进行修复和更换。
总之,严格执行压铸模具标准对于保证产品质量、提高生产效率和降低生产成本具有重要意义。
只有在材料、设计、加工和检测等方面都符合标准要求,才能保证模具在长期使用过程中保持稳定的性能和精度。
因此,压铸模具的标准化工作还需要在各个环节上加强,以逐步提高国内压铸模具的质量水平。
压铸件设计规范详解

压铸件设计规范详解压铸件是指利用压铸工艺将熔融金属注入模具中,经过凝固和冷却后得到的零件。
由于该工艺具有生产效率高、成本低、制造精度高等优点,被广泛应用于汽车、航空航天、电子等领域。
为了保证压铸件质量和安全性,需要遵循一系列的设计规范。
下面将详细介绍压铸件设计规范。
一、材料选择1.铝合金:常用的有A380、A383、A360等。
根据使用条件和要求,选择合适的铝合金材料,确保压铸件具有良好的强度和塑性。
2.压铸型腔材料:常用的有铜合金、热处理工具钢等。
要选择适当的材料,以耐高温和磨损。
二、模具设计1.模具设计必须满足压铸件的要求,保证铸件的尺寸精度和表面质量。
2.模腔设计要考虑到铸件收缩率、冷却速度等因素,以避免产生缺陷和变形。
3.合理安排模具冷却系统,保证压铸件内部和表面的冷却均匀。
三、尺寸设计1.压铸件的尺寸设计应符合产品技术要求和工艺要求,确保功能和安装的需要。
2.避免设计尺寸太小或太薄,以免产生破裂和变形。
3.设计保证良好的表面质量,避免设计中出现接触不良、挤压不足等问题。
四、壁厚设计1.壁厚不应过薄,以免影响产品的强度和刚性。
2.避免壁厚过大,以减少成本和缩短冷却时间。
3.边缘和角部应注意壁厚过渡,避免产生应力集中。
五、设计角度和半径1.设计时应根据铝合金的流动性选择合适的角度和半径。
2.避免设计尖锐角度和太小的半径,以免产生气孔和挤压不足。
3.设计角度和半径应保持一定的一致性,避免因设计不当导致铸件变形和收缩不均匀。
六、设计放射状构件1.当压铸件具有放射状构件时,要合理设计放射状梁的位置和数量,以充分利用材料,并减少成本。
2.注意放射状构件的设计不应影响整体结构的强度。
七、设计排气系统1.设计时要考虑到铸件内部的气孔、气泡等气体排出问题。
2.合理安排和设计排气道,以保证良好的注模效果和铸件质量。
八、设计孔和螺纹1.设计孔和螺纹时应遵循标准规范,确保质量和安装的可靠性。
2.孔和螺纹的位置和尺寸应符合产品要求,保证压铸件的功能和使用要求。
压铸模具标准
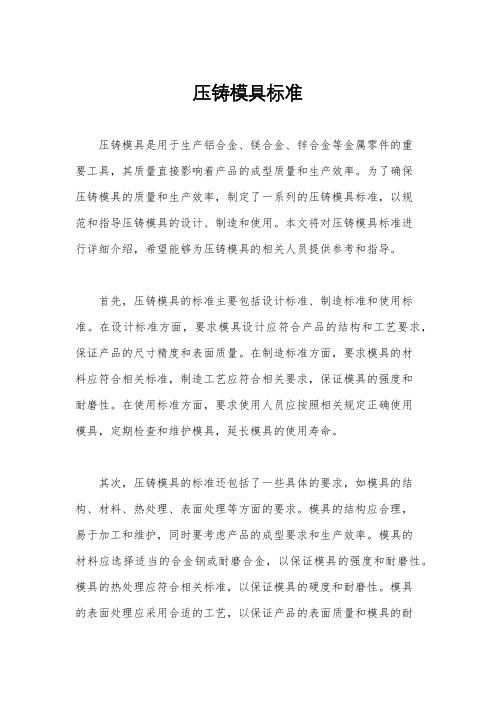
压铸模具标准压铸模具是用于生产铝合金、镁合金、锌合金等金属零件的重要工具,其质量直接影响着产品的成型质量和生产效率。
为了确保压铸模具的质量和生产效率,制定了一系列的压铸模具标准,以规范和指导压铸模具的设计、制造和使用。
本文将对压铸模具标准进行详细介绍,希望能够为压铸模具的相关人员提供参考和指导。
首先,压铸模具的标准主要包括设计标准、制造标准和使用标准。
在设计标准方面,要求模具设计应符合产品的结构和工艺要求,保证产品的尺寸精度和表面质量。
在制造标准方面,要求模具的材料应符合相关标准,制造工艺应符合相关要求,保证模具的强度和耐磨性。
在使用标准方面,要求使用人员应按照相关规定正确使用模具,定期检查和维护模具,延长模具的使用寿命。
其次,压铸模具的标准还包括了一些具体的要求,如模具的结构、材料、热处理、表面处理等方面的要求。
模具的结构应合理,易于加工和维护,同时要考虑产品的成型要求和生产效率。
模具的材料应选择适当的合金钢或耐磨合金,以保证模具的强度和耐磨性。
模具的热处理应符合相关标准,以保证模具的硬度和耐磨性。
模具的表面处理应采用合适的工艺,以保证产品的表面质量和模具的耐蚀性。
最后,压铸模具的标准还包括了一些检验和测试的要求,如模具的出厂检验、使用前检验、定期检验等。
模具的出厂检验应包括模具的尺寸检验、材料检验、热处理检验等,以保证模具的质量。
使用前检验应包括模具的装配检验、润滑检验、保养检验等,以保证模具的正常使用。
定期检验应包括模具的尺寸检验、磨损检验、裂纹检验等,以保证模具的使用寿命。
总之,压铸模具标准是保证压铸模具质量和生产效率的重要依据,对压铸模具的设计、制造和使用都有着重要的指导作用。
压铸模具的相关人员应严格按照相关标准执行,以保证产品质量和生产效率,推动压铸模具行业的健康发展。
希望本文所介绍的压铸模具标准能够为相关人员提供参考和指导,推动我国压铸模具行业的发展。
压铸模具的技术要求文档

压铸模具的技术要求文档压铸模具是现代工业生产中常用的一种模具,用于制造各种金属制品。
压铸模具的技术要求非常高,对模具的设计、制造、使用等方面都有相应的要求。
本文将从几个方面详细介绍压铸模具的技术要求。
一、设计要求1.模具结构设计要合理,要考虑到产品的结构特点、工艺要求等因素,并保证在模具使用中有较高的稳定性和精度。
2.模腔的设计要充分考虑充型性、冷却性、顶出性等要素,确保产品成型质量稳定。
3.模具的开口方式、进料方式等设计要符合产品要求,并能保证模具的安全操作。
二、材料要求1.模具材料应具有良好的刚性、韧性和耐磨性,能够承受较大的冲击负荷和高温环境,如工具钢、合金钢等。
2.模具的热处理要求良好,能够使模具硬度均匀、稳定,延长使用寿命。
三、制造要求1.模具加工要求高精度、高质量,要保证模具的尺寸精度和表面质量。
2.维修和保养要定期进行,及时处理模具的磨损、损伤等问题,确保模具的正常使用和寿命。
四、使用要求1.模具的操作人员要具备一定的技能和经验,严格按照操作规程进行操作,保证操作的安全和准确性。
2.模具的使用环境要保持清洁、干燥,避免灰尘、水汽等对模具的损坏。
3.模具的顶出装置、冷却装置等要保持良好的工作状态,及时进行维修和更换。
五、质量控制要求1.模具的尺寸精度、表面质量等要进行严格的检测和控制,保证产品的准确性和一致性。
2.定期对模具进行检测和维修,及时发现并解决模具的问题,防止因模具问题引起的产品质量问题。
总结:压铸模具的技术要求非常高,对模具的设计、制造、使用等方面都有严格要求。
只有合理的设计,良好的材料和制造工艺,正确的使用和维护,才能保证模具的高质量和长寿命,从而保证产品的质量和生产效率。
因此,在实际应用中,需要充分重视压铸模具的技术要求,综合考虑各方面因素,确保模具的高效稳定运行。
压铸模标准

压铸模具制造标准目录一、总体要求:1、按本公司的压铸机尺寸设计外形,防止干涉。
(88T~800T)见附表(1)。
2、吊装孔至少为M30深45的,顶部至少2个,大型模具800T-900T为M42深60mm,,动定模架上要各2个,需设于模具的重心上(每半模),以利于吊装时的安全。
3、模具码模槽,最小30 mm×30 mm(400T以下),40 mm×40 mm(400T以上),到型板高最小30 mm(400T以下),40 mm(400T以上)。
4、跨距大于150 mm时都应考虑加支撑。
支撑柱直径(或宽)不小于60 mm,尽可能靠近压射变形位。
5、为减小变形,动模架支撑模芯的厚度至少为悬空位宽度的三分之一(大于或等于80mm)。
定模架支撑模芯的厚度大于或等于70mm。
特殊指定除外。
6、分流锥和浇口套按本公司的标准设计。
浇口套与压铸机熔杯联接处尺寸ΦD,ΦD1,L2参照附表(1)。
下图为本公司普通压铸的标准化浇口套:10模具有形状相同或对称的镶件,抽芯等必须设计防呆结构,动定模芯不能设计为正方形。
11模具各部份的尺寸关系,如果没有特殊说明,按以下关系设计。
B1D2 D1FT2T1E1E2P2P1WABBA二、模芯:1、加工后热处理前做去应力处理。
真空淬火热处理硬度:500吨及以上模具为HRC46°-48°,500吨以下模具为HRC48°-50°。
平面分型的,型腔位不深的(例如:电烫斗等)可以做到50°-52°。
精加工后按模具工艺之具体规定再做去应力处理,2、省模和抛光按客户要求的粗糙度和模具出模方向执行。
3、型腔最小圆角R0.5,最小拔模斜度1.5°~2°。
特殊指定的除外。
4、多腔模模芯可以分为两块制造,以利于热处理。
制造配合间隙在0.1mm以内。
350T以下除外。
5、模芯上有镶件必须线割时,必须预先打穿丝孔,当跨距大于200mm时,穿丝孔要做2个。