典型零件的成形工艺-举例
冲压,压铸,模锻,低压铸造等26种常见金属成型工艺
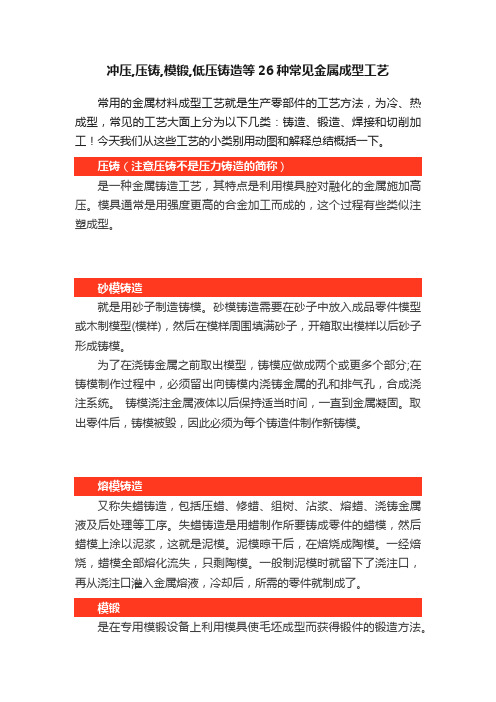
冲压,压铸,模锻,低压铸造等26种常见金属成型工艺常用的金属材料成型工艺就是生产零部件的工艺方法,为冷、热成型,常见的工艺大面上分为以下几类:铸造、锻造、焊接和切削加工!今天我们从这些工艺的小类别用动图和解释总结概括一下。
是一种金属铸造工艺,其特点是利用模具腔对融化的金属施加高压。
模具通常是用强度更高的合金加工而成的,这个过程有些类似注塑成型。
就是用砂子制造铸模。
砂模铸造需要在砂子中放入成品零件模型或木制模型(模样),然后在模样周围填满砂子,开箱取出模样以后砂子形成铸模。
为了在浇铸金属之前取出模型,铸模应做成两个或更多个部分;在铸模制作过程中,必须留出向铸模内浇铸金属的孔和排气孔,合成浇注系统。
铸模浇注金属液体以后保持适当时间,一直到金属凝固。
取出零件后,铸模被毁,因此必须为每个铸造件制作新铸模。
又称失蜡铸造,包括压蜡、修蜡、组树、沾浆、熔蜡、浇铸金属液及后处理等工序。
失蜡铸造是用蜡制作所要铸成零件的蜡模,然后蜡模上涂以泥浆,这就是泥模。
泥模晾干后,在焙烧成陶模。
一经焙烧,蜡模全部熔化流失,只剩陶模。
一般制泥模时就留下了浇注口,再从浇注口灌入金属熔液,冷却后,所需的零件就制成了。
是在专用模锻设备上利用模具使毛坯成型而获得锻件的锻造方法。
根据设备不同,模锻分为锤上模锻,曲柄压力机模锻,平锻机模锻,摩擦压力机模锻等。
辊锻是材料在一对反向旋转模具的作用下产生塑性变形得到所需锻件或锻坯的塑性成形工艺。
它是成形轧制(纵轧)的一种特殊形式。
是一种利用锻压机械对金属坯料施加压力,使其产生塑性变形以获得具有一定机械性能、一定形状和尺寸锻件的加工方法,锻压(锻造与冲压)的两大组成部分之一。
通过锻造能消除金属在冶炼过程中产生的铸态疏松等缺陷,优化微观组织结构,同时由于保存了完整的金属流线,锻件的机械性能一般优于同样材料的铸件。
相关机械中负载高、工作条件严峻的重要零件,除形状较简单的可用轧制的板材、型材或焊接件外,多采用锻件。
模具成型零件制造工艺及实例分析

第9卷第5期2009年10月湖南工业职业技术学院学报J OURNAL OF HUNAN I NDUSTRY POLYTECHN I CV ol 9N o 5O ct 2009模具成型零件制造工艺及实例分析胡彦辉 程 莉(湖南工业职业技术学院,湖南长沙 410208)[摘 要] 根据模具成型零件制造工艺要求,着重分析了模具成型零件的制造工艺性及加工方法,以典型模具成型零件为实例,确定加工工艺路线,编制零件的制造工艺过程及实施步骤。
[关键词] 模具;成型零件;制造工艺;实例分析[中图分类号] TH 162 9[文章标识码] A[文章编号] 1671-5004(2009)05-0004-02M ol d PartM anufacturi ng D esire and Exa m ple Anal ysisHU Yan-hu,i C H E NG L i(H unan Indu stry Pol ytech ic ,C hangs ha 410208,H unan)[Ab stract] Accordi ng to m ol d partm anu f act u ri ng techn i cs require ,analys is m ol d part m anufacturi ng m anu fact u rab ilit y and m ach i n i ng m ethod ,ensurem ach i n i ng w ays ,m ak i ng partm anu f act u ri ng technics process and i m ple m ent steps[K ey word s] mo l d ;m olding part ;m anufact u ri ng techn i cs ;examp le anal ys i s[收稿日期] 2009-08-25[作者简介] 胡彦辉(1964-),男,湖南湘阴人,湖南工业职业技术学院机械工程系副教授,工学学士,主要从事模具设计与制造专业方向的研究。
独领风骚的金属加工工艺以及金属成型工艺大盘点

独领风骚的金属加工工艺以及金属成型工艺大盘点金属加工工艺一、金属注射成型(MIM)1.简介金属注射成型(Metal Injection Molding,MIM)是一种适于生产小型、三维复杂形状以及具有特殊性能要求制品的近净成形工艺。
该技术是将现代塑料注射成形技术引入粉末冶金领域而形成的一门新型粉末冶金近净形成形技术。
2.工艺流程将各种微细金属粉末(一般小于20μm)按一定的比例与预设粘结剂,制成具有流变特性的喂料,通过注射机注入模具型腔成型出零件毛坯,毛坯件经过脱除粘结剂和高温烧结后,即可得到各种金属零部件。
MIM流程结合了注塑成型设计的灵活性和精密金属的高强度和整体性,来实现极度复杂几何部件的低成本解决方案。
(MIM工艺流程示意图)3.适用材料及典型结合剂(MIM适用材料)(MIM典型结合剂)4.金属注射成形(MIM)应用范围MIM具有常规粉末冶金、机加工和精密铸造方法无法比拟的优势,最突出优点为:● 适合各种粉末材料的成形,产品应用十分广泛;● 能直接成形几何形状复杂的小型零件(0.03g~200g);● 零件尺寸精度高(±0.1%~±0.5%),表面光洁度好(粗糙度1~5μm);● 产品相对密度高(95~100%),组织均匀,性能优异;● 原材料利用率高,生产自动化程度高,适合连续大批量生产。
因此在轻武器、手表、电子仪器、牙齿矫正支架、汽车发动机零件、电子密封、切削工具及运动器材中得到大量应用。
二、纳米注塑成型技术(NMT)1.简介金属与塑料以纳米技术结合的工艺称为纳米注塑成型技术(NMT)。
先对金属表面进行纳米化处理,再将塑料注射在在金属表面,可将镁、不锈钢、钛等金属与硬质树脂结合,实现一体化成型。
2.NMT工艺流程3.适用材料(铝材和铝材的结合)金属基材:铝及其合金:1000-7000系列(5052、6061、6063、7072、7075)铜及其合金:CAC16、C110、C5191、C1020、KFC5、KLF194 镁及其合金:AZ-31B、AZ-91D钛及其合金:KSTI、KS40不锈钢:SUS-304、SUS-316、316L及其他铁系列合金(MIM304L)(结合样件形式)塑料基材:PPS:宝理PPS5120(白)/PPS 1135(黑)/ PPS F458A(黑)东漕BGX120(黑)/BGX140(黑)/BGX545(黑)PBTPA(Nylon尼龙):黑色(包括PA6、PA66)PPA:多种颜色4.应用范围NMT产品可拓展到很广阔的领域,包括各类3C电子产品外壳及汽车零部件等。
弯曲成形工艺

1、影响回弹量的因素
材料力学性能 屈服强度愈高,弹性模 量愈小,加工硬化愈严重,则回弹量也 愈大。 相对弯曲半径r/t 相对弯曲半径r/t 越小, 回弹值越小。
曲率回弹:
ΔK = 1 ρ0 1 ρ0 '
角度回弹: Δα = α α 0
《汽车结构及制造技术》
弯曲中心角α 弯曲中心角α越大,弯曲后回弹角Δα越大。 曲件形状 形状愈复杂,由于各部分相互牵制,回弹困难。 模具间隙 弯曲模具的间隙愈大,回弹也愈大,所以板料厚度 允差愈大,回弹值愈不稳定。 模具圆角半径和摩擦等都对弯曲件回弹量有影响。
应力:材料或构件在单位截面上所承受的垂直作用力 应变:在外力作用下,单位长度材料的伸长量或缩短量,称为应变量 在一定的应力范围(弹性形变)内,材料的应力与应变量成正比,它们的比例常数称为弹性模量
《汽车结构及制造技术》
6.2 弯曲件质量分析与工艺设计
6.2.1 弯曲件的回弹
卸载后弯曲件曲率和角度发生变化的 现象,称为弯曲回弹(简称回弹)。 弯曲回弹表现为弯曲半径和弯曲中心角的 变化。 • 弯曲回弹是不可避免的。
图 6-14
板料纤维方向对弯曲半径的影响
《汽车结构及制造技术》
3. 最小相对弯曲半径经验数值的确定
《汽车结构及制造技术》
6.2.3 弯曲中的偏移及防止措施
坯料在弯曲过程中沿制件的长度方向产生移动,使制件两 边的高度不符合图样要求的现象。
《汽车结构及制造技术》
采用压料装置,使坯料 在压紧的状态下逐渐弯 曲成形,从而防止坯料 的滑动,而且能得到较 平整的制件。
《汽车结构及制造技术》
总结提高
学生归纳
1
弯曲变形过程 弯曲变形特点
2
影响回弹的因素 减小回弹的措施
典型RP第2章 光固化快速成型(SLA)工艺PPT课件

2-1 光固化快速成型工艺的基本原理和特点
❖ 2.1 光固化成型的基本原理
图2-1 光固化快速成型工艺原理
液槽中盛满液态光敏树脂,氦-镉激 光器或氩离子激光器发出的紫外激光 束在控制系统的控制下按零件的各分 层截面信息在光敏树脂表面进行逐点 扫描,使被扫描区域的树脂薄层产生 光聚合反应而固化,形成零件的一个 薄层。一层固化完毕后,工作台下移 一个层厚的距离,以使在原先固化好 的树脂表面再敷上一层新的液态树脂, 刮板将粘度较大的树脂液面刮平,然 后进行下一层的扫描加工,新固化的 一层牢固地粘结在前一层上,如此重 复直至整个零件制造完毕,得到一个 三维实体原型。
4
2-1 光固化快速成型工艺的基本原理和特点
图2-2 光固化成型制造过程中残留的多余树脂
因为树脂材料的高粘性,在每层固化之后,液面很难在短时间内 迅速流平,这将会影响实体的精度。采用刮板刮切后,所需数量 的树脂便会被十分均匀地凃敷在上一叠层上,这样经过激光固化 后可以得到较好的精度,使产品表面更加光滑和平整。
12
2-2 光固化快速成型材料及设备
(3)混杂型光固化树脂
目前的趋势是使用混杂型光固化树脂。其优点主要有: 1)环状聚合物进行阳离子开环聚合时,体积收缩很小甚至
产生膨胀,而自由基体系总有明显的收缩。混杂型体系可以设计 成无收缩的聚合物。
2)当系统中有碱性杂质时,阳离子聚合的诱导期较长,而 自由基聚合的诱导期较短,混杂型体系可以提供诱导期短而聚合 速度稳定的聚合系统。
20
2-2 光固化快速成型材料及设备
21
2-2 光固化快速成型材料及设备
(4)DSM公司的SOMOS系列
DSM公司的SOMOS系列环氧树脂主要是面向光固化快速成型开发的系列材料, 部分型号的性能及主要指标如下表所示。
汽车内饰件的搪塑成型工艺-精

汽车内饰件的搪塑成型工艺面对竞争日益激烈的汽车市场和对产品质量要求越来越高的汽车用户,各大汽车制造商日益关注相关零部件的制造工艺技术,汽车内饰成型工艺备受关注。
汽车仪表板与门内饰板是汽车内饰的重要组成部分,是汽车内饰产品新工艺、新技术发展的具体体现。
目前汽车仪表板、门内饰板表皮的制造工艺类型有很多,其中搪塑发泡模的居多。
搪塑工艺主要优点表皮纹理清晰均匀,产品设计时不用考虑脱模角度,设计自由度大。
下面给大家具体介绍下搪塑模具及产品的相关要点;一、搪塑模具成型工艺:根据数模,加上收缩率,减去皮纹层的厚度,数控加工出木模→在木模上贴上皮纹皮(贴皮引起模具上有拼缝)→翻出软的硅树脂模(有拼缝)→翻出硬的树脂主模型,并手工修掉拼缝→翻出硅树脂模→翻出电极阳模(为了导电,表面喷银粉,并布置电极)→电镀出搪塑模具外壳→加上支撑,形成搪塑模。
数控加工木模包皮纹皮浇注硅胶脱模环氧树脂脱模电极阳模电镀出镍壳去除环氧树脂+精加工镍壳装于支架二、搪塑模具的结构搪塑模具一般由框架、镍盒、过渡盒、粉盒组成。
图示如下:三、搪塑表皮的成型工艺搪塑表皮成型的工艺流程如下图所示:1.首先将搪塑模具本体加热至230-250℃;2.然后将模具与粉箱对合并夹紧(以防粉末露出),模具在上,粉箱在下;3.模具和粉箱一起旋转至粉箱在上,模具在下,粉箱里的粉末这时落在模具里,在高温的作用下,紧贴在模具的那一层就融化并相互粘在一起,然后继续旋转,使得模具的每个角落都有粉末,且融化并粘在一起,直至形成的表皮厚度增加至符合要求为止(一般的PVC的厚度为1。
1mm),这时粉箱在下方,剩余的粉末又回到粉箱里;4.模具与粉箱分离,并移到冷却工位,用水或空气等对模具进行快速冷却至60-80℃时,人工扒下表皮。
四、搪塑设备的分类(按模具的加热方式分类)1、气加热设备:价格最便宜。
它是通过燃烧天然气或重油产生的热风来加热模具。
它有一个加热炉,整个模具置于炉子中加热。
典型零件的机械加工工艺实例分析

第4章典型零件的机械加工工艺分析本章要点本章介绍典型零件的机械加工工艺规程制订过程及分析,主要内容如下:1.介绍机械加工工艺规程制订的原则与步骤。
2.以轴类、箱体类、拨动杆零件为例,分析零件机械加工工艺规程制订的全过程。
本章要求:通过典型零件机械加工工艺规程制订的分析,能够掌握机械加工工艺规程制订的原则和方法,能制订给定零件的机械加工工艺规程。
§4.1 机械加工工艺规程的制订原则与步骤§4.1.1机械加工工艺规程的制订原则机械加工工艺规程的制订原则是优质、高产、低成本,即在保证产品质量前提下,能尽量提高劳动生产率和降低成本。
在制订工艺规程时应注意以下问题:1.技术上的先进性在制订机械加工工艺规程时,应在充分利用本企业现有生产条件的基础上,尽可能采用国内、外先进工艺技术和经验,并保证良好的劳动条件。
2.经济上的合理性在规定的生产纲领和生产批量下,可能会出现几种能保证零件技术要求的工艺方案,此时应通过核算或相互对比,一般要求工艺成本最低。
充分利用现有生产条件,少花钱、多办事。
3.有良好的劳动条件在制订工艺方案上要注意采取机械化或自动化的措施,尽量减轻工人的劳动强度,保障生产安全、创造良好、文明的劳动条件。
由于工艺规程是直接指导生产和操作的重要技术文件,所以工艺规程还应正确、完整、统一和清晰。
所用术语、符号、计量单位、编号都要符合相应标准。
必须可靠地保证零件图上技术要求的实现。
在制订机械加工工艺规程时,如果发现零件图某一技术要求规定得不适当,只能向有关部门提出建议,不得擅自修改零件图或不按零件图去做。
§4.1.2 制订机械加工工艺规程的内容和步骤1.计算零件年生产纲领,确定生产类型。
2.对零件进行工艺分析在对零件的加工工艺规程进行制订之前,应首先对零件进行工艺分析。
其主要内容包括:(1)分析零件的作用及零件图上的技术要求。
(2)分析零件主要加工表面的尺寸、形状及位置精度、表面粗糙度以及设计基准等;(3)分析零件的材质、热处理及机械加工的工艺性。
模具典型零件的加工工艺

镗孔工序可以在专用镗床、坐标镗床、 双轴镗床上进行,为了保证上、下模座的 导柱、导套孔距一致,在镗孔时可以将上、 下模座重叠在一起,一次装夹,同时镗出 导柱、导套的安装孔。
2.导柱、导套的加工
(1)导柱、导套的技术要求 1)为了保证良好的导向作用,导柱和 导套的配合间隙应小于凸、凹模之间的间 隙,导柱和导套的配合间隙一般采用H7/h6, 精度要求很高时为H6/h5。导柱与下模座孔, 导套与上模座孔采用H7/r6的过盈配合。
2)导柱和导套的工作部分的圆度公差 应满足: 当直径d≤30mm时,圆度公差不大于 0.003mm;当直径d>30~60mm时,圆度公 差不大于0.005mm;当直径d≥60mm时,圆 度公差不大于0.008mm。
(2)导柱和导套的加工工艺路线 1)导柱的加工工艺路线 对于图4-3(a)所示的导柱,采用如 表4-4所示的加工工艺路线。 导柱的心部要求韧性好,材料一般选用20 号低碳钢。 在导柱加工过程中,外圆柱面的车削 和磨削以两端的中心孔定位,使设计基准 与工艺基准重合。
(3)电火花线切割加工 如图4-21所示的凸模的电火花线切割工 艺过程如下: 1)准备毛坯,将圆形棒料锻造成六面体, 并进行退火处理。 2)在刨床或铣床上加工六面体的六个面。 3)钻穿丝孔。 4)钻孔、攻螺纹,加工出固定凸模用的两 个螺钉孔。
5)将工件进行淬火、回火处理,要求 表面硬度达到HRC 58~HRC 62。 6)磨削上、下两平面,表面粗糙度Ra <0.8μ m 。 7)去除穿丝孔内杂质,并进行退磁处 理。 8)线切割加工凸模。 9)研磨。线切割加工后,钳工研磨凸 模工作部分,使工作表面粗糙度降低。
第4章 模具典型零件的加工工艺
4.1
模架的加工
冲裁凸模和凹模的加工 塑料模型腔的加工
- 1、下载文档前请自行甄别文档内容的完整性,平台不提供额外的编辑、内容补充、找答案等附加服务。
- 2、"仅部分预览"的文档,不可在线预览部分如存在完整性等问题,可反馈申请退款(可完整预览的文档不适用该条件!)。
- 3、如文档侵犯您的权益,请联系客服反馈,我们会尽快为您处理(人工客服工作时间:9:00-18:30)。
选择成形工艺方法思考题
1.选材 2.选择成形方法
生产要求: 1.100件/8小时 2.生产1000件 3.20天交货 摩托车汽缸头
加工途径选项: 1.毛坯件:钢棒料(6米长的棒料经切割获得)、 机加工所有孔及各表面; 2.采用砂型铸造(用铸钢材料),在经机加工 完成; 3.采用砂型铸造(用铸铁材料),在经机加工 完成; 4.铸铁熔模铸造 5.青铜金属型铸造 6.青铜压铸,免机加工 问:你认为采用何种方法最合适、最经济,并 能按时交货?为什么?
(1)损伤失效的主要形式有2种:疲劳断裂和 轴颈严重磨损。 性能要求:高强度;一定的冲击韧度;足够的 抗弯、扭转、疲劳强度;足够的刚度;轴径表 面有高的硬度和耐磨性。
(2)汽车曲轴的生产工艺路线: 下料→模锻→调质→切削加工→轴颈表面淬火。 调质:做好组织准备,工件整个截面获得综合 机械性能。 表面淬火:提高表面硬度。
毛坯以锻钢件或圆钢件为主
2. 盘类零件 盘类零件轴向(纵向)尺寸一般小于其径向(横向) 尺寸,如齿轮、皮带轮、法兰盘、联轴器,轴 承以及螺母、垫圈等。
盘类零件
①齿轮毛坯多采用钢材锻造生产,一些较小的 齿轮也可采用圆钢为毛坯。 大型齿轮,其整体锻造困难,可以采用镶拼 的方法组合。 对于要求不高的大齿轮也可以采用球墨铸铁 整体铸造毛坯。 较小的齿轮,如仪器仪表内的小齿轮,可以 采用冲压、挤压成形,也可以用注射成型的 塑料齿轮代替金属齿轮。
(1)阐述汽车齿轮的损伤失效的主要形 式,对其性能有何要求? (2)写出汽车齿轮的生产工艺路线(含 机加工及热处理工艺),并写出所采用的 热处理工艺的目的。
(1)损伤失效的主要形式
(1)损伤失效的主要形式有3种:断齿、破坏 性胶合和破坏性点蚀。
(1)损伤失效的主要形式有3种:断齿、破坏 性胶合和破坏性点蚀。 性能要求:
一.常用机械零件 1. 轴杆类零件
轴、杆类零件其形状特点是轴向(纵向)尺寸远大于 径向(横向)尺寸。 轴、杆类零件有不同的使用功能,如传动轴、机 床主轴、齿轮轴、曲轴、丝杠、连杆、拨叉、摇 臂及螺栓、销钉等。
轴杆类零件
凸轮轴
连杆
螺栓
轴、杆类零件在机械设备中多数为重要的受 力和传动零件,材料多数采用钢,毛坯以锻 钢件或圆钢件为主。 对较小、形状复杂的曲轴、凸轮轴也可以采 用球墨铸铁铸造毛坯。 在一些特殊情况下,还可以采用锻造—焊接、 铸造—焊接的方法生产形状特殊或尺寸较大 的轴、杆类毛坯。
机架、箱体类零件
机身、底座、支架、横梁零件: 特点:结构复杂,有不规则的外形与内腔; 作用:起支承和连接各部分机械零件的作用; 工作时受力:压力、冲击力; 要求:很好的稳定性、刚性和减振性。 工作台、导轨零件要求有较好的耐磨性。 齿轮箱、缸体、泵体则要求有良好的刚度和密封性。
曲轴是汽车发动机上重要的部件之一,其工作 可靠性和寿命在很大程度上决定了发动机的可 靠性与寿命,曲轴材料可选用40Cr钢,为提高 其性能,在机加工过程中通常穿插着要对其进 行热处理。
(1)阐述汽车曲轴的损伤失效的主要形式, 对其性能有何要求? (2)写出汽车曲轴的生产工艺路线(含机加 工及热处理工艺),并写出所采用的热处理工 艺的目的。
减速器箱体
齿 条
轧 辊
锁紧轴 磨辊
凸轮轴
某镗床镗杆选用38CrMoAlA制造;其制 造工艺路线: 备料 调质 磨 锻造 退火 粗加工 精加工 时效处理 粗 氮化 精磨、研磨
镗床镗杆
试从机械性能和成分角度来说明选择此钢 材的优越性和各热处理工序的作用。
减速器箱体:
毛坯件:
材料的选择:
钢材: 铸铁 铝合金
性能要求: 要求齿轮的整体具有高的弯曲疲劳强度, 心部要求高的强度和冲击韧性, 齿面要求高硬度、高耐磨性和一定的耐腐蚀性。
(2)汽车齿轮的生产工艺路线:
(2)汽车齿轮的生产工艺路线: 下料+锻造+正火+切削加工+渗碳、淬火、低温 回火+磨削加工。 正火:细化晶粒,做好组织准备。 渗碳、淬火、低温回火:提高表面硬度。
螺母
②皮带轮、飞轮、手轮等盘类零件,工作时受 力较小,强度要求不高,通常采用灰铸铁材 料铸造毛坯。
灰铸铁材料 铸造毛坯。
皮带轮
③法兰盘、联轴器、套环、轴承等盘类零件, 可以采用的毛坯材料有铸铁、碳钢、合金钢、 有色金属、粉末冶金及塑料,其成形方法应 根据具体情况确定。
法兰盘
3. 机架、箱体类零件 机架、箱体类零件包括各种机械的机身、底座、支 架、横梁、工作台以及齿轮箱、缸体、泵体、轴承 座等。
机架、箱体类零件最常用的材料为铸铁,采用铸造 成形毛坯。 对于受力较大的机身可以采用铸钢或钢板焊接成形。 对于受力不大的缸体、泵体也可以采用铝合金铸造 成形。
水泵
齿轮箱
摩托车发动工方法: 铸造、锻造,、 板料切割
齿轮是汽车发动机上重要的部件之一,其工作可靠性 和寿命在很大程度上决定了发动机的可靠性与寿命, 齿轮材料可选用20CrMnTi钢,为提高其性能,在机加 工过程中通常穿插着要对其进行热处理。