催化裂化联合装置工程建设特点、难点
加氢裂化和制氢装置开工重点难点分析及对策
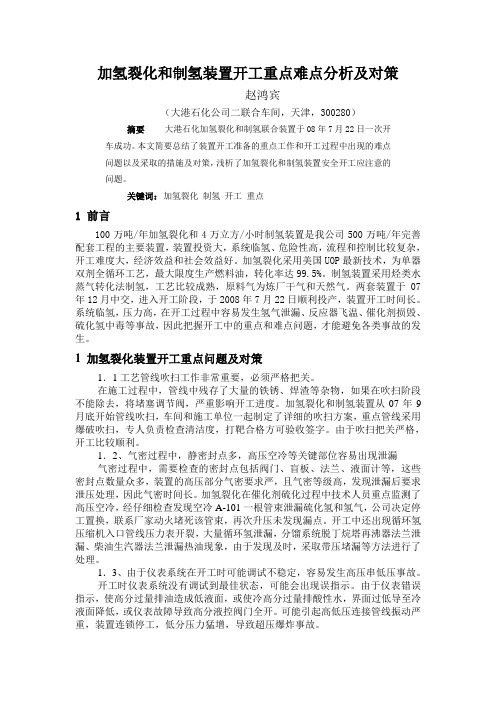
加氢裂化和制氢装置开工重点难点分析及对策赵鸿宾(大港石化公司二联合车间,天津,300280)摘要大港石化加氢裂化和制氢联合装置于08年7月22日一次开车成功。
本文简要总结了装置开工准备的重点工作和开工过程中出现的难点问题以及采取的措施及对策,浅析了加氢裂化和制氢装置安全开工应注意的问题。
关键词:加氢裂化制氢开工重点1 前言100万吨/年加氢裂化和4万立方/小时制氢装置是我公司500万吨/年完善配套工程的主要装置,装置投资大,系统临氢、危险性高,流程和控制比较复杂,开工难度大,经济效益和社会效益好。
加氢裂化采用美国UOP最新技术,为单器双剂全循环工艺,最大限度生产燃料油,转化率达99.5%。
制氢装置采用烃类水蒸气转化法制氢,工艺比较成熟,原料气为炼厂干气和天然气。
两套装置于07年12月中交,进入开工阶段,于2008年7月22日顺利投产,装置开工时间长。
系统临氢,压力高,在开工过程中容易发生氢气泄漏、反应器飞温、催化剂损毁、硫化氢中毒等事故,因此把握开工中的重点和难点问题,才能避免各类事故的发生。
1 加氢裂化装置开工重点问题及对策1.1工艺管线吹扫工作非常重要,必须严格把关。
在施工过程中,管线中残存了大量的铁锈、焊渣等杂物,如果在吹扫阶段不能除去,将堵塞调节阀,严重影响开工进度。
加氢裂化和制氢装置从07年9月底开始管线吹扫,车间和施工单位一起制定了详细的吹扫方案,重点管线采用爆破吹扫,专人负责检查清洁度,打靶合格方可验收签字。
由于吹扫把关严格,开工比较顺利。
1.2、气密过程中,静密封点多,高压空冷等关键部位容易出现泄漏气密过程中,需要检查的密封点包括阀门、盲板、法兰、液面计等,这些密封点数量众多,装置的高压部分气密要求严,且气密等级高,发现泄漏后要求泄压处理,因此气密时间长。
加氢裂化在催化剂硫化过程中技术人员重点监测了高压空冷,经仔细检查发现空冷A-101一根管束泄漏硫化氢和氢气,公司决定停工置换,联系厂家动火堵死该管束,再次升压未发现漏点。
催化裂化装置产汽系统及余热锅炉技术特点概述

催化裂化装置产汽系统及余热锅炉技术特点概述催化裂化是一种重要的炼油工艺,通过将重质石油馏分裂解成较轻的产品,如汽油和柴油等,以满足市场需求。
在催化裂化装置中,产汽系统及余热锅炉是其重要组成部分,其技术特点对于提高催化裂化装置的生产效率和能源利用率至关重要。
本文将对催化裂化装置产汽系统及余热锅炉的技术特点进行概述,以期为相关行业提供参考。
一、催化裂化装置产汽系统的技术特点1. 多级产汽系统设计催化裂化装置中的多级产汽系统是为了最大限度地利用热能,提高能源利用效率。
通常采用的是高温高压的产汽方式,将裂化反应过程中产生的热能转化为高温高压的蒸汽,用于提供装置运行所需的动力和热能。
多级产汽系统能够有效地增加蒸汽的压力和温度,提高其能量利用率,从而降低了生产成本,提高了装置的经济效益。
2. 蒸汽余热回收催化裂化装置中,裂化反应过程会产生大量的余热,这些余热如果不能得到合理的利用将会造成能源的浪费。
对于产汽系统而言,余热回收是其重要的技术特点之一。
通过余热锅炉将裂化反应产生的余热进行回收利用,将余热转化为蒸汽,从而进一步提高了热能的利用率,降低了能源消耗,减少了环境污染。
3. 自动控制与安全保护产汽系统作为催化裂化装置的重要组成部分,其自动控制与安全保护技术是至关重要的。
通过自动控制系统对产汽系统的运行参数进行实时监控和调节,确保系统的稳定运行和高效工作。
配备完善的安全保护系统,对于产汽系统的各个部分进行全方位的监测和保护,有效预防了可能发生的事故和故障,保障了装置的安全运行。
二、余热锅炉的技术特点1. 高效换热余热锅炉是一种利用余热进行能量回收的设备,其技术特点之一是高效换热。
通过采用先进的换热器件和换热技术,余热锅炉能够将裂化反应产生的余热充分利用,实现热能的高效转化。
2. 多种余热回收方式余热锅炉的技术特点还体现在其多种余热回收方式上。
根据裂化装置产生的余热特点和需要利用的热能形式,余热锅炉可以采用不同的回收方式,如蒸汽余热回收、热油余热回收、热水余热回收等,以实现余热的高效回收利用。
催化裂化装置关键设备故障分析及对策

催化裂化装置关键设备故障分析及对策天津 300270摘要:催化裂化装置是石油加工工艺中的重要环节之一,同时也是炼油厂中最需要注重安全的场所之一。
在催化裂化装置运行过程中,可能会出现一些故障,这不仅会影响设备的性能和生产质量,还可能会对人员的生命财产造成威胁。
因此,下文将对催化裂化装置的关键设备故障进行详细的介绍和分析,以期提高我们对催化裂化装置的故障了解和维护能力。
关键词:催化裂化装置;关键设备;故障分析;对策;引言:催化裂化装置在石油加工工艺中占据着重要的地位,是炼油厂的关键设备之一。
然而,在其长期运行的过程中,可能会出现各种各样的故障,如催化剂失活、热点堵塞、噪声故障、泄漏故障等,这些故障都会对设备的性能和生产质量产生严重影响,甚至危及人员生命财产安全。
针对这些可能出现的故障,我们需要深入探究其原因和对策,及时制定应对方案。
例如,对于催化剂失活故障,需要重视对催化剂的清洗及维护;对于热点堵塞故障,需要定期对反应器进行清洗,保证设备的正常运行;对于噪声故障,需要加强设备的维护保养和调整;对于泄漏故障,需要进行紧急处理和加强安全防范措施等等。
在日益严格的环保和安全要求下,催化裂化装置的关键设备故障处理显得愈发重要,需要我们对其进行深入探究和分析,从而找到有效的对策方案,保障设备的正常运行,提高生产效率和产品质量。
本文将对催化裂化装置关键设备故障进行详细论述和分析,并提出一系列的对策希望能为行业发展做出一点贡献。
一、催化裂化装置简介催化裂化装置是一种高度技术化的炼油装置,用于将石油或石油产品中的高分子化合物裂解成较小的分子。
它采用一系列反应器、加热器、冷却器、催化剂等设备,通过改变化学反应条件,实现高分子化合物分解与分解产物再结合的反应过程。
在催化裂化装置中,原料石油或石油产品经过预热后,进入到第一反应器中,在高温(600℃-700℃)、低压(0.2-0.3MPa)的反应条件下,遇到催化剂开始反应。
重点难点-重油催化裂化

催化装置重点、难点两器重点、难点1.再生器为整体热处理,危险性高施工难度大,热处理方法为燃油法,主要控制燃烧的稳定性及燃烧温度。
2.反应器为局部热处理热处理方法为电加热法。
热处理过程中要控制好升温及降温的速度,并要有详细的记录。
3.提升管龟甲网材质为0Cr18Ni9焊接难度大,焊接后不能有松动、漏焊等缺陷,衬里施工要求严格,施工难度大,施工时要控制好压实,外观不能有裂纹等缺陷。
4.两器几何尺寸大,焊接预热难度大、吊装难度大组焊焊缝多,焊接任务量大,环形挡板、人字挡板衬里施工难度大,安装时要求压实,衬里的安装不能有贯通缝及裂纹,安装精度高。
5.两器衬里整体烘炉难度要求高,施工难度大。
6.内部旋风分离系统的安装精度要求严格,又为现场吊装施工,所以安装精度控制难度大,要时刻保证旋风分离系统的安装精度。
7.两器几何尺寸过大,要求分段吊装,对对口错边量控制难度大。
8.高空焊接时,由于现场风沙较大,对焊接影响亦较大,要控制高空焊接作业的焊接质量。
9.安装标高高,安全作业难度大。
C-201分馏塔的重点难点1.分馏塔材质为复合板,焊接要求高,施工难度大,在施工作业中严格控制焊条的使用情况。
2.安装标高高8000mm,整体高度高53050mm 吊装难度大。
分段吊装时,对口错边量控制难度大。
3.由于为分段吊装,塔体垂直度及其他安装精度控制难度大。
4.由于受限空间作业,不方便施工,所以塔内件安装精度控制难度大。
D-202/203燃料油缓冲罐/回炼油中间罐1.共计15带板,4个封头。
由于整体过高,高空分段吊装时对口错边量控制难度大。
安装尺寸控制难度大。
受现场风沙影响,焊接质量的控制难度大,要做好现场的防风措施。
D-101~103冷、热、废催化剂罐1.均为8带板,2个封头。
组焊焊缝多,焊接量大,热处理难度大。
由于为分段吊装,高空组对,受现场风沙影响,焊接质量的控制难度大,要做好现场的防风措施。
D-301气压机出口油气分离器1.材质为复合板,施焊难度大,整体规格大,组焊焊缝多,焊接量大,热处理难度大。
催化裂化装置解读

催化裂化装置催化裂化是炼油工业重要的二次加工装置,是提高轻质油收率,生产高辛烷值汽油,同时又多产柴油的重要手段,随着重油催化工艺的实现,其地位更加倍增。
作为一项传统的重油加工工艺,催化裂化实现工业化已经有60年的历史,其总加工能力超过加氢裂化、焦化和减粘裂化之和,是目前最重要的重油轻质化工艺。
虽然曾多次受到加氢裂化工艺的竞争和清洁燃料标准的挑战,但由于催化裂化技术的进步,各种以催化裂化技术为核心的催化裂化“家族工艺”的不断出现,已经将催化裂化转变为“炼油-化工一体化”的主体装置,催化裂化仍然保持了其在石油化工行业中的重要地位。
我国的催化裂化技术与国际先进水平保持同步,进入21世纪以后,由于我国催化裂化装置在炼厂地位的特殊性,技术发展的势头更猛,目前为止,基本解决了由于产品升级换代给催化裂化工艺带来的各种问题,而且在应对产品质量问题的技术开发过程中,拓宽了催化裂化产品的品种和范围,为确保催化裂化技术在未来石油化工中的核心地位提供了技术保证。
催化裂化装置的工艺原理是在流化状态下的催化剂作用下,重质烃类在480--520 ℃及0.2-0.3MPa(a)的条件下进行反应。
主要包括:1).裂解反应:大分子烃类裂解为小分子,环烷烃进行断环或侧链断裂,单环芳烃的烷基侧链断裂。
2).异构化反应:正构烷烃变成异构烷烃,带侧链的环烃或烷烃变成环异烷,产品中异构烃含量增加。
3).芳构化反应:环己烷脱氢生成芳香烃,烯烃环化脱氢生成芳烃。
4).氢转移反应:多环芳烃逐渐缩合成大分子直至焦炭,同时一种氢原子转移到烯烃分子中,使烯烃饱和成烷烃。
催化裂化装置的规模近三十年来逐步发展到350万吨/年(加工1000万吨/年原油)。
加工的原料为常压蜡油、减压渣油以及蜡油加氢裂化尾油。
原料主要性质装置由反应再生、分馏、吸收稳定(包括产品精制)、烟气能量回收几个部分组成。
装置主要产品为液化气、汽油、重石脑油和轻柴油,副产部分干气和油浆。
液化气去气体分馏装置。
催化裂化装置能耗特点分析及节能措施探讨
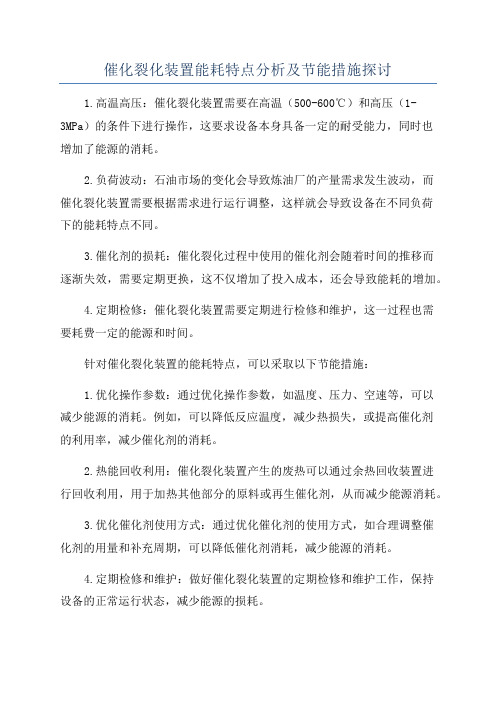
催化裂化装置能耗特点分析及节能措施探讨1.高温高压:催化裂化装置需要在高温(500-600℃)和高压(1-3MPa)的条件下进行操作,这要求设备本身具备一定的耐受能力,同时也增加了能源的消耗。
2.负荷波动:石油市场的变化会导致炼油厂的产量需求发生波动,而催化裂化装置需要根据需求进行运行调整,这样就会导致设备在不同负荷下的能耗特点不同。
3.催化剂的损耗:催化裂化过程中使用的催化剂会随着时间的推移而逐渐失效,需要定期更换,这不仅增加了投入成本,还会导致能耗的增加。
4.定期检修:催化裂化装置需要定期进行检修和维护,这一过程也需要耗费一定的能源和时间。
针对催化裂化装置的能耗特点,可以采取以下节能措施:1.优化操作参数:通过优化操作参数,如温度、压力、空速等,可以减少能源的消耗。
例如,可以降低反应温度,减少热损失,或提高催化剂的利用率,减少催化剂的消耗。
2.热能回收利用:催化裂化装置产生的废热可以通过余热回收装置进行回收利用,用于加热其他部分的原料或再生催化剂,从而减少能源消耗。
3.优化催化剂使用方式:通过优化催化剂的使用方式,如合理调整催化剂的用量和补充周期,可以降低催化剂消耗,减少能源的消耗。
4.定期检修和维护:做好催化裂化装置的定期检修和维护工作,保持设备的正常运行状态,减少能源的损耗。
5.技术改进和创新:通过技术改进和创新,如引入先进的催化剂、改进反应装置结构等,可以提高催化裂化装置的效率,降低能源的消耗。
总之,催化裂化装置的能耗特点是高温高压、负荷波动、催化剂损耗和定期检修等。
针对这些特点,可以通过优化操作参数、热能回收利用、优化催化剂使用方式、定期检修和维护以及技术改进和创新等节能措施来降低能源消耗,提高装置的能效性能。
催化裂化装置产汽系统及余热锅炉技术特点概述

催化裂化装置产汽系统及余热锅炉技术特点概述随着工业化进程的不断推进,石油化工行业的发展也愈发迅猛。
炼油业作为石油化工产业中最重要的产业之一,对能源资源的利用和环境保护提出了更高的要求。
在炼油过程中,催化裂化装置产汽系统及余热锅炉技术扮演着重要的角色。
在这篇文章中,我们将概述催化裂化装置产汽系统及余热锅炉技术的特点和应用。
一、催化裂化装置产汽系统1.技术原理催化裂化是一种重要的炼油工艺,在炼油过程中通过催化剂将重质原油分解成轻质油品的方法。
催化裂化装置产汽系统是催化裂化装置中的一个重要组成部分,其主要作用是产生高温高压的蒸汽,为催化裂化反应提供所需的热量和压力。
2.技术特点(1)高效节能:催化裂化装置产汽系统采用先进的节能技术,能够充分利用燃料燃烧产生的热能,实现高效节能。
(2)稳定可靠:产汽系统运行稳定,设备可靠,能够满足催化裂化装置在不同工况下的运行需求。
(3)自动化控制:采用先进的自动化控制系统,实现对产汽系统的精准控制,提高生产效率,降低人工操作成本。
(4)环保节能:产汽系统能够充分利用余热资源,减少能源消耗,降低对环境的影响。
3.应用领域催化裂化装置产汽系统广泛应用于炼油、化工等行业,为生产提供所需的蒸汽能源,是炼油生产过程中不可或缺的重要设备。
二、余热锅炉技术余热锅炉是一种利用工业生产过程中废热资源的能源回收设备,其原理是将工业生产过程中产生的高温废热转化为蒸汽或热水,用于供暖或生产过程中的热能需求。
(1)废热回收:余热锅炉技术能够有效回收工业生产过程中产生的废热能源,提高能源利用效率。
(2)灵活多样:余热锅炉技术可以根据不同的工业生产过程和废热特点进行定制设计,满足不同用户的热能需求。
(3)环保节能:余热锅炉技术能有效减少工业生产过程中的能源消耗,降低排放,具有显著的环保效益。
(4)经济效益:余热锅炉技术的应用能够有效降低企业的能源成本,改善生产效率,提高企业的经济效益。
余热锅炉技术广泛应用于炼油、化工、钢铁、造纸等行业,为工业生产提供经济、环保的热能解决方案。
重油催化裂化装置停工大检修安全环保对策
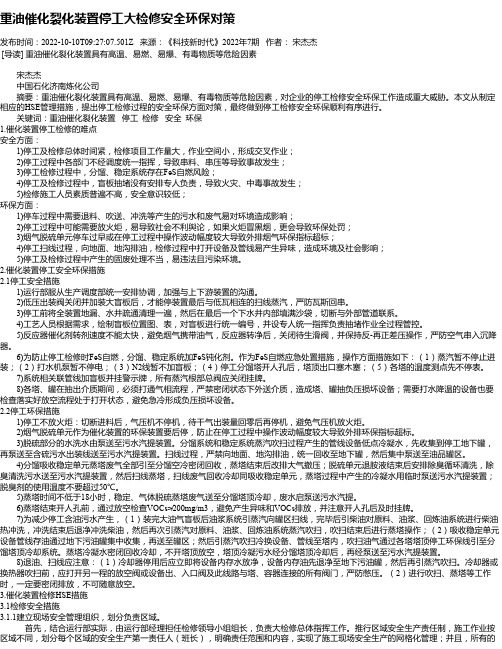
重油催化裂化装置停工大检修安全环保对策发布时间:2022-10-10T09:27:07.501Z 来源:《科技新时代》2022年7期作者:宋杰杰[导读] 重油催化裂化装置具有高温、易燃、易爆、有毒物质等危险因素宋杰杰中国石化济南炼化公司摘要:重油催化裂化装置具有高温、易燃、易爆、有毒物质等危险因素,对企业的停工检修安全环保工作造成重大威胁。
本文从制定相应的HSE管理措施,提出停工检修过程的安全环保方面对策,最终做到停工检修安全环保顺利有序进行。
关键词:重油催化裂化装置停工检修安全环保1.催化装置停工检修的难点安全方面:1)停工及检修总体时间紧,检修项目工作量大,作业空间小,形成交叉作业;2)停工过程中各部门不经调度统一指挥,导致串料、串压等导致事故发生;3)停工检修过程中,分馏、稳定系统存在FeS自燃风险;4)停工及检修过程中,盲板抽堵没有安排专人负责,导致火灾、中毒事故发生;5)检修施工人员素质普遍不高,安全意识较低;环保方面:1)停车过程中需要退料、吹送、冲洗等产生的污水和废气易对环境造成影响;2)停工过程中可能需要放火炬,易导致社会不利舆论,如果火炬冒黑烟,更会导致环保处罚;3)烟气脱硫单元停车过早或在停工过程中操作波动幅度较大导致外排烟气环保指标超标;4)停工扫线过程,向地面、地沟排油,检修过程中打开设备及管线易产生异味,造成环境及社会影响;5)停工及检修过程中产生的固废处理不当,易违法且污染环境。
2.催化装置停工安全环保措施2.1停工安全措施1)运行部服从生产调度部统一安排协调,加强与上下游装置的沟通。
2)低压出装阀关闭并加装大盲板后,才能停装置最后与低瓦相连的扫线蒸汽,严防瓦斯回串。
3)停工前将全装置地漏、水井疏通清理一遍,然后在最后一个下水井内部填满沙袋,切断与外部管道联系。
4)工艺人员根据需求,绘制盲板位置图、表,对盲板进行统一编号,并设专人统一指挥负责抽堵作业全过程管控。
5)反应器催化剂转剂速度不能太快,避免烟气携带油气,反应器转净后,关闭待生滑阀,并保持反-再正差压操作,严防空气串入沉降器。
- 1、下载文档前请自行甄别文档内容的完整性,平台不提供额外的编辑、内容补充、找答案等附加服务。
- 2、"仅部分预览"的文档,不可在线预览部分如存在完整性等问题,可反馈申请退款(可完整预览的文档不适用该条件!)。
- 3、如文档侵犯您的权益,请联系客服反馈,我们会尽快为您处理(人工客服工作时间:9:00-18:30)。
催化裂化联合装置工程建设特点、难点
1、工程建设特点
1.1本项目超大型设备多,设备重量重。
1.2厂内地方紧张,共有11台超大设备需要在现场制造,设备运输困难。
1.3施工周期长,既有专业之间的相互交叉施工,又有工序之间的交叉和多层作业的交叉,施工的工序要求严格,各工种交叉作业多。
1.4地下障碍物多,不可预见因素多。
1.5工程量大,决定了本工程安装的工期比较紧张。
1.6散件吊装量大,吊装工作量密度大。
1.7 电气仪表、联锁控制点多,逻辑关系复杂,监控要求可靠性高。
2、工程建设难点
2.1 设备规格大、吨位重、施工难度大
装置的核心设备再生器、反应沉降器、分馏塔、稳定塔、解吸塔、下流式外取热器、三级旋风分离器、冷、热、废催化剂罐等大规格、大吨位的设备吊装给施工带来较大的难度,对施工组织、工艺方案和质量控制均提出了较高的要求。
2.2 催化裂化三大机组施工难度大
该装置的三大机组——主风机、气压机和增压机是装置的心脏。
其中主风机组为三机组组合,即:烟机+主风机+电动机。
该机组安装、调试存在四大特点、难点:机组的轴系长,整机组水平度、同轴同心
度要求高;烟机在高温下运行,导致机组几何尺寸及各部位间隙变化大;压缩机静叶角度,马达标尺位置和仪表三者同步控制要准;机组轴心距离大,压缩机转子重量大,运行平稳首当其中;采用大型吊车吊装,对设备、器材到货提出了更高的要求。
2.3 衬里工程量大,质量要求高,施工难度较大
两器、余热锅炉等设备衬里质量要求高,衬里是本工程的关键之一。
衬里施工与其它施工工序密切相关,施工难度较大,部分工序需与安装穿插进行施工。
2.4两器构架占地面积大,主体构架结构高;设备安装、部件布置密集。
2.5因场地狭窄,使大吊就位的设备较多,要认真统筹规划好设备基础的施工进度和设备进场时间。
2.6高空作业多,各工种深度交叉作业大,施工安全管理难度大。
2.7焊接工程量大,合金钢、不锈钢管道及现场组焊设备工程量大,是质量控制的重点和难点。
2.8因施工区域周边都是生产区域,必须减少粉尘给周边生产造成影响,加大HSE的管理难度。
2.9 电缆架空敷设作业难度大。
2.10 与仪表连锁机泵多,增加调试难度。