模具第四章完成
塑料成型机械及模具 第四章 注射机
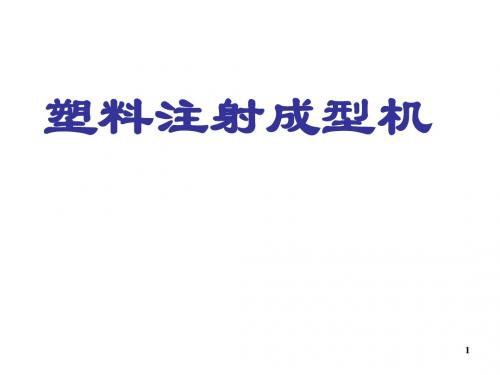
容易成型的 制品 一般制品 高粘度、有 精度要求的 制品 高粘度、高 精度、充模 难的制品
P模腔=40~70%P注射
实 例 模腔平均压 力 25MPa PE、PP、PS等壁厚均 匀的日用品容器类制品 30MPa 在模具温度较高的条件 下,薄壁容器类制品 35MPa ABS等有精度要求的工 业零件,如壳体、齿轮 等 40MPa 高精度的工业零件
7
4.1.3注射成型机的工作过程及组成
?
一 注射成型机的工艺过程
a) 闭模和锁紧
b) 注射装置前移和注射
c) 压力保持
d) 制品冷却和预塑化
e) 注射装置后退和开模顶出装置
8
注射成型机工作循环周期图
闭模
试合模 发信
高压低速锁紧
注座前移
注射
制品落下检测发信
开模
冷却 塑化退回
保压
注 射 动 作 选 择
41
4.1.7
• • • • • • •
注射部分主要性能参数
1、注射量 2、注射压力 3、注射速度和注射速率 4、锁模力 5、塑化能力 6、合模装置基本尺寸 7、工作效率参数
42
1、注射量
• 定义:机器在对空注射条件下,注射螺杆 (柱塞)作一次最大注射行程时,注射装 置所能达到的最大注射量 • 注射量由注射机的螺杆直径和螺杆移动行 程决定。
57
•
螺杆的塑化能力,应该在规定的时间内,保 证提供足够量的塑化均匀的熔料 塑化能力应满足: G>=3.6×W/t 其中: t---制件最短冷却时间(s) W--机器注射量(g) G---螺杆塑化能力(Kg/h)
58
6、合模装置基本尺寸
• 合模装置的尺寸直接关系到机器所能加工制品的范 围,如制品的面积,高度 • 1 模板尺寸和拉杆有效间距 模板尺寸(H*V) 拉杆有效间距(Ho*Vo) 一般模板面积大约是拉杆有效面积的2.5倍。
第四章 模具设计与制造
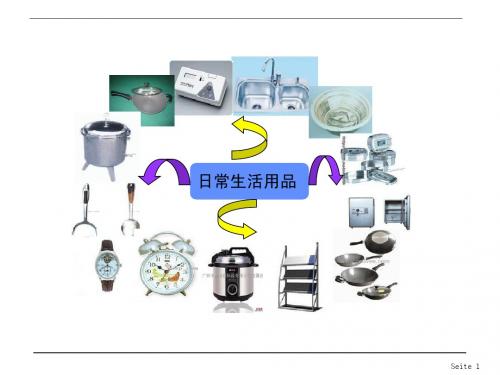
Seite 14
§4-3 圆筒形件的工艺计算
一、 修边余量δ的确定:
δ :拉深件口部或凸缘周边不齐,留余量, 事后切掉。称:~ δ 值:查表4-4(无凸);表4-5 有凸缘圆 筒;
Seite 21
表4-18 表4-19
表4-20
表4-23
§4-4 其他形状零件拉深
一、阶梯圆筒形件的拉深
根据不同的阶梯件尺寸,按下面的方法进行拉深。
1、由大阶梯到小阶梯逐次拉深。 当每个相邻阶梯的直径比 d2/d1,d3/d4....均大于相应的圆筒形件
的极限拉深系数时,则可以在每次拉深形成一个台阶,由大
拉深过程 §4-1 一、 拉深:
利用拉深模将平板毛坯 拉成 开口空心件的冲压工序。
拉深的基本原理
二、拉深的特点:
生产效率高;材料消耗小; 零件的强度和刚度高;工件的精度也较高; 件尺寸精度高达 IT8~IT10; 精整拉深( 不复杂件),达IT6~IT8(磨削)。
Seite 3
第四章 拉深及拉深模设计 (拉延)
图4-15
ϕ 19
6
R3 .5
68
ϕ 12
表4-4 表4-7
• •
Байду номын сангаас• •
图 = 6133 .44 = 78.32 ≈ 78 mm ③ 确定是否用压边圈: 根据毛坯相对厚度 t/D×100=1/78 =1.28 查表4-18 应采用压边圈 ④ 确定拉深次数 n: 采用查表法,当 t/D×l00 = 1.28,h / d = 3.7 (包括修边余量后的h为74mm)时,由表4-12查得 n = 4
塑料模具设计第七周 第一讲(第四章)
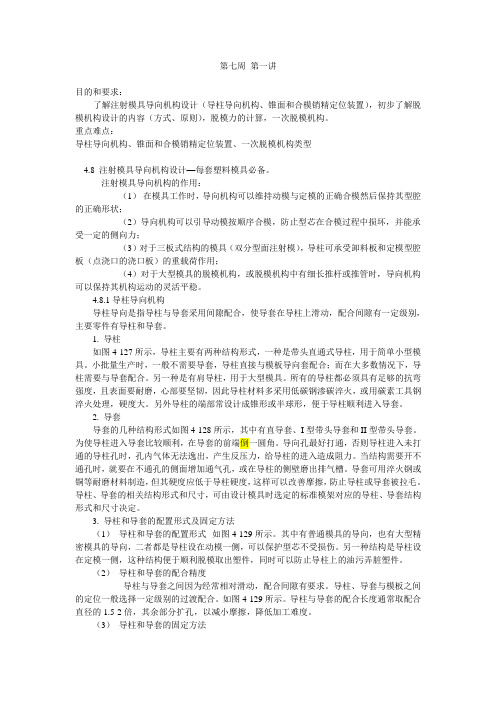
第七周第一讲目的和要求:了解注射模具导向机构设计(导柱导向机构、锥面和合模销精定位装置),初步了解脱模机构设计的内容(方式、原则),脱模力的计算,一次脱模机构。
重点难点:导柱导向机构、锥面和合模销精定位装置、一次脱模机构类型4.8 注射模具导向机构设计—每套塑料模具必备。
注射模具导向机构的作用:(1)在模具工作时,导向机构可以维持动模与定模的正确合模然后保持其型腔的正确形状;(2)导向机构可以引导动模按顺序合模,防止型芯在合模过程中损坏,并能承受一定的侧向力;(3)对于三板式结构的模具(双分型面注射模),导柱可承受卸料板和定模型腔板(点浇口的浇口板)的重载荷作用;(4)对于大型模具的脱模机构,或脱模机构中有细长推杆或推管时,导向机构可以保持其机构运动的灵活平稳。
4.8.1导柱导向机构导柱导向是指导柱与导套采用间隙配合,使导套在导柱上滑动,配合间隙有一定级别,主要零件有导柱和导套。
1. 导柱如图4-127所示,导柱主要有两种结构形式,一种是带头直通式导柱,用于简单小型模具。
小批量生产时,一般不需要导套,导柱直接与模板导向套配合;而在大多数情况下,导柱需要与导套配合。
另一种是有肩导柱,用于大型模具。
所有的导柱都必须具有足够的抗弯强度,且表面要耐磨,心部要坚韧,因此导柱材料多采用低碳钢渗碳淬火,或用碳素工具钢淬火处理,硬度大。
另外导柱的端部常设计成锥形或半球形,便于导柱顺利进入导套。
2. 导套导套的几种结构形式如图4-128所示,其中有直导套、I型带头导套和II型带头导套。
为使导柱进入导套比较顺利,在导套的前端倒一圆角。
导向孔最好打通,否则导柱进入未打通的导柱孔时,孔内气体无法逸出,产生反压力,给导柱的进入造成阻力。
当结构需要开不通孔时,就要在不通孔的侧面增加通气孔,或在导柱的侧壁磨出排气槽。
导套可用淬火钢或铜等耐磨材料制造,但其硬度应低于导柱硬度,这样可以改善摩擦,防止导柱或导套被拉毛。
导柱、导套的相关结构形式和尺寸,可由设计模具时选定的标准模架对应的导柱、导套结构形式和尺寸决定。
UG NX 10.0模具设计教程第4章
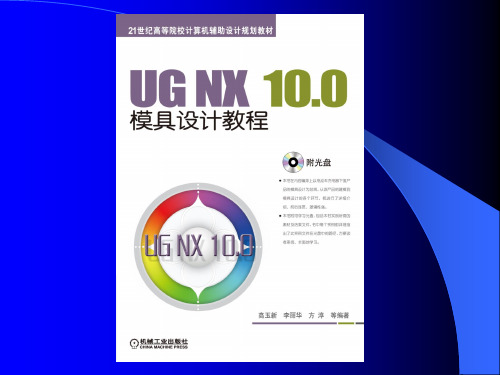
【例4-2】 定义模具坐标系 继续以例4-1的模型进行讲述,首先打开附带光盘 ch04/ch04_02_02中的顶层装配文件“shiduyi_top_050”,操作步骤 如图4-12所示。
2
1
3
图4-9
3)完成产品模型加载后,系统会自动载入一些装配文件,并自动保
存在项目路径下
4.3 模具坐标系
模具坐标系是所有模具装配部件的参考基准,它的正确设置与
否直接关系到模具的结构设计。在定义模具坐标系之前,首先要 分析产品结构,弄清产品的开模方向及分型面所处的位置;然后
通过坐标系的移动及旋转操作将模型的工作坐标系调整到产品模
默认的参数,单击“确定”按钮,生成工件,如图4-4所示。
图4-4
4.型腔布局
8
8
单击“注塑模向导”工具栏中的“型腔布局”按钮,弹出“型腔 布局”对话框,其操作过程如图4-5所示。
1
3
2
4
5
图4-5
4.2 初始化项目
UG NX 10.0 模具设计中产品模型 的加载是通过“注塑模向导”工具栏 的“初始化项目”工具按钮来完成, 并可设置项目的名称及保存路径。
1.插入腔 2.变换
3.移除
移除功能用于对工件进行移除操作。选择待移除工件后,单击“移除” 按钮即可,但至少留下一个型腔。
4.自动对准中心 自动对准中心的功能是将模具坐标系自动移动到模具布局的中心位置, 该中心位置将作为模架的调入中心。单击“编辑布局”分组中的 “自动对准中心”按钮,即可执行模具坐标系对中操作。 【例4-4】 型腔布局
锻造工艺与模具设计 第四章

II
h
III
I III II I
Seite 36
I
平砧镦粗变形分布与应力状态分析
r
区域(II)
处于坯料中断内部,属于大变形区,原因:受摩擦力影 响小应力状态有利于变形;
II
h
III
I III II I
Seite 37
H0/D0=2. 5Ⅲ Ⅰ Ⅲ Ⅱ Ⅳ ⅢⅡ Ⅲ Ⅰ H0/D0=1~0.67 Ⅰ Ⅲ Ⅱ Ⅲ Ⅰ
HO/D0=1.45 Ⅰ Ⅲ Ⅱ Ⅳ Ⅲ Ⅱ Ⅰ
H0/D0=0.22 ⅢⅡ Ⅰ Ⅰ ⅡⅢ
II
h
III
I III II I I
r
Seite 38
平砧镦粗变形分布与应力状态分析
3.镦粗结果:
a.坯料由圆柱形变为鼓形。另外,(I)区与工具接触,温 度降低快,也是难变形的原因之一。 b.这样三个区域的变形不均匀使金属内部晶粒粗细不一。 大变形区变形充分,得到细晶粒;难变形区,还保留粗大 的铸态组织。 c.(Ⅱ)(Ⅲ)区变形的不均,又引起了侧表面裂纹的产 生。
同时击碎合金工具钢中的块状碳化物,并使其分布均匀
以提高锻件的使用性能。 ⑷ 提高锻件的横向力学性能以减小力学性能的异向性。
Seite 32
(二)镦粗分类:
圆截面镦粗 原料来分: 矩形截面镦粗 方截面镦粗等
平砧镦粗
镦粗方式:
垫环镦粗
局部镦粗
Seite 33
(三)主要质量问题和变形流动特点
-------针对圆截面坯料的镦粗讨论
Seite 22
图4-6 空心类锻件的锻造过程 a)圆环的锻造过程 b)圆筒的锻造过程
《模具技术》4
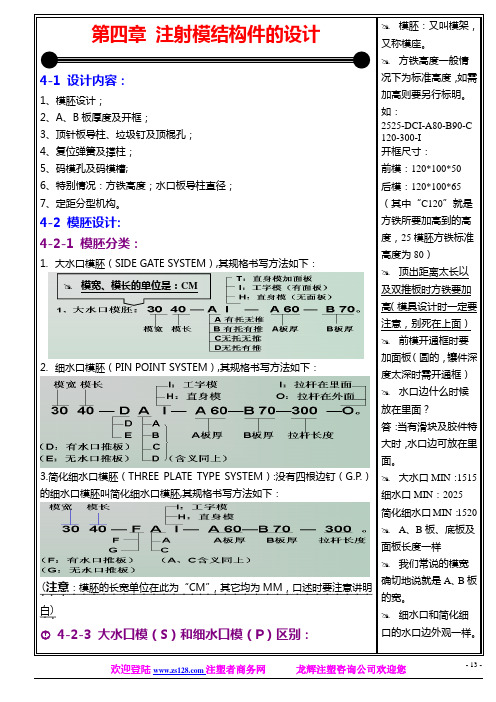
第四章注射模结构件的设计4-1 设计内容:1、模胚设计;2、A、B板厚度及开框;3、顶针板导柱、垃圾钉及顶棍孔;4、复位弹簧及撑柱;5、码模孔及码模槽;6、特别情况:方铁高度;水口板导柱直径;7、定距分型机构。
4-2 模胚设计:4-2-1 模胚分类:1.大水口模胚(SIDE GATE SYSTEM),其规格书写方法如下:2.细水口模胚(PIN POINT SYSTEM),其规格书写方法如下:3.简化细水口模胚(THREE PLATE TYPE SYSTEM):没有四根边钉(G.P.)的细水口模胚叫简化细水口模胚,其规格书写方法如下:(.注意..:模胚的长宽单位在此为“............CM..”,其它均为......MM..,口述时要注意讲明白..........). 4-2-3 大水口模(S)和细水口模(P)区别:一、下列结构或零件P有而S无:1、水口推板;2、水口边;3、定距分型机构(包括扣基)。
二、S又称二板模,单分型面,水口和胶件从同一个地方取出;P又称三板模,双分型面,水口和胶件从不同地方取出。
三、进胶(入水)方式不同:1、P可从型腔内任一点入水;2、S大多从型腔侧面入水。
四、成本不同:P较贵,且在生产过程中出故障率高。
模胚:又叫模架,又称模座。
方铁高度一般情况下为标准高度,如需加高则要另行标明。
如:2525-DCI-A80-B90-C 120-300-I开框尺寸:前模:120*100*50后模:120*100*65 (其中“C120”就是方铁所要加高到的高度,25模胚方铁标准高度为80)顶出距离太长以及双推板时方铁要加高(模具设计时一定要注意,别死在上面) 前模开通框时要加面板(圆的,镶件深度太深时需开通框) 水口边什么时候放在里面?答:当有滑块及胶件特大时,水口边可放在里面。
大水口MIN:1515 细水口MIN:2025简化细水口MIN:1520 A、B板、底板及面板长度一样我们常说的模宽确切地说就是A、B板的宽。
14592模具制造工艺学 第四章讲课稿

三、数控加工的特点与应用
(4)提高可靠性 数控系统比较贵重,用户期望发挥投资效 益,要求设备可靠,特别是对要用在长时间无人操作环境 下运行的数控系统,可靠性成为人们最为关注的问题。 (5)具有更高的通信功能 为适应FMC、FMS以及进一步联 网组成CIMS的要求,一般的数控系统都具有RS—232C和R S—422高速串行接口,高档的数控系统应具有DNC接口。 (6)具有开放性 传统的数控系统是一种专用封闭式系统, 各个厂家的产品之间以及与通用计算机之间不兼容,维修、 升级困难,越来越难以满足市场对数控技术的要求。
成形磨床、连续轨迹坐标磨床 三种。加工中心:加工中心机床 即是多工序可自动换刀的数控 镗铣床。
二、数控机床的工作原理与分类
1.数控机床的工作原理
图4-1 数控机床的组成
二、数控机床的工作原理与分类
2.数控机床的组成 (1)控制介质 控制介质是用于记载各种加工信息(如零件加 工的工艺过程、工艺参数和位移数据等)的媒体,经输入装 置将加工信息送给数控装置。 (2)数控装置 数控装置是数控机床的核心,它的功能是接 受输入装置输入的加工信息,经过数控装置的系统软件或 逻辑电路进行译码、运算和逻辑处理之后,发出相应的脉 冲送给伺服系统,通过伺服系统控制机床的各个运动部件 按规定要求动作。
二、数控机床的工作原理与分类
(2)金属成形类 属于此类的有数控折弯机、数控弯管机、 数控冲床、数控旋压机等。 (3)特种加工类 属于此类的有数控电火花线切割机床、数 控电火花成形机床及数控激光切割焊接机等。 (4)其他类 属于此类的有数控火焰切割机床、数控激光热 处理机床、三坐标测量机等。
三、数控加工的特点与应用
c) 数控机床加工
① 根据工件形状和尺寸、材料、技术要求,进行程序设 计;通过数控装置的变换,发出相应的指令,控制机床的动作。 原理:
第四章 拉深工艺及模具设计

拉深过程中影响起皱的主要因素
板料的相对厚度 t/D
t dt d
t/D 越小,拉深变形区抗失稳的能力越差,越易起皱。
拉深系数 m(切向压应力的大小)
m 越小,拉深变形程度越大,切向压应力的数值越大;另外, 变形区的宽度越大,抗失稳的能力变小,越易起皱。
模具工作部分几何形状
用锥形凹模拉深时,由于毛坯的 过渡形状使拉深变形区有较大的抗失 稳能力,与平端面凹模相比可允许用 相对厚度较小的毛坯而不致起皱。
划分为五个区: I 凸缘部分 II 凹模圆角部分 III 筒壁部分 IV 凸模圆角部分 V 筒底部分
下标1、2、3分别代表 坯料径向、厚向、切 向的应力和应变
坯料各区的应力与应变是很不均匀的。
24.10.2023
IV
24.10.2023
I II
III V
三、拉深变形过程中凸缘变形区的应力分布
拉深至某一瞬时 R t
使
max 1 max
出现在
R t0.7~0.9R 0
即拉深早期。
24.10.2023
四、筒壁传力区的受力分析
(1)压边力Q 引起的摩擦应力
M
2 Q dt
(2)材料流过凹模圆角半径产生弯 曲变形的阻力
W 14b
rd
t t
2
(3)材料流过凹模圆角后又被拉直 成筒壁的反向弯曲力
'WW14b
t rdt
2
24.10.2023
§4-3 直壁旋转体零件的拉深
一、拉深毛坯尺寸的确定
拉深毛坯尺寸的确定原则: 体积不变原则: 若拉深前后料厚不变,拉深前坯料表面积与拉深后
冲件表面积近似相等,得到坯料尺寸。
- 1、下载文档前请自行甄别文档内容的完整性,平台不提供额外的编辑、内容补充、找答案等附加服务。
- 2、"仅部分预览"的文档,不可在线预览部分如存在完整性等问题,可反馈申请退款(可完整预览的文档不适用该条件!)。
- 3、如文档侵犯您的权益,请联系客服反馈,我们会尽快为您处理(人工客服工作时间:9:00-18:30)。
第四章拉深工艺及拉深模设计4.1什么是拉深?拉深过程中,变形区的材料是怎样流动的?答:拉深是利用拉深模具将冲裁好的平板毛坯制成各种开口的空心件,或将已制成的开口空心件加工成其他形状空心件的一种冲压加工方法。
拉深过程中,毛坯受凹模拉伸力的作用,在凸缘毛坯的变形区内受径向拉应力和切向压应力的作用,产生塑性变形,在他们共同作用下,将毛坯的环形部分变为圆筒形件的直壁。
壁行变形的程度,由底部向上逐渐的增大,在圆筒顶部的变形达到最大值。
该处的材料,在圆周方向受到最大的压缩,高度方向获得最大的伸长。
拉深过程中,圆筒的底部基本上没有塑性变形。
4.2拉伸时材料的应力应变状态怎么样?答:在拉伸过程中,材料在不同的部位具有不同的应力状态和应变状态。
以筒形件为例说明:课本上p85图4-5,(画图)是筒形状在有压边圈的首次拉伸中某一时刻的应力应变情况;根据应力应变状态的不同,将拉伸毛料分为五个区域:1.凸缘部分应力:径向手拉力,厚度方向受压力,切向受压应变:径向变长,厚度变厚,切向变短2.凹模圆角部分应力:径向受拉应力,切向受压应力,厚度方向压应力应变; 厚度减薄。
3筒壁部分 4.凸模圆角部分应力:受拉应力应变;伸长应变,压缩应变。
应力:径向受拉、厚度方向受压,切向拉应应变;5.筒形件的底部应力:应变;可认为无塑性变形。
又在筒壁与底部转角处稍上的部分,传递拉伸力的截面积较小,产生的拉应力较大。
4.3什么是拉深系数?拉深系数对拉伸工作有什么影响?答:拉深系数m是对于拉深零件,拉深后的零件的直径与毛料直径之比。
意义:拉深系数表示了拉深前后毛料直径的变化量,反映了毛料外边缘在拉深时切向压缩变形的大小,其是衡量拉深时毛料变形程度的一种指标,拉深系数是小于1的数值,其值愈大表示拉深前后毛坯的直径变化愈小,即变形程度小。
4.5什么是极限拉深系数?影响极限拉深系数的因素有哪些?怎样确定拉伸次数?答:拉深工件在危险断面不至拉裂的条件下,所能达到的最小拉深系数,称为极限拉深系数。
影响极限拉深系数的因素有:(1)材料的机械性能:愈小,对拉深愈有利,(2)材料的相对厚度t/D::相对厚度愈大,拉深愈有利。
(3)润滑润滑条件良好对拉深有利,可以减小工件拉深系数(4)模具的几何参数:凸凹模的圆角半径和凸凹模之间的间隙对拉深系数也有影响。
实际上拉深系数有两个不同的概念,一是零件所需的拉深系数mε, mε=d/D。
式中,mε--零件总的拉深系数,d--零件的直径,D--该零件所需毛料的直径。
另一个是按材料的性能和加工条件等因素在一次拉深中所能达到的极限拉深系数m,如果零件所要求的拉深系数mε值大于极限拉深系数m,则所给零件可以一次拉深成型,否则多次拉深。
多次拉深时的拉深系数,确定方法有1)查表法。
筒形件的拉深次数,可更具零件的相对搞对h/d和毛料的相对厚度(t/Dx 100)2)推算法。
可根据极限拉深系数,m1,m2,m3……从第一道工序开始依次求半成品直径d1=m1D,d2=m2D1=m1m2D…. d n=m n D n−1=m1m2…m n D一直计算到得出的直径不大于零件要求的直径为止。
4.6拉深模中,凸凹模的圆角半径对拉深工作有什么影响?怎么选择凸凹模的圆角半径?拉深过程中,板料在凸模圆角部位滑动时产生较大的弯曲变形,由凹模圆角区进入直壁部分时,又被重新拉直,或在通过凸凹之间的间隙时受到校直作用。
若凹模圆角半径过小,则板料在经过圆角部位时的变形阻力以及在模具间隙里通过时的阻力都要增大,势必引起总拉深力增大和模具因弯曲力摩擦力增大而使寿命降低。
凹模圆角半径过大,使在拉深初始阶段不与模具表面接触的毛料宽度加大,毛料拉深压边效果降低,使这部分毛料很容易起皱。
拉深后期,过大的圆角半径也使毛料外缘过早的脱离压边圈的作用而起皱,尤其当毛料的相对厚度较小时起皱现象十分突出。
凸模圆角半径对拉深工作的影响:过小的凸模圆角半径会使毛料在这个部位上受到过大的弯曲变形,结果降低了毛料的危险断面的强度,也使极限拉深系数增大。
另外,即使毛料在危险断面不被拉裂,过小的凸模圆角半径也会引起危险断面附近毛料厚度局部变薄且这个局部变薄和弯曲的痕迹经过后拉深工序以后,还会在成品零件的侧壁上遗留下来,以影响零件的质量。
在多工序拉深时,后道工序的压边圈的圆角半径等于前道工序的凸模圆角半径,所以当凸模圆角半径过小时,在后道的拉深工序里毛料沿压边圈的滑动阻力增大,这对拉深过程的进行不利。
凸模圆角半径过大,会使在拉深初始阶段不与模具表面接触的毛料宽度加大,因此,这部分毛料容易起皱。
(1)拉深凹模圆角半径可按下式确定:γd=0.8√(D−d)t(mm)D—毛料直径(mm);d—凹模直径(mm);t—板料厚度(mm);当工件直径d>200mm时,按式γdmin=0.089d+2(mm)计算拉深凹模圆角也可根据工件材料及其厚度来确定。
(2)凸模圆角半径γp的确定单次或多次拉深中的第一次:γp=(0.7~1.0) γd多次拉深中的以后各次:γp=(d n−1−d n)/2n−1d n−1、d n前后两道工序中毛料的过渡直径(mm)最后一次拉深的凸模圆角半径即等于零件的圆角半径,但不得小于(2~3)t4-7、什么是拉深间隙?拉深间隙对拉深工艺有何影响?答:拉深间隙,是指拉深模的凸凹模的间隙(z=(d d−d p)/2),即单边间隙。
拉深间隙对拉深工艺的影响:(1)拉深力:间隙愈小,材料流入困难,拉深力雨大;(2)零件质量:间隙过大,容易起皱,且毛料口部的变厚得不到消除也会使零件出现锥度。
间隙过小,则会使零件容易拉断或变薄特别严重;(3)模具寿命:间隙小,则磨损加剧,间隙大寿命长但成型精度差;4-8、怎样确定凸凹模工作部分尺寸及制造公差?答:(一)对最后一道工序的拉深膜,其凹模、凸模的尺寸及其公差应按工件的要求来确定。
当工件要求外型尺寸时,以凹模为基准,凹模尺寸为D d=(D−34∆)0+δd凸模尺寸为D p=(D−34∆−2Z)−δp当工件要求内形尺寸时,以凸模为基准,凸模尺寸为D p=(D+0.4∆)−δp凹模尺寸为D d=(D+0.4∆+2Z)+δd(二)对于多次拉深时的中间过渡拉深,毛料的尺寸公差没有必要予以严格限制,这是模具尺寸只要等于毛料过度尺寸即可。
若以凹模为基准,则凹模尺寸为D d=D0+δd凹模尺寸为D p=(D−2Z)−δp式中:δp(凸模制造公差)——一般按公差等级IT6-IT8选取;δd(凹模制造公差)——一般按公差等级IT6-IT8选取;4-9、压边圈再拉深中起何作用?答:压边圈在拉深中作用是防止拉深毛料在拉深过程中变形区(主要是凸缘区域)应切向压应力过大造成厚度方向材料失稳而起皱。
4-15冲压生产如图所示零件,材料为10钢,请完成以下工作:(1)计算该零件的毛坯尺寸;(2)确定该零件的拉深次数和中间半成品尺寸;(3)确定最后一次拉深时模具工作部分尺寸及其公差;(4)画出首次拉深及其最后一次拉深的模具结构草图。
解:(1)计算该零件的毛料尺寸由于对拉深高度 h =h-0.5x2= 75mm,拉深相对高度h/d = 75/(30-2)=2.71mm,查表4-2得该零件的修边尺寸余量δ=6mm,H=h+δ=75+6=81mm,零件的中型层直径d=30-2=28mm将零件分成三部分,分别计算各部分,最后可得毛料直径为=√(d−2r)2+2πr(d−2r)+8r2+4d(H−r)= √(28−2x4)2+2xπx4(28−2x4)+8x42+4x28x(81−4)=98.3mm(2)确定该零件的拉深系数和中间半成尺寸1)判断是否能一次完成拉深对于图示的零件,毛料的相对厚度t/Dx100=2,从P91表4-4查出各次拉深系数:m1=0.6,m2=0.75,m3=0.80,m4=0.84,m5=0.87,由已知条件可知零件总的拉深系数m∈=dD =1898.3=0.29<m1,故需多次拉深。
2)计算拉伸次数d1=m1D=0.68*98.3=58.8mm d2=m2D1=0.75*58.8=44mm d3=m3D2=0.80*44=35.2mm d4=m4D3=0.84*35.2=29.6mm d5=m5D4=0.87*29.6=25.8mmd 1,d 2,d 3,d 4均大于18,也就是变形程度大于材料的极限变形程度,而经过第五次拉深才可以,故该零件需五次拉深才行。
3)确定半成品尺寸:A .半成品直径拉深系数确定后,再根据计算直径d n 应等于d I 件的原则对拉深系数进行调整,使实际采用的拉深系数大于推荐拉深系数时所采用的极限拉深系数。
零件实际拉深系数应调整为:m 1=0.61,m 2=0.77,m 3=0.82,m 4=0.85,m 5=0.88 原来m 1=0.6,m 2=0.75,m 3=0.80,m 4=0.84,m 5=0.87,调整好拉深系数后,重新计算各次拉深的圆筒直径即得半成品直径第一次:d 1=60mm ,m 1,=6098=0.61第二次:d 2=46mm ,m 2,=4660=0.77 第三次:d 3=38mm ,m 3,=3846=0.82第四次:d 4=32mm ,m 4,=3238=0.85第五次:d 5=28mm ,m 5,=2832=0.88B .半成品高度h 1=0.25×(D 2d 1−d 1)+0.43r1d 1(d 1−0.32r 1) …h n =0.25×(D 2d n −d n )+0.43rn d n (d n −0.32r n ) 式中:D —毛料直径,D=98mm h 1,h 2…h n —半成品各次拉深高度(mm ) d 1,d 2…d n —半成品各次拉深后直径(中性层值,mm ) r 1,r 2…r n —半成品各次拉深后底部圆角半径(mm )据P94表4-6查出:γd=(10~6)t=20~12,取γd=20mm 由式4-8,γp1=(0.7~1.0) γd=14~20,取γp=15mm由式4-9,γp2=(d2-d3-2t)/2=(46-38-2x2)/2=2mm, 但γp2≥(2~3)t,取γp2=10,同取γp3=8mm,γp4=4mm,故r1=15mm,r2=10mm,r3=8mm,r4=4mm,代入公式: h1=0.25×(98260−60)+0.431560(60−0.32×15)=32mm同理得:h2=45mm,h3=57mm,h4=69mm各次半成品总高度:H1=h1+r1+t/2=32+15+1=48mm,H2=h2+r2+t/2=45+10+1=56mm,同理得:H3=66mm,H4=74mm(3)确定最后一次拉深时模具工作部分的尺寸和公差由于工件要求外形尺寸,故要以凹模为基准凹模尺寸为:D d=(D−34∆)0+δd=(30−3/4×0.4)+0.020=29.70+0.020凸模尺寸为:D p=(D d−2Z)−δp0 =(29.7−2×2.2)=25.3间隙Z=t max+ct=2+0.1+2=2.2mm,据P97表4-7查出增大系数c=0.1。