数控机床的动态特性概述
基于SAMCEF平台的机床整机动态特性分析

基于SAMCEF平台的机床整机动态特性分析机床的动态性能决定了机床的加工能力。
为分析优化机床的动态特性,研发人员在SAMCEF平台下,建立了机床的动力学模型,对该模型进行模态分析,同时采用LMS设备对该机床进行模态测试。
对比发现有限元计算振型与实验基本一致,计算得到的固有频率与实验得到的频率误差在16%之内,验证了该模型的可靠性。
利用该有限元模型,把所有部件作为柔性体建立动力学模型,进行多体动力学分析,研究载荷作用下导向部件及结构部件的动态应力变化情况,分析结果为机床优化设计提供方向。
机床作为生产的重要工具和设备,也被称为工作母机,其动态性能与其加工性能紧密相关,并直接影响所加工零件的精度。
随着现代设计方法的广泛运用,对机床进行动态特性分析,用动态设计取代静态设计已成为机床设计发展的必然趋势。
在设计中,仅对机床部件进行动态分析无法全面反映机床的整体性能。
因此,要对机床性能进行准确的预测,必须对机床整机进行动力学分析。
伴随着计算机计算速度的飞速提升,有限元分析成为分析计算复杂结构的一种极为有效的数值计算方法,为机床整机的振动模态理论分析提供了有力的工具。
本文利用SAMCEF动力学仿真平台和模态实验相结合的方式,对机床进行有限元计算和模态实验分析,为新产品研发设计提供了参考。
一、模态分析的基本理论振动现象是机械结构经常需要面对的问题之一。
由于振动会造成结构的共振或疲劳,从而破坏结构,所以必须通过模态分析了解模型的各阶固有频率和振型,避免在实际工况中因共振因素造成结构的损坏。
模态分析可以用来确定模型或结构的振动特性,对复杂结构进行精确的模态分析,将为评价现有结构的动态特性,诊断及预报结构系统的故障,新产品动态性能的预估及优化设计提供科学的依据。
三、机床模态实验本次试验是与LMS公司中国区技术支持工程师共同合作完成,针对VMC0540d立式加工中心进行模态实验,确定该机床的结构动力学参数,如图4所示。
同时,此次试验采用了LMS提供的测试设备及相应的分析软件:LMS SC310前端、PCB 333B30单向加速度计、激振器及功率放大器(3台)以及LMS Test Lab 9B模态测试分析软件等。
数控机床主轴加工过程中的动态特性控制方法
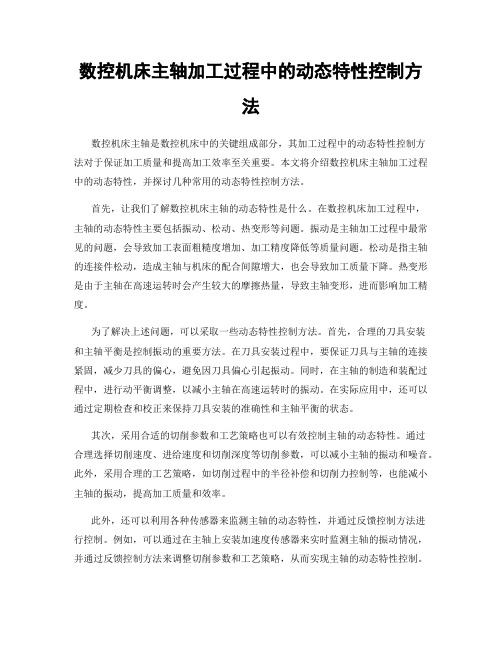
数控机床主轴加工过程中的动态特性控制方法数控机床主轴是数控机床中的关键组成部分,其加工过程中的动态特性控制方法对于保证加工质量和提高加工效率至关重要。
本文将介绍数控机床主轴加工过程中的动态特性,并探讨几种常用的动态特性控制方法。
首先,让我们了解数控机床主轴的动态特性是什么。
在数控机床加工过程中,主轴的动态特性主要包括振动、松动、热变形等问题。
振动是主轴加工过程中最常见的问题,会导致加工表面粗糙度增加、加工精度降低等质量问题。
松动是指主轴的连接件松动,造成主轴与机床的配合间隙增大,也会导致加工质量下降。
热变形是由于主轴在高速运转时会产生较大的摩擦热量,导致主轴变形,进而影响加工精度。
为了解决上述问题,可以采取一些动态特性控制方法。
首先,合理的刀具安装和主轴平衡是控制振动的重要方法。
在刀具安装过程中,要保证刀具与主轴的连接紧固,减少刀具的偏心,避免因刀具偏心引起振动。
同时,在主轴的制造和装配过程中,进行动平衡调整,以减小主轴在高速运转时的振动。
在实际应用中,还可以通过定期检查和校正来保持刀具安装的准确性和主轴平衡的状态。
其次,采用合适的切削参数和工艺策略也可以有效控制主轴的动态特性。
通过合理选择切削速度、进给速度和切削深度等切削参数,可以减小主轴的振动和噪音。
此外,采用合理的工艺策略,如切削过程中的半径补偿和切削力控制等,也能减小主轴的振动,提高加工质量和效率。
此外,还可以利用各种传感器来监测主轴的动态特性,并通过反馈控制方法进行控制。
例如,可以通过在主轴上安装加速度传感器来实时监测主轴的振动情况,并通过反馈控制方法来调整切削参数和工艺策略,从而实现主轴的动态特性控制。
最后,定期维护和保养主轴也是保证主轴动态特性稳定的重要手段。
定期清洗和润滑主轴的连接件,检查主轴的工作状态,及时更换磨损的零部件,可以延长主轴的使用寿命,保持其稳定的动态特性。
总结起来,数控机床主轴的动态特性控制方法包括合理的刀具安装和主轴平衡、采用合适的切削参数和工艺策略、利用传感器进行监测和反馈控制以及定期维护和保养主轴。
数控铣床主轴部件动态特性分析

模型 , 用 A S S对主轴部件进行模态分析 , 出主轴部件 的 应 NY 得 固有频率和 主振型 , 判断转速是否远低于主轴的一 阶临界转速 ,
为铣床主轴部件 的优化设计提供普遍的指导意义 。
图 1主 轴 一轴 承 的 简化 模 型 图
2主轴部件 的动力学模 型
21 . 主轴部件的结构分析
L U Da - in , HEN T o , HEN S u — h n W ANG Yu I o qa C a S h n c eg, e
( col f lc o eh ncl nier g Wu a nvr t o eh ooy Wu a 3 0 0 C ia h o o et m c ai g ei , h nU i s y f c n l , hn4 0 7 , hn ) S E r aE n n e i T g (. o i rvneMahnr e sahIs tt C .t. h n a g10 3 ,hn )  ̄ ann Po ic c ie R aec tue o d, e yn 10 2 C ia J g y ni L S
【 摘要 】 以某数控铣床主轴为研 究对象, 了轴和 角接触轴承的等效动力学模 型. 究 了轴承等 建立 研
效刚度和预紧力参数对主轴 系统固有频率影响规律 , 通过模 态分析确定主轴部件的 固有频率和振型, 验证 数控铣 床 主轴部件 结构 设计 的合理性 。 关键词 : 轴部 件 ; 限元分 析 ; 态特 性 ; 主 有 动 数控 铣床
到铣床 的加工精度 , 主轴部件在外力作用下将产生较大的变形 , 容 易引起振动 , 降低加工精度和表面质量。 主轴部件 的变形对机
床 的加工精度 , 表面质量有很大的影响, 为了使数控机床的主轴
综述数控机床检测技术

综述数控机床检测技术综述数控机床检测技术1.引言数控机床是现代制造业中不可或缺的关键设备,其精度和性能的稳定性直接影响着工件的加工质量和生产效率。
为了确保数控机床的正常运行和高精度加工,数控机床检测技术起到了重要的作用。
本文将综述数控机床检测技术的发展和应用,探讨其在制造业中的重要性。
2.数控机床检测技术的发展历程2.1 传统机床检测技术传统机床检测主要依靠人工操作和直观经验,存在检测不准确、效率低下和主观因素影响等问题。
由于制造工艺的特殊性,传统机床检测无法满足数控机床高精度加工的要求。
2.2 数控机床检测技术的出现随着计算机技术和传感器技术的进步,数控机床检测技术得到了快速发展。
通过在数控机床上安装传感器,实时采集机床的各项参数,再通过计算机进行数据处理和分析,可以实现对机床性能、加工精度和稳定性的准确评估。
3.数控机床检测技术的分类3.1 几何误差检测技术几何误差是数控机床加工精度的重要影响因素,几何误差检测技术主要通过测量数控机床各轴移动的精度和定位误差,来对几何误差进行评估和调整。
3.2 动态特性检测技术动态特性检测技术主要通过测量数控机床在加工过程中的振动、冲击和动态特性,来评估机床的稳定性和工作状态。
3.3 加工质量检测技术加工质量检测技术主要通过检测加工后的工件精度、表面质量和尺寸等指标,来评估数控机床的加工性能和加工质量。
4.数控机床检测技术的应用领域4.1 精密加工领域在需要高精度加工的领域,如航天器械、光学仪器和精密模具制造等,数控机床检测技术能够确保加工精度和稳定性,提高产品质量。
4.2 自动化生产领域数控机床检测技术与自动化生产相结合,能够实现生产过程的智能化和自动化,提高生产效率和工作安全。
4.3 故障诊断与维护领域数控机床检测技术可以实时监测机床的工作状态和健康状况,及时发现故障和异常,减少机床维护和停机时间。
5.数控机床检测技术的挑战与展望5.1 多参数综合评估技术目前数控机床检测技术主要以单一参数为基础进行评估,如何将多种参数综合评估,更全面地反映数控机床的性能和加工质量,是亟待解决的问题。
数控机床直线电机进给伺服系统的动态特性分析与研究

数控机床直线电机进给伺服系统的动态特性分析与研究1. 数控机床直线电机进给伺服系统概述随着科技的不断发展,数控机床在工业生产中扮演着越来越重要的角色。
为了提高数控机床的加工精度和效率,近年多的研究者开始关注直线电机进给伺服系统的研究与应用。
直线电机进给伺服系统是一种采用直线电机作为驱动源的高精度、高速度、高可靠性的伺服系统,广泛应用于数控机床、机器人、自动化生产线等领域。
直线电机进给伺服系统具有很多优点,如结构简单、体积小、重量轻、响应速度快、转矩大等。
这些优点使得直线电机进给伺服系统在数控机床中的应用越来越广泛。
由于直线电机本身的特点以及伺服系统的复杂性,对其进行动态特性分析与研究具有很大的挑战性。
本文将对数控机床直线电机进给伺服系统的动态特性进行深入研究,以期为实际应用提供理论依据和技术支撑。
1.1 研究背景随着现代制造业的快速发展,数控机床在各个领域的应用越来越广泛。
数控机床的性能和精度对于提高产品质量、降低生产成本具有重要意义。
直线电机进给伺服系统作为数控机床的关键部件之一,其动态特性直接影响到数控机床的加工精度、速度和稳定性。
研究数控机床直线电机进给伺服系统的动态特性,对于提高数控机床的整体性能具有重要的现实意义。
传统的数控机床进给伺服系统主要采用步进电机驱动,虽然在一定程度上满足了加工需求,但其动态特性较差,如速度响应慢、加速度范围窄、负载能力有限等。
这些问题限制了数控机床在高速、高精度加工方面的应用。
随着直线电机技术的不断发展,直线电机进给伺服系统逐渐成为数控机床领域的研究热点。
直线电机具有功率密度高、加速度响应快、速度快、转矩大等优点,可以有效提高数控机床的性能。
由于直线电机进给伺服系统涉及到多个学科领域,如电机学、控制理论、机械设计等,因此对其动态特性的研究具有较高的难度。
本论文旨在对数控机床直线电机进给伺服系统的动态特性进行分析与研究,以期为提高数控机床的性能和稳定性提供理论依据。
数控车床主轴单元动特性分析

数控车床主轴单元动特性分析
刘晶;虎恩典
【期刊名称】《宁夏工程技术》
【年(卷),期】2003(002)001
【摘要】在对某型数控车床进行切削动态试验的基础上,建立了机床主轴组件的有限元动力学模型,并对主轴单元的动特性进行了计算和分析,提出了改进意见.文中有限元计算结果与试验数据的误差小于5%.
【总页数】2页(P43-44)
【作者】刘晶;虎恩典
【作者单位】宁夏大学,机械工程系,宁夏,银川,750021;宁夏大学,机械工程系,宁夏,银川,750021
【正文语种】中文
【中图分类】TH502
【相关文献】
1.数控管螺纹车床主轴单元动态特性分析 [J], 杨威;张伟;李运生
2.数控机床主轴单元基本动特性的研究与预测 [J], 赵相松;徐燕申
3.数控智能车床主轴液压变挡控制及典型故障分析 [J], 张秀印
4.数控车床主轴单元结构节能性优化设计 [J], 何吉祥;李聪波;吕岩;李娟
5.数控车床主轴系统热特性分析与验证 [J], 陈维范;薛丹
因版权原因,仅展示原文概要,查看原文内容请购买。
关于数控机床模态分析的综述

关于数控机床模态分析的综述数控机床模态分析是一种对数控机床进行动态特性分析和优化的方法。
模态分析可以帮助工程师了解和改进机床的刚性、自振频率、模态阻尼等参数,以提高机床的加工精度和稳定性。
数控机床模态分析方法包括理论分析、有限元分析和实验测试等。
理论分析是利用工程力学理论和振动理论推导机床的自振频率和振型分布等参数。
有限元分析则是将机床建模为有限元模型,通过有限元软件计算模态参数。
实验测试方法通常需要用到加速度传感器、传动器和数据采集系统等设备进行振动信号采集和分析。
数控机床模态分析可以揭示机床的动态性能问题,指导机床的设计和改进。
通过模态分析,可以方便地了解机床各模态的自振频率、振型和消能能力,从而为机床的优化设计提供参考。
此外,模态分析还可用于检验机床的加工稳定性和动态刚性情况,评估机床的工作性能。
数控机床模态分析的应用范围非常广泛。
首先,在机床的设计阶段,模态分析可以帮助工程师了解机床的固有频率,并对其激振频率进行避免和设计。
其次,在机床的改进和优化过程中,模态分析可以帮助确定改进措施、指导改进方向,提高机床的精度和稳定性。
再次,在机床故障诊断和维护中,模态分析可以用于检测机床的振动异常情况,快速定位故障和精确定位问题所在。
然而,数控机床模态分析仍然存在一些挑战和局限性。
首先,模态分析涉及到大量的振动信号采集和分析,需要专业的设备和技术支持。
其次,机床的振动特性受到多种因素影响,如机床结构、切削过程、刀具、工件材料等。
因此,模态分析结果需要结合实际情况进行综合分析和判断。
最后,随着机床的不断更新和演变,模态分析方法和技术需要不断发展和改进,以适应新型机床的需求。
总的来说,数控机床模态分析是一种重要的机床动态性能分析方法,可以为机床的设计、改进和维护提供有力的支持。
随着模态分析技术的不断发展,相信它会在数控机床行业中得到越来越广泛的应用。
数控机床伺服系统动态特性的理论分析与仿真研究
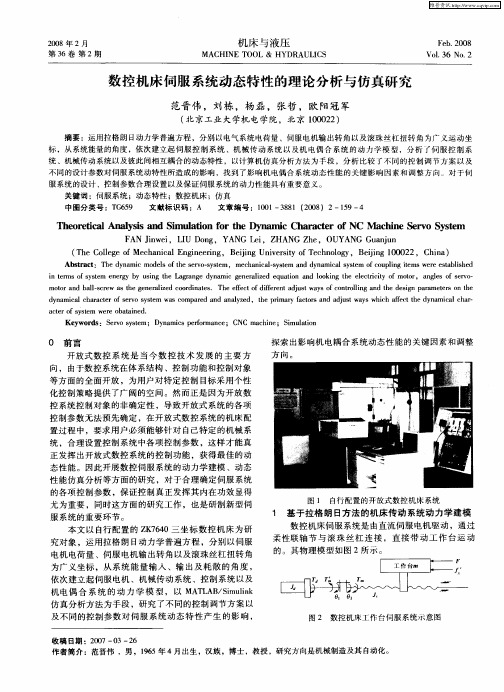
20 0 8年 2月
机 床 与 液 压
MACHI NE TOOL & HYDRAUL CS I
Fe . 0 8 b 20 Vo. 6 No 2 13 .
第3 6卷 第 2期
数 控 机床 伺 服 系统 动态 特 性 的 理论 分 析 与 仿真 研 究
范晋伟 ,刘栋 ,杨磊 ,张哲 ,欧 阳冠 军
( 北京 工业 大 学机 电学 院 ,北京 10 2 ) 00 2
摘要 :运用拉格 朗 日动力学普遍方 程 ,分别 以电气 系统 电荷 量 、伺服电机输 出转角 以及滚珠 丝杠扭转 角 为广 义运动坐 标 ,从系统能量的角度 ,依次建立起 伺服 控制 系统 、机械 传动 系统 以 及机 电偶 合 系统 的动力 学模 型 ,分析 r伺 服控 制 系
F NJ w i I og A i e ,LU D n ,YA G L i HA G Z e U A G G ajn n N e,Z N h ,O Y N unu ( h o eeo ca ia E gn eig e igU iesyo e h o g ,B in 0 0 2 T eC l g f l Meh ncl n ier ,B in nvr t f c nl y e ig10 2 ,C ia n j i T o j hn )
at f yt eeoa ie . c r s m w r btn d eos e a
Ke w o ds: S r o s se ; Dy mis p ro a c y r e v y tm na c e f r n e; CNC ma hi m c ne; Si u ain m lto
0 前 言
探索 出影 响机 电耦合系统动态性能 的关键 因素和调整
- 1、下载文档前请自行甄别文档内容的完整性,平台不提供额外的编辑、内容补充、找答案等附加服务。
- 2、"仅部分预览"的文档,不可在线预览部分如存在完整性等问题,可反馈申请退款(可完整预览的文档不适用该条件!)。
- 3、如文档侵犯您的权益,请联系客服反馈,我们会尽快为您处理(人工客服工作时间:9:00-18:30)。
数控机床的动态特性概述李凯旋研究机床动态特性的重要性和必要性现代机床正向高速,大功率,高精度的方向发展,除了要求机床重量轻,成本低,使用方便和具有良好的工艺性能外,对机床的加工性能要求也愈来愈高。
机床的加工性能与其动态特性紧密相关。
由于受到理论分析和测试实验手段落后的限制,传统的机床设计的主要依据是静刚度和静强度,对机床的动态特性考虑较少。
结果常常是以较大的安全系数加强机床结构。
导致机床结构尺寸和重量加大。
并不能从根本上改观机床的动态特性。
机床的动态特性的基本概念机床的动态性能是指机床运转之后振动、噪声、热变形与磨损等性能的总称。
但长期以来主要指的是机床的振动性能,即主要指机床抵抗振动的能力。
【1】⎪⎪⎪⎪⎩⎪⎪⎪⎪⎨⎧===振型)振型(一阶振型,二阶变形大小)动态柔度变形的能力。
动刚度:动载荷下抵抗变形的能力。
静刚度:静载荷下抵抗为临界阻尼系数为阻尼系数,阻尼比)(固有角频率固有频率(/1r r ,r/r 2/f f co co n n n n d k ωξπωω机床结构的动态特性参数主要参数包括固有频率,阻尼比,振型,动刚度等。
机床的动态分析主要是研究抵抗振动的能力,包括抗振性和切削稳定性,【2】⎪⎪⎩⎪⎪⎨⎧⎪⎩⎪⎨⎧切削自激振的能力)切削稳定性(机床抵抗主要零件的固有频率阻尼特性机床的结构刚度振动的能力)抗振性(机床抵抗受迫激振力:由回转的不平衡质量作为振动系统的振动源产生的周期性简谐振动。
【1】诸乃雄,机床动态设计原理与应用[M]上海:同济大学出版社,1987:1-3【2】陈雪瑞,金属切削机床设计[ M ] 太原: 山西科学教育出版社, 1988.147-151主要指标外力的激励频率与物体的固有频率相等时,物体的振动形态成为主振型或一阶振型。
外力的激励频率是物体固有频率二倍时,物体的振动形态为二阶振型,以此类推.......机床的动态特性基本概念抗振性的衡量标准一般用产生单位振动量所需要的激振力表示。
切削稳定性的衡量标准一般用切削时开始出现自激振动的极限切削宽度来表示。
极限切削宽度越大,切削稳定性越好。
机床的振动类型及消除措施⎪⎪⎪⎪⎩⎪⎪⎪⎪⎨⎧⎪⎩⎪⎨⎧⎪⎩⎪⎨⎧)的频率自激振动(外部激振力平衡导致)受迫振动(旋转体的不的固有频率)自由振动(频率为系统产生振动的原因机床零部件整体振动动部件结合面间的相对振整机摇晃振动特性分类振动类型机床动态特性的基本概念1,消除受迫振动的方法主要有:采用隔振措施合理提高机床的动刚度,使受迫振动的频率与系统的固有频率远离。
2,自激振动与切削相关,切削用量愈大,切削力愈大,自激振动愈剧烈。
方法:改变切削条件,找出机床的主振型及引起该主振型的薄弱环节,通过增强机床的动刚度或采取减振措施。
可见提高机床的动刚度非常重要!下面是提高机床动刚度的措施⎪⎪⎪⎪⎪⎪⎪⎩⎪⎪⎪⎪⎪⎪⎪⎨⎧⎪⎩⎪⎨⎧⎪⎩⎪⎨⎧切削力方向)尽量使振动方向垂直于变更振型的振动方向(涂层在支承件表面采用阻尼内的空腔尼材料填充机床支承件采用泥芯和混凝土等阻阻尼利用好结合面间的摩擦性改善机床结构的阻尼特基联接处的刚度改善构件间或构件与地筋条合理布置构件的筋板和状及尺寸合理设计构件的断面形和固有频率提高机床构件的静刚度321321机床动态特性的基本概念小结:现阶段,研究机床动态特性及确定机床动刚度的方法主要是通过对实际机床或模型作激振试验,采用正弦信号,随机信号,脉冲信号和非周期信号,根据不同的输入信号方式,采用不同的分析,测量方法。
通过实验,找到影响动刚度的薄弱环节,提出改进措施,以改进结构设计,或安装有效的减振装置,从而达到提高机床的动刚度,使机床有较合适的动态特性的目的。
机床动态特性的研究内容机床动态特性的研究包括动力分析和动力设计两部分。
⎪⎪⎪⎩⎪⎪⎪⎨⎧⎩⎨⎧)条件,跟自激振动有关切削颤振和爬行的临界动力稳定性(确定产生一定范围内振力的动力响应控制在动力响应(将受到的激比值)模态振型(两个振幅的各阶固有频率固有特性(复杂系统)动力分析)1,动力分析指在已知系统的动力模型,外部激励和系统工作条件的基础上分析研究系统的动态特性。
包括固有特性,动力响应,动力稳定性三方面。
【3】2,自激振动:振动系统在一定的条件和运转状态下,可能产生自激振动。
自激振动主要由系统本身的动力特性所决定的振动,产生自激振动的系统称为不稳定系统。
例如,机床在一定的切削条件下,可能产生切削颤振;低速相对运动在一定条件下,有可能产生爬行现象。
【3】杜君文,机械制造技术装备及设计[M]天津:天津大学出版社1998,222一224机床动态特性的研究内容对机床结构进行动力分析有两种手段:1.对机床结构的动力学模型进行理论分析。
2对机床结构进行动态测试。
【4】手段1优点:可获得机床的各种动力特性和动力分析所需的数据,还可获得表示该机床机构偏离最优化涉及到何种程度的指标,对哪些部件改进,如何具体改进,并且改进后的效果也可以估计出来。
缺点:由于机床结果十分复杂,不确定因素很多,有些问题从理论到实践还未得到解决,在研发过程中,完全依赖理论分析无法满足实际要求。
动态测试主要应用激振响应法测定结构的动态特性,包括各阶固有频率,各阶主模态振型,结构上有关点的动柔度频率响应等,应用这些数据进行分析,找出机床结构的薄弱环节,加以改进。
不足:动态测试只能定型的指出改进设计的方向,不能定量确定结构改进的程度,改进设计效果也需要等到新机床制造出来后进行试验才知道。
【4】王世军,黄玉美.机床整机特性的有限元分析方法[J].机床与液压,2005( 3) :20-22.机床动态特性的研究内容机床的动态设计机床的动态设计指的是机床的动态性能在其图纸设计阶段就能得到预测和优化,从而寻求一种经济合理的结构,使其动态性能满足预先给定的设计要求。
包括:CAD/CAE,计算机图形学,振动理论,有限元,振动测试技术等。
【5】满足要求修改动力学模型检验是否满足要求)对系统动态特性仿真建立动力学模型设计要求→⇔→→→→(机床动态设计的一般过程动力分析为动力学的“正”问题,动态设计为动力学的“逆”问题。
动态设计师比动力分析更为复杂的问题,尽管理论上已经提出了一些动态设计的方法,但目前大多数仍将动态设计问题转化为动力分析问题来处理。
目前针对机床一般的动态设计大多根据经验和各方面的设计要求拟出原始的方案进而逐步展开的。
【5】王富强,精密机床床身的动态特性分析与优化[D].兰州;兰州理工大学2007,06-29机床动态特性的研究内容动态设计的基本原则动态设计的目标是在保证机械系统满足其功能要求的条件下具有良好的动态性能,使其经济合理、运转平稳、可靠。
因此,必须把握机械结构的固有频率、振型和阻尼比,通过动态分析找出系统的薄弱环节来改进设计。
动态设计的原则是:(1) 防止共振;(2) 尽量减小机器振动幅度;(3) 尽量增加结构各阶模态刚度,并且最好接近相等;(4) 尽量提高结构各阶模态阻尼比;(5) 避免零件疲劳破坏;(6) 提高系统振动稳定性,避免失稳。
具体设计时,以上述为基本原则,应根据具体设备的要求,给出动态设计指标。
机床动态特性的研究内容模态分析相关概念模态分析是研究机构动力特性的一种近代特性方法。
模态是机械结构的固有振动特性。
每一个模态具有特定的固有频率,阻尼比和模态振型。
这些模态参数可由计算或试验分析取得,其过程为模态分析。
分析过程由有限元方法得出,称之为计算模态分析。
若通过试验将采集的系统输入与输出信号经过参数识别获得,则为试验模态分析。
模态参数有:模态频率、模态质量、模态向量、模态刚度和模态阻尼等模态分析的应用:1评价现有结构系统的动态特性。
2在新产品设计中进行结构动态特性的预估和优化设计。
机床动态特性的研究内容⎪⎩⎪⎨⎧合建模)二者相结合的方法(综实验建模及其分析方法阵分析法)(主要采用有限元法矩理论建模及其分析方法1,理论建模及其分析方法是基于结构动力学原理,根据结构的设计方案,图纸和资料等建立起来模拟机床动态特性的的有限元动力模型而无需依赖已有的机械设备。
优点:可经济迅速地达到优化设计的目标,把提高机床的动态特性的问题解决在方案及图纸设计阶段。
缺点:误差大。
2,实验建模又称为系统辨识,对机械系统(实物或模型)进行激振(输入),通过观测到的系统的输入,输出数据,对系统确定一个一个数学模型,使这个数学模型尽可能精确地放反映系统的动态特性。
优点:模型及其动态特性对机床模拟精度都较高。
缺点:投资大,动态试验及信号分析数据处理过程中都要受到各种随机噪声的干扰,测试仪器误差,各种信号误差,从而给动态性能带来一定误差。
3,综合建模将有限元分析技术和模态分析技术有机的结合起来,发挥各自的长处,以得到能确切反映实际,实用的动态特性分析技术。
机床动态特性的研究现状机床的动态特性研究主要包括机床分部件和整机的动态特性分析。
整机的动态特性又是与分部件的动态特性和结合面的动态特性相关的。
国外研究现状国外的机床动态分析和动态设计领域的研究较多,并在结构优化设计方面取得了很多的成绩。
特点如下:【6】(1)设计与分析平行。
机床结构设计的各个阶段均有结构分析参与,并且贯穿整个设计过程。
这样确定的机床结构设计方案,基本就是定型方案。
(2)结构优化的思想被用于设计的各个阶段。
(3)大量的虚拟试验代替实物实验。
国内研究现状国内对机床的动态特性研究可按整机分析和部件分析两个方面归纳如下(1)机床整机的研究现状,在整机建模与分析方面,上交,天大等院校都有一定的研究,提出了整机动态特性预测的方法及相关软件的研发。
eg:1福州大学林有希提出整机有限元法,利用静态凝聚法和结构技术,大幅度缩减自由度对整机进行建模。
【6】杨永亮.基于有限元的车床床身结构优化:[D]. 大连:大连理工大学机械系,2006,1-3机床动态特性的研究现状2上海交通大学张广鹏等运用均质梁,集中力量及结合部单元进行了整机预测软件包的研制。
3东南大学毛海军等利用阻抗匹配法建立了磨床整机的动力学模型,并进行了实验验证。
4昆明理工大学杜奕利用试验模态技术,对MSY7115平面磨床整机结构的动态特性进行了模态分析,并建立了立柱和整机的有限元模型,并对其进行了动态特性优化的改进设计。
梁志强采用理论建模和试验建模相结合的方法研究TH6350加工中心整机的动态特性。
5北京机床研究所赵宏林等利用自行开发的机床整机特性分析软件包--ANTPOS 软件包对一台立式加工中心实现了在图纸阶段预测其整机综合特性的目的,并与试验值进行了比较。
6北京理工大学采用用户自定义矩阵单元处理机床结合部的接触问题,利用I-DEAS Master Series 划分有限元网络,主要采用二维壳单元建立了立式加工中心的动力学模型,并进行了动态特性分析。