缩孔_缩松--缺陷位置
铸件缩孔、缩松有何区别?如何解决?

铸件缩孔、缩松有何区别?如何解决?在铸造⽣产中,铸件⽓孔和铸件缩孔有时是伴⽣的,有时是独⽴存在。
当出现⽓孔和缩孔时,我们要快速的判断出缺陷是⽓孔还是缩孔对于解决问题⼗分必要。
⽓孔类缺陷与防治⽅法在铸造⽣产中,孔洞类缺陷是常见缺陷,也是给铸造⼚造成损失⽐较⼤的缺陷之⼀。
孔洞类缺陷分为⽓孔和缩孔。
⽓孔多为由于⾦属液中侵⼊、裹⼊、卷⼊⽓体所⾄。
铸件⽓孔出现在铸件上的位置不同,其产⽣的原因也不同。
这就要求我们的铸造技术员在判断⽓孔缺陷病因时,要掌握各类⽓孔发⽣的原理,具有什么样的特征。
只有如此才能对症下药,将出现的⽓孔缺陷解决掉。
⽓孔特征:(1)卷⼊⽓孔:⾦属液在充型过程中因卷⼊⽓体⽽在铸件内形成⽓孔,多呈孤⽴存在的圆形或椭圆形⼤⽓孔,位置不固定,⼀般偏铸件中上部。
(2)侵⼊⽓孔:由型、芯、涂料、芯撑、冷铁产⽣的⽓孔侵⼊铸件表层⽽形成⽓孔,多呈梨形或椭圆形,尺⼨较⼤,孔壁光滑,表⾯多呈氧化⾊。
(3)反应⽓孔:由⾦属液内部某些成分之间或⾦属液与型、芯在界⾯上发⽣化学反应⽽形成群分布的⽓孔。
位于铸件表层的针头形或腰圆形反应⽓孔称为表⾯针孔与⽪下⽓孔,由⾦属液与型、芯涂料发⽣界⾯反应所⾄;分散或成群分布在铸件整个断⾯上或某个局部区域的针头反应⽓孔。
形成原因:(1)由于炉料潮湿、锈蚀、油污、⽓候的潮湿,熔练⼯具和浇包未烘⼲,⾦属液成分不当,合⾦液为精炼与精炼不⾜,使⾦属液中含有⼤量⽓体或⽓体物质,导致在铸件中析出⽓孔或反应⽓孔。
(2)型、芯未充分烘⼲,透⽓性差,通⽓不良,含⽔分和发⽓物质过多,涂料未烘⼲或含发⽓成分过多,冷铁、芯撑有锈斑、油污或未烘⼲,⾦属型排⽓不良,在铸件中形成侵⼊⽓孔。
(3)浇注系统不合理,浇注和充型速度过快,⾦属型排⽓不良,使⾦属液在浇注和充型过程中产⽣紊流、涡流或断流⽽卷⼊⽓体,在铸件中形成卷⼊性⽓孔。
(4)合⾦液易可吸⽓,在熔炼和浇注过程中未采取有效的精炼、保护和净化措施,使⾦属液中含有⼤量⽓体、夹渣和夹⽓成分,在充型和凝固过程中形成析出⽓孔和反应⽓孔。
铸件外观缺陷图

铸件常见缺陷常见缺陷缺陷的分类:铸件常见缺陷分为孔眼、裂纹、表面缺陷、残缺类缺陷、形状及尺寸和重量不合格、成份及组织和性能不合格六大类。
1孔眼类缺陷孔眼类缺陷包括气孔、缩孔、缩松、渣眼、砂眼、等。
1.1.1气孔:别名气眼,气泡、由气体原因造成的孔洞。
铸件气孔的特征是:其表面一般比较光滑,主要呈梨形\圆形和椭圆形.一般在铸件表面露出,大孔常孤立存在,小孔则成群出现。
(如图)产生的原因是:来源于气体,炉料潮湿或绣蚀、表面不干净、炉气中水蒸气等气体、炉体及浇包等修后未烘干、型腔内的气体、浇注系统不当,浇铸时卷入气体、铸型等。
1.1.2缩孔缩孔别名缩眼,由收缩造成的孔洞。
缩孔的特征是:形状不规则,孔壁粗糙并带有技状晶,常出现在铸件最后凝固的部位,广义的缩孔包括缩松。
(如图)产生的原因是:金属在液体及凝固期间由于补缩不良而产生的孔洞,主要有以下几点:铸件结构设计不合理,浇铸系统不适当,冷铁的大小、数量、位置不符实际、铁水化学成份不符合要求,如含磷过高等。
浇注温度过高浇注速度过快等。
1.1.3缩松缩松别名疏松、针孔蜂窝、由收缩耐造成的小而多的孔洞。
缩松的特征是:铸件断面上出现的分散而细小的缩孔.助高倍放大镜才能发现的缩松称为显微缩松,铸件有缩松的部位,在气密性实验时易渗漏。
(如图)产生的原因同以上缩孔。
1.1.4渣眼渣眼别名夹渣、包渣、脏眼、铁水温度不高、浇注挡渣不当造成。
渣眼的特征是:铸件浇注位置上表面的非金属夹杂物。
通常在加工后发现与气孔并存,孔径大小不一,成群集结。
(如图)产生的原因是:铁水纯净度差、除渣不净、浇注时挡渣不好,浇注系统挡渣作用差、浇注时浇口未充满或断流。
1.1.5砂眼砂眼是夹着砂子的砂眼。
砂眼的特征是:铸件内部或表面带有砂粒的孔洞(如图)。
产生的原因是:型砂损坏脱落,型腔内的散砂或砂块未清除干净、型砂紧实度差、浇注时冲坏型芯、浇注系统设计不当、型芯表面涂料不好等。
1.1.6铁豆铁豆是夹着铁珠的孔眼、别名铁珠、豆眼、铁豆砂眼等。
复习第四章铸件凝固过程缩孔、缩松的预测
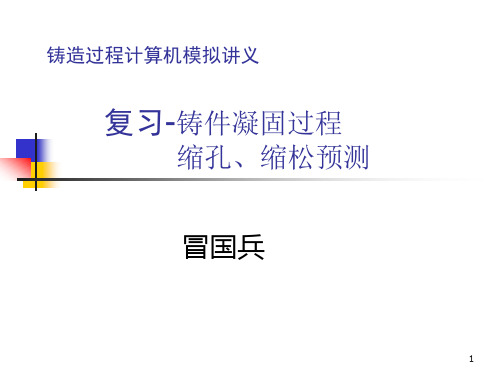
( 平均渗透率) ( 平均液相率)
g Li + g Lj 2
∆ L - i , j 单元的节点间距。
13
第一节 收缩缺陷预测方法及判据
然后在各个流导值中取最大者为单元 的流导 然后在各个流导值中取最大者为单元i的流导,即: 在各个流导值中取最大者为单元 的流导,
K
d
= max(
k
µ g L ⋅∆L
铸造过程计算机模拟讲义
复习-铸件凝固过程
缩孔、缩松预测 冒国兵
1
内容 1、收缩缺陷预测方法及判据 、 (1)等温曲线法 ) (2)温度梯度法 ) (3)流导法 ) (4)G ⋅ τ f ) (5)新山英辅(NiYama)判据 )新山英辅( ) 2、铸件凝固过程数值模拟工程应用 、
2
第一节 收缩缺陷预测方法及判据
∆p =
µg L ∆x
K
⋅V
11
第一节 收缩缺陷预测方法及判据
µg L∆x
即可视为流动阻力,据此可将流导 上式系数 即可视为流动阻力,据此可将流导 K Kd定义为流动阻力的倒数,即: 定义为流动阻力的倒数,
K Kd = µg L ∆x
K-渗透率;gL-体积液相率;µ-动力粘度。 -渗透率; 体积液相率; -动力粘度。 (2)数值模拟中流导的应用 )
6
第一节 收缩缺陷预测方法及判据
2 、温度梯度法 铸件在凝固过程中存在着朝向冒口的补缩通道, 铸件在凝固过程中存在着朝向冒口的补缩通道,但 温度梯度大,补缩通道的扩张就大, 在(a)中,温度梯度大,补缩通道的扩张就大,补缩就 ) 充分。 因温度梯度小,虽也存在补缩通道, 充分。而(b)中,因温度梯度小,虽也存在补缩通道, ) 但补缩就很困难,冒口无法发挥补缩作用。如图1-2所示。 但补缩就很困难,冒口无法发挥补缩作用。如图 所示。 所示
3.2.2 缩孔、缩松的形成及防止方法

缩孔、缩松的形成及防止方法副教授:陈云铸件中的缩孔与缩松液态金属在铸型内凝固过程中,由于液态收缩和凝固收缩导致体积缩小,若其收缩得不到补充,就在铸件最后凝固的部分形成孔洞。
大而集中的孔洞称为缩孔,细小而分散的孔洞称为缩松。
(a)铝合金缩孔、缩松(b)金相显微镜下缩松(c)扫描电镜下缩松一、缩孔的形成纯金属、共晶成分和凝固温度范围窄的合金,浇注后在型腔内是由表及里的逐层凝固。
在凝固过程中,如得不到合金液的补充,在铸件最后凝固的地方就会产生缩孔。
缩孔形成的条件:铸件呈逐层凝固方式凝固,成分为纯金属或共晶成分的合金。
缩孔产生的基本原因:是合金的液态收缩和凝固收缩值大于固态收缩值,且得不到补偿。
缩孔产生的部位在铸件最后凝固区域,如壁较厚大的上部或铸件两壁相交处,这些地方称为热节。
热节位置可用画内接圆的方法确定。
用画内切圆法确定缩孔位置二、缩松的形成铸件最后凝固的收缩未能得到补充,或者结晶温度范围宽的合金呈糊状凝固,凝固区域较宽,液、固两相共存,树枝晶发达,枝晶骨架将合金液分割开的小液体区难以得到补缩所致。
缩松形成的条件:铸件主要呈糊状凝固方式凝固,成分为非共晶成分或有较宽结晶温度范围的合金。
形成缩松的基本原因:是合金的液态收缩和凝固收缩值大于固态收缩值。
缩松一般出现在铸件壁的轴线区域、冒口根部、热节处,也常分布在集中缩孔的下方。
三、影响缩孔和缩松形成的因素1、合金成分结晶温度范围越小的合金,产生缩孔的倾向越大;结晶温度范围越大的合金,产生缩松的倾向越大。
铁碳合金成分和体积收缩的关系V总—总体积收缩容积;V孔—缩孔容积;V松—缩松容积2、浇注条件提高浇注温度时,合金的总体积收缩和缩孔倾向增大。
浇注速度很慢或向冒口中不断补浇高温合金液,使铸件液态和凝固收缩及时得到补偿,铸件总体积收缩减小,缩孔容积也减小。
V 总—总体积收缩容积;V 孔—缩孔容积;V 松—缩松容积铁碳合金成分和体积收缩的关系3、铸型材料铸型材料对铸件冷却速度影响很大 。
(推荐)铸件外观缺陷图

铸件常见缺陷常见缺陷缺陷的分类:铸件常见缺陷分为孔眼、裂纹、表面缺陷、残缺类缺陷、形状及尺寸和重量不合格、成份及组织和性能不合格六大类。
1孔眼类缺陷孔眼类缺陷包括气孔、缩孔、缩松、渣眼、砂眼、等。
1.1.1气孔:别名气眼,气泡、由气体原因造成的孔洞。
铸件气孔的特征是:其表面一般比较光滑,主要呈梨形\圆形和椭圆形.一般在铸件表面露出,大孔常孤立存在,小孔则成群出现。
(如图)产生的原因是:来源于气体,炉料潮湿或绣蚀、表面不干净、炉气中水蒸气等气体、炉体及浇包等修后未烘干、型腔内的气体、浇注系统不当,浇铸时卷入气体、铸型等。
1.1.2缩孔缩孔别名缩眼,由收缩造成的孔洞。
缩孔的特征是:形状不规则,孔壁粗糙并带有技状晶,常出现在铸件最后凝固的部位,广义的缩孔包括缩松。
(如图)产生的原因是:金属在液体及凝固期间由于补缩不良而产生的孔洞,主要有以下几点:铸件结构设计不合理,浇铸系统不适当,冷铁的大小、数量、位置不符实际、铁水化学成份不符合要求,如含磷过高等。
浇注温度过高浇注速度过快等。
1.1.3缩松缩松别名疏松、针孔蜂窝、由收缩耐造成的小而多的孔洞。
缩松的特征是:铸件断面上出现的分散而细小的缩孔.助高倍放大镜才能发现的缩松称为显微缩松,铸件有缩松的部位,在气密性实验时易渗漏。
(如图)产生的原因同以上缩孔。
1.1.4渣眼渣眼别名夹渣、包渣、脏眼、铁水温度不高、浇注挡渣不当造成。
渣眼的特征是:铸件浇注位置上表面的非金属夹杂物。
通常在加工后发现与气孔并存,孔径大小不一,成群集结。
(如图)产生的原因是:铁水纯净度差、除渣不净、浇注时挡渣不好,浇注系统挡渣作用差、浇注时浇口未充满或断流。
1.1.5砂眼砂眼是夹着砂子的砂眼。
砂眼的特征是:铸件内部或表面带有砂粒的孔洞(如图)。
产生的原因是:型砂损坏脱落,型腔内的散砂或砂块未清除干净、型砂紧实度差、浇注时冲坏型芯、浇注系统设计不当、型芯表面涂料不好等。
1.1.6铁豆铁豆是夹着铁珠的孔眼、别名铁珠、豆眼、铁豆砂眼等。
3.2.2 缩孔、缩松的形成及防止方法

缩孔、缩松的形成及防止方法副教授:陈云铸件中的缩孔与缩松液态金属在铸型内凝固过程中,由于液态收缩和凝固收缩导致体积缩小,若其收缩得不到补充,就在铸件最后凝固的部分形成孔洞。
大而集中的孔洞称为缩孔,细小而分散的孔洞称为缩松。
(a)铝合金缩孔、缩松(b)金相显微镜下缩松(c)扫描电镜下缩松一、缩孔的形成纯金属、共晶成分和凝固温度范围窄的合金,浇注后在型腔内是由表及里的逐层凝固。
在凝固过程中,如得不到合金液的补充,在铸件最后凝固的地方就会产生缩孔。
缩孔形成的条件:铸件呈逐层凝固方式凝固,成分为纯金属或共晶成分的合金。
缩孔产生的基本原因:是合金的液态收缩和凝固收缩值大于固态收缩值,且得不到补偿。
缩孔产生的部位在铸件最后凝固区域,如壁较厚大的上部或铸件两壁相交处,这些地方称为热节。
热节位置可用画内接圆的方法确定。
用画内切圆法确定缩孔位置二、缩松的形成铸件最后凝固的收缩未能得到补充,或者结晶温度范围宽的合金呈糊状凝固,凝固区域较宽,液、固两相共存,树枝晶发达,枝晶骨架将合金液分割开的小液体区难以得到补缩所致。
缩松形成的条件:铸件主要呈糊状凝固方式凝固,成分为非共晶成分或有较宽结晶温度范围的合金。
形成缩松的基本原因:是合金的液态收缩和凝固收缩值大于固态收缩值。
缩松一般出现在铸件壁的轴线区域、冒口根部、热节处,也常分布在集中缩孔的下方。
三、影响缩孔和缩松形成的因素1、合金成分结晶温度范围越小的合金,产生缩孔的倾向越大;结晶温度范围越大的合金,产生缩松的倾向越大。
铁碳合金成分和体积收缩的关系V总—总体积收缩容积;V孔—缩孔容积;V松—缩松容积2、浇注条件提高浇注温度时,合金的总体积收缩和缩孔倾向增大。
浇注速度很慢或向冒口中不断补浇高温合金液,使铸件液态和凝固收缩及时得到补偿,铸件总体积收缩减小,缩孔容积也减小。
V 总—总体积收缩容积;V 孔—缩孔容积;V 松—缩松容积铁碳合金成分和体积收缩的关系3、铸型材料铸型材料对铸件冷却速度影响很大 。
焊接缩孔与缩松的机理及因素及防止措施
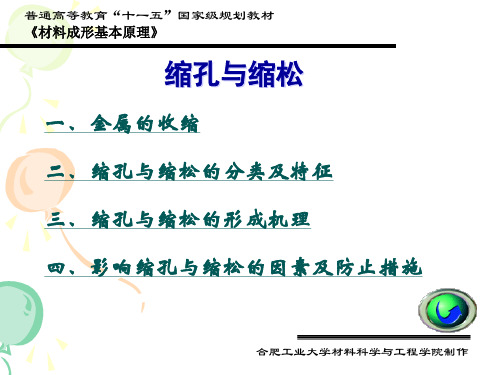
合肥工业大学材料科学与工程学院制作
普通高等教育“十一五”国家级规划教材 《材料成形基本原理》
温度 /℃ 温度 温度 m = ( 100 % n ( T ) L S ) V( LS) 0 L S V 液 V 液 浇 V 凝 S 固 V ( L V 固 /℃ /℃
合肥工业大学材料科学与工程学院制作
普通高等教育“十一五”国家级规划教材 《材料成形基本原理》
a)明缩孔
b)凹角缩孔
c)芯面缩孔
d)内部缩孔
合肥工业大学材料科学与工程学院制作
普通高等教育“十一五”国家级规划教材 《材料成形基本原理》
缩 孔 特 点
常出现于纯金属、共晶成分合金和结晶温度范围 较窄的以层状凝固方式凝固的铸造合金中; 多集中在铸件的上部和最后凝固的部位;铸件厚 壁处、两壁相交处及内浇口附近等凝固较晚或凝 固缓慢的部位(称为热节),也常出现缩孔; 缩孔尺寸较大,形状不规则,表面不光滑。
金属从浇注温度冷却到室温所产生的体收缩为液
态收缩、凝固收缩和固态收缩之和,即:
εV总=εV液+εV凝+εV固
其中,液态收缩和凝固收缩是铸件产生缩孔
和缩松的基本原因 。而固相收缩对应力、变形
与裂纹影响较大。
合肥工业大学材料科学与工程学院制作
普通高等教育“十一五”国家级规划教材 《材料成形基本原理》
二、缩孔与缩松的分类及特征 缩孔 缩松
普通高等教育“十一五”国家级规划教材 《材料成形基本原理》
(一)影响缩孔与缩松的因素
金属的性质 铸型的冷却能力 (收缩系数α大) (蓄热系数b小)
浇注温度与浇注速度 (高,快) 铸件尺寸 补缩能力 (大) (弱)
例:铸铁的缩孔、缩松倾向
铸铁件缩松、缩孔、凹陷缺陷的原因分析与防止方法
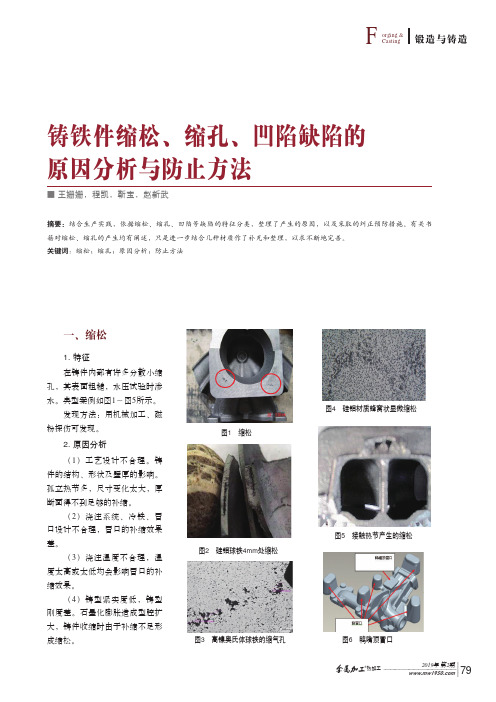
2019年第2期热加工79F锻造与铸造orging &Casting铸铁件缩松、缩孔、凹陷缺陷的原因分析与防止方法■王姗姗,程凯,靳宝,赵新武摘要:结合生产实践,依据缩松、缩孔、凹陷等缺陷的特征分类,整理了产生的原因,以及采取的纠正预防措施。
有关书籍对缩松、缩孔的产生均有阐述,只是进一步结合几种材质作了补充和整理,以求不断地完善。
关键词:缩松;缩孔;原因分析;防止方法一、缩松1. 特征在铸件内部有许多分散小缩孔,其表面粗糙,水压试验时渗水。
典型案例如图1~图5所示。
发现方法:用机械加工、磁粉探伤可发现。
2. 原因分析(1)工艺设计不合理。
铸件的结构、形状及壁厚的影响。
孤立热节多,尺寸变化太大,厚断面得不到足够的补缩。
(2)浇注系统、冷铁、冒口设计不合理,冒口的补缩效果差。
(3)浇注温度不合理,温度太高或太低均会影响冒口的补缩效果。
(4)铸型紧实度低,铸型刚度差。
石墨化膨胀造成型腔扩大,铸件收缩时由于补缩不足形成缩松。
图1 缩松图2 硅钼球铁4mm处缩松图4 硅钼材质蜂窝状显微缩松图3 高镍奥氏体球铁的缩气孔图5 接触热节产生的缩松图6 鸭嘴顶冒口2019年 第2期 热加工80F锻造与铸造orging &Casting(5)碳、硅含量低,磷含量较高;凝固区间大。
硅钼和高镍球墨铸铁对碳、硅含量和氧化铁液的敏感性特大,铁液严重氧化或碳、硅量低时,易出现显微缩松。
即便在薄壁处也容易出现缩松(见图2、图3、图4)。
(6)孕育不充分,石墨化效果差。
(7)残余镁量和稀土量过高。
钼含量较高时也会增加显微缩松。
(8)浇注速度太快。
(9)炉料锈蚀,氧化铁多。
(10)铁液在电炉内高温停放时间太长,俗称“死铁水”,造成严重氧化。
(11)冲天炉熔炼时底焦太底,风量太大,元素烧损大,铁液严重氧化。
(12)冒口径处形成接触热节产生缩松(见图5)。
(13)压箱铁不够(或箱卡未锁紧,箱带断裂等),浇注后由于涨箱造成缩松。