鼓泡塔气相特性及返混特性测定实验
4月1日单元3任务2鼓泡塔式反应器仿真操作
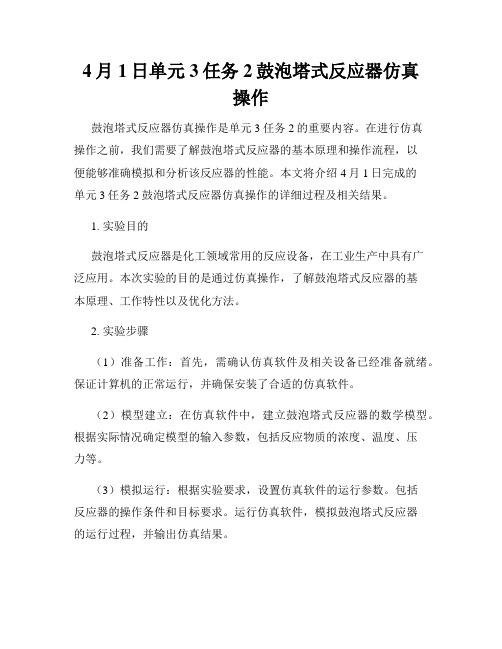
4月1日单元3任务2鼓泡塔式反应器仿真操作鼓泡塔式反应器仿真操作是单元3任务2的重要内容。
在进行仿真操作之前,我们需要了解鼓泡塔式反应器的基本原理和操作流程,以便能够准确模拟和分析该反应器的性能。
本文将介绍4月1日完成的单元3任务2鼓泡塔式反应器仿真操作的详细过程及相关结果。
1. 实验目的鼓泡塔式反应器是化工领域常用的反应设备,在工业生产中具有广泛应用。
本次实验的目的是通过仿真操作,了解鼓泡塔式反应器的基本原理、工作特性以及优化方法。
2. 实验步骤(1)准备工作:首先,需确认仿真软件及相关设备已经准备就绪。
保证计算机的正常运行,并确保安装了合适的仿真软件。
(2)模型建立:在仿真软件中,建立鼓泡塔式反应器的数学模型。
根据实际情况确定模型的输入参数,包括反应物质的浓度、温度、压力等。
(3)模拟运行:根据实验要求,设置仿真软件的运行参数。
包括反应器的操作条件和目标要求。
运行仿真软件,模拟鼓泡塔式反应器的运行过程,并输出仿真结果。
(4)结果分析:对仿真结果进行分析和评估。
包括反应物质的转化率、反应速率等指标的计算和比较。
观察反应器的温度、压力和流体分布等变化情况。
(5)参数调整:根据分析结果,对反应器的相关参数进行调整。
可以改变反应物质的初始浓度、温度和流速等参数,以获得更好的反应效果。
(6)结果验证:对调整后的参数进行仿真运行,并观察结果的变化。
通过与实际操作的对比,验证仿真结果的准确性和可靠性。
3. 实验结果根据仿真操作和分析,得到了鼓泡塔式反应器的相关结果:(1)反应物质的转化率随时间的变化曲线;(2)反应物质的浓度随反应器高度的变化曲线;(3)反应器中温度和压力的变化曲线;(4)气液两相混合的程度及流体的流动情况。
4. 结果分析根据仿真结果的分析,可以得到以下结论:(1)反应物质的转化率随时间的增加而逐渐增加,并趋于稳定;(2)反应物质的浓度随着反应器高度的增加而逐渐减小,且呈现非线性变化;(3)反应器中的温度随着反应进行而升高,压力也随之增加;(4)气液两相的混合程度在鼓泡塔内较好,流体的流动呈现较好的均匀性。
鼓泡塔反应器气液两相流CFD数值模拟_李光

Abst ract : Numerical simulatio ns o f gas-liquid f low in a cy lindrical bubble column wi th tw o-fluid approach were conducted at superficial gas veloci ties varying f rom 0 . 02 m · s -1 t o 0 . 30 m · s -1. A si ng le scalar t ranspo rt equati on w hich described bubble size chang es characterized by bubble int erfacial areas w as also i ncorporated into t he simulatio ns. In t he model s , the eff ect o f bubble co alescence and break-up w as taken i nt o conside ration. A modif ied kεt urbulence m odel was used t o describe liquid phase turbulence in the simulatio ns , by acco unti ng fo r t he pseudo t urbulence due to bubbles , w hile t he g as phase turbulence viscosit y w as estim ated based on t he T chen' s t heo ry. The simulations only adopted the drag force fo r phase momentum exchange . The time averaged axial liquid velocities , gas hold up and gas phase interfacial areas obtained from the simulations were compared w ith the available ex perimental result s. I t w as demo nst rated f rom the simulatio ns that the modeling in t his w o rk can reaso nably predict t he g as-liquid f low in the bubble column . Key w o rds :bubble column ; gas-liquid f low ; bubble model ; coalescence ; break-up
鼓泡塔气相特性及返混特性测定实验

一、实验目的1. 了解鼓泡塔的结构和操作方法;2. 测定鼓泡塔的气含率εG ,气体比表面a ,返混程度参数Pe 等。
二、实验原理1. 气含率气含率是表征气液鼓泡反应器流体力学特性的基本参数之一。
它直接影响反应器内气液接触面积,从而影响传质速率与宏观反应速率,是气液鼓泡反应器的重要设计参数。
测定气含率的方法很多,静压法是较精确的一种,基本原理由反应器内柏努力方程而来,可测定各段平均气含率,也可测定某一水平位置的局部气含率。
根据柏努利方程有:1c G L g dp g dHερ⎛⎫⎛⎫=+ ⎪⎪⎝⎭⎝⎭ (1) 采用U 型压差计测量时,两测压点平均气含率为:G hHε∆=(2) 当气液鼓泡反应器空塔气速改变时,气含率G ε会作相应变化,一般有如下关系: εG∝n Gu(3)n 取决于流动状况。
对安静鼓泡流,n 值在0.7~1.2之间;在湍动鼓泡流或过渡流区,G u 影响较小,n 为0.4~0.7范围内。
假设 εG =kn Gu(4)则 G G u lg n k lg lg +=ε (5)根据不同气速下的气含率数据,以1G g ε对1G n gu 作图标绘,或用最小二乘法进行数据拟合,即可得到关系式中参数k 和n 值。
2.气泡比表面气泡比表面是单位液体积的相界面积,也称气液接触面积、比相界面积,也是气液鼓泡反应器很重要的参数之一。
许多学者进行了这方面的研究工作,如光透法、光反射法、照相技术、化学吸收法和探针技术等,每一种测试技术都存在着一定的局限性。
气泡比表面积a 可由平均气泡直径us d 与相应的气含率G ε计算:usG d 6a ε=(6)Gestrich 许多学者的计算a 的关系进行整理比较,得到了计算a 值的公式:0.30.003026.0()G H a K Dε=⋅⋅ (7) 其中K-液体模数 :L LLK g ρσμ=; 方程式适用范围: u G ≤0.60m/s 02.224H D≤≤ 5115.71010K ⨯≤<因此在固定气速u G 下,测定反应器的气含率εG 数据,就可以间接得到气液化表面a 。
关于鼓泡塔反应器的研究报告
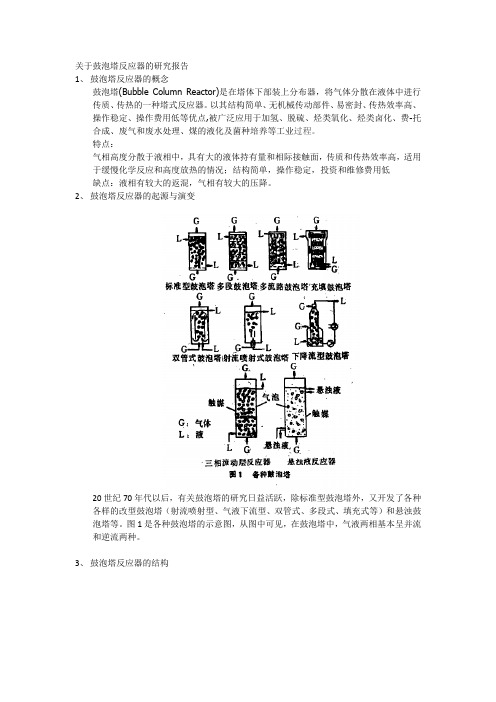
关于鼓泡塔反应器的研究报告1、鼓泡塔反应器的概念鼓泡塔(Bubble Column Reactor)是在塔体下部装上分布器,将气体分散在液体中进行传质、传热的一种塔式反应器。
以其结构简单、无机械传动部件、易密封、传热效率高、操作稳定、操作费用低等优点,被广泛应用于加氢、脱硫、烃类氧化、烃类卤化、费-托合成、废气和废水处理、煤的液化及菌种培养等工业过程。
特点:气相高度分散于液相中,具有大的液体持有量和相际接触面,传质和传热效率高,适用于缓慢化学反应和高度放热的情况;结构简单,操作稳定,投资和维修费用低缺点:液相有较大的返混,气相有较大的压降。
2、鼓泡塔反应器的起源与演变20世纪70年代以后,有关鼓泡塔的研究日益活跃,除标准型鼓泡塔外,又开发了各种各样的改型鼓泡塔(射流喷射型、气液下流型、双管式、多段式、填充式等)和悬浊鼓泡塔等。
图1是各种鼓泡塔的示意图,从图中可见,在鼓泡塔中,气液两相基本呈并流和逆流两种。
3、鼓泡塔反应器的结构3.1简单鼓泡塔的基本结构图2简单鼓泡塔1-塔体;2-夹套;3-气体分布器;4-塔体;5-挡板;6-塔外换热器;7-液体捕集器;8-扩大段主要由塔体和气体分布器组成。
塔体可安装夹套或其它型式换热器或设有扩大段、液滴捕集器等;塔内液体层中可放置填料;塔内可安置水平多孔隔板以提高气体分散程度和减少液体返混。
简单鼓泡塔内液相可近似视为理想混合流型,气相可近似视为理想置换流型。
最佳空塔气速应满足两个条件:(1)保证反应过程的最佳选择性;(2)保证反应器体积最小。
影响传质的因素:当气体空塔气速低于0.05m/s时,气体分布器的结构就决定了气体的分散状况、气泡的大小,进而决定了气含率和液相传质系数的大小。
当气体空塔气速大于0.1m/s时,气体分布器的结构无关紧要。
此时的气泡是靠气流与液体间的冲击和摩擦而形成,气泡大小及其分布状况主要取决于气体空塔气速。
3.2气体升液式鼓泡塔图3 气体升液式鼓泡塔1-筒体;2-气升管;3-气体分布器塔内装有气升管,引起液体形成有规则的循环流动,可以强化反应器传质效果,并有利于固体催化剂的悬浮。
填料塔液相轴向混合特性测定实验报告

填料塔液相轴向混合特性测定实验报告一、实验背景填料塔在化工生产中的重要性填料塔作为化工生产中常用的分离设备,在精馏、吸收、解吸等单元操作过程中发挥着至关重要的作用。
其结构主要由塔体、填料、液体分布器、填料支撑装置、液体再分布器、除沫装置等组成。
填料是填料塔的核心部件,提供气液接触面积,强化气体湍动,降低气相传质阻力,更新液膜表面,降低液相传质阻力。
填料种类多样,包括散装填料和规整填料。
散装填料如环形填料、鞍形填料、环鞍形填料及球形填料等,以随机的方式堆积在塔内;规整填料按一定的几何构形排列,整齐堆砌,如格栅填料、波纹填料、脉冲填料等。
选择填料时需考虑传质效率、通量、压降、抗污堵性能等因素,同时要综合考虑生产工艺要求、设备投资和操作费用等。
液体分布器的作用是均匀分布液体,避免发生沟流现象。
大中型填料塔塔顶回流分布器在无脏堵情况下应优先选择带管式预分布器的二级槽式液体分布器,以便于安装、检修,且不易形成液沫夹带。
槽盘式气液分布器是一种重力式液体分布器,具有抗脏堵性能强的优点。
填料支撑装置主要用途是支撑填料,确保其分布均匀,同时减小压降。
若设计不当,填料塔的液泛可能首先在填料支撑装置上发生。
液体再分布器的作用是减小壁流现象。
在乱堆填料层内存在的液体逐渐流向塔壁的现象称为壁流,会使气液两相在填料层中分布不均,从而使传质效率下降。
因此,在填料层内每隔一定高度设置液体再分布装置。
除沫装置用于除去出口气流中的液滴。
当塔内操作气速较大或液沫夹带现象严重时,除沫装置尤为重要。
填料塔具有生产能力大,分离效率高,压降小,持液量小,操作弹性大等优点。
但也存在一些不足之处,如填料造价高;当液体负荷较小时不能有效地润湿填料表面,使传质效率降低;不能直接用于有悬浮物或容易聚合的物料;对侧线进料和出料等复杂精馏不太适合等。
总之,对填料塔结构、性能及内部流体流动状况的研究具有重要的理论和实际意义,有助于优化化工生产过程,提高生产效率和产品质量。
鼓泡反应器中汽泡比表面及气含率的测定实验报告

鼓泡反应器中汽泡比表面及气含率的测定实验报告一、实验目的本实验旨在通过鼓泡反应器中气泡的形态、数量和大小来测定汽泡比表面及气含率。
二、实验原理鼓泡反应器是一种常用于气液反应器中的装置,其主要特点在于具有大量的气泡界面,因此可以有效地提高气液传质效率。
在该装置中,气体通过底部进入,并通过孔板等装置将气体分散成小的气泡。
当液体从顶部注入时,会与底部的气泡相互作用,形成大量的界面。
因此,在鼓泡反应器中测定汽泡比表面及气含率是非常重要的。
三、实验步骤1. 准备工作:清洗鼓泡反应器,并将其放置在水槽中。
2. 测定汽泡比表面:将水注入到鼓泡反应器中,调节流速和压力使得产生均匀大小的气泡,并记录下流速和压力值。
然后使用高速摄像机拍摄产生的气泡图像,并利用图像处理软件对图像进行处理和分析。
3. 测定气含率:将水注入到鼓泡反应器中,调节流速和压力使得产生均匀大小的气泡,并记录下流速和压力值。
然后使用气相色谱仪测定反应器中的气体组成,并计算出气含率。
四、实验结果1. 汽泡比表面:通过高速摄像机拍摄产生的气泡图像,并利用图像处理软件对图像进行处理和分析,得到了汽泡比表面为0.0138 m2/m3。
2. 气含率:通过气相色谱仪测定反应器中的气体组成,得到了氧气含量为0.21%,二氧化碳含量为0%。
五、实验分析1. 汽泡比表面:汽泡比表面是指单位体积液体中汽泡的总表面积。
该值可以直接反映出鼓泡反应器中液相与气相之间的传质效率。
因此,在鼓泡反应器设计和操作过程中,需要考虑如何提高汽泡比表面。
2. 气含率:在鼓泡反应器中,液相与气相之间的传质效率取决于液相和气相之间的物质传递速度。
因此,在设计和操作鼓泡反应器时,需要考虑如何控制气含率,以提高传质效率。
六、实验结论通过本实验的测定,得到了鼓泡反应器中的汽泡比表面和气含率。
这些参数可以用于评估鼓泡反应器的传质效率,并为鼓泡反应器的设计和操作提供参考。
鼓泡塔气体吸收实验报告
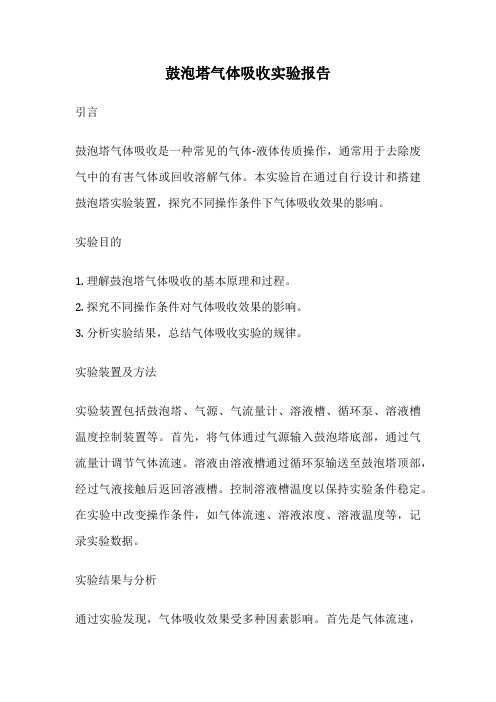
鼓泡塔气体吸收实验报告
引言
鼓泡塔气体吸收是一种常见的气体-液体传质操作,通常用于去除废气中的有害气体或回收溶解气体。
本实验旨在通过自行设计和搭建鼓泡塔实验装置,探究不同操作条件下气体吸收效果的影响。
实验目的
1. 理解鼓泡塔气体吸收的基本原理和过程。
2. 探究不同操作条件对气体吸收效果的影响。
3. 分析实验结果,总结气体吸收实验的规律。
实验装置及方法
实验装置包括鼓泡塔、气源、气流量计、溶液槽、循环泵、溶液槽温度控制装置等。
首先,将气体通过气源输入鼓泡塔底部,通过气流量计调节气体流速。
溶液由溶液槽通过循环泵输送至鼓泡塔顶部,经过气液接触后返回溶液槽。
控制溶液槽温度以保持实验条件稳定。
在实验中改变操作条件,如气体流速、溶液浓度、溶液温度等,记录实验数据。
实验结果与分析
通过实验发现,气体吸收效果受多种因素影响。
首先是气体流速,
气体流速越大,气体与溶液接触的时间越短,吸收效果相对较差。
其次是溶液浓度,溶液浓度越高,吸收效果越好。
最后是溶液温度,溶液温度升高会加快气体在溶液中的扩散速度,提高吸收效率。
结论
鼓泡塔气体吸收实验结果表明,操作条件对气体吸收效果有显著影响。
在实际应用中,可以根据具体需要调节操作条件,以达到最佳的气体吸收效果。
本实验为进一步研究气体吸收提供了重要参考。
结语
通过本次鼓泡塔气体吸收实验,我深刻理解了气体吸收的原理和影响因素。
在未来的学习和工作中,我将继续探索气体传质操作,为环境保护和资源回收做出更大的贡献。
感谢实验给予我这次宝贵的学习机会。
浅析旋流式鼓泡塔内部流场特性的实验模拟

浅析旋流式鼓泡塔内部流场特性的实验模拟本文从网络收集而来,上传到平台为了帮到更多的人,如果您需要使用本文档,请点击下载按钮下载本文档(有偿下载),另外祝您生活愉快,工作顺利,万事如意!鼓泡塔广泛应用于石油化学工程、生物工程、环境以及能源工业领域中,如加氢、费托合成、污水处理、煤液化等。
近年来,大量的科研工作者通过各种实验模拟研究了鼓泡塔反应器内的流体特性。
本文利用CFD 技术中的FLUENT 计算软件对入口气速分别为2,3,4,5 m/s 时的旋流式鼓泡反应器流场进行了模拟,研究结果对鼓泡塔的优化设计及工业放大有实际的意义。
1 旋流式鼓泡反应器的结构新型旋流式鼓泡塔的总体结构。
旋流式鼓泡反应器基本由筒体,气体分布器,气液分离器三部分组成。
2 数值模拟建立模型模拟对象为圆柱形旋流式鼓泡三相反应器,它的内径为800 mm、高为1 400 mm。
主要相为液相—水;次要相为气相—空气,喷射鼓气管直径为20mm。
喷气径与反应器直径的比值(环径比)为。
网格划分(a)总体结构(b)网格加密边界条件在本算例中,边界条件设定包括壁面(wall)、速度入口( velocity-inlet )、压力出口(pressure-outlet)。
边界条件的设定,对于复杂流场的收敛性有着决定性的影响。
模拟变量边界条件为:入口为气相,在模拟过程中,入口的湍流强度(Turbulent Intensity)为5%。
水力直径(HydraulicDiameter)由模型中喷气管的数量不同而不同;出口为压力出口,压力为表压为0 Pa。
出口的湍流强度(Turbulent Intensity)为1%,水力直径(HydraulicDiameter)为800 m;壁面定义为无滑移边界条件。
3 模拟结果分析本文通过CFD 技术中的Fluent 对旋流式鼓泡塔反应器流场进行数值模拟计算,再通过CFD-Post对其结果进行后处理,得出不同气速下反应器中的速度矢量图,速度云图, 水的体积分数云图等并对其结果进行分析比较,确定最佳的入口气速。
- 1、下载文档前请自行甄别文档内容的完整性,平台不提供额外的编辑、内容补充、找答案等附加服务。
- 2、"仅部分预览"的文档,不可在线预览部分如存在完整性等问题,可反馈申请退款(可完整预览的文档不适用该条件!)。
- 3、如文档侵犯您的权益,请联系客服反馈,我们会尽快为您处理(人工客服工作时间:9:00-18:30)。
一、实验目的
1. 了解鼓泡塔的结构和操作方法;
2. 测定鼓泡塔的气含率εG ,气体比表面a ,返混程度参数Pe 等。
二、实验原理
1. 气含率
气含率是表征气液鼓泡反应器流体力学特性的基本参数之一。
它直接影响反应器内气液接触面积,从而影响传质速率与宏观反应速率,是气液鼓泡反应器的重要设计参数。
测定气含率的方法很多,静压法是较精确的一种,基本原理由反应器内柏努力方程而来,可测定各段平均气含率,也可测定某一水平位置的局部气含率。
根据柏努利方程有:
1c G L g dp g dH ερ⎛⎫⎛⎫=+ ⎪ ⎪⎝⎭⎝⎭ (1)
采用U 型压差计测量时,两测压点平均气含率为:
G h
H
ε∆=
(2) 当气液鼓泡反应器空塔气速改变时,气含率G ε会作相应变化,一般有如下关系:
εG ∝n G
u (3) n 取决于流动状况。
对安静鼓泡流,n 值在0.7~1.2之间;在湍动鼓泡流或过渡流区,G u 影响较小,n 为0.4~0.7范围内。
假设 εG =k
n G
u (4)
则 G G u lg n k lg lg +=ε (5)
根据不同气速下的气含率数据,以1G g ε对1G n gu 作图标绘,或用最小二乘法进行数据拟合,即可得到关系式中参数k 和n 值。
2.气泡比表面
气泡比表面是单位液体积的相界面积,也称气液接触面积、比相界面积,也是气液鼓泡反应器很重要的参数之一。
许多学者进行了这方面的研究工作,如光透法、光反射法、照相技术、化学吸收法和探针技术等,每一种测试技术都存在着一定的局限性。
气泡比表面积a 可由平均气泡直径us d 与相应的气含率G ε计算:
us
G
d 6a ε=
(6)
Gestrich 许多学者的计算a 的关系进行整理比较,得到了计算a 值的公式:
0.30.003
026.0(
)G H a K D
ε=⋅⋅ (7) 其中K-液体模数 :L L
L
K g ρσμ=; 方程式适用范围: u G ≤0.60m/s 0
2.224H D
≤
≤ 5115.71010K ⨯≤<
因此在固定气速u G 下,测定反应器的气含率εG 数据,就可以间接得到气液化表面a 。
Gestrich 经大量据数比较后确认式(7)的计算偏差在15%±之内。
3、鼓泡塔液相返混特性
描述返混的数学模型很多,较简单实用的是一维扩散模型。
一维扩散模型的数学表达 式:
θ
∂∂=∂∂-∂∂⋅c z c z c Pe 221 (8) Dax
UH
Pe =
(9) 式中P e 为彼克列数,描述返混程度的模型参数。
对式(8)求解:
定解条件:实验采用脉冲法加入示踪剂,在上游处测定示踪剂浓度,闭式容器,列出如下定解条件:
取 ),(θz f c = 初始条件:0)0,(=z c 边界条件:()θθ1),0(c c = 有限量=∞),(θc 用Laplace 变换解得:
()⎥⎦
⎤
⎢⎣⎡--⎪⎭⎫ ⎝⎛=2314ex p 2)(θθπθθPe Pe c (10) 估计模型参数Pe :估计的方法有多种,如矩量法、传递函数法、拟合法等。
本实验采用矩量法,需用到如下两个定义:
⑴ 浓度c (t )的一阶原点矩:
()()t dt
t c tdt t c M ˆ001=⎰⎰=∞∞
(11)
⑵ 浓度c (t )的二阶中心矩:
()()()()()
22002002ˆˆt t
dt
t c dt t t c dt
t c dt t t t c M θ=-⎰⎰=
⎰⎰-=∞
∞∞
∞ (12)
式中:t ˆ—数学期望; 2t θ—方差或称散度。
由式(11)和式(12),可导出如下方程:
()
Pe t Pe Pe t
θθθθ-⎪⎭⎫ ⎝⎛-==1122ˆ2
22
2 (13)
实验测得c (t )与t 的关系数据,由式(11)求得t ˆ,由式(12)求得2t θ,通过(13)求得Pe 的值。
三、流程及设备的主要技术数据
流程图:(见图一)
1— 水箱 ,2—水泵,3—空气压缩机,4—三通阀 ,5—空气流量计,6—空气进量控制阀, 7—阀7 ,8—示踪剂储罐 ,9—测孔,10—压力表,11—空气进料口 ,12—示踪剂进口,13—鼓泡塔,14—电导电极 ,15—电导率仪,16—计算机采集系统 ,17—溢流管 ,18——压力传感器 ,19—阀19 ,20—压差表 ,21—流体分布器,22—放液阀 ,23
—回流管阀,24—放液阀,25—液体进料口,26—液体流量控制阀,27—液体流量计
如图一所示,示踪剂缓冲罐内配有饱和的氯化钾溶液
鼓泡塔:塔高2m, 反应器直径为200mm, 气体分布器采用十字型,并有若干小孔使气体达到一定的小孔气速。
反应器用有机玻璃管加工,便于观察。
反应器壁面沿轴向开有一排小孔与压力传感器相连,用于测量压差。
四、实验内容和操作步骤
1、气含率及气泡比表面的测定
(1)系统接上电源,打开总开关,开启水泵后将清水加入反应器床层内,至一定高度(约1.5m)。
(2)检查一下压差表读数是否为0,如果不是则应该打开与压差传感器相连的铜管上的阀门1将水铜管内充满了水(排除掉由于零点漂移所造成的误差)。
(3)固定液体流量在一个适当值,本实验可取水流量值为200L/h,并通过空气流量计阀门调节进气量。
(4) 观察床层内气液两相流流动状态。
(5) 等待压力表读数稳定后记录各进气量下的压差值。
(6) 改变气体流量,重复上述操作(可以做6-8个条件)。
(7) 注意事项:在进行鼓泡塔气相特性测定时应保证阀2全开(回液阀门),阀3全闭(放水阀门),阀4(回液阀门)全闭,阀5全闭(密闭容器与压缩机相连的阀门)。
(8) 记录下压差值后安实验所给公式计算处气含率和气泡比表面。
2、返混特性参数Pe数的测定
(1)启动数据采集系统,使其处于工作状态。
(2)将阀门5微开,使得的示踪剂储罐上方的压力达到0.1兆帕左右,在开启电磁阀通入示踪剂之后即可将阀5关闭,泄压。
(3)取实验数据:待系统稳定之后(即空气流量、水流量稳定在预定值),命令微机采集数据,启动电磁阀注入示踪剂。
采数结束后,采集软件会自动进行数据进处理,并输出结果—TD(数学期望),DD(方差)和PE(彼克列数)。
⑷维持空气流量不变,改变水的流量,取实验数据。
(本实验中可取空气流量为1m3/h,水的流量分别取为60,100,150,200
(5)每一水流量条件下,重复两次取数据,使PE值的相对误差≤±5%。
然后改变水流量进行下一个实验,完毕为止。
3、实验完毕后,关闭空压机、真空泵、进水阀门、电导率仪、微机系统等仪器设备的电源,并将所有仪器复原。
五、注意事项
1)试验开启应该先通水,到一定位置后约1m左右,开启压缩机鼓气。
实验开始时应保证与静态压差传感器与直径为0.8mm的铜管相连,避免了弹性效应,并且以要在铜管内充满水,这样铜管内无液体流动,从根本上消除了“呼吸”作用,使铜管中无气泡进入,保证压差测量准确性。
2)应该在固定操作条件一段时间后,反应器稳定后在读取压差表的读数(这里的稳定指的是瞬态稳定,即压差表的读数在某一个范围内呈稳定波动即可)3)在测定鼓泡塔内气相特性时将示踪剂储罐下方的进气阀7关闭;等到开始测定返混特性时应将此阀7微开使示踪剂储罐内压力升至0.1兆帕左右即可,示踪剂打入后要关闭阀7。
4)测定返混特性时将鼓泡塔装置下方的回流阀23,24均关闭,放液阀22打开:保证加有示踪剂的液体不回流水储槽中,并应保证不断有新鲜的物料加入水槽中补给物料。
六、实验数据记录与出理。