球化参考资料退火
球化退火

Ac1下20-30长t 保温-空冷,低中c,低 合金结钢冷变形快
球
图9-4 形变球化退火工艺曲线 a)低温形变球化退火 b)高温形变球化退火
Ac1上30-50,缓 冷,轧锻件的锻后 余热,弹簧钢轴承
Ac1
550℃
适于共析及过 共析钢,球化 较充分,周期 长。
缓慢冷却球化退火 t
a
7
② 等温球化
T Ac1+20~30℃
AC3
AC1 Ar1-(20~30℃)
适于过共析钢,合 金工具钢,球化充 分,易控制,周期 短,适于大件。
等温球化退火
t
a
8
③循环球化退火
Ac1+20℃ Ar1- 20℃
:
球化退火主要适用于含C>0.6%的各种高C工具钢、模 具钢、轴承钢的预备热处理。
当中C及中C合金钢要求硬度极低而韧性极高(如用于 冷冲压坯料)时。
低C钢球化退火后,不适于切削前处理(太软,发 粘),但可以改善冷变形的加工性能
a
2
(1) 低温球化退火
低温球化退火是把钢加热到Ac1以下10~30℃长
体及部分未溶碳化物,然后通过缓慢冷却或低于临界点等温 分解,或在A1点上下循环加热冷却使碳化物球化。高碳钢循 环加热(周期球化退火)—碳化物↑球化均匀↑效率↑。
图9-3 不均匀奥氏体中碳的聚集球化退火 a)缓慢冷却球化退火 b)等温球化退火 c)周期(循环)球化退火 d)感应加热快速球化
退火
a
4
(3) 形变球化退火
钢
a
球化退火与软化退火
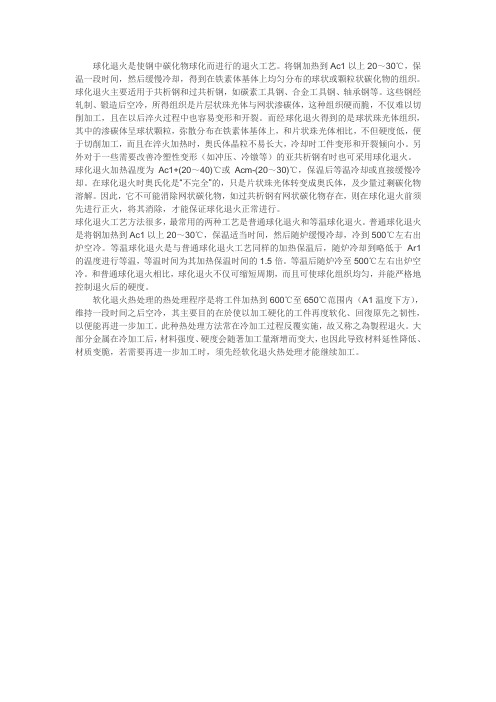
球化退火是使钢中碳化物球化而进行的退火工艺。
将钢加热到Ac1以上20~30℃,保温一段时间,然后缓慢冷却,得到在铁素体基体上均匀分布的球状或颗粒状碳化物的组织。
球化退火主要适用于共析钢和过共析钢,如碳素工具钢、合金工具钢、轴承钢等。
这些钢经轧制、锻造后空冷,所得组织是片层状珠光体与网状渗碳体,这种组织硬而脆,不仅难以切削加工,且在以后淬火过程中也容易变形和开裂。
而经球化退火得到的是球状珠光体组织,其中的渗碳体呈球状颗粒,弥散分布在铁素体基体上,和片状珠光体相比,不但硬度低,便于切削加工,而且在淬火加热时,奥氏体晶粒不易长大,冷却时工件变形和开裂倾向小。
另外对于一些需要改善冷塑性变形(如冲压、冷镦等)的亚共析钢有时也可采用球化退火。
球化退火加热温度为Ac1+(20~40)℃或Acm-(20~30)℃,保温后等温冷却或直接缓慢冷却。
在球化退火时奥氏化是“不完全”的,只是片状珠光体转变成奥氏体,及少量过剩碳化物溶解。
因此,它不可能消除网状碳化物,如过共析钢有网状碳化物存在,则在球化退火前须先进行正火,将其消除,才能保证球化退火正常进行。
球化退火工艺方法很多,最常用的两种工艺是普通球化退火和等温球化退火。
普通球化退火是将钢加热到Ac1以上20~30℃,保温适当时间,然后随炉缓慢冷却,冷到500℃左右出炉空冷。
等温球化退火是与普通球化退火工艺同样的加热保温后,随炉冷却到略低于Ar1的温度进行等温,等温时间为其加热保温时间的1.5倍。
等温后随炉冷至500℃左右出炉空冷。
和普通球化退火相比,球化退火不仅可缩短周期,而且可使球化组织均匀,并能严格地控制退火后的硬度。
软化退火热处理的热处理程序是将工件加热到600℃至650℃范围内(A1温度下方),维持一段时间之后空冷,其主要目的在於使以加工硬化的工件再度软化、回復原先之韧性,以便能再进一步加工。
此种热处理方法常在冷加工过程反覆实施,故又称之為製程退火。
大部分金属在冷加工后,材料强度、硬度会随著加工量渐增而变大,也因此导致材料延性降低、材质变脆,若需要再进一步加工时,须先经软化退火热处理才能继续加工。
球化退火介绍

提问者: 映月沙丘- 江湖新秀最佳答案球化退火球化退火是使钢中碳化物球化而进行的退火工艺。
将钢加热到Ac1以上20~30℃,保温一段时间,然后缓慢冷却,得到在铁素体基体上均匀分布的球状或颗粒状碳化物的组织。
球化退火主要适用于共析钢和过共析钢,如碳素工具钢、合金工具钢、轴承钢等。
这些钢经轧制、锻造后空冷,所得组织是片层状珠光体与网状渗碳体,这种组织硬而脆,不仅难以切削加工,且在以后淬火过程中也容易变形和开裂。
而经球化退火得到的是球状珠光体组织,其中的渗碳体呈球状颗粒,弥散分布在铁素体基体上,和片状珠光体相比,不但硬度低,便于切削加工,而且在淬火加热时,奥氏体晶粒不易长大,冷却时工件变形和开裂倾向小。
另外对于一些需要改善冷塑性变形(如冲压、冷镦等)的亚共析钢有时也可采用球化退火。
球化退火加热温度为Ac1+(20~40)℃或Acm-(20~30)℃,保温后等温冷却或直接缓慢冷却。
在球化退火时奥氏化是“不完全”的,只是片状珠光体转变成奥氏体,及少量过剩碳化物溶解。
因此,它不可能消除网状碳化物,如过共析钢有网状碳化物存在,则在球化退火前须先进行正火,将其消除,才能保证球化退火正常进行。
球化退火工艺方法很多,最常用的两种工艺是普通球化退火和等温球化退火。
普通球化退火是将钢加热到Ac1以上20~30℃,保温适当时间,然后随炉缓慢冷却,冷到500℃左右出炉空冷。
等温球化退火是与普通球化退火工艺同样的加热保温后,随炉冷却到略低于Ar1的温度进行等温,等温时间为其加热保温时间的1.5倍。
等温后随炉冷至500℃左右出炉空冷。
和普通球化退火相比,球化退火不仅可缩短周期,而且可使球化组织均匀,并能严格地控制退火后的硬度。
等温球化退火的工艺路线
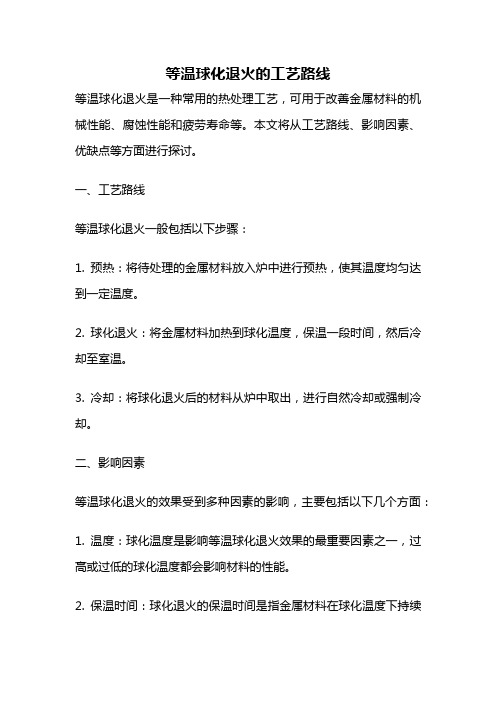
等温球化退火的工艺路线等温球化退火是一种常用的热处理工艺,可用于改善金属材料的机械性能、腐蚀性能和疲劳寿命等。
本文将从工艺路线、影响因素、优缺点等方面进行探讨。
一、工艺路线等温球化退火一般包括以下步骤:1. 预热:将待处理的金属材料放入炉中进行预热,使其温度均匀达到一定温度。
2. 球化退火:将金属材料加热到球化温度,保温一段时间,然后冷却至室温。
3. 冷却:将球化退火后的材料从炉中取出,进行自然冷却或强制冷却。
二、影响因素等温球化退火的效果受到多种因素的影响,主要包括以下几个方面:1. 温度:球化温度是影响等温球化退火效果的最重要因素之一,过高或过低的球化温度都会影响材料的性能。
2. 保温时间:球化退火的保温时间是指金属材料在球化温度下持续保温的时间,保温时间过短或过长都会影响球化效果。
3. 冷却方式:冷却方式包括自然冷却和强制冷却两种,选择合适的冷却方式对材料的性能影响较大。
4. 材料成分:不同成分的金属材料对等温球化退火的响应不同,因此需要针对不同的材料进行相应的处理。
三、优缺点等温球化退火具有以下优点:1. 可以改善金属材料的机械性能,提高其延展性和韧性。
2. 可以提高金属材料的腐蚀性能,减少材料的腐蚀损失。
3. 可以提高金属材料的疲劳寿命,延长材料的使用寿命。
等温球化退火也存在以下缺点:1. 工艺时间较长,需要耗费较多的能源和成本。
2. 球化后的材料容易出现晶界腐蚀等问题。
3. 对于一些特殊材料,球化退火可能无法起到明显的效果。
四、总结等温球化退火是一种常用的热处理工艺,可以改善金属材料的性能,但其效果受到多种因素的影响。
因此,在实际应用中需要根据不同材料的成分和工艺要求选择合适的球化温度、保温时间和冷却方式,以达到最佳的处理效果。
GC r15 钢球化退火工艺设计介绍

GC r15 钢球化退火工艺设计介绍引言GCr15 轴承钢按正常的工艺规范进行锻造后, 得到的是细片状珠光体组织(索氏体) , 硬度较高, 达255~340 HBS, 难以进行切削加工, 故需要进行一次球化退火, 以降低硬度, 同时也为淬火作好组织上的准备. 因为经过大量的试验和生产实践证明, 只有当轴承零件的原始组织为细球状珠光体时, 经过淬火加低温回火后, 才能获得隐晶回火马氏体及在其上分布着细小碳化物颗粒的组织, 这种金相组织才使得轴承零件具有高强度和韧性. 在工业生产中, 常用的球化退火工艺包括一次球化退火工艺、等温球化退火工艺和周期球化退火等工艺. 某厂使用等温球化退火工艺来对轴承零件进行球化处理, 但遇到工艺周期长、耗能多、效率低等问题, 球化质量也不稳定, 直接影响到工件的淬火开裂倾向. 为此本文对GCr15 钢制轴承零件的球化退火工艺进行了研究, 结合宁波市神光电炉有限公司对中频电炉的改造, 得出一个比较切合实际的球化退火工艺.1球化退火工艺试验1. 1试验材料及检测设备GCr15 钢制轴承套圈, 内圈壁厚7 mm , 外径400mm; 外圈壁厚7mm , 外径500mm. 试验样品按正常工艺锻造后, 随机取出, 编号为18# (外圈) , 22# (外圈) , 23# (内圈) , 24# (外圈) 样品为等温球化处理的成品.检测设备为箱式电阻炉, 型号SX24210, 炉膛尺寸300 mm ×200 mm ×120 mm; 用毫伏计控温, 型号KSW 24D211; 用MM 6 型金相显微镜观察金相显微组织, 在布氏硬度试验机上测定HBS值, 作为工件球化效果的定量指标.1. 2工艺试验1. 2. 1原用等温球化退火工艺宁波市神光电炉有限公司制定的等温球化退火工艺如图所示. 这一工艺曲线严格遵循了退火工艺的三要素, 即加热温度、保温时间和冷却速度. GCr15 钢的退火加热范围为780~810 ℃, 因而该厂采用790 ℃. 冷却速度控制在15~20℃öh 范围内, 整个工艺过程需要17h. 该厂根据这一工艺路线对轴承零件进行球化处理, 要求硬度为179~207 HBS, 球化组织级别为2~4 级.1. 2. 2周期球化退火工艺的选用周期球化退火的工艺曲线如图2 所示. 将钢加热至略高于A c1的温度, 保温一定时间后, 随炉冷至略低于A r1的温度等温处理. 如此反复加热和冷却, 最后冷至室温, 每一阶段的保温时间为1 h, 目的是增加球化的核心, 以获得较为满意的球化组织. 这种工艺特别适用于难以球化的钢种.1. 2. 3工艺参数的制定文献指出, GCr15钢的A c1是一个温度区间为735~765 ℃, 加热温度超过A c1时, 珠光体开始向奥氏体转变, 温度越高, 奥氏体化后钢的组织越趋于均匀, 未溶的碳化物越少, 这对珠光体的球化是不利的. 文献研究了40 Cr 钢的奥氏体化条件与等温温度对硬度的影响, 结果表明在临界区对钢加热, 一旦加热温度升高, 则钢的淬火硬度明显增高, 这说明发生了奥氏体的富碳过程, 即碳化物溶解过多, 这样会导致球化困难. 同时还指出, 在高的温度奥氏体化下, 若保温时间延长, 同样会使球化困难, 而且影响十分明显. 这样看来, 退火加热温度是一个关键, 为此根据GCr15 钢的A c1, 在试验时将循环曲线的加热温度制定为770 ℃.文献研究了等温温度即珠光体转变温度对球化过程的影响规律, 发现若将等温温度降低, 即使在奥氏体中有大量的未溶碳化物, 也将导致大量的片状珠光体形成. 因而让珠光体在比较高的温度下长时间保温对球化组织的形成也是很重要的. 为此笔者做了一个对比试验, 将轴承钢在770 ℃加热2h 后在不同的温度下等温2 h, 然后以30 ℃öh 冷却至650 ℃下再空冷的试验(见表1) , 从试验结果可看出, 在720 ℃等温是合理的.还可以这样来解释720 ℃等温的合理性, 因为冷却速度会影响奥氏体向珠光体转变的温度范围,冷速越慢, 转变温度越高, 而在周期球化退火工艺中, 工件从770 ℃进入到720 ℃后, 冷速不会很快, 因此在720 ℃等温是合理的.文献对球化退火过程中冷却速度的影响做了详细的研究, 特别是在转变终了温度上作了很好的说明.文献中指出, 在转变终了温度后的冷却速度对工件的硬度没有影响, 因此转变后的冷速应该较快.本试验在制定冷却速度时, 考虑到不致于给工件产生热应力, 将冷速定为30 ℃。
42crmo4球化退火要求
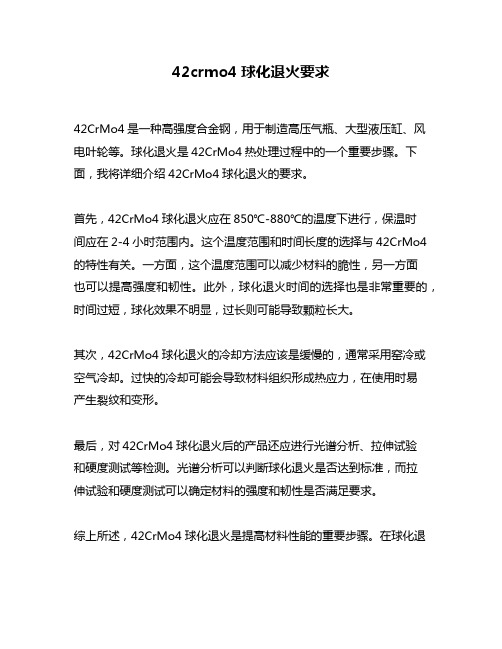
42crmo4球化退火要求
42CrMo4是一种高强度合金钢,用于制造高压气瓶、大型液压缸、风电叶轮等。
球化退火是42CrMo4热处理过程中的一个重要步骤。
下面,我将详细介绍42CrMo4球化退火的要求。
首先,42CrMo4球化退火应在850℃-880℃的温度下进行,保温时
间应在2-4小时范围内。
这个温度范围和时间长度的选择与42CrMo4的特性有关。
一方面,这个温度范围可以减少材料的脆性,另一方面
也可以提高强度和韧性。
此外,球化退火时间的选择也是非常重要的,时间过短,球化效果不明显,过长则可能导致颗粒长大。
其次,42CrMo4球化退火的冷却方法应该是缓慢的,通常采用窑冷或空气冷却。
过快的冷却可能会导致材料组织形成热应力,在使用时易
产生裂纹和变形。
最后,对42CrMo4球化退火后的产品还应进行光谱分析、拉伸试验
和硬度测试等检测。
光谱分析可以判断球化退火是否达到标准,而拉
伸试验和硬度测试可以确定材料的强度和韧性是否满足要求。
综上所述,42CrMo4球化退火是提高材料性能的重要步骤。
在球化退
火过程中,需要注意温度和时间的选择,以及冷却方法的缓慢。
此外,在球化退火后,要进行多项检测以确保材料的质量达到标准。
球化退火炉

一、化退火楷述球化退火主要的目的,是希望藉由热处理使钢铁材料内部的层状或网状碳化物凝聚成为球状,使改善钢材之切削性能及加工塑性,特别是高碳的工具钢,轴承钢更是需要此种退火处理。
常见的球化退火处理包括:(1)在钢材A1温度的上方、下方反覆加热、冷却数次,使A1变态所析出的雪明碳铁,继续附著成长在上述球化的碳化物上;(2)加热至钢材A3或Acm温度上方,始碳化物完全固溶於沃斯田体后急冷,再依上述方法进行球化处理。
使碳化物球化,尚可增加钢材的淬火后韧性、防止淬裂,亦可改善钢材的淬火回火后机械性质、提高钢材的使用寿命。
二、球化退火(spheroidizeannealing)将钢中珠光体内的片层状渗碳体和先共析渗碳体转化为均匀分布于铁素体基体上的球状或粒状碳化物以获得球状珠光体的热处理方法,是不完全退火的一种。
因为片状渗碳体表面积大,处于不稳定状态,硬度比较高,切削加工后零件的表面粗糙度高,淬火过程中工件容易变形和开裂。
而球状碳化物有最小界面,能量最低,处于稳定的平衡状态,硬度低,切削性能好,韧性高,冷加工能力大,淬火时工件不易变形和开裂。
因此,碳素工具钢、一部分合金工具钢和滚珠轴承钢钢材都应经过球化退火才能交货。
根据钢种和退火目的,球化退火可分以下几种:(1)普通球化退火,即将钢加热到730~740℃保温足够时间,然后以小于20℃/h的速度缓冷到650℃出炉。
这种退火工艺适用于共析成分附近的碳素工具钢。
(2)周期球化退火,也叫循环退火。
它是在A、点附近的温度反复进行加热和冷却,一般进行3~4个周期,使片状珠光体在几次溶解一析出的反复过程中,碳化物得以球化。
该工艺生产周期较长,操作不方便,难以控制,适用于片状珠光体比较严重的钢。
(3)等温球化退火。
一般加热到800±l0℃,保温后快冷到700±10℃(A1附近)再进行较长时间保温,之后,以30~50℃/h的速度冷却到600℃出炉。
一般轴承钢多采用此工艺。
双炉等温球化退火

双炉等温球化退火双炉等温球化退火是一种常用的金属热处理工艺,可以改善金属材料的力学性能和组织结构。
本文将介绍双炉等温球化退火的原理、过程和影响因素,并探讨其在金属加工中的应用。
一、原理双炉等温球化退火是利用高温加热和适当冷却处理金属材料,使其晶粒得到细化和均匀化,从而提高材料的强度和韧性。
该工艺的原理是通过控制加热和冷却的温度和时间,在材料中形成细小均匀的球状晶粒,从而改善材料的力学性能和组织结构。
二、过程双炉等温球化退火通常分为两个步骤:加热和冷却。
1. 加热:将金属材料放入加热炉中,通过加热炉内的加热元件将材料加热至一定温度。
在加热过程中,需要控制加热速度和加热温度,以确保材料温度均匀上升并达到球化退火所需的温度。
2. 冷却:将加热后的材料迅速放入冷却介质中,如水或油,进行快速冷却。
冷却过程中,需要控制冷却速度和冷却介质的温度,以确保材料得到适当的冷却,从而形成细小均匀的球状晶粒。
三、影响因素双炉等温球化退火的效果受到多个因素的影响,包括材料的成分、加热温度和时间、冷却速度和介质等。
1. 材料成分:不同金属材料的球化退火效果有所差异,通常是由材料的成分和热处理工艺共同决定的。
2. 加热温度和时间:加热温度和时间的选择直接影响着球化退火的效果。
通常情况下,需要在材料的临界温度以上进行加热,且时间越长,晶粒的细化程度越高。
3. 冷却速度和介质:冷却速度和介质的选择也会对球化退火的效果产生影响。
一般来说,快速冷却可以得到更细小的球状晶粒,而慢速冷却则可以得到较大的晶粒。
四、应用双炉等温球化退火广泛应用于金属材料的加工和制造过程中,以改善材料的力学性能和组织结构。
具体应用包括以下几个方面:1. 钢材加工:双炉等温球化退火可以用于冷拔钢丝、冷拔钢管等产品的制造过程中,以提高产品的强度和韧性。
2. 铝合金加工:双炉等温球化退火可以用于铝合金的热处理过程中,以改善铝合金的抗拉强度和塑性。
3. 铜材加工:双炉等温球化退火可以用于铜材的退火处理,以提高铜材的导电性和弯曲性能。
- 1、下载文档前请自行甄别文档内容的完整性,平台不提供额外的编辑、内容补充、找答案等附加服务。
- 2、"仅部分预览"的文档,不可在线预览部分如存在完整性等问题,可反馈申请退款(可完整预览的文档不适用该条件!)。
- 3、如文档侵犯您的权益,请联系客服反馈,我们会尽快为您处理(人工客服工作时间:9:00-18:30)。
热处理技术——球化退火
球化退火是使钢获得弥散分布于铁素体基体上的细粒状(球状)碳化物组织的工艺方法。
其目的为改善切削性能,减小淬火时的变形开裂倾向性,使钢件得到相当均匀的最终性能。
球化退火主要应用于轴承零件、刀具、冷作模具等的预备热处理,以改善切削加工性能及加工精度,消除网状或粗大碳化物颗粒所引起的工具的脆断和刃口崩落,提高轴承的接触疲劳寿命等。
中碳及中碳合金钢只当要求硬度极低而韧性极高(例如用于冷冲压坯料)时,才用球化退火。
低碳钢一般不进行球化退火,否则由于硬度过低(160~170HBS)反而使切削加工性能变坏。
在工具钢及轴承钢碳化物的概念中,应包括一次(液析)碳化物、二次碳化物(由奥氏体中析出)及共析碳化物这三方面的球化。
一次碳化物系铸锭枝晶偏析所引起的亚稳定莱氏体结晶的产物,颗粒尺寸较大,常沿轧制方向分布,形成偏析碳化物带,硬度高、脆性大,易引起淬火裂纹,使钢的耐磨性变差,以至工件在使用中造成表面脱落或中心破裂。
一次碳化物的球化主要靠合理的锻造工艺,例如反复镦拔(相当大的总锻造比:十几、二十几以上)和适当的扩散退火来得到。
二次碳化物与共析碳化物的球化与锻造过程有关。
为了使退火后能获得均匀分布的粒状碳化物,锻造后的组织应为细片状珠光体及细些断续网状碳化物(或含有少量马氏体)。
如果终锻温度南过高或冷却太慢,则易引起粗大网状在化物,退火中无法消除。
如终锻温度过低<800℃,碳化物易沿晶界变形方向析出而形成线条状组织,退火后将有方向性,使钢的强度降低,加工性能变坏。
珠光体片较细时,球化退火时可采用较低,加工性能变坏。
珠光体片较细时,球化退火时可采用较低的的温度和较短的时间。
退火温度愈低、未溶解的碳化物数量越多,容易获得均匀分布的细粒状珠光体组织。
珠光体片较粗时,在正常退火工艺情况下,不易获得均匀分布的细粒状珠光体。
因此,为了得到良好的球化组织,必须严格控制锻造工艺过程。
1。