中速磨磨辊堆焊工艺流程
磨辊堆焊(谷风技术)

针对中速磨煤机高铬铸铁抗磨损件的磨损失效机理,研制了两种焊接工艺性能优良关键词:针对中速磨煤机高铬铸铁抗磨损件的磨损失效机理研制了两种焊接工艺性能优良一、概述中速磨煤机抗磨损件(主要是高铬铸铁磨辊和磨盘)在磨制煤粉过程中不断磨损,其失效形式主要是煤对抗磨损件的摩擦损耗产生的三体磨料磨损,其磨损方式主要是煤中的硬质颗粒对抗磨损件表面造成的显微切削、犁沟塑变以及碳化物的破碎与剥落;磨损机理为微切削磨损、塑性疲劳磨损、脆断和剥落磨损三种机制并存,但以微切削磨损为主。
为保证中速磨煤机的出力,高铬铸铁抗磨损件需定期检查、调整、修复或更换。
采用药芯焊丝自动堆焊方式修复废旧高铬铸铁抗磨损件的经济效益和社会效益显著,自保护药芯焊丝自动焊即明弧自动焊因综合性能优异逐步取代埋弧自动焊成为堆焊发展的潮流,但国内配套自保护药芯焊丝的品质和种类明显不能满足目前由于电力建设空前壮大引起的中速磨煤机抗磨损件备件紧张的局面。
本文针对中速磨煤机高铬铸铁抗磨损件的磨损失效机理,研制了两种焊接工艺性能优良,堆焊层具有高硬度和高耐磨性的多元合金强化型自保护药芯焊丝,并对研制焊丝自保护机制的实现和堆焊层高耐磨性的原因进行了探讨。
二、设计原则研制药芯焊丝(脚号58—O、60—O)外皮采用韩国进口低碳冷轧钢带H08AL,截面为O形,药芯填充系数调整范围45%~55%,先轧后拔工艺生产,成丝直径为3.2mm。
研制药芯焊丝为金属粉型;合金系采用多元合金(Mo、W、V、Nb、Ni、Cu、Zr、Ti、B、Re等)强化的Fe-Cr-C系耐磨合金;主要采用造气-合金元素自保护机制。
研制药芯焊丝的成分如表1所示。
三、研制药芯焊丝的性能1.焊接工艺性能由于自保护药芯焊丝的工艺参数适应性小,所以试验中对其进行了优化,如表2所示。
药芯焊丝58—O,60—O的焊接工艺性能优良:电弧燃烧稳定,焊道成形好,飞溅少,气孔很少,堆焊层致密无缩松,表面有少量渣点,不予清理不影响连续多层焊接,烟尘不大,噪声低。
中速磨煤机磨辊堆焊修复的工艺研究

中速磨煤机磨辊堆焊修复的工艺研究摘要:磨煤机是火力发电厂的重要设备之一,而磨煤机中磨辊又是磨煤机的关键部件,其质量的优劣,特别是耐磨性能直接影响到制粉的作业率、煤粉质量、磨辊消耗和生产成本。
由于任何磨辊材料,在制粉工况条件下,都有较为严重的磨损,磨辊在一定程度的磨损范围内,仍能正常工作。
当磨损程度达到某一限度后,外圆过小就失去使用意义,即报废处理。
因此,国内外都在大力研究复合铸铁及堆焊磨辊等工艺,其目的就是制造一种新的复合磨辊,使磨辊基体与工作表面分别满足于磨煤时的抗冲击、耐磨损等性能要求。
其中,磨辊表面堆焊制造已成为国内外制造、修复磨辊及延长磨辊使用寿命的一个重要手段。
采用特制的高铬高碳药芯焊丝,对旧的中速磨煤机磨辊进行堆焊修复,可获得性能较为优异的耐磨层,修复后磨辊经现场运行考核,可有效地提高使用寿命,经济效益和社会效益显著。
关键词:中速磨煤机;磨辊;堆焊修复工艺1磨辊失效原因分析磨辊失效形式主要是煤对磨辊及磨盘的摩擦损耗产生的三体磨料磨损,在磨料磨损中磨料硬度是一个重要指标,磨料本身的莫氏硬度比较低,为1.0~3.75(相当于HV50-214),但对于磨辊磨损起主要作用的却是煤中含有的矿物杂质,以粘土、方解石、石英和黄铁矿为主,他们的硬度在HV1000左右,远远大于磨料的硬度,特别是煤矸石的存在使得磨损表面产生塑性变形而形成犁沟,加上磨粒压入磨损表面或磨粒对磨损表面的严重划伤,磨损材料中磨沟增多并明显变深变宽,最终导致磨辊寿命大大降低。
2提高堆焊式磨辊耐磨的方法2.1堆焊材料的选择目前国内堆焊材料种类较多,从化学成分来看有低合金钢及高锰钢等,低合金钢在抵抗意外冲击形变方面确有优良的性能,具有较强的硬度。
但其主要缺点是生产中的碎裂。
而作为靠加工硬化来提高耐磨性的高锰钢,在低应力的磨辊磨料磨损中其作用很难得到发挥。
目前国外广泛使用高碳铬铁,因为它具有较高的韧性及抗磨性,同时在该合金系中加入钒、硼、钼、钨等合金元素后其耐磨性明显提高。
磨辊 磨盘、轧辊、轴齿等硬面堆焊修复技术及施工方案
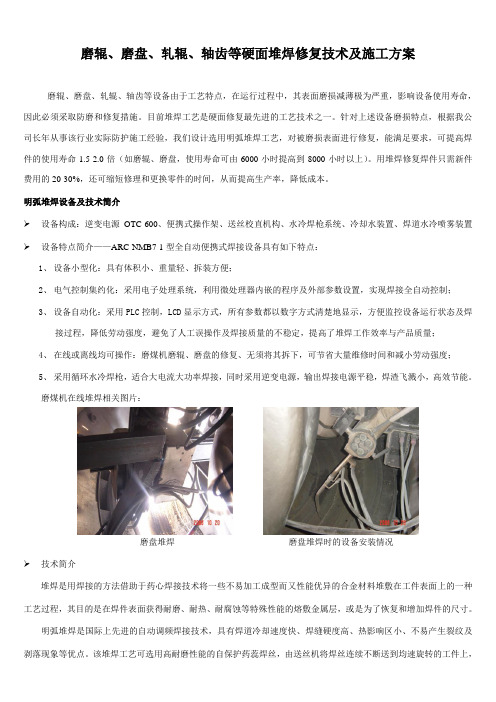
磨辊、磨盘、轧辊、轴齿等硬面堆焊修复技术及施工方案磨辊、磨盘、轧辊、轴齿等设备由于工艺特点,在运行过程中,其表面磨损减薄极为严重,影响设备使用寿命,因此必须采取防磨和修复措施。
目前堆焊工艺是硬面修复最先进的工艺技术之一。
针对上述设备磨损特点,根据我公司长年从事该行业实际防护施工经验,我们设计选用明弧堆焊工艺,对被磨损表面进行修复,能满足要求,可提高焊件的使用寿命1.5-2.0倍(如磨辊、磨盘,使用寿命可由6000小时提高到8000小时以上)。
用堆焊修复焊件只需新件费用的20-30%,还可缩短修理和更换零件的时间,从而提高生产率,降低成本。
明弧堆焊设备及技术简介➢设备构成:逆变电源OTC-600、便携式操作架、送丝校直机构、水冷焊枪系统、冷却水装置、焊道水冷喷雾装置➢设备特点简介——ARC-NMB7-1型全自动便携式焊接设备具有如下特点:1、设备小型化:具有体积小、重量轻、拆装方便;2、电气控制集约化:采用电子处理系统,利用微处理器内嵌的程序及外部参数设置,实现焊接全自动控制;3、设备自动化:采用PLC控制,LCD显示方式,所有参数都以数字方式清楚地显示,方便监控设备运行状态及焊接过程,降低劳动强度,避免了人工误操作及焊接质量的不稳定,提高了堆焊工作效率与产品质量;4、在线或离线均可操作:磨煤机磨辊、磨盘的修复、无须将其拆下,可节省大量维修时间和减小劳动强度;5、采用循环水冷焊枪,适合大电流大功率焊接,同时采用逆变电源,输出焊接电源平稳,焊渣飞溅小,高效节能。
磨煤机在线堆焊相关图片:磨盘堆焊磨盘堆焊时的设备安装情况➢技术简介堆焊是用焊接的方法借助于药心焊接技术将一些不易加工成型而又性能优异的合金材料堆敷在工件表面上的一种工艺过程,其目的是在焊件表面获得耐磨、耐热、耐腐蚀等特殊性能的熔敷金属层,或是为了恢复和增加焊件的尺寸。
明弧堆焊是国际上先进的自动调频焊接技术,具有焊道冷却速度快、焊缝硬度高、热影响区小、不易产生裂纹及剥落现象等优点。
3#辊压机辊面堆焊修复

图二
在十字万向节联轴器位置安装链传动装置, 使辊子进行慢转。
图三
自动焊装置,该装置可以 自动控制横向和纵向的位 置,加链传动装置控制周 向位移,实施对辊面的自
动焊接。
缓冲层焊接
图四
焊剂
焊丝
图五
缓冲层直接焊接至耐 磨层位置,一般预留
耐磨层8mm.
3.5、耐磨层焊接
3.5.1 用TB8106焊条焊接耐磨层,焊接时用模具做 引导,以利于焊接的平整和外圆面的平缓性(图 六)。
3.4、缓冲层焊接
3.4.1 用CS104∮4.0埋弧焊丝进行缓冲层焊 接,该焊丝与母材焊接有较高连接,可抗 较高冲击力和挤压力。
3.4.2 用传动链形式传动装置带动辊子慢转 (图二),同时用直流焊机对辊面进行缓冲 层焊接(图三、四)。
3.4.3 缓冲层焊接时要注意预留耐磨层厚度, 一般耐磨层在250℃的温度下烘干2 个小时。
3.5.3 焊接时电焊机的地线必须直接搭在磨辊上, 否则可能烧坏主轴承,另外焊机电流不宜过大。
3.5.4 焊接时,需要用液化气将辊压机辊面预热至 150-200℃之间(图七),彻底消除因机械加工产 生的油份及残余应力,防止裂纹的产生。
3.5.5 堆焊时注意测量堆焊的高度,要保证辊子的圆 度,以免辊子不圆而导致辊压机振动.
图六
用模具进行引 导堆焊,可以 提高堆焊质量
图七
辊面预热
3.5.6 用TB2106焊条焊接菱形花纹及中间硬 质点,菱形花纹尺寸为50×50.
3.6、退火
• 辊压机辊子加温至150℃-200 ℃,再在表面 用石棉布包住,待辊子自然冷却到常温状态. 主要是为了减少焊接后的残余应力.
四、总结
• 辊压机最大的缺点是辊面磨损严重.所以在 日常的检修过程中,要时刻注意辊面耐磨层 的磨损状况,一旦轻微磨损,要进行及时补焊, 以免造成更严重的后果.同时,要注意辊压机 的使用工况,尽量减少铁器等物件进入辊压 机,只有这样,才能提高辊压机辊面的使用寿 命.
磨辊堆焊操作规程

磨辊堆焊设备操作规程一、焊接前的准备工作:1、确认操作架、变位机及放丝单元各部件的减速箱内已加润滑油,各减速箱内的油位已达到指定位置;2、确认操作架及变位机的链条(丝杠)、各行走轮、牙齿、牙轮、导轨等行走机构已经得到良好的润滑;3、检查操作架、变位机、放丝单元及送丝部分各行走机构是天有障碍及过松过紧的现象;4、观察焊枪冷却装置(水冷器)的水位计,看是否有冷却水,如没有应拧开水冷器顶盖上的塑料盖,注入冷却水,使水位达到水位计的刻度;5、观察焊道自动冷却装置中水箱的水位计,看是否有冷却水,如没有应注入一定量的冷却水,使水位达到水位计的刻度;6、合上总电源开关,将控制柜的电源打开,控制变位机单元、操作架单元、放丝单元、送丝单元、十字滑架单元,观察各单元的转动部分是否灵活动作;7、把变位机翻转至水平位置,将工装安装在工作台上,在安装时应保证工装处于工作台的中心位置;8、将磨煤辊装于工装上,在安装时使磨煤辊与工作台处于平行状态;9、安装焊丝:9.1、将焊丝从放丝盘中拉出,把焊丝插入送丝轮中,当焊丝伸到送丝机时,按送丝单元中的进按钮,焊丝将沿着送丝机送入导电嘴;9.2、当焊丝伸出导电嘴时,利用控制柜(或手操盒)上送丝单元中的进、退按钮,使焊丝的干伸长保持在25—35mm之间;9.3、将控制柜上送丝单元中的速度调节旋钮旋转到2.8—3.5之间(如用远调,则应将手操盒上的焊接电流调节旋钮旋转到2.8—3.5之间);10、定位工作台:10.1、通过控制柜(或手操盒)上变位机单元中的翻上、翻下按钮将变位机翻转到工件表面的待焊部分呈水平位置;10.2、利用控制柜(或手操盒)上变位机单元中的正转、反转按钮调节焊道的连接处;10.3、将控制柜(或手操盒)上的变位机转速调节旋钮旋转到0.9—1.2之间;11、定位焊嘴的位置:11.1、通过控制柜(或手操盒)上操作架单元中的伸、缩按钮将焊枪调整到待焊工件上方;11.2、通过控制柜(或手操盒)上操作架单元中的升、降按钮将焊枪的高度粗调到焊嘴距工件表面约40mm左右;11.3、利用控制柜(或手操盒)上十字滑架单元中的上、下按钮细调焊枪的高度,使焊嘴距工件表面的距离保持在25mm—35mm之间;11.4、利用控制柜(或手操盒)上十字滑架单元中的左、右按钮调整焊枪的左、右位置,从而达到各种焊接工艺;12、设定控制柜的参数:12.1、将主控单元中的控制方式切换到远控方式,焊接方式切换到正焊及环焊状态(系统初始状态为近控方式,如用控制柜操作,这步操作可省去);12.2、将变位机单元中的调节方式切换到远调方式(系统初始状态为近调方式,如用控制柜操作,这步操作可省去);12.3、将送丝单元中的调节方式切换到远调方式(系统初始状态为近调方式,如用控制柜操作,这步操作可省去);12.4、将操作架单元中的进、退按钮根据焊接方式选择进或退(系统初始状态为进的模式);12.5、将操作架单元中的速度调节旋钮调到20左右(此参数的调节还要根据实际的焊接工艺确定);12.6、将放丝单元中的速度调节旋钮调到10左右(此参数的调节还要根据实际的送丝速度确定);13、合上焊接电源空气开关,将焊接方式开关切换到恒压方式,将控制方式开关切换到遥控方式(如控制模式开关切换在机控时,这时应旋转电压调节旋钮到8左右);14、按下除尘器上的启动按钮;二、焊接过程:按控制柜(或手操盒)上主控单元中的焊启按钮,焊枪水冷器开始工作,焊道自动冷却装置工作,变位机工作台回转,放丝系统开始放丝,送丝机开始自动送丝,焊丝自动刮擦起弧,焊接开始,除尘器开始工作。
中速磨磨辊堆焊工艺操作规范

中速磨磨辊堆焊工艺操作规范Document serial number【KK89K-LLS98YT-SS8CB-SSUT-SST108】堆焊工艺流程(修改后)1、外观检查,仔细检查磨辊裂纹情况,有较长贯穿裂纹的需要及时报告并派专人与跟电厂协商,有局部密集裂纹导致焊层有脱落风险的应去除,存在较大凹坑的地方需提前手工补焊;2、除锈:用角磨机安装铁刷子进行打磨,直到露出金属光泽;3,使用高压气体吹磨辊表面,去除表面的煤粉,尤其是裂纹内部的煤粉切记除尽,否则会造成气孔、断弧,严重的导致堆焊层脱落。
4、当磨辊环境温度低于10℃时,需要使用氧乙炔火焰加热,将磨辊表面加热到50-60℃,否则将影响焊接质量,严重的导致堆焊层脱落。
火焰加热不得使磨辊套的温度升高至250℃,加热要均有,防止磨辊套局部受热爆裂。
5,吊装工具包括吊环、钢丝绳等,以上均满足起重要求,防止断裂。
吊环可以直接安装在磨辊套小头上的螺丝孔上,但不得损坏螺丝孔。
6,将磨辊套安装在变位机上的专用工具上。
在堆焊前压紧,力度适中。
堆焊6h后要重新对严禁螺丝复紧,防止受热膨胀磨辊套位置变化。
7,在掌握基本的设备性能、操作技巧、焊接工艺后,方可开始焊接。
8、堆焊打底层,当磨辊基体为20SiMn或者磨辊基材Mn含量大于1%,Si含量大于0.5%时,先用打底材料YYD-101Mn焊丝,磨辊基体为高铬铸铁则无需打底。
焊接主要设备:焊接电源(硅整流或逆变电源)、变位机、控制中心等。
极性:直流反接。
明弧自动焊电流:360~420A。
电弧电压:32~36V。
(目的是提高温度,增大熔深)焊接线速度:300~1000mm/min。
合理焊道参数:宽10mm,高3mm,后一道近似覆盖前一道的40%。
冷却方式:明弧自动焊采用高压雾状水冷或空冷,保证母材通体温度在120℃以下。
打底层根据磨辊材质堆焊,一般不超过2层。
9、堆焊中间层,材料使用YYD-100VMo焊丝,焊接主要设备:焊接电源(硅整流或逆变电源)、变位机、控制中心等。
磨辊堆焊工艺

磨辊堆焊工艺哎,说起磨辊堆焊工艺,这可真是个技术活儿,得有两把刷子才行。
我有个哥们儿,他可是干这行的老手了,每次听他讲起这个,我都听得津津有味的。
这哥们儿告诉我,磨辊堆焊,简单来说,就是给磨辊穿上一件“铁甲”,让它更耐磨、更耐用。
这活儿可不简单,得精确控制,一点差错都不能有。
他给我讲了一次他亲身经历的堆焊过程,那细节,听得我目瞪口呆。
那天,他一大早就到了工厂,换上了工作服,戴上了安全帽和护目镜。
他说,安全第一,这是必须的。
然后,他就开始检查设备,什么焊机啊、焊条啊,都得一一检查,确保一切正常。
他告诉我,这就像战士上战场前检查武器一样,马虎不得。
接下来,就是堆焊的重头戏了。
他把磨辊固定在工作台上,然后开始预热。
他说,预热很重要,能让金属表面达到一个合适的温度,这样焊条熔化后,就能更好地和磨辊融合在一起。
他一边说,一边调整着温度,那专注的样子,就像在进行一场精密的手术。
预热完成后,他就开始堆焊了。
他拿着焊枪,一点一点地在磨辊上堆焊。
他说,这得慢慢来,不能急。
每一道焊缝都要均匀,不能有气泡,也不能有裂缝。
他一边焊,一边用小锤子敲击焊缝,说是这样可以释放应力,防止焊缝开裂。
焊完后,他还得检查一遍,看看有没有漏焊的地方,或者焊缝不均匀的地方。
他说,这就像画家完成一幅画后,总要检查一遍,看看有没有瑕疵。
最后,就是清理和打磨了。
他用砂轮机一点点地打磨焊缝,直到磨辊表面光滑如新。
他说,这最后的打磨,就像给磨辊穿上了一件新衣,让它焕然一新。
听他讲完这个过程,我真是佩服得五体投地。
这磨辊堆焊工艺,看似简单,实则复杂,需要精湛的技艺和极大的耐心。
我那哥们儿,就是靠着这门手艺,赢得了大家的尊重和认可。
每次看到他那专注工作的样子,我都忍不住想,这才是真正的工匠精神啊!。
辊压机现场堆焊
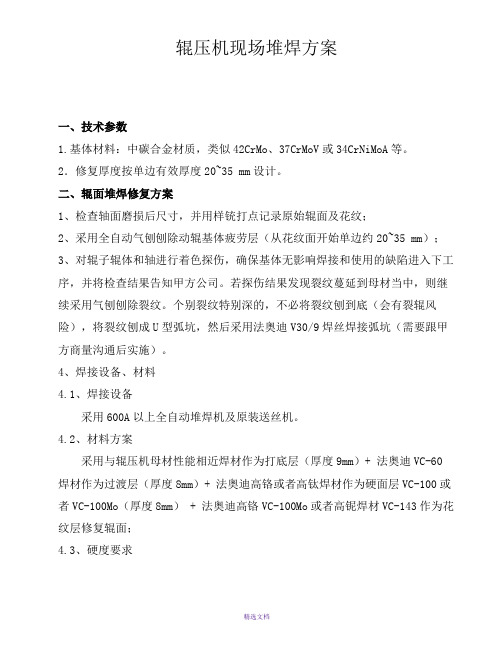
辊压机现场堆焊方案一、技术参数1.基体材料:中碳合金材质,类似42CrMo、37CrMoV或34CrNiMoA等。
2.修复厚度按单边有效厚度20~35 mm设计。
二、辊面堆焊修复方案1、检查轴面磨损后尺寸,并用样铳打点记录原始辊面及花纹;2、采用全自动气刨刨除动辊基体疲劳层(从花纹面开始单边约20~35 mm);3、对辊子辊体和轴进行着色探伤,确保基体无影响焊接和使用的缺陷进入下工序,并将检查结果告知甲方公司。
若探伤结果发现裂纹蔓延到母材当中,则继续采用气刨刨除裂纹。
个别裂纹特别深的,不必将裂纹刨到底(会有裂辊风险),将裂纹刨成U型弧坑,然后采用法奥迪V30/9焊丝焊接弧坑(需要跟甲方商量沟通后实施)。
4、焊接设备、材料4.1、焊接设备采用600A以上全自动堆焊机及原装送丝机。
4.2、材料方案采用与辊压机母材性能相近焊材作为打底层(厚度9mm)+ 法奥迪VC-60焊材作为过渡层(厚度8mm)+ 法奥迪高铬或者高钛焊材作为硬面层VC-100或者VC-100Mo(厚度8mm) + 法奥迪高铬VC-100Mo或者高铌焊材VC-143作为花纹层修复辊面;4.3、硬度要求辊面:打底层180—220HB,过度层工作硬化情况下硬度为HRC40-50,硬面层HRC55—58,花纹层HRC58—62,各焊层整个层厚硬度均匀。
5、工艺5.1、清理打磨待焊面,去除铁锈和油污,使之露出金属光泽。
5.2、采用多头氧乙炔火焰器预热辊面,达到温度100℃左右。
5.3、堆焊辊面:采用自动明弧焊工艺堆焊辊面凹坑及打底层,过渡层和硬面层,焊丝直径2.8mm,焊接电流350±10A,焊接弧压30±5V,线速度大约0.6~0.9m/min,堆焊打底层时控制层间温度不低于预热温度。
5.4、焊完采用石棉布缓冷到室温。
5.5、法奥迪VC-60材料堆焊两侧面。
5.6、外形辊面检查,堆焊后外形符合图纸尺寸。
5.7、整个堆焊过程中保护好非修复部位,并检测轴温,若轴温大于70℃立即采用风冷或者水冷方式冷却轴。
- 1、下载文档前请自行甄别文档内容的完整性,平台不提供额外的编辑、内容补充、找答案等附加服务。
- 2、"仅部分预览"的文档,不可在线预览部分如存在完整性等问题,可反馈申请退款(可完整预览的文档不适用该条件!)。
- 3、如文档侵犯您的权益,请联系客服反馈,我们会尽快为您处理(人工客服工作时间:9:00-18:30)。
中速磨磨辊堆焊工艺流
程
Document number:WTWYT-WYWY-BTGTT-YTTYU-2018GT
堆焊工艺流程(修改后)
1、外观检查,仔细检查磨辊裂纹情况,有较长贯穿裂纹的需要及时报告并派专人与跟电厂协商,有局部密集裂纹导致焊层有脱落风险的应去除,存在较大凹坑的地方需提前手工补焊;
2、除锈:用角磨机安装铁刷子进行打磨,直到露出金属光泽;
3,使用高压气体吹磨辊表面,去除表面的煤粉,尤其是裂纹内部的煤粉切记除尽,否则会造成气孔、断弧,严重的导致堆焊层脱落。
4、当磨辊环境温度低于10℃时,需要使用氧乙炔火焰加热,将磨辊表面加热到50-60℃,否则将影响焊接质量,严重的导致堆焊层脱落。
火焰加热不得使磨辊套的温度升高至 250℃,加热要均有,防止磨辊套局部受热爆裂。
5,吊装工具包括吊环、钢丝绳等,以上均满足起重要求,防止断裂。
吊环可以直接安装在磨辊套小头上的螺丝孔上,但不得损坏螺丝孔。
6,将磨辊套安装在变位机上的专用工具上。
在堆焊前压紧,力度适中。
堆焊 6h 后要重新对严禁螺丝复紧,防止受热膨胀磨辊套位置变化。
7,在掌握基本的设备性能、操作技巧、焊接工艺后,方可开始焊接。
8、堆焊打底层,当磨辊基体为20SiMn或者磨辊基材Mn含量大于1%,Si含量大于%时,先用打底材料YYD-101Mn焊丝,磨辊基体为高铬铸铁则无需打底。
焊接主要设备:焊接电源(硅整流或逆变电源)、变位机、控制中心等。
极性:直流反接。
明弧自动焊电流:360~420A。
电弧电压:32~36V。
(目的是提高温度,增大熔深)
焊接线速度: 300~1000mm/min。
合理焊道参数:宽 10mm,高 3mm,后一道近似覆盖前一道的 40%。
冷却方式:明弧自动焊采用高压雾状水冷或空冷,保证母材通体温度在120℃以下。
打底层根据磨辊材质堆焊,一般不超过2层。
9、堆焊中间层,材料使用YYD-100VMo焊丝,
焊接主要设备:焊接电源(硅整流或逆变电源)、变位机、控制中心等。
极性:直流反接。
明弧自动焊电流:360~400A。
电弧电压:30~35V。
焊接线速度: 300~1000mm/min。
合理焊道参数:宽 10mm,高 3mm,后一道近似覆盖前一道的 40%。
冷却方式:明弧自动焊采用高压雾状水冷或空冷,保证母材通体温度在120℃以下。
10、堆焊最后一层(盖面层最多不超过2层),材料使用YYD-150焊丝,
焊接主要设备:焊接电源(硅整流或逆变电源)、变位机、控制中心等。
极性:直流反接。
明弧自动焊电流:360~400A。
电弧电压:28~34V。
焊接线速度: 300~700mm/min。
合理焊道参数:宽 12mm,高 3mm,后一道近似覆盖前一道的 25%。
(目的焊道堆焊层要饱满、连续、均匀、美观,便于电厂检测硬度指标)
冷却方式:明弧自动焊采用高压雾状水冷或空冷,保证母材通体温度在120℃以下。
堆焊后表面宏观硬度: HRC58~62。
11,用制作的专用测量卡具对磨辊套进行测量,尺寸不足时继续堆焊。
测量时注意多点测量,检查出高点、低点,然后有针对性的堆焊,直到磨辊套多点测量尺寸基本一致。
12,堆焊结束后,利用起吊设备将磨辊套吊出,放置在枕木上,在室内空气中均匀冷却,不得置于室外钢件上,防止冷却速度的不同导致磨辊套爆裂。
13,堆焊YYD-200VMo及YYD-300V时工艺参数基本与YYD-100Mo一致。
焊接主要设备:焊接电源(硅整流或逆变电源)、变位机、控制中心等。
极性:直流反接。
明弧自动焊电流:360~400A。
电弧电压:30~35V。
焊接线速度: 300~1000mm/min。
合理焊道参数:宽 10mm,高 3mm,后一道近似覆盖前一道的 40%。
冷却方式:明弧自动焊采用高压雾状水冷或空冷,保证母材通体温度在120℃以下。
14,YYD-300V盖面与上述盖面参数一致。
焊接主要设备:焊接电源(硅整流或逆变电源)、变位机、控制中心等。
极性:直流反接。
明弧自动焊电流:360~400A。
电弧电压:28~34V。
焊接线速度: 300~700mm/min。
合理焊道参数:宽 12mm,高 3mm,后一道近似覆盖前一道的 25%。
(目的焊道堆焊层要饱满、连续、均匀、美观,便于电厂检测硬度指标)
冷却方式:明弧自动焊采用高压雾状水冷或空冷,保证母材通体温度在120℃以下。