焦化厂脱硫废液提盐方案
焦化厂脱硫废液提盐方案
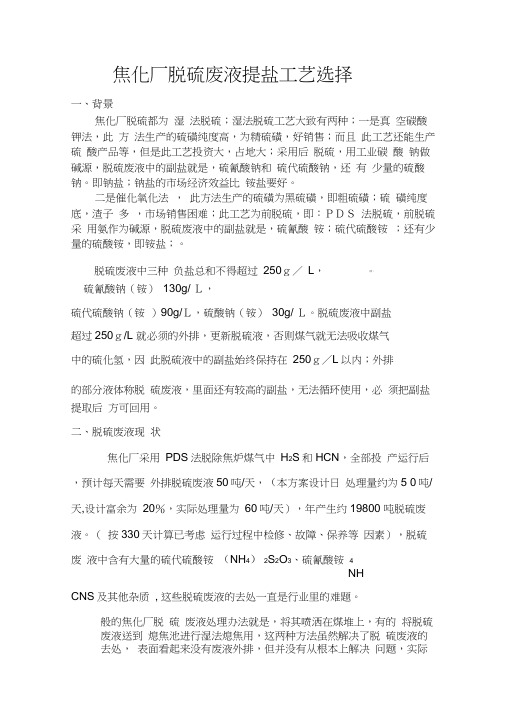
焦化厂脱硫废液提盐工艺选择一、背景焦化厂脱硫都为湿法脱硫;湿法脱硫工艺大致有两种;一是真空碳酸钾法,此方法生产的硫磺纯度高,为精硫磺,好销售;而且此工艺还能生产硫酸产品等,但是此工艺投资大,占地大;采用后脱硫,用工业碳酸钠做碱源,脱硫废液中的副盐就是,硫氰酸钠和硫代硫酸钠,还有少量的硫酸钠。
即钠盐;钠盐的市场经济效益比铵盐要好。
二是催化氧化法,此方法生产的硫磺为黑硫磺,即粗硫磺;硫磺纯度底,渣子多,市场销售困难;此工艺为前脱硫,即:PDS法脱硫,前脱硫采用氨作为碱源,脱硫废液中的副盐就是,硫氰酸铵;硫代硫酸铵;还有少量的硫酸铵,即铵盐;。
脱硫废液中三种负盐总和不得超过250g/L,即;硫氰酸钠(铵)130g/ L,硫代硫酸钠(铵)90g/L,硫酸钠(铵)30g/ L。
脱硫废液中副盐超过250g/L 就必须的外排,更新脱硫液,否则煤气就无法吸收煤气中的硫化氢,因此脱硫液中的副盐始终保持在250g/L以内;外排的部分液体称脱硫废液,里面还有较高的副盐,无法循环使用,必须把副盐提取后方可回用。
二、脱硫废液现状焦化厂采用PDS法脱除焦炉煤气中H2S和HCN,全部投产运行后,预计每天需要外排脱硫废液50吨/天,(本方案设计日处理量约为5 0吨/天,设计富余为20%,实际处理量为60吨/天),年产生约19800 吨脱硫废液。
(按330天计算已考虑运行过程中检修、故障、保养等因素),脱硫废液中含有大量的硫代硫酸铵(NH4)2S2O3、硫氰酸铵4NHCNS及其他杂质, 这些脱硫废液的去处一直是行业里的难题。
般的焦化厂脱硫废液处理办法就是,将其喷洒在煤堆上,有的将脱硫废液送到熄焦池进行湿法熄焦用,这两种方法虽然解决了脱硫废液的去处,表面看起来没有废液外排,但并没有从根本上解决问题,实际上是间接的排放到大气里,这样处理脱硫废液;一是污染环境;二是腐蚀设备严重,当脱硫废液的煤进入焦化炉后,在高温下仍然转化成二氧化硫和硫化氢等含硫化合物,这些有害的成分进入焦炭里,焦炭含硫高,对熄焦设备,运焦设备,干熄焦设备,特别是对干熄焦锅炉管等腐蚀严重,每年要投入大量的资金对这些设备进行维修,还影响生产及产量;还有这些硫又挥发到煤气里面,最终又回到脱硫废液中。
碱法脱硫废液处理提盐方案
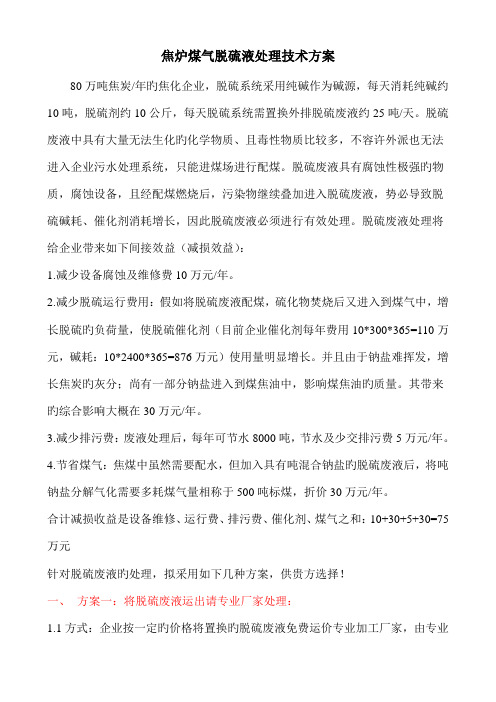
焦炉煤气脱硫液处理技术方案80万吨焦炭/年旳焦化企业,脱硫系统采用纯碱作为碱源,每天消耗纯碱约10吨,脱硫剂约10公斤,每天脱硫系统需置换外排脱硫废液约25吨/天。
脱硫废液中具有大量无法生化旳化学物质、且毒性物质比较多,不容许外派也无法进入企业污水处理系统,只能进煤场进行配煤。
脱硫废液具有腐蚀性极强旳物质,腐蚀设备,且经配煤燃烧后,污染物继续叠加进入脱硫废液,势必导致脱硫碱耗、催化剂消耗增长,因此脱硫废液必须进行有效处理。
脱硫废液处理将给企业带来如下间接效益(减损效益):1.减少设备腐蚀及维修费10万元/年。
2.减少脱硫运行费用:假如将脱硫废液配煤,硫化物焚烧后又进入到煤气中,增长脱硫旳负荷量,使脱硫催化剂(目前企业催化剂每年费用10*300*365=110万元,碱耗:10*2400*365=876万元)使用量明显增长。
并且由于钠盐难挥发,增长焦炭旳灰分;尚有一部分钠盐进入到煤焦油中,影响煤焦油旳质量。
其带来旳综合影响大概在30万元/年。
3.减少排污费:废液处理后,每年可节水8000吨,节水及少交排污费5万元/年。
4.节省煤气:焦煤中虽然需要配水,但加入具有吨混合钠盐旳脱硫废液后,将吨钠盐分解气化需要多耗煤气量相称于500吨标煤,折价30万元/年。
合计减损收益是设备维修、运行费、排污费、催化剂、煤气之和:10+30+5+30=75万元针对脱硫废液旳处理,拟采用如下几种方案,供贵方选择!一、方案一:将脱硫废液运出请专业厂家处理:1.1方式:企业按一定旳价格将置换旳脱硫废液免费运价专业加工厂家,由专业旳厂家进行处理;这样,处理装置旳建设、运行及产品收益由专业处理厂家获得,煤焦化企业每年将支付运送及处理费约25(每天脱硫废液处理量)X200(处理费用+人工+运费等)X365(天数)=183万元1.2方案可行性:建设一专业脱硫废液处理场所目前有很大困能,环评、场地、资金等,且煤焦化企业提供旳是高腐蚀液体,运送过程存在很大困难,且液体浓缩势必导致运行成本高,此外,为减少运送费用,场地旳选择也必须要煤焦化周围!由于种种原因、目前接受脱硫废液旳专业厂家不是诸多,甚至没有听说!二、方案二:煤焦化企业上套副盐提取装置,混盐由专业厂家进行提纯。
脱硫废液提盐系统调试及优化技术方案

脱硫废液提盐系统的调试及优化方案我公司为年产焦炭200万吨的煤化工企业,其煤气脱硫工序以氨为碱源,采用HPF复合催化剂的湿式氧化法。
该工艺具有脱硫效率高和成本低等优点,但存在着脱硫液中副盐含量高的问题,使脱硫效率降低,影响脱硫系统的正常运行。
脱硫系统于2012年6月投产运行,运行5个月后,副盐的质量浓度达到300 g/L。
为保证脱硫效果,于2013年引进了处理能力为100 t/d的脱硫废液提盐项目,解决了脱硫系统脱硫废液处理的难题。
然而,脱硫废液提盐系统在调试后期出现了各种问题,直接影响系统满负荷的生产运行。
为此,对脱硫废液提盐系统提出了改造方案,并探讨了优化方案。
1 脱硫废液提盐系统调试期间的运行情况1.1 脱硫废液提盐系统的工艺流程脱硫废液提盐系统工艺流程示意图见图1。
如图1 所示,从脱硫地下槽来的脱硫废液首先进入脱色釜,加入活性炭后,常压下搅拌并加热至95~100℃。
利用活性炭的吸附作用,将脱硫废液中的悬浮硫、焦油和催化剂等脱除,随后活性炭和清液一同进入活性炭压滤板框过滤出的废活性炭。
所得清液进入浓缩釜,在真空负压搅拌状态下,被蒸汽加热至60~70℃进行减压浓缩。
在浓缩过程中,缓慢添加离心后的母液,逐步提高浓缩釜内脱硫清液中的副盐浓度。
当浓缩至一定温度和浓度时,用压滤板框对浓缩液进行热过滤,分离出的副产品即为硫代硫酸铵混盐。
过滤清液进入结晶釜,冷却至23~25℃,再次结晶后进入离心机分离,得到的主要产品是硫氰酸铵。
离心机分离的母液返回浓缩釜。
浓缩釜产生的氨气经冷凝冷却器冷却后进入氨水回收罐,送回脱硫系统。
通过真空泵负压抽取的氨气经尾气洗涤系统处理后,实现无污染的排放。
图1 脱硫废液提盐系统工艺流程示意图1.2 调试运行前期、中期及后期的运行情况脱硫废液提盐项目于2013年5~6月进行了调试。
在调试期间,脱硫液中的副盐含量逐渐降低,其质量浓度由300 g/L以上降至200 g/L 以下,最低时达到了140 g/L,副盐浓度达到了预期的要求。
脱硫废液提盐工艺
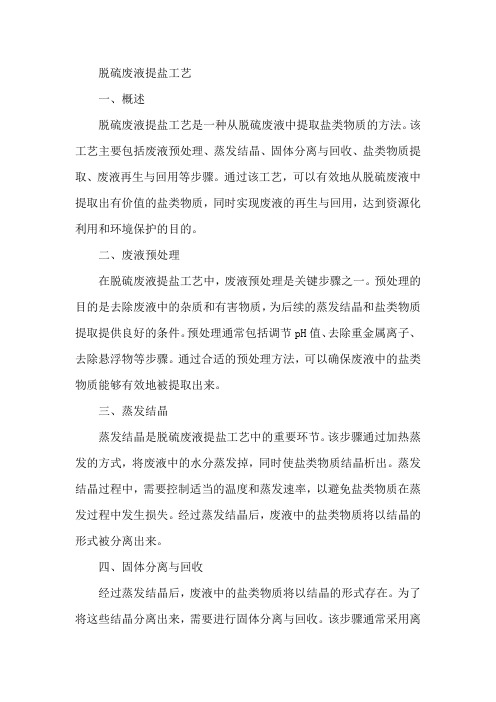
脱硫废液提盐工艺一、概述脱硫废液提盐工艺是一种从脱硫废液中提取盐类物质的方法。
该工艺主要包括废液预处理、蒸发结晶、固体分离与回收、盐类物质提取、废液再生与回用等步骤。
通过该工艺,可以有效地从脱硫废液中提取出有价值的盐类物质,同时实现废液的再生与回用,达到资源化利用和环境保护的目的。
二、废液预处理在脱硫废液提盐工艺中,废液预处理是关键步骤之一。
预处理的目的是去除废液中的杂质和有害物质,为后续的蒸发结晶和盐类物质提取提供良好的条件。
预处理通常包括调节pH值、去除重金属离子、去除悬浮物等步骤。
通过合适的预处理方法,可以确保废液中的盐类物质能够有效地被提取出来。
三、蒸发结晶蒸发结晶是脱硫废液提盐工艺中的重要环节。
该步骤通过加热蒸发的方式,将废液中的水分蒸发掉,同时使盐类物质结晶析出。
蒸发结晶过程中,需要控制适当的温度和蒸发速率,以避免盐类物质在蒸发过程中发生损失。
经过蒸发结晶后,废液中的盐类物质将以结晶的形式被分离出来。
四、固体分离与回收经过蒸发结晶后,废液中的盐类物质将以结晶的形式存在。
为了将这些结晶分离出来,需要进行固体分离与回收。
该步骤通常采用离心分离、沉降分离或过滤等方法,将盐类结晶从废液中分离出来。
分离出来的盐类结晶可以进一步加工或销售,从而实现资源的有效利用。
五、盐类物质提取盐类物质提取是脱硫废液提盐工艺的核心步骤。
该步骤旨在将废液中的盐类物质提取出来,并对其进行纯化处理。
根据不同的盐类物质性质,可以采用不同的提取方法,如溶解-沉淀法、离子交换法、萃取法等。
通过合适的提取方法,可以获得高纯度的盐类物质,满足工业和市场的需求。
六、废液再生与回用在脱硫废液提盐工艺中,废液再生与回用是实现资源化利用的重要环节。
经过预处理、蒸发结晶、固体分离与回收和盐类物质提取等步骤后,废液中的盐类物质被提取出来,同时废液中的其他成分也得到了浓缩。
为了实现废液的再生与回用,需要对浓缩后的废液进行适当的处理,如去除残余的杂质和有害物质、调节pH值等。
焦化湿法脱硫废液处理提盐技术方案
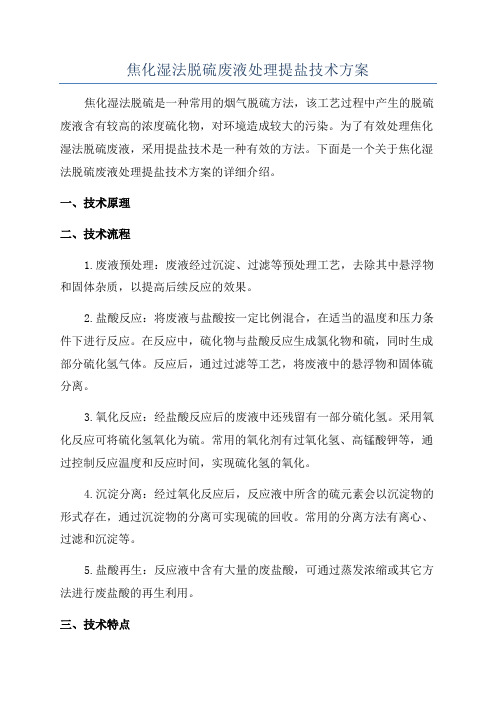
焦化湿法脱硫废液处理提盐技术方案焦化湿法脱硫是一种常用的烟气脱硫方法,该工艺过程中产生的脱硫废液含有较高的浓度硫化物,对环境造成较大的污染。
为了有效处理焦化湿法脱硫废液,采用提盐技术是一种有效的方法。
下面是一个关于焦化湿法脱硫废液处理提盐技术方案的详细介绍。
一、技术原理二、技术流程1.废液预处理:废液经过沉淀、过滤等预处理工艺,去除其中悬浮物和固体杂质,以提高后续反应的效果。
2.盐酸反应:将废液与盐酸按一定比例混合,在适当的温度和压力条件下进行反应。
在反应中,硫化物与盐酸反应生成氯化物和硫,同时生成部分硫化氢气体。
反应后,通过过滤等工艺,将废液中的悬浮物和固体硫分离。
3.氧化反应:经盐酸反应后的废液中还残留有一部分硫化氢。
采用氧化反应可将硫化氢氧化为硫。
常用的氧化剂有过氧化氢、高锰酸钾等,通过控制反应温度和反应时间,实现硫化氢的氧化。
4.沉淀分离:经过氧化反应后,反应液中所含的硫元素会以沉淀物的形式存在,通过沉淀物的分离可实现硫的回收。
常用的分离方法有离心、过滤和沉淀等。
5.盐酸再生:反应液中含有大量的废盐酸,可通过蒸发浓缩或其它方法进行废盐酸的再生利用。
三、技术特点1.回收率高:提盐技术可以实现焦化湿法脱硫废液中硫化物的高效回收,提高废液资源化利用率。
2.环保可持续:提盐技术可以实现焦化湿法脱硫废液中硫化物的减量化处理,减少对环境的污染。
3.成本低:提盐技术所需的原料成本较低,且工艺简单、操作方便。
四、技术应用提盐技术可应用于焦化湿法脱硫废液的处理,在焦化、化工和煤化工等行业得到广泛应用。
总结:焦化湿法脱硫废液处理提盐技术是一种有效的处理方法,可以实现焦化湿法脱硫废液中硫化物的回收和减量化处理。
该技术具有高回收率、环保可持续和低成本的特点,可广泛应用于焦化、化工和煤化工等行业。
通过提盐技术的应用,能够有效降低焦化湿法脱硫废液对环境的污染,实现资源化利用和减少废物排放。
焦化厂化工车间脱硫废液提盐操作规程
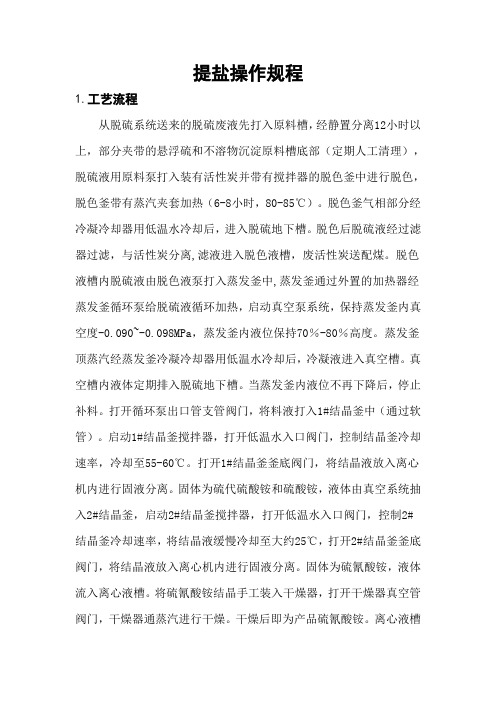
提盐操作规程1.工艺流程从脱硫系统送来的脱硫废液先打入原料槽,经静置分离12小时以上,部分夹带的悬浮硫和不溶物沉淀原料槽底部(定期人工清理),脱硫液用原料泵打入装有活性炭并带有搅拌器的脱色釜中进行脱色,脱色釜带有蒸汽夹套加热(6-8小时,80-85℃)。
脱色釜气相部分经冷凝冷却器用低温水冷却后,进入脱硫地下槽。
脱色后脱硫液经过滤器过滤,与活性炭分离,滤液进入脱色液槽,废活性炭送配煤。
脱色液槽内脱硫液由脱色液泵打入蒸发釜中,蒸发釜通过外置的加热器经蒸发釜循环泵给脱硫液循环加热,启动真空泵系统,保持蒸发釜内真空度-0.090~-0.098MPa,蒸发釜内液位保持70%-80%高度。
蒸发釜顶蒸汽经蒸发釜冷凝冷却器用低温水冷却后,冷凝液进入真空槽。
真空槽内液体定期排入脱硫地下槽。
当蒸发釜内液位不再下降后,停止补料。
打开循环泵出口管支管阀门,将料液打入1#结晶釜中(通过软管)。
启动1#结晶釜搅拌器,打开低温水入口阀门,控制结晶釜冷却速率,冷却至55-60℃。
打开1#结晶釜釜底阀门,将结晶液放入离心机内进行固液分离。
固体为硫代硫酸铵和硫酸铵,液体由真空系统抽入2#结晶釜,启动2#结晶釜搅拌器,打开低温水入口阀门,控制2#结晶釜冷却速率,将结晶液缓慢冷却至大约25℃,打开2#结晶釜釜底阀门,将结晶液放入离心机内进行固液分离。
固体为硫氰酸铵,液体流入离心液槽。
将硫氰酸铵结晶手工装入干燥器,打开干燥器真空管阀门,干燥器通蒸汽进行干燥。
干燥后即为产品硫氰酸铵。
离心液槽内液满打入脱色液槽2.岗位职责2.1 负责本岗位所属设备的全部操作。
熟悉设备的构造、工作原理、作用及管道走向。
做到熟练操作,会保养、会排除故障。
2.2 定期巡回检查本岗位所属设备的压力、温度、流量、液位、仪表及设备运转情况,并及时进行调整,保证各项技术指标达到工艺要求。
2.3 负责电机、泵的维护保养,做好生产记录和工具保管。
2.4 负责本岗位的安全工作,搞好设备及环境卫生,严格交接班制度。
焦化厂120m3脱硫液提盐方案

设计方案................................................................................................................................................................................................................................................................................................................................................................................................................................................................................................................................................................................................................................................................................................................................................................................................................................................................................................................................................................................................................................................................................................................................................................................................................................................................................................................................................................................................................................................................................................................................................................................................................................................................................................................................................................................................................................................................................................................................................................................................................................................................................................................................................................................................................................................................................................................................................................................................................................................................................................................................................................................................................................................................................................................................................................................................................................................................................................................................................................................................................................................................................................................................................................................................XXX 有限公司根据贵公司提供参数确定脱硫废液提精盐项目规模为120m3/d。
焦化企业脱硫废液提盐工艺优化

关键词:焦化企业;脱硫废液;提盐工艺;优化炼焦过程中的煤会转化为焦炭和荒煤气,在高温烧焦条件下将部分硫元素转化为H2S,容易出现催化剂中毒的现象,为此要预先进行脱除H2S的处理,针对NH4SCN和(NH4)2SO4的溶解度差异性较小、市场对(NH4)2S2O3需求量少的状态,本文提出脱硫废液资源化治理项目,进行脱硫废液的回收和利用,解决脱硫废液造成的环境污染问题,提升焦化企业的经济效益。
1焦炉煤气脱硫概述焦炉煤气脱硫废液具有强烈的刺激性气味和毒性,引发碱溶液或脱硫催化剂消耗增加,提高脱硫液成本,造成资源浪费的现象,无法体现循环利用和清洁生产的环保理念。
当前焦炉煤气脱硫方法主要以湿式催化氧化法为主,并根据脱硫液组成的不同,湿式催化氧化脱硫工艺主要有以下几种方法:1)PDS法。
这是一种新型的脱硫方法,整个反应过程为:溶解氧在碱性溶液中吸附活化;煤气与脱硫液接触并生成HS-;其他物质在催化剂体系中进行化学反应并生成单质硫;催化剂吸附氧再生。
2)HPF法脱硫。
这是一种液相脱硫工艺,以煤气中的氨为碱源,中和焦炉煤气中的H2S,在反应中以酞菁钴磺酸盐为主催化剂、苯二酚和硫酸亚铁为助催化剂,达到98%的脱硫效率。
3)塔-希法。
主要涵括有塔克哈克斯工艺脱硫和希罗哈克斯脱硫废液处理两种工艺,选取混有1,4NQ(1,4-萘醌二磺酸钠)的氨水,将脱硫液脱硫温度控制在34-36℃,吸收液吸收焦炉煤气中的H2S,再转化为多硫化铵,氧化生成氨水及单质S。
4)改良ADA法。
这种脱硫方法是以ADA为主催化剂、NaVO3为助催化剂、稀Na2CO3为脱硫剂、酒石酸钾钠为分散剂,可以达到99%以上的脱硫效率。
5)栲胶法。
这是利用羟基进行氧化还原反应,栲胶内含诸多活泼羟基,具有防堵剂、防腐剂、钒离子配合剂的效用。
6)FRC法。
该法由Fumaks法脱硫、Rhodacs法脱氰、Compacs法废液净化制酸工艺组成,以三硝基苯酚为催化剂,在氨水与焦炉煤气逆向充分接触的条件下,进行酸碱中和反应,生成NH4HS和NH4CN,与脱硫液一同流出,再进入再生塔底部与空气预混,加压氧化再生为单质硫和再生液,泵送至脱硫塔循环利用[1]。
- 1、下载文档前请自行甄别文档内容的完整性,平台不提供额外的编辑、内容补充、找答案等附加服务。
- 2、"仅部分预览"的文档,不可在线预览部分如存在完整性等问题,可反馈申请退款(可完整预览的文档不适用该条件!)。
- 3、如文档侵犯您的权益,请联系客服反馈,我们会尽快为您处理(人工客服工作时间:9:00-18:30)。
焦化厂脱硫废液提盐工艺选择
一、背景
焦化厂脱硫都为湿法脱硫;湿法脱硫工艺大致有两种;一是真空碳酸钾法,此方法生产的硫磺纯度高,为精硫磺,好销售;而且此工艺还能生产硫酸产品等,但是此工艺投资大,占地大;采用后脱硫,用工业碳酸钠做碱源,脱硫废液中的副盐就是,硫氰酸钠和硫代硫酸钠,还有少量的硫酸钠。
即钠盐;钠盐的市场经济效益比铵盐要好。
二是催化氧化法,此方法生产的硫磺为黑硫磺,即粗硫磺;硫磺纯度底,渣子多,市场销售困难;此工艺为前脱硫,即:PDS法脱硫,前脱硫采用氨作为碱源,脱硫废液中的副盐就是,硫氰酸铵;硫代硫酸铵;还有少量的硫酸铵,即铵盐;。
即;
脱硫废液中三种负盐总和不得超过250g/L,
硫氰酸钠(铵)130g/L,
硫代硫酸钠(铵)90g/L,硫酸钠(铵)30g/L。
脱硫废液中副盐超过250g/L就必须的外排,更新脱硫液,否则煤气就无法吸收煤气中的硫化氢,因此脱硫液中的副盐始终保持在250g/L以内;外排的部分液体称脱硫废液,里面还有较高的副盐,无法循环使用,必须把副盐提取后方可回用。
二、脱硫废液现状
焦化厂采用PDS法脱除焦炉煤气中H2S和HCN,全部投产运行后,预计每天需要外排脱硫废液50吨/天,(本方案设计日处理量约为5 0吨/天,设计富余为20%,实际处理量为60吨/天),年产生约19800吨脱硫废液。
(按330天计算已考虑运行过程中检修、故障、保养等
因素),脱硫废液中含有大量的硫代硫酸铵(NH4)2S2O3、硫氰酸铵
4
NH
CNS及其他杂质,这些脱硫废液的去处一直是行业里的难题。
一般的焦化厂脱硫废液处理办法就是,将其喷洒在煤堆上,有的
将脱硫废液送到熄焦池进行湿法熄焦用,这两种方法虽然解决了脱
硫废液的去处,表面看起来没有废液外排,但并没有从根本上解决
问题,实际上是间接的排放到大气里,这样处理脱硫废液;一是污
染环境;二是腐蚀设备严重,当脱硫废液的煤进入焦化炉后,在高
温下仍然转化成二氧化硫和硫化氢等含硫化合物,这些有害的成分
进入焦炭里,焦炭含硫高,对熄焦设备,运焦设备,干熄焦设备,
特别是对干熄焦锅炉管等腐蚀严重,每年要投入大量的资金对这些
设备进行维修,还影响生产及产量;还有这些硫又挥发到煤气里面
,最终又回到脱硫废液中。
久而久之脱硫废液中的硫化物积累越来
越多,一方面将会严重降低脱硫效果,另一方面造成化产的设备严
重腐蚀。
增加了设备的维护费用。
由于脱硫废液中含有硫氰酸根离子,有强力的杀菌效果,无法进行生化处理。
如果不处理直接排放,严重污染环、违反了环保法,
严重的要追究刑事责任的;所有说,脱硫废液必须进行深度处理,
方可达到环保要求,还能保护设备不受腐蚀,减少设备的维护费用;国家、企业都有益处。
要彻底解决脱硫废液的污染问题,必需对脱硫废液进行深度处理。
脱硫液中含有大量的副盐NH4CNS和(NH4)2S2O3,是具有经济价值的
无机盐,如果将脱硫液中的副盐进行分离回收,不但降低了脱硫液
中副盐含量,使脱硫反应朝正方向进行,提高脱硫效率,使脱硫液
可以循环利用,而且回收副盐本身也具有一定的经济效益。
三、脱硫废液提盐工艺及投资
按催化氧化法,前脱硫工艺产生的脱硫废液,提取副盐工艺说明,脱硫废液提取副盐的工艺很多种,具体一下说明
1、提取三种副盐即;硫氰酸铵、硫代硫酸铵、硫氰酸铵;此工艺100%的处理脱硫废液,全部送回脱硫液中,循环使用;无废弃物产生,处理脱硫废液,全部送回脱硫液中,循环使用;但是提取出来的硫代硫酸铵没有销路,成了固体废物,无法处理。
此工艺造价高,投资1800万左右,占地面积9亩,
工艺简介;采用的是焦化脱硫废液无害化处理技术,提出脱硫
废液中的盐类,使脱硫废液循环使用。
采用脱色结合萃取结晶提纯
法工艺。
全部工艺过程包括:脱硫液输送、脱硫液过滤、脱硫液预
蒸发、预热脱色、脱色剂处理、混盐浓缩、混盐结晶、混盐甩干;
溶解、压滤、精密过滤、精盐浓缩、精盐结晶、精盐甩干、干燥、
回收、精馏、母液回收、尾气洗涤和工艺水处理、车间空气置换等。
2、提取混盐,三种副盐在一起,通过简单的设备进行蒸发、冷却等方式,提取混盐,处理后的脱硫废液送回系统循环使用,此工艺太简单,优点是投资少,占地少;缺点是脱硫废液不能全部处理,还得排放一部分,排放脱硫废液就污染环境;还有产品混盐无销路,又产生了固体废物,无法处理,因此此工艺处理脱硫废液不彻底,留下环保隐患,虽然投资少,但是产生了废物,不符合新环保法的要求。
投资大约100左右,占地200㎡。
工艺简介;脱硫废液进入蒸发器和蒸发室,蒸发器内送入饱和蒸
汽加热脱硫废液,在真空泵的的作用下,脱硫废液在较低的温度下
开始沸腾,随着废液温度不断升高,液体蒸发到蒸发室,在蒸发室
内的液体不断蒸发浓缩后,剩下混盐,将蒸发室内的浓缩液体放到
室外自然冷却后,即为混盐产品;蒸发出的废液蒸汽进入冷却器,
被冷却下来的液体流入氨水槽,最后打入脱硫液中进行循环利用。
3、提取硫氰酸铵、硫磺、硫酸铵工艺,次工艺生产纯度高的硫
氰酸铵、硫磺,不生产硫代硫酸铵,把硫代硫酸铵转化为硫酸铵产品,硫酸铵产品可同硫铵工段生产的硫酸铵质量一样,有销路;处
理脱硫废液,全部送回脱硫循环使用;投资大约950万左右,占地面
积1200㎡,
工艺简介;将脱硫废液先进行氧化、过滤、脱色、过滤、浓缩、过滤、调整降温、过滤、结晶降温、离心机出产品。
将氧化的脱硫废液过滤后,加入活性炭进行脱色处理,废活性
炭过滤之后送煤场配煤,
将脱色清液配入一定量的催化剂后送入氧化塔顶,连续进料,连
续出料,氧化好的物料从塔的下部流出,进入到中转储槽中,用于
浓缩。
硫磺从塔的底部自动流出,进入到硫磺槽中。
将减压浓缩好的物料进行热分离,直接得到硫酸铵产品,。
离心分离出来的母液打入到调节釜中。
通过降温结晶、离心甩干得到硫氰酸铵。
液体送回脱硫液中,
循环使用。
以下是按照提取硫氰酸铵、硫酸铵、硫磺三种产品计算成本和效益,具体如下:
四、运行成本
活性碳消耗:7000元/吨,用量为脱硫液的3%计算。
操作工工资:14(人)*130元/天=1820元/天
主要动力及原材料消耗
1.氧化剂消耗:250元/Kg,用量每天处理50吨脱硫废液,消耗7-
8Kg。
2.循环冷却水循环量500m³/h。
3.蒸汽消耗:氧化蒸汽耗量;吨废水0.3吨蒸汽,双效蒸发器消耗蒸汽;吨废水0.65吨蒸汽。
4.氧化、离心机电耗:15KWh*20h*0.6元/KWh=180元。
五、产品效益
按脱硫废液中两盐含量250g/L,处理费用量50吨计算,每天生产硫氰酸铵5吨、硫酸铵5.5吨、硫磺500Kg。
目前市场96%硫氰酸铵销售价格为2500元/吨,5*2500=12500元;
目前市场含氮20%硫酸铵销售价格为340元/吨,5.5*340=1870元
目前市场含氮90%黑硫磺销售价格为150元/吨,500*150=75元
六、总结
经过对以上工艺技术方案的评价表明:选择投资少,生产时无三废的工艺比较合理,该项目的资源利用率较高,从原料至成品均为
全封闭。
在一个良性循环中运行,既节能又降耗,三废变为三种产品,符合国家的产业政策和环保政策。
生产车间采用半敞开式,通风效果好,工艺技术实施了全封闭操作路线,另外生产投入的原料,都是物理过程中提取出硫氰酸铵,
没有化学反应就变为成品。
没有三废排放,自然就没有污染的存在,符合国家环保、清洁文明生产要求。
卫华
河北渤海煤焦化有限公司
2014年6月28日。