传动轴振动分析
轴的分析报告

轴的分析报告1. 引言轴是机械领域中常见的零部件,承担着支撑、传动和定位等重要功能。
在机械设计和生产过程中,轴的分析是必不可少的一部分。
本报告旨在通过对轴的分析,进一步了解轴的设计、应用和优化方法。
2. 轴的基本概念轴是一种长条形零件,通常是圆形截面,用于连接和支撑其他部件。
在机械设计中,轴的主要作用是传递力、承受载荷和保持对零件的位置限制。
轴通常具有以下几个重要的特征:•材料选择:轴的材料应具有足够的强度和硬度,以承受来自其他部件的载荷和力矩。
常用的轴材料包括钢、铝和合金等。
•几何形状:轴通常具有圆柱形状,但在某些特殊情况下,也可以使用其他截面形状,如六边形或方形。
•表面处理:轴的表面通常需要进行处理,以提高其耐磨性和耐腐蚀性。
常见的表面处理方法包括镀铬、磨光和氮化等。
3. 轴的设计原则在轴的设计过程中,需要考虑以下几个关键因素:•载荷和应力分析:首先需要对轴所承受的载荷和力矩进行分析和计算。
通过材料的强度和刚度等参数,可以确定轴的尺寸和形状。
•振动和失稳分析:轴在运转过程中可能会发生振动和失稳现象。
因此,需要进行振动和失稳分析,以确定轴的稳定性。
•热量传递分析:在某些特殊应用中,轴可能会受到高温影响。
因此,需要进行热传导分析,以确定轴的热量传递能力和稳定性。
•轴承和连接方式:轴通常需要与其他部件进行连接,如轴承和联轴器等。
因此,需要选择适当的轴承和连接方式,以确保轴与其他部件的良好配合和运转。
4. 轴的应用案例分析4.1 传动轴传动轴是常见的一种轴类型,用于将动力从一个部件传递到另一个部件。
传动轴通常需要考虑转矩、转速、弯曲和振动等因素。
通过对传动轴的应力和振动分析,可以确定适当的材料和尺寸,以确保传动轴能够稳定工作。
4.2 支承轴支承轴用于支撑其他部件或装置。
在支承轴的设计中,需要考虑载荷、外力和挠度等因素。
通过应力和变形分析,可以确定支承轴的材料和尺寸,以确保其能够承受外部载荷并满足精度要求。
工厂振动测试实验报告(3篇)
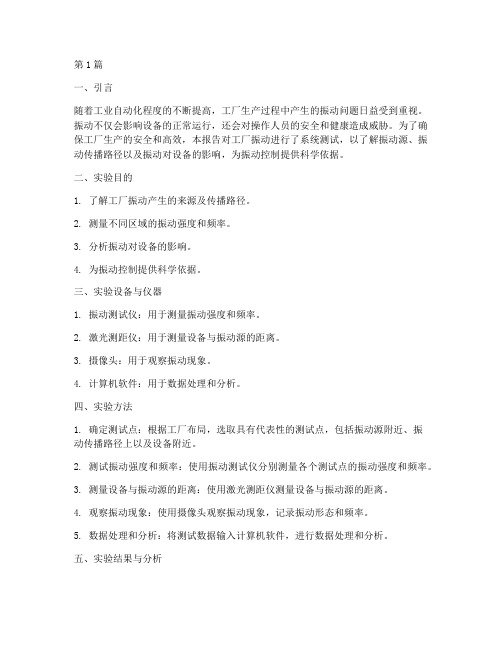
第1篇一、引言随着工业自动化程度的不断提高,工厂生产过程中产生的振动问题日益受到重视。
振动不仅会影响设备的正常运行,还会对操作人员的安全和健康造成威胁。
为了确保工厂生产的安全和高效,本报告对工厂振动进行了系统测试,以了解振动源、振动传播路径以及振动对设备的影响,为振动控制提供科学依据。
二、实验目的1. 了解工厂振动产生的来源及传播路径。
2. 测量不同区域的振动强度和频率。
3. 分析振动对设备的影响。
4. 为振动控制提供科学依据。
三、实验设备与仪器1. 振动测试仪:用于测量振动强度和频率。
2. 激光测距仪:用于测量设备与振动源的距离。
3. 摄像头:用于观察振动现象。
4. 计算机软件:用于数据处理和分析。
四、实验方法1. 确定测试点:根据工厂布局,选取具有代表性的测试点,包括振动源附近、振动传播路径上以及设备附近。
2. 测试振动强度和频率:使用振动测试仪分别测量各个测试点的振动强度和频率。
3. 测量设备与振动源的距离:使用激光测距仪测量设备与振动源的距离。
4. 观察振动现象:使用摄像头观察振动现象,记录振动形态和频率。
5. 数据处理和分析:将测试数据输入计算机软件,进行数据处理和分析。
五、实验结果与分析1. 振动源:通过测试发现,工厂振动的主要来源为机械设备运行、物料运输以及空气流动等。
2. 振动传播路径:振动主要沿地面、墙壁以及设备本身传播。
3. 振动强度和频率:不同区域的振动强度和频率存在差异,振动源附近振动强度较大,频率较高;振动传播路径上振动强度逐渐减弱,频率降低;设备附近振动强度较小,频率较低。
4. 振动对设备的影响:振动可能导致设备疲劳、磨损,甚至损坏。
长期处于高振动环境下,设备的使用寿命将大大缩短。
六、振动控制措施1. 优化设备布局:将振动源与设备保持一定距离,减少振动传播。
2. 使用减振设备:在振动源附近安装减振垫、减振器等,降低振动强度。
3. 改善物料运输方式:采用低速、平稳的运输方式,减少物料运输过程中的振动。
传动轴高速抖动的原因

传动轴高速抖动的原因1.传动轴不平衡:传动轴上的零部件可能因制造过程中的不良加工或安装不当而导致不平衡。
这种不平衡会在高速旋转时产生振动,导致传动轴抖动。
2.传动轴扭曲或弯曲:传动轴可能在使用过程中发生扭曲或弯曲,例如在过大的负载下或因碰撞等原因。
这会导致传动轴在旋转时发生振动,使其高速抖动。
3.轴承故障:传动轴上的轴承可能会因磨损、老化或损坏而失去正常运转,从而导致传动轴在高速下抖动。
4.传动系统不平衡:如果传动系统中的其他部分(如变速器、差速器等)存在不平衡或故障,也会导致传动轴高速抖动。
5.使用材料的质量问题:如果传动轴的制造材料质量不达标,或者在使用中存在材料疲劳、开裂等问题,都可能导致传动轴高速抖动。
6.传动轴设计或安装问题:如果传动轴的设计不合理或安装不当,例如尺寸不匹配、装配不良等,会导致传动轴在高速下抖动。
7.驱动系统动力输出不均衡:驱动系统中的动力输出不均衡,例如由于发动机不平衡或点火系统问题导致的驱动力不连续,也会引起传动轴高速抖动。
为解决传动轴高速抖动问题,可以采取以下措施:1.进行动平衡:通过在传动轴上安装补偿重物或进行轴的细微加工,以使传动轴在高速旋转时平衡。
2.更换轴承:如发现轴承故障,应即时更换损坏的轴承以确保传动轴正常运转。
3.修复或更换传动轴:如果传动轴发生扭曲、弯曲或其他严重损坏,应及时修复或更换传动轴。
4.进行系统平衡:对于整个传动系统,要确保各个零部件的匹配性和正常运转,如检查变速器、差速器等部件是否存在故障,及时进行维修或更换。
5.改善材料和制造工艺:在传动轴的制造过程中,选择优质材料,确保制造工艺符合标准,以避免材料质量问题和制造缺陷。
6.优化设计和安装:在传动轴的设计和安装中,应充分考虑尺寸匹配、装配工艺和质量控制,以确保传动轴的正常运转。
7.修复或调整驱动系统:如发现驱动系统动力输出不均衡的问题,应及时修复或调整驱动系统,以消除传动轴高速抖动的原因。
汽车传动轴振动和异响的原因——宝典

汽车传动轴振动和异响的原因——宝典1.传动轴不平衡:传动轴在使用过程中可能会因为各种原因而不平衡。
这通常是因为轴的制造过程中存在问题,或者在使用过程中轴上的配重失效了。
不平衡的传动轴会导致车辆在高速行驶时出现振动和异响。
解决这个问题的方法是重新平衡传动轴,或者更换一个新的传动轴。
2.传动轴老化和磨损:长时间的使用会导致传动轴的老化和磨损。
这些问题可能会导致传动轴的松动和偏移,从而引起振动和异响。
解决这个问题的方法是更换一个新的传动轴,或者进行维修和加固。
3.传动轴轴承故障:传动轴上的轴承可能会因为长时间的使用而失效。
当轴承发生故障时,传动轴会出现振动和异响。
解决这个问题的方法是更换一个新的轴承。
4.传动系统的错位:当传动系统的各个部分不正确安装时,会导致传动轴的错位。
这种错位会引起传动轴的振动和异响。
解决这个问题的方法是重新调整和安装传动系统的各个部分。
5.传动轴松动:传动轴在使用过程中可能会因为松动而引起振动和异响。
这通常是由于传动轴的连接螺栓松动或者传动轴的支撑装置松动所导致的。
解决这个问题的方法是进行适当的紧固和固定。
6.其他故障部件:除了传动轴本身,其他与传动系统相关的部件也有可能导致振动和异响。
例如,离合器和传动器等部件的故障也会引起这些问题。
解决这个问题的方法是检查和修理这些部件。
总之,汽车传动轴振动和异响的原因可能有很多种。
对于车主来说,及时的检查和维修非常重要,以避免更严重的损坏和安全隐患。
如果你对自己进行维修没有信心,建议寻求专业的技术支持和帮助。
传动轴共振的案例研究

一个关于传动轴共振的案例研究闵福江重庆长安汽车股份有限公司汽车工程研究院【摘要】NVH是汽车研究与设计过程中既需要一定的理论基础,又需要大量实践经验才能解决的应用问题。
文章阐述了汽车动力系统引起整车NVH问题的原理,以及解决这些NVH问题的一些方法。
【主题词】传动系 共振 汽车 轰鸣声A Case Study on the Syntony of Drive shaftMin FujiangChongqing Changan Automobile Stock CO . LTDAutomotive Engineering Institute【Abstract】NVH is a application problem to be solved with certain theoretical basis and much practical experience .This paper describes the complete vehicle NVH problem principally caused by power system ,and introduce some ways how to solve this problem。
【Key Words】Transmission system , Syntony , Vehicle , Booming Noise1前言某新研发的车辆,在样车试制期间,发现当车辆在行驶过程中发动机转速达到3300转/分时,车内产生明显的轰鸣声(Booming Noise),该车型如果投放市场,必然引起顾客抱怨,影响市场销售。
经诊断分析确定为传动轴一阶弯曲共振导致,必须针对传动轴采取措施,解决轰鸣噪声。
本文系统地阐述了该问题的分析和解决过程。
2传动轴共振引发的NVH问题汽车的动力系统时刻向传动轴施加各种激振,尤其以发动机的往复惯性力与传动轴不平衡产生的惯性力冲击最为显著。
14SLA10A型立式中开泵取水泵传动轴振动问题

14SLA-10A型取水泵传动轴振动问题一装置情形湖南省衡阳县某电灌站于1983年安装了13台14SLA-10A型泵,配套电机功率为225kw,转速为1450r/min二运行故障及前期处置情形该电灌站关于衡阳县来讲,那时(1984年)是一个最大的取水浇灌水利工程(最大的取水量可达12000T/H),受到地县领导及广大农人群众的重视和关注。
1984年新春,泵站建成以后,第一次开车当日,举行了盛大的通水典礼,地县领导和数千群众聚集泵站周围,泵站建筑物上张灯结彩,而且预备了鞭炮和锣鼓乐队,只等开车取水,就锣鼓鞭炮齐鸣,到场领导和男女老幼群众就会齐声欢呼,掌声如雷。
可是首台一开车,水还没来得及喷涌到渠道,传动轴就开始打摆子一样动起来,操作人员一看势头不对就赶紧停车,接着开启第二台机组,情形又是如此,开第三台仍是如此。
开车欢庆典礼,不得以就此告吹,周围群众悲观丧气,大失所望,不欢而散。
为此,我厂紧急派员到现场分析处置。
第一以为是安装不合格,从装配车间抽调一名体会丰硕的师傅前去将一台机组从头安装校准一次,再次试车,传动轴仍是振动,后来又以为是轴的刚度不够,专门是最上面的一根轴振动最厉害,于是将上面一根轴由φ70改成φ90.精心改换最上一根传动轴以后,振动情形有所改善,但仍是明显振动。
如此反复拨弄,时刻已过半年,问题仍是没有解决。
三处置进程及成效时至1984年8月初,厂里派我(时任设计科副科长)前去现场协助分析处置。
那时现场已有好几位同志,我到现场后问他们对振动缘故通过理论分析没有,他们只说是有过定性分析,但没有定量分析。
于是我从泵站的一名技术人员那里借来一本材料力学教科书,计算和复核传动轴的强度和刚度,通过计算分析,发觉GL70型传动装置不能用于14SLA-10A型泵装置,而要改用CH70型传动装置。
其缘故是扭转刚度不够。
解决扭转刚度不足的有效方法是缩小轴的两支点跨度,即将传动答复到原先的CH70型传动(CH70型传动每根轴有两个轴承支架,后来取消一个支架,两轴之间用夹壳刚性联轴器,定名为GL70型传动)。
传动轴高速抖动的原因

传动轴高速抖动的原因1.传动轴失衡传动轴的失衡是引起高速抖动的常见原因之一、失衡指的是传动轴在运转时,轴线与质量中心线不重合,导致转动不平衡。
失衡会产生一系列的不均匀力矩,从而引发传动轴的抖动。
2.传动轴材质和制造缺陷传动轴材质的选择和制造工艺的缺陷也可能导致其在高速运转时出现抖动。
材质选择不当,无法承受高速运转的压力,容易发生变形或断裂;而制造工艺缺陷,例如精度不高、表面光洁度不够等也会影响传动轴的运转稳定性。
3.传动轴与传动装置的不匹配传动轴与驱动装置之间的不匹配也可能导致传动轴高速抖动。
例如,轴承安装不正,轴承摩擦力过大,或者轴与传动装置之间的间隙不合适等情况都会引起传动轴的抖动。
4.传动系统配重问题传动系统中的其他部件和配重也可能会对传动轴的运转稳定性产生影响。
例如,万向节平衡铁的松动、断裂或缺失,都会导致传动轴的抖动。
此外,配重块分布不均匀也会导致传动轴的运转不稳定。
5.转速过快或过慢传动轴的高速抖动还可能是由于传动轴的转速过快或过慢引起的。
当传动轴转速过快时,由于惯性效应,会引发传动轴的振动和抖动;而转速过慢则容易导致失衡和共振现象,从而引起传动轴抖动。
6.传动轴受损或老化长期使用和磨损会导致传动轴的性能下降,例如轴的强度减弱、表面磨损等,这些因素都会导致传动轴在高速运转时出现抖动。
7.粗糙路面和不平衡荷载粗糙的路面和不平衡的荷载也可能导致传动轴高速抖动。
当车辆行驶在凹凸不平的路面上,或者载荷分布不均匀时,会通过传动系统传递到传动轴上,引发抖动现象。
为了解决传动轴高速抖动的问题,可以采取以下措施:1.平衡传动轴定期对传动轴进行动平衡处理,确保轴线与质量中心线重合,减少传动轴的失衡现象。
2.优化材质和制造工艺选择合适的材质,并确保传动轴的制造工艺合格,减少材质和工艺带来的不稳定因素。
3.检查和调整传动系统的配重定期检查和调整传动系统中的各个部件的配重,确保其均衡和稳定。
4.控制转速在设计和使用传动轴时,注意控制转速范围,避免过快或过慢的转速。
齿轮传动轴的动态特性测试与模态分析

齿轮传动轴的动态特性测试与模态分析引言齿轮传动系统在机械装置中扮演着关键的角色,它通过齿轮的相互啮合传递力与运动。
在实际应用中,齿轮传动轴的动态特性对于确保传动系统的稳定性、可靠性以及寿命都起着至关重要的作用。
本文将深入探讨齿轮传动轴的动态特性测试与模态分析,以提供对传动系统性能优化的基础理论和实践指导。
一、齿轮传动轴动态特性的测试方法1. 强制激励法强制激励法是一种常用的齿轮传动轴动态测试方法,它通过对传动轴施加特定的荷载或力矩,从而观察其自由振动状态下的响应特性。
一般情况下,引入外加力或力矩后,通过合适的传感器采集传动轴的振动响应信号,并将其转化为频谱图分析,可以获得传动轴在不同激励条件下的振动模态。
2. 自由振动法自由振动法是另一种常用的齿轮传动轴动态测试方法,它在没有外界强制激励的情况下,通过对传动轴施加初速度或初位移,观察其自由振动过程中的响应特性。
测试时应尽量降低传动轴的阻尼,以减小振动信号的衰减,并采集振动响应信号进行频谱分析,进而得到传动轴的振动模态。
二、齿轮传动轴的模态分析1. 模态分析的基本原理模态分析是一种通过对某个结构或系统施加激励并测量其振动响应,来研究其特定振动模态的方法。
在齿轮传动轴的模态分析中,通过将传动轴固定在一端,施加激励并测量振动响应,可以得到传动轴的自由振动模态频率、振型和阻尼比等信息。
这些信息对于齿轮传动轴的动态特性和谐波分析等方面具有重要的意义。
2. 模态分析的步骤a. 激励源与传感器的安装:在模态分析实验中,需要选择合适的激励源,如锤击法、电磁激振器等,并通过传感器采集传动轴的振动信号。
传感器通常安装在传动轴的不同位置,以获取全面的振动模态信息。
b. 数据采集与处理:采集传感器测得的振动信号,并对其进行滤波和放大等处理。
通常使用频谱分析方法将时域信号转换为频域信号,得到传动轴不同频率上的振动响应特性。
c. 振型识别与模态提取:通过对频谱图的分析,可以识别出传动轴的振动模态,并提取出相应的模态参数,如频率、振型和阻尼比。
- 1、下载文档前请自行甄别文档内容的完整性,平台不提供额外的编辑、内容补充、找答案等附加服务。
- 2、"仅部分预览"的文档,不可在线预览部分如存在完整性等问题,可反馈申请退款(可完整预览的文档不适用该条件!)。
- 3、如文档侵犯您的权益,请联系客服反馈,我们会尽快为您处理(人工客服工作时间:9:00-18:30)。
毕业设计(论文)题目:传动轴振动分析院别:汽车与交通学院专业班级:交通运输学生姓名:XXX学号:XXXXXXXXX指导老师:XXX2010年5月21日摘要传动轴作为汽车传动系统的主要部件在汽车行驶过程中起着传递运动及扭矩的作用。
由于传动轴在使用过程中的特点是转速高,并且其结构较为复杂,所以不可避免的存在振动现象。
传动轴的振动存在许多危害,首先会产生噪音,作为汽车部件这会大大地影响汽车舒适性;还会降低传动效率,产生配合松动,乃至于使元件断裂,从而导致事故的发生。
本文的中心内容是利用Solidworks软件来研究传动轴的振动问题,也就是针对某种车型的传动轴这一特定的旋转体,先使用大型CAD软件Solidworks 进行实体建模,利用其自有的计算模块分别计算各个不同部件的质量,然后利用Solidworks 中的Simulation 插件进行有限元分析,建立相应的CAE模型,进行网格化,分成一定数量的单元,再通过计算机的分析计算,经过有限元算法的处理,得出相应的数据结果,最后算出临界速度和固有频率。
通过阅读了大量的国内外相关的技术研究文献,对当前本课题研究的最新状况进行比较全面的、深入的研究。
总结各类结构有限元分析的优点,找出存在的问题,立足于工作中的实际存在的问题和实用性,对其进行分析和研究。
关键词:传动轴;有限元分析;模态分析;临界转速;固有频率ABSTRACTAs the car transmission shaft of the main parts in the process of vehicle movement and torque transmission. Due to the characteristics of transmission is in use process, and its structure of high speed is more complicated, so there are inevitably vibration phenomenon.There are many hazards shaft vibration and noise, first as automobile parts will greatly affect auto comfort, Still can reduce transmission efficiency and cooperate with loose, and even make component fault, causing accidents.This center is to study using Solidworks software shaft vibration problem, also is this particular tothe shaft, large CAD software used for modeling, Solidworks its own calculation module of different components are calculated respectively, and the quality of the Simulation using Solidworks plugin fe analysis, establish corresponding CAE model, the grid, into a certain number of units, through the analysis and calculation of computer, through the finite element algorithm, corresponding data, and finally calculate critical speed and the inherent frequency.Through reading a lot of domestic and foreign relevant technical research literature on this subject, the current situation of the latest research on comprehensive and thorough research. Summarizes the advantages of finite element analysis, find out the existing problems in actual work, based on the existing problems and practical, carries on the analysis and research.KEY WORDS:shaft, Finite element analysis, Modal analysis, The critical speed, Inherent frequency摘要 (II)ABSTRACT ................................................................................................................. I II 目录 (1)1 绪论 (2)1.1课题的来源及研究的目的和意义 (2)1.2课题的研究背景及其发展趋势 (3)1.3 本文研究方法和主要内容 (4)2球笼式等速万向节传动轴 (7)2.1传动轴总成介绍 (7)2.2传动轴振动分析的原理、方法和意义 (9)2.2.1 传动轴总成的力学分析 (9)2.2.2 传动轴振动分析的原理 (14)2.3 有限元思想及分析软件介绍 (17)3 球笼式等速万向节传动轴的设计与建模 (22)3.1传动轴轴杆 (22)3.2外球笼 (24)3.3内球笼 (31)3.4传动轴总成 (38)3.5有限元模型的建立 (39)4 全文总结和展望 (47)致谢 (49)参考文献 (50)随着经济的发展,私家车的数量也随之上升。
人们在追求速度之余,越来越重视汽车的舒适性和可靠性。
而本文研究的传动轴——汽车传动系统的主要部件,它的振动严重关系到整车的舒适性和可靠性。
本文通过研究计算出其临界转速,避免共振的发生,为有效的改善传动轴的性能提供参考。
本文研究的传动轴是以某种车型的球笼式等速万向节传动轴为例展开研究的。
首先,根据传动轴的样品实体得到基本数据和关键参数。
利用AutoCAD 绘制出二维图形,然后利用Solidworks 软件建立实体模型,然后利用Simulation 插件进行有限元分析。
最后,通过分析得出临界条件。
通过本文的设计分析,得出传动轴的临界条件,有效的减少了震动带来的危害。
1.1课题的来源及研究的目的和意义汽车工业的发展,及用户对汽车的使用、转向享受追求,要求汽车有更好的动力性、操纵性及舒适性,促使了FF及4WD型车的出现。
它们的前轮必须具有转向和驱动两种功能,作为转向轮,要求车轮能在一定的转角范围内任意偏转某一角度;作为驱动轮,则要求半轴在车轮偏转过程中以相同的角速度不断地把动力从主减速器传到车轮。
在这样两个轴线不重合,且位置还经常变化的两轴间传递动力的机构就是等速万向节。
转向驱动桥半轴不能制成整体而要分段,在车轮和半轴间用等速万向节将两者联接起来。
即使采用后轮驱动,由于居住性的要求,使用独立悬挂.车轮和半轴轴线不重合,也需等速万向节传动。
传动轴作为汽车传递转矩和扭矩的重要部件。
由于受其使用性能和结构较为复杂等因素的制约,导致在不平衡力的作用下不可避免的存在着振动现象,这种振动对汽车的舒适性和可靠性均有极大的影响。
因此,国内外汽车生产厂家向来十分重视对汽车传动轴的振动分析研究,均迫切希望能最大限度的降低传动轴的不平衡量。
在当今的经济体制下,企业之间的竞争主要体现在产品的竞争上。
对于产品则体现在开发时间、生产成本、质量水平等各方面。
开发一个产品,则需要经过结构设计、审核、模具验收,小批量试制、进一步检验、大批量生产。
以前,进行审核是一个长期又复杂的过程,需要到现场运行,采集数据等等,需要耗费大量的人力、物力和财力。
随着科学技术的发展,像Solidworks等软件的运用,它可以模拟实际场景和受力载荷,大大他提高了产品开发的效率,同时也减少人力、物力的消耗。
1.2课题的研究背景及其发展趋势汽车是一个复杂的多自由度“质量——刚度——阻尼”振动系统,是由多个具有固有振动特性的子系统组成,如车身的垂直振动、纵向角振动和侧倾振动、发动机曲轴的扭转振动、传动系统的振动等。
这些不同形式的振动及其耦合,是影响汽车行驶平顺性、舒适性的主要原因,要改善汽车的整体性能,就必须对汽车的各个系统的振动特性进行深入研究。
车辆动力传动系的振动可分为弯曲振动和扭转振动,二者不仅有各自的振动特性,而且还存在一定程度的振动耦合,对车辆行驶平顺性、乘坐舒适性及动力传动系零部件使用寿命有着重要影响,因此对车辆动力传动系的整体振动进行深入细致的研究十分重要。
传动轴作为汽车传动系统的主要部件在汽车行驶过程中起着传递运动及扭矩的作用。
由于传动轴在使用过程中的特点是转速高,并且其结构较为复杂,所以不可避免的存在振动现象。
作为汽车传动系的主要部件,传动轴在汽车行驶过程中起着传递运动及转矩的作用。
由于传动轴结构本身的运动学、动力学特点,不可避免的存在振动现象。
传动轴的振动由许多危害,首先会产生噪声,影响汽车舒适性;其次会降低传动效率,产生配合松动,甚至使元件断裂,从而导致事故的发生。
传动轴振动的激励源主要是发动机,当量夹角过大、传动轴自身不平衡、止口跳动量以及任何形式的旋转补平衡也会引起传动轴的振动。
合理的设计汽车传动轴系对解决汽车的振动和噪声问题是十分重要的,特别是我国汽车工业与发达国家差距还很大,随着我国道路条件的改善和车速的提高,汽车的振动、噪声问题将会越来越突出,是提高产品质量和竞争能力所必须解决的问题。
本文的中心内容是利用Simulation插件来研究传动轴的振动问题,也就是针对传动轴这一特定的旋转体,先使用大型CAD软件Solidworks 进行实体建模,利用其自有的计算模块分别计算各个不同部件的质量,在有限元分析软件Simulation中,建立相应的CAE模型,进行网格化,分成一定数量的单元,在通过计算机的分析计算,经过有限元算法的处理,得出相应的数据结果,最后算出临界速度和固有频率。
1.3 本文研究方法和主要内容本文主要是依据Solidworks 软件来进行研究的。