制造技术机械第6-7章_部分习题解答
机械制造技术基础课后部分习题及答案

2-2切削过程的三个变形区各有何特点?它们之间有什么关联?答:切削塑性金属材料时,刀具与工件接触的区域可分为3个变形区:①第一变形区(基本变形区):是切削层的塑性变形区,其变形量最大,常用它来说明切削过程的变形情况;②第二变形区(摩擦变形区):是切屑与前面摩擦的区域;③第三变形区(表面变形区):是工件已加工表面与后面接触的区域。
它们之间的关联是:这三个变形区汇集在切削刃附近,此处的应力比较集中而且复杂,金属的被切削层就在此处与工件基体发生分离,大部分变成切屑,很小的一部分留在已加工表面上。
2-3分析积屑瘤产生的原因及其对加工的影响,生产中最有效的控制积屑瘤的手段是什么?答:在中低速切削塑性金属材料时,刀—屑接触表面由于强烈的挤压和摩擦而成为新鲜表面,两接触表面的金属原子产生强大的吸引力,使少量切屑金属粘结在前刀面上,产生了冷焊,并加工硬化,形成瘤核。
瘤核逐渐长大成为积屑瘤,且周期性地成长与脱落。
积屑瘤粘结在前刀面上,减少了刀具的磨损;积屑瘤使刀具的实际工作前角大,有利于减小切削力;积屑瘤伸出刀刃之外,使切削厚度增加,降低了工件的加工精度;积屑瘤使工件已加工表面变得较为粗糙。
由此可见:积屑瘤对粗加工有利,生产中应加以利用;而对精加工不利,应以避免。
消除措施:采用高速切削或低速切削,避免中低速切削;增大刀具前角,降低切削力;采用切削液。
2-7车削时切削合力为什么常分解为三个相互垂直的分力来分析?分力作用是什么?答:(1)车削时的切削运动为三个相互垂直的运动:主运动(切削速度)、进给运动(进给量)、切深运动(背吃刀量),为了实际应用和方便计算,在实际切削时将切削合力分解成沿三个运动方向、相互垂直的分力。
(2)各分力作用:切削力是计算车刀强度、设计机床主轴系统、确定机床功率所必须的;进给力是设计进给机构、计算车刀进给功率所必需的;背向力是计算工件挠度、机床零件和车刀强度的依据,与切削过程中的振动有关。
2-11背吃刀量和进给量对切削力和切削温度的影响是否一样?为什么?如何运用这一定律知道生产实践?答:不一样。
机械制造技术基础第六章课后题答案

6-1什么是生产过程,工艺过程和工艺规程(1)生产过程一一将原材料转变为成品的过程。
(2)工艺过程一一在生产过程中,凡是改变生产对象的形状、尺寸、位置和性质等,使其成为成品或半成品的过程称为工艺过程。
(3)工艺规程一一把合理工艺过程的有关内容写成工艺文件的形式,用以指导生产,这些工艺文件称为工艺规程。
6-2何谓工序、工步、走刀(1)工序是指一个(或一组)工人,在一台机床上(或一个工作地点)对同一工件(或同时对几个工件)所连续完成的那部分工艺过程。
(2)工步是在加工表面不变,加工工具不变,切削用量不变的条件下所连续完成的那部分工序。
(3)走刀又叫工作行程,是加工工具在加工表面上加工一次所完成的工步。
6-3零件获得尺寸精度、形状精度、位置精度的方法有哪些(1)零件获得尺寸精度的方法:试切法、定尺寸刀具法、调整法、自动控制法。
(2)零件获得形状精度的方法:轨迹法、成形法、展成法。
(3)零件获得位置精度的方法:找正法、装夹法。
6-4不同生产类型的工艺过程的特点:p222-223表6-4.6-5试述工艺规程的设计原则、设计内容、设计步骤。
(1)工艺规程的设计原则:1所设计的工艺规程应能保证机器零件的加工质量(或机器的装配质量),达到设计图样上规定的各项技术要求。
2应使工艺过程具有较高的生产率,使产品尽快投放市场。
3设法降低制造成本。
4注意减轻劳动工人的劳动强度、保证生产安全。
(2)工艺规程的设计内容及步骤:1分析研究产品的零件图及装配图。
2确定毛坯。
3拟定工艺路线,选择定位基准。
4确定各工序所采用的设备。
5确定各工序所采用的刀具、夹具、量具和辅助工具。
6确定各主要工序的技术技术要求及检验方法。
7确定各工序的加工余量,计算工序尺寸和公差。
8确定切削用量。
9确定工时定额。
10技术经济分析。
11填写工艺文件。
6-6拟定工艺路线需完成那些工作拟定工艺路线须完成的工作:1确定加工方法。
2安排加工顺序。
3确定夹紧方法。
机械制造基础第七章铸铁及其热处理习题解答

第七章铸铁及其热处理习题解答7-1 铸造生产中,为什么铸铁的碳、硅含量低时易形成白口? 而同一铸铁件上,为什么其表层或薄壁处易形成白口?答:因为碳、硅是促进石墨化的元素,当它们含量含量低时石墨化不易进行,所以容易形成白口。
同一铸件上表层和薄壁的冷却速度比较快,不利于石墨化,故易形成白口。
7-2 在铸铁的石墨化过程中,如果第一、第二阶段完全石墨化,而第三阶段分别为完全、部分或未石墨化时,问它们各获得哪种基体组织的铸铁?答:第三阶段石墨化完全进行时,获得铁素体基体铸铁;部分进行时为铁素体+珠光体基体铸铁;未进行石墨化时为珠光体基体铸铁。
7-3 机床的床身、床脚和箱体为什么大都采用灰铸铁铸造?能否用钢板焊接制造?试将两者的使用性和经济性作简要比较。
答:1、因为灰铸铁的性能适合制造这些零件:抗压性能比抗拉性能好,铸造性能优良,减摩性好,减振性强,切削加工性良好,缺口敏感性较低。
2、能用钢板焊接制造,但钢板的减摩性、减振性不如灰铸铁。
在使用性和经济性上,灰铸铁成本低,易于铸造结构复杂的零件,并且其尺寸不受限制,这些都是用钢板制造不能达到的。
7-4 有一壁厚为20~30mm的铸件,要求抗拉强度为150MPa,应选用何种牌号的灰铸铁制造?答:根据强度要求和壁厚,应选用HT200。
7-5 生产中出现下列不正常现象,应采取什么措施予以防止或改善?(1) 灰铸铁精密床身铸造后即进行切削,在切削加工后发现变形量超差;(2) 灰铸铁件薄壁处出现白口组织,造成切削加工困难。
答:(1) 应在切削前进行去应力退火,消除铸造应力。
去应力退火通常是将铸件缓慢加热到500~560℃,保温一段时间(每l0mm厚度保温1h),然后随炉冷至150~200℃后出炉。
(2)应进行消除白口组织退火。
退火方法是把铸件加热到850~950℃,保温1~3h,使共晶渗碳体发生分解,即进行第一阶段的石墨化,然后又在随炉冷却中进行第二和第三阶段石墨化,析出二次石墨和共析石墨,到500~400℃再出炉空冷。
机械制造技术基础课后答案第六章
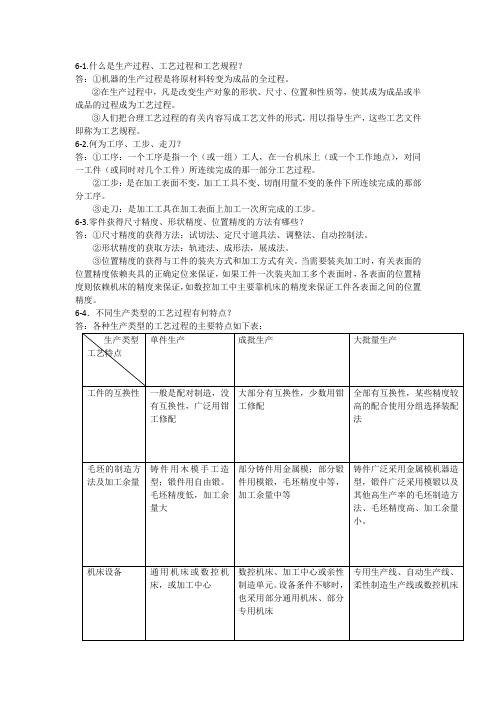
6-1.什么是生产过程、工艺过程和工艺规程?答:①机器的生产过程是将原材料转变为成品的全过程。
②在生产过程中,凡是改变生产对象的形状、尺寸、位置和性质等,使其成为成品或半成品的过程成为工艺过程。
③人们把合理工艺过程的有关内容写成工艺文件的形式,用以指导生产,这些工艺文件即称为工艺规程。
6-2.何为工序、工步、走刀?答:①工序:一个工序是指一个(或一组)工人,在一台机床上(或一个工作地点),对同一工件(或同时对几个工件)所连续完成的那一部分工艺过程。
②工步:是在加工表面不变,加工工具不变、切削用量不变的条件下所连续完成的那部分工序。
③走刀:是加工工具在加工表面上加工一次所完成的工步。
6-3.零件获得尺寸精度、形状精度、位置精度的方法有哪些?答:①尺寸精度的获得方法:试切法、定尺寸道具法、调整法、自动控制法。
②形状精度的获取方法:轨迹法、成形法,展成法。
③位置精度的获得与工件的装夹方式和加工方式有关。
当需要装夹加工时,有关表面的位置精度依赖夹具的正确定位来保证,如果工件一次装夹加工多个表面时,各表面的位置精度则依赖机床的精度来保证,如数控加工中主要靠机床的精度来保证工件各表面之间的位置精度。
6-4.不同生产类型的工艺过程有何特点?答:各种生产类型的工艺过程的主要特点如下表:6-5试简述工艺规程的设计原则、设计内容及设计步骤:答:步骤:原则:①所设计的工艺规程应能保证机器零件的加工质量;达到设计图样上规定的各项技术要求。
②应使工艺过程具有较高的生产率,是产品尽快投放市场。
③设法降低制造成本。
④注意减轻工人的劳动强度;保证生产安全。
设计内容及步骤:⒈分析研究产品的装配图和零件图⒉确定毛坯⒊拟定工艺路线,选择定位基面⒋确定各工序所采用的设备⒌确定各工序所采用的刀具、夹具、量具和辅助工具⒍确定各主要工序的技术要求及检验方法⒎确定各工序的加工余量,计算工序尺寸和方差⒏确定工时定额⒐确定切削用量⒑技术经济分析⒒填写工艺文件6-6.拟定工艺路线需完成的工作答:确定加工方法,安排加工顺序,确定定位夹紧方法,以及安排热处理、检验及其他辅助工序(去毛刺、倒角等)。
机械制造技术基础习题及答案第6章

学后评量参考答案1.轴类零件有何功用和技术要求?答:轴类零件主要用来支承回转运动的传动零件(如齿轮),并用于传递运动和扭矩。
轴类零件的技术要求:(1)尺寸精度:对于同一根轴而言,轴颈的尺寸精度要求比较高,轴头的尺寸精度一般要求较低;精密轴颈为IT5级、重要轴颈为IT6~IT7级、一般轴颈为IT8~IT9。
(2)几何公差:轴头相对于轴颈的同轴度、端面对轴线的垂直度,通常用径向圆跳动衡量。
普通精度轴的径向圆跳动为0.01~0.03 mm,高精度轴的径向圆跳动为0.001 ~0.005mm;轴颈的圆度、圆柱度。
一般应将其限制在尺寸公差范围内,当精度要求较高时,零件图上应单独标注其允许的偏差。
(3)表面结构:表面结构应与表面工作要求相适应。
轴头的表面结构为Ra2.5~0.63μm;轴颈的表面结构为Ra0.63~0.16μm。
2.轴类零件材料和毛坯的选择有何要求?答:根据轴的工作场合,选用合适的材料:一般精度,选中碳钢;中等精度、转速较高,选合金结构钢;高转速、重载荷,选低碳合金钢;高精度、高转速,选氮化钢。
轴类零件的毛坯常采用棒料、锻件和铸件等毛坯形式。
一般光轴或外圆直径相差不大的阶梯轴采用棒料;外圆直径相差较大或较重要的轴常采用锻件;某些大型的或结构复杂的轴(如曲轴)可采用铸件。
3.轴类零件常用的装夹方法有哪些?各有何特点及应用?答:轴类零件常用的装夹方法、特点及应用见下表:4.简述轴类零件常用的加工方法?答:轴类零件常用的加工方法:(1)车削外圆柱面:根据加工要求和切除余量多少的不同,可分粗车、半精车、精车、精细车。
(2)车削端面和台阶:常使用45°弯头刀、或左右偏刀进行车削。
(3)切槽和切断:轴类零件内、外表面上的沟槽一般用相应的成形车刀,通过横向进给实现。
(4)车削圆锥面:轴类零件上圆锥面的车削方法有转动小滑板车削圆锥面、偏移尾座车削圆锥面、靠模法车削圆锥面。
(5)车削螺纹:在车床上按螺距调整机床,用螺纹车刀加工出螺纹。
机械制造技术基础课后答案

第二章2-1.金属切削过程有何特征?用什么参数来表示?答:2-2.切削过程的三个变形区各有什么特点?它们之间有什么关联?答:第一变形区:变形量最大。
第二变形区:切屑形成后与前刀面之间存在压力,所以沿前刀面流出时有很大摩擦,所以切屑底层又一次塑性变形。
第三变形区:已加工表面与后刀面的接触区域。
这三个变形区汇集在切削刃附近,应力比较集中,而且复杂,金属的被切削层在此处于工件基体分离,变成切屑,一小部分留在加工表面上。
2-3.分析积屑瘤产生的原因及其对加工的影响,生产中最有效地控制它的手段是什么?答:在中低速切削塑性金属材料时,刀—屑接触表面由于强烈的挤压和摩擦而成为新鲜表面,两接触表面的金属原子产生强大的吸引力,使少量切屑金属粘结在前刀面上,产生了冷焊,并加工硬化,形成瘤核。
瘤核逐渐长大成为积屑瘤,且周期性地成长与脱落。
积屑瘤粘结在前刀面上,减少了刀具的磨损;积屑瘤使刀具的实际工作前角大,有利于减小切削力;积屑瘤伸出刀刃之外,使切削厚度增加,降低了工件的加工精度;积屑瘤使工件已加工表面变得较为粗糙。
由此可见:积屑瘤对粗加工有利,生产中应加以利用;而对精加工不利,应以避免。
消除措施:采用高速切削或低速切削,避免中低速切削;增大刀具前角,降低切削力;采用切削液。
2-4切屑与前刀面之间的摩擦与一般刚体之间的滑动摩擦有无区别?若有区别,而这何处不同?答:切屑形成后与前刀面之间存在压力,所以流出时有很大的摩擦,因为使切屑底层又一次产生塑性变形,而且切屑与前刀面之间接触的是新鲜表面,化学性质很活跃。
而刚体之间的滑动摩擦只是接触表面之间的摩擦,并没有塑性变形和化学反应2-5车刀的角度是如何定义的?标注角度与工作角度有何不同?答:分别是前角、后角、主偏角、副偏角、刃倾角(P17)。
工作角度是以切削过程中实际的切削平面、基面和正交平面为参考平面确定的刀具角度。
2-6金属切削过程为什么会产生切削力?答:因为刀具切入工具爱你,是被加工材料发生变形并成为切屑,所以(1)要克服被加工材料弹性变形的抗力,(2)要克服被加工材料塑性变形的抗力,(3)要克服切屑与前刀面的摩擦力和后刀面与过度表面和以加工表面之间的摩擦力。
机械制造技术课后习题参考答案(部分)教学内容
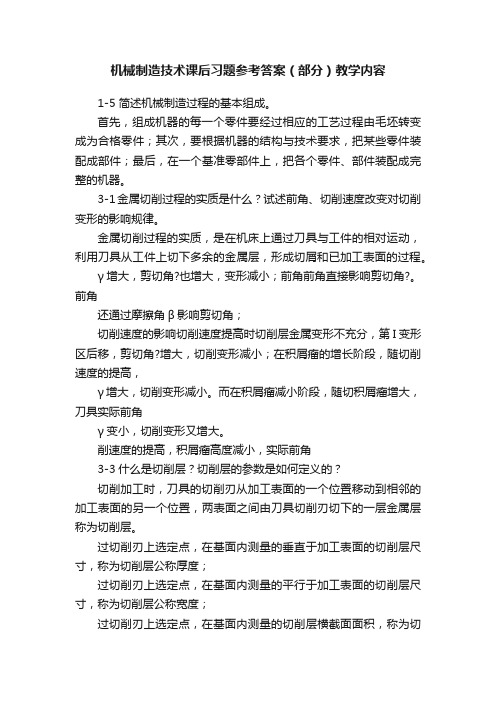
机械制造技术课后习题参考答案(部分)教学内容1-5 简述机械制造过程的基本组成。
首先,组成机器的每一个零件要经过相应的工艺过程由毛坯转变成为合格零件;其次,要根据机器的结构与技术要求,把某些零件装配成部件;最后,在一个基准零部件上,把各个零件、部件装配成完整的机器。
3-1金属切削过程的实质是什么?试述前角、切削速度改变对切削变形的影响规律。
金属切削过程的实质,是在机床上通过刀具与工件的相对运动,利用刀具从工件上切下多余的金属层,形成切屑和已加工表面的过程。
γ增大,剪切角?也增大,变形减小;前角前角直接影响剪切角?。
前角还通过摩擦角β影响剪切角;切削速度的影响切削速度提高时切削层金属变形不充分,第I变形区后移,剪切角?增大,切削变形减小;在积屑瘤的增长阶段,随切削速度的提高,γ增大,切削变形减小。
而在积屑瘤减小阶段,随切积屑瘤增大,刀具实际前角γ变小,切削变形又增大。
削速度的提高,积屑瘤高度减小,实际前角3-3什么是切削层?切削层的参数是如何定义的?切削加工时,刀具的切削刃从加工表面的一个位置移动到相邻的加工表面的另一个位置,两表面之间由刀具切削刃切下的一层金属层称为切削层。
过切削刃上选定点,在基面内测量的垂直于加工表面的切削层尺寸,称为切削层公称厚度;过切削刃上选定点,在基面内测量的平行于加工表面的切削层尺寸,称为切削层公称宽度;过切削刃上选定点,在基面内测量的切削层横截面面积,称为切削层公称横截面积;3-4分别说明切削速度、进给量及背吃刀量改变对切削温度的影响。
在切削用量中,切削速度对切削温度影响最大,进给量次之,背吃刀量影响最小。
因为,背吃刀量增大后,切削宽度也增大,切屑与刀具接触面积以相同比例增大,散热条件显著改善;进给量增大,切削厚度增大,但切削宽度不变,切屑与前刀面接触长度增加,散热条件有所改善;切削速度提高,消耗的功增加,产生的热量增多,而切削面积并没有改变,所以切削是影响切削温度的主要因素。
制造技术机械第6-7章_部分习题解答

《机械制造技术基础》部分习题参考解答第六章机床夹具设计6-1 机床夹具有哪几部分组成?各有何作用?6-2 为什么夹具具有扩大机床工艺范围的作用,试举三个实例说明。
6-3 习题6-3图所示连杆在夹具中定位,定位元件分别为支承平面1、短圆柱销2和固定短V形块3。
试分析习题6-3图所示定位方案的合理性并提出改进方法。
习题6-3图习题6-6图6-4 试分析比较可调支承、自位支承和辅助支承的作用和应用范围。
6-5 试分析各典型夹紧机构的特点及应用场合。
6-6 已知切削力F,若不计小轴1、2的摩擦损耗,试计算习题6-6图所示夹紧装置作用在斜楔左端的作用力F Q。
6-7 习题6-7图所示为气动夹紧机构,夹紧工件所需夹紧力F J=2000N,已知:气压p=4×105Pa,α=15°,L1=100mm,L2=200mm,L3=20mm,各相关表面的摩擦系数μ=0.18,铰链φd处摩擦损耗按5%计算。
问需选多大缸径的气缸才能将工件夹紧。
习题6-7图6-8 试分析各类钻床夹具的结构特点及应用范围。
6-9 钻床夹具在机床上的位置是根据什么确定的?车床夹具在机床上的位置是根据什么确定的?6-10 铣刀相对于铣床夹具的位置是根据什么确定的?试校核习题6-10图所示铣床夹具所标尺寸(15.43±0.06)mm 的正确性。
习题6-10图6-11 习题6-11图所示为在成批生产中钻螺栓连接孔φ7和φ5的工序简图,定位基面均为已加工面。
已知:工件两定位孔的距离为(230±0.06)mm ,大头孔直径为0.04042φ+mm ,小头孔直径为0.021022φ+mm 。
试为该工序徒手绘制一钻床夹具草图。
要求根据加工要求绘制定位元件、导向元件、夹紧装置和夹具体,并在装配图上标注装配尺寸及技术要求。
习题6-11图6-12 习题6-12图所示为大量生产中铣2mm 槽的工序简图,已知:工件定位孔间距为(170±0.05)mm ,大头孔直径为0.021026φ+mm ,小头孔直径为0.018016φ+mm 。
- 1、下载文档前请自行甄别文档内容的完整性,平台不提供额外的编辑、内容补充、找答案等附加服务。
- 2、"仅部分预览"的文档,不可在线预览部分如存在完整性等问题,可反馈申请退款(可完整预览的文档不适用该条件!)。
- 3、如文档侵犯您的权益,请联系客服反馈,我们会尽快为您处理(人工客服工作时间:9:00-18:30)。
《机械制造技术基础》部分习题参考解答
第六章机床夹具设计
6-1 机床夹具有哪几部分组成?各有何作用?
6-2 为什么夹具具有扩大机床工艺范围的作用,试举三个实例说明。
6-3 习题6-3图所示连杆在夹具中定位,定位元件分别为支承平面1、短圆柱销2和固定短V形块3。
试分析习题6-3图所示定位方案的合理性并提出改进方法。
习题6-3图习题6-6图
6-4 试分析比较可调支承、自位支承和辅助支承的作用和应用范围。
6-5 试分析各典型夹紧机构的特点及应用场合。
6-6 已知切削力F,若不计小轴1、2的摩擦损耗,试计算习题6-6图所示夹紧装置作用在斜楔左端的作用力F Q。
6-7 习题6-7图所示为气动夹紧机构,夹紧工件所需夹紧力F J=2000N,已知:气压p=4×105Pa,α=15°,L1=100mm,L2=200mm,L3=20mm,各相关表面的摩擦系数μ=0.18,铰链φd处摩擦损耗按5%计算。
问需选多大缸径的气缸才能将工件夹紧。
习题6-7图
6-8 试分析各类钻床夹具的结构特点及应用范围。
6-9 钻床夹具在机床上的位置是根据什么确定的?车床夹具在机床上的位置是根据什么确定的?
6-10 铣刀相对于铣床夹具的位置是根据什么确定的?试校核习题6-10图所示铣床夹具所标尺寸(15.43±0.06)mm 的正确性。
习题6-10图
6-11 习题6-11图所示为在成批生产中钻螺栓连接孔φ7和φ5的工序简图,定位基面均为已加工面。
已知:工件两定位孔的距离为(230±0.06)mm ,大头孔直径为0.04042φ+mm ,小头孔直径为0.021022φ+mm 。
试为该工序徒手绘制一钻床夹具草图。
要求根
据加工要求绘制定位元件、导向元件、夹紧装置和夹具体,并在装配图上标注装配尺寸及技术要求。
习题6-11图
6-12 习题6-12图所示为大量生产中铣2mm 槽的工序简图,已知:工件定位孔间
距为(170±0.05)mm ,大头孔直径为0.021026φ+mm ,小头孔直径为0.018016φ+mm 。
试为该
工序徒手绘制一铣床夹具草图。
要求根据加工要求绘制定位元件、夹紧装置、对刀元件和夹具体,并在装配图上标注装配尺寸及技术要求。
习题6-12图
第七章机械制造技术的新发展
7-1试论述当代机械制造技术的发展方向。
7-2为什么切削工具所能切除的最小极限背吃刀量与切削刃钝圆半径有关?为什么它还与机床加工系统的刚度有关?
7-3试分析归纳超精密加工与纳米级加工的基本原理。
7-4试分析超精密切削、超精密磨削的工艺特征及其应用范围。
7-5在习题7-5图中,为什么在对x方向的一对电极分别施加电压+U x和-U x后,压电陶瓷管会带动探针在x方向移动?
习题7-5图
7-6为什么说发展自动化制造技术对保证产品加工质量、提高生产效率、降低产品制造成本、提高企业的市场竞争能力均具有重要意义?试举例说明。
7-7试论述大批量生产自动化和多品种、中小批量生产自动化的异同。
7-8试分析FMC与FMS、FMS与FML的异同,各适于何种场合?
7-9影响新产品快速上市的关键环节有哪些?各有几种解决方案?试分析比较其优缺点。
7-10设计制造机械产品,怎样才能减少对环境和人体健康的负面影响,并提高资源和能源的利用率?。