棒材轧制过程数学模型
数学建模轧钢问题
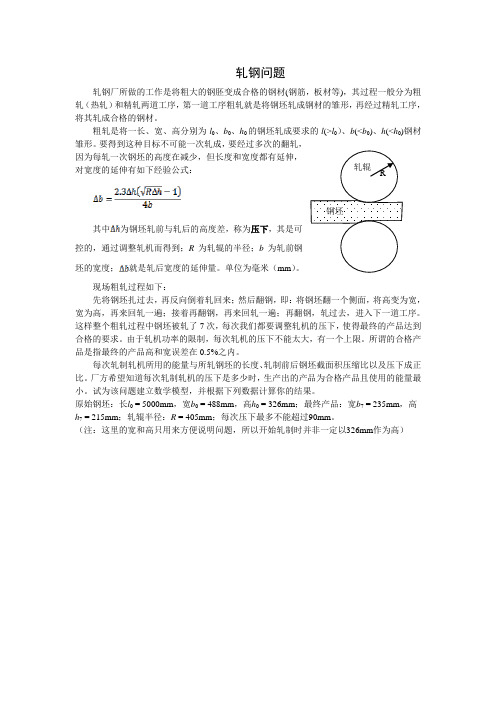
轧钢问题轧钢厂所做的工作是将粗大的钢胚变成合格的钢材(钢筋,板材等),其过程一般分为粗轧(热轧)和精轧两道工序,第一道工序粗轧就是将钢坯轧成钢材的雏形,再经过精轧工序,将其轧成合格的钢材。
粗轧是将一长、宽、高分别为l0、b0、h0的钢坯轧成要求的l(>l0)、b(<b0)、h(<h0)钢材雏形。
要得到这种目标不可能一次轧成,要经过多次的翻轧,对宽度的延伸有如下经验公式:其中为钢坯轧前与轧后的高度差,称为压下,其是可控的,通过调整轧机而得到;R为轧辊的半径;b为轧前钢坯的宽度;就是轧后宽度的延伸量。
单位为毫米(mm)。
现场粗轧过程如下:先将钢坯扎过去,再反向倒着轧回来;然后翻钢,即:将钢坯翻一个侧面,将高变为宽,宽为高,再来回轧一遍;接着再翻钢,再来回轧一遍;再翻钢,轧过去,进入下一道工序。
这样整个粗轧过程中钢坯被轧了7次,每次我们都要调整轧机的压下,使得最终的产品达到合格的要求。
由于轧机功率的限制,每次轧机的压下不能太大,有一个上限。
所谓的合格产品是指最终的产品高和宽误差在0.5%之内。
每次轧制轧机所用的能量与所轧钢坯的长度、轧制前后钢坯截面积压缩比以及压下成正比。
厂方希望知道每次轧制轧机的压下是多少时,生产出的产品为合格产品且使用的能量最小。
试为该问题建立数学模型,并根据下列数据计算你的结果。
原始钢坯:长l0 = 5000mm,宽b0 = 488mm,高h0 = 326mm;最终产品:宽b7 = 235mm,高h7 = 215mm;轧辊半径:R = 405mm;每次压下最多不能超过90mm。
(注:这里的宽和高只用来方便说明问题,所以开始轧制时并非一定以326mm作为高)。
Φ720mm周期轧管机轧制速度参数数学模型的建立

E t bI h en fM a h sa i m s tO t ema i a o t I c M de o f ̄7 0 m m l rM i Roln t 2 Pi ge l l l g Da a i
空心的毛管 ,与一般纵轧不同的是轧辊的旋转方向 与 喂入轧 件 的方 向相 反 。 当轧 辊旋转 时 ,孔 型 的净 宽尺寸在不断改变 ,因而轧辊在每旋转一周 中孑 型 L 的轮廓 尺寸不 断变 化着 周期轧管机孔型分为 4 ,钢管的变形区随着 段
孔 型的变 化而 不 断变化 ( 1 : 图 )
定 性 因素 ,在 日常 的生 产操 作和新 产 品开 发 中 占有 举 足轻 重 的地位 。通过对 周 期轧 管机 轧制 参数 计算 的基本 原 理进行 分 析 ,借 鉴 和消 化 国 内外 在周 期 轧
1 周期 轧管工艺的基本原理
11 周 期轧 管机 的轧制 过程 .
周期 轧管是 在 轧辊可 变 的孔型 中和 芯棒上 辗轧
~
大 、轧制钢种范围广 、品种规格适应性强等特点 , 比较适合生产大直径高合金厚壁无缝钢管。其所使 用 的现 代化 喂料 器采 用 了液压 机械 式 限制 喂料 装置 和转角补偿机构 ,实现 了高精度 的喂料和转 角补 偿 。油压制动装置和可调空气压缩孑 腔能保证迅速 L 而 平 稳 的制 动 ,且 易 于 实 现 喂料 器 与 轧辊 的 同步 。 周期 轧 管机 轧制 参数 作为 钢 管质量 和机 组产 能 的决
5 4
_ j 接; I 浸蔫
( )锻轧段 a
圆_椭圆_圆孔型中轧制合金钢棒材时宽展迭代模型的建立

对式 ( 24) 进行积分得到
Hm / 2 =
2 CY ・CZ + 2arctan ( CY / CZ ) ・R2g ( 25) 4 CY
引 言
随着钢铁冶金技术的快速发展 , 合金钢的应用 越来越普遍 , 其产量也大幅度提高 。在棒线材和型 钢生产中 , 合金钢占了非常大的比例 , 合金钢材的 质量不但取决于炼钢和热处理工艺 , 也与孔型系统 的设计精度和轧制生产工艺密切相关 。轧制机组的
高速化和连续化趋势对孔型系统的设计精度和轧制 工艺提出了更高的要求 。对于目前的棒线材连轧 , 大多按照圆2椭圆2圆孔型顺序轧制 , 把前一道次的 出口断面作为下一道次的入口断面 , 即每一道次的 轧后宽展都将影响后续道次的轧制工艺参数设定和 终轧产品的形状 。因此 , 连轧过程轧制工艺参数是 否合理 , 能否得到满意的成品尺寸 , 跟宽展预测模 型的精度有很大关系 。所以建立精确的合金钢棒材 轧制过程宽展预测模型有很重要的现实意义 。
第 16 卷 第 2 期 2009 年 4 月
塑性工程学报
J OU RNAL O F PL A S TICI T Y EN GIN EERIN G
Vol1 16 No1 2 Ap r1 2009
圆2椭圆2圆孔型中轧制合金钢棒材时宽展迭代模型的建立
( 燕山大学 机械工程学院 , 秦皇岛 066004 ) 董永刚 ( 哈尔滨工业大学 机电工程学院 , 哈尔滨 150001)
2
R0 ・( H0 - H m0 ) H0 = A0 - A s 2 CY0
H m0 =
A0 - A s - A h 2 CY0
R0 = Rmax + G/ 2 - H0
式中 W 0 , H0 , A 0 — — — 入口轧件最大宽度 , 最大 高度及断面积 A s , A h — — — 非接触断面的面积和高度方向减 小的断面积 H m0 — — — 出口断面等效高度 H0 — — — 入口断面等效高度 l — — — 接触区等效接触弧长 R0 — — — 入口断面轧辊平均工作半径 γ — — — 修正系数 [ 5 ] , 圆轧件进椭圆孔型轧制 碳钢时取 γ= 01 97 , 椭圆轧件进圆孔型 轧制碳钢时取 γ= 01 83 如图 1 、图 2 所示 , 求 A s 和 A h 时必须先确定 参考点 ( CY0 , CZ0 ) 的坐标 。 圆 2椭圆孔型中轧制时 , 参考点 ( CY0 , CZ0 ) 坐标 值为
棒材工艺教程(第二章第二节轧制原理2)

宽展的种类
自由宽展:坯料轧制过程中,被压下的金属 体积其金属质点横向移动时,具有垂直于轧制方 向两侧自由移动的可能性,金属流动除受接触摩 擦影响外,不受其它任何的阻碍和限制。 限制宽展:坯料轧制过程中,金属质点横向 移动时,除受接触摩擦影响外,还承受孔型侧壁 的限制作用,因而破坏了自然流动条件。 强迫宽展:坯料在轧制过程中,金属质点横 向移动时,不受任何阻碍,且受强烈的推动作用, 使轧件宽度产生附加的增长。强迫宽展要大于自 由宽展。
轧制压力
D、外摩擦的影响:轧辊与轧件间的摩擦力越大,轧制时金属流
动阻力愈大,单位压力愈大,需要的轧制力也愈大。在光滑的 轧辊上轧制比在表面粗糙的轧辊上轧制时所需要的轧制力小。 E、轧辊直径的影响:轧辊直径对轧制压力的影响通过两方面起 作用,当轧辊直径增大,变形区长度增长,使得接触面积增大, 导致轧制力增大。另一方面,由于变形区长度增大,金属流动 摩擦阻力增大,则单位压力增大,所以轧制力也增大。 F、轧件宽度的影响:轧件越宽,接触面积增加,轧制力增加; 轧件宽度对单位压力的影响一般是宽度增大,单位压力增大。 G、压下率的影响:压下率愈大,轧辊与轧件接触面积愈大,轧 制力增大;同时随着压下量的增加,平均单位压力也增大。
变形区主要参数 咬入:依靠旋转的轧 辊与轧件之间的摩擦 力,轧辊将轧件拖入 轧辊之间的现象称为 咬入。 接触弧长度:轧件与 轧辊相接触的圆弧的 水平投影长度l。 咬入角:轧件与轧辊 相接触的圆弧所对应 的圆心角α
变形区主要参数 欲使轧辊能自由咬入金属(不 对金属施加其它的外力)必须使摩 擦系数大于咬入角的正切,或者说, 必须使摩擦角大于咬入角。如果咬 入加大于摩擦角,轧辊将不能自由 咬入金属。
影响宽展的因素
E、轧制道次的影响 实验证明,在总压下量相同的条件下,轧制道次越 多,总的宽展量越小。 F、张力对宽展的影响 实验证明,后张力对宽展有很大影响,而前张力对 宽展影响很小。原因是轧件变形主要产生在后滑区。 在后滑区内随着后张力的增大,宽展减小,这是因 为在后张力作用下使金属质点纵向流动阻力减小, 必然使延伸加大、宽展减小。 G、孔型形状对宽展的影响 孔型形状对宽展量 影响也是很大的。型钢轧制时, 经常利用孔型形状达到强迫 宽展和限制宽展的目的。
棒材热连轧温度场数学模型探究

棒材热连轧温度场数学模型探究棒材热连轧是一种常见的制造方法,它可以通过连续热轧方式使金属棒材的截面积和长度发生变化,从而生产出满足不同需求的金属制品。
在这个过程中,棒材的温度变化会对整个轧制过程产生极大的影响,因此需要建立一个数学模型来预测和控制棒材的温度场变化。
棒材的热连轧实际上就是一个变温度的加工过程,所以该过程中的温度场数学模型应当包含对棒材内部和外部的温度变化进行分析。
首先,我们需要对棒材内部的温度变化进行建模。
棒材在热轧过程中会受到不同方向的压力,这会导致其表层和内部的温度变化方向和速率不同。
因此,我们需要假设棒材内部的温度分布为三维的非均匀场,并采用热传导方程进行分析:∂T/∂t=α∂^2T/∂x^2+α∂^2T/∂y^2+α∂^2T/∂z^2其中,T为温度场,t为时间,x,y,z表示三个空间方向,α为热扩散系数。
这个方程可以很好地描述棒材内部的温度变化规律,并可用于模拟棒材的加工过程。
其次,我们需要对棒材的外部温度变化进行建模。
棒材在热轧机中会受到大量的热辐射和导热,这会导致其表面温度在极短时间内发生急剧变化。
为了描述这种变化,我们可以采用一个表面传热系数来模拟棒材的表面温度变化,即:q=h(T-T∞)其中,q为表面传热流量,h为表面传热系数,T为棒材表面的温度,T∞为热环境的温度。
根据这个方程,我们可以计算出棒材表面温度的变化规律,进而对棒材的整个温度场进行建模和分析。
最后,在建立数学模型之后,我们需要进行实验验证和比对,以确保该模型的准确性和适用性。
通过实验数据的采集和处理,可以将模型预测的温度场与实际温度场进行比较,从而确定模型的可靠性和适用范围。
只有在模型的准确性得到保证的情况下,才能将其应用于实际生产中,帮助企业优化制造流程,提高产品质量。
综上所述,棒材热连轧温度场数学模型的研究是一个重要的课题,它可以从理论上分析和控制棒材的温度变化,优化制造流程,提高棒材生产效率和质量。
棒材轧制过程数学模型

1轧制过程数学模型1.1轧制工艺参数模型随着科学技术的发展,计算机已广泛应用于轧钢生产过程的控制,促使轧钢生产向自动化、高速和优质方向发展。
电子计算机在线控制生产过程,不仅仅只是电子计算机本身的硬件和软件的作用,更重要的是控制系统和各种各样的数学模型,正因为有适合轧钢生产的各种数学模型,才有可能实现电子计算机对整个轧钢生产各个环节的控制,获得高精度的产品。
线材连轧生产过程的主要内容基本上可归纳为尺寸变化和温度变化两大类性质极不相同但又相互紧密联系的物理过程,涉及的数学模型主要是轧制工艺参数的制定、各环节的温降变化、产品质量控制及实现线材连轧生产的可靠性等。
在线材连轧生产过程中,准确地计算(预估)各个环节的温度变化是实现计算机控制的重要前提,这是因为轧件各道次的变形阻力、轧制压力、轧制力矩的准确确定与温度是分不开的,而各机架轧制压力的预估精度将直接关系到设备的使用安全等。
下面分别讨论线材连轧生产过程中的温降模型、变形阻力模型、轧制力与轧制力矩模型。
1.1.1延伸系数及孔型尺寸计算模型在制订棒线材轧制工艺时,当坯料和产品断面面积F 0和F n 给定之后,总延伸系数∑μ就可唯一确定:nn n i i n i F FF F F F F F F F 011211021===-+∑ μμμμμ 其中:n ——总轧制道次;μi ——某一道次的延伸系数; F i ——某一道次的轧件断面面积。
椭圆孔示意图mB R F +-=)sin (2θθRB 2arcsin2=θ ⎪⎭⎫ ⎝⎛--=2cos 12θR h m对于圆孔,轧件断面面积可通过下式计算:圆孔示意图απθ2-=αθtan 422R R F +=1.1.2前滑模型孔型轧制时的前滑率计算可采用筱篬或斋藤提出的实验模型。
两者都认为前滑仅是轧件、孔型几何尺寸的函数。
斋藤模型以平均工作辊径定义前滑,当道次变形量较小时会出现负前滑的计算结果;筱篬模型改用孔型槽底处的最小辊径定义前滑,即前滑S f 为:S f =V 1/V R -1 (1.1) 其中:V 1 ,V R ——轧件出口速度及孔型槽底处的轧辊线速度。
轧制过程数学模型
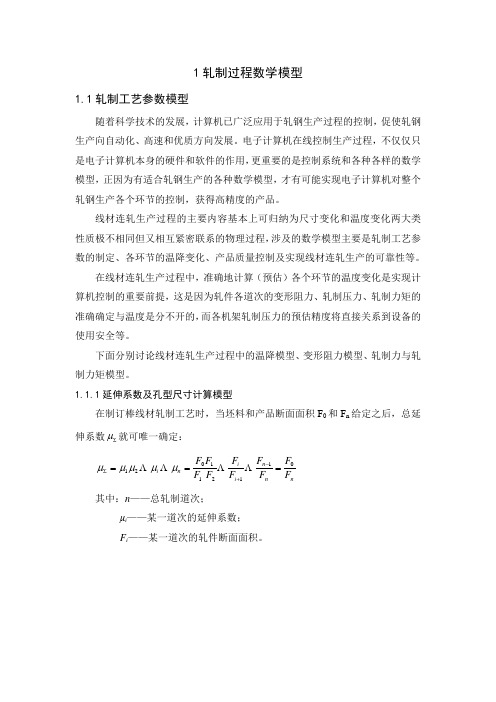
1轧制过程数学模型1.1轧制工艺参数模型随着科学技术的发展,计算机已广泛应用于轧钢生产过程的控制,促使轧钢生产向自动化、高速和优质方向发展。
电子计算机在线控制生产过程,不仅仅只是电子计算机本身的硬件和软件的作用,更重要的是控制系统和各种各样的数学模型,正因为有适合轧钢生产的各种数学模型,才有可能实现电子计算机对整个轧钢生产各个环节的控制,获得高精度的产品。
线材连轧生产过程的主要内容基本上可归纳为尺寸变化和温度变化两大类性质极不相同但又相互紧密联系的物理过程,涉及的数学模型主要是轧制工艺参数的制定、各环节的温降变化、产品质量控制及实现线材连轧生产的可靠性等。
在线材连轧生产过程中,准确地计算(预估)各个环节的温度变化是实现计算机控制的重要前提,这是因为轧件各道次的变形阻力、轧制压力、轧制力矩的准确确定与温度是分不开的,而各机架轧制压力的预估精度将直接关系到设备的使用安全等。
下面分别讨论线材连轧生产过程中的温降模型、变形阻力模型、轧制力与轧制力矩模型。
1.1.1延伸系数及孔型尺寸计算模型在制订棒线材轧制工艺时,当坯料和产品断面面积F 0和F n 给定之后,总延伸系数∑μ就可唯一确定:nn n i i n i F FF F F F F F F F 011211021===-+∑ μμμμμ 其中:n ——总轧制道次;μi ——某一道次的延伸系数; F i ——某一道次的轧件断面面积。
椭圆孔示意图mB R F +-=)sin (2θθRB 2arcsin2=θ ⎪⎭⎫ ⎝⎛--=2cos 12θR h m对于圆孔,轧件断面面积可通过下式计算:圆孔示意图απθ2-=αθtan 422R R F +=1.1.2前滑模型孔型轧制时的前滑率计算可采用筱篬或斋藤提出的实验模型。
两者都认为前滑仅是轧件、孔型几何尺寸的函数。
斋藤模型以平均工作辊径定义前滑,当道次变形量较小时会出现负前滑的计算结果;筱篬模型改用孔型槽底处的最小辊径定义前滑,即前滑S f 为:S f =V 1/V R -1 (1.1) 其中:V 1 ,V R ——轧件出口速度及孔型槽底处的轧辊线速度。
大棒材热轧工艺的数值模拟

大棒材热轧工艺的数值模拟随着经济的飞速发展和人们对品质的不断追求,大棒材热轧工艺在现代工业中起着越来越重要的作用。
而数值模拟则是优化大棒材热轧工艺的重要手段之一。
本文将介绍大棒材热轧工艺的数值模拟。
一、大棒材热轧工艺的基本情况大棒材是常用的钢材产品之一,应用广泛。
大棒材热轧工艺指的是将钢坯通过连续轧机进行加工,使其变形成为规定形状的钢材产品。
该加工过程需要高温高压,同时还需要对加工参数进行精确控制,从而使得最终的钢材产品符合规定的标准。
大棒材的热轧工艺一般可分为三个阶段:初轧、中轧和精轧。
其中初轧阶段是将加热后的钢坯进行初步加工,此时钢坯已经被加热至膨胀状态,因此此阶段的加工需要控制好加热温度和轧制速度。
中轧阶段则需要进一步加工,此时钢坯的温度和塑性都较高,可进行更大程度的变形,但同时也需要保证轧制速度和加热温度的平衡。
精轧阶段是将已经经过初轧和中轧的钢坯进行进一步的加工,此时钢坯的温度已经下降,但依然需要保证加工参数的精确定位。
二、大棒材热轧工艺的数值模拟大棒材热轧工艺的数值模拟指的是通过数值方法对大棒材热轧过程进行模拟和分析,从而优化加工参数,提高产品质量和生产效益的一种方法。
其具有以下几个优点:1、可模拟多种不同情况下的加工效果通过数值模拟方法,可以模拟不同加工参数下的钢材加工效果。
这些参数包括钢坯的加热温度、轧制速度、轧制力、模具几何形状等等。
模拟结果可以帮助工程师了解每个参数对加工质量的影响,从而优化加工方案。
2、可提高生产效率通过数值模拟方法,可以根据模拟结果来优化加工参数,降低产品的废品率,提高生产效率。
这样可以帮助企业减少损失,提高生产效益。
3、可降低人为干预在传统的加工过程中,需要大量的人为干预,以调整加工参数,从而达到理想的加工效果。
而数值模拟方法则可以帮助减少或消除这些干预,从而提高加工的精度和稳定性。
4、可节约成本数值模拟方法可以帮助企业节约成本,减少试错次数,提高生产效率,降低废品率,从而改善企业的经济效益。
- 1、下载文档前请自行甄别文档内容的完整性,平台不提供额外的编辑、内容补充、找答案等附加服务。
- 2、"仅部分预览"的文档,不可在线预览部分如存在完整性等问题,可反馈申请退款(可完整预览的文档不适用该条件!)。
- 3、如文档侵犯您的权益,请联系客服反馈,我们会尽快为您处理(人工客服工作时间:9:00-18:30)。
1轧制过程数学模型1.1轧制工艺参数模型随着科学技术的发展,计算机已广泛应用于轧钢生产过程的控制,促使轧钢生产向自动化、高速和优质方向发展。
电子计算机在线控制生产过程,不仅仅只是电子计算机本身的硬件和软件的作用,更重要的是控制系统和各种各样的数学模型,正因为有适合轧钢生产的各种数学模型,才有可能实现电子计算机对整个轧钢生产各个环节的控制,获得高精度的产品。
线材连轧生产过程的主要内容基本上可归纳为尺寸变化和温度变化两大类性质极不相同但又相互紧密联系的物理过程,涉及的数学模型主要是轧制工艺参数的制定、各环节的温降变化、产品质量控制及实现线材连轧生产的可靠性等。
在线材连轧生产过程中,准确地计算(预估)各个环节的温度变化是实现计算机控制的重要前提,这是因为轧件各道次的变形阻力、轧制压力、轧制力矩的准确确定与温度是分不开的,而各机架轧制压力的预估精度将直接关系到设备的使用安全等。
下面分别讨论线材连轧生产过程中的温降模型、变形阻力模型、轧制力与轧制力矩模型。
1.1.1延伸系数及孔型尺寸计算模型在制订棒线材轧制工艺时,当坯料和产品断面面积F 0和F n 给定之后,总延伸系数∑μ就可唯一确定:nnn i i n i F F F F F F F F F F 011211021===-+∑μμμμμ其中:n ——总轧制道次;μi ——某一道次的延伸系数; F i ——某一道次的轧件断面面积。
椭圆孔示意图mBR F +-=)sin (2θθRB 2arcsin2=θ⎪⎭⎫ ⎝⎛--=2cos 12θR h m对于圆孔,轧件断面面积可通过下式计算:圆孔示意图απθ2-=αθtan 422R R F +=1.1.2前滑模型孔型轧制时的前滑率计算可采用筱篬或斋藤提出的实验模型。
两者都认为前滑仅是轧件、孔型几何尺寸的函数。
斋藤模型以平均工作辊径定义前滑,当道次变形量较小时会出现负前滑的计算结果;筱篬模型改用孔型槽底处的最小辊径定义前滑,即前滑S f 为:S f =V 1/V R -1 (1.1) 其中:V 1 ,V R ——轧件出口速度及孔型槽底处的轧辊线速度。
在孔型中轧制时,前滑值取平均值f S ,其计算式为()[]1cos 1cos ++-=hhD Sfγγ⎪⎪⎭⎫ ⎝⎛+=βααγ212 Dh H --=1cos α式中 γ——变形区中性角的平均值; α——咬入角的平均值;β——摩擦角,一般为21~27度; D ——轧辊工作直径的平均值;h H ,——轧件轧前、轧后高度的平均值; 1.1.3轧件温降模型轧件在轧制过程中的温度变化,是由辐射、传导、对流引起的温降和金属变形所产生的温升合成的,可用下式表示:b d Z f T T T T T ∆-∆+∆+∆=∆(1.5)以上四项起作用的是辐射损失和金属变形热所产生的温升。
各项温度变化的计算按下式进行:1、由于辐射引起的温降计算 41000072.0⎪⎭⎫⎝⎛=∆T G Ft T f(1.6)式中:ΔT f ——辐射引起的温降,℃; F ——轧件的散热表面积,m 2; t ——冷却时间,s ;T ——轧件表面绝对温度,K 。
2、由于传导引起的温降计算cZ Z Z Gh c t F T 08.1λ=∆ (1.7)式中:ΔT Z ——传导引起的温降,℃;λ——钢材的导热系数,λ≈1.255KJ/(m ·h ·℃);Fz ——轧件与导热系体的接触面积,m 2,对于轧辊Fz =2l c b c ×10-6;l c ——轧件与轧辊的接触弧长,mm ; b c ——轧件轧前与轧后的平均宽度,mm ;c 0——钢材平均比热容,在若杂货温度西热轧温度下取c 0=0.627KJ/Kg ·℃tz ——传导时间,s ;hc ——轧件轧前与轧后的平均高度,mm 。
3、由于对流引起的温降计算 frd T T T T t V T T T ∆⎪⎭⎫⎝⎛-⎥⎥⎦⎤⎢⎢⎣⎡+-∆405.220301003.0ε(1.8)式中ΔTd ——对流引起的温降,℃; T ——轧件表面绝对温度,K ; T 0——环境绝对温度,K ; V 0——轧件的移动速度,m/s ; t ——对流时间,s ;εr ——轧件表面的相对黑度,εr ≈0.8;ΔTf ——同时间内的辐射温降,℃; 4、由于变形热产生的温升计算 Gc a A T b 0427)1(-=∆(1.9)式中ΔTb ——变形热产生的温升,℃;A ——该道次所需变形功,根据公式A=pVln(H/h);P ——平均单位压力,MPa ,粗略估计可用p=(t y0-t -75)×σb /1500计算; V ——轧件体积,mm 3H 、h ——轧件轧前、轧后高度,mm ;a ——系数,表明被轧件吸收的变形能的相对部分,在T/T y0>0.4时,当静力变形时(102s -1)为0.9%~2.6%; 当动力变形时(102s -1)为19%~21%;σb ——强度极限,MPa ; t y0——钢材的熔点温度,K 。
取钢材的密度γ=7.8,则得:)/l n ()1(184.0h H a p T b -=∆(1.10)由于传导和对流引起的温降很小,甚至可以忽略不计。
此时可以采用А.И.采利柯夫方法计算在孔型中轧制和移送到下一孔型时间内,轧件温度得变化:27327310000255.0100033100+⎪⎪⎭⎫ ⎝⎛+∆++-=∆t t Fltt T (1.11)式中t 0——进入该孔型前得轧件温度,℃; l ——轧后轧件横截面周边长,mm ; F ——轧后轧件横截面面积,mm 2; t ——轧件冷却时间,s ;Δt 1——在该孔型中金属温度得升高,℃; Δt 1值按下式确定:Δt 1=0.183K m ln μ(1.13) 式中K m ——金属塑性变形抗力,MPa ; μ——延伸系数。
1.1.4变形抗力模型钢铁材料在热状态下的物理特性,与其温度、化学成分、应力、应变状态等诸多因素有关。
目前在这方面的研究还不够充分,对于大多数钢种,只能给出离散数据的描述;但对于碳钢,平均变形抗力(MPa/mm 2)可按以下模型计算: m m f m f K )10/(εσ=(1.14)其中:f σ——简单应力状态下的材料热变形抗力。
0.28exp (05.001.00.5+-C T) (T ≥T d )f σ=0.28g (C,t )exp(05.001.00.5+-C T d) (T <T d )(1.15)式中:参数T ,T d 按下式计算: T=10002730+tT d =0.9532.041.0++C C(1.16)其中:t 0——轧件温度;C ——材料的碳含量百分数。
式(2)中的函数g(C,t)为:09.006.042.049.095.0)9.0(0.30),(2+++⎪⎭⎫ ⎝⎛++-∙+=C C C C T C t C g (1.17) 式(1)中的f m 为考虑材料应变量等因素的影响系数:⎪⎪⎭⎫⎝⎛-⎪⎪⎭⎫⎝⎛+=2.015.02.013.1εεnmn f C n 07.041.0-=(1.18)在孔型设计时,式(1)、式(5)中的平均应变ε和平均应变速率.ε按下式计算: ε=ln HF F F -00.ε=mm L N R 602επ(1.19)其中:F 0,F H ——轧件入口断面面积和轧件被孔型压掉部分的断面面积; F ——轧辊平均工作半径; N ——轧辊转数,r/min ; Lm ——接触弧平均长度。
式(1)中的指数m 由下式给出:(—0.019C +0.126)T +0.075C -0.05 (T ≥T d )(0.081C -0.154)T +-0.019C +0.207+0.027/(C +0.32)(T ≤Td ) (1.20) 该模型的适用范围为:材料的碳含量小于1.2%,温度在(700-1200)℃范围内,平均应变小于0.7,平均应变速率在(0.1~100)s -1范围之内,该模型的最大优点是其数学上的完整性,利于实现计算机编程计算,但也因此使其精确性有所降低,可用来进行预报。
另外,为了适应计算机在线控制轧钢生产对变形阻力数学模型的要求和进一步提高计算精度,周纪华等采用碳钢和合金在高温、高速下测定得到的变形温度、变形速度和变形程度对变形阻力影响的大量实测数据而建立了非线性回归模型。
它是以各种钢种为单位,得到各回归系数值,结构如下式。
⎥⎥⎦⎤⎢⎢⎣⎡--⎪⎭⎫ ⎝⎛⨯⎪⎭⎫⎝⎛+=+4.0)1(4.010)exp(66210543γγμσσa a a T a a a T a (1.21)式中 1000273+=t T ;0σ——基准变形阻力,即t =1000℃、γ=0.4和μ=10s-1时的变形阻力(MPa );t ——变形温度(℃);u ——变形速度(s -1); γ——变形程度(对数应变);γ⋅=lv u 1, (1.23))ln(μγ= (1.24)式中 v 1——轧件出口速度; l ——变形区长度; R ——轧辊半径; h 0——轧前高度。
0σ、1a ~6a ——回归系数,其值取决于钢种。
各回归系数值按钢种的分类列于表1-1至表1-14。
表1-1普通碳钢变形抗力数学模型回归系数表1-2优质碳素结构钢变形抗力数学模型回归系数表1-3低合金钢变形抗力数学模型回归系数注:1.①②③表示Nb含量不同。
2.*在进行变形抗力试验时,将试件加热到1250℃,再冷却到850~1150℃进行压缩得到变形抗力的试验数据。
表1-4合金结构钢变形抗力数学模型回归系数表1-5碳素工具钢变形抗力数学模型回归系数表1-6合金工具钢变形抗力数学模型回归系数表1-7弹簧钢变形抗力数学模型回归系数表1-8轴承钢变形抗力数学模型回归系数表1-9不锈耐酸钢变形抗力数学模型回归系数表1-10硅钢变形抗力数学模型回归系数将此模型的计算结果与经典的变形抗力曲线图对比后发现,当变形速度在1~30s -1,变形温度在850~1200℃之间时,结果能够很好的吻合曲线。
因此在编制程序进行计算时采用的便是此模型。
1.1.5轧制压力模型工程计算中经常采用如下简化的专用于孔型轧制的轧制压力公式计算轧制压力:Q F K P d m =(1.25) 式中:m K ——平均变形抗力;dF ——接触投影面积;确定轧件与轧辊的接触面积,经常采用如下公式:用矩形-箱形孔,方-六角,六角-方,方-平椭圆,平椭圆-方以及矩形-平辊系统轧制时⎪⎪⎭⎫ ⎝⎛-+=1122101ηA B B H S (1.26) 按方-椭轧制方案时75.0)1(121-+=A H S ηξη(1.27)()⎪⎪⎭⎫ ⎝⎛++⎪⎪⎭⎫⎝⎛-++⎪⎪⎭⎫ ⎝⎛-++=213.009.011845.0375.01128.0)1(29.071.0221k k a a ηηηδξ 按椭-椭,椭-圆,圆-椭,椭-立椭和立椭-椭轧制时⎪⎪⎭⎫⎝⎛-=1121ηξA H S (1.28) 椭圆-圆 )1.01)(62.1(201K K a a --=δδξ(1.29)圆-椭圆 )4.01)(62.1(2101δδδξK K a a +-=(1.30)Q ——载荷系数,针对各种孔型轧制情况的Q 值回归模型为:WW Q /61.10771.0731.0++-=式中:W ——考虑不同轧制条件的无量纲参数; 102F F F W d +=其中:10,F F 分别如出口断面面积。