提高孔加工的精度的方法终审稿)
提高钻孔精度的方法
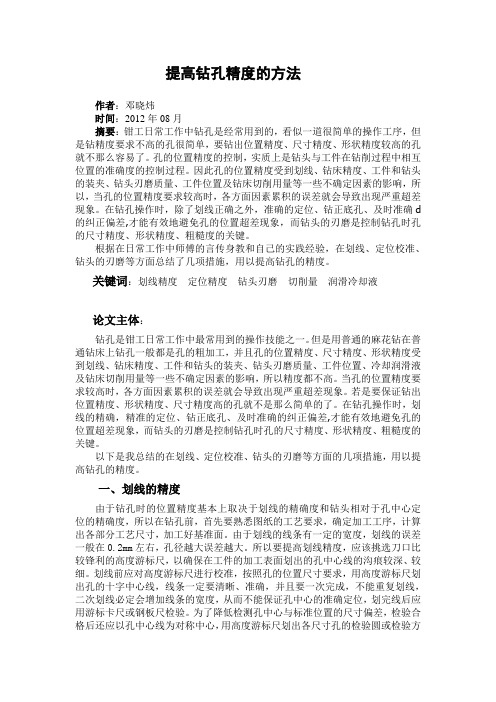
提高钻孔精度的方法作者:邓晓炜时间:2012年08月摘要:钳工日常工作中钻孔是经常用到的,看似一道很简单的操作工序,但是钻精度要求不高的孔很简单,要钻出位置精度、尺寸精度、形状精度较高的孔就不那么容易了。
孔的位置精度的控制,实质上是钻头与工件在钻削过程中相互位置的准确度的控制过程。
因此孔的位置精度受到划线、钻床精度、工件和钻头的装夹、钻头刃磨质量、工件位置及钻床切削用量等一些不确定因素的影响,所以,当孔的位置精度要求较高时,各方面因素累积的误差就会导致出现严重超差现象。
在钻孔操作时,除了划线正确之外,准确的定位、钻正底孔、及时准确d 的纠正偏差,才能有效地避免孔的位置超差现象,而钻头的刃磨是控制钻孔时孔的尺寸精度、形状精度、粗糙度的关键。
根据在日常工作中师傅的言传身教和自己的实践经验,在划线、定位校准、钻头的刃磨等方面总结了几项措施,用以提高钻孔的精度。
关键词:划线精度定位精度钻头刃磨切削量润滑冷却液论文主体:钻孔是钳工日常工作中最常用到的操作技能之一。
但是用普通的麻花钻在普通钻床上钻孔一般都是孔的粗加工,并且孔的位置精度、尺寸精度、形状精度受到划线、钻床精度、工件和钻头的装夹、钻头刃磨质量、工件位置、冷却润滑液及钻床切削用量等一些不确定因素的影响,所以精度都不高。
当孔的位置精度要求较高时,各方面因素累积的误差就会导致出现严重超差现象。
若是要保证钻出位置精度、形状精度、尺寸精度高的孔就不是那么简单的了。
在钻孔操作时,划线的精确,精准的定位、钻正底孔、及时准确的纠正偏差,才能有效地避免孔的位置超差现象,而钻头的刃磨是控制钻孔时孔的尺寸精度、形状精度、粗糙度的关键。
以下是我总结的在划线、定位校准、钻头的刃磨等方面的几项措施,用以提高钻孔的精度。
一、划线的精度由于钻孔时的位置精度基本上取决于划线的精确度和钻头相对于孔中心定位的精确度,所以在钻孔前,首先要熟悉图纸的工艺要求,确定加工工序,计算出各部分工艺尺寸,加工好基准面。
一种提高C型中心孔加工精度和效率的方法
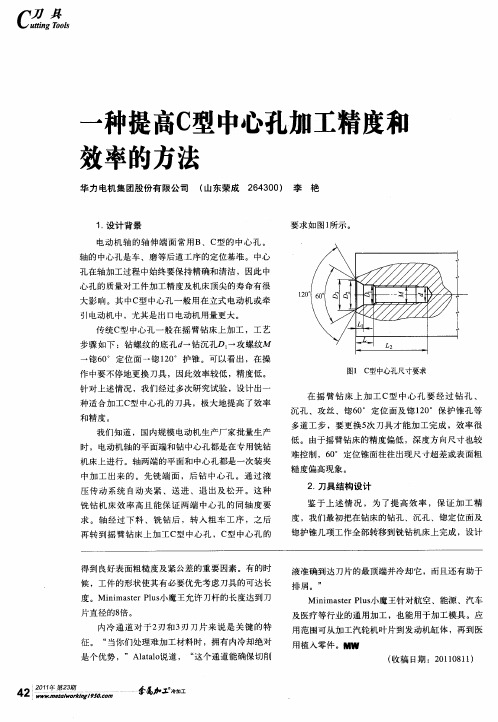
我们知道 ,国内规模 电动机生产厂 家批量生产 时 ,电动机轴 的平面端和钻 中心孔都是在专用铣钻 机床上进行。轴两端的平面和中心孔都是一次装夹 中加工 出来的 。先铣 端面 ,后 钻 中心 孔 。通过 液
及医疗等行业的通用加工 ,也能用于加工模具 。应 用范围可从加工汽轮机叶片到发动机缸体 ,再到医 用植入零件。MW ( 收稿 日期 :2 10 1 ) 0 181
内冷通 道对 于2 刃和3 刀片 来说是 关键 的特 刃
征 。 “ 你们 处 理难 加 工 材 料 时 ,拥 有 内冷 却 绝 对 当
是个优势 ,”A aa 说道 , “ l l to 这个通道能确保切削
4 2
嘲, 一
参磊 籼工
引 电动 机 中 ,尤 其 是 出 口电动机 用 量 更大 。
要求如图1 示。 N
传 统c型中心孔一般在摇 臂钻床 上加 工,工艺
步 骤 如 下 :钻 螺 纹 的底 孔 钻 沉 孔D 一攻 螺 纹M 一
一
锪 6 。 定位 面 一锪 10 护 锥 。可 以 看 出 ,在操 0 2。
得到 良好表面粗糙度及紧公差的重要因素 。有的时 候 ,工件 的形状使其有必要优先考虑刀具的可达长 度 。Mii atr ls  ̄ nm s ud 魔王允许刀杆的长度达到刀 eP
片 直 径 的8 。 倍
液准确到达刀片的最顶端并冷却它 ,而且还 有助于
排 屑 。” Mii s r lsa 王针 对 航 空 、能 源 、汽车 nm退 出 及 松 开 。 这 种
试论如何提高钻孔的加工精度

试论如何提高钻孔的加工精度摘要:结合钻孔的实际要求,合理的提高钻孔加工精度,对于保证钻孔的质量有很大帮助。
然而,在这之前需要详细的分析钻孔容易产生的缺陷及其原因,以此作为提高钻孔加工精度注意事项的依据,才能够保证钻孔加工质量,使其能够合理的运用。
因此,本文就如何提高钻孔的加工精度进行详细的分析和探讨,希望对提高钻孔质量有一定的作用。
关键词:钻孔加工精度钻削钻孔是一项非常基本的、简单的工作,在很多不同类型的工作中都会用到。
尽管钻孔操作非常的简单,但是在进行钻孔的过程中很容易受到某些不良因素的影响而出现错误。
为了最大限度的提高钻孔质量,需要就当前钻孔工作进行详细的分析,找出其中存在的缺陷,采用适合的措施对钻孔进行优化,提高钻孔的加工精度,使钻孔能够有效的应用。
一、钻孔容易产生的缺陷及原因分析所谓钻孔是指在实体材料上加工孔的方法。
对于机械加工操作工来说是一项简单的基本工作。
然而,钻孔工作容易产生缺陷,降低工作质量。
为了能够最大限度的提高钻孔质量,对钻孔比较容易产生的缺陷及原因进行分析是非常必要的。
以下笔者就钻孔容易产生的缺陷及其原因提出了几点自己的观点。
1.钻孔容易呈现多角度。
钻孔过程中,所应用的钻头容易受到某些因素的影响而出现角度不对称、两切削刃的长短不一等情况,应用此种不标准的钻头就会导致钻孔呈现多个角度的问题。
2.钻孔后孔径超出标准要求。
钻孔过程中所应用的钻孔技术如若出现钻头摆动、两切削刃高度或长短不标准等情况都会使钻孔增大,此种情况的出现对后续的工作影响较大,应当将提高钻孔的加工精度中作为工作重点。
3.钻孔位置出现偏差。
对钻孔工作有一定了解的人都知道,在实体材料上进行钻孔,必须保证钻头与实体材料是垂直的,这样才能够保证钻孔的标准。
然而,钻孔位置出现偏差的情况在钻孔工作确是比较常见的。
导致此缺陷出现的主要原因是工件安装不正确,钻头垂直方向对准的工件位置并不是标准位置,钻孔后就会得到位置出现偏差的钻孔。
孔加工精度的提高
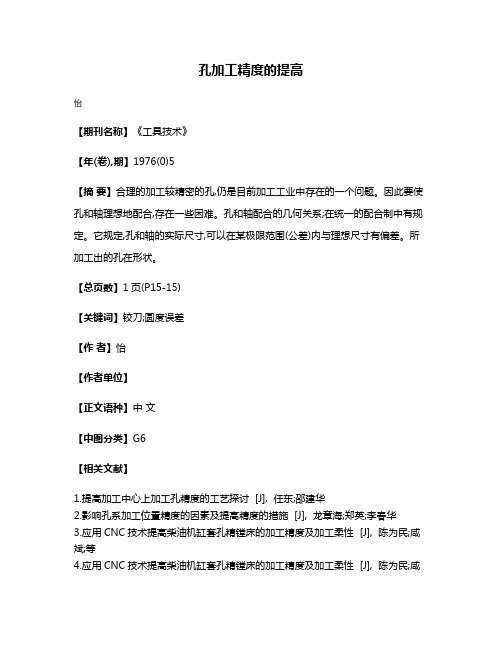
孔加工精度的提高
怡
【期刊名称】《工具技术》
【年(卷),期】1976(0)5
【摘要】合理的加工较精密的孔,仍是目前加工工业中存在的一个问题。
因此要使孔和轴理想地配合,存在一些困难。
孔和轴配合的几何关系;在统一的配合制中有规定。
它规定,孔和轴的实际尺寸,可以在某极限范围(公差)内与理想尺寸有偏差。
所加工出的孔在形状。
【总页数】1页(P15-15)
【关键词】铰刀;圆度误差
【作者】怡
【作者单位】
【正文语种】中文
【中图分类】G6
【相关文献】
1.提高加工中心上加工孔精度的工艺探讨 [J], 任东;邵建华
2.影响孔系加工位置精度的因素及提高精度的措施 [J], 龙章海;郑英;李春华
3.应用CNC技术提高柴油机缸套孔精镗床的加工精度及加工柔性 [J], 陈为民;咸斌;等
4.应用CNC技术提高柴油机缸套孔精镗床的加工精度及加工柔性 [J], 陈为民;咸
斌;华茂发
5.提高钻、铰孔加工精度的加工方法 [J], 狄庆华;张长明;丁华中;贾大虎;吴狄因版权原因,仅展示原文概要,查看原文内容请购买。
浅谈提高孔加工精度的方法
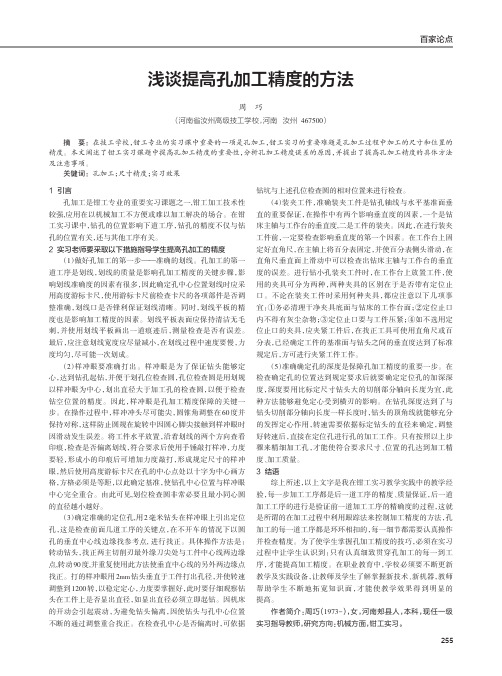
百家论点浅谈提高孔加工精度的方法周巧(河南省汝州高级技工学校,河南汝州467500)摘要:在技工学校,钳工专业的实习课中重要的一项是孔加工,钳工实习的重要难题是孔加工过程中加工的尺寸和位置的精度。
本文阐述了钳工实习课题中提高孔加工精度的重要性,分析孔加工精度误差的原因,并提出了提高孔加工精度的具体方法及注意事项。
关键词:孔加工;尺寸精度;实习效果1引言孔加工是钳工专业的重要实习课题之一,钳工加工技术性较强,应用在以机械加工不方便或难以加工解决的场合。
在钳工实习课中,钻孔的位置影响下道工序,钻孔的精度不仅与钻孔的位置有关,还与其他工序有关。
2实习老师要采取以下措施指导学生提高孔加工的精度(1)做好孔加工的第一步——准确的划线。
孔加工的第一道工序是划线,划线的质量是影响孔加工精度的关键步骤,影响划线准确度的因素有很多,因此确定孔中心位置划线时应采用高度游标卡尺,使用游标卡尺前检查卡尺的各项部件是否调整准确,划线口是否锋利保证划线清晰。
同时,划线平板的精度也是影响加工精度的因素。
划线平板表面应保持清洁无毛刺,并使用划线平板画出一道痕迹后,测量检查是否有误差。
最后,应注意划线宽度应尽量减小,在划线过程中速度要慢,力度均匀,尽可能一次划成。
(2)样冲眼要准确打出。
样冲眼是为了保证钻头能够定心,达到钻孔起钻,并便于划孔位检查圆,孔位检查圆是用划规以样冲眼为中心,划出直径大于加工孔的检查圆,以便于检查钻空位置的精度。
因此,样冲眼是孔加工精度保障的关键一步。
在操作过程中,样冲冲头尽可能尖,圆锥角调整在60度并保持对称,这样防止圆规在旋转中因圆心脚尖接触到样冲眼时因滑动发生误差。
将工件水平放置,沿着划线的两个方向查看印痕,检查是否偏离划线,符合要求后使用手锤敲打样冲,力度要轻,形成小的印痕后可增加力度敲打,形成规定尺寸的样冲眼,然后使用高度游标卡尺在孔的中心点处以十字为中心画方格,方格必须是等距,以此确定基准,使钻孔中心位置与样冲眼中心完全重合。
提高钻孔精度的方法(1)
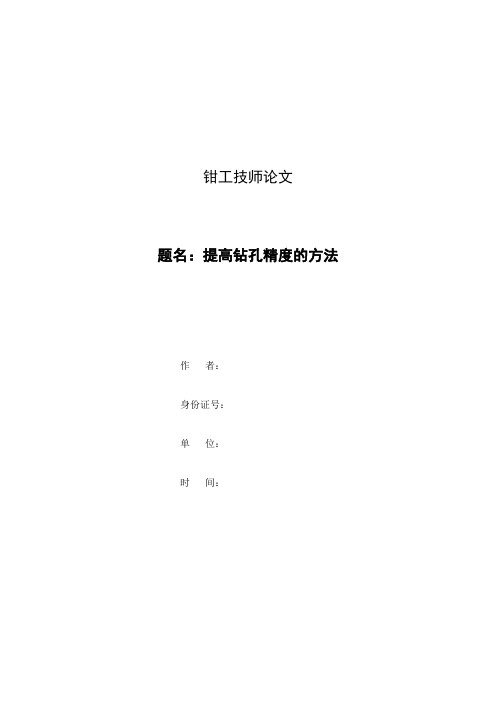
钳工技师论文题名:提高钻孔精度的方法作者:身份证号:单位:时间:提高钻孔精度的方法作者:邓晓炜时间:2012年08月摘要:钳工日常工作中钻孔是经常用到的,看似一道很简单的操作工序,但是钻精度要求不高的孔很简单,要钻出位置精度、尺寸精度、形状精度较高的孔就不那么容易了。
孔的位置精度的控制,实质上是钻头与工件在钻削过程中相互位置的准确度的控制过程。
因此孔的位置精度受到划线、钻床精度、工件和钻头的装夹、钻头刃磨质量、工件位置及钻床切削用量等一些不确定因素的影响,所以,当孔的位置精度要求较高时,各方面因素累积的误差就会导致出现严重超差现象。
在钻孔操作时,除了划线正确之外,准确的定位、钻正底孔、及时准确d 的纠正偏差,才能有效地避免孔的位置超差现象,而钻头的刃磨是控制钻孔时孔的尺寸精度、形状精度、粗糙度的关键。
根据在日常工作中师傅的言传身教和自己的实践经验,在划线、定位校准、钻头的刃磨等方面总结了几项措施,用以提高钻孔的精度。
关键词:划线精度定位精度钻头刃磨切削量润滑冷却液论文主体:钻孔是钳工日常工作中最常用到的操作技能之一。
但是用普通的麻花钻在普通钻床上钻孔一般都是孔的粗加工,并且孔的位置精度、尺寸精度、形状精度受到划线、钻床精度、工件和钻头的装夹、钻头刃磨质量、工件位置、冷却润滑液及钻床切削用量等一些不确定因素的影响,所以精度都不高。
当孔的位置精度要求较高时,各方面因素累积的误差就会导致出现严重超差现象。
若是要保证钻出位置精度、形状精度、尺寸精度高的孔就不是那么简单的了。
在钻孔操作时,划线的精确,精准的定位、钻正底孔、及时准确的纠正偏差,才能有效地避免孔的位置超差现象,而钻头的刃磨是控制钻孔时孔的尺寸精度、形状精度、粗糙度的关键。
以下是我总结的在划线、定位校准、钻头的刃磨等方面的几项措施,用以提高钻孔的精度。
一、划线的精度由于钻孔时的位置精度基本上取决于划线的精确度和钻头相对于孔中心定位的精确度,所以在钻孔前,首先要熟悉图纸的工艺要求,确定加工工序,计算出各部分工艺尺寸,加工好基准面。
谈如何提高钻孔精度(最新整理)
谈如何提高钻孔精度江苏省徐州技师学院孙波内容摘要如何提高钻孔精度一直是钳工教师探讨的一个热门话题。
本文作者结合自己的教学实践经验对此进行了论述,望与同行交流。
关键词钻孔精度刃磨划线装夹找正钻孔是钳工的一项重要基本操作技能,因此钻孔精度的提高是钳工实习教学的重点,同时也是难点。
学生在实习操作中存在的主要问题是:1、划线精度不高,造成孔距超差;2、钻头刃磨质量较差,造成孔径扩大、孔面粗糙;3、钻孔时没有找正或找正不准,盲目落钻,造成钻头中心线与孔中心线不重合;4、对刀时强行找正,使钻头(特别是小钻头)弯曲,孔轴心线倾斜;5、歪斜时强行借正,造成钻头折断。
如何才能避免上述问题的发生,钻出精确的孔呢?笔者结合自己多年的教学实践经验,谈谈自己的一点体会。
1刃磨好钻头是前提要钻出精确的孔,必须刃磨好钻头。
俗话说:“三分功夫,七分刀具。
”钻孔前应选择好相应的钻头进行刃磨。
刃磨的钻头除了保正顶角、后角、横刃斜角准确,两主切削刃长度相等且与钻头中心线对称、两主后刀面光滑外,为便于定心和减小孔壁的粗糙,还应对横刃和主切削刃做适当修磨(最好先在砂轮机上粗磨,再在油石上精修)。
针对不同情况,适当修磨棱边、前刀面、分屑槽等也是非常必要的,这是钻好孔的前提。
由于学生初学时,对这些不易掌握,除要求他们多练习刃磨以外,检验刃磨质量最好的方法是试钻。
用自己刃磨的钻头在废料上练习钻孔,通过观察切削的平稳性、出屑的流畅、对称与否,判定刃磨质量,如此反复试钻、修磨,直至合格。
2精确划线是基础用高度尺精确划线,首先应保正尺寸准确,划线时使划针角与工件划线平面之间形成40~60度的夹角(沿划线方向),使划出的线条清晰均匀。
要注意划线基准面的选择,基准面要加工精确,要保证本身的平面度及与相邻面的垂直度。
孔位十字线划出后,为保证钻孔时便于找正,应用中心冲在十字线上冲出中心点(要求冲点要小,位置要准)。
首先用刃磨准确锋利的30度中心冲轻轻在十字线上冲出较浅的锥坑,观察无偏差后再用60度中心冲扩大冲出稍深锥坑,然后根据所钻孔用划规划出几个大小不等的同心检查圆,也可以中心点为中心划出大小不一的几个检查方。
浅析提高钻孔加工质量的方法
浅析提高钻孔加工质量的方法钻孔加工是机械加工中常用的方法,本文从分析问题和问题产生的原因入手,总结了在实际生产中如何巧妙运用刃磨和找正,来提高钻孔质量。
一、钻孔时可能出现的问题和产生原因1.孔大于规定尺寸(1)钻头两切削刃长度不等,高低不一致。
(2)钻床主轴径向偏摆或工作台未锁紧有松动。
(3)钻头本身弯曲或装夹不好,使钻头有过大的径向跳动现象。
2.孔壁粗糙(1)钻头不锋利。
(2)进给量太大。
(3)切削液选用不当或供应不足。
(4)钻头过短,排屑槽堵塞。
3.孔位偏移(1)工件划线不正确。
(2) 钻头横刃太长定心不准,起钻过偏。
4.孔歪斜(1)工件上与孔垂直的平面与钻轴不垂直或钻床主轴与台面不垂直。
(2)安装接触面上的切屑未清除干净。
(3)工件装夹不稳,钻孔时产生歪斜,或工件有砂眼。
(4)进给量过大使钻头产生弯曲变形。
5.钻孔呈多角形(1)钻头后角太大。
(2)钻头两主切削刃长短不一,角度不对称。
6.钻头工作部分折断(1)钻头用钝仍继续钻孔。
(2)钻孔时未经常退钻排屑。
(3)孔将钻通时没有减小给进量。
(4)工件未夹紧。
(5)在钻黄铜一类软金属时,钻头后角太大。
前角又没有修磨小造成扎刀。
7.切削刃迅速磨损或碎裂(1)切削速度太快。
(2)没有根据工件材料硬度来刃磨钻头角度。
(3)工件表皮或内部硬度高或有砂眼。
(4)进给量过大。
(5)切削液不足。
二、针对问题和原因对钻头作刃磨和找正1.钻头刃磨钻头初磨后,把钻头切削部分向上竖立,视线与钻头轴线平行,同时目测两主切削刃长短,以及切削后角。
用角尺测量主切削刃与钻头轴线夹角,感觉一致后在钻床试钻孔。
测量孔径,若产生孔径不圆或偏大现象,可在一条主切削刃上作出标记,轻磨另一条主切削刃,再上钻床试钻,测量后孔径缩小,说明刃磨这条切削刃正确,修磨至合适为止。
若试钻后孔径继续增大,说明刃磨此主削刃导致两刃长度差异更大,应改磨另一条主切削刃直至合适。
也可在钻头切削状态下停车,观察两主切削刃前刀面处铁屑差异,以此来判断两刃切削情况和刃磨的准确性。
[精选]106提高加工精度工艺措
[精选]106提高加工精度工艺措施pptx汇报人:日期:•加工精度概述•刀具选择与调整•夹具设计与使用目录•切削参数优化•加工过程监控与调整•质量检验与控制•总结回顾与展望未来01加工精度概述指零件加工后的实际几何参数与理想几何参数的符合程度。
加工精度加工精度是保证产品质量、提高生产效率、降低生产成本的关键因素。
重要性定义与重要性影响加工精度的因素机床的几何误差、热误差等都会影响加工精度。
工件装夹不牢固、定位不准确等会导致加工误差。
刀具磨损、制造误差等会影响加工精度。
测量设备、测量方法等都会影响测量精度,进而影响加工精度。
机床误差工件装夹误差刀具误差测量误差优化机床采用高精度机床,提高机床的几何精度和热稳定性。
精确装夹采用高精度的夹具和定位方法,确保工件装夹牢固、定位准确。
选用合适刀具根据加工要求选用合适材质、精度的刀具,并定期检查刀具磨损情况。
精确测量采用高精度的测量设备和测量方法,提高测量精度,进而提高加工精度。
工艺控制通过合理的工艺安排和控制,减少加工过程中的误差传递和积累。
人员培训加强操作人员的技术培训,提高操作技能和责任心,确保加工过程的稳定性和精度。
提高加工精度的方法与措施02刀具选择与调整切削刀具磨削刀具孔加工刀具齿轮加工刀具刀具类型与特点01020304常用的车刀、铣刀、钻头等,用于切除材料。
砂轮等,用于磨削加工。
钻头、铰刀等,用于加工孔。
滚刀、插齿刀等,用于加工齿轮。
后刀面磨损、前刀面磨损、切削刃崩刃等。
根据刀具磨损情况及时更换,避免因刀具磨损导致加工精度下降。
刀具磨损与寿命管理刀具寿命管理刀具磨损形式根据加工要求调整刀具角度、长度等参数,确保加工精度。
刀具调整采用软件补偿或硬件补偿方式,对刀具磨损进行补偿,提高加工精度。
补偿方法刀具调整与补偿方法03夹具设计与使用适用于不同工件的夹具,如三爪卡盘、四爪卡盘等。
通用夹具专用夹具可调夹具针对特定工件设计的夹具,具有结构简单、操作方便、夹紧力大等特点。
探讨提高钳工钻孔精度
探讨提高钳工钻孔精度摘要:在日常生产、维护中,经常需要使用普通台式钻床加工孔,在单件生产、技能评估或竞争中,也有高精度间隙和孔间隙,但为了确保钻孔位置的准确性,很难使用绘图和对齐等基本操作获得技能表现的基本点。
尽管许多同行已经达到了合格的高级运营官或更高级别,但孔的精度只能靠运气来实现,他们无法准确理解满足精度要求的孔,这直接影响了加工产品的质量。
有许多关于车加工细长轴的文章,但很少有提高安装人员钻孔精度的经验。
关键词:钳工;钻孔精度;技能一、钳工钻孔精度不高的影响因素安装人员钻孔定位精度低的原因是绘制线的精度、钻头定位和加工过程中的压力。
第一,工件的形状精度不高,因此很难精确测量、计算和查找。
第二,高度游标的精度不够,导致绘制的线条出现偏差,绘制线条后无法进行精确控制。
第三,画的线条太粗,造成了孔中心的偏移。
第四,在校正和冲孔时,钻具的位置不精确,不易维修。
第五种是由于工件的夹持力不够或者没有牢固地保持,导致工件在钻孔时运动,造成了孔的变形。
第六,钻头没有磨好,在钻进时,定心不好,造成孔径增大或产生弹性变形;如果钻头是弯的,那么钻心就会从定位中心偏移。
第七、机床的精确度低、主轴间隙大、主轴与机床不相垂直;这样就不能在钻孔中精确地发现并增大孔径。
第八,在钻进时,由于进给压力过大,造成了张拉钻工作面的弹性变形等原因,造成了孔的位移。
第九,在铰孔时,铰刀的精确度不高或力不稳,使孔径增大。
第十,因累积错误,导致精确度超过容差。
二、提高钻孔精度的方法1、把握好手工刃磨钻头钻头是钻孔的保证。
要钻一个精确的孔,请选择一个合理的钻头直径,并用砂轮机将钻头磨好角度。
钻孔技能基于熟悉钻头的几何尺寸和获得钻头手动研磨方法。
在磨削钻头之前,必须正确理解和评估钻头的不同几何参数,并选择相应的钻头进行磨削。
为了保证顶角、背角和交叉斜角的精确性,两个主要刀片的长度与钻头的中心线相等,并且两个主要切割表面都是平滑的,这样有利于对心和减小孔壁的粗糙度;十字形刀片和主要刀片要经过合适的磨光(最好是在磨光机上,再用油石粉)。
- 1、下载文档前请自行甄别文档内容的完整性,平台不提供额外的编辑、内容补充、找答案等附加服务。
- 2、"仅部分预览"的文档,不可在线预览部分如存在完整性等问题,可反馈申请退款(可完整预览的文档不适用该条件!)。
- 3、如文档侵犯您的权益,请联系客服反馈,我们会尽快为您处理(人工客服工作时间:9:00-18:30)。
提高孔加工的精度的方法文稿归稿存档编号:[KKUY-KKIO69-OTM243-OLUI129-G00I-FDQS58-提高孔加工的精度的方法对于钳工专业而言,钻孔是其中最重要的加工操作,它是一种确定孔系和孔位置准确度的方式。
钻削加工时,操作者可以利用理论联系实际的方法分析出孔的中心位置、确定钻床主轴线和被加工工件表面的垂直度以及做好麻花钻刃磨的质量提升工作,从而达到不断提升钻孔工艺以及提高钳工操作能力的目的,希望本文能够使更多的人掌握钳工孔加工精度的方法在钳工专业的基本实习训练中,孔加工是相对比较难掌握的基本操作之一。
在孔加工实习训练中反映问题最多的是单孔的直径控制和多孔的孔距精度控制,特别是对孔距的精度控制最为突出。
在实践中,如果是成批量的生产加工,可以通过制做工卡具来实现对孔距的控制,这样不仅能满足产品的技术要求,还能极大地提高工作效率。
但在小批量的生产加工中,对孔和孔距的形状和位置精度控制,则要通过划线、找正等方法来予以保证。
一、钳工孔加工实习课题训练中容易出现的问题:1、钻孔时孔径超出尺寸要求,一般是孔径过大;2、孔的表面粗糙度超出规定的技术要求;3、孔的垂直度超出位置公差要求;4、孔距(包括边心距和孔距)超出尺寸公差的要求;二、孔加工中出现问题的主要原因分析:1、钻头刃磨时两个主切削刃不对称,在钻削过程中,使钻头的径向受力;2、对钻削的切削速度选择不当;3、钻削时工件未与钻头保持垂直;4、未对孔距尺寸公差进行跟踪控制;三、提高孔加工精度的方法:在孔加工的课题训练中,对于前三个问题,需要加强练习。
比如主切削刃的不对称问题,在刃磨时,要对砂轮面进行检查,如果砂轮的磨削面不平整,应及时进行修整,刃磨的角度应保持一致。
对于不同的孔径,要选择相应的切削速度。
在钻孔过程中,自始至终都要避免钻头的径向受力。
钻孔时,不仅要保证平口钳的上平面与钻头的垂直,也要保证夹持工件时夹持面与加工表面的垂直。
夹持要牢固,避免在钻孔过程中,由于夹持不牢使工件发生滑陷。
这些都需要在实习的过程中让学生慢慢体会和认真掌握的。
最容易出现也是最难掌握的问题是孔距精度的控制问题,在这里作一下重点阐述。
传统的孔的位置精度的检查是靠划出“检查圆”和“检查框”的方法。
“检查圆”它是在钻孔划线完毕后,用划规以样冲眼为中心,划出比需要加工孔的直径大的“检查圆”,作为钻孔时检查位置是否准确的参照基准。
由于划规在旋转中其确定圆心的脚尖与样冲眼的接触中会产生滑动,使划规划的“检查圆”容易产生误差。
“检查框”是利用高度游标卡尺在孔的十字中心线上划出等距的方格,是在钻孔的初期样冲眼灭失时,用来替代样冲眼检查孔位置是否正确的依据,“检查框”确定的找正基准可以保证钻孔的中心与样冲眼定位的中心重合,保证划线精度,也避免了划“检查圆”的误差。
这两种保证孔位置精度的做法在教学中很难被学生掌握。
在多年的钳工实习教学实践中,对于孔距的控制我采用的是“跟踪控制法”。
所谓“跟踪控制”,就是从划线开始,到加工结束,每一道加工工序都要通过认真的检查来保证孔距的精度要求在加工者的控制之中。
做到前道加工工序是后一道加工工序的精度控制前提,后一道加工序是前一道加工工序的精度控制保证。
一环扣一环,从而实现对孔距精度的控制。
首先是划线,划线是孔加工的第一道工序,划线的质量是确保孔加工孔距精度的重要前提。
俗话说“工欲善其事,必先利其器”。
在孔加工确定孔中心位置的划线中,一般是采用高度游标卡尺,要划线前一是要检查高度尺的示值误差是否在规定的精度误差范围内,以保证所划线条的尺寸准确,检查高度游标卡尺的划线刃口是否锋利,以确保所划线条清晰均匀;二是要检查划线平板的精度,确保划线平板工作表面清洁、无毛刺,以免影响划线精度。
调整好尺寸后,可以在工件上轻轻划出一道可见的痕迹,然后用游标卡尺测量一下这个痕迹,看是否有误差。
如果有误差,就要相应调整高度游标卡尺,直到痕迹符合精度要求。
接下来就可以按照图纸要求划出清晰均匀的孔的中心线了。
其次是打出准确的样冲眼,样冲眼的作用是为钻头定心。
样冲必须磨得圆而尖并保持足够的硬度,根据多年的教学经验,样冲的顶角为40-50度最为适宜。
在打样冲眼时,要使样冲与工件垂直,轻轻敲击出痕迹,然后观察所敲击的样冲眼是否位于孔的十字中心线的正中。
检查符合要求后,再加大敲击力度,使将样冲眼加大,这时应该注意,样冲眼不宜过大,否则容易出现视觉上的误差,以能达到引孔时准确地定心的目的即可。
第三是用2mm钻头在样冲眼上引出定位孔,这是验证上道工序是否符合要求的关键。
具体做法是:用2mm钻头在打出的样冲眼上引出孔径,操作时要保证钻头与工件的垂直,转速调整到1200转左右,转速越高,定心越稳。
控制好力度,认真观察,让钻头的顶角部分刚刚进入工件,能看到2mm钻头在工件上显出直径即起钻,如果钻的过深在有误差的时候就会加大下一步的修正难度。
由于钻头的结构决定了横刃的存在,横刃的长度越长,其定位的稳定性就越差,如果直接用标定尺寸的钻头直接钻出浅窝,就容易造成定位不准而发生偏移。
使用2mm的钻头,其横刃长度相对于样冲眼的直径来说几乎可以忽略不计,其定心作用非常稳定,基本可以做到与样冲眼在位置上的重合。
而只引出2mm钻头直径的目的一是为了进一步测量,二是为标定钻头的加工定心。
第四是用卡尺测量定位孔的边心距和孔心距。
其方法是用卡尺的外测量爪来测量孔壁与基准面的距离,测量的长度加上孔的半径就是边心距。
如果是测量孔距,则分别用游标卡尺的内外测量爪来测量出两个定位孔的最大边距和最小边距的精确尺寸,然后用最大边距和最小边距之和除以2,就可以得到所测两孔的真实孔心距了。
一般情况下,只要严格按照这样的操作程序,一般都能够保证孔的加工精度。
通过测量,如果定位孔的边心距或孔心距超出尺寸公差的要求范围,这个时候就要确定其偏差方向和偏差量,再用3mm 的钻头进行修正。
具体方法是,调整好钻床的转速,处于是校正的目的,所以钻床转速不易过快,以每分种600转左右为宜。
要特别注意进给量,钻头要慢慢靠近工件2mm的浅孔,就要接触到浅孔时,根据偏差量,将工件向偏移的相反方向慢慢推移,有切削出现时停止进给并保持工件稳定,靠钻头顶部发生的径向位移所产生的弹性来切削工件消除偏移量,此时要注意观察,当锪出能看到3mm钻头的直径时,迅速起钻。
这个步骤有一定难度,只要多练习,就能够熟练掌握。
第五是在确定孔的位置符合要求后,再加深定位孔的深度。
深度以稍大于标定尺寸钻头切削部分轴向长度即可。
这样用标定的钻头钻削的时候,可以消除横刃对定心的影响。
当钻孔的深度达到钻头切削部分轴向长度的时候,钻头的顶角就可以起到稳定的定心作用了。
第六是根据标定钻头直径调整好转速,通过定位孔直接进行孔的加工,一个符合尺寸和位置要求的孔和孔系就加工完成了。
一、在机械加工中,有时会面对一些位置精度及同轴度要求极高的零件。
如图1、2、3,这类零件的加工精度受机床自身精度、装夹定位误差、被加工材料及加工刀具等多种因素的影响而难以满足设计要求。
一般来讲,位置精度要求小于φ0.03,同轴度要求小于φ0.03的零件,均属于形位精度要求极高的零件。
在加工时若不能及时排除上述各种因素的影响,加工质量则无法保证。
图1图2图3二、高精度位置孔的加工方法1、影响高精度位置孔加工的因素材料的性能及内部应力的消除情况,基准面的加工精度,如圆度、粗糙度、圆柱度,数控机床的定位精度和重复定位精度,主轴的刚性及旋转圆度,刀具的锋利程度、工件材料刚性、机床几何精度、零件装夹方法、切削速度、润滑冷却方式等有关。
2、具备有大型三坐标机测量方法的厂家,采用如下方法,如图4。
图4例如某个公司,采用如图将零件装夹在龙门五面加工中心上面,工件找正方法是采用将千分表把2个φ196孔打正,将千分表从4处φ196孔穿进去,以相同直径大小打表检测基准φ660h7的4处外圆弧面,X、Y方向分中设定程序坐标原点。
首先将φ195孔加工到φ194h6,送三坐标机检测,数据如下:位置度为0.0022、0.0556、0.0223、0.0556;半径为434.9403、434.9788、435.0190、434.9656;弦长为615.1653、615.1444、615.1656、615.1363。
分析半径和弦长与理论值偏小,将加工程序多加大0.01,第二次将φ196孔加工到φ195h6,送三坐标机检测,数据如下:位置度为0.0647、0.0564、0.0917、0.0859;半径为434.9677、435.0045、434.9671、434.9760;弦长为615.1682、615.1435、615.1599、615.1400。
分析半径和弦长与理论值还是偏小,将加工程序再多加大0.01,第三次φ196孔精加工到位,送三坐标机检测,数据如下:位置度为0.0264、0.0458、0.0436、0.0305;半径为434.9868、435.0028、435.0172、435.0229;弦长为615.208、615.2、615.1912、615.2060。
通过三次加工,基本达到零件设计要求。
这个例子说明加工中心不是万能的,要达到这么高的精度,需要反复试切,逐步逼近达到高精度要求。
3、对于没有大型三坐标机测量方法的,采用如图5方法。
图5按照下面计算公式,计算半径和弦长:22222121)2()2()2()2(d D d D r R -+-+=;24252324)2()2()2()2(d D d D s L -+-+= 通过测量和分析计算半径和弦长与理论值的偏差,加工中心或者数显镗床显示的孔中心数显的坐标值,调整程序,将这些“游离”的位置点“拽”到正确的位置,保证位置度要求。
如图6。
图6没有大型三坐标测量机的厂家,采用数显镗床加工,半精加工后测量一次,用内分厘尺测量各个孔大小,外分厘尺测量半径、弦长数据。
将行星孔中心与基准孔中心数显的坐标值、孔大小、半径、弦长所有数据进行分析,然后调借位置尺寸。
最后精镗孔到位。
将孔大小尺寸、半径、弦长数据、行星孔中心与基准孔中心数显的坐标值,由技术人员通过软件图形分析位置度,形成书面资料,不断地与客户三坐标机测量的数据进行验证,进行对比测量。
形成有规律性的数据联系。
图74、对于图7零件,采用进口的高精度德国DMG加工中心,购买高性能HSK 63-A刀柄,高刚性刀杆,微调镗刀头,锋利的刀片,加大改进零件铸造外形,设计适宜的夹具,将基准孔φ110H7与5个φ8H8位置孔、φ78H7一次装夹同时加工出来,保证了位置度要求φ0.02,同轴度0.01。
这种方法优点是彻底排除了基准孔的找正误差,零件的加工精度主要受设备自身精度的影响。
三、高同轴度孔的加工方法1、影响高同轴度孔加工的因素基准面的加工精度,数控机床的定位精度和重复定位精度,主轴的刚性及旋转圆度,刀柄的动平衡、镗刀杆的刚性、长刀杆的挠度,刀具的锋利程度、工件的材料性质、机床加工条件、零件装夹的夹具精度、切削速度、润滑冷却方式、精加工前的夹紧力大小等。