第讲零件加工精度获得方法
精密微小零件加工方法

精密微小零件加工方法1.切割加工切割加工是一种常用的精密微小零件加工方法。
它包括线切割、放电加工和激光切割等。
这些方法都能够实现高精度的零件切割,特别适用于适应性强、材料硬度高的零件加工。
线切割是一种通过金属丝进行切割的方法,广泛应用于塑料、金属、合金和陶瓷材料的微小零件加工。
线切割具有高精度、小损耗和表面质量好的特点。
放电加工是一种通过放电腐蚀加工的方法,适用于加工深孔和复杂形状的微小零件。
放电加工具有高加工精度、良好的表面质量和适应性强的特点。
激光切割是一种使用激光束进行切割的方法,具有高精度、无接触切削和适应性强的特点。
激光切割适用于加工脆性材料和高硬度材料的微小零件。
2.铣削加工铣削加工是一种通过旋转刀具切削材料的方法,适用于加工平面、曲线和复杂零件。
常见的铣削加工方法包括立铣、平面铣和数控铣削等。
立铣是一种通过立式铣床进行加工的方法,适用于加工平面和简单形状的微小零件。
立铣具有切削力大和加工效率高的特点。
平面铣是一种通过平面铣床进行加工的方法,适用于加工平面、曲线和复杂形状的微小零件。
平面铣具有加工范围广和加工精度高的特点。
数控铣削是一种通过数控机床进行加工的方法,适用于高精度和高自动化要求的微小零件加工。
数控铣削具有高精度、高效率和稳定性好的特点。
3.研磨和抛光加工研磨和抛光加工是一种通过磨料对零件进行加工的方法,可用于去除表面不平整、加工粗糙度和提高表面光洁度。
常见的研磨和抛光加工方法包括机械研磨、化学抛光和电化学抛光等。
机械研磨是一种通过磨料进行加工的方法,适用于加工硬度高和精度要求高的微小零件。
机械研磨具有加工效率高和表面光洁度好的特点。
化学抛光是一种通过化学溶液进行加工的方法,适用于去除表面氧化和锈蚀的微小零件。
化学抛光具有加工速度快和加工控制简单的特点。
电化学抛光是一种通过电化学反应进行加工的方法,适用于加工高硬度和高耐腐蚀性材料的微小零件。
电化学抛光具有加工精度高和表面质量好的特点。
机械零件加工精度统计分析方法探略

增加。 若Cp 值为 1 或小于 1, 工序 加工能力较弱, 表明 产品的次品率
就可能上升, 这时必须采取相应措施, 来改善工艺过程。 利用分布曲线 可以比较方便的研究加工精度, 可以分辨出工序的随机误差的大小以 及是否存在着系统误差, 但不能把规律性变化的系统误差从随即误差 中区分出来。采取分布曲线法控制加工精度时, 必须检查所有加工的 零件, 只有将一批零件加工完毕后方能绘制出分布曲线图。 3. 确定加工误差的类型 在己调整好的机床上加工一批工件,由各种工艺因素所产生的 加工误差, 可分为两大类, 即系统误差和随机误差。 系统误差包括因调 整等因素引起的常值系统误差和因刀具磨损 、机床热变形等引起 的 有规律变化趋势的变值系统误差。随机误差则是由尺寸分散造成的。 二、 机械零件加工精度统计分析的基本方法 1、 分布曲线法。目 前进行加工精度统计分析的方法之一是分布 曲线法。 在机械加工中, 用调整法加工一批零件, 其尺寸误差是有很多 相互独立的随机误差综合作用的结果, 如果其中没有一个是起决定作 用的随机误差, 则加工后零件的尺寸将近似于正态分布。理论正态分 它的方程式如下;
科技前沿
析工艺过程的稳定性、 查明工序的精度以及确定机床的调整精度、 确保产品的加工质量具有非常重要的
作用。
〔 要l 加 精 的 计 析 机 制 技术 的 个 常 要的 作, 精 计 析 分 摘 工 度 统 分 是 械 造 中 一 非 重 工 加工 度统 分 对于
〔 关键词」 械 工 精 统 分 方 机 加 度 计 析 法
它不是平滑曲线而是折线。 实验分布曲线是根据一批零件的加工尺
寸绘制出来的。通常 一批零件数量在 50 件以上, 越多则越能反映出 它的分布规律, 是分析数据常用的一种方法。
工件获得尺寸精度的方法
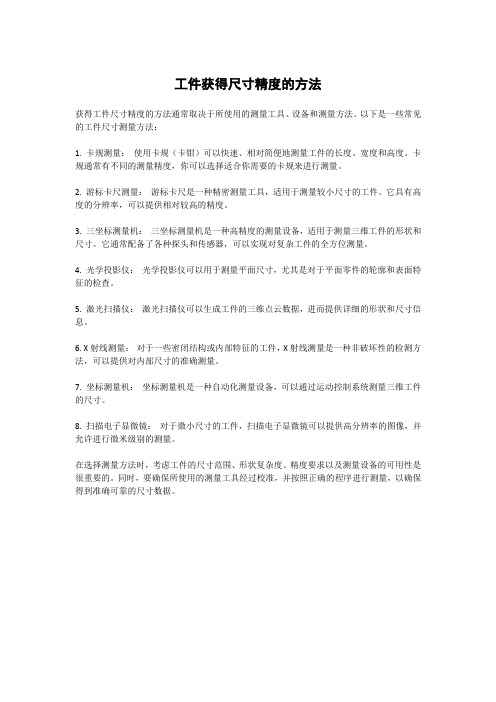
工件获得尺寸精度的方法
获得工件尺寸精度的方法通常取决于所使用的测量工具、设备和测量方法。
以下是一些常见的工件尺寸测量方法:
1. 卡规测量:使用卡规(卡钳)可以快速、相对简便地测量工件的长度、宽度和高度。
卡规通常有不同的测量精度,你可以选择适合你需要的卡规来进行测量。
2. 游标卡尺测量:游标卡尺是一种精密测量工具,适用于测量较小尺寸的工件。
它具有高度的分辨率,可以提供相对较高的精度。
3. 三坐标测量机:三坐标测量机是一种高精度的测量设备,适用于测量三维工件的形状和尺寸。
它通常配备了各种探头和传感器,可以实现对复杂工件的全方位测量。
4. 光学投影仪:光学投影仪可以用于测量平面尺寸,尤其是对于平面零件的轮廓和表面特征的检查。
5. 激光扫描仪:激光扫描仪可以生成工件的三维点云数据,进而提供详细的形状和尺寸信息。
6. X射线测量:对于一些密闭结构或内部特征的工件,X射线测量是一种非破坏性的检测方法,可以提供对内部尺寸的准确测量。
7. 坐标测量机:坐标测量机是一种自动化测量设备,可以通过运动控制系统测量三维工件的尺寸。
8. 扫描电子显微镜:对于微小尺寸的工件,扫描电子显微镜可以提供高分辨率的图像,并允许进行微米级别的测量。
在选择测量方法时,考虑工件的尺寸范围、形状复杂度、精度要求以及测量设备的可用性是很重要的。
同时,要确保所使用的测量工具经过校准,并按照正确的程序进行测量,以确保得到准确可靠的尺寸数据。
加工精度
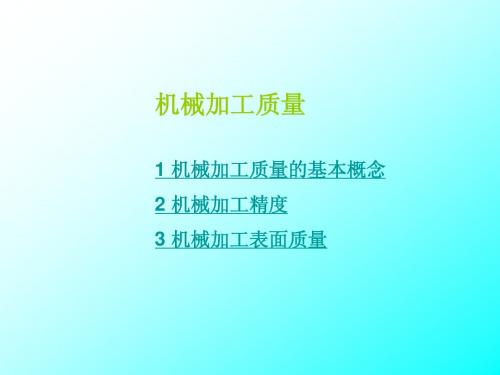
返回本章目录
工件回转(车削)的情况: ①工件回转在1处: R1 = R - A ②工件回转在2处: R2 = R ③工件回转在3处: R3 = R + A ④工件回转在4处: R4 = R D1-3= R1+R2=2R D2-4= 2R = D1-3
返回本章目录
工件孔轴心线
α
主轴回转轴心线
主要影响工件的形状精度
垂直误差
两者比较
R y 400Rz
结论:普通机床导轨水平误差比垂直误差对加 工误差影响大得多。(此例两者相差400倍)
返回本章目录
误差敏感方向— 对加工误差影响大的加工表面的法线方向。 平面磨床误差敏感方向为
导轨垂直误差。
返回本章目录
2)主轴误差
主轴回转误差
—主轴实际回转中心的瞬时位置 与理想位置的最大偏差。 一般把主轴误差分解为三种独立运动形式: ①纯轴向窜动△x ②纯径向移动△r ③纯角度摆动△α
机械加工质量
1 机械加工质量的基本概念 2 机械加工精度 3 机械加工表面质量
机械加工质量
1 机械加工质量的基本概念
机器零件的加工质量决定了机器的: 1.性能 2.质量 3.寿命 机器产品加工质量的内容: 1.加工精度 2.加工表面质量
返回本章目录
机器产品加工质量要求越来越高(近30年) 加工精度 (普通)从0.01mm →0.005mm (精密)从1μm → 0.02μm (超精密)从0.1μm →0.001μm 加工表面质量粗糙度方面已获得小于 0.0005μ m的粗糙度。 加工质量与设备、工艺方法、工艺措施有关。
返回本章目录
(4)工艺系统受力变形 工艺系统在加工过程中受: ①切削力; ②惯性力; ③重力; ④夹紧力 力作用→产生工艺系统变形→加工误差
机械零件加工精度测量技术及相关问题阐述
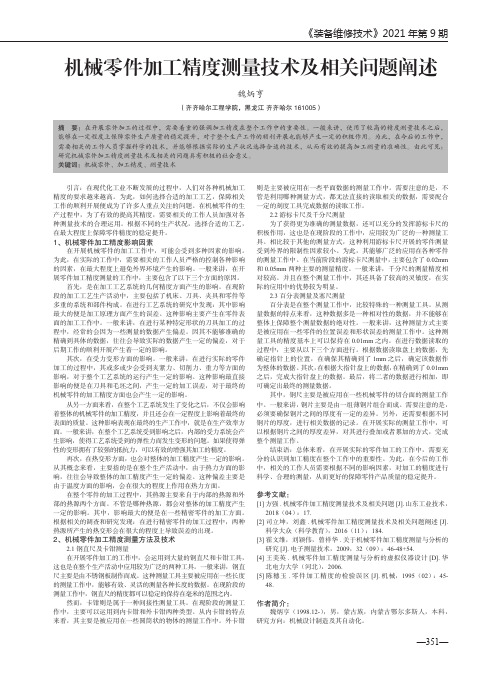
《装备维修技术》2021年第9期机械零件加工精度测量技术及相关问题阐述魏炳亨(齐齐哈尔工程学院,黑龙江 齐齐哈尔 161005)摘 要:在开展零件加工的过程中,需要着重的强调加工精度在整个工作中的重要性。
一般来讲,使用了较高的精度测量技术之后,能够在一定程度上保障零件生产质量的稳定提升,对于整个生产工作的顺利开展也能够产生一定的积极作用。
为此,在今后的工作中,需要相关的工作人员掌握科学的技术,并能够根据实际的生产状况选择合适的技术,从而有效的提高加工测量的准确性。
由此可见:研究机械零件加工精度测量技术及相关的问题具有积极的社会意义。
关键词:机械零件、加工精度、测量技术引言:在现代化工业不断发展的过程中,人们对各种机械加工精度的要求越来越高。
为此,如何选择合适的加工工艺,保障相关工作的顺利开展便成为了许多人重点关注的问题。
在机械零件的生产过程中,为了有效的提高其精度,需要相关的工作人员加强对各种测量技术的合理运用。
根据不同的生产状况,选择合适的工艺,在最大程度上保障零件精度的稳定提升。
1、机械零件加工精度影响因素 在开展机械零件的加工工作中,可能会受到多种因素的影响。
为此,在实际的工作中,需要相关的工作人员严格的控制各种影响的因素,在最大程度上避免外界环境产生的影响。
一般来讲,在开展零件加工精度测量的工作中,主要包含了以下三个方面的原因。
首先,是在加工工艺系统的几何精度方面产生的影响。
在现阶段的加工工艺生产活动中,主要包括了机床、刀具、夹具和零件等多重的系统和部件构成。
在进行工艺系统的研究中发现:其中影响最大的便是加工原理方面产生的误差。
这种影响主要产生在零件表面的加工工作中。
一般来讲,在进行某种特定形状的刀具加工的过程中,经常的会因为一些测量的数据产生偏差。
因其不能够准确的精确到具体的数据,往往会导致实际的数据产生一定的偏差,对于后期工作的顺利开展产生着一定的影响。
其次,在受力变形方面的影响。
一般来讲,在进行实际的零件加工的过程中,其或多或少会受到夹紧力、切削力、重力等方面的影响,对于整个工艺系统的运行产生一定的影响。
机械制造工艺与机床夹具 第2版 教学课件 吴年美 吴拓 第二章 机械加工精度
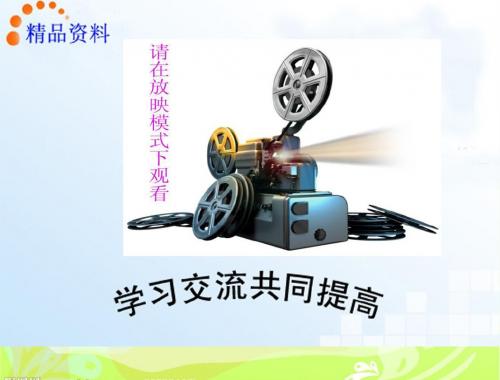
而且毛坯结构越复杂、壁厚越不均,散热的条件差别越大,毛坯内
部产生的残余应力也越大。
第二节 影响加工精度的因素及其分析
(2)冷校直带来的残余应力 直工艺进行校直。 某些刚度低的零件,如细长轴、曲轴和
丝杠等,由于机加工产生弯曲变形不能满足精度要求,常采用冷校
第二节 影响加工精度的因素及其分析
图2-12 冷校直引起的残余应力 a)冷校直方法 b)加载时残余应力的分布 c)卸载后残余应力的分布
教材其余课件及动画素材请查阅在线教务辅导网 在线教务辅导网:
QQ:349134187 或者直接输入下面地址:
第二章
机械加工精度
第二章 机械加工精度 第一节 概 述
第二节 影响加工精度的因素及其分析 第三节 加工误差的综合分析 第四节 保证和提高加工精度的主要途径
证工件位置精度的安装方法。
第二节 影响加工精度的因素及其分析
图2-1 原始误差
一、加工原理误差
第二节 影响加工精度的因素及其分析
加工原理误差是指采用了近似的成形运动或近似的切削刃轮廓进行 加工而产生的误差。 二、工艺系统的几何误差 1.机床几何误差 (1)机床主轴误差。 1)主轴回转误差。
图2-2 主轴回转轴线的运动误差
一、加工误差的性质 根据一批工件加工误差出现的规律,可将影响加工精度的误差因素 按其性质分为两类: (1)系统误差 (2)随机误差 在顺序加工的一批工件中,若加工误差的大小和方向 在顺序加工的一批工件中,其加工误差的大小和方向 都保持不变或按一定规律变化,这类误差统称为系统误差。 的变化是无规律的,称为随机误差,例如,毛坯误差的复映、残余 应力引起的变形误差和定位、夹紧误差等都属于随机误差。 二、加工误差的数理统计方法
机械加工质量
(4)调整误差 机械加工过程中的每一道工序都要进行各种各样 的调整工作,由于调整不可能绝对准确,因此必 然会产生误差,这些误差称为调整误差。
2、工艺系统的受力变形 (1)工艺系统的刚度 机械加工过程中,工艺系统在切削力、传动力、惯
性力、夹紧力、重力等外力的作用下,各环节将 产生相应的变形,使刀具和工件间已调整好的正 确位置关系遭到破坏而造成加工误差。例如,在 车床上车削细长轴时,工件在切削力的作用下会 发生变形,使加工出的工件出现两头细中间粗的 腰鼓形
第七章 机械加工质量
尺寸精度
机械加工精度
形状精度
加 工 质 量
表面质量
位置精度 表面粗糙度
表面层的物理、力学性能
第一节 概述 一、机械加工精度 1、机械加工精度的概念
所谓机械加工精度,是指零件在加工后的几何 参数(尺寸大小、几何形状、表面间的相互位 置)的实际值与理论值相符合的程度。符合程 度高,加工精度也高;反之则加工精度低。机 械加工精度包括尺寸精度、形状精度、位置精 度三项内容,三者有联系,也有区别。
3)定尺寸刀具法 用具有一定形状和尺寸精度的刀 具进行加工,使加工表面达到要求的形状和尺寸的 加工方法。如用钻头、铰刀、键槽铣刀等刀具的加 工即为定尺寸刀具法。定尺寸刀具法生产率较高, 加工精度较稳定,广泛的应用于各种生产类型。 4)自动控制法 把测量装置、进给装置和控制机构 组成一个自动加工系统,使加工过程中的尺寸测量、 刀具的补偿和切削加工一系列工作自动完成,从而 自动获得所要求的尺寸精度的加工方法。该方法生 产率高,加工精度稳定,劳动强度低,适应于批量 生产。
原始误差主要来自两方面:一方面是在加工前就存 在的工艺系统本身的误差(几何误差),包括加 工原理误差,机床、夹具、刀具的制造误差,工 件的安装误差,工艺系统的调整误差等;另一方 面是加工过程中工艺系统的受力变形、受热变形、 工件残余应力引起的变形和刀具的磨损等引起的 误差,以及加工后因内应力引起的变形和测量引 起的误差等。
机械加工精度
机械加工精度
1. 获得尺寸精度的方法
(1) (2) (3) (4) 试切法 调整法 定尺寸法 自动控制法
机械加工精度
2. 获得形状精度的方法 (1)轨迹法 (2)成形法 (3)展成法 3. 获得位置精度的方法 (1)根据工件加工过的表面进行找正的 方法; (2)工件的位置精度由夹具来保证。
机械加工精度
机械加工表面质量
四、 影响表面层物理机械性能的因素 1.影响表面层冷作硬化的因素
(1)切削用量 ①切削速度: 随着切削速度的增大,被加工金属塑性变形减小,同时由于 切削温度上升使回复作用加强,因此冷硬程度下降。 ②进给量: 进给量增大使切削厚度增大,切削力增大,工件表面层金属的 塑性变化增大,故冷硬程度增加。 (2)刀具 ①刀具刃口圆弧半径 增大,表面层金属的塑性变形加剧,冷硬程度增大。 ②刀具后刀面磨损宽度VB 增大,刀具后刀面与工作表面摩擦加剧,塑性变 形增大,导致表面层冷硬程度增大。 ③前角增大,可减小加工表面的变形,故冷硬程度减小。刀具后角、主偏角、 副偏角及刀尖圆角半径等对表面层冷硬程度影响不大。 (3)工件材料 工件材料的塑性越大,加工表面层的冷硬程度越严重,碳钢中含碳量越高, 强度越高,其冷硬程度越小。
机械加工精度
4)刀具热变形及对加工精度的影响 (1)刀具连续工作时 (2)刀具间歇工作 ξ(μm)
ξmax
连续切削升温曲线
间断切削升温曲线 冷却曲线
图中 ξ—— 热伸长量; ξmax —— 达到热平衡热伸长量; τ—— 切削时间; τc —— 时间常数(热伸长量为热平 衡热伸长量约63%的时间,常取3~4分钟 )。
机械加工表面质量
二、 表面质量对零件使用性能的影响 1.表面质量对零件耐磨性的影响
工件获得尺寸精度的方法 -回复
工件获得尺寸精度的方法-回复工件获得尺寸精度是制造业中非常重要的一项技术要求,它直接关系到制造品质的稳定性和产品的成本效益。
工件的尺寸精度决定了它是否能够准确地嵌入到其他零部件中,从而确保整个产品的功能正常运行,同时还对产品的外观质量、耐用度等方面产生重要的影响。
因此,精确的尺寸测量和控制是确保工件质量的重要步骤。
下面将一步一步回答如何获得工件的尺寸精度。
第一步:设计阶段的尺寸参数确定在产品设计阶段,首先需要明确工件的尺寸要求和公差范围。
公差是指工件尺寸在设计允许范围内的变化量,通过公差的控制,可以确保工件在生产过程中达到所需的尺寸精度要求。
第二步:材料选择与处理材料的选择和处理对工件尺寸精度有很大影响。
材料的强度、膨胀系数、塑性等特性会对工件的尺寸稳定性产生巨大影响。
因此,在选材时需要综合考虑这些因素,选择合适的材料,并通过热处理、冷却等工艺进行材料性能调控,以提高工件的尺寸精度。
第三步:加工工艺优化加工工艺是决定工件尺寸精度的关键因素之一。
在加工过程中,通过选用合适的机床设备和切削工具,合理设置加工参数,采用合适的加工工艺流程,可以有效提高工件的尺寸精度。
例如,采用切削速度、进给量、切深等参数的优化组合,可以减小切削力对工件尺寸的影响,提高加工精度。
第四步:测量与反馈在加工过程中,持续的测量和反馈是确保工件尺寸精度的关键步骤之一。
通过使用高精度的测量工具和设备,如千分尺、示波器等,对工件的尺寸进行实时监控和测量。
将测量结果与设计要求进行对比,及时发现工件尺寸的差异,并对加工过程进行调整和修正,以确保工件尺寸的精度满足要求。
第五步:质量控制与持续改进在加工过程中,质量控制和持续改进是确保工件尺寸精度的关键环节。
通过建立完善的质量管理体系,制定标准化的工艺操作规程和验收标准,加强工人技能培训和质量意识教育,不断强化质量控制和改进,以提高工件的尺寸精度。
综上所述,工件获得尺寸精度的方法主要包括设计阶段的尺寸参数确定、材料选择与处理、加工工艺优化、测量与反馈以及质量控制与持续改进。
机械零件加工测量尺寸的精度方法
• 自动控制法机械零件加工的质量稳定、生 产率高、加工柔性好、能适应多品种生产, 是目前机械制造的发展方向和计算机辅助 制造(CAM)的基础。
机械零件加中测量工件尺寸 精度的方法,主要有以下几种。
• (1)试切法 即先试切出很小部分加工表面,测量试切所得的尺寸,按照加 工要求适当调刀具切削刃相对工件的位置,再试切,再测量, 如此经过两三次试切和测量,当被加工尺寸达到要求后,再切 削整个待加工表面。 试切法通过“试切-测量-调整-再试切”,反复进行直到达 到要求的尺寸精度为止。例如,箱体孔系的试镗加工。试切法 达到的精度可能很高,它不需要复杂的装置,但这种方法费时 (需作多次调整、试切、测量、计算),效率低,依赖工人的 技术水平和计量器具的精度,质量不稳定,所以只用于单件小 批生产。 作为试切法的一种类型——配作,它是以已加工件为基准,加 工与其相配的另—工件,或将两个(或两个以上)工件组合在 一起进行机械零件加工的方法。配作中最终被加工尺寸达到的 要求是以与已加工件的配合要求为准的。
• (3)定尺寸法 用刀具的相应尺寸来保证工件被加工部位尺寸 的方法称为定尺寸法。它是利用标准尺寸的刀 具加工,加工面的尺寸由刀具尺寸决定。即用 具有一定的尺寸精度的刀具(如铰刀、扩孔钻、 钻头等)来保证工件被加工部位(如孔)的精 度。 定尺寸法操作方便,生产率较高,加工精度比 较稳定,几乎与工人的技术水平无关,生产率 较高,在各种类型的生产中广泛应用。例如钻 孔、铰孔等。
•
(5)自动控制法 这种方法是由测量装置、进给装置和控制系统等组成。它是把测量、进给装 置和控制系统组成一个自动加工系统,加工过程依靠系统自动完成。 尺寸测量、刀具补偿调整和切削加工以及机床停车等一系列工作自动完成, 自动达到所要求的尺寸精度。例如在数控机床上机械零件加工时,零件就是 通过程序的各种指令控制加工顺序和加工精度。自动控制的具体方法有两种: ①自动测量-即机床上有自动测量工件尺寸的装置,在工件达到要求的尺寸时, 测量装置即发出指令使机床自动退刀并停止工作。 ②数字控制-即机床中有控制刀架或工作台精确移动的伺服电动机、滚动丝杠 螺母副及整套数字控制装置,尺寸的获得(刀架的移动或工作台的移动)由 预先编制好的程序通过计算机数字控制装置自动控制。 初期的自动控制法是利用主动测量和机械或液压等控制系统完成的。目前已 广泛采用按加工要求预先编排的程序,由控制系统发出指令进行工作的程序 控制机床(简称程控机床)或由控制系统发出数字信息指令进行工作的数字 控制机床(简称数控机床),以及能适应加工过程中加工条件的变化,自动 调整加工用量,按规定条件实现加工过程最佳化的适应控制机床进行自动控 制加工。
- 1、下载文档前请自行甄别文档内容的完整性,平台不提供额外的编辑、内容补充、找答案等附加服务。
- 2、"仅部分预览"的文档,不可在线预览部分如存在完整性等问题,可反馈申请退款(可完整预览的文档不适用该条件!)。
- 3、如文档侵犯您的权益,请联系客服反馈,我们会尽快为您处理(人工客服工作时间:9:00-18:30)。
第5页
机械制造工程——
二.满足加工精度的方法
静调整法:样件法
在不切削的情况下,用对刀块或样件 来调整刀具的位置
镗床上,用对刀块来调整镗刀的位置,以 保证镗孔的直径尺寸; 铣床上,用对刀块来调整刀具的位置,保 证工件的高度尺寸; 车床上,用行程档块来调整尺寸,保证车 削的长度。
第6页
第13页
机械制造工程——
影响加工精度的因素
从机械加工的全过程来分析影响加工精度的
因素,包括机械加工采用的加工方法、工艺
系统(机床、夹具、刀具及工件组成的系统)
本身误差、切削过程可能产生的问题、工作 环境、零件检验等
第14页
机械制造工程——
影响加工精度的因素
影响加工精度的主要因素:
1. 原理误差
2. 工艺系统的制造精度和磨损
3. 工艺系统的受力变形 4. 工艺系统的受热变形 5. 工艺系统调整误差 6. 工件安装夹紧误差 7. 度量误差
第15页
机械制造工程——
1. 原理误差
由于采用了近似的加工运动或者近似的刀具廓轮而
产生的。
如车削模数螺纹,由于模数螺纹的导程t=πm,而π是一
个无限小数,用交换齿轮来得到导程值时,就引入了原 理误差 成形铣刀加工齿轮,齿形形状是近似的,存在原理误差
零件机械加工精度
精度概念和获得精度的方法
影响加工精度的因素 加工误差的分析与控制 工件的安装与夹具
第1页
机械制造工程——
一. 加工精度的概念
加工精度:零件经过加工后几何参数(尺寸、几何形状以及
相互位置等参数)的实际值与理想值的符合程度 加工误差:零件经过加工后的几何参数(尺寸、几何形状以 及相互位置等参数)的实际值与理想值的偏离程度
方法三:尺寸刀具法
尺寸刀具法大多利用定尺寸的孔加工刀具,如钻头、镗
刀块、拉刀及铰刀等来加工孔。
用成形刀具加工也属于尺寸刀具法
零件精度由刀具来保证,生产率高; 由于刀具磨损后尺寸就不能保证,因此成本较高,多用
于大批量生产中。
第8页
机械制造工程——
二.满足加工精度的方法
方法四:主动测量法
加工精度在数值上通过加工误差的大小来表示;精度和误差
是对同一问题的两种不同的说法:
精度越高,误差越小; 精度越低,误差越大。
第2页
机械制造工程——
加工精度的内容
零件的几何参数包括几何形状、尺寸和相互位置三个方面
加工精度包括: 尺寸精度:限制加工表面与其基准间尺寸误差不超过一定的范围; 几何形状精度:限制加工表面宏观几何形状误差,如圆度、圆柱
按是否与切削状态有关来分:静态误差和切削状态
误差
静态误差:工艺系统在不切削状态下所出现的误差,
如机床的几何精度和传动精度;
切削状态误差:工艺系统在切削状态下所出现的误
差,如机床在切削时的受力变形和受热变形等。
第12页
机械制造工程——
零件机械加工精度
精度概念和获得精度的方法
影响加工精度的因素 加工误差的分析与控制 工件的安装与夹具
在加工过程中,边加工边
测量加工尺寸,达到要求
时,就立即停止加工
精度高,质量稳定,生产 率高
数显主动测量值,数控切
削运动
第9页
机械制造工程——
三. 机械加工误差的分类
按是否被人们所掌握分:系统误差与随机误差
系统误差
加工过程中有一定规律、可用函数关系来表达的误差
常值系统误差 系统 误差
导轨是机床中确定主要部件相对位置的基准,也是运动的基
准,它的各项误差直接影响被加工工件的精度 机床导轨平直度与主轴轴线的平行度均影响加工表面的形状 和尺寸精度
第18页
机械制造工程——
若垂直面或水平面内,导轨不直则产生刀尖的位移量δz和
δy,从而引起工件的尺寸误差δR和δR’
第19页
机械制造工程——
定不变,即回转精度 主轴的回转精度和主轴组件的制造精度(包括加工精度和装 配精度)有关,而且还和受力后主轴的变形有关,并且在高 速时,还要解决主轴轴承的散热问题。
度、平面度、直线度
相互位置精度:限制加工表面与其基准间的相互位置误差,如平
行度、垂直度、同轴度、位. 满足加工精度的方法
方法一:试切法
工人在每一工步或走刀前进行对刀,然后切出一小段,
测量其尺寸是否合适,如不合适,调整刀具的位置,再
试切一小段,直到达到尺寸要求后才加工这一尺寸的全 部表面。
机械制造工程——
二.满足加工精度的方法
动调整法:尺寸调整法
按试切零件进行调整,直接测量试切零件的尺寸,可以
试切一件或一组零件(2-15件),所有试切零件合
格,即调整完毕,可以进行加工。
用于大批量生产
考虑了加工过程中的影响因素,精度比静调整法高。
第7页
机械制造工程——
二.满足加工精度的方法
如由于铰刀直径较大,加工的孔 直径也较大
变值系统误差
如刀具磨损以及热伸长所造成的 工件尺寸误差。
第10页 机械制造工程——
三. 机械加工误差的分类
随机误差
加工过程中规律性不强,表现为噪声误差性质,符合统
计规律
如由于工件材质不均、毛坯尺寸形状差异而引起的误差
第11页
机械制造工程——
三. 机械加工误差的分类
生产率低、对工人要求高
用于单件小批生产
第4页
机械制造工程——
二.满足加工精度的方法
方法二:调整法
先按规定尺寸调整好机床、夹具、刀具和工件的相对位 置及进给行程,从而保证在加工时自动获得尺寸。 调整法加工时,不再进行试切,生产率大大提高,但精 度低些,主要决定于机床、夹具的精度和调整误差 调整法可分为静调整法和动调整法两种
在垂直面内导轨的弯曲对加工精度的影响很小,可以忽略不
计;而在水平面内同样大小的导轨弯曲就不能忽视。
第20页
机械制造工程——
2.1 机床的制造精度和磨损(2)主轴误差
机床主轴是工件或刀具的位置基准和运动基准,它的误差直
接影响着工件的加工精度
对主轴的要求,就是在运转的情况下能保持轴心线的位置稳
第16页
机械制造工程——
2. 工艺系统的制造精度和磨损
工艺系统中机床、刀具、夹具本身的制造精度及磨损对工件
的加工精度有不同程度的影响。包括:
机床的制造精度和磨损
导轨误差 主轴误差
刀具的制造精度和尺寸磨损 夹具的制造精度和磨损
第17页
机械制造工程——
2.1 机床的制造精度和磨损(1)导轨误差