MEMS工艺-表面微机械加工技术
mems 工艺流程
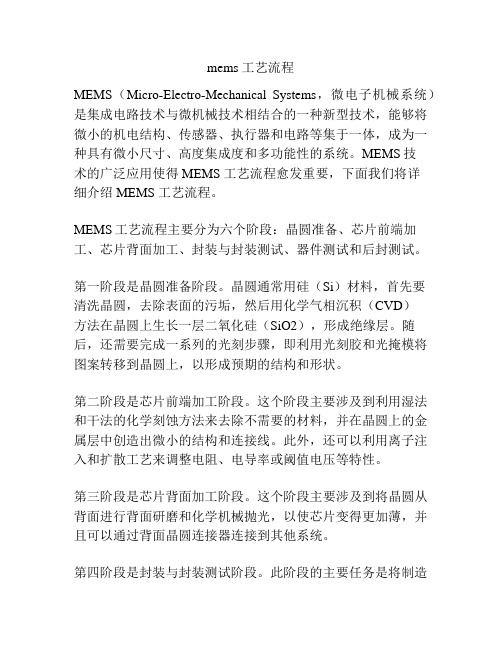
mems 工艺流程MEMS(Micro-Electro-Mechanical Systems,微电子机械系统)是集成电路技术与微机械技术相结合的一种新型技术,能够将微小的机电结构、传感器、执行器和电路等集于一体,成为一种具有微小尺寸、高度集成度和多功能性的系统。
MEMS技术的广泛应用使得 MEMS 工艺流程愈发重要,下面我们将详细介绍 MEMS 工艺流程。
MEMS工艺流程主要分为六个阶段:晶圆准备、芯片前端加工、芯片背面加工、封装与封装测试、器件测试和后封测试。
第一阶段是晶圆准备阶段。
晶圆通常用硅(Si)材料,首先要清洗晶圆,去除表面的污垢,然后用化学气相沉积(CVD)方法在晶圆上生长一层二氧化硅(SiO2),形成绝缘层。
随后,还需要完成一系列的光刻步骤,即利用光刻胶和光掩模将图案转移到晶圆上,以形成预期的结构和形状。
第二阶段是芯片前端加工阶段。
这个阶段主要涉及到利用湿法和干法的化学刻蚀方法来去除不需要的材料,并在晶圆上的金属层中创造出微小的结构和连接线。
此外,还可以利用离子注入和扩散工艺来调整电阻、电导率或阈值电压等特性。
第三阶段是芯片背面加工阶段。
这个阶段主要涉及到将晶圆从背面进行背面研磨和化学机械抛光,以使芯片变得更加薄,并且可以通过背面晶圆连接器连接到其他系统。
第四阶段是封装与封装测试阶段。
此阶段的主要任务是将制造好的 MEMS 芯片进行封装,以保护并提供使其正常运行所需的外部连接。
封装的方法包括胶封、承载式封装和芯片柔性封装。
随后,对封装后的芯片进行测试以确认其性能和质量。
第五阶段是器件测试阶段。
在这个阶段,将芯片插入到测试设备中,对其进行各种电学、力学或物理特性的测试。
测试可以包括压力测试、温度测试、震动测试等,以验证 MEMS 芯片的性能和可靠性。
最后一个阶段是后封测试阶段。
在这个阶段,将经过器件测试的芯片进行再次封装,以保护芯片不受外界环境的影响,并进行最后的测试以确保其正常运行。
mems 工艺
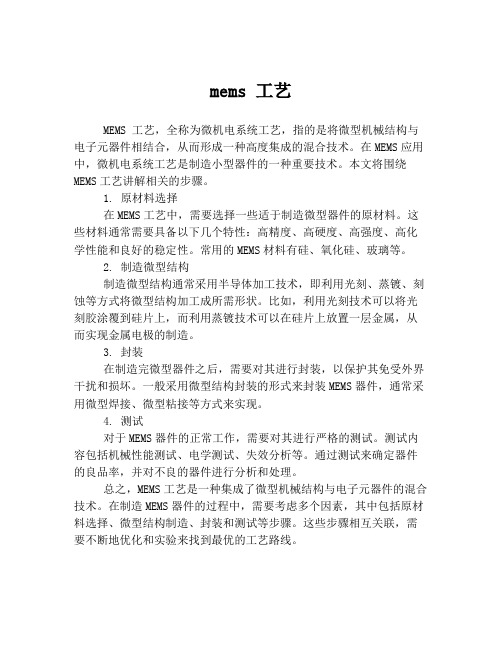
mems 工艺
MEMS 工艺,全称为微机电系统工艺,指的是将微型机械结构与电子元器件相结合,从而形成一种高度集成的混合技术。
在MEMS应用中,微机电系统工艺是制造小型器件的一种重要技术。
本文将围绕MEMS工艺讲解相关的步骤。
1. 原材料选择
在MEMS工艺中,需要选择一些适于制造微型器件的原材料。
这些材料通常需要具备以下几个特性:高精度、高硬度、高强度、高化学性能和良好的稳定性。
常用的MEMS材料有硅、氧化硅、玻璃等。
2. 制造微型结构
制造微型结构通常采用半导体加工技术,即利用光刻、蒸镀、刻蚀等方式将微型结构加工成所需形状。
比如,利用光刻技术可以将光刻胶涂覆到硅片上,而利用蒸镀技术可以在硅片上放置一层金属,从而实现金属电极的制造。
3. 封装
在制造完微型器件之后,需要对其进行封装,以保护其免受外界干扰和损坏。
一般采用微型结构封装的形式来封装MEMS器件,通常采用微型焊接、微型粘接等方式来实现。
4. 测试
对于MEMS器件的正常工作,需要对其进行严格的测试。
测试内容包括机械性能测试、电学测试、失效分析等。
通过测试来确定器件的良品率,并对不良的器件进行分析和处理。
总之,MEMS工艺是一种集成了微型机械结构与电子元器件的混合技术。
在制造MEMS器件的过程中,需要考虑多个因素,其中包括原材料选择、微型结构制造、封装和测试等步骤。
这些步骤相互关联,需要不断地优化和实验来找到最优的工艺路线。
mems工艺技术路线
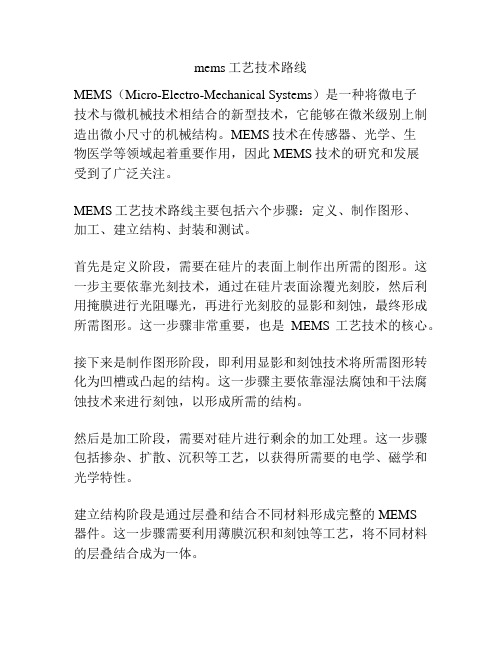
mems工艺技术路线MEMS(Micro-Electro-Mechanical Systems)是一种将微电子技术与微机械技术相结合的新型技术,它能够在微米级别上制造出微小尺寸的机械结构。
MEMS技术在传感器、光学、生物医学等领域起着重要作用,因此MEMS技术的研究和发展受到了广泛关注。
MEMS工艺技术路线主要包括六个步骤:定义、制作图形、加工、建立结构、封装和测试。
首先是定义阶段,需要在硅片的表面上制作出所需的图形。
这一步主要依靠光刻技术,通过在硅片表面涂覆光刻胶,然后利用掩膜进行光阻曝光,再进行光刻胶的显影和刻蚀,最终形成所需图形。
这一步骤非常重要,也是MEMS工艺技术的核心。
接下来是制作图形阶段,即利用显影和刻蚀技术将所需图形转化为凹槽或凸起的结构。
这一步骤主要依靠湿法腐蚀和干法腐蚀技术来进行刻蚀,以形成所需的结构。
然后是加工阶段,需要对硅片进行剩余的加工处理。
这一步骤包括掺杂、扩散、沉积等工艺,以获得所需要的电学、磁学和光学特性。
建立结构阶段是通过层叠和结合不同材料形成完整的MEMS器件。
这一步骤需要利用薄膜沉积和刻蚀等工艺,将不同材料的层叠结合成为一体。
封装是将MEMS器件封装到特定的封装中,保护器件并提供良好的电气和机械性能。
这一步骤主要包括背面研磨、切割、粘接等工艺。
最后是测试阶段,对制造好的MEMS器件进行各种测试。
这一步骤主要包括电学测试、机械测试、光学测试等,以确保器件的性能符合设计要求。
总的来说,MEMS工艺技术路线是一个复杂而精细的过程,需要运用各种微加工和微细结构制造技术。
这一技术路线的研究与发展为MEMS技术的进一步应用和推广提供了重要的支持。
同时,MEMS工艺技术路线也需要不断地进行改进和创新,以适应不断发展的科技需求。
MEMS的制造技术

4.1. 体微加工
硅的体微加工技术包含硅的湿法和干法技术,硅 刻蚀自终止技术、LIGA技术、以及DEM技术。
4.1.1. 湿法刻蚀技术 技术原理:硅表面点作为随机分布的局部区域的阳 极与阴极。由于这些局部区域化电解电池的作用,硅 表面发生了氧化反应并引起相当大的腐蚀电流,一般 超过100A/cm2。 硅表面的缺陷、腐蚀液的温度、腐蚀液所含的杂质、 腐蚀时扰动方式以及硅腐蚀液界面的吸附过程等因素 对刻蚀速度以及刻蚀结构的质量都有很大的影响。
图4.2表面取向对腐蚀速率的影响与温度的关系
图4.3 腐蚀速率与温度的关系(高HF区,无稀释) 自下而上每族曲线对应的配比为:95%HF+5% HNO3, 90%HF+10% HNO3,85%HF+1F+20% HNO3+15%H2O, 20%HF+60% HNH3+20%H2O
硝酸硅发生氧化反应生成二氧化硅,然后由HF将 二氧化硅溶解 Si+HNO3+HF=H2SiF6+HNO2+H2O+H2
水和乙酸(CH3COOH)通常作为稀释剂,在HNO3 溶液中,HNO3几乎全部电离,因此H+浓度较高, 而CH3COOH是弱酸,电离度较小,它的电离反应 为
CH3COOH=CH3COO-+H+
图4.5腐蚀速率与成分的关系
下图给出分别用H2O和CH3COOH作为稀释剂的HF+ HNO3,系统腐蚀 硅的等腐蚀线(常用的浓酸的重量百分比是49.2%HF和69.5% HNO3)。
H2O和CH3COOH作为稀释剂的功能相似,共同特 点: (1)在低HNO3及高HF浓度区(见图4.6的顶角区), 等腐蚀曲线平行于等HNO3浓度线,由于该区有过量 的HF可溶解反应产物SiO2,所以腐蚀速率受HNO3的 浓度所控制。 (2)在低HF高HNO3区(见图4.6的右下角),等腐 蚀线平行于HF浓度线。 (3)当HF HNO3=1 1,稀释液浓度百分比小于 10%时,随稀释液的增加对腐蚀速率影响较大草原稀 释液从10% 30%,腐蚀速率随秋耕释液的增加呈减 小;稀释液大于30%后,稀释的微小变化会引起腐蚀 速率的很大变化。
MEMS工艺
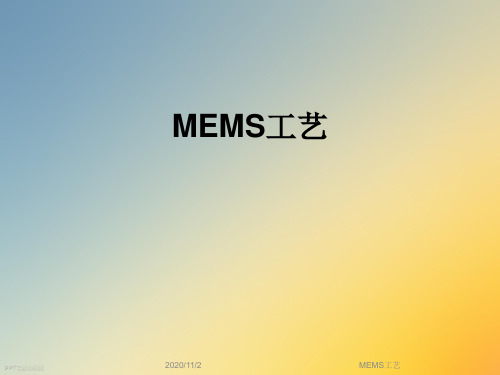
PPT文档演模板
MEMS工艺
Ø 表面微加工过程特点:
Ø添加——图形——去除 Ø添加:薄膜沉积技术 Ø图形:光刻 Ø去除:腐蚀技术
PPT文档演模板
MEMS工艺
2.残余应力
在微机械加工中是固有的
PPT文档演模板
MEMS工艺
3.存在于薄膜结构中本身的应力
Ø由微加工过程中原子结构局部变化产 生的
Ø例如,过量掺杂会导致结构在表面微 加工后产生很大的残余应力
PPT文档演模板
MEMS工艺
粘连
Ø两个分离薄片粘附在一起的现象称为 粘连;
PPT文档演模板
MEMS工艺
PPT文档演模板
MEMS工艺
表面微机械加工的特点
Ø 1、在表面微机械加工中,硅片本身不被刻 蚀,没有穿过硅片,硅片背面也无凹坑。
Ø 2、表面微机械加工适用于微小构件的加工, 结构尺寸的主要限制因素是加工多晶硅的 反应离子刻蚀工艺。
Ø 3、形成层状结构的特点为微器件设计提供 较大的灵活性。
Ø酒精、液态CO2置换水; Ø依靠支撑结构防止塌陷。
PPT文档演模板
MEMS工艺
PPT文档演模板
典型牺牲层腐蚀工艺
Ø 氧化,做体硅腐蚀掩膜层; Ø 光刻氧化层,开体硅腐蚀窗口; Ø 体硅腐蚀出所需底层结构; Ø 去除SiO2; Ø 生长或淀积牺牲层材料; Ø 光刻牺牲层材料成所需结构; Ø 生长结构材料; Ø 光刻结构材料; Ø 牺牲层腐蚀,释放结构层; Ø 防粘结处理。
MEMS工艺
MEMS工艺(表面硅加工技术)

D、横向腐蚀形成空腔
腐蚀掉SiO2形成空腔,即得到多晶硅桥式可活动 的硅梁
五、影响牺牲层腐蚀 的因素
牺牲层厚度 腐蚀孔阵列
多晶
LT
塌陷和粘连及防止方法
酒精、液态 置换水; 酒精、液态CO2置换水; 依靠支撑结构防止塌陷。 依靠支撑结构防止塌陷。
六、表面微加工特点及关键 技术
表面微加工过程特点:
ASSEMBLY INTO PACKAGE
PACKAGE SEAL
FINAL TEST
采用特殊的检测和划 片工艺保护释放出来的机 械结构封装时暴 Nhomakorabea部分零件
机、电系统 全面测试
三、表面微加工原理 表面微加工技术主要靠在基底上逐 层添加材料而构造微结构 表面微加工器件是由三种典型的部 件组成:⑴牺牲层;⑵微结构层; ⑶绝缘层部分
MEMS的典型生产流程
膜越厚, 膜越厚,腐蚀 次数越少。 次数越少。
多次循环 成膜
DEPOSITION OF MATERIAL
去除下层材料, 去除下层材料, 释放机械结构
光刻
PATTERN TRANSFER
腐蚀
REMOVAL OF MATERIAL
PROBE TESTING
SECTIONING
INDIVIDUAL DIE
添加——图形——去除 添加:薄膜沉积技术 图形:光刻 去除:腐蚀技术 表面微加工和IC工艺的区别:形成机械结构! 形成机械结构! 形成机械结构
参考文献
[1]任小中 现代制作技术 任小中.现代制作技术 武汉: 任小中 现代制作技术[M].武汉:华中科技大学,2009,9. 武汉 华中科技大学, [2]微电机系统(MEMS)原理、设计和分析 微电机系统( 西安: 微电机系统 )原理、设计和分析[M].西安:西安 西安 电子科技大学出版社, 电子科技大学出版社,2009,5.
典型MEMS工艺流程
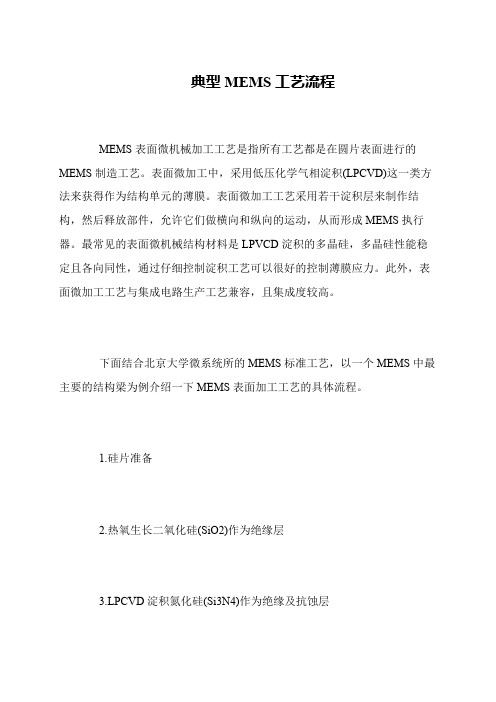
典型MEMS工艺流程
MEMS表面微机械加工工艺是指所有工艺都是在圆片表面进行的MEMS制造工艺。
表面微加工中,采用低压化学气相淀积(LPCVD)这一类方法来获得作为结构单元的薄膜。
表面微加工工艺采用若干淀积层来制作结构,然后释放部件,允许它们做横向和纵向的运动,从而形成MEMS执行器。
最常见的表面微机械结构材料是LPVCD淀积的多晶硅,多晶硅性能稳定且各向同性,通过仔细控制淀积工艺可以很好的控制薄膜应力。
此外,表面微加工工艺与集成电路生产工艺兼容,且集成度较高。
下面结合北京大学微系统所的MEMS标准工艺,以一个MEMS中最主要的结构梁为例介绍一下MEMS表面加工工艺的具体流程。
1.硅片准备
2.热氧生长二氧化硅(SiO2)作为绝缘层
3.LPCVD淀积氮化硅(Si3N4)作为绝缘及抗蚀层。
MEMS工艺(5表面硅加工技术)

表面微加工
表面微加工技术主要靠在基底上逐 层添加材料而构造微结构
表面微加工器件是由三种典型的部 件组成:⑴牺牲层;⑵微结构层; ⑶绝缘层部分
基本概念
在微机械加工中,通常将两层薄膜中的下 面一层腐蚀掉,只保留上面的一层,这种 技术称为牺牲层腐蚀,又称为分离层腐蚀。 利用牺牲层腐蚀技术直接在衬底表面制作 微机械元件结构的技术被称为“硅表面微 机械加工技术”。
不同淀积方法生成的二氧化硅性质表
。)
PECVD 200℃ SiO1。9(H) 可变(Adams 说 不一致) 失氢 2.3 1.47 300(压)到300 (拉) 3到6
淀积类型 典型温度 成分 台阶覆盖率 热稳定性 密度(g/cm3) 折射率 应力(Mpa) 电介质强度 (106V/cm或 102V/μm) 腐蚀速率 (nm/min)(H2O: HF=100:1)
多晶硅材料的主要特点 (2)多晶硅薄膜对生长衬底的选择不 苛刻。衬底只要有一定的硬度、平整度 及能耐受住生长工艺温度即可。 (3)可以通过对生长条件及后工艺的 控制来调整多晶硅薄膜的电阻率,使它 成为绝缘体、导体或半导体,从而适应 不同器件或器件不同部分的需要。
多晶硅材料的主要特点
(4)多晶硅薄膜作为半导体材料 可以像单晶硅那样通过生长、扩散 或离子注入进行掺杂,形成N型或 P型半导体,制成p-n结;可以采用 硅平面工艺进行氧化、光刻、腐蚀 等加工。
二氧化硅当然是硅加工实验室中最常用的 介质。它可以自身生长,也可以淀积,有 无掺杂剂都行,既使掺杂后仍然绝缘。
热生长型SiO2常用作MOS门绝缘层。如 果淀积的SiO2 中掺入磷,那就叫做磷硅 玻璃、“P玻璃”或PSG,它常用作最终 钝化层;
如果掺入硼,那就叫做硼硅玻璃或BSG;如 果在玻璃中掺入磷和硼的混合物,则常称为 BPSG或低温氧化物(LTO),它具有良好 的低温回流特性,可使高深宽比表面结构 “光洁化”或平面化。 在IC工艺中,SiO2是一种多用途的基本材料, 它通过热氧化生长和为满足不同要求采用不 同工艺淀积获得。
- 1、下载文档前请自行甄别文档内容的完整性,平台不提供额外的编辑、内容补充、找答案等附加服务。
- 2、"仅部分预览"的文档,不可在线预览部分如存在完整性等问题,可反馈申请退款(可完整预览的文档不适用该条件!)。
- 3、如文档侵犯您的权益,请联系客服反馈,我们会尽快为您处理(人工客服工作时间:9:00-18:30)。
1
2
3
方法二:采用疏水涂层
在微结构和衬底上采用疏水涂层可以降低结合能,从而降低粘附。 表面覆盖一层自组装的长链分子,这种长链分子叫做单层疏水自组 装。
除了用于防粘附涂层外,疏水表面处理还可以应用于其他领域。 例如: 采用疏水的图形化区域降低了表面结合能,就可以不采用牺牲 层湿法刻蚀便从模具中提起圆片级尺度的器件; 局部疏水处理可以使小部件按照自组织方式进行自动组装。
2.它制造的机械结构基本上都是二 维,因为机械 结构的厚度完全受限 于沉积薄膜的厚度。
2.由于体微机械加工 工艺无法做到零部件 的平面化布局,因此 它不能够和微电子线 路直接兼容。
在硅片上淀积一层牺牲层
二、基本工艺流程
光刻定义图形层
淀积结构层薄膜
图形化结构层薄膜
去除牺牲层,释放结构层
形成最终结构
•举例:方案一 —— 微型马达基本制造工艺流程
一.基本概念
•微机械加工
微机械加工技术是加工微米量级机械的技术,即是为微传感 器、微执 行器和微电子机械系统制作微机械部件和结构的加工技术。
•分类方法
硅基微机械加工
按加工材料分类 非硅基微机械加工 体微机械加工 在工艺中经常 同时使用
按加工类型分类
表面微机械加工
复合微机械加工
•表面微机械加工的定义
悬浮结构与衬底的接触会导致不可逆的损坏。一旦接触,强大的分子力(例如范 德华力)会加强悬浮结构和衬底间的吸引。另外,由于存在新的反应副产品,很 可能会产生固体桥接。 微结构的这种失效模式称为粘附(stiction)。 粘附(stiction)=粘连(sticking)+摩擦(friction) 解决粘附问题的方法均源于以下四种途径之一: 1. 改变固体与液体界面的化学性质以减小毛细吸引力。 2. 防止产生过大的结合力,如提高溶液温度或减少表面接触面积。 3. 采用各种形式的能量输入释放粘附在衬底上的结构,这些方法 可以局部进行也可以整体进行。 4. 为机械结构提供反向力以防止其相互接触,如利用本征应力引 起的弯曲现象。 下面详细介绍利用上述途径的两种典型方法。
第11章 表面微机械加工
汇报人:胡文艳 时 间:2017.6.10
目录
01 - 相关基本概念介绍
02 - 表面微机械加工基本工艺介绍
Contents
03 - 结构层材料和牺牲层材料的选择
04 - 加速牺牲层刻蚀的方法——钻蚀释放速度的技术 05 - 粘附机制和抗粘附的方法——与烘干工艺相关的失效以及改进方法
在氢氟酸刻蚀牺牲层时的低刻蚀速率
氮化硅
3SiH4+4NH3 绝缘的电解质,具有本征张应力。 =Si3N4+24H SiH4+O2 =SiO2+2H2
二氧化硅 500℃
附加的磷化氢气体掺入LTO(低温氧化硅,即没有被掺杂的二氧化 硅),可生成磷硅玻璃(PSG),掺入磷原子可加速二氧化硅在氢 氟酸中的刻蚀速率。 PECVD
•结构层和牺牲层材料的制备方法
实际中广泛应用到的结构层和牺牲层材料的淀积方法是化学气相沉积(CVD), 根据提供能量不同有如下分类:
能量仅由热能提供且 反应在低压中进行
能量由等离子能源提供
低压化学气相沉积 (LPCVD)
等离子体增强化学 气相沉积(PECVD)
LPCVD沉积腔(多 个温度区用于提高材 料生长的均匀性)
体微机械加工 微机械加工工艺 表面微机械加工 复合微机械加工
定义:能够制造附着于衬底表面附近的微结构的工艺。 与体微机械加工不同,表面微机械加工没有移除或刻蚀 体衬底材料。
•表面微机械加工和体微机械加工工艺特点:
表面微机械加工 优点 充分利用了现有的IC生产工艺,对 机械零部件尺度的控制与IC一样好, 因此这种技术和IC完全兼容。 1.机械加工层越 多微 型元件的布局 问题、平面化问题 和减小残余应力 问题也更难解决。 缺点 体微机械加工 可以相对容易地 制造 出大质量的零部 件。 1.很难制造精细灵敏 的悬挂系统。
这些孔可以使其下的牺牲层被快速移除而不需要借助大尺寸的刻 蚀孔。因为孔尺寸达到纳米量级,所以它们对器件的工作影响很 小。
五、粘附机制和抗粘附的方法
——与烘干工艺相关的失效以及改进方法
牺牲层去除常常采用化学溶剂来完成,因为其刻蚀速率高,设备简单刻蚀选择性好。 它常需要采用自然蒸发或强制蒸发的后处理方法对圆片和芯片进行干燥。具体情况如 下图。
四、加速牺牲层刻蚀的方法
——钻蚀释放速度的技术
方法一:
以上图磁执行器为例,每个板由两个悬臂梁支撑,板上的四个刻蚀孔使得牺牲层钻蚀不但可以在板 的边缘发生,而且可以在其内部进行。这种方法可以大大减少刻蚀所需时间。 右图为刻蚀孔的显微照片。大多数情况下,刻蚀孔应当比较小,以免在器件工作时产生不良影响。
方案三 —— 微型马达制造工艺流程改进
为了解决上述由于转子和定子的接触而产生额外摩擦问题,这里采用氮化硅 作为接触面以降低转子和定子间的摩擦系数。 定子的侧壁具有摩擦控制层,底槽区域内沉积的氮化硅可以防止定子落到衬 底表面。
三、结构层材料和牺牲层材料
工艺材料选择标准:
理想工艺规则: 1. 将结构层淀积在牺牲层上时,不能导致牺牲层熔化、溶解、开裂、 分解、变得不稳定或其他形式毁坏。 2. 用于结构层图形化的工艺不能破坏牺牲层和衬底上已有的其他薄层。 3. 用于除去牺牲层的工艺不能侵蚀、溶解、损坏结构层和衬底。 多重结构层和牺牲层规则(如前述微型马达工艺流程): 1. 淀积的材料层不能破坏其底层材料。 2. 牺牲层刻蚀工艺中不能破坏硅片上的其他任何材料。 3. 将牺牲层或者结构层图形化的任何工艺过程,不能刻蚀损坏现存硅 片上的其它层材料。
(刻蚀孔、改变刻蚀方法和刻蚀材料等)
05 - 粘附机制和抗粘附的方法——与烘干工艺相关的失效以及改进方法
(超临界流体烘干、采用疏水涂层等)
本章小结:
01 - 相关基本概念介绍
(微机械加工、表面微机械加工、分类方法、表面微机械加工和体微机械比较)
02 - 表面微机械加工基本工艺介绍
(以微型马达基本制造工艺流程为例,三种方法的改进)
03 - 结构层材料和牺牲层材料的选择
(工艺材料选择标准、结构层和牺牲层材料的制备方法)
04 - 加速牺牲层刻蚀的方法——钻蚀释放速度的技术
刻蚀剂对牺牲层的刻蚀速率
刻蚀剂对结构层的刻蚀速率
Q&A:这个比值应该尽可能的大还是小?
刻蚀选择性=
rs a rs t
理想情况下,较高的牺牲层刻蚀速率rsa意味着完成牺牲层刻蚀过程的 时间减少。 如果两种备选方案具有相同的刻蚀选择性,那么具有较高牺牲层刻蚀 速率rsa的方案更受青睐。 如果其中的一种方案对牺牲层的刻蚀速率较慢但是比另一种方案的刻 蚀选择性高,那么在选择方案时应考虑其他因素。 综上,可以看出,刻蚀选择性应当尽可能地大。
溅射
除LPCVD外的 其他方法:
硅、氧化硅、氮化硅
多晶硅
•其他表面微机械加工材料与工艺:
其他材料及其优点: 锗硅及多晶锗: 1. 较低的加工温度(多晶硅580℃,锗硅工艺温度只有450℃) 2. 与多晶硅相比,锗硅的生长速率更高。 聚合物及金属薄膜: 1. 在更低的温度下加工。 2. 采用更简单的设备进行沉积。 其他工艺 对于聚合物材料: 旋涂、汽相涂覆、喷涂和电镀。 对于金属元素: 蒸发及溅射:沉积薄金属膜(小于1μm) 电镀:制造厚金属膜(大于2μm)
a) b) c) d) e) f) g) h)
在硅片上淀积一层牺牲层。 淀积多晶硅作为结构层材料,制造转子。 光刻胶作掩膜,反应离子刻蚀使图形转移到多晶硅结构层上。 硅片表面沉积另一层氧化物牺牲层(材料可能与前一层不同,常选择 LPCVD 二氧化硅) 加工出与衬底相连的锚区窗口(为了制造定子,限制转子的侧向平移) 沉积第二层结构层,该结构层通过锚区窗口与衬底相连(制造定子) 再次涂敷光刻胶用于光刻第二层结构形状。 浸入氢氟酸刻蚀液以除去两层牺牲层。
在MEMS中应用的LPCVD材料主要有三种:多晶硅、氮化硅和二氧化硅:
LPCVD 材料 反应 温度 580℃ ~ 620℃ 800℃ 化学反应 方程式 保形性 SiH4=Si+2H2 应力 刻蚀速率
其他性质及其他
保形覆盖的目的是覆盖三维结构的图形 对于螺母结构:会引起扣住的现象
多晶硅
对于悬臂梁结构:厚度方向的梯度应力会引起形变
方法二:改变刻蚀方法和刻蚀材料
在某些应用中,刻蚀孔对器件性能有一定的影响。例如, 光反射器上的刻蚀孔不但会降低反射系数,而且会导致衍射 的发生。所以除此方法外,据研究表明,以下材料具有非常 快的刻蚀速率和很高的刻蚀选择性: 1. 树状聚合物,例如超分支聚合物。 2. 氧化锌薄层。 若牺牲层是金属,可通过加偏压使其在电解液中溶解的方法来 加速钻蚀。 使用自组装的单分子层来释放大面积的微器件而不需要采用化 学湿法刻蚀。
•方案一带来的问题:
定子 转子 衬底
1. 转子在重力作用下很容易落在衬底上,产生大面积接触。 2. 转子在高速转动过程中会与定子产生接触,产生额外的摩 擦和磨损。
方案二 —— 微型马达制造工最主要的不同之处是第二层结构层(定子)的材料用氮化硅取代了多晶硅。
产生的问题:转子和衬底仍有可能粘连,但接触的可能性减小到微小的凸 点上。
方法一:超临界流体烘干
可以防止液体与空气界面处出现反向表面张力,超临界相出现在高温高压的环境下。下图为 超临界相技术的典型烘干工艺。 1、将带有释放微结构的芯片浸 入液体中并置于合适的压强和室 温下。初始状态在相图中用点1 表示。 2、增加液体的温度并保持压强 不变,溶剂从液相转变为超临 界相(点2) 3、降低超临界相流体的压力, 使得超临界流体转变为汽相 (点3) 优点:从液相转变为超临界相以及从超临界相转变为汽相的过程中不存在表面张力。