垂直分型射压造型线型砂质量控制及生产应用
DISA垂直射压铸造生产线的管理要点
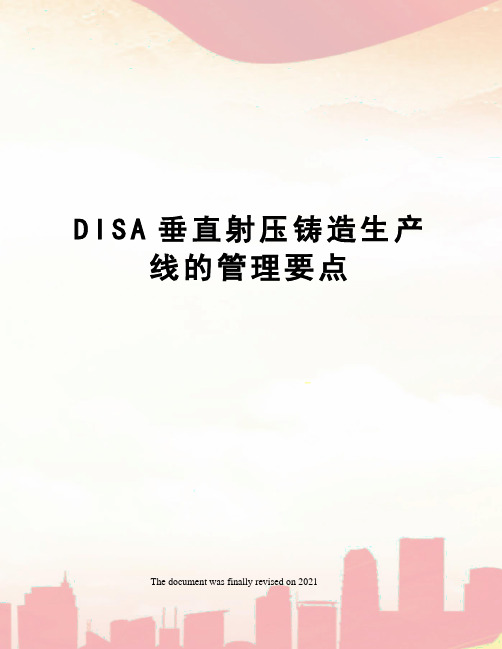
D I S A垂直射压铸造生产线的管理要点The document was finally revised on 2021DISA垂直射压铸造生产线的管理要点摘要:丹麦DISA 公司生产的DISA湿型砂垂直射压造型机具有性能可靠、精度高、表面质量好、错型值小、操作简单和生产效率高等优点,目前在造型机行业处于最高水平。
有人说DISA 造型机就象傻瓜相机一样操作简单;也有用印钞机来比喻DISA造型机。
但实际经验告诉我们上,如果没有好的管理,好的设备并不能发挥好的作用。
即使有了先进的造型机,也不一定能生产出合格的铸件。
铸造生产是一个连续的过程,而且铸造是一个影响因素很多的系统,如果这个系统中有一个环节出了问题,就很有可能出废品。
又因为DISA 公司造型机的生产效率很高,所以一旦开始出废品,产生废品的速度也是惊人的。
因此,我们应该用系统的观点来考虑问题。
本文从新产品的开发谈起,就有关DISA 垂直射压造型生产线运行中应该注意的问题谈一些粗浅的看法。
关键词:铸造 DISA垂直射压造型线生产管理?1.全面准确地理解客户的要求让顾客满意的前提是要准确理解顾客的要求。
顾客的要求包括对产品质量特性的要求(如机械性能、化学成分、金相组织、尺寸公差、表面质量、检测方法的规定等)、对产品交付方面的要求(产品的数量、交付期、交货目的地等)、对价格方面的要求(价格条件、付款方式、结算方式等)及违约责任等其他特殊要求。
顾客的要求应该以书面的形式来表达,避免以后与顾客发生争执。
2.新产品的开发在新产品的开发阶段,首先要明确输入的顾客信息并制定开发计划,其次对设计开发的不同阶段要进行评审和验证,直至样品被顾客接受。
制定控制计划、作业指导书是该阶段必须要做的事情。
3. 原料采购铸造行业原材料所占的成本大约在60-70 %,因此通过在原料采购中对所有的原材料均应招标采购,这样做可以比较明显的降低原材料的价格和采购成本,提高原材料的质量。
垂直分型无箱射压造型机生产线[发明专利]
![垂直分型无箱射压造型机生产线[发明专利]](https://img.taocdn.com/s3/m/ce421ff9cc7931b764ce1526.png)
专利名称:垂直分型无箱射压造型机生产线
专利类型:发明专利
发明人:胡雷,孙会平,于化军,李永国,董春兰,尹燕义,孙飞申请号:CN201911159921.1
申请日:20191123
公开号:CN110722113A
公开日:
20200124
专利内容由知识产权出版社提供
摘要:本发明涉及一种垂直分型无箱射压造型机生产线,属于铸造加工生产线的技术领域,其技术方案要点是一种垂直分型无箱射压造型机生产线,包括型砂破碎及输送工段、砂型成型工段、铸件铸造以及凝固工段和砂件分离工段,所述型砂破碎及输送工段、砂型成型工段、铸件铸造以及凝固工段和砂件分离工段呈闭环状排列,且铸件铸造以及凝固工段设置有铸造辅助组件,铸造辅助组件包括支架、连接座和铸液桶,连接座的顶部与支架滑移连接,且连接座的底部与铸液桶铰接相连,达到提高生产效率的效果。
申请人:济南平阴天宫铸造有限公司
地址:250400 山东省济南市平阴县孝直镇大天宫村
国籍:CN
更多信息请下载全文后查看。
垂直分型线在铸造厂应用分析
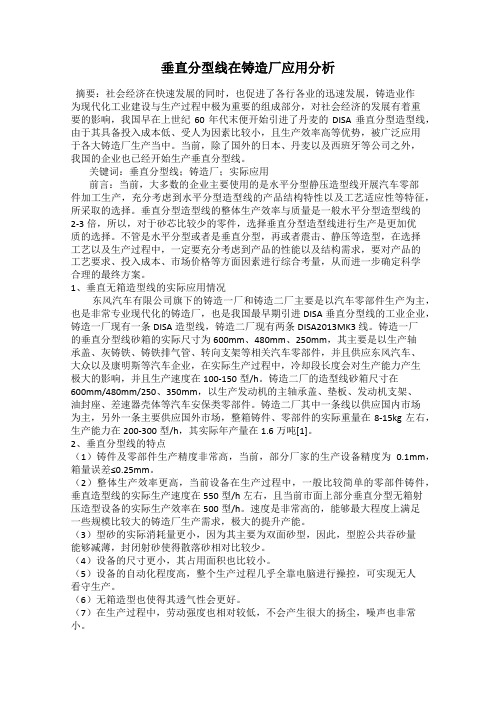
垂直分型线在铸造厂应用分析摘要:社会经济在快速发展的同时,也促进了各行各业的迅速发展,铸造业作为现代化工业建设与生产过程中极为重要的组成部分,对社会经济的发展有着重要的影响,我国早在上世纪60年代末便开始引进了丹麦的DISA垂直分型造型线,由于其具备投入成本低、受人为因素比较小,且生产效率高等优势,被广泛应用于各大铸造厂生产当中。
当前,除了国外的日本、丹麦以及西班牙等公司之外,我国的企业也已经开始生产垂直分型线。
关键词:垂直分型线;铸造厂;实际应用前言:当前,大多数的企业主要使用的是水平分型静压造型线开展汽车零部件加工生产,充分考虑到水平分型造型线的产品结构特性以及工艺适应性等特征,所采取的选择。
垂直分型造型线的整体生产效率与质量是一般水平分型造型线的2-3倍,所以,对于砂芯比较少的零件,选择垂直分型造型线进行生产是更加优质的选择。
不管是水平分型或者是垂直分型,再或者震击、静压等造型,在选择工艺以及生产过程中,一定要充分考虑到产品的性能以及结构需求,要对产品的工艺要求、投入成本、市场价格等方面因素进行综合考量,从而进一步确定科学合理的最终方案。
1、垂直无箱造型线的实际应用情况东风汽车有限公司旗下的铸造一厂和铸造二厂主要是以汽车零部件生产为主,也是非常专业现代化的铸造厂,也是我国最早期引进DISA垂直分型线的工业企业,铸造一厂现有一条DISA造型线,铸造二厂现有两条DISA2013MK3线。
铸造一厂的垂直分型线砂箱的实际尺寸为600mm、480mm、250mm,其主要是以生产轴承盖、灰铸铁、铸铁排气管、转向支架等相关汽车零部件,并且供应东风汽车、大众以及康明斯等汽车企业,在实际生产过程中,冷却段长度会对生产能力产生极大的影响,并且生产速度在100-150型/h。
铸造二厂的造型线砂箱尺寸在600mm/480mm/250、350mm,以生产发动机的主轴承盖、垫板、发动机支架、油封座、差速器壳体等汽车安保类零部件。
垂直分型造型线方案讨论

垂直分型造型线方案讨论一. 可供选择的造型线型号:造型线型号铸型分型面尺寸(mm)416A 600*480416B 650*535417A 700*535417B 750*535造型线的选择既要考虑生产效率,还要考虑出品率和成品率,太古张敢开的玛钢厂选用的是417B垂直分型造型线,边树林推荐416B,两者价格相差5-8万元。
416的可靠性会可能会高一些,合箱精度比417高。
二. 空压机的选择每条线要配备6m3/分钟的空压机,如同时上2条线,应配备3台6m3/分钟的空压机,其中1台作为备用机。
每台空压机均需配一个储气罐,压力为7kg/cm2,每条线的现场还要配一个储气罐,压力为4.5-5.0 kg/cm2。
国内比较知名的品牌是英格索兰和寿力,张敢使用的是河北产的空压机。
根据我们的经验,压缩空气管路不要铺设在管沟内,最好架空,这样做的好处是如果管路漏风,能及时发现。
空压站的配置要有前瞻性,你可能只上2条线,也可能要上10条线。
三. 砂处理系统的配置张敢选用的是常州格瑞-卡斯丁公司生产的砂处理系统:每套铸型的型砂体积:0.75*0.535*0.16=0.064m3铸型密度:1.6t/m3生产率:240型/小时每小时的型砂用量:0.064*1.6*240=24.6t≈25t2条线配置1套砂处理系统故砂处理能力应达到25*2=50t/h每条线需配置一台混砂机,按平均每4分钟混制一碾砂计算,每小时可混制15碾砂,由此可以算出混砂机的容量应达到25÷15=1.67t/碾,松散砂的密度按1.4 t/m3计算:混砂机的容量应达到1.67÷1.4=1.2m3/碾。
四. 生产能力的估算以每型40件;每件0.165kg;出品率62%计算:每型的铁水消耗量为40*0.165÷0.62=10.65kg/型按240型/h的能力计算:每条线一小时的铁水需求量为:10.65*240=2556kg/h按出品率62%计算,每条线一小时可生产扣件:2556*0.62=1585 kg/h五. 浇包的数量和容量的确定每条线需配置3只浇包按240型/h的能力计算:2个铸型浇注时间间隔为:60*60秒÷(240-1)=15秒每只浇包每小时可浇注240÷3=80型如果每包铁水每次浇注8箱:则每包铁水的浇注时间为(8*15=120秒。
水平分型脱箱造型线的应用与垂直分型造型线展望

水平分型脱箱造型线的应用与垂直分型造型线展望白凤文【摘要】分别对单、双工位水平分型脱箱造型线的使用情况作了介绍,并对垂直分型无箱射压造型线的调研情况进行了总结.【期刊名称】《中国铸造装备与技术》【年(卷),期】2010(000)003【总页数】3页(P54-56)【关键词】水平分型;垂直分型;造型线【作者】白凤文【作者单位】烟台胜地机械制造有限公司,山东烟台市264006【正文语种】中文【中图分类】TG231.6烟台胜地机械制造有限公司主要采用水平分型造型线生产刹车盘等铸件。
2003年,配备了两条Z146震实造型线,砂箱内尺寸为700mm×480mm,每条线设计能力为70型/h。
随着生产的发展,2005年又增设一条单工位水平分型脱箱造型线,砂箱内尺寸为610mm×508mm,设计能力为120型/h。
随着生产的进一步发展,2007年、2008年又先后上了四条双工位水平分型脱箱造型线,砂箱内尺寸为608mm× 500mm,设计能力为170型/h。
用水平造型线生产铸件具有投资少,工艺传统、简单,工艺出品率高,模样、浇道在模板上布局方便等优点。
用水平分型脱箱造型线生产铸件,又具有工装投入少、维护费用低、占用面积小等优点,更适用于小型、大批量铸件的生产模式。
近两年,我们又对高速、高效垂直分型造型线进行了考察和调研,并对其有了进一步的了解,解除了对垂直分型造型线的一些顾虑,有望在今后的技术改造、扩大生产中选用。
为了给同行在设备选用上提供一点借鉴,或把已有的设备用好,本文总结了近年来本公司水平脱箱造型线的使用经验,并综述了对垂直分型造型线考察、调研的情况及笔者的一些看法。
供大家在设备改造和新建铸造厂时参考。
1.1 出现的问题我们最初选用的单工位脱箱造型自动线,相比Z146震实式造型机开式有箱造型线,虽然具有结构简单、占地面积小、设备投资少、工装投入少以及自动化程度高、用人少等几方面优点。
垂直分型射压造型线型砂质量控制及生产应用

压造 型 线 , 液 采用 中频 电炉 熔炼 , 件 以薄 壁 铸 铁 铁 铸 ( 灰铸 铁 和球 墨 铸 铁 ) 为 主 , 品包 括 汽车 零配 件 、 件 产 管道 件 阀门件 等 。我 公 司经 过 多年 生产 实 践 , 型 在 砂质 量控 制方 面做 了大量 工作 , 并取 得 了 良好效 果 。
用 的工 装 ( 箱 ) 钢 质 的 , 以 即使在 砂 箱 上 打 箱 砂 是 所
维普资讯
材 料工艺
T R, &TC N L G  ̄t. EH OO Y J J
垂直分型射压造型线型砂质量控制及生产应用
Modn a dQu l yCo to n eo ria ligS n ai nr l dUs f t l t a Ve c
Pa tn h o q e z o d n n r i g S o tS u e eM l i g Li e
赵占良( 河北 裕 龙铸 造有 限 公司 , 北 省石 家庄 市 河 003 5 0 5)
关键 词 : 型砂 性 能 , 量控 制 质
中图分 类号 : G 2 文 献标识 码 : ; T 2 l: A 文章编 号 : 0 — 6 8 2 0 ) 6 3 l 9 ( 0 7 0 — 06 5
样气 体 压力 骤 然上 升 ,且 裂解 产 物来 不 及 排 出时 出
现 反喷从 而 伤人 。浇 注过程 中 , 口杯始 终处 于充 满 浇
状 态 , 不 能 断 流 , 保 证 直 浇 道 处 于封 闭状 态 , 且 要 不
能充 入空 气 。 因为型 腔 内 的 E S模 样是 在 高 温高压 P
1 原 材 料 质 量 要 求 11 原 砂 .
12 煤粉 .
迪砂(Disa)线
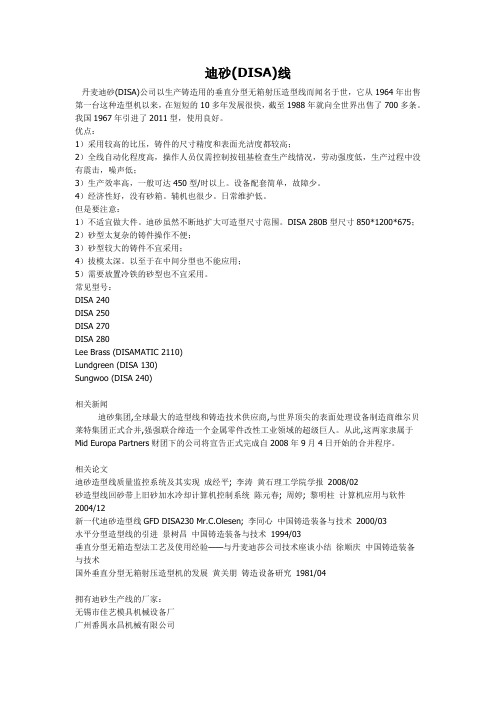
迪砂(DISA)线丹麦迪砂(DISA)公司以生产铸造用的垂直分型无箱射压造型线而闻名于世,它从1964年出售第一台这种造型机以来,在短短的10多年发展很快,截至1988年就向全世界出售了700多条。
我国1967年引进了2011型,使用良好。
优点:1)采用较高的比压,铸件的尺寸精度和表面光洁度都较高;2)全线自动化程度高,操作人员仅需控制按钮基检查生产线情况,劳动强度低,生产过程中没有震击,噪声低;3)生产效率高,一般可达450型/时以上。
设备配套简单,故障少。
4)经济性好,没有砂箱。
辅机也很少。
日常维护低。
但是要注意:1)不适宜做大件。
迪砂虽然不断地扩大可造型尺寸范围。
DISA 280B型尺寸850*1200*675;2)砂型太复杂的铸件操作不便;3)砂型较大的铸件不宜采用;4)拔模太深。
以至于在中间分型也不能应用;5)需要放置冷铁的砂型也不宜采用。
常见型号:DISA 240DISA 250DISA 270DISA 280Lee Brass (DISAMATIC 2110)Lundgreen (DISA 130)Sungwoo (DISA 240)相关新闻迪砂集团,全球最大的造型线和铸造技术供应商,与世界顶尖的表面处理设备制造商维尔贝莱特集团正式合并,强强联合缔造一个金属零件改性工业领域的超级巨人。
从此,这两家隶属于Mid Europa Partners财团下的公司将宣告正式完成自2008年9月4日开始的合并程序。
相关论文迪砂造型线质量监控系统及其实现成经平; 李涛黄石理工学院学报2008/02砂造型线回砂带上旧砂加水冷却计算机控制系统陈元春; 周婷; 黎明柱计算机应用与软件2004/12新一代迪砂造型线GFD DISA230 Mr.C.Olesen; 李同心中国铸造装备与技术2000/03水平分型造型线的引进景树昌中国铸造装备与技术1994/03垂直分型无箱造型法工艺及使用经验——与丹麦迪莎公司技术座谈小结徐顺庆中国铸造装备与技术国外垂直分型无箱射压造型机的发展黄关朋铸造设备研究1981/04拥有迪砂生产线的厂家:无锡市佳艺模具机械设备厂广州番禺永昌机械有限公司山西晋城小笠原铸造有限公司广东省韶铸集团有限公司无锡小天鹅精密铸造有限公司济南玫德铸造有限公司衡水格林铸鑫科技有限责任公司上海罕睿能机械有限公司恒盛模具有限责任公司?河北思尔可金属科技有限公司河南星鹏铸件有限责任公司安徽神剑科技股份有限公司东贝集团=-轻工铸造厂山东弘德机械工业有限公司华翔3.5万吨迪砂精铸??莲花山铸造有限公司--拟引进林州市龙鼎铸业有限公司济南玛钢股份有限公司北京吉美特管道科技有限公司桂林汽车零部件厂。
射压造型型砂性能要求

前言高密度造型方法(或称高紧实度造型,包括多触头高压、气冲、挤压、射压、静压、吸压造型方法)的生产效率高、铸件品质较好,因而国内外应用都很普遍。
高密度造型对型砂品质的要求比较严格。
本文用表格(见文后附表)列举部分典型的国内外铸造厂实际应用的和部分设备公司推荐的高密度砂型主要的和经常测定的型砂性能,并加以评论。
1 紧实率和含水量湿型砂不可太干,否则膨润土未被充分润湿,起模困难,砂型易碎,表面的耐磨强度低,铸件容易生成砂孔和冲蚀缺陷。
型砂也不可太湿,过湿型砂易使铸件产生针孔、气孔、呛火、水爆炸、夹砂、粘砂等缺陷,而且型砂太粘、型砂在砂斗中搭桥、造型流动性降低。
使砂型型腔表面松紧不均;还可能导致造型紧实距离过大和压头陷入砂箱边缘以内而损伤模具和砂型吃砂量过小。
表明型砂干湿状态的参数有两种:紧实率和含水量。
附表中国内各厂的紧实率和含水量除特别注明以外,取样地点都在混砂机处。
但是型砂紧实率和含水量的控制应以造型处取样测定为准。
从混砂机运送到造型机时紧实率和含水量下降幅度因气候温度和湿度状况、运输距离、型砂温度等因素而异。
如果只根据混砂机处取样检测结果控制型砂的湿度,就要略增少许,以补偿紧实率和水分的损失。
以前的观点认为手工造型和震压式机器造型最适宜于湿状态下的紧实率大约在45~50%;高压造型和气冲造型时为40~45%;挤压造型要求流动性好,紧实率为35~40%。
由表中可以看出,目前铸件品质较好的工厂,高密度造型的型砂紧实率(大多是从混砂机取样)通常都在25~45%范围内,比较集中于30~40%之间,比以前有明显降低。
这是由于高密度造型设备的起模精度提高,而且要求砂型各部位硬度均匀分布,使型砂的流动性成为重要因素。
工厂的控制原则大多是只要能够保证起模顺利就尽力降低紧实率。
从减少铸件气孔缺陷的角度出发,要求最适宜干湿状态下型砂的含水量尽可能低。
高强度型砂的膨润土加入量多,型砂中含有较多灰分,所购入煤粉和膨润土因品质低劣而需要增大加入量,混砂机的加料顺序不当、揉碾作用不强、刮砂板磨损、混砂时间太短,以致型砂中存在较多不起粘结作用的小粘土团块,都会提高型砂的含水量。
- 1、下载文档前请自行甄别文档内容的完整性,平台不提供额外的编辑、内容补充、找答案等附加服务。
- 2、"仅部分预览"的文档,不可在线预览部分如存在完整性等问题,可反馈申请退款(可完整预览的文档不适用该条件!)。
- 3、如文档侵犯您的权益,请联系客服反馈,我们会尽快为您处理(人工客服工作时间:9:00-18:30)。
垂直分型射压造型线型砂质量控制及生产应用在粘土砂铸造生产过程中,型砂是关键,其性能控制得好与坏,质量稳定与否,将对铸件质量产生巨大的影响。
我公司的造型线为ZZ416垂直分型射压造型线,铁液采用中频电炉熔炼,铸件以薄壁铸铁(灰铸铁和球墨铸铁)件为主,产品包括汽车零配件、管道件、阀门件等。
我公司经过多年生产实践,在型砂质量控制方面做了大量工作,并取得了良好效果。
1原材料质量要求1.1原砂选用河北围场擦洗砂,含泥量<1.0%,SiO2>85%,原砂粒度70/140目。
由于垂直分型射压造型属高密度造型,为减少砂型受热膨胀,避免因砂粒受挤压从砂型表面脱落而引起铸造缺陷,粒度要求不宜过于集中,原砂最好采用4筛集中率85%以上,主峰筛(100目)量控制在40%以内。
新砂补加量在5%以下。
1.2煤粉煤粉灰份应<10%,煤粉含灰量过高,使得型砂含泥量增加,影响型砂使用性能。
含硫量≤1.5%;煤粉粒度≥95%以上的颗粒通过140目筛,并且煤粉不允许有大颗粒存在,因其在浇注过程中遇金属液燃烧时间长,阻止铁液靠近型壁,待铁液凝固后,便会造成铸件表面凹坑,影响铸件表面粗糙度。
挥发分的高低是衡量煤粉质量好坏的主要指标之一,好的煤粉挥发分含量较高,浇注时,型腔内易形成还原性气体,析出大量的光亮碳,提高铸件的外观质量。
但挥发分超过40%,型砂发气量增大,铸件易产生气孔、浇不足等缺陷。
因此,挥发分一般在30%-38%。
1.3膨润土选用钠基膨润土。
湿压强度≥120kPa,吸蓝量(g/100g)≥38,粒度过200目≥90%。
2型砂性能质量控制2.1湿压强度如果型砂湿态强度不足,在起模、搬运砂型、下芯、合型等过程中,砂型有可能破损和塌落;浇注时砂型承受不住金属液的冲刷和冲击造成砂孔缺陷,甚至铁液泄漏。
一般用湿压强度来表示型砂湿态强度,一般控制在150-200kPa。
2.2透气性型砂的透气率不可太低以免浇注过程中发生呛火和铸件产生气孔缺陷,但绝不能理解为型砂透气率越高越好。
因为透气率过高表明沙粒间孔隙较大,金属液易于渗透而造成表面粗糙,还可能产生机械粘砂。
湿粘砂的透气率根据浇注金属的种类和温度、铸件的大小和壁厚、造型方法、型砂的发气量大小等决定,一般控制在90-160。
2.3紧实率和含水量紧实率和含水量是衡量型砂综合性能的重要参数。
湿型砂水分一定要适中,否则膨润土未被充分润湿影响混砂,进而导致造型起模困难且砂型发脆易碎、表面耐磨强度低,铸件易产生砂眼和冲蚀缺陷。
一般紧实率控制在32%-40%,最佳34%-38%。
高密度造型用型砂含水量在2.8%-3.8%。
型砂的紧实率/含水量比值一般在10-12。
2.4含泥量高密度造型最理想的铸铁用型砂含泥量(含煤粉)为10%-13%,不应≥14%;理想的旧砂含泥量为8%-11%,不应≥12%。
2.5有效粘土型砂的有效膨润土是指全部仍然具有粘结能力的膨润土。
一般高密度造型的有效膨润土控制在6%-8%。
2.6有效煤粉量(燃损)煤粉高温下气相分解,在砂粒表面沉积形成“光亮碳”,防止铸件表面粘砂,提高铸件表面质量。
如果型砂中有效煤粉含量过高,同时型砂透气性又较差,因型腔内气体量增大,铸件易产生气孔、冷隔、浇不足等缺陷。
为此大多数铸造企业通过测定型砂及附加物的发气量,计算有效煤粉含量,一般控制在3.0%-4.5%。
根据我们的经验并参照其他企业做法,我们将测定有效煤粉含量的方法改为测定型砂挥发分。
挥发分的测定时将样砂放入的坩埚并置于马弗炉内,在649℃下煅烧1h后称重测得。
现场通过型砂挥发分量的变化来控制有效煤粉含量更切合实际,测发气性不是很准确,原因是型砂中有机物(砂芯)等也是发气的,不易分辨。
一般型砂挥发分含量控制在2.0%-3.0%(质量分数)。
2.7粒度型砂粒度直接影响透气性和铸件表面粗糙度,但原砂粒度并不能代表实际型砂中砂子的粒度,因为在铸造过程中部分砂粒可能破碎成细粉,另一部分可能烧结成粗粒,而且不同粗细的砂芯溃碎后也会混入旧砂,因此应将测定含泥量的型砂用筛分法测定粒度,一般型砂粒度AFS值控制在55—65。
2.8回用砂(旧砂)质量控制(a)回用砂的降温:因垂直分型造型线为造型、浇注连续作业,回用砂反复循环使用,其温度的高低将直接影响型砂的温度,从而影响型砂的整体性能:其一,热砂有粘贴在较冷料仓壁的倾向并形成料斗缩管,使系统砂中只有少部分被频繁使用,砂的周转率增加速度,使系统砂中只有少部分被频繁使用,砂的周转率增加速度,使砂温进一步升高;其次,热型砂与模具接触,由于水分凝结而粘结在一起,脱模时造成型腔表面粗糙及砂粒松散;其三,砂温越高,砂型水蒸气压越大,砂型表面的水分蒸发速度越快,风干现象越严重,风干后的型砂强度更低,浇注时铁液冲刷型腔内的风干砂导致铸件产生砂眼缺陷。
因此如何降低回用砂温度,将成为造型线能否生产出优质铸件的关键因素之一。
回用砂温度控制的目的是最终向混砂机输送的旧砂温度应低于45℃。
最佳方法是在落砂机后安装冷却装置(冷却滚筒、沸腾冷却床、双盘冷却器等)。
其中沸腾冷却床冷却效果较好,因回用砂在沸腾冷却床中翻腾与喷水雾同时进行,从而增加了水与砂的接触面积和时间,达到降低砂温之目的。
而传统的做法向传送带上的砂子喷水并不能有效地冷却回用砂,是不可取得。
其原因是,传统方法中的水没有足够的时间与所有砂粒充分接触,并且局部热砂和水的混合物有可能使周围空气的湿度达到饱和,在此情况下不可能将水由液体转变为气体,并把形成的水蒸汽有效排除。
(b)回用砂(旧砂)水分控制:为了更好利用回用砂中的膨润土,回用砂必须在进入混砂机前保持充足的水分,以便膨润土吸收更多的水分,更大发挥回用砂中膨润土的粘结作用以及减少膨润土的加入量。
因此应在砂处理系统中尽可能在早期添加水,混砂前回用旧砂含水量保持在混制型砂水分的70%-80%,使膨润土有充分的膨涨时间,前提是不堵塞任何砂处理设备。
这样,不仅能缩短混砂时间,也可缩小混制后型砂湿压强度的波动范围,混砂效果好。
因此要求回用砂进入旧砂斗中有足够的滞留时间,旧砂中的有效粘土就会部分复水。
(c)回用砂中芯砂的影响:砂芯的加入对湿型砂性能有影响。
铸型浇注后仅有部分砂芯的砂粒表层数值被烧坏,而未被烧掉的仍滞留在型砂中,因砂芯打部分是覆膜砂芯(以树脂为粘结剂),芯砂表面树脂不亲水,补加的湿润膨润土很难与其粘结,导致产生脆性型砂。
脆性型砂不能保证砂型棱角处的质量,而且随着铁液的冲刷极易产生砂眼。
此外,脆性型砂还会给起模带来不良影响。
为了防止芯砂的加入对湿型砂的影响,加入新砂的量应保持在混制沙总量的2%--5%。
并且在安排铸件生产时应注意有芯和无芯产品的合理搭配,尽可能减少型砂中的芯砂量。
3生产应用3.1混砂工艺混砂过程首先应做到将砂、膨润土、水及附加物混和均匀;在揉搓各种材料使粘土膜均匀包覆在砂粒周围。
加料顺序一般是先将干料混合,再加水湿混。
但经观察,型砂经过松砂后总有些像小米粒大小坚硬的砂团包裹在型砂中,其成分实际上就是膨润土和砂子的烧结物和粘土球,该砂团遇水就开。
所以混砂工艺建议改为,加砂后先加水湿混化解粘砂团,再加其它粉料。
旧砂+新砂+水(最好为雾化水);湿混15s后,加膨润土+煤粉+添加剂,混120~150s。
混砂时间不易过长,否则砂子发热降低流动性,强度反而受影响。
3.2造型造型前应先预热模板(尤其是冬天寒冷季节),使其温度高于型砂5℃为宜,起模时不粘模,表面也不干燥,铸型表面光洁。
3.3型砂检测一是严格原材料的进货检验(包括原砂、膨润土、煤粉等);二是加强型砂的在线检测,对型砂性能进行定期检测,及时发现问题并及时解决。
3.4型砂好坏的判断有些企业认为,可以“用湿压强度的值”代替“有效膨润土的值”来决定混砂机中膨润土的添加量,这种观点是不成立的。
简单说,在型砂中的膨润土和死粘土都产生湿压强度,增加死粘土的量,而紧实率不变,湿压强度的值也会增加,所以湿压强度会有误导作用。
在考虑湿压强度的时候还要同时考虑其他性能和有效粘土、含泥量的结果。
“有效粘土含量测试”是唯一能够测定型砂中膨润土含量的方法。
在保证有效粘土含量的前提下,混砂现场应重点控制型砂紧实率,使型砂中的膨润土和水分比例适中,充分发挥膨润土的粘结作用,避免因水分过多使型砂出现自由水的现象。
3.5浇注应快速、高温、连续浇注,快速充型;否则易产生串气、冲砂,形成水分迁移(俗称放炮),造成砂型损坏,出现铸件废品。
4主要缺陷分析与对策4.1砂眼砂眼是由于浇注系统或型内掉有砂粒或因铁液冲刷型壁,零散砂粒掉落引起。
如果型砂混制位置与造型线距离较远,湿砂型在皮带输送过程中,型砂表层脱水强度急剧下降,北方天气干燥季节中“风干”现象更加严重,应引起注意和重视。
另外旧砂反复使用若型砂中的灰分、含泥量过高,将导致型砂韧性低发脆、起模性能差,使砂型的棱角和边缘破碎,引起砂眼缺陷。
防止砂眼措施:①采用优质膨润土,根据季节(干燥、潮湿等)变化,合理控制型砂水分,提高型砂强度;②调解旧砂除尘设备,将旧砂含泥量控制在12%以下,造型处型砂紧实率提高为34%-38%,含水量为3.2%-3.8%,使紧实率与含水量的比例在10—12的范围内;③型砂中加入少量淀粉,提高型砂韧性,降低起模摩擦阻力,增强表面风干强度;④及时调整旧砂中芯砂含量,适当延长混碾时间。
4.2粘砂粘砂是由于铁液渗透铸型而产生的表面缺陷。
采取的对策为:①采用粒度较细、分布适中的原砂,提高型砂的流动性和紧实度(铸型硬度控制在90左右),减少铸型表面的空隙;②使用高效优质煤粉,控制型砂中的有效煤粉含量即挥发分,减少铁液表面氧化及对砂型表面的湿润和渗透;③适当减低浇注温度,减少铁液压力。
4.3球铁件气孔气孔防止:①提高型砂透气性;②控制型砂煤粉加入量及水分和芯砂含量,减少型砂发气量;③模板上合理布置排气槽,利于铸型内气体向外逸出;④适当提高浇注温度(>1380℃)和速度,在浇包液面上撒冰晶石粉。