蜗杆的加工与检测
蜗杆加工工艺技术
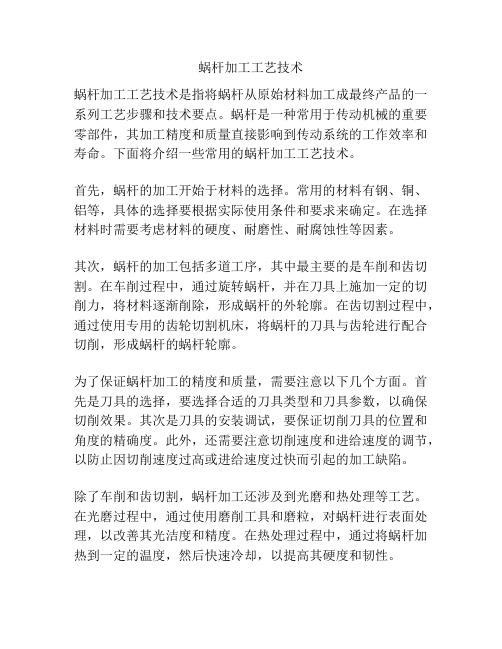
蜗杆加工工艺技术蜗杆加工工艺技术是指将蜗杆从原始材料加工成最终产品的一系列工艺步骤和技术要点。
蜗杆是一种常用于传动机械的重要零部件,其加工精度和质量直接影响到传动系统的工作效率和寿命。
下面将介绍一些常用的蜗杆加工工艺技术。
首先,蜗杆的加工开始于材料的选择。
常用的材料有钢、铜、铝等,具体的选择要根据实际使用条件和要求来确定。
在选择材料时需要考虑材料的硬度、耐磨性、耐腐蚀性等因素。
其次,蜗杆的加工包括多道工序,其中最主要的是车削和齿切割。
在车削过程中,通过旋转蜗杆,并在刀具上施加一定的切削力,将材料逐渐削除,形成蜗杆的外轮廓。
在齿切割过程中,通过使用专用的齿轮切割机床,将蜗杆的刀具与齿轮进行配合切削,形成蜗杆的蜗杆轮廓。
为了保证蜗杆加工的精度和质量,需要注意以下几个方面。
首先是刀具的选择,要选择合适的刀具类型和刀具参数,以确保切削效果。
其次是刀具的安装调试,要保证切削刀具的位置和角度的精确度。
此外,还需要注意切削速度和进给速度的调节,以防止因切削速度过高或进给速度过快而引起的加工缺陷。
除了车削和齿切割,蜗杆加工还涉及到光磨和热处理等工艺。
在光磨过程中,通过使用磨削工具和磨粒,对蜗杆进行表面处理,以改善其光洁度和精度。
在热处理过程中,通过将蜗杆加热到一定的温度,然后快速冷却,以提高其硬度和韧性。
最后,蜗杆加工还需要进行质量检测和表面处理。
通过使用专用的测量工具和设备,对蜗杆的尺寸、形状和表面质量进行检测,以确保其符合设计要求。
在表面处理中,可以进行镀铬、喷涂等处理,以提高蜗杆的耐磨性和耐腐蚀性。
综上所述,蜗杆加工工艺技术包括材料选择、车削、齿切割、光磨、热处理等一系列步骤和技术要点。
通过合理的选择和应用这些技术,可以提高蜗杆的加工精度和质量,从而提高传动系统的工作效率和寿命。
蜗杆加工工艺技术是一项复杂的机械加工工艺,要求加工过程具有高度的精度和稳定性。
下面将继续介绍相关的技术内容。
在蜗杆的加工过程中,车削是一个关键的工艺步骤。
蜗杆的加工与检测
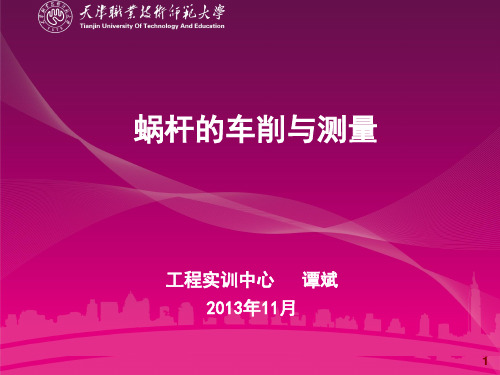
编写数控程序及精度控制
O0009;(第一次精加工) G40G97G99M03S180T11; G00 X50.0 Z5.0; G76 P020130 Q50 R0.03; G76 X39.2 Z-47 P4400 Q2000 F6.283; (G76C2A30X39.2Z-64K4.4U0.03V0.05Q2.0F6.283华中) G00 X150.0; Z200; M05; M30;
2.蜗杆车刀的装夹
(1)水平装刀法 车轴向直廓蜗杆时,用水平装刀法。在装夹车刀时一般用样板找正装夹。 装夹模数较大的蜗杆车刀,容易把车刀装歪。可采用万能量角器来找正车刀 刀尖角位置(见左图)。
(2)垂直装刀法 车削法向直廓蜗杆时,必须把车刀两侧切削刃组成的平面装得与蜗杆齿侧 垂直。 由于蜗杆的导程角比较大,为了改善切削条件和达到垂直装刀要求, 可采用可回转刀杆(见右图)。刀头可相对刀杆回转一个所需的导程角,然后用 螺钉紧固。这种刀杆开有弹性槽,车削时不易产生扎刀。 用水平装刀法车削蜗杆时,由于其中一侧切削刃的前角变得很小,切削不 顺利,所以在粗车轴向直廓蜗杆时,也常采用垂直装刀法。
六、蜗杆的测量方法
蜗杆的主要测量参数有齿距、齿顶圆直径、分度圆直径、法向齿厚。其中 齿顶圆直径可用千分尺测量,齿距由机床传动链保证。 1.分度圆直径的测量 分度圆直径的测量用三针或单针测量,方法与测量梯形螺纹相同(公式不同)。 M=d1+3.924dD-4.316mX d1-分度圆直径,dD=量针直径 dD=1.672 mx 2.法向齿厚的测量 法向齿厚使用齿轮游标卡尺测量(见下图)。适用于精度要求不高的蜗杆。 因图样上一般注明的是轴向齿厚,所以先要把轴向齿厚换算成法向齿厚。
五、蜗杆的车削方法 蜗杆的车削方法和车削梯形螺纹相似。有斜向进刀切削 法、左右切削法、车直槽法和车阶梯槽法。 由于蜗杆的齿距大,齿型深,切削面积大,车削时比梯 形螺纹困难些。一般粗车后留精车余量0.2~0.4mm,在精车 时,采用均匀的单面车削。切削深度不宜过深,否则会发生 “啃刀”现象。所以在车削过程中,必须注意观察切削情况, 控制切削用量,防止“扎刀”。最后再用刀尖角略小于齿型 角的车刀,精车蜗杆底径,把齿型修整清晰,以便保证蜗杆 齿面的表面粗糙度和精度要求。
蜗杆加工工艺路线和论证

蜗杆加工工艺路线和论证蜗杆加工工艺路线:1. 材料选择:蜗杆材料通常选择高强度、高硬度的合金钢、不锈钢、铜合金等材料。
2. 切削加工:蜗杆是通过切削工艺来制造的,常见的切削方式有车削、铣削、磨削、拉削等。
3. 热处理:为了提高蜗杆的强度和耐磨性,通常需要对其进行热处理。
常见的热处理工艺有淬火、回火、渗碳等。
4. 精密加工:蜗杆是精密零件,需要进行精密加工处理。
常见的精密加工方式有磨齿、研磨等。
5. 表面处理:蜗杆表面处理通常采用镀铬、喷涂、阳极氧化等方式,提高其表面硬度和耐磨性。
6. 装配和检验:蜗杆制造完成后,需要进行装配和检验,确保其质量符合要求。
论证:蜗杆是机械传动中常用的零件之一,其加工质量的好坏直接影响到机械传动的稳定性和可靠性。
针对蜗杆的加工工艺路线,需要考虑以下几个方面:1. 材料选择的合理性:蜗杆通常承受较大的负荷,因此需要选择高强度、高硬度的材料。
在选择材料时需要综合考虑其成本、可加工性、耐磨性等因素。
2. 切削加工的精度和表面质量:蜗杆是高精度零件,其几何形状和表面粗糙度直接影响到传动的精度和噪声水平。
因此在切削加工时需要考虑刀具的选择、切削参数的控制、加工过程中的冷却和润滑等因素。
3. 热处理的工艺控制:蜗杆的热处理需要精确控制温度、时间和冷却方式,以保证其组织结构和性能指标符合要求。
4. 精密加工的工艺控制:蜗杆的磨齿和研磨加工需要使用高精密度的设备,并严格控制加工过程中的参数和误差,以确保蜗杆的精度和表面质量符合要求。
5. 表面处理的效果评价:蜗杆表面处理需要注意其基材与涂层之间的黏着度和密合性,以及涂层的厚度和硬度等因素。
需要进行表面质量的评价和质量检查,确保蜗杆表面的质量符合要求。
6. 装配和检验的质量控制:在蜗杆的装配和检验过程中,需要严格控制加工误差和装配偏差,保证蜗杆的传动精度和噪声水平符合要求,并进行可靠性测试。
蜗轮蜗杆的工艺性分析
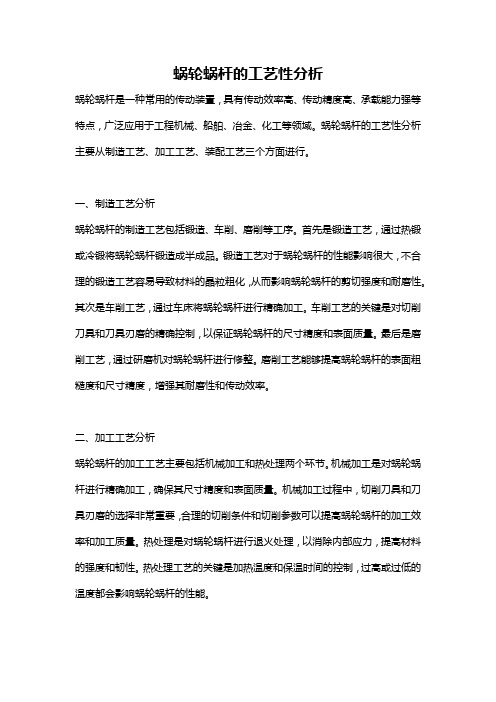
蜗轮蜗杆的工艺性分析蜗轮蜗杆是一种常用的传动装置,具有传动效率高、传动精度高、承载能力强等特点,广泛应用于工程机械、船舶、冶金、化工等领域。
蜗轮蜗杆的工艺性分析主要从制造工艺、加工工艺、装配工艺三个方面进行。
一、制造工艺分析蜗轮蜗杆的制造工艺包括锻造、车削、磨削等工序。
首先是锻造工艺,通过热锻或冷锻将蜗轮蜗杆锻造成半成品。
锻造工艺对于蜗轮蜗杆的性能影响很大,不合理的锻造工艺容易导致材料的晶粒粗化,从而影响蜗轮蜗杆的剪切强度和耐磨性。
其次是车削工艺,通过车床将蜗轮蜗杆进行精确加工。
车削工艺的关键是对切削刀具和刀具刃磨的精确控制,以保证蜗轮蜗杆的尺寸精度和表面质量。
最后是磨削工艺,通过研磨机对蜗轮蜗杆进行修整。
磨削工艺能够提高蜗轮蜗杆的表面粗糙度和尺寸精度,增强其耐磨性和传动效率。
二、加工工艺分析蜗轮蜗杆的加工工艺主要包括机械加工和热处理两个环节。
机械加工是对蜗轮蜗杆进行精确加工,确保其尺寸精度和表面质量。
机械加工过程中,切削刀具和刀具刃磨的选择非常重要,合理的切削条件和切削参数可以提高蜗轮蜗杆的加工效率和加工质量。
热处理是对蜗轮蜗杆进行退火处理,以消除内部应力,提高材料的强度和韧性。
热处理工艺的关键是加热温度和保温时间的控制,过高或过低的温度都会影响蜗轮蜗杆的性能。
三、装配工艺分析蜗轮蜗杆的装配工艺主要包括配合间隙的设计和装配精度的控制。
蜗轮蜗杆的配合必须满足一定的间隙要求,既不能过大以影响传动精度,也不能过小以增加传动功率损失。
装配过程中,需要对蜗轮蜗杆的尺寸精度和运动配合进行严格控制,以保证蜗轮蜗杆装配后的工作性能。
综上所述,蜗轮蜗杆的工艺性分析涉及制造工艺、加工工艺和装配工艺三个方面。
制造工艺的良好选择和控制能够提高蜗轮蜗杆的性能和精度,加工工艺的优化能够提高蜗轮蜗杆的加工效率和质量,装配工艺的精确控制能够确保蜗轮蜗杆的工作性能。
蜗轮蜗杆的工艺性分析对于提高蜗轮蜗杆的传动效率和使用寿命具有重要意义,也对推动相关行业的发展起到积极的推动作用。
蜗杆加工程序
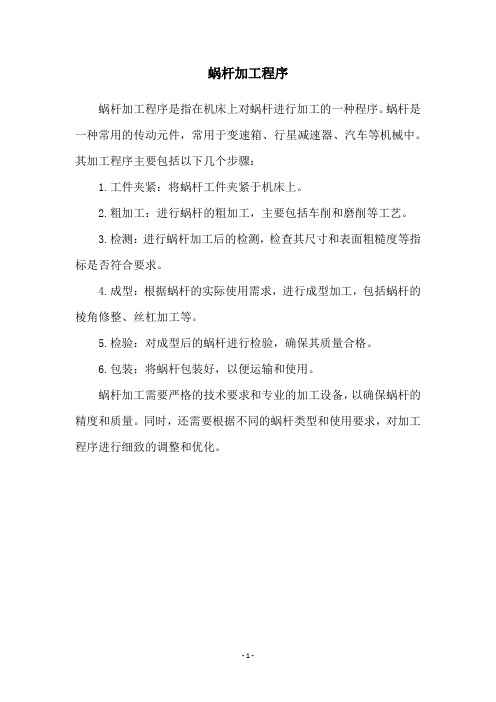
蜗杆加工程序
蜗杆加工程序是指在机床上对蜗杆进行加工的一种程序。
蜗杆是一种常用的传动元件,常用于变速箱、行星减速器、汽车等机械中。
其加工程序主要包括以下几个步骤:
1.工件夹紧:将蜗杆工件夹紧于机床上。
2.粗加工:进行蜗杆的粗加工,主要包括车削和磨削等工艺。
3.检测:进行蜗杆加工后的检测,检查其尺寸和表面粗糙度等指标是否符合要求。
4.成型:根据蜗杆的实际使用需求,进行成型加工,包括蜗杆的棱角修整、丝杠加工等。
5.检验:对成型后的蜗杆进行检验,确保其质量合格。
6.包装:将蜗杆包装好,以便运输和使用。
蜗杆加工需要严格的技术要求和专业的加工设备,以确保蜗杆的精度和质量。
同时,还需要根据不同的蜗杆类型和使用要求,对加工程序进行细致的调整和优化。
- 1 -。
蜗杆的加工分析

中图分类号 : TB
文献标识码 : A
文章 编 号 :6 23 9 (O O 2—3 60 17 —1 8 2 L ) 00 1 —1 () 车螺距大于 4 2粗 mm( > 4 的梯 形 螺 纹 时 可 采 用 “ P ) 左 右切削法” “ 直槽 法” 为防 止三个 切 削刃 同时切 削 , 或 车 。 导
1 蜗 杆
蜗杆 、 蜗轮组成 的蜗 轮副常 用在作 减速运 动 的传动 中 ,
蜗杆 和 蜗 轮 啮 合 时 两 轴 空 间 交 错 成 9 。 O。
致 切 削 力 过 大 而 产 生 “ 动 ” “ 刀 现 象 ” 应 采 用 左 右 切 振 或 扎 , 削法。车直槽法 : 由于 左 右 切 削 法 操 作 不 方 便 , 车 时 可 用 粗 车槽 刀 采 用 直 进 法 在 工 件 上 车 出 螺 旋 直 槽 , 后 用 梯 形 螺 然
杆 ( N 蜗 杆 ) Z 。
() 向直廓蜗杆在 过蜗杆 轴线 的截 面内齿形 为直 线 , 1轴 在垂直于轴线 的截 面 内齿形 为 阿基 米德 螺旋 线 , 以轴 向 所
直廓蜗杆又叫阿基米 德蜗杆 。 ( ) 向 直 廓 蜗 杆 在 蜗杆 的 法 向 截 面 ( 直 于 齿 面 的 截 2法 垂
“ 梯 槽 ” 方 法 。具 体 车 削 步 骤 是 先 用 刀 头 宽 度 小 于 P 2 阶 的 / 的车槽刀 、 用车 直 槽 的方 法 车 至 近 中径 处 , 用 刀 头 宽 度 略 再
杆 按 齿 形 分 又 分 为 轴 向 直 廓 蜗 杆 ( A 蜗 杆 ) 法 向 直 廓 蜗 Z 和
纹 车刀粗车两侧 面。
2 蜗 杆 的 种 类
蜗杆精度国标

蜗杆精度国标摘要:一、蜗杆精度国标概述二、蜗杆精度国标的主要内容1.蜗杆参数2.蜗杆精度等级3.蜗杆检测方法4.蜗杆精度国标在我国的应用三、蜗杆精度国标的意义和价值四、结论与展望正文:一、蜗杆精度国标概述蜗杆精度国标(GB/T 10085-1998)是我国针对蜗杆传动精度制定的技术标准。
蜗杆传动是一种常见的减速传动方式,广泛应用于各类机械设备中。
蜗杆精度国标旨在规范蜗杆的精度等级、检测方法以及应用范围,以确保蜗杆传动的性能和可靠性。
二、蜗杆精度国标的主要内容1.蜗杆参数蜗杆精度国标对蜗杆的参数进行了详细的规定,包括蜗杆的模数、压力角、蜗杆齿形、蜗杆材料等。
这些参数是蜗杆设计、制造和选用的重要依据。
2.蜗杆精度等级蜗杆精度国标将蜗杆的精度等级分为0、1、2、3、4、5级。
精度等级越高,蜗杆的传动精度越高,但制造和加工难度也越大。
根据实际应用需求,选择合适精度等级的蜗杆至关重要。
3.蜗杆检测方法蜗杆精度国标规定了蜗杆的检测方法,包括光学投影仪、坐标测量仪、蜗杆检测仪等。
这些检测方法为蜗杆精度的检验提供了有效手段。
4.蜗杆精度国标在我国的应用蜗杆精度国标在我国得到了广泛的应用,对蜗杆传动的研发、生产和应用起到了良好的指导作用。
符合国标要求的蜗杆传动产品,能够在保证性能的同时,提高我国机械行业的整体水平。
三、蜗杆精度国标的意义和价值蜗杆精度国标对蜗杆传动的精度、参数和检测方法进行了规范化,有助于提高蜗杆传动的质量,降低故障率,延长使用寿命。
同时,蜗杆精度国标还有利于推动我国蜗杆传动技术的发展,提高我国机械产品的竞争力。
四、结论与展望总之,蜗杆精度国标在规范蜗杆传动领域发挥了重要作用。
随着科技的不断进步和市场需求的提高,蜗杆精度国标也将不断优化和完善,以适应新时代的发展需求。
蜗杆轴零件的加工工艺

蜗杆轴零件的加工工艺1. 简介蜗杆轴是一种常见的传动装置,在机械设备中用于实现传动和变速功能。
蜗杆轴零件的加工工艺对于其质量和性能起着决定性的作用。
本文将介绍蜗杆轴零件的加工工艺流程以及相关注意事项。
2. 加工工艺流程2.1 材料准备蜗杆轴常用的材料有钢、铸铁等,选择合适的材料对于提高蜗杆轴的耐磨性和强度非常重要。
在加工工艺中,需要根据设计要求选择相应的材料,并进行材料预处理。
2.2 切削加工蜗杆轴的加工通常包括车削、铣削、钻削等切削加工过程。
在切削加工中,需要根据蜗杆轴的尺寸和形状要求,采用适当的切削工艺和工具进行加工。
切削加工时,需确保加工精度和表面质量,避免产生划痕和变形等缺陷。
2.3 热处理蜗杆轴常常需要进行热处理,以提高其硬度和耐磨性。
常用的热处理方法包括淬火、回火和表面渗碳等。
在热处理中,需要控制好加热温度和保温时间,以及冷却速度,以确保蜗杆轴在热处理后具有良好的性能。
2.4 修磨和校验蜗杆轴的表面精度和几何形状对于传动的性能有很大影响。
因此,在加工过程中,需要进行修磨和校验工序。
修磨过程中使用砂轮或砂带进行研磨,校验过程中则使用测量工具如千分尺、游标卡尺等对蜗杆轴进行检测和校正。
2.5 表面处理为了提高蜗杆轴的耐腐蚀性和摩擦性能,常常需要对其进行表面处理。
常见的表面处理方法有镀铬、电镀、喷涂、氮化等。
选择合适的表面处理方法,可以大幅度提高蜗杆轴的使用寿命和传动效率。
3. 注意事项在蜗杆轴零件的加工过程中,还需要注意以下几点:3.1 安全操作加工过程中,需要严格遵守安全操作规程,使用合适的防护设备,避免事故发生。
同时,要保证加工环境良好,防止灰尘、杂质等对加工质量的影响。
3.2 加工精度蜗杆轴是一种高精度零件,加工过程中需严格控制尺寸公差和表面粗糙度。
需要使用合适的切削工具和设备,保证加工精度符合设计要求。
3.3 耐磨性和润滑性蜗杆轴在工作过程中承受较大的摩擦和磨损,因此在加工过程中要注意提高其耐磨性和润滑性。
- 1、下载文档前请自行甄别文档内容的完整性,平台不提供额外的编辑、内容补充、找答案等附加服务。
- 2、"仅部分预览"的文档,不可在线预览部分如存在完整性等问题,可反馈申请退款(可完整预览的文档不适用该条件!)。
- 3、如文档侵犯您的权益,请联系客服反馈,我们会尽快为您处理(人工客服工作时间:9:00-18:30)。
工作任务
相关理论知识
一.蜗杆概述 1.蜗杆的作用及种类 蜗杆、蜗轮传动常用于作减速运动的传动机构中。常用的蜗杆有米制蜗杆(模 数),齿形角为20º(牙形角40º);英制蜗杆(径节),齿型角为14.5º(牙形角 29º),我国采用米制蜗杆。
2.蜗杆的齿形 常用的蜗杆齿形按齿廓形状可分为轴向直廓蜗杆和法向直廓蜗杆两种。
六、蜗杆的测量方法
蜗杆的主要测量参数有齿距、齿顶圆直径、分度圆直径、法向齿厚。其中 齿顶圆直径可用千分尺测量,齿距由机床传动链保证。
1.分度圆直径的测量
分度圆直径的测量用三针或单针测量,方法与测量梯形螺纹相同(公式不同)。
M=d1+3.924dD-4.316mX dD=1.672 mx
d1-分度圆直径,dD=量针直径
二.蜗杆技术工艺要求 1.蜗杆的齿距必须等于蜗轮齿距。 2.法向或轴向齿厚要符合要求。 3.齿型两侧面表面粗糙度要小。 4.蜗杆径向跳动不得大于允许范围。 三、工件的装夹
粗车时为了提高工件的装夹刚度,应尽量缩短工件的长度。 最好把工件的一端夹在单动卡盘内,另一端用顶尖支顶。
精车时,应注意工件的同轴度,工件要以两顶尖孔定位装夹, 以保证加工精度。 四、蜗杆车刀及其装夹
向齿厚≈法向齿厚)
• 实际加工时,在一次循环结束后,用三针测量实 测M值,计算出刀具Z向偏置量,然后在刀长补 偿或磨耗存贮器中设置Z向刀偏量,再次用G76 循环加工就能一次性精确控制中径等参数值。
编写数控程序及精度控制
O0009;(第一次粗加工) G40G97G99M03S180T11; G00 X50.0 Z5.0; G76 P020130 Q50 R0.03; (设定精加工两次,精加工 余量为0.1mm,倒角量等于0.1倍螺距,牙型角为30°, 最小切深为0.05mm。) G76 X39.2 Z-64 P4400 Q500 F6.283;(设定螺纹高为 4.4mm,第一刀切深为0.5mm。) (G76C2A30X39.2Z-47K4.4U0.03V0.05Q0.5F6.283华中) G00 X150.0; Z200; M05; M30;
用水平装刀法车削蜗杆时,由于其中一侧切削刃的前角变得很小,切削不 顺利,所以在粗车轴向直廓蜗杆时,也常采用垂直装刀法。
五、蜗杆的车削方法
蜗杆的车削方法和车削梯形螺纹相似。有斜向进刀切削 法、左右切削法、车直槽法和车阶梯槽法。
由于蜗杆的齿距大,齿型深,切削面积大,车削时比梯 形螺纹困难些。一般粗车后留精车余量0.2~0.4mm,在精车 时,采用均匀的单面车削。切削深度不宜过深,否则会发生 “啃刀”现象。所以在车削过程中,必须注意观察切削情况, 控制切削用量,防止“扎刀”。最后再用刀尖角略小于齿型 角的车刀,精车蜗杆底径,把齿型修整清晰,以便保证蜗杆 齿面的表面粗糙度和精度要求。
蜗杆的车削与测量
工程实训中心 谭斌 2013年11月
1
学习目标
知识目标 ◎了解蜗杆的作用、种类、齿形。 ◎蜗杆主要参数的名称、符号、计算公式。 ◎了解蜗杆的技术要求,学会确定蜗杆的参数。 ◎了解蜗杆车刀的几何形状和角度要求。
技能目标 ◎掌握轴向直廓蜗杆车刀的刃磨方法。 ◎掌握单头轴向直廓蜗杆的车削方法。 ◎掌握轴向直廓蜗杆的多种测量方法。
2.蜗杆车刀的装夹
(1)水平装刀法 车轴向直廓蜗杆时,用水平装刀法。在装夹车刀时一般用样板找正装夹。 装夹模数较大的蜗杆车刀,容易把车刀装歪。可采用万能量角器来找正车刀
刀尖角位置(见左图)。
(2)垂直装刀法 车削法向直廓蜗杆时,必须把车刀两侧切削刃组成的平面装得与蜗杆齿侧
垂直。 由于蜗杆的导程角比较大,为了改善切削条件和达到垂直装刀要求, 可采用可回转刀杆(见右图)。刀头可相对刀杆回转一个所需的导程角,然后用 螺钉紧固。这种刀杆开有弹性槽,车削时不易产生扎刀。
蜗杆车刀与梯形螺纹车刀基本相同,但因蜗杆的导程较大,
所以在刃磨蜗杆车刀时,更应考虑导程角对车刀前角和后角的 影响,另外蜗杆的精度较高,所以一般低速车削,用高速钢车刀。
1.高速钢车刀蜗杆车刀及几何角度
蜗杆粗车刀
蜗杆精车刀
蜗杆车刀的角度
a)刀尖角:粗车刀刀尖角小于蜗杆牙型角;精车刀刀尖角应等于蜗杆牙型角。 b)刀头宽度:刀头宽度应小于齿根槽宽。 c)纵向前角:粗车刀一般为15º左右;精车刀为了保证牙型角正确,前角应等于0º。 d)纵向后角:一般为6º~8º。 e)两侧刀刃后角:考虑蜗杆旋向和导程角。右旋车刀:左侧后角为(3º~5º)+γ, 右侧后角为(3º~5º)—γ。左旋车刀则相反。 f)刀尖适当倒圆。
轴向直廓蜗杆又称为ZA蜗杆,这种蜗杆的轴向齿廓为直线,而在垂直于轴线 的截面内,齿形是阿基米德螺线,所以又称为阿基米德蜗杆。
法向直廓蜗杆又称为ZN蜗杆,这种蜗杆在垂直于齿面的法向截面内,齿 廓为直线,所以又称为法向直廓蜗杆。
3.蜗杆主要参数的名称、符号、计算公式及参数确定
蜗杆参数计算
轴向齿距:PX=π*mx=3.1416×2=6.2832mm 导程: PZ=Z1*π*mx=3.1416×2=6.2832mm 齿顶高:ha=mx=2mm 齿根高:hf=1.2mx=1.2×2=2.4mm 全齿高:h=2.2mx=2.2×2=4.4mm 齿顶圆直径:da=d1+2mx=44+2×2=48mm 齿根圆直径:df=d1-2.4mx=44-2.4×2=39.2mm 轴向齿顶宽:Sa=0.843mx=0.843×2=1.686mm 轴向齿根槽宽:ef=0.697mx=0.697×2=1.394mm 轴向齿厚:Sx=Px/2=π*mx/2=3.1416×2/2=3.142mm 导程角:tanr=PZ/π*d1=6.2832/3.1416×44=2.6023° 法向齿厚:Sn=Pz/2*cosr=6.2832/2×cos(2.6023)=3.145mm
2.法向齿厚的测量
法向齿厚使用齿轮游标卡尺测量(见下图)。适用于精度要求不高的蜗杆。
因图样上一般注明的是ຫໍສະໝຸດ 向齿厚,所以先要把轴向齿厚换算成法向齿厚。
计算Z向刀具偏置值
• Z向偏置量的计算方法如下:三针测量 • 设M实测- M理论=δ • Z向偏置量=0.3636δ 、δ = 2.75*Z向偏置量(轴