民用飞机复合材料结构孔隙率的影响及检测
飞机复合材料结构损伤与检测—复合材料结构损伤检测方法

最小检测区域原则
红外成像检测法特点
红外线照相检测法也是一种非接触式检测方法。它具 有灵敏度高、检测效率高和缺陷显示直观等优点,可用于 检测复合材料结构件的脱胶、分层以及蜂窝夹芯结构中的 积水。
应用
检测雷达罩积水
1
检测出蜂窝夹芯结构的积水区域
1
复合材料面板与蜂窝芯脱胶
目视检测
目视检测 ( Visual inspection)
如果将WP-632连接到WP-632M上, WP-632检测数据可详细地显示 在WP-632M的液晶显示器上并存储。通过数据线,还可将检测数据传送到 个人电脑。
红外成像检测法
红外成像检测法 Infrared thermography
红外线成像检测法利用被检物体不连续性缺陷区域 热传导性能不同导致的物体表面红外辐射能力差异, 通过红外摄像将红外辐射差异转化为可见的温度图像, 从而确定物体损伤或缺陷。
“啄木鸟”检测仪
日本MITSUI公司生产的“WP-632/632M 型啄木鸟(wood pecker)” 是一种带有声光报警、操作简便的分层敲击检测仪,如图5.9示。其工作原 理为:首先采用标准试块或选择被检查部件符合粘接质量要求区域作为检测 基准,然后使用WP-632敲击被检测区域并通过声音差异分析判断是否存在 分层。如果发现分层,检测仪的“红色” 指示灯亮并有报警声。
敲击法
敲击法(TAP TEST)
敲击法是一种采用硬币、专用敲击棒、敲击锤或者敲击仪等轻轻 敲击复合材料结构表面,通过辨听敲击构件时的声音变化来确定 损伤的检测方法。
复合材料超声检测技术概述及应用
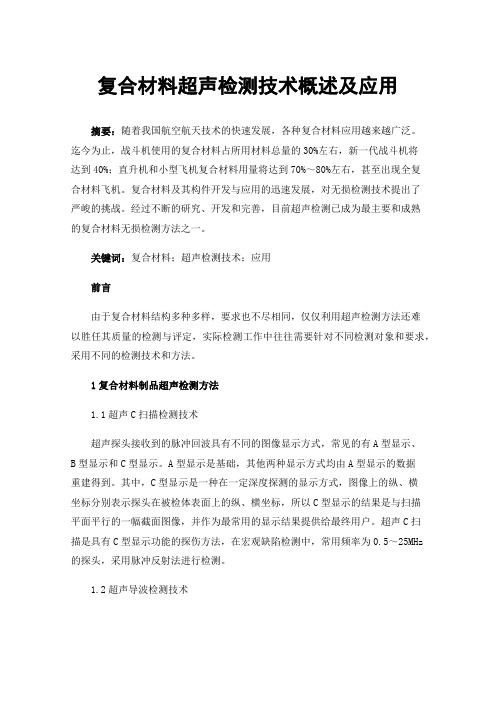
复合材料超声检测技术概述及应用摘要:随着我国航空航天技术的快速发展,各种复合材料应用越来越广泛。
迄今为止,战斗机使用的复合材料占所用材料总量的30%左右,新一代战斗机将达到40%;直升机和小型飞机复合材料用量将达到70%~80%左右,甚至出现全复合材料飞机。
复合材料及其构件开发与应用的迅速发展,对无损检测技术提出了严峻的挑战。
经过不断的研究、开发和完善,目前超声检测已成为最主要和成熟的复合材料无损检测方法之一。
关键词:复合材料;超声检测技术;应用前言由于复合材料结构多种多样,要求也不尽相同,仅仅利用超声检测方法还难以胜任其质量的检测与评定,实际检测工作中往往需要针对不同检测对象和要求,采用不同的检测技术和方法。
1复合材料制品超声检测方法1.1超声C扫描检测技术超声探头接收到的脉冲回波具有不同的图像显示方式,常见的有A型显示、B型显示和C型显示。
A型显示是基础,其他两种显示方式均由A型显示的数据重建得到。
其中,C型显示是一种在一定深度探测的显示方式,图像上的纵、横坐标分别表示探头在被检体表面上的纵、横坐标,所以C型显示的结果是与扫描平面平行的一幅截面图像,并作为最常用的显示结果提供给最终用户。
超声C扫描是具有C型显示功能的探伤方法,在宏观缺陷检测中,常用频率为0.5~25MHz的探头,采用脉冲反射法进行检测。
1.2超声导波检测技术导波是指由于介质边界的存在而产生的波,在介质尺寸跟声波波长可比的情况下,介质中的波以反射或折射的形式与边界发生作用并多次来回反射,发生纵波与横波间的模态转换,形成复杂的干涉,呈现出了多种传播形式,形成各种类型的导波。
导波本质上还是由纵波、横波等基本类型的超声波以各种方式组成的。
导波的主要特性包括频散现象、多模式和传播距离远。
超声导波检测是一种快速大范围的初步检测方法,一般只能对缺陷定性,而定量是近似的,对可疑部位仍需要采用其他检测方法才能作出最终的评估。
1.3空气耦合超声检测技术传统超声无损检测方法由于需要使用耦合剂,无法适用于某些航空航天用复合材料构件的检测,主要原因是耦合剂会使试样受潮或变污,且有可能渗入损伤处,这会严重影响构件的力学强度和稳定性。
基于飞机设计的复合材料结构孔隙研究

基于飞机设计的复合材料结构孔隙研究作者:罗鹏殷跃洪冯万喜肖军来源:《工业设计》2018年第07期摘要:本文概述了复合材料结构孔隙率的形成机理,探讨了孔隙率与复合材料力学特性的内在规律,阐述了孔隙率的检测方法并提出了孔隙率的控制措施以及未来的研究方向。
关键词:孔隙率;形成机理;力学特性;检测方法中国分类号:TB472 文献标识码:A文章编码:1672-7053(2018}07-0155-02先进复合材料因具有轻质高强的特性使其在飞机结构上被广泛应用,其占飞机机体结构重量的比重不断提高,从AirbusA380的22%到Boeing787的50%,再到A350的52%。
但复合材料领域仍存在诸多问题有待研究和解决,比如孔隙率。
不同标准对孔隙有着不同的定义,但本质含义基本一致,即复合材料中内部尺寸较小的孔洞(可能是空气、挥发物或空穴),通常用单位体积所合孔隙的百分比来表示,也称为孔隙率。
孔隙的线性尺寸可能从几微米到几百微米不等,其跨度很大。
在Boeing的规范中,一簇密集孔穴缺陷中只要最大的直径小于6.35mm,该簇孔即被视为孔隙。
孔隙是复合材料构件内部最常见且无法避免的缺陷。
即使较小的孔隙也会对材料的性能产生不利影响,零件结构强度降低,最终危害飞行安全。
为此对复合材料构件生产中孔隙的形成机理及与复合材料力学性能的内在关系进行研究,进而提出有效的孔隙率控制措施,这将具有重要的指导意义。
1 孔隙的形成机理目前在航空制造领域内,复合材料构件的生产工艺主要是采用预浸料铺贴后热压罐或固化炉成型及液体成型,但无论何种方式,固化过程中的孔隙均是无法避免的,通常存在层间界面处或纤维束之间。
产生这一原因主要有以下几点:1)固化过程中树脂与纤维浸润性较差,纤维不能完全被浸润,空气难以挤压排出,从而产生孔隙,这对于树脂流动性差或纤维密集的预浸料易于产生孔隙。
该孔隙一般平行于纤维轴向,形状为柱形,并且孔隙率较大。
2)在固化过程中复合材料产生的挥发性组份主要来源包括树脂中或浸渍纤维用的有机溶剂;储存和运输过程中吸收的水份;树脂在成型过程中释放的挥发物以及预浸料在铺贴过程中裹入的气泡。
复合材料成型缺陷分析与控制

复合材料成型缺陷分析与控制在现代工业领域中,复合材料因其优异的性能,如高强度、高刚度、良好的耐腐蚀性等,被广泛应用于航空航天、汽车、船舶、体育器材等众多领域。
然而,复合材料的成型过程并非一帆风顺,常常会出现各种缺陷,这些缺陷不仅影响产品的外观质量,更可能严重削弱其性能和可靠性,甚至导致产品报废。
因此,对复合材料成型缺陷进行深入分析,并采取有效的控制措施,具有至关重要的意义。
一、复合材料成型缺陷的类型及成因(一)孔隙孔隙是复合材料成型中最常见的缺陷之一。
它表现为材料内部存在的微小空洞,其成因较为复杂。
树脂浸润纤维不充分、固化过程中产生的挥发物无法及时排出、成型压力不足等都可能导致孔隙的产生。
孔隙的存在会降低材料的强度和刚度,影响其耐疲劳性能和耐腐蚀性。
(二)分层分层指的是复合材料层间的分离现象。
通常是由于层间结合力不足、成型过程中的冲击或振动、树脂固化不均匀等原因引起的。
分层会显著降低复合材料的层间强度,使其承载能力大幅下降。
(三)纤维弯曲和断裂在成型过程中,纤维可能会发生弯曲和断裂。
这可能是由于纤维在铺放过程中受到不当的张力或压力,或者在模具中流动的树脂对纤维产生了剪切作用。
纤维的弯曲和断裂会直接影响复合材料的力学性能,使其强度和刚度达不到设计要求。
(四)树脂富脂和贫脂区树脂分布不均匀会导致富脂区和贫脂区的出现。
富脂区树脂含量过高,会增加材料的重量和成本,同时降低其强度;贫脂区则由于树脂不足,无法充分浸润和保护纤维,影响复合材料的性能和耐久性。
(五)表面缺陷表面缺陷包括表面粗糙、凹坑、鼓包等。
这可能是由于模具表面不光滑、脱模剂使用不当、树脂固化收缩不均等原因造成的。
表面缺陷不仅影响产品的外观质量,还可能成为应力集中点,降低材料的使用寿命。
二、复合材料成型缺陷的影响(一)力学性能下降孔隙、分层、纤维弯曲和断裂等缺陷都会导致复合材料的力学性能,如强度、刚度、韧性等下降。
这使得复合材料在使用过程中无法承受预期的载荷,增加了失效的风险。
复合材料结构中的缺陷检测与评估

复合材料结构中的缺陷检测与评估第一章绪论复合材料是由两个或更多不同材料的组合物构成的新材料。
由于其高强度、高刚度和低密度等优点,复合材料广泛应用于航空、航天、汽车、建筑等领域。
在复合材料的生产和应用过程中,缺陷问题是一个重要的技术难题。
如何及早检测和评估复合材料结构中的缺陷,对于确保其性能和安全具有重要的意义。
本章将介绍复合材料的基本概念和结构特点,以及复合材料结构中常见的缺陷类型和成因。
第二章复合材料结构中的缺陷类型复合材料结构中的缺陷可以根据其类型分为以下几类:1.孔隙:孔隙是指复合材料中没有填充材料的空洞或气泡。
这种缺陷通常由于材料填充不均匀、挤压不当等原因造成。
2.夹杂物:夹杂物是指复合材料中存在的杂质或异物。
这些杂质或异物会削弱复合材料的力学性能。
3.毛刺:毛刺是指复合材料表面存在的尖锐物质。
这些毛刺容易导致应力集中,从而导致复合材料的破坏。
4.裂纹和缺陷:裂纹和缺陷是指复合材料中存在的裂纹、裂口或缺损。
这种缺陷通常是由于材料受力过大或者材料本身缺陷造成的。
第三章复合材料结构中的缺陷评估方法为了及早发现和评估复合材料结构中的缺陷,需要采用一些有效的检测方法。
常用的检测方法包括:1.光学检测:光学检测能够用于检测复合材料表面的缺陷,如毛刺和裂纹等。
光学检测的主要优点是快速、非接触和高分辨率。
2.超声波检测:超声波检测能够用于检测更深层的缺陷,如孔隙和夹杂物等。
超声波检测的主要优点是高灵敏度和非破坏性。
3.X射线检测:X射线检测能够用于检测复合材料内部的缺陷,如裂纹和缺损等。
X射线检测的主要优点是高分辨率和无损伤。
4.热红外检测:热红外检测能够用于检测复合材料表面的缺陷,如毛刺和裂纹等。
热红外检测的主要优点是快速、非接触和高分辨率。
第四章复合材料结构中缺陷修复方法如果复合材料结构中存在缺陷,需要及时采取修复措施,以确保其性能和安全。
常用的修复方法包括:1.填充:通过填充材料来填补孔隙或夹杂物等缺陷。
孔隙率超声检测技术在复合材料中的应用

递数据。以后就可直接采用US59校准仪器,
以便取得并建立与法宇航相一致的评定基准。并
按规定的检测技术规范实施孔隙率的测量。 从而达到检测结果能以法宇航的标准进行等效评 定的目的。 5.2但就目前的现状,由于还没有绘制出分贝衰减值与孔隙率的对应关系典线(或数据), 目前我们仅仅是根据标准中规定的用(中心频率lO~91z的宽频带)双探头超声穿透法检测时, 最大可接收孔隙率:2%,相当于-6分贝的衰减,这一要求对复合材料进行孔隙率的质量控制。 对于每一衰减分贝值所对应的孔隙率的含量,尚需做更多的试验。 5.3孔隙率的含量对超声波的衰减有着不同影响。此方法的建立对于其它类型的复合材料的 超声波衰减与孔隙率的相应关系也具有指导意义。
和
图2(a)可以看出当孔隙率较低时,孔隙的尺寸较小而且它们彼此之间相互分离;而当孔隙率 较大时,孔隙的长度均较大而且它们之间的距离也比较近,有时会连在一起,这些较大的孔 隙对孔隙率的大小起了决定性的作用。
4
孔隙率标准的建立
超声检测孔隙率的评定基准是个关键问题,即使是作为抽样破坏性检测孔隙率,也仍然
存在评定基准的标准化的问题。采取“逐次逼近”法建立孔隙率为o%的评定基准的方法,即 按法宇航标准要求,在实施检测的产品上,于相同N层的区域内寻找对超声吸收最小的部位 作为基准。而每次对送检产品的检测都是取包括本次之前所有产品上所能得到的最小吸收界 限作为评定基准,这样经过多次、火量产晶检测的统计逼近,最终达到或趋近一个最小的吸 收极限,这个最小的吸收极限就定义为理论上的孔隙率为O%的基准。 我们是以制造出来的碳纤维复合材料层压板结构最好对比试块,且与US59对比试块进行 比较分析,并在理论上就把US59对比试块当作孔隙率为096的标准试样,用来校准系统灵敏度。 但这并不是一个很严密的定量条件,所谓孔隙率为O%实际上是不存在的,只不过将可忽略的 孔隙率(小于0.5%)在理论上看作为o%而已,以便建立基准波高值,从而解决校准检测系统 灵敏度与孔隙率评定的需要。在实际检测过程中我们是以一dB表示相对孔隙率含量值,并通过 A/D转换按2dB量化,分8级色彩记录C扫描图像来代表相应量化界限范围内的孔隙率。但 要想针对测试的衰减-dB值找出具体对应的孔隙率含量,则需通过人量的试验测定出以Pv/一dB 表示复合材料层压板的内部孔隙率值Pv的关系曲线。应当指出,随选定校准试块的质量不同, 其测试结果是会有差异的。
复合材料孔隙率的超声检测方法探讨

复合材料孔隙率的超声检测方法探讨姓名:学号:摘要: 简单介绍了复合材料中孔隙的形成原因, 叙述了孔隙率对材料机械性能的影响, 综述了孔隙率测量的超声无损检测方法现状, 说明了目前各种检测方法的检测效果和优缺点, 并对将来孔隙率的检测方法作了展望。
关键词: 孔隙率; 复合材料; 超声检测孔隙是复合材料最常见的微小缺陷。
孔隙的出现会降低材料的性能, 如层间剪切强度, 纵向和横向的弯曲强度和拉伸强度、抗疲劳性以及高温下的抗氧化性能等。
即使孔隙含量很小, 也会对材料的寿命造成很大的影响[1- 4], 因此孔隙率的检测对复合材料的性能保证非常重要。
目前比较常用的无损检测方法是超声波检测, 国内外已对此种检测方法做了不少的研究, 并取得了一定的进展。
1 孔隙的形成及对材料的影响由于复合材料比较复杂的加工工艺, 完全没有孔隙的复合材料是没有的。
一般来说, 空隙的形成有两种原因[5]: 一是制作过程中树脂未完全浸润或叠层间空气未完全排除, 造成空气存留在其中, 这种原因形成的孔隙一般数量较多, 形状是扁圆形或拉长形; 二是由于工艺过程中产生挥发性物质, 这时形成的孔隙一般呈圆形, 孔隙数量较少, 孔隙的尺寸一般较小, 直径为几微米到几百微米。
评定孔隙对材料影响程度大小的定量指标是孔隙率, 有面积孔隙率和体积孔隙率两种定义。
面积孔隙率是单位面积所含孔隙的面积的百分比, 体积孔隙率是单位体积所含孔隙的体积百分比。
具体根据实际检测技术的不同采取不同的指标描述。
复合材料的机械性能对孔隙十分敏感。
ALmei2da[6]等人用实验证明, 即使孔隙的存在对材料的静态强度只有中等程度的影响, 它却可以使疲劳寿命显著下降。
研究指出, 孔隙率在0% ~ 5% , 每增加1%, 其层间剪切强度平均下降7% 左右, 其他性能如弯曲强度以10% 左右的比例下降, 弯曲模量则以5% 左右的比例下降。
不过孔隙的存在并不是对材料都具有有害的影响。
飞机复合材料结构损伤和检测维修方法分析
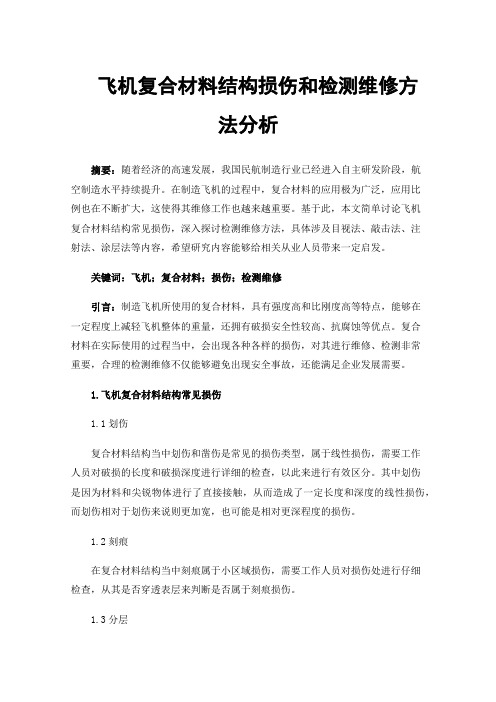
飞机复合材料结构损伤和检测维修方法分析摘要:随着经济的高速发展,我国民航制造行业已经进入自主研发阶段,航空制造水平持续提升。
在制造飞机的过程中,复合材料的应用极为广泛,应用比例也在不断扩大,这使得其维修工作也越来越重要。
基于此,本文简单讨论飞机复合材料结构常见损伤,深入探讨检测维修方法,具体涉及目视法、敲击法、注射法、涂层法等内容,希望研究内容能够给相关从业人员带来一定启发。
关键词:飞机;复合材料;损伤;检测维修引言:制造飞机所使用的复合材料,具有强度高和比刚度高等特点,能够在一定程度上减轻飞机整体的重量,还拥有破损安全性较高、抗腐蚀等优点。
复合材料在实际使用的过程当中,会出现各种各样的损伤,对其进行维修、检测非常重要,合理的检测维修不仅能够避免出现安全事故,还能满足企业发展需要。
1.飞机复合材料结构常见损伤1.1划伤复合材料结构当中划伤和凿伤是常见的损伤类型,属于线性损伤,需要工作人员对破损的长度和破损深度进行详细的检查,以此来进行有效区分。
其中划伤是因为材料和尖锐物体进行了直接接触,从而造成了一定长度和深度的线性损伤,而划伤相对于划伤来说则更加宽,也可能是相对更深程度的损伤。
1.2刻痕在复合材料结构当中刻痕属于小区域损伤,需要工作人员对损伤处进行仔细检查,从其是否穿透表层来判断是否属于刻痕损伤。
1.3分层分层和脱胶这两种情况相对来说比较相似,需要工作人员检查其复合材料的内部,确定出现损伤的位置来判断属于哪种损伤情况。
其中分层是复合材料的层合板结构当中,各个纤维层之间出现剥离破坏,而脱胶则是复合材料结构当中,蜂窝和纤维层之间出现剥离破坏。
1.4穿孔在损伤问题当中,凹坑和穿孔也是比较相似的损伤情况,需要工作人员对损伤的部位进行检查,确认破坏的深度和穿透复合材料的厚度来区分属于哪种破损情况。
1.5雷击在实际的应用当中,复合材料因受到雷击或者明火从而引起复合材料的烧蚀损伤,对这种损伤问题检查工作比较简单,只需要人工观察材料表面就可以找到损伤的位置和相应的问题。
- 1、下载文档前请自行甄别文档内容的完整性,平台不提供额外的编辑、内容补充、找答案等附加服务。
- 2、"仅部分预览"的文档,不可在线预览部分如存在完整性等问题,可反馈申请退款(可完整预览的文档不适用该条件!)。
- 3、如文档侵犯您的权益,请联系客服反馈,我们会尽快为您处理(人工客服工作时间:9:00-18:30)。
民用飞机复合材料结构孔隙率的影响及检测廉 伟中国商用飞机有限责任公司上海飞机设计研究院上海201210摘要:本文从工程实践出发,总结了民用飞机复合材料结构中孔隙率产生的原因及相关工艺控制措施与孔隙率之间的内在关系,对比分析了目前航空工业界和主制造商可接受的孔隙率标准,探讨了孔隙率对复合材料理化特性及力学特性影响机理,对比了不同孔隙率的检测方法和孔隙率的控制方法,并给出了考虑结构安全和成本,在工程设计、制造和验证中统筹考虑可接受孔隙率的建议。
关键词:民用飞机复合材料结构孔隙率无损检测1 引言机体结构主要采用高性能复合材料的新型民机B787引领了复合材料在民机结构中应用的飞跃式发展和航空结构材料的应用变革,其复材用量重量占比接近50%;其竞争机型A350复材用量更高,达到52%;波音最近声明B777的改进型B777X的机身结构和此前宣布的机翼结构同样将采用复合材料;中俄即将联合研制的宽体客机中结构材料用量也将达同等水平。
由此可见,航空界已对复合材料在降低结构重量、油耗与排放、全寿命周期成本上达成共识。
航空复材结构的飞跃式发展是以材料进步、工艺发展、评价体系逐步成熟和大尺寸产品制造问题解决等为基础的,即便如此,复合材料领域还有诸多问题有待继续研究和解决,孔隙率便是其中之一。
对于孔隙,不同的手册、标准和规范给出了不同的定义,但其本质含义基本统一,即复合材料内部的、几何尺寸很小的、多点分布的孔洞(可能是空气、挥发物或空穴)。
孔隙是复合材料结构中常见缺陷的一种,通常用其体积占材料总体积的百分比来表征,也即孔隙率。
孔隙的尺寸跨度很大,线性尺寸可能从几个微米到几百个微米不等,在波音公司的规范中,甚至认为一簇密集孔穴缺陷中只要最大的直径小于6.35mm,该簇孔穴即被视为孔隙。
2 孔隙产生的原因及其影响目前航空工业领域,复合材料结构主要采用预浸料-热压罐固化工艺或液体成型工艺,虽然工艺形式和参数各不相同,但本质过程都是树脂基体与纤维增强材料之间的复合及树脂固化的过程,因此孔隙总存在于基体、树脂纤维界面或层间,典型的孔隙形貌如图1、2所示。
图1 典型复合材料层压板内部孔隙 图2 R区典型内部孔隙孔隙的产生有多种诱因,且可能源于原材料、铺贴或固化过程中的各个环节。
预浸料制备过程中树脂与纤维的浸润可能是不完全的,特别是固定单向纤维的纬线或织物中经纬纤维搭接位置难以完全浸润,固化后则形成孔隙。
采用单向带和织物预浸料铺贴时空气会裹入层间,若抽真空和加压过程中空气不能排出,孔隙则在层间聚集。
对于液体成型工艺,孔隙和“干区”同样是常见的制造缺陷,而此类缺陷的程度取决于时间-温度曲线、真空度、压力、流量、树脂粘度、树脂成分等因素和参数,树脂流动和浸润不充分将导致孔隙和贫胶缺陷的发生。
目前航空主结构材料上常用的是高温热固性树脂体系,如177°C固化的环氧树脂,其很容易变质,对存储条件、存储期限和操作时间有严格限制,用超期或变质预浸料所生产的层压板,因树脂的流动性较差或部分质变引起的不良固化,其孔隙率可能会很高。
另外热固性树脂在固化反应过程中会产生挥发物,需要施加真空或固化压力予以排除,但树脂一旦凝固,留存其中的挥发物将无法排出,孔隙随之产生。
同时水分是一种易被纤维、基体、预浸料甚至辅助材料吸附的物质,从原材料到后续的下料或铺设过程表面都会吸附空气中的水分,而若这些水分在固化过程中的蒸汽压小于树脂压力不能排出而引发孔隙。
固化压力是影响孔隙率的重要工艺参数。
固化过程中加压可以排出裹入的空气(结合真空辅助),压缩留存的空气或挥发物的体积,高压力甚至可以将空气、水汽及挥发物溶解在液态树脂中,压力不足会截留固化过程中所产生的挥发物或水蒸气而导致固化后的复合材料孔隙率偏高。
在模具的闭角处或结构厚度变化处(如丢层),常因纤维架桥而出现局部压力无法传递或不均匀,内部树脂压力较低甚至接近于零,气体或水气随之聚集,孔隙(甚至是分层和孔洞)会显著增加。
另外,复合材料固化过程中内应力的存在及其变化也是引起层压板中孔隙或微裂纹的重要原因,同时在铺设和固化工艺的操作过程中,任何来自外界的污染,如空气的漂浮物、护手霜、皮肤分泌物等都会污染材料,这些污染会导致孔隙率增高。
对于胶接结构,孔隙率是固化胶膜的重要缺陷,二次胶接结构都是“硬-硬”胶接,共胶接为“软-硬”胶接,当压力施加到“硬”的构件上时,易出现压力不均或局部压力无法传递的情况,在压力较低区域胶流聚集,湿气、挥发物不能顺利排出,出现较高的孔隙率从而直接导致固化后的胶层的剪切强度和剥离强度降低,特别胶层强度或耐久性会因孔隙率提高导致吸湿量的增加降低更多。
若被粘接复材结构中的空袭出现在临近表面位置,将不利于粘接,且容易吸湿而引发与邻近金属结构的腐蚀。
对于修补结构,特别是外场修补结构,通常是普通自然环境、不良的加热和加压条件,因受设备、外场环境、快速服役要求等限制,通常采用低压力、低固化温度、较短固化时间等工艺过程和参数,同时邻近结构的散热或曲率较大结构的架桥等现象使得修理过程中预浸料、胶膜等固化过程中易受湿度、非均匀加热、较低压力等导致结构内部孔隙率偏高。
孔隙的存在对固化后材料的理化特性[1-3]、静力性能[4-12]、疲劳特性[13-14]或功能[15]都存在一定的影响,且基本上都是不利影响。
孔隙率对复合材料力学性能的影响是结构设计、制造、验证和使用维护中关心的核心问题之一,也是领域研究的热点之一。
因孔隙主要存在于层间或纤维基体界面上,所以孔隙率主要影响基体或界面控制的力学性能(如层间剪切,微屈曲导致的压缩失效),而对纤维控制的力学性能影响不太大(如拉伸)。
当孔隙率较小时,基体裂纹和疲劳裂纹的起始位置主要是富树脂区[14],而当孔隙率增加时,孔隙本身则成为裂纹萌生点。
特别是孔隙的长轴方向垂直于载荷方向时,较高的孔隙率会导致萌生于相邻不同孔隙的裂纹发生耦合关联,进而显著影响结构力学性能(这与宏观结构中的MSD或WFD概念类似)。
层压板内部的孔隙率会恶化复合材料的吸湿特性[1-3],当环境中的水汽在基体中扩散导致孔隙区充水而其后暴露在高温环境时,积水气化将加速复合材料的溶胀老化,且蒸汽压力可能导致基体产生更多的微裂纹,从而加剧材料的吸湿老化特性,降低复材结构的静强度和疲劳强度。
这一点对蜂窝夹芯结构尤其严重,因为对于夹层结构,共固化压力较低,孔隙率通常较高,除面板本本身,水分还容易从面板侵入芯子,从引起耐久性问题。
除上述影响之外,孔隙的存在还在其他方面存在不利影响,如:a)对于复合材料中进行外来物检测时,孔隙的存在会增加外来物检测难度;b)孔隙率较高时,进行湿热处理后层压板玻璃态转化温度(Tg)因吸湿量的增加而降低,这将影响Tg值较为临界的复材结构安全;c)对于油箱区域,结构中较高的孔隙率可能使得表面张力极小的航空燃油沿着内部孔隙和缺陷发生渗漏,这对油箱安全和耐久性都有不利影响;d)当采用显微观察法确定纤维体积含量时,是否计入孔隙会影响纤维体积含量的判定;e)孔隙的存在对于一些功能性复合材料,如碳碳复合材料的电磁屏蔽特性也存在一些特殊的影响[15]。
3 孔隙率接受标准在理想条件下制造孔隙率接近于零的结构件并不困难,但在实际生产中,考虑到真实产品的结构尺寸、铺层、厚度变化、几何外形、曲率变化及结构组合,要稳定地批量生产低孔隙率的复材结构是非常困难的。
只有在严格按照相关质量体系和工艺规范,由具有相应资质的工艺人员在符合要求的环境条件下进行谨慎操作才能达到一定孔隙率要求。
虽然从力学性能要求和产品质量来看,孔隙率是越低越好,但是考虑到批量生产的效率和成本,结构设计、强度和制造需要确定一个合理的可接受孔隙率标准。
表1给出了所收集的复合材料结构的孔隙率接受标准。
表1 孔隙率可接受标准型号/规范/标准部位/结构等级接受标准型号/规范/标准部位/结构等级接受标准B xxxx规范(*1)次级复材结构无检测要求原型机(NASA/DOD)[16]主结构-单向带 ≤3%(10%结构面积)B xxxx 规范(*1)主结构≤2%或≥2%时一定面积要求主结构-织物 ≤5%(10%结构面积) R区超声检测不作要求次结构-单向带 ≤3%(15%结构面积) A型号翼梢小翼 ≤2% 次结构-织物 ≤5%(15%结构面积) 方向舵 同C型号 非结构-单向带 ≤4%(20%结构面积) C型号A区(关键区域) ≤1% 非结构-织物 ≤4%(20%结构面积)B区(重要区域) ≤1.5% 生产型(NASA/DOD)[16]主结构-单向带 ≤2%(5%结构面积)C区(一般区域) ≤2% 主结构-织物 ≤3%(5%结构面积) C型号部段研制中央翼(油箱区) ≤1.5%,R区不要求 次结构-单向带 ≤2%(10%结构面积) 后机身 关键区域≤1%,其他区域≤1.5%次结构-织物 ≤3%(10%结构面积) 尾翼 同C型号 非结构-单向带 ≤3%(10%结构面积) 复材机翼(C)外翼及中央翼(油箱区)同C型号非结构-织物 ≤4%(15%结构面积) A(*1)AXXX飞机CFRP结构 ≤2.5% (体积) AST 采用RFI工艺主结构 ≤2%AXXX飞机CFRP结构 ≤3% (面积) 某型号(*1)所有部位 ≤2%AXXX飞机 ATL工艺 ≤2% AGATE(*2)小型飞机复材结构 ≤4%Glare结构 ≤2% (验收标准)Glare结构 ≤2.5% (ADL)*1:为免责,本表格中对部分引用的规范或公司名称进行了隐藏处理;2:AGATE(Advanced General Aviation Transport Experiments),是美国上世纪90年代后期面向FAR23认证的小型通用飞机复合材料验证试验项目。
从上表中可以看出两个特点:1、我国新型民机飞机复材结构件中孔隙率的要求与其他主制造商或标准相比整体偏严,主要考虑保守设计以确保产品性能;2、即便是同一型号不同部件中可能规定不同的标准,这是因为不同的设计人员对孔隙问题有不同的认识。
严格的孔隙率标准固然对保证结构安全有利,但在非临界条件下孔隙率标准提高将带来制造、检测成本和超差率的上升。
此前工程界曾认为复合材料主结构3%的孔隙率是可以接受的,但通过对具有该孔隙率的结构在湿热环境下的层间剪切、压缩和弯曲强度试验测试证实这些性能下降明显,设计结果是非保守的。
随着人们认识的提高和工艺水平的改进,现在一般认为2%的孔隙率对于主结构来说是可接受的,包括油箱区域,波音、空客等主结构中所要求的孔隙率水平与此相同或相近,甚至在一定条件下可以放松。
而对于次级结构,视其承载大小及失效对飞机安全的影响可降低或不作检测要求。
但不作检测要求并非意味着孔隙率不加控制,而是通过经鉴定的工艺过程保证其孔隙率稳定在一个可以接受的范围内。