铝型材挤压
铝型材模具挤压成型所出现的问题

铝型材模具挤压成型问题分析1. 引言铝型材模具挤压成型是一种常用的铝型材加工方法,通过将铝料加热至柔软状态,然后通过挤压机将其挤压至模具中,形成所需的截面形状。
然而,在实际生产中,铝型材模具挤压成型过程中常常会出现一些问题,如尺寸偏差、表面缺陷等。
本文将对这些问题进行详细分析,并提出相应的解决方案。
2. 尺寸偏差问题尺寸偏差是指铝型材在挤压成型过程中与设计要求相比存在一定的误差。
尺寸偏差问题可能由以下几个方面引起:2.1 材料性质不同批次的铝料性质可能存在一定的差异,如硬度、弹性模量等。
这些差异会直接影响到铝料在挤压过程中的变形行为,从而导致尺寸偏差。
解决方案: - 选择稳定性能好的铝料供应商,并与其建立长期合作关系。
- 在生产前对每批铝料进行严格的质量检测,确保其性质符合要求。
2.2 模具设计模具的几何形状和尺寸对最终产品的尺寸精度有着直接影响。
如果模具设计不合理,如孔型尺寸过大或过小、边缘过于锐利等,都会导致挤压成型后的铝型材出现尺寸偏差。
解决方案: - 优化模具设计,确保孔型尺寸和边缘处理符合要求。
- 使用先进的CAD/CAM技术对模具进行设计和制造,提高制造精度。
2.3 挤压工艺参数挤压工艺参数是控制挤压成型过程中铝料变形行为的重要因素。
如果工艺参数设置不当,如挤压速度过快、温度控制不准确等,都会导致铝型材出现尺寸偏差。
解决方案: - 对挤压工艺进行充分的试验和优化,找到最佳的工艺参数组合。
- 加强对挤压机设备和温度控制系统的维护和管理,确保其正常运行。
3. 表面缺陷问题表面缺陷是指铝型材在挤压成型过程中表面出现的瑕疵,如气泡、划痕、凹陷等。
表面缺陷问题可能由以下几个方面引起:3.1 模具磨损模具在长期使用过程中会出现磨损,特别是挤压孔型部分。
模具磨损会导致挤压成型时铝料与模具壁之间的间隙不均匀,从而引起表面缺陷。
解决方案: - 定期对模具进行检修和维护,及时更换磨损严重的模具部件。
铝型材挤压设计注意事项
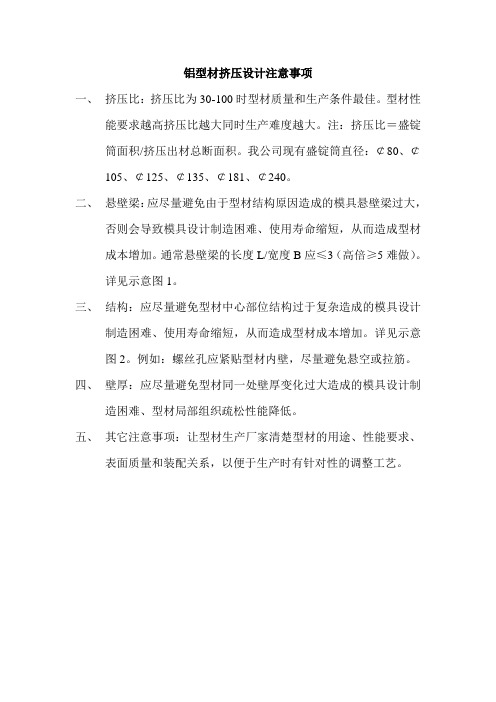
铝型材挤压设计注意事项
一、挤压比:挤压比为30-100时型材质量和生产条件最佳。
型材性
能要求越高挤压比越大同时生产难度越大。
注:挤压比=盛锭
筒面积/挤压出材总断面积。
我公司现有盛锭筒直径:¢80、¢
105、¢125、¢135、¢181、¢240。
二、悬壁梁:应尽量避免由于型材结构原因造成的模具悬壁梁过大,
否则会导致模具设计制造困难、使用寿命缩短,从而造成型材
成本增加。
通常悬壁梁的长度L/宽度B应≤3(高倍≥5难做)。
详见示意图1。
三、结构:应尽量避免型材中心部位结构过于复杂造成的模具设计
制造困难、使用寿命缩短,从而造成型材成本增加。
详见示意
图2。
例如:螺丝孔应紧贴型材内壁,尽量避免悬空或拉筋。
四、壁厚:应尽量避免型材同一处壁厚变化过大造成的模具设计制
造困难、型材局部组织疏松性能降低。
五、其它注意事项:让型材生产厂家清楚型材的用途、性能要求、
表面质量和装配关系,以便于生产时有针对性的调整工艺。
铝型材挤压企业标准

铝型材挤压企业标准是指铝型材挤压企业在生产过程中需要遵守的一系列规范和标准,以 确保产品的质量和安全性。以下是一些常见的铝型材挤压企业标准:
1. GB/T 5237-2008《铝合金建筑型材》:该标准规定了铝合金建筑型材的技术要求、试 验方法、检验规则和标志、包装、运输和贮存等。
2. GB/T 6892-2015《铝合金挤压型材》:该标准规定了铝合金挤压型材的技术要求、试 验方法、检验规则和标志、包装、运输和贮存等。
铝型材挤压企业标准
3. GB/T 3190-2017《铝及铝合金化学成分分析方法》:该标准规定了铝及铝合金化学成 分分析的方法,包括光谱法、化学分析法和物理分析法等。
4. GB/T 3199-2018《铝及铝合金挤压型材》:该标准规定了铝及铝合金挤压型材的尺寸 、外观质量、物理性能、机械性能、耐腐蚀性能等技术要求。
以上是一些常见的铝型材挤压企业标准,具体标准的选择和适用应根据企业的实0《铝及铝合金挤压型材机械性能试验方法》:该标准规定了铝及铝合 金挤压型材的拉伸性能、屈服强度、抗拉强度、伸长率等机械性能的试验方法。
铝型材挤压企业标准
6. GB/T 5237.6-2012《铝合金建筑型材表面着色膜耐久性的试验方法》:该标准规定了 铝合金建筑型材表面着色膜的耐久性试验方法,包括耐湿热性、耐盐雾性、耐紫外线性等。
铝型材挤压企业名录
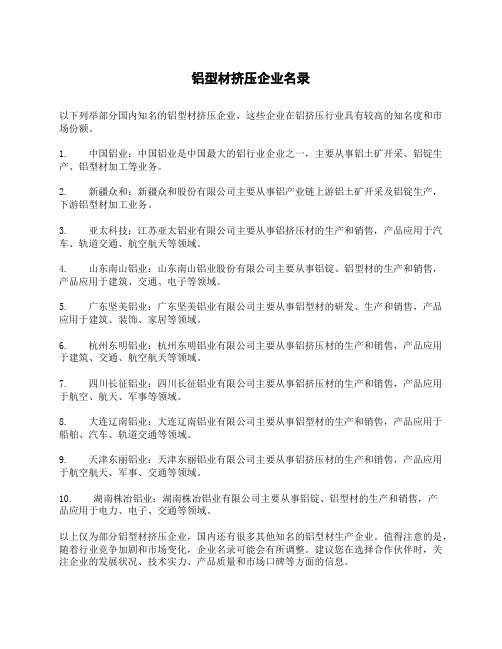
铝型材挤压企业名录
以下列举部分国内知名的铝型材挤压企业,这些企业在铝挤压行业具有较高的知名度和市场份额。
1. 中国铝业:中国铝业是中国最大的铝行业企业之一,主要从事铝土矿开采、铝锭生产、铝型材加工等业务。
2. 新疆众和:新疆众和股份有限公司主要从事铝产业链上游铝土矿开采及铝锭生产,下游铝型材加工业务。
3. 亚太科技:江苏亚太铝业有限公司主要从事铝挤压材的生产和销售,产品应用于汽车、轨道交通、航空航天等领域。
4. 山东南山铝业:山东南山铝业股份有限公司主要从事铝锭、铝型材的生产和销售,产品应用于建筑、交通、电子等领域。
5. 广东坚美铝业:广东坚美铝业有限公司主要从事铝型材的研发、生产和销售,产品应用于建筑、装饰、家居等领域。
6. 杭州东明铝业:杭州东明铝业有限公司主要从事铝挤压材的生产和销售,产品应用于建筑、交通、航空航天等领域。
7. 四川长征铝业:四川长征铝业有限公司主要从事铝挤压材的生产和销售,产品应用于航空、航天、军事等领域。
8. 大连辽南铝业:大连辽南铝业有限公司主要从事铝型材的生产和销售,产品应用于船舶、汽车、轨道交通等领域。
9. 天津东丽铝业:天津东丽铝业有限公司主要从事铝挤压材的生产和销售,产品应用于航空航天、军事、交通等领域。
10. 湖南株冶铝业:湖南株冶铝业有限公司主要从事铝锭、铝型材的生产和销售,产
品应用于电力、电子、交通等领域。
以上仅为部分铝型材挤压企业,国内还有很多其他知名的铝型材生产企业。
值得注意的是,随着行业竞争加剧和市场变化,企业名录可能会有所调整。
建议您在选择合作伙伴时,关注企业的发展状况、技术实力、产品质量和市场口碑等方面的信息。
铝型材挤压痕的解决方法

铝型材挤压痕的解决方法嘿,咱今儿就来说说铝型材挤压痕这档子事儿!你想想看,好好的铝型材,要是出现了那一道道让人看着就别扭的挤压痕,多闹心呀!这就好比一件漂亮衣服上突然有了块污渍,那可太影响美观和质量啦!那怎么解决呢?咱得先搞清楚这挤压痕是咋来的呀!有时候可能是模具设计不合理,这就好像给铝型材准备的“家”不合适,它能舒服地出来吗?肯定不行呀,就容易留下痕迹。
还有啊,挤压工艺参数不对也会惹祸呢,就跟人走路姿势不对会摔跟头一个道理。
那要解决就得对症下药。
模具设计不合理,咱就得好好琢磨琢磨,怎么改进能让铝型材顺顺利利地出来,还不带痕迹。
这可得下点功夫,不能马虎。
然后就是调整那些工艺参数啦,什么温度啦、压力啦、速度啦,都得恰到好处。
温度太高或太低,压力太大或太小,速度太快或太慢,都可能搞出挤压痕来。
再说说设备的维护吧。
你想想,设备要是不好好保养,就跟人老了不注意身体似的,容易出毛病呀!设备要是出了问题,那挤压出来的铝型材能好吗?所以呀,定期给设备做做“体检”,该修的修,该换的换,可别舍不得这点功夫和钱。
还有啊,操作人员也得注意呀!得有经验,得细心,不能大大咧咧的。
就像厨师做菜一样,火候掌握不好,菜能好吃吗?操作人员要是不注意细节,那挤压痕不就找上门来了嘛!你说这铝型材挤压痕的解决方法重要不?那当然重要啦!这可关系到产品的质量和外观呢!咱可不能让这些小小的挤压痕坏了大事呀!你想想,要是因为这个导致产品不合格,那得损失多少呀!所以呀,大家都得重视起来,从模具到工艺参数,从设备维护到操作人员,每一个环节都不能掉以轻心。
咱不能怕麻烦,解决挤压痕的过程可能会有点繁琐,但这都是为了最后的好结果呀!就跟爬山一样,虽然累,但到了山顶看到那美丽的风景,一切都值了!咱得有耐心,有决心,把这挤压痕的问题给解决掉。
这样生产出来的铝型材才能光溜溜的,让人看着就喜欢,用着也放心。
总之呢,解决铝型材挤压痕的问题可不是一件容易的事儿,但只要咱用心,办法总比困难多呀!大家一起加油,让那些挤压痕都消失得无影无踪吧!。
铝型材挤压方案

铝型材挤压方案引言铝型材是一种常用的轻质金属材料,具有优异的耐腐蚀性、导热性和可加工性。
铝型材的制备方法多种多样,其中挤压是一种常见且经济高效的制备方法。
本文将介绍铝型材挤压的方案,包括挤压原理、挤压工艺以及挤压设备的选择。
挤压原理铝型材的挤压是通过将加热的铝合金坯料放入挤压机中,通过外力使其通过模具的孔口挤出来,从而得到所需形状的铝型材。
挤压的原理主要包括两个方面:金属流动和应力状态。
金属流动在挤压过程中,金属材料会受到应力的作用,从而使其流动起来。
当铝合金坯料通过模具的孔口时,由于受到压力的作用,金属材料会形成膨胀流动的金属流,逐渐填满模具中的形状,并且在流动过程中会受到形状约束,从而使所得到的铝型材具有与模具孔口相同的形状。
应力状态挤压过程中,铝型材受到的应力状态决定了挤压的效果和形状。
在挤压机中,铝合金坯料被加热,使得它的塑性变得较高,能够更容易地流动起来。
同时,通过施加外力,将金属材料挤出模具孔口,所施加的压力必须与材料的应力相平衡,以确保金属材料能够顺利地流动,并形成所需的形状。
挤压工艺铝型材的挤压工艺主要包括预热、加热、挤压和冷却四个主要阶段。
预热在挤压之前,铝合金坯料需要进行预热处理。
预热的目的是提高铝合金的塑性变形能力,从而更容易地进行挤压。
预热温度通常需要根据具体的铝合金材料来确定,一般在400℃-500℃之间。
加热在铝合金坯料预热后,需要进一步加热至挤压温度。
加热温度也需要根据具体的铝合金材料来确定,一般在500℃-520℃之间。
加热的时间根据铝合金的厚度和尺寸来确定,一般需要保温30分钟至1小时。
挤压加热后的铝合金坯料被放入挤压机的料斗中,通过来自挤压机的外力将其挤压出来。
挤压需要根据铝型材的具体形状来选择合适的模具,并根据模具的孔口尺寸来调整挤压机的压力和速度。
冷却挤压完成后,铝型材需要进行冷却处理。
冷却的目的是使铝型材能够保持所需的形状,并增加其强度。
冷却通常采用水冷方式,将挤压得到的铝型材放入冷却槽中,并保持一定的冷却时间,以达到所需的冷却效果。
铝型材挤压流程
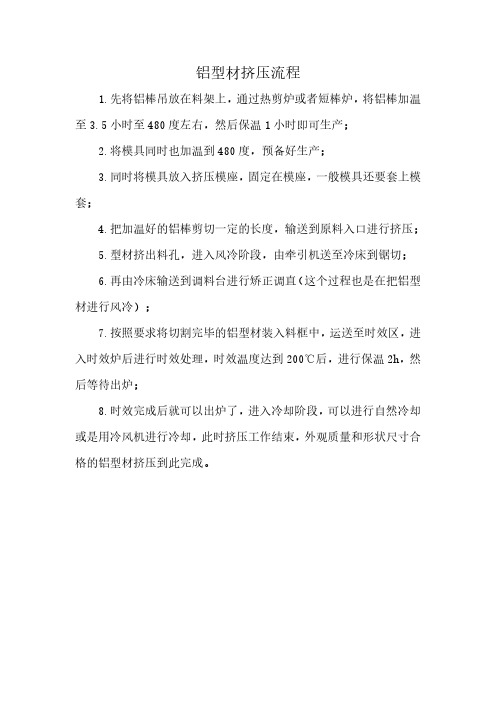
铝型材挤压流程
1.先将铝棒吊放在料架上,通过热剪炉或者短棒炉,将铝棒加温至3.5小时至480度左右,然后保温1小时即可生产;
2.将模具同时也加温到480度,预备好生产;
3.同时将模具放入挤压模座,固定在模座,一般模具还要套上模套;
4.把加温好的铝棒剪切一定的长度,输送到原料入口进行挤压;
5.型材挤出料孔,进入风冷阶段,由牵引机送至冷床到锯切;
6.再由冷床输送到调料台进行矫正调直(这个过程也是在把铝型材进行风冷);
7.按照要求将切割完毕的铝型材装入料框中,运送至时效区,进入时效炉后进行时效处理,时效温度达到200℃后,进行保温2h,然后等待出炉;
8.时效完成后就可以出炉了,进入冷却阶段,可以进行自然冷却或是用冷风机进行冷却,此时挤压工作结束,外观质量和形状尺寸合格的铝型材挤压到此完成。
铝合金型材挤压工艺

铝合金型材挤压工艺一、引言铝合金型材在现代制造业中扮演着重要的角色,其具有重量轻、强度高、耐腐蚀等优点,因此在建筑、交通、电子、航空等领域得到广泛应用。
而铝合金型材的生产加工采用挤压工艺成为主流趋势,因为挤压工艺可以实现高效率、低成本、灵活性强等优势。
本文将就铝合金型材挤压工艺进行详细的介绍,包括挤压工艺的原理和流程,工艺参数的优化,设备的选择和维护等方面,旨在为相关行业提供指导和参考。
二、挤压工艺的原理和流程挤压是一种将金属通过压力挤压成型的加工方法,它是铝合金型材的常用生产工艺。
挤压过程通过金属在一定条件下受到挤压力而发生形变,从而获得所需的截面形状。
一般来说,挤压工艺包括以下几个步骤:1.模具设计和制造挤压工艺的第一步是进行模具设计和制造。
模具的设计要满足产品的形状和尺寸要求,同时考虑金属的流动性和挤压后的变形情况。
模具的制造需要选用耐磨、高强度的材料,以确保模具的稳定性和寿命。
2.铝合金型材的选择在挤压工艺中,选择合适的铝合金型材是非常关键的一步。
不同的合金成分会影响挤压的难易程度和成品的性能。
通常使用的铝合金包括6000系列和7000系列,它们具有良好的挤压性能和机械性能。
3.挤压过程挤压过程是铝合金型材生产中最关键的一步。
在挤压过程中,铝型材通过挤压机的挤压头部分受到一定的挤压力,从而在模具中形成所需的截面形状。
挤压速度、挤压力和温度是影响挤压质量的重要工艺参数,需要严格控制。
4.后处理工艺挤压成型后的铝合金型材还需要进行后处理工艺,包括去毛刺、锯切、拉伸、热处理等。
这些工艺主要是为了改善铝合金型材的表面质量和性能。
三、挤压工艺参数的优化挤压工艺参数的优化是铝合金型材生产中非常重要的一环。
通过合理的工艺参数优化,可以提高型材的表面质量、机械性能和成品率,降低能耗和生产成本。
1.挤压速度挤压速度是影响挤压成品质量的重要参数。
过快的挤压速度会导致金属晶粒的变形和拉伸,从而影响型材的表面质量;而过慢的挤压速度则会增加挤压力,增加能耗和降低生产效率。
- 1、下载文档前请自行甄别文档内容的完整性,平台不提供额外的编辑、内容补充、找答案等附加服务。
- 2、"仅部分预览"的文档,不可在线预览部分如存在完整性等问题,可反馈申请退款(可完整预览的文档不适用该条件!)。
- 3、如文档侵犯您的权益,请联系客服反馈,我们会尽快为您处理(人工客服工作时间:9:00-18:30)。
挤压车间工艺操作规程1.主要内容和工艺范围1.1本标准规定了铝合金挤压型材的工艺制度要求。
1.2本标准适用于本公司6063、6063A、6061铝合金挤压型材生产。
2.挤压生产工艺流程图质量控制点3.工序工艺条件及操作方法3.1生产前准备3.1.1人员3.1.1.1新员工上岗必须进行有关《挤压工艺规程》、《挤压设备操作规程》以及安全生产、劳动纪律等方面的岗前培训,经试用及培训合格方能持上岗证到指定岗位独立上岗。
3.1.1.2配备好各工序所需岗位人员。
3.1.2定单3.1.2.1车间计划员根据生产计划部下发的生产指令单,按交货时间的先后、各机台的产能等相关参数,合理下发机台。
3.1.2.2计划员将各工序的补单(经生产计划部审核后),随同生产指令单一同下发机台。
3.1.3设备各机台班组按《挤压设备操作规程》的规定要求执行,操作前对各种设备的电控系统、冷却及加热系统等分别检查,无异常时进行空裁运行,确定正常方可生产。
如发现设备故障必须及时通知维修人员且上报当班主任,故障排除后试运行。
3.1.3.1挤压工具(物品)各机台由各工序岗位人员,将生产时的各种使用工具及物品,准备好,放置规定地点。
如模具夹、铝棒夹、接垫钩、装模钩、挤压用润滑剂、石棉手套、压余桶、成品框、废品框等。
3.1.3.2挤压筒由机台组长或主机手,在开机前12小时内将挤压筒温度升至400±20℃,严禁超温至450℃。
新筒按阶梯式加温法,即24小时内升至400±20℃。
3.1.3.3模具开机前,由机台组长或主机手,按生产指令单的要求,到模具车间将模具及对应模具跟踪卡一起拉回机台,装入模具加热炉加温,并记录好模具型号及其进出炉时间。
炉温及时间见下表:模具出炉后应在5分钟内装配好,装好后测量其实际温度符合工艺要求后才能挤压。
模具加热不允许超过12小时,否则应取出重新保养。
3.1.4铝棒3.1.4.1开机前,由机台(短棒炉)组长或主机手,按生产指令单的要求,计算出所需铝棒的长度从铝棒仓领取铝棒(必须是挂有“合格”标识牌的铝棒),并如实记录铝棒规格、数量和批号。
3.1.4.2机手装炉前对每根铝棒作目视检查,凡表面有泥沙、油污或弯曲超标的铝棒不得入炉,并隔离堆放做好标记。
分两层将铝棒整齐排列放入加热炉加热。
3.1.4.3按下油枪点火开关。
工艺控制见下表:注:铝棒温度严格控制在工艺范围内,否则不得上机挤压。
(温度偏低应继续加热,待够温再挤压,温度过高可出炉稍冷至符合工艺要求再挤压) 3.2 挤压生产3.2.1 试车,空载试运行。
确认运转正常和棒温、模温和盛锭筒温符合工艺要求且铝棒进入正常位置方可投入生产。
3.2.2装模按指令单要求,主机手用模具夹将已加热到温的使用模具自 炉内取出装模,装模过程中只许用铝棒敲打。
3.2.3挤压应用手动流量调好模具所出料需要的流量速度,如10秒内压力达到21Mpa 应马上停机卸模检查原因。
工艺质量控制a) 出料前垫好石墨板,石墨板如损坏应及时更换,以防型材被划伤、擦伤。
若发现型材超标或质量问题,经质检员鉴定不合格时,应立即停机,待卸换模具后再生产,并对不合格模具进行标识、记录和送修。
b) 出料后每套模具挤压的第一支型材必须做好标记并检验。
引导型材到滑动台并将前进中的(小料)料头弯曲,便于料前行。
c)组长及主机手严格按指令单的要求进行生产,严禁无单生产,每个品种生产完毕,必须与锯切负责人确认后在生产通知单上减数,签名。
d)使用模具必须按以下规定操作:1)试模合格的模具未经氮化不得生产。
2)模具第一次氮化后的用棒数不得超过60支。
3)第二次氮化后不超过100支。
4)第三次及以上不超120支铝棒。
3.2.4淬火3.2.4.1挤压淬火的前提条件是:在挤压型材进入出料台时,通过冷却风机提供大量风量,将型材在进入冷却台迅速冷却至200℃以下;3.2.4.2冷却风量的大小可以通过调节冷却风机进风量的大小进行调节,也可以通过冷却风扇开、关数量进行调节;3.2.4.3任何需要通过冷却风扇进风口的大小来调节冷却风量时,冷却风扇的进风口大小均不得小于进风口全开时的一半;3.2.4.4每年05月01日至09月30日期间,所有冷却风扇必须全部打开,在确保冷却速度足够的前提下,冷却风量的调节允许通过调节进风口的大小进行调节,不允许关闭任何冷却风扇;3.2.4.5每年10月01日至次年04月30日期间,在确保冷却速度足够的前提下,可以关闭一半的冷却风扇,冷却风量的调节允许通过调节进风口的大小进行调节;3.2.4.6对于生产壁厚大于1.5mm(不含)以上的型材,生产时不分季节变化,所有冷却风扇必须全部打开,在确保冷却速度足够的前提下,冷却风量的调节只允许通过调节进风口的大小进行调节,不允许关闭任何冷却风扇;3.2.4.7对于部分型材因产品特性原因,不能全开风机或不能开风机的情况下,除经批准的列表中的型材外,必须由车间主任或车间带班主任在车间工艺记录上签字确认,否则在检查时发现的视为违规操作;3.2.5中断并根据滑动台的长度和型材接头位置合理断料,断料时,每支的锯头、锯尾控制在200mm~1500mm之间,对发现的有明显质量缺陷(如气泡、夹渣等)的型材上做“×”标识。
3.2.6矫直矫直前打开马达空载运行一次,确认无异常后方可开始工作。
型材应冷却至50℃以下才能进行拉伸矫直,拉伸率≤1.5%。
拉伸时应注意型材形状尺寸的变化,避免拉伸过量,严禁多支矫直。
矫直时如发现型材存在扭拧、面粗、拉伤等问题应立即通知主机手解决。
对于方管类及内腔较大的型材,必须用合适的铝块充填后再拉伸,以减少料头的变形量,提高成品率。
质量控制3.2.6定尺锯切锯切前先空载运行锯床一次,确认无异常后方可开始工作。
启动进料床,把矫直好的型材送到定尺滑动台,然后再根据一次能锯量将型材送到定尺锯切台。
确定好锯头、锯尾后,在锯片在打油,然后开始锯切。
锯切头尾时,以切去拉伸时引起的变形区段为准,通常切头尾长度在200mm ~1500mm 。
锯切好的型材装框前必须遂支检查,凡有气泡、拉花、碰划伤、拖模、斜角、扭拧、平面间隙超标等质量缺陷一律不能入框。
如发现质量问题,必须向上道工序反馈。
工艺和质量控制经检验合格的型材装框时,轻轻放入料框,摆放时应分层排放,每层之间用铝隔条隔开,端头对齐(非定尺料有一端对齐),不得交叉,长的放底层,短的放上层,大载面的放底层,小载面的放上层。
框装满后,锯切工序负责人按生产指令单要求,填写“生产随行卡”,同时将相关数据输入“铝业之星”,将随行卡交付本机台组长。
3.3 时效 3.3.1时效工艺制度说明炉温-时间曲线:TT:炉内温度;t2:时效温度h2–h1:保温时间h1 h2 H3.3.2时效作业程序3.3.2.1准备工作a)设备点检b)确认设备周围安全;c)启动空炉,开启加热器按钮,查看操作盘上的仪表参数是否正常;d)查看电机运转情况;e)全部关闭。
3.3.2.2产品确认3.3.2.2.1依据生产随行卡或挤压完毕的型材标签中的内容,查看时效状态;3.3.2.2.2型材在料框内的码放是否在装炉时不受损伤,码放不合格的产品不予时效并通知车间主任。
3.3.2.3温度设置3.3.2.3.1温度调节仪表的设置应根据不同合金、不同状态、不同产品结构要求确定合适的时效温度范围,具体见HPLC-JS-1102《铝合金时效工艺操作规程》;3.3.2.4操作程序3.3.2.4.1将料筐装入台车(取下产品标签);3.3.2.4.2料筐平稳落于台车上,并且不能超出台车边;3.3.2.4.3上下两层料筐位置整齐;3.3.2.4.4操作过程1)打开炉门时,先松开转动手柄,再打开炉门。
2)开动台车a)首先确认台车周围无其它物品;b)确认炉门处于最高位置;c)启动台车驱动按钮;d)观察台车运转情况,直至到位;3)关闭炉门,拧紧手柄。
4)将温度调节仪表的开关拨到“0N”的位置。
5)启动风机按钮。
6)将六个加热器旋钮置于“入”的位置。
7)检查时效炉运转情况,并在《型材时效记录》上认真做好记录。
8)按取下的产品标签填写《型材时效记录》。
9)出现异常情况时要及时切断电源,报告有关人员。
10)按工艺制度达到保温时间后,按如下程序关闭炉子。
关闭加热器开关;关闭循环风机开头;11)将紧固手柄拧开并打开炉门。
12)将台车拉出,炉门关闭。
13)将时效标签分别按筐号挂或、贴在每种型材垫条端头,多种型材在一个料筐时,应按型材型号决定标签位置。
将时效炉号、操作人员等填写于工艺随行卡上,将料筐吊出台车,放置于待验收区。
挤压车间整形料的运作流程1目的为提高生产过程的数据准确性,更好的完成订单,现对挤压车间整形工序的流程做一规范;2适用范围本制度适用于挤压车间整形工序;3流程内容3.1未入中转仓整形料的流程3.1.1机台产出料后,将经质检员判定需整形料,单独装框,严禁与其它料混装;3.1.2机台负责填卡、录入人员,将所产出的需整形料数据信息录入铝业之星系统,并按正常程序填写好对应随行卡;3.1.3质检员在随行卡上将需整形料存在的缺陷记录清楚,且注明“此料需整形”字样并签名;3.1.4机台人员持此“需整形”卡,将料吊至整形区与整形班人员办理签收手续,料卡相随,无卡或无质检签字的整形班拒绝收料;3.1.5整形班接到整形料后,即时将整形料数据信息录入服务器“SERVER”—“tuzhi”—“挤压整形记录”—《挤压整形记录台账》中(因目前铝业之星系统中无此模块,故用EXCEL电子表格代替)以便生产部查阅;3.1.6有需时效后整形的料,由整形班判定并跟踪整个时效过程;3.1.7整形完毕,经质检员判定的合格品,由整形班负责在铝业之星系统中原挤压产出单号上进行修改、审核,原“需整形”随行卡交质检员修改并签字。
整形班持此卡连同合格料一起与中转仓收数员办理入仓交接手续;3.1.8经判定的不合格品,由质检员开具《不合格品通知单》。
整形班直接与废品仓办理报废手续;将废品票据连同成品票据一起交挤压车间统计员审核、记账(废品只计机台废品,不做质量废品处罚);3.1.9整形班将质检员开具的《不合格品通知单》,送交生产部(或车间主任)进行排产补单;3.1.10每批次的整形料交付完成后,必须将所有整形数据、时间等信息及时、详细地录入“挤压整形记录台帐”。
3.2已入中转仓或后工序检出的整形料的流程3.2.1在转序过程中或后工序生产中发现的需整形料,由检出工序质检员开具五联不合格通知单,且写清楚料的缺陷,注明“此料需整形”字样,交发现工序;(以便其与挤压车间办理交接手续)3.2.2检出工序持“需整形”字样的《不合格品通知单》,随同待整形料一起送交挤压整形班,并办理签收手续;3.2.3整形班接料后当即确定“约定完工时间”,并报由生产部审核后,将新确定的“约定完工时间”,连同此批料的其它相关数据信息一起,及时录入电脑EXCEL台账(整形记录台账);3.2.4整形完成后,未出现废品,由整形工序的质检员在原“需整形”字样的《不合格品通知单》上注明“整形合格”字样、并签名。