植物油乳化剂word本
乳化剂ppt课件【可编辑全文】

精品ppt
38
油相
月桂酸
蜂蜡
鲸蜡醇
硬脂醇
液体石蜡 (轻)
液体石蜡 (重) 油酸
表2-3 乳化油相所需的HLB值
O/W型 16 12 15 14 10.5
10~12 17
W/O型
油相
-
凡士林
4
无水羊
毛脂
-
硬脂酸
棉子油
4
蓖麻油
4
亚油酸
-
精品ppt
O/W型 9 10
15~18 10 14 16
W/O型 4 8 5 -
因本品粘度低,单独用作乳化剂制成的乳 剂容易分层,常与西黄蓍胶、果胶、琼脂、 海藻酸钠等合用。
精品ppt
23
阿拉伯胶
本品适用于乳化植物油或挥发油,广泛应 用于内服乳剂。因可在皮肤上存留一层有 不适感的薄膜,不作外用乳剂的乳化剂。
阿拉伯胶内含有氧化酶,易使其酸败,故 用前应在80℃加热30min以破坏之。
精品ppt
14
乳化剂的基本要求
①具有较强的乳化能力。乳化能力是指乳化剂能显著 降低油水两相之间的表面张力,并能在乳滴周围形 成牢固的乳化膜的能力;
②有一定的生理适应能力,无毒,无刺激性,可以口 服,外用或注射给药;
③受各种因素的影响小。乳剂处方中除药物外,常加 有许多其它成分,如酸、碱、辅助乳化剂等,乳化 剂应不受这些成分的影响。
其其他他组组成成
防腐剂、调味剂等
精品ppt
4
乳乳 剂剂 的的 种种 类类
基基本本Байду номын сангаас型
复复合合型型
O/W
W /O
W /O/W O/W /O
内相 外相 内相 外相
wo型乳化剂处方分析
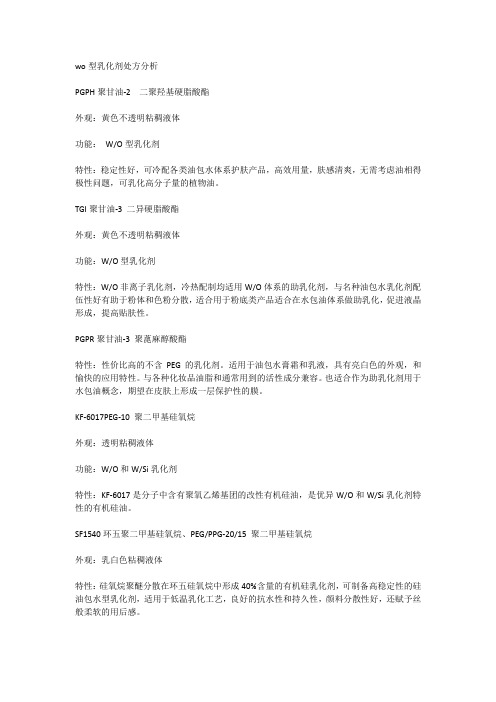
wo型乳化剂处方分析PGPH聚甘油-2 二聚羟基硬脂酸酯外观:黄色不透明粘稠液体功能:W/O型乳化剂特性:稳定性好,可冷配各类油包水体系护肤产品,高效用量,肤感清爽,无需考虑油相得极性问题,可乳化高分子量的植物油。
TGI聚甘油-3 二异硬脂酸酯外观:黄色不透明粘稠液体功能:W/O型乳化剂特性:W/O非离子乳化剂,冷热配制均适用W/O体系的助乳化剂,与名种油包水乳化剂配伍性好有助于粉体和色粉分散,适合用于粉底类产品适合在水包油体系做助乳化,促进液晶形成,提高贴肤性。
PGPR聚甘油-3 聚蓖麻醇酸酯特性:性价比高的不含PEG的乳化剂。
适用于油包水膏霜和乳液,具有亮白色的外观,和愉快的应用特性。
与各种化妆品油脂和通常用到的活性成分兼容。
也适合作为助乳化剂用于水包油概念,期望在皮肤上形成一层保护性的膜。
KF-6017PEG-10 聚二甲基硅氧烷外观:透明粘稠液体功能:W/O和W/Si乳化剂特性:KF-6017是分子中含有聚氧乙烯基团的改性有机硅油,是优异W/O和W/Si乳化剂特性的有机硅油。
SF1540环五聚二甲基硅氧烷、PEG/PPG-20/15 聚二甲基硅氧烷外观:乳白色粘稠液体特性:硅氧烷聚醚分散在环五硅氧烷中形成40%含量的有机硅乳化剂,可制备高稳定性的硅油包水型乳化剂,适用于低温乳化工艺,良好的抗水性和持久性,颜料分散性好,还赋予丝般柔软的用后感。
ES-5300月桂基PEG-10 三(三甲基硅氧基)硅乙基聚甲基硅氧烷外观:微黄色透明粘稠液体特性:有机硅乳化剂,能够形成低粘度的油包水乳液,具有油相灵活性,能够乳化硅油,有机油脂及其混合物,可广泛应用于各种个人护理品配方。
5225C环五聚二甲基硅氧烷、PEG/PPG-18/18聚二甲基硅氧烷外观:透明至半透明液体特性:可作稳定W/SI配方,肤感清爽,润肤剂,可分散颜料,适合冷配,能制作透明配方。
EM-90鲸蜡基PEG/PPG-10/1 聚二甲基硅氧烷外观:无色透明液体功能:W/O乳化剂特性:硅油改性的W/O乳化剂,肤感轻盈、稳定性好。
农药常用乳化剂

农药常用乳化剂1、农乳300# (农药乳化剂300号)化学名称及组成二苄基联苯基聚氧乙烯醚非离子乳化剂。
与其他乳化剂复配成混合塑乳化剂。
用于各种有机氯,有机磷杀虫剂及除草剂2、农乳500#(农药乳化剂500号)十二烷基苯磺酸钙阴离子乳化剂和分散剂,与其他乳化剂复配成混合型乳化剂,用于有机氯、有机磷农药及除草剂3、农乳600#1(农药乳化剂600号)苯乙烯基苯基聚氧乙烯醚与农乳500#、700#复配制成混合型乳化剂,可大大降低乳化剂用量和农药成本4、农乳700#(农药乳化剂700号)烷基酚甲醛树脂聚氧乙烯醚非离子乳化剂和润湿剂,适用于有机氯、有机磷农药作为乳化性能调整剂,是除草剂用乳化剂的特效单体5、农乳1600#(农药乳化荆1600号苯乙基苯基聚氧乙烯一聚氧丙烯醚有机氯、有机磷农药乳化剂单体6、宁乳700#苯乙樟(或α-甲基苯乙烯)苯酚甲醛树脂聚氧乙烯醚非离子农药乳化剂,适用于各种杀虫剂,杀菌荆和除草剂制造7、宁乳33#苯乙烯基苯酚甲醛树脂聚氧乙烯-聚氧丙烯嵌段型聚醚非离子乳化剂,适用于杀虫剂,杀菌剂和除草剂等农药配制8、宁乳34#苯乙烯苯酚甲醛树脂聚氧乙烯聚氧丙烯醚非离子乳化剂,用于各种农药生产9、宁乳37#苯乙烯基苯酚甲醛树脂聚氧乙烯醚非离子乳化剂,用于生产杀虫剂,杀菌剂和除草剂10、农药乳化剂0201阴离子与非离子表面活性剂的复配物用于配制对硫磷乳剂,用量为10%,也适用于配制辛硫磷乳剂;与农乳0203-B复配用于配制杀螟威乳剂11、农药乳化剂0201B阴离子与非离子表面活性剂的复配物用于配制对硫磷乳剂,用量为8%;也适用于配制50%辛硫磷乳剂;与农乳0203—B复配用于配制杀螟威乳剂;也可配调50%乙基1605,50%倍硫磷12、农药乳化剂02非离子和阴离子表面活性剂与溶剂的复配物13、农药乳化剂02C特殊非离子和阴离子表面活性剂的复配物配制粮食防护荆防虫磷(高浓度马拉硫磷乳油)的专用乳化剂14、农药乳化剂0203A阴离子与非离子表面活性剂的复配物以6%用量调配敌敌畏乳剂.呈有色透明溶液;用于配制抗菌素402乳剂.用量为5%~10%15、农药乳化剂0203B阴离子、非离子表面活性剂与溶剂的复配物以3%~6%的甩量可调配80%DDVP,40%~50%甲胺磷、40%氧化乐果等农药乳油16、乳农药化剂0204十二烷基苯磺酸钙和烷基酚聚氧乙烯醚的复配物以3%用量调配乙酰甲胺磷农药;以6%用量调配乐果17、农药乳化剂0204C非离子和阴离子表面活性剂的复配物以3%~6%的甩量配制40%乐果,50%久效磷l以10%的用量调配20%叶蝉散等农药乳油18、农药乳化剂0205非离子、阴离子表面活性剂及溶剂的复配物以10%的用量可调配50%治螟磷(治螟灵)19、农药乳化剂0206阴离子和非离子表面活性剂的复配物以10%的用量可配制50%甲基硫磷乳剂20、农药乳化剂0206B非离子和阴离子表面活性剂与溶剂的复配物以10%的用量可调配50%甲基—1605、72%4D丁酯、50%喹硫磷等农药乳油21、农药乳化剂0207特殊的非离子和阴离子表面活性剂与溶剂的复配物以10%的用量配制40%异稻瘟净、50%稻瘟净等农药乳油22、农药乳化剂0208非离子和阴离子表面活性剂与溶剂的复配物以10%~13%的用量配制40%水胺磷等农药乳油23、农药乳化剂1201非离子和阴离子表面活性荆的复配物虫满净(氧化乐果十克死螨)合剂专用乳化剂24、农药乳化剂1202非离子和阴离子表面活性剂的复配物配制30%双效菊配合剂(克死螨+S-5602)的专用乳化剂25、农药乳化xx1204非离子、阴离子表面活性剂及溶剂的复配物以10%的用量调配20%甲基对硫磷与20%甲胺磷混合农药乳油26、农药乳化剂2000 (农药乳化剂20)烷基酚聚氧乙烯醚磺化琥珀酸酯用作农药的可湿粉剂、胶囊剂和水剂的助荆,农药胶悬剂的特效助剂27、农药乳化剂2201阴离子和非离子表面活性荆与溶荆的复配物以10%~12%的用量配制拟除虫菊酯系农药乳油。
食品乳化剂演示文稿
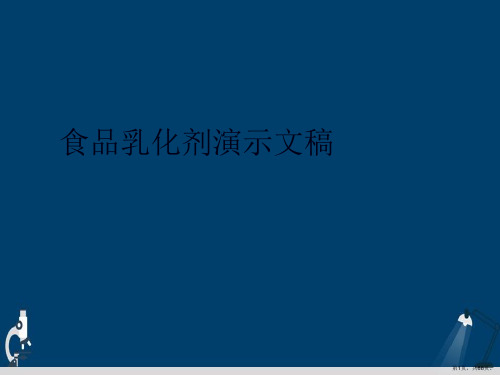
(9)防腐:乳浊液在制备和使用过程中会受 到微生物的污染,商业出售的产品中因含有防 腐剂而不会出现微生物过速增长,用防腐体系 保护乳浊液是很有必要的。许多公司将所生产 的产品进行破坏试验来判断防腐剂体系的防腐 效果。
第32页,共88页。
2.2 乳化剂的亲水亲油平衡值(HLB)
根据乳浊液类型,采用强的亲水性乳化剂或亲 油乳化剂,用于破坏乳浊液。
破坏泡沫的最好乳化剂随泡沫而变化。
第18页,共88页。
1.5 络合作用
乳化剂可络合淀粉。 如在面包和蛋卷生产中,乳化剂可调理生面
团,促进结构形成均匀,改善性能。 乳化剂在揉和好的生面筋结构中的作用是改
善面筋体积和颗粒,增强面筋结构。 乳化剂可以在面包生产中帮助脱模。 亲水乳化剂具有抗硬化作用和调理面团两个
第33页,共88页。
乳化剂分子中同时有亲油、亲水两基团,整 个分子亲水亲油的倾向,取决于两类基团的 作用,是两者亲和力平衡后分子所表现的综 合效果。
第34页,共88页。
决定乳化剂的两亲特性因素
乳化剂的亲水性
亲水基的种类 亲油基的种类 脂肪基: 带脂烃链的芳香基
芳香基: 带弱亲水基的亲油基 分子结构与相对分子量
第16页,共88页。
1.3 悬浮作用
悬浮液是不溶性物质分散到液体介质中形成 的稳定分散液,分散颗粒大小0.1-100μm。
用于悬浮液的乳化剂,对不溶性颗粒也有润 湿作用,这有助于确保产品的均匀性。
悬浮液乳化剂通常与稳定剂或增稠剂共用。
第17页,共88页。
1.4 破乳作用和消泡作用
在许多需要破乳化作用过程中,常采用相反类 型乳化剂或投入超出平衡所需要的乳化剂。
类 聚氧化乙烯(20)甘油单硬脂酸酯
乳化剂专题课件

四、乳化剂在食品中的作用
乳化剂是最重要的一类食品添加剂,不仅使互不相溶的水、 油两相得以乳化成为均匀、稳定的乳状液,还能与食品中的碳 水化合物、蛋白质、脂类发生特殊作用,起到多种功效。
1.与淀粉络合 2.与蛋白络合,改善食品结构及流变特性,增强面团 强度 3.与脂类化合物的相互作用 4.其他作用 乳化剂食品被吸附在气-液界面,降 低界面张力,增加气体和液体接触的面积,有利于发 泡和泡沫的稳定,可改善学及习文档稳定气泡组织。
(1)性质 白色至黄色粉末,或无色至微黄色的黏稠液体或软 固体,无臭或稍有特殊气味。①溶解性:易溶于乙醇、丙酮。 单酯可溶于热水,但二酯和三酯难溶于水。单酯含量高,亲水 性强;二酯和三酯含量越多,亲油性越强。②耐热性:差,在 受热条件下酸值明显增加,蔗糖基团可发生焦糖化作用,使颜 色加深。③稳定性:酸、碱和酶都会导致蔗糖脂肪酸酯水解, 水解作用在20℃以下很小,但随着温度的增高而加强。
可用于油脂、配酥油和人造奶油等,用量为0.1 %~0.5%。
由于乳化剂的协同效应,蔗糖脂肪酸酯与其他乳化 剂复配使用,在食品中的应用更广泛。
应用时先将蔗糖脂肪酸酯用适量冷水调和成糊状, 再加入所需的水,升温至60~80℃,搅拌溶解或将蔗 糖脂肪酸酯加到适量的油中,搅拌令其溶解和分散, 再加到制品原料中。
学习文档
三、卵磷脂
大多数是大豆磷脂,为纯天然乳化剂。 卵磷脂是一种存在于大豆的各种磷酸甘油 酯及其衍生物的脂质混合物,主要包括胆碱磷 脂(卵磷脂)、胆胺磷脂(脑磷脂)和肌醇磷 脂,并含有一定的植物油。 几乎所有天然存在的卵磷脂都属于α-卵磷脂。 饱和脂肪酸基连接在末端碳上,不饱和脂肪酸 基一般连接在中间碳上。
学习文档
在我国,单硬脂肪酸甘油酯用量约占乳化剂 总用量的70%,是食品工业中应用最广泛的乳化 剂,其中在面包、饼干和糕点等,用量最大,其 次为黄油、人造奶油及冰淇淋等。
乳化剂.doc

乳化剂.doc1、乳化剂:O-10;易溶于水及有机溶剂,对酸、碱、硬水稳定。
具有良好的润湿、乳化、净洗性能。
在化纤工业中,作多种化纤纺丝油剂组分之一,具良好的可纺性;在一般工业中作乳化剂,对动、植、矿物油具有良好的乳化性能,配制的乳液十分稳定;还可用于配制家用洗涤剂、工业净洗剂、金属清洗剂;在纺织工业中作润湿剂;在农药行业作乳化剂的组分之一。
HLB值12.5~132、乳化剂MOA-3;易溶于油及极性溶剂中,水中呈扩散状,具有良好的乳化性能,作w/o型乳化剂,用于矿物油、脂族溶剂的乳化,聚氯乙烯塑料溶胶的降粘剂,在化纤油剂中广泛使用。
HLB值6~73、乳化剂MOA-9;易溶于水,具有优良的乳化、净洗、润湿性能,在毛纺工业中作羊毛净洗剂及脱脂剂、织物的精练剂、净洗剂;可作为液体洗涤剂的重要组成部分;在化妆品和软膏生产中作乳化剂;对矿物油和动、植物油脂均有极好的乳化、分散、润湿性能;还可作为为玻璃纤维抽丝油剂的乳化剂。
HLB值13~144、乳化剂NP-10;TX-10易溶于水,具有优良的乳化净洗能力,是合成洗涤剂重要组分之一,能配制各种净洗剂,对动、植、矿物油污清洗能力特强;除显示乳化性能外,且具有除静电效果;该乳液对胶体有保护作用;一般工业作乳化剂,配制乳液稳定;用作防腐剂、润湿剂、电池缓蚀剂;在农药、医药、橡胶工业用作乳化剂,建筑行业可作为乳化沥清的乳化剂,又是金属水基清洗剂的重要组成之一;HLB值12~13 5、乳化剂OP-15;易溶于水,耐酸、碱、盐、硬水,具有良好的乳化、润湿、扩散、增溶性能;HLB值~156、聚乙二醇PEG;用作医药及化妆品的基质,橡胶工业与纺织工业的润滑剂和润湿剂。
7、司盘S-20;溶于油及有机溶剂,分散于水中呈半乳状液体。
在医药、化妆品生产中作W/O型乳化剂、稳定剂、增塑剂、润滑剂、干燥剂;纺织工业中作柔软剂、抗静电剂、整理剂;亦用作机械润滑剂;作为添加型防雾剂,具有良好的初期及低温防雾滴性,适用于PVC(1~1.5%)、聚烯烃薄膜(0.5~0.7%)、EVA薄膜。
饲料添加剂之乳化剂

胆汁酸盐 一、在肉鸡生产中的应用 1、对肉鸡生产性能的影响: 大豆磷脂能提高家禽的食欲改善营养物质的消化率尤其是亲水的胆碱基与疏水的脂肪酸相结合有利于营养物质与家禽消化酶的结合。
2、对肉鸡的保健功能:胆碱、肌醇、VB12、VE、亚油酸和一些未知生长因子对动用和消除肝中的多余脂肪是不可缺少的。
大豆磷脂中含有丰富的胆碱、肌醇和亚油酸在鸡饲料中添加大豆磷脂对防止鸡脂肪肝综合症等疾病的发生非常有效,同时可保持肝脏/体重比值正常3、在蛋鸡生产中的应用:蛋鸡饲料中添加大豆磷脂可以促进其生长发育、提高产蛋率和节约饲料。
[7] 二、大豆磷脂在猪日粮的作用1、帮助仔猪软蓬松,并且在融化过程中可保持形状。
[22]单甘酯Glycerinmonostearate简称:GMS 单硬脂酸甘油脂非离子分子量:358.57分子结构式:CH2OH—CHOH—CH2OOC(CH2)16CH3白色或微黄色蜡状片形或珠形固体。
无味或油脂味、无臭、无毒。
不溶于水和甘油,但能在热水中形成稳定的水合分散体,溶于热有机溶剂。
HLB值3.6-4.0【23】酯化反应、水解反应等糖苷酯类乳化剂的性能和营养功能均优于市场上其他现有的乳化剂。
此类乳化剂充分解决了普通乳化剂经常发生的乳化体系不稳定、易破乳重新形成油层的不足【23】化学法主要有酯交换、酯化法两种,其原料主要是甘油、脂肪酸(酯)。
【24】酶法:以天然油脂、合成酯、脂肪酸和甘油为原料,脂肪酶催化反应。
【25】①2%(t0)的复配乳化剂(亲水性单甘酯与大豆磷酯为1:1),可得含油30%(∞)左右的稳定的乳状液。
【26】②单甘酯与蔗糖酯以4:1进行搭配时对豆油的乳化效果最好。
【23】除乳化剂外还可作为消泡剂、分散剂、增稠剂、湿润剂、流滴剂和防雾剂、润滑剂、抗静电剂等。
广泛应用于食品、化妆品、医药、塑料助剂、农业等领域。
【27】蔗糖酯SucroseFattyAcidEsters(Sucrose Estersof FattyAcids;Sucroesters)蔗糖酯的全称为蔗糖脂肪酸酯(SE)非离子型表面活性剂(RCOO)nC12H12O3(OH)8-n化学结构R为脂肪酸烃基;n为蔗糖的羟基酯化数蔗糖酯为白色至棕黄色的粉末,无臭、无味。
(完整word版)植物油全书(word文档良心出品)

杏桃仁油 Apricot kernel oil学名:Prunus armeniaca L. 科名:蔷薇科(Rosaceae)词源:源自拉丁文Prunus李树和armeniaca亚美尼亚两字。
植物与环境:杏桃原产于中国,后传至中东。
现今美国、法国南部大量栽种杏桃树作为商业用. 杏桃为落叶性植物,可长到约9公尺高,每年2到三月前后,随着叶子抽芽不久,就会开出白色带点红色的花朵,杏桃的嫩叶有着红色叶尖,此一特色使得杏桃更佳吸引人,也使之得以和桃树区别。
植物油特性:杏桃仁油和甜杏仁油其实几乎完全相同,但或许因为产量较少稍微昂贵些。
杏桃仁油的生产过程没什么价值,因此通常在实际榨取开始前,会添加杏仁或樱桃等其他果仁。
桃仁油(又译:杏仁油 Persic oil)是一种将各种杏桃、桃子、樱桃和李子的果仁以冷压法萃取出的植物油。
萃取方法:品质最佳的杏桃仁油,是以冷压果仁的方式所萃取得来的。
民俗疗法与传统用法:磨碎后的果实可以当做面膜以软化肌肤。
蔷薇科的种子如杏桃、桃子和李子都含有大量的苦杏仁素,因此偶尔会发生中毒反应。
传统中医讲杏桃果仁当做止咳药。
止气喘药、治疗肿瘤药。
内服疗效:杏桃仁油和甜杏仁油的用法非常相似,据说它可以有效减少血中胆固醇的含量,且可以作为松弛剂。
外用疗效:对于保护皮肤有很棒的效果,同时也可以软化滋润皮肤。
因为其质地易于吸收,可以缓和因湿疹所引起的瘙痒。
对敏感、干燥和老化的皮肤很有帮助。
化妆品方面的运用:这种油具有美发的功效。
细磨过的壳有时可以当做磨砂膏来去除老旧角质。
习惯上杏桃仁油被使用于化妆品里,因为它具有软化肌肤的功效,也常被使用在肥皂和冷霜中。
注意事项:无毒性反应。
摄取杏桃核仁是氰化物中毒最常见的现象。
因为除非少量添加,杏桃核仁很少被加到杏桃果酱中。
也有报告指出有人曾因接触杏桃核仁而造成皮肤炎。
鳄梨油 Avocado oil学名:Persea gratissima Caertn., P.Americana Mill 科名:樟科(Lauranceae)词源:Persea是希腊文中“树”的意思,而gratissima在拉丁文中代表非常令人喜爱的。
- 1、下载文档前请自行甄别文档内容的完整性,平台不提供额外的编辑、内容补充、找答案等附加服务。
- 2、"仅部分预览"的文档,不可在线预览部分如存在完整性等问题,可反馈申请退款(可完整预览的文档不适用该条件!)。
- 3、如文档侵犯您的权益,请联系客服反馈,我们会尽快为您处理(人工客服工作时间:9:00-18:30)。
US 2004/0055678 A1Mar. 25, 20041EMULSION PHASE HAVING IMPROVED STABILITY乳液稳定性得到改善相[0001] The present invention comprises a method for forming a stable, polymeric emulsifier based, water-in-oil emulsion phase having improved stability following homogenization. 本发明包括形成稳定高分子乳化剂的方法,油包水型乳液在均质化作用后使稳定性得到改善背景[0002] Water-in-oil emulsion explosives, hereafter termed"emulsion explosives乳化炸药," are well-known in the industry. They comprise an emulsified dispersion of a discontinuous phase of inorganic oxidizer salt solution droplets in a continuous organic fuel phase. This dispersion or emulsion phase is heldin place by a water-in-oil emulsifier 乳化剂(hereafter "emulsifier")provided the emulsified state remains stable. The inorganic oxidizer salt solution droplets typically are in a supercooled state and thus want to crystallize and consequently destabiline the emulsified state. Thus if the emulsified state weakphases that are less stable with time than those formed with primarily or solely polymeric emulsifiers, both before and after homogenization均化作用. Thus, where mixtures of polymeric and non polymeric emulsifiers were used, both stability and homogenize ability were compromised to a degree. The present invention allows an emulsion phase to be formed that is both stable and homogenize able.[0004]Based Although polymeric emulsifiers, such as on various adducts of polyisobutenyl succinic those anhydride ("PIBSA"), are found to form stable emulsion phases under certain conditions, emulsion phases containing polymeric emulsifiers tend to destabilize upon homogenization. Efforts at inhibiting such destabilization include replacing a portion of the polymeric emulsifier with nonpolymeric emulsifiers that are less susceptible to homogenization destabilization such as sorbitan monooleate (SMO). The nonpolymeric emulsifiers, however, tend to form emulsion[0003] Destabilization is a common problem when the emulsion explosive is subjected to "working" or is worked," which means to subject the emulsion phase to shearing action such as when the emulsion phase is pumped or otherwise transferred into a borehole or other container or is mixed with additional ingredients such as sensitizing microballoons or AN prills. In explosives applications, an emulsion phase is commonly subjected to working in this fashion and thus the emulsion phase must be able to retainits stability even after working. The formulations disclosed herein have greater stability when subjected to these normal processing and handling conditions. In addition to these common transfer and mixing operations, an emulsion phase may purposely be subjected to very high shear conditions by various means in order to increase the viscosity of the emulsion phase. This process is commonly (and herein) referred to as homogenization. As homogenization occurs, the dispersed oxidizer salt solution droplets become smallerin size and consequently the viscosity of the emulsion phase increases. This viscosity increase oftentimes is desirable because it enables the emulsion explosive to resist water intrusion, retain its stability and remain in the borehole rather than flowing out of an upwardly extending borehole or into cracks or fissures. Along with the viscosity increase and smaller solution droplet size that result from homogenization, however, the propensity of the emulsion phase to experience crystallization increases under such high shear conditions. Thus, for a given composition there is a practical limit to the degree of homogenization that can occur before crystallization becomes unacceptable.[0005] One method for homogenizing emulsion explosives is disclosed in U.S. Pat. No. 4,615,752, which involves positioning a valve at the end of a delivery hose in order to increase the viscosity of the explosive through the shearing action of the valve. In addition, in-fine mixing devices to impart high shear to an emulsion during flow (pumping) are used in the industry, and these can be positioned anywhere within the delivery train of the emulsion. Another method for improving homogenization is disclosed in U.S. Pat. No.5,322,576, which discloses replacing at least a portion of the organic fuel phase with a vegetable oil.ens, the emulsion will destabilize and the salts in the droplets will crystallize, causing further destabilization. This crys- tallization desensitizes the emulsion explosive and can render it undetonableSUMMARY概要[0006] The method of the present invention for forming a stable, polymeric emulsifier-based emulsion phase following homogenization comprises:[0007] (a) forming an inorganic oxidizer salt solution,形成无机氧化剂盐溶液[0008] (b) forming an organic fuel phase which comprises at least about 3% by weight of the fuel phase of an homogenization additive selected from the group consisting of animal oils and fatty acids, [0009] (c) mixing the organic fuel phase and the inorganic oxidizer salt solution phase in the presence of a polymeric emulsifier with sufficient shear to form the emulsion phase,[0010] (d) and then,homogenizing the emulsion phase to increase its viscosity prior to placement or packaging of the product.[0011] The use of an homogenization additive selected from the group consisting of animal oils and fatty acids in an amount of at least about 3% by weight of the organic fuel phase has been found to improve the longterm stability of a homogenized emulsion phase that contains a polymeric emulsifier. In test results shown in the tables below, this stability improvement surprisingly is better than that provided by an organic fuel phase that contains a vegetable oil.DETAITED DESCRIPTION[0012] The method of the present invention involves forming a water-in-oil emulsion phase that comprises a continuous phase of organic liquid fuel, an emulsifier and a discontinuous phase or inorganic oxidizer salt solution. A homogenizing additive is added and other additives may be present as described below. [0013] The organic liquid fuel forming the continuous phase of the emulsion phase is immiscible with water and is present in an amount of from about 3% to about 12%, and preferably in an amount of from about 4% to about 8% by weight of the emulsion phase. The actual amount used can be varied depending upon the particular immiscible fuels) used and upon the presence of other fuels, if any. The immiscible organic liquid fuels can be aliphatic, alicyclic, and/or aromatic and can be saturated and/or unsaturated, so long as they are liquid at the formulation temperature. Preferred fuels include mineral oil, waxes, paraffin oils,benzene, toluene, xylenes, mixtures of liquid hydrocarbons generally referred to as petroleum distillates such as gasoline, kerosene and diesel fuels, and vegetable oils such as corn oil, cottonseed oil, peanut oil, and so沙can oil. Particularly preferred liquid fuels are mineral oil, No. 2 fuel oil, paraffin waxes, microcrystalline waxes, and mixtures thereof. Aliphatic and aromatic vitro-compounds and chlorinated hydrocarbons also can be used. Mixtures of any of the above can be used.[0014] Optionally, and in addition to the immiscible liquid organic fuel, solid or other liquid fuels or both can be employed in selected amounts. Examples of solid fuels which can be used are finely divided aluminum particles; finely divided carbonaceous materials such as gilsonite or coal; finely divided vegetable grain such as wheat; and sulfur. Miscible liquid fuels, also functioning as liquid extenders, are listed below. These additional solid and/or liquid fuels can be added generally in amounts ranging up to about 25% by weight. If desired, undissolved oxidizer salt can be added to the composition along with any solid or liquid fuels.[0015] The inorganic oxidizer salt solution forming the discontinuous phase of the emulsion phase generally comprises inorganic oxidizer salt, in an amount from about 45% to about 95% by weight of the emulsion phase, and water and/or water-miscible organic liquids, in an amount of from about 0% to about 30%. The oxidizer salt preferably is primarily ammonium nitrate休哟,but other salts may be used in amounts up to about 50% of the total salts. The other oxidizer salts are selected from the group consisting of ammonium, alkali and alkaline earth metal nitrates, chlorates and perchlorates. Of these, sodium nitrate (S哟and calcium nitrate (C 哟are preferred. AN and ANFO prills also can be added in solid form as part of the oxidizer salt in the final composition.[0016] Water generally is employed in an amount of from 3% to about 30% by weight of the emulsion phase. It is commonly employed in emulsions in an amount of from about 5% to about 20%, although emulsions can be formulated that are essentially devoid of water.[0017] Water-miscible organic liquids can at least partially replace water as a solvent for the salts, and such liquids also function as a fuel for the composition. Moreover, certain organic compounds also reduce the crystallization temperature of the oxidizer salts in solution. Soluble or miscible solid or liquid fuels can include alcohols such as methyl alcohol, glycols such as ethylene glycols, polyols such as sugars, amides such as formamide, amines, amine nitrates, urea and analogous nitrogen-containing fuels. As is well known in the art, the amount and type of water-miscible liquids) or solids) used can vary according to desired physical properties.[0018] A polymeric emulsifier is used in forming the emulsion and typically is present in an amount of from about 0.2% to about 5% by weight of the emulsion phase. Polymeric water-in-oil emulsifiers are moleculeswhich have a polymeric hydrophobic portion and a polar moiety that serves as the hydrophilic portion. The polymer can be derived from any of a number of monomers such as ethylene, propylene, and isobutene. The hydrophilic moiety can be any polar moiety which is attracted to water or ionic solutions of water such as carboxyl groups, esters, amides, and imides. U.S. Pat. No. 4,820,361 describes a polymeric emulsifier derivatized from tris hydroxy methyl aminomethane and polyisobutenyl succinic anhydride("PIBSA"), which is particularly effective in combination with organic microspheres and is a preferred emulsifier. Other derivatives of polypropene or polybutene have been disclosed. Preferably the polymeric emulsifier comprises polymeric amines and their salts or an amine, alkanolamine or polyol derivative of a carboxylated or anhydride deriva- tized olefinic or vinyl addition polymer. U.S. Pat. No. 4,931,110 discloses a polymeric emulsifier comprising a bis-alkanolamine or bis-polyol derivative or a bis-carboxylated or anhydride derivatized olefinic or vinyl addition polymer in which the olefinic or vinyl addition polymer chain has an average chain length of from about 10 to about 32 carbon atoms, excluding side chains or branching.[0019] Polymeric emulsifiers are known to give excellent shelflife存期to emulsion explosives due to enhanced steric stabilization effected by the hydrophobic portion of the molecules, as compared to conventional water-in-oil emulsifters such as sorbitan monooleate. However, attempts to homogenize polymeric emulsifier-based emulsions generally causes significant crystallization to occur. As previously mentioned, shorter chained water-in-oil emulsifiers such as sorbitan monooleate have been included in the emulsion to improve homogenizeability. These emulsifiers, however, negatively affect the shelf-life orlong-term stability of the emulsion phase both before and after homogenization.[0020] The present invention greatly enhances the ability of a polymeric emulsifier-based emulsion explosive to undergo significant, purposeful homogenization without also undergoing crystallization of the super-cooled internal phase and consequent loss of detonation properties. This is accomplished by adding an homogenization additive to the continuous phase of the emulsion phase to prevent or minimize crystallization during homogenization. The additive is selected from the group consisting of animal oils and fatty acids. The animal oils are rendered from animal fats and preferably are selected from the group consisting of lard oil, tallow oil and poultry oil. The fatty acids can be derived from a number of sources including the hydrolysis of glycerol esters, such as those found in animal oils or vegetable oils or other plant oils or extracts therefrom such as tall oils. The fatty acids can be composed of from 8 to 22 carbon atoms, usually even numbered, and preferably from 14 to 20 carbon atoms, and can be either saturated or unsaturated (olefinic) and solid, semisolid or liquid. Examples of saturated acids are palmitic and stearic acid. Examples of unsaturated acids are oleic or linoleic acid. The additives are present in the amount of from about 3% to about 40% by weight of the organic liquid fuel phase, and more preferably from about 5% to about 15% by weight ofthe organic liquid fuel phase.[0021] One theory as to why the homogenization additives are effective is that they are more mobile (they diffuse or migrate more easily) than the more bulky polymeric emulsifters. Thus, when new interfaces between the internal (oxidizer salt solution phase) and external (organic liquid fuel phase) phases are created by the high shearing action of homogenization, the more mobile animal oils or fatty acids migrate to the interface to stabilize it, thereby promoting the formation of smaller droplet sizes and also preventing crystallization of the internal phase. It is further theorized that the additives gradually are replaced by the more tightly bound (thermodynamically favored) polymeric emulsifiers which impart greater stability to the resulting product. Thus, the additives do not degrade substantially the stability of the emulsion phase either before or after homogenization as does, for example, sorbitan monooleate, which competes as an emulsifier at the droplet interface with the polymeric emulsifier molecules thereby yielding a less stable emulsion. [0022] Homogenization that is purposely effected on an emulsion explosive generally at least doubles its viscosity and more generally increases its viscosity by 3 to 10 times or more. The homogenization of the emulsion explosive (absent any significant crystallization) also increases sensitivity, detonation velocity, column integrity in bulk loaded boreholes, the ability to stay in upwardly loaded boreholes, the stiffness of the rheology in packaged emulsions, and so on. Such properties enhance the performance and function of the emulsion explosive in many applications.[0023] The emulsion phase of the present invention may be formulated in a conventional manner as is known in the art. Typically, the oxidizer salts) first is dissolved in the water (or aqueous solution of water and miscible liquid fuel) at an elevated temperature of from about 25℃to about 90℃. or higher, depending upon the crystallization temperature of the salt solution. The aqueous oxidizer solution then is added to a solutionof the emulsifier, homogenization additive and the immiscible liquid organic fuel, which solutions preferably are at the same elevated temperature, and the resulting mixture is stirred with sufficient vigor to produce an emulsion of the aqueous solution in a continuous liquid hydrocarbon fuel phase. Usually this can be accomplished essentially instantaneously with rapid stirring. (The compositions also can be prepared by adding the liquid organic to the aqueous oxidizer solution.) Stirring should be continued until the formulation is uniform. The formulation process also can be accomplished in a continuous manner as is known in the art. [0024] It is advantageous to pre dissolve the emulsifier in the liquid organic fuel prior to combining the organic fuel with the aqueous solution to form an emulsion. This method allows the emulsion to form quickly and with minimum agitation. However, the emulsifier may be added separately as a third component if desired.[0025] Though not required, microballoons can be added to the emulsion phase to sensitize it to initiation. The microballoons preferably are plastic microspheres having a nonpolar surface and comprising homo-, co- or terpolymers of vinyl monomers. A preferred composition of the plastic microspheres is a thermoplastic copolymer of acrylonitrile and viny lidine chloride乙烯基氯化物. Additionally, the microballons may be made from siliceous (silicate-based), ceramic (aluminosilicate) glass such as soda-lime-borosilicate glass, polystyrene, perlite or mineral perlite material. Further, the surface of any of these microballoons may be modified with organic monomers or homo-, co- or terpolymers of vinyl or other monomers, or with polymers of inorganic monomers. In the emulsion phase, microballoons preferably are employed in an amount of from about 0.1% to about 1% for plastic microballoons or 1% to 6% for glass microballoons. Chemical gassing agents also can be used in the emulsion as is known in the art[0026] The pH of the emulsion phase preferably is from about 2 to about 7, and more preferably from about 3.5 to about 5.0. These pH ranges facilitate chemical gassing and also limit the solubility of the fatty acid (in its basic form) in the aqueous solution, thus preserving the fatty acid in its acid form, which is efficacious for purposes of this invention.[0027] The invention can be illustrated further by reference to the following examples and tables. In the tables the following key applies: "MB" stands for minimum booster in the cylindrical diameter and with the detonator strength indicated. "D" is detonation velocity in the sizes indicated when initiated with a detonator or booster of the strength or size indicated (3C=454 grams pen tolite三硝基甲苯). All detonation velocities are "unconfined" detonation velocities and hence are lower, particularly in smaller charge diameters, than would be their calculated theoretical detonation velocities.[0028] In most examples, the emulsions were formed as described below and then allowed to cool to ambient temperature over one or more days. The emulsion phases then were subjected to homogenization and, in some cases, simultaneous chemical gassing and/or mixing with other ingredients. In some examples, the hot emulsion was formed and then immediately was homogenized and mixed with further components. In some cases the detonation properties of the resulting mixes were determined. The viscosities of the phases were measured before and after homogenization using an HA model Brookfield digital viscometer with a #7 spindle at 20 rpm. In all cases the emulsion phases or final mixes were measured for stability to crystallization using the qualitative grading scale shown in Table 1.EXAMPT,E 1[0029] A series of emulsions were prepared by adding the oxidizer salt solution at an elevated temperature to the mixture of organic liquid fuel and homogenization additive,while stirring at 1500 rpm for two minutes with a Ji助stirrer. The emulsions were stored at ambient temperature overnight and then subjected to high shear by passing them through an inline adjustable shearing valve (mini-kunkle valve) at 160 psi back pressure. The emulsion temperature and viscosity were measured prior to and after homogenization. Also, samples of pre-homogenized emulsion as well as post-homogenized emulsion were stored at ambient temperature and monitored over an 18-week time period for stability (i.e. degree of crystallization). Table 2 shows these results along with the formulation for each emulsion.[0030] Formulation 1 was made with a PIBSA-based polymeric emulsifier but with no co-emulsifier (SMO) or homogenization additive. Although this emulsion was very stable prior to being homogenized, high shear homogenization resulted in heavy crystal formation and an accompanying large temperature increase. The viscosity of the emulsion increased more than three times due to the high crystal formation. Formulations 2 through 6 contain the same ingredients except that 5% of the fuel phase consists of either a co-emulsifier or homogenization additive.[0031] Formulation 2 illustrates the effect of SMO addedto the emulsion. The addition of SMO allowed homogenization to occur without significant crystallization initially, but the pre-homogenized andpost-homogenized emulsion both degraded over time. There was a small temperature rise with no crystals observed while a viscosity increase of about 3.4 times was seen. Formulations 3 and 4 show similar results with corn oil and tall oil (of only approximately 56 percent fatty acid content) added respectively. lations, but a significant improvement is shown in the storage stability of the homogenized emulsion containing animal oil. [0032] Formulations 5 and 6 show the pronounced improvement in both pre-homogenized and post-homog- enized emulsion stability when two different animal oils were added to the emulsion in amounts of 5% of the fuel phase.[0036] While the present invention has been described with reference to certain illustrative examples and preferred embodiments, various modifications will be apparent to those skilled in the art and any such modifications are intended to be within the scope of the invention as set forth in the appended claims. EXAMPT,E 2[0033] Table 3 further illustrates the invention in emulsions made with PIBSA-based polymeric emulsifiers. For-mulation 1 contained no homogenization additive, but For-mulations 2 and 3 contained the animal oils shown. The emulsions were formed as in Example 1 and then, after cooling to ambient temperature overnight, they were subjected to several tests designed to show resistance to crystallization when homogenized: ambient gassing and mixing with ANFO, ambient gassing and mixing with micro balloons, ambient stress mixing concurrent with viscosity measurement, and an AN stability test that consisted in mixing the emulsion with 50 percent KT AN prill and monitoring for crystallization. The ungassed emulsion matrix also was stored at ambient temperatures. Table 3 shows that in each instance an improvement in stability was observed when an animal oil homogenization additive was present.[0034] ature, repumped twice and then subjected to homogenization through a high shear valve at 300 psi back pressureTable 4 contains examples of emulsions produced in a continuous process. Hot oxidizer salt solution was mixed with hot organic liquid fuel in a blender containing rotors and stators and the resulting emulsion was cooled to ambient temper while mixing with microballoons. Formulation 1 contained 10 percent SMO in the fuel phase while Formulation 2 contained 10 percent tall oil of approximately 95 percent fatty acid content. Samples of each formulation were collected before and after homogenization and prior to mixing with microballoons. Aviscosity increase of 9.6 times and 12.5 times was observed for Formulations 1 and 2, respectively, with little crystallization. These samples were monitored over time and found to have similar storage stability, although Formulation 2 exhibited better storage stability following homogenization. These formulations also were detonated and found to have similar detonation properties as shown in Table 4 [0035] Further examples of emulsions produced through a continuous process are illustrated in Table 5. In these examples, 10% of the organic liquid fuel was substituted by either SMO or animal oil. The emulsions were formed similarly to those in Example 3 and then immediately gassed, homogenized, and blended with ANFO. Viscosity increases of 4.4 and 5.6 times were observed for the SMO and animal oil homogenized formulations, respectively. Table 5 shows similar detonation results for the two formulations,but a significant improvement is shown in the storage stability of the homogenized emulsion containing animal oil。