常用齿轮表面处理及力学性能
齿轮渗氮、氮碳共渗工艺及质量控制

齿轮渗氮、氮碳共渗工艺及质量控制
齿轮渗氮是一种提高齿轮表面硬度和耐磨性的表面处理方法,可以通过在齿轮表面注入氮气,使其在表面形成氮化层。
齿轮渗氮的主要工艺包括气体渗氮和盐浴渗氮两种方法。
1. 气体渗氮工艺:气体渗氮是将齿轮置于渗氮炉中,通过加热至高温状态,然后通过氨气或氮气等气体进行渗透处理,使氮原子渗入齿轮表面形成氮化层。
这种工艺具有操作简单、渗透深度可控、成本较低等优点。
2. 盐浴渗氮工艺:盐浴渗氮是将齿轮浸入温度较高的盐浴溶液中进行处理,使盐浴溶液中的氮原子渗透到齿轮表面形成氮化层。
这种工艺渗透速度较快,渗透深度大,但操作复杂,成本较高。
质量控制是齿轮渗氮过程中非常重要的环节,主要包括以下几个方面:
1. 温度控制:温度是齿轮渗氮过程中的重要参数,需要控制在合适的范围内,以保证渗透效果和避免过热损坏齿轮。
2. 渗氮时间控制:渗氮时间是影响氮化层深度和均匀性的重要因素,需要根据齿轮的具体要求和设计要求来确定。
3. 渗氮介质控制:选择合适的渗氮介质对于渗透效果和氮化层质量都有重要影
响,需要根据具体情况进行选择。
4. 清洗和处理后的质量检验:渗氮后需要对齿轮进行清洗和处理,以去除表面的残留物,然后进行质量检验,包括硬度测试、金相分析、氮化层厚度测量等。
通过合理的工艺选择和质量控制,可以确保齿轮渗氮的效果和质量,提高齿轮的使用寿命和性能。
齿轮表面热处理

I齿的转动,带动了II齿 的转动,啮合点A的位置 也会由上而下地在II齿 表面移动直到II齿的根 部。 在啮合点A处还有一个特 点,就是两个齿表面有 相对的滑动,滑动方向 与压应力垂直。
当齿表面磨损到一定程度,就会使两齿的啮合不平稳。
于是,大的噪声、大的振动就会接踵而来,使车床主
轴产生度可达3200℃,用 它加热钢的表面,加热速度快,使钢表层一定深度内加热 到橘红色,大约850℃,而钢的里边温度还不高。
这时,浇上水,表面和里面很快冷却,表层一定深度 内就淬火了,硬度很高,很耐磨,而里面却因为温度低,
淬不上火,硬度就低,韧性好,这不就达到三高了吗?!
在整个齿轮齿面表面淬火后,还不能直接用,因为表 面虽然很硬了,但脆性大,用起来容易裂,也容易崩块。
控制感应线圈对零件的感应加热时间,就可有效地控制加 热温度,待表面达到所需的温度就可将感应线圈移开、喷水, 使零件在加热深度范围内淬火,获得高硬度的淬火层。
对于钢,加热温度850℃以上时,加热深度与感应电 流频率的关系为:
式中,δ f
50 (cm)
f
加热深度(cm) 感应电流频率(Hz)
例如,当f=8000Hz时,加热深度为0.56cm,即5.6mm; 当f=1MHz时,加热深度为0.O5cm,即0.5Omm。
齿轮用感应加热表面淬火法就很 容易达到三高(高耐磨性、高强 度、高韧性)的要求。
无论是碳钢还是合金钢,可以通 过加热和冷却来改变它们的性能。
把 三 块 45 钢 ( 碳 的 质 量 分数为0.45%的一种碳 钢)放在电炉里都加热 到 830℃ , 一 块 取 出 投 入水盆中冷却,一块取 出放在地上在空气中自 然冷却,最后一块就放 在电炉里停了电后让它 同炉子一块冷却。
齿轮渗碳厚度范围
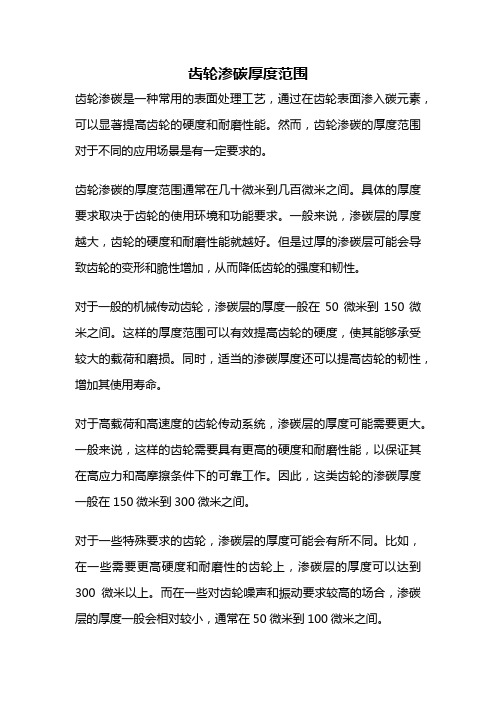
齿轮渗碳厚度范围
齿轮渗碳是一种常用的表面处理工艺,通过在齿轮表面渗入碳元素,可以显著提高齿轮的硬度和耐磨性能。
然而,齿轮渗碳的厚度范围对于不同的应用场景是有一定要求的。
齿轮渗碳的厚度范围通常在几十微米到几百微米之间。
具体的厚度要求取决于齿轮的使用环境和功能要求。
一般来说,渗碳层的厚度越大,齿轮的硬度和耐磨性能就越好。
但是过厚的渗碳层可能会导致齿轮的变形和脆性增加,从而降低齿轮的强度和韧性。
对于一般的机械传动齿轮,渗碳层的厚度一般在50微米到150微米之间。
这样的厚度范围可以有效提高齿轮的硬度,使其能够承受较大的载荷和磨损。
同时,适当的渗碳厚度还可以提高齿轮的韧性,增加其使用寿命。
对于高载荷和高速度的齿轮传动系统,渗碳层的厚度可能需要更大。
一般来说,这样的齿轮需要具有更高的硬度和耐磨性能,以保证其在高应力和高摩擦条件下的可靠工作。
因此,这类齿轮的渗碳厚度一般在150微米到300微米之间。
对于一些特殊要求的齿轮,渗碳层的厚度可能会有所不同。
比如,在一些需要更高硬度和耐磨性的齿轮上,渗碳层的厚度可以达到300微米以上。
而在一些对齿轮噪声和振动要求较高的场合,渗碳层的厚度一般会相对较小,通常在50微米到100微米之间。
齿轮渗碳的厚度范围是根据齿轮的使用环境和功能要求来确定的。
在实际应用中,需要根据具体情况选择合适的渗碳厚度,以保证齿轮的性能和可靠性。
同时,在进行齿轮渗碳处理时,还需要注意控制渗碳的工艺参数,以确保渗碳层的均匀性和一致性,从而提高齿轮的质量和使用寿命。
齿轮材料选择和表面处理__概述说明以及解释

齿轮材料选择和表面处理概述说明以及解释引言部分的内容如下:1. 引言1.1 概述齿轮作为一种常见的传动装置,在各类机械设备中扮演着重要角色。
齿轮材料的选择和表面处理是影响齿轮性能和寿命的关键因素之一。
本文将对齿轮材料选择和表面处理进行系统的概述、说明和解释,以揭示其在工程应用中的意义。
1.2 文章结构本文共分为五个主要部分:引言、齿轮材料选择、齿轮表面处理、实际应用案例分析以及结论与展望。
在“齿轮材料选择”部分,我们将探讨材料性能要求、介绍常见齿轮材料并详细阐述材料选择原则。
接着,在“齿轮表面处理”部分,我们将介绍不同的表面硬化技术,并对表面改性方法与效果进行分析,并提供针对表面处理选择与优化的建议。
随后,在“实际应用案例分析”部分,我们将通过具体案例来探讨齿轮材料选择和表面处理在实际工程中的应用和效果研究。
最后,在“结论与展望”部分,我们将对整篇文章进行总结,并提出当前存在的问题以及未来改进和展望。
1.3 目的本文旨在给读者提供关于齿轮材料选择和表面处理的全面指南。
通过对材料选择和表面处理原理、方法以及实际案例的研究分析,读者将能够更好地理解齿轮材料选择和表面处理在机械设计中的重要性,从而为工程实践提供参考和指导。
通过本文的阅读,读者将掌握到相应技术领域内的基础知识,并能够运用于自己的项目中,以提高设备的传动效率、减少故障率并延长使用寿命。
2. 齿轮材料选择:2.1 材料性能要求:选择适合的齿轮材料需要考虑一系列的性能要求。
首先,齿轮材料应具有足够的强度和硬度,以承受工作条件下的载荷和磨损。
此外,耐疲劳是关键指标之一,因为齿轮通常要经历数以百万计的旋转循环。
良好的耐蚀性也很重要,在潮湿或腐蚀环境中工作时,这可以有效延长齿轮的使用寿命。
温度和摩擦系数也会对材料选择产生影响,特别是在高温或高速运动下。
2.2 常见齿轮材料介绍:常用的齿轮材料包括钢、铸铁、铜合金和塑料。
钢具有出色的强度和韧性,并且适用于大多数应用场景。
齿轮的材料及热处理方法

齿轮的材料及热处理齿轮的材料渗碳硬化钢这是指低碳合金钢。
含碳量为 0.15% ∼ 0.20% 的钢中添加了 Ni,Cr,Mo,Mn 等元素,通过渗碳淬火处理提高表面硬度后使用。
在日本,一般使用的材料如下表所示。
铝青铜铸造合金青铜铸造合金机械结构用碳素钢钢材最为普及的材料,亦是本公司使用最多的材料。
可以施加高频淬火处理。
铬钼钢钢材经过淬火,回火,高频淬火后使用。
淬火对轮齿表面进行硬化处理以提高轮齿强度。
方法有很多,具有代表性的有以下几种。
渗碳淬火渗碳 => 淬火 => 洗净 => 回火 => 喷砂处理 => 检查【方法】一般使用碳酸气进行气体渗碳。
- 表面硬度⋯⋯⋯ 55 - 60HRC- 硬化深度⋯⋯⋯ 1.0 ㎜左右(使用负载越大,硬化层就需越深)低碳合金钢在渗碳环境中加热到转变点以上并保持这个温度,碳素从表面渗入。
碳素渗入后,与 S45C 等在同等条件下进行淬火处理,表面硬度提高。
【特点】由表面到中心部,硬度由硬到软连续变化,所以表面硬而内部富有韧性。
材料一般使用 SCM415 等。
左图 / 渗碳淬火炉右图 / 齿轮的淬火层高频淬火【方法】调质材 => 淬火 => 回火【特点】只有被感应圈所加热的周围产生硬化。
根据形状使用各种不同的感应器,不熟悉的话,会产生裂纹及翘曲变形。
为了防止淬火裂纹,使用含硫,含磷量少的材料。
通常,含碳量在 0.55% 以下的材料产生淬火裂纹的可能性比较小。
材料牌号有 S45C,SCM440 等等。
左图 / 淬火设备右图 / 回火炉。
齿轮热处理

齿轮热处理
齿轮热处理是在特定的温度环境下,对齿轮表面进行热处理,以提高齿轮的物理和力学性能的一种处理方法。
它主要包括硬化、淬火、回火和正火等多种处理方式,以有效改善材料的硬度、强度、延性、疲劳性能、耐磨性和抗腐蚀性能。
齿轮热处理可以分为局部热处理和综合热处理。
局部热处理是指对部分齿轮面进行热处理以改变齿轮表面的组织,从而改变部分或全部材料的性能。
综合热处理则指不仅仅是表面热处理,而是对整个齿轮材料进行热处理,从而影响材料的内部组织。
硬化是齿轮热处理的一种,既可以在表面硬化,也可以综合硬化。
表面硬化主要使用气体燃烧、激光热处理、散热弹、激光诱导等多种方式,将齿轮表面层处理硬度提高,从而改善齿轮外形精度、疲劳强度、耐磨耗和使用寿命。
局部硬化处理也可以改善接合面和精加工部位的疲劳性能。
综合热处理可以分为淬火、正火和回火等几种方式。
淬火是将铁素体材料在较高温度环境中,可以使材料硬度更高,但延性会降低;正火可以使齿轮表面层硬度、强度和延性得到改善,但要求环境非常严格;回火是把淬火或正火的齿轮在低温环境下加热到一定温度,以稳定材料组织,改善物理力学性能和抗腐蚀性能。
齿轮热处理有利于改善齿轮物理和力学特性,提高齿轮耐磨性和抗腐蚀性,延长使用寿命,减少噪音,并有助于建立齿轮耐磨损、耐氧化和耐腐蚀性的技术规范。
因此,表面处理对齿轮的性能特性有着重要的作用,在设计和制造齿轮有重要的意义。
齿轮热处理

DI— 某一钢材在冷却速度为无穷大的 冷却介质中淬火后,其钢材中心部分 获得50%马氏体组织时的最大直径
表38
钢在各种常用淬火剂中的冷却速度和冷却强度
在下列温度区间的最高冷却速 度/(℃/s) 650~550℃ 300℃ 85 85 70 5 6 9 80 45 30 以20℃水为标准的相对冷却强 度H 650~550℃ 1.00 0.79 0.54 0.19 0.30 0.40 0.69 0.60 0.52 300℃ 1.00 1.00 0.82 0.06 0.07 0.11 0.94 0.53 0.35
汽化热
蒸汽压
添加剂的影响
添加剂
温 度
外界因素的影 响 冷却条件
表40 冷却条件对冷却强度的影响
冷 却 强 度 H 冷却状态
空 气
静 止 轻微搅动 缓慢搅动 中等搅动 强烈搅动 激烈搅动 端淬喷水 0.02
油
0.25~0.30 0.30~0.35 0.35~0.40 0.40~0.50 0.50~0.80 0.80~1.10 -
图20 要求的最低硬度与调质钢强度之间的关系
相对硬度值的大小对调质钢的强度、塑性和韧性有影响,特别是在高强度时 这种影响就显得更大,图21给出了这种关系。
图21 相对淬火硬度对力学性能的影响
3.3.3 齿轮钢材的调质深度 表44 已知钢材及圆棒直径求截面硬度分布的方法
求作方法步骤 参 考 图
已知: 求
Dc—在某一冷却介质中淬火后能获得 完全淬透的最大截面直径 例: Dc 水 =37.5mm ,表示这种钢在水 中淬火的临界直径为37.5mm
临 界 直 径 法
理 想 临 界 直 径 计算法
通过 钢材的化学成分和本质晶粒度来计算其淬透性 DI=DIc×FSi×FMn×FCr×FMo×…… 式中: DI—理想临界直径(mm) DIc—碳钢在不同含碳量及晶粒度时的理想临界直径( mm) FSi—合金元素Si一定含量时的淬透性系数(FMn、 FCr……意 义相同)
齿轮所有热处理总结-

--齿轮热处理例如:30CrMnTi 调质275~310HB,齿轮表面淬火58~63HRC,淬火深度1~2mm一、工作条件以及材料与热处理要求1.条件: 低速、轻载又不受冲击要求: HT200 HT250 HT300 去应力退火2.条件: 低速(<1m/s)、轻载,如车床溜板齿轮等要求: 45 调质,HB200-2503.条件: 低速、中载,如标准系列减速器齿轮--要求: 45 40Cr 40MnB (5042MnVB) 调质,HB220-2504.条件: 低速、重载、无冲击,如机床主轴箱齿轮要求: 40Cr(42MnVB) 淬火中温回火HRC40-455.条件: 中速、中载,无猛烈冲击,如机床主轴箱齿轮要求: 40Cr、40MnB、42MnVB 调质或正火,感应加热表面淬火,低温回火,时效,HRC50-556.条件: 中速、中载或低速、重载,如车床变速箱中的次要齿轮要求: 45 高频淬火,350-370℃回火,HRC40-45(无高频设备时,可采用快速加热齿面淬火)7.条件: 中速、重载要求: 40Cr、40MnB(40MnVB、42CrMo、40CrMnMo、40CrMnMoVBA)淬火,中温回火,HRC45-50.8.条件: 高速、轻载或高速、中载,有冲击的小齿轮要求: 15、20、20Cr、20MnVB渗碳,淬火,低温回火,HRC56-62.38CrAl 38CrMoAl 渗氮,渗氮深度0.5mm,HV900 9.条件: 高速、中载,无猛烈冲击,如机床主轴轮.要求: 40Cr、40MnB、(40MnVB)高频淬火,HRC50-55.10.条件: 高速、中载、有冲击、外形复杂和重要齿轮,如汽车变速箱齿轮(20CrMnTi淬透性较高,过热敏感性小,渗碳速度快,过渡层均匀,渗碳后直接淬火变形较小,正火后切削加工性良好,低温冲击韧性也较好)要求: 20Cr、20Mn2B、20MnVB渗碳,淬火,低温回火或渗碳后高频淬火,HRC56-62.18CrMnTi、20CrMnTi(锻造→正火→加工齿轮→局部镀同→渗碳、预冷淬火、低温回火→磨齿→喷丸)渗碳层深度1.2-1.6mm,齿轮硬度HRC58-60,心部硬度HRC25-35.表面:回火马氏体+残余奥氏体+碳化物.中心:索氏体+细珠光体11.条件: 高速、重载、有冲击、模数<5要求: 20Cr、20Mn2B 渗碳、淬火、低温回火,HRG56-62.12.条件: 高速、重载、或中载、模数>6,要求高强度、高耐磨性,如立车重要螺旋锥齿轮要求: 18CrMnTi、20SiMnVB 渗碳、淬火、低温回火,HRC56-6213.条件: 高速、重载、有冲击、外形复杂的重要齿轮,如高速柴油机、重型载重汽车,航空发动机等设备上的齿轮.要求: 12Cr2Ni4A、20Cr2Ni4A、18Cr2Ni4W A、20CrMnMoVBA(锻造→退火→粗加工→去应力→半精加工→渗碳→退火软化→淬火→冷处理→低温回火→精磨)渗碳层深度1.2-1.5mm,HRC59-62.14.条件: 载荷不高的大齿轮,如大型龙门刨齿轮要求: 50Mn2、50、65Mn 淬火,空冷,HB≤24115.条件: 低速、载荷不大,精密传动齿轮.要求: 35CrMO 淬火,低温回火,HRC45-5016.条件: 精密传动、有一定耐磨性大齿轮.要求: 35CrMo 调质,HB255-302.17.条件: 要求抗磨蚀性的计量泵齿轮.要求: 9Cr16Mo3VRE 沉淀硬化18.条件: 要求高耐磨性的鼓风机齿轮.要求: 45 调质,尿素盐浴软氮化.19.条件: 要求耐、保持间隙精度的25L油泵齿轮。
- 1、下载文档前请自行甄别文档内容的完整性,平台不提供额外的编辑、内容补充、找答案等附加服务。
- 2、"仅部分预览"的文档,不可在线预览部分如存在完整性等问题,可反馈申请退款(可完整预览的文档不适用该条件!)。
- 3、如文档侵犯您的权益,请联系客服反馈,我们会尽快为您处理(人工客服工作时间:9:00-18:30)。
齿轮常用表面处理及力学性能
为了保证齿轮工作的可靠性,提高其使用寿命,齿轮的材料及其热处理应根据工作条件和材料的特点来选取。
对齿轮材料的基本要求是:应使齿面具有足够的硬度和耐磨性,齿心具有足够的韧性,以防止齿面的各种失效,同时应具有良好的冷、热加工的工艺性,以达到齿轮的各种技术要求。
常用的齿轮材料为各种牌号的优质碳素结构钢、合金结构钢、铸钢、铸铁和非金属材料等。
一般多采用锻件或轧制钢材。
当齿轮结构尺寸较大,轮坯不易锻造时,可采用铸钢;开式低速传动时,可采用灰铸铁或球墨铸铁、低速重载的齿轮易产生齿面塑性变形,轮齿也易折断,宜选用综合性能较好的钢材;高速齿轮易产生齿面点蚀,宜选用齿面硬度高的材料;受冲击载荷的齿轮,宜选用韧性好的材料。
对高速、轻载而又要求低噪声的齿轮传动,也可采用非金属材料、如夹布胶木、尼龙等。
常用的齿轮材料及其力学性能列表
钢制齿轮的热处理方法主要有以下几种:
●表面淬火表面淬火常用于中碳钢和中碳合金钢,如 45、 40Cr 钢等。
表面淬火后,齿面硬度一般为40~55HRC。
特点是抗疲劳点蚀、抗胶合能力高。
耐磨性好;由于齿心部分未淬硬,齿轮仍有足够的韧性,能承受不大的冲击载荷。
●渗碳淬火渗碳淬火常用于低碳钢和低碳含金钢,如 20、 20Cr 钢等。
渗碳淬火后齿面硬度可达56~62HRC,而齿轮心部仍保持较高
的韧性,轮齿的抗弯强度和齿面接触强度高,耐磨性较好,常用于受冲击载荷的重要齿轮传动。
齿轮经渗碳淬火后,轮齿变形较大,应进行磨削加工。
●渗氮渗氮是一种表面化学热处理。
渗氮后不需要进行其他热处理,齿面硬度可达700~900HV。
由于渗氮处理后的齿轮硬度高,工艺温度低,变形小,故适用于内齿轮和难以磨削的齿轮,常用于含铅、钼、铝等合金元素的渗氮钢,如38CrMoAl等。
●调质调质一般用于中碳钢和中碳合金钥,如45、40Cr、35SiMn 钢等。
调质处理后齿面硬度一般为220~280HBS。
因硬度不高,轮齿精加工可在热处理后进行。
●正火正火能消除内应力,细化晶粒,改善力学性能和切削性能。
机械强度要求不高的齿轮可采用中碳钢正火处理,大直径的齿轮可采用铸钢正火处理。
根据热处理后齿面硬度的不同,齿轮可分为软齿面齿轮(≤350HBS)和硬齿面齿轮(>350HBS)。
一般要求的齿轮传动可采用软齿面齿轮。
为了减小胶合的可能性,并使配对的大小齿轮寿命相当,通常使小齿轮齿面硬度比大齿轮齿面硬度高出30~50HBS。
对于高速、重载或重要的齿轮传动,可采用硬齿面齿轮组合,齿面硬度可大致相同。