曲柄连杆机构的检测
曲柄连杆机构的故障原因及检查方法
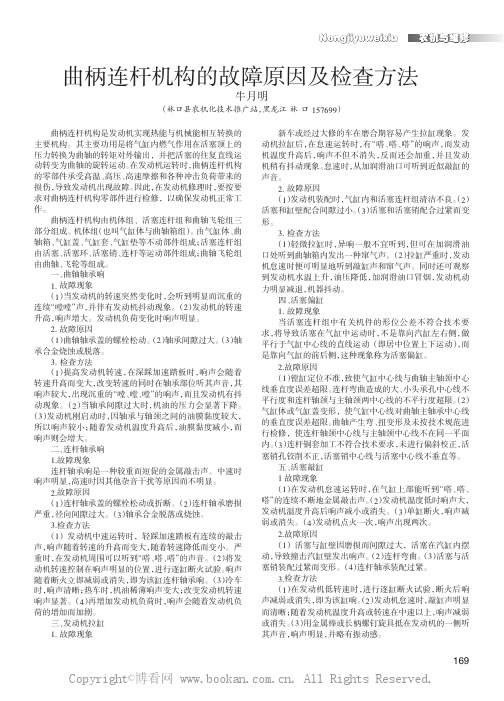
N o n g j i y u w e i x i u曲柄连杆机构是发动机实现热能与机械能相互转换的主要机构。
其主要功用是将气缸内燃气作用在活塞顶上的压力转换为曲轴的转矩对外输出,并把活塞的往复直线运动转变为曲轴的旋转运动。
在发动机运转时,曲柄连杆机构的零部件承受高温、高压、高速摩擦和各种冲击负荷带来的损伤,导致发动机出现故障。
因此,在发动机修理时,要按要求对曲柄连杆机构零部件进行检修,以确保发动机正常工作。
曲柄连杆机构由机体组、活塞连杆组和曲轴飞轮组三部分组成。
机体组(也叫气缸体与曲轴箱组)。
由气缸体、曲轴箱、气缸盖、气缸套、气缸垫等不动部件组成;活塞连杆组由活塞、活塞环、活塞销、连杆等运动部件组成;曲轴飞轮组由曲轴、飞轮等组成。
一、曲轴轴承响1.故障现象(1)当发动机的转速突然变化时,会听到明显而沉重的连续“嘡嘡”声,并伴有发动机抖动现象。
(2)发动机的转速升高,响声增大。
发动机负荷变化时响声明显。
2.故障原因(1)曲轴轴承盖的螺栓松动。
(2)轴承间隙过大。
(3)轴承合金烧蚀或脱落。
3.检查方法(1)提高发动机转速,在深踩加速踏板时,响声会随着转速升高而变大,改变转速的同时在轴承部位听其声音,其响声较大,出现沉重的“嘡、嘡、嘡”的响声,而且发动机有抖动现象。
(2)当轴承间隙过大时,机油的压力会显著下降。
(3)发动机刚启动时,因轴承与轴颈之间的油膜黏度较大,所以响声较小;随着发动机温度升高后,油膜黏度减小,而响声则会增大。
二、连杆轴承响1.故障现象连杆轴承响是一种较重而短促的金属敲击声。
中速时响声明显,高速时因其他杂音干扰等原因而不明显。
2.故障原因(1)连杆轴承盖的螺栓松动或折断。
(2)连杆轴承磨损严重,径向间隙过大。
(3)轴承合金脱落或烧蚀。
3.检查方法(1)发动机中速运转时,轻踩加速踏板有连续的敲击声,响声随着转速的升高而变大,随着转速降低而变小。
严重时,在发动机周围可以听到“嗒、嗒、嗒”的声音。
汽车发动机机械维修 任务三 曲柄连杆机构的监测与维修

三、学习项目Leabharlann 四 、资料收集引导问题1 曲柄连杆机构的作用及组成是什么?
曲柄连杆机构由机体组、活塞连杆组和曲轴飞轮组三部分组成(图3-1)。
3-8-d 飞轮安装面
水冷发动机的汽缸体和曲轴箱制为一体且多缸发动机的各个汽缸 也和铸成一体(图3-9),称为汽缸体-曲轴箱,简称汽缸体。
图3-9 汽缸体 TU5JP4发动机汽缸体技术参数,其中A处为识别标记(维修尺寸),见表3-4。 TU5JP4发动机汽缸体技术参数表 表3-4 尺寸(mm) ØC(0,+0.03) B(-0.05,+0.05) 标准尺寸 78.5 265.23 维修尺寸 78.9 265.03
学习任务三 曲柄连杆机构的检测与维修
一、学习目标
通过本章的学习,你应该能:
1、叙述曲柄连杆机构的基本构造和工作原理; 2、明确汽缸、连杆、曲轴、活塞等主要部件的检测 及维修方法; 3、明确活塞连杆的拆装工艺与活塞环的拆装工艺; 4、正确地使用工具和设备; 5、与同学密切合作,规范地拆装汽缸盖;
二、学习任务描述
类 型 特 性 壁 厚 与汽缸的配合 关系 过盈配合 间隙配合 定 位 干式汽缸 套 湿式汽缸 套 不与冷却水接触 与冷却水接触,其外装有耐油、耐热 橡胶密封圈 1~3mm 5~9mm 过盈配合 上部凸缘的支承 平面
表3-5
装配要求 检查圆度和圆柱度误 差 高出汽缸体0.05~ 0.15mm
4.油底壳 油底壳的功用是储存机油并密封曲轴箱。油底壳的其底部装有磁性的放油 螺栓,用来放油和吸附润滑油中的铁屑,减少发动机的磨损(图3-13)。 放油螺塞下的密封垫为一次性件,拆后换新的;油底壳漏油多半是油底壳 衬垫出现老化、裂纹或折断,导致漏油现象发生,所以油底壳漏油时要更 换油底壳衬垫。
2.2曲柄连杆机构的性能检测
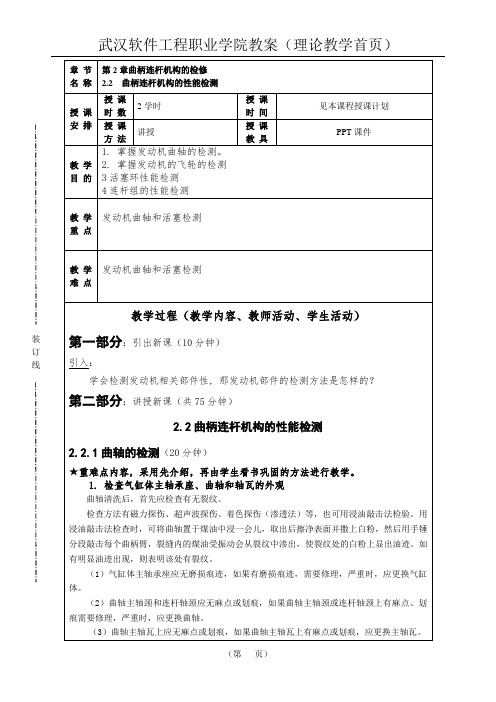
(3)曲轴主轴瓦上应无麻点或划痕,如果曲轴主轴瓦上有麻点或划痕,应更换主轴瓦。
2. 曲轴径向跳动值检测
用百分表和 V 形块测量径向跳动值。曲轴放置V型块上,用百分表测量中间主轴颈处,转动曲轴一圈,百分表指针所示最大摆差,即径向圆跳动。
章节名称
第2章曲柄连杆机构的检修
2.2曲柄连杆机构的性能检测
授课安排
授课
时数
2学时
授课时间
见本课程授课计划
授课
方法
讲授
授课教具
PPT课件
教学目的
1. 掌握发动机曲轴的检测。
2. 掌握发动机的飞轮的检测
3活塞环性能检测
4连杆组的性能检测
教学重点
发动机曲轴和活塞检测
教学
难点
发动机曲轴和活塞检测
教学过程(教学内容、教师活动、学生活动,应更新齿圈。新齿圈采用热装配法,即先将齿圈加热至623K-673K,再进行热压装配;齿圈与飞轮配合过盈为0.30-0.60mm,如图2.78齿圈与飞轮的装配检测。
更换齿圈后,对飞轮进行静平衡试验,不平衡量不超过10g•cm。
2.2.3活塞环性能检测(20分钟)
最大轴向间隙:0.18 mm (0.0071 in.)
如果轴向间隙大于最大值,则成套更换止推垫圈。
2.2.2飞轮的检测(15分钟)
1.飞轮平面度误差的检测
(1)清洁飞轮齿圈表面及量具。
(2)检查飞轮工作表面是否有明显的划伤沟槽。当飞轮端面磨损成波浪形或起槽深度超过0.5mm时,应采用车削或磨削的方法修平。
(5)分别推动两表检测头,检查百分表指针是否转动自如。再将两表归零,如图2.86所示。
技能点5 能正确检测与维修曲柄连杆机构

汽车发动机维修 气缸体平面度检测
维修方法 ✓ 气缸体变形的修理
汽车发动机维修
在整个平面上,
平面度误差较
平面度误差不大于 大时,可采用平面
0.05mm,或仅有 磨床磨削加工修复
局部凸起,可用刮 或在铣床上铣削加
刀刮平。
工。
用高度游标卡 尺测量上下平面, 磨削量不能超过 0.24~0.50mm, 影响压缩比,不能 使用。
(4)漏光度 活塞环漏光度检查
汽车发动机维修
➢ 同一环上漏光不大于两处,每处漏光弧长所 对应的圆心角总和不大于45度。
➢ 活塞环开口两端各30度范围内不允许有漏光。 ➢ 漏光度的最大缝隙不大于0.03毫米。
(5)活塞环侧隙的检验
测量的方法 将环放在槽内,围绕
槽滚动一周,应能自由滚 动,既不能松动,又不能 有阻滞现象。
将气缸盖(气缸体)放在干净的 检验平台上,把等于或大于气缸体对 角线长度的刀口尺放到气缸体被测平 面上,将适当厚度的塞尺塞入尺子与 气缸体平面之间的缝隙中,稍用力能 拉动尺子,读塞尺厚度,记录。沿气 缸盖(气缸体)平面的横向、纵向、 对角线方向、多处测量,求平面度误 差。测量过程中,观察气缸体平面的 局部凸起,并作记录。
汽车发动机维修
(6)活塞环端隙的检验
汽车发动机维修
测量的方法 先将活塞环平整地放
在待配的气缸内,用活塞 头将活塞环推平,然后用 厚薄规插入活塞环开口处 进行测量。
(7)活塞环背隙的检验
测量的方法
测量活塞环槽直径d, 测量气缸直径D,测量活 塞环宽度b,活塞环背隙 =(D-d)/2-b(mm)。
(2)弹力 • 弹力过大使环的磨损加剧;弹力过弱,气缸密封性能差,燃料消耗
增加,积碳严重。
曲柄连杆机构的测量
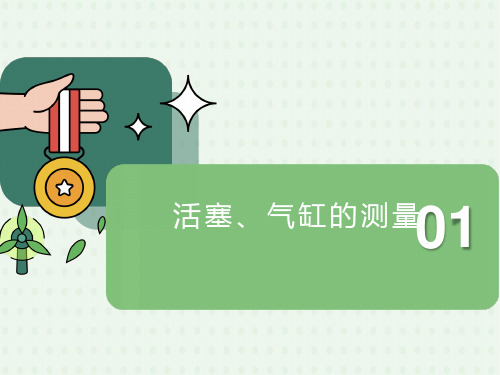
5
0
0
45
答案:L= 1+ 0 + 0.004 = 1.004 mm
7、请你读出下列测量结果:
0.905
45
40
0
35
答案:L= 0+ 0.5 + 0.405 = 0.905 mm
活塞的检测
检测工具:外径千分尺
方法:用千分尺在活塞下边缘的测 量点A处与活塞销轴线成90度角测量 活塞直径。 注:点A位置与发动机类型有关。参 见维修手册。一般为10mm左右。
百分表使用之前应检查其灵敏状况,检查方 法是用手指连续压缩百分表活动探头数次,应 没有卡滞现象,且松开后百分表指针每次都能 回到原位。
活动探头
b.量缸表灵敏度检验
将百分表装在量缸表表杆上,使百分表表面 与活动测杆在同一方向,且表针应有1/2~1圈 左右的预压量,并锁紧螺母固定百分表。
根据气缸的直径选择合适的接杆固定在量缸 表下端。接杆固定好后与活动测杆的总长度应 比被测气缸的直径大1.5~2mm左右。
10
111000 1100
4.读数
主尺数+游尺数
0
1
2
3
0
5
10
测砧
弓形尺架
测微螺杆
固定套筒
活动套管
微分筒
锁紧装置
棘轮 螺钉
使用方法
测量之前------擦试干净量具, 校对零位,看零位是否重合,如有 偏差要进行调整;
读数时最好不要取下千分尺,如 需取下,要进行锁紧后,再轻轻 取下,防止尺寸变动。
45
02 调 零 准 确 0
4、螺旋测微器的读数原理:
整刻度: 每刻度为
1mm
半刻度:每刻度为 0.5mm
项目三、曲柄连杆机构的检测与维修(理论知识)

活塞销偏置是的工作情况
(二)活塞环
是具有弹性的开口环,分为气环和油环。 工作条件:
高温、高压、高速、极难润滑。 平均寿命:
6万公里 材料:
合金铸铁或球墨铸铁(有时表面涂有保护层)
(1)气环
作用:保证气缸与活塞间的密封性,防止 漏气,并把活塞顶部吸收的大部分热量传 给气缸壁,再由冷却水将其带走。
活塞应具备的特点
A 刚度和强度应足够大,传力可靠。 B 导热性能好,耐高压、高温、磨损 活塞应具备 C 质量较小,尽可能减少往复惯性力 的特点 D 耐热的活塞顶及弹性的活塞裙 E 活塞与气缸壁间有较小的摩擦系数
4、结构
(1)活塞顶部
功用:是燃烧室的组成部分,主要作用承受气体压力。
顶部:构成燃烧室,承 受气体压力。
二、曲轴
1、功用:把活塞连杆组传来的气体压力转变为扭矩对外输 出。还用来驱动发动机的配气机构及其他各种辅助装置。
2、工作条件:受气体压力、惯性力、惯性力矩。承受交变 载荷的冲击。
3、结构:
连杆轴颈 前端轴
曲轴轴颈
平衡重
后端轴
曲柄
曲拐
曲拐:由一个连杆轴颈和它两端曲柄及主轴颈构成。
4、材料:中碳钢(汽)、合金铸铁(柴)、球墨铸铁。
气缸盖罩 气缸垫 油道和水道 曲轴箱
油底壳
(一)、气缸体
1、气缸体:水冷发动机的气缸体和上曲轴箱
常铸成一体,称为气缸体——曲轴箱
2、气缸体分类
(1)按气缸体与油底壳安装平面位置不同分为
油底壳安 装平面和 曲轴旋转 中心在同 一高度
一般式
油底壳安装平
龙门式面低于曲轴的隧道式
旋转中心
气缸体上曲 轴的主轴承 孔为整体式
项目4 发动机曲柄连杆机构的检测与维修

【任务学习】
2.2曲轴的拆解 2.2.1曲轴结构及作用 曲轴由曲轴前端、连杆轴颈、主轴颈、曲柄、
平衡块和曲轴后端凸缘组成。如下图所示。 曲轴的作用是把活塞的直线运动转换成旋转运
动。
【任务学习】
曲轴有主轴颈和曲柄销硬化处理使其持久和耐 磨,为了平衡旋转的曲轴还必须设计有平衡重。 主轴颈和曲柄销上铸有油孔,如下图所示,机 油从气缸体主油道流入,进入主轴颈油孔,穿 过油道到曲柄销。
【任务学习】
2.4 曲轴主轴承轴瓦检测与维修 为改变曲轴主轴颈油膜间隙精度,防止异常噪
音和咬死以及保持良好的燃油经济性须选择相 应尺寸的轴承,此时就必须根据曲轴轴径实际 尺寸选择对应的轴瓦尺寸代码。 一般当尺寸代码数值增大时,轴承厚度以微米 为单位增加。当曲轴主轴颈磨损,或油膜间隙 变大时,可改用较厚尺寸的轴承。
【任务学习】
3.气环切口形状 直角型:工艺性好,
密封性差; 阶梯形:密封性好,
工艺性差; 斜切口:密封性和工
艺性介于上述二者之 间。 如右图气环切口。
【任务学习】
4.气环断面形状分类 矩形环 锥面环 扭曲环 梯形环 桶面环 如右图所示。
【任务学习】
5.油环 油环分为普通环和组合环,组合环通常由一个
1.1活塞连杆组的拆解 1.1.1活塞连杆组的作用 活塞连杆组将活塞的往复运动变为曲轴的旋转
运动,同时将作用在活塞上的力转变为曲轴的 对外输出转矩,以驱动汽车车轮转动。活塞的 顶部还与气缸盖、气缸壁共同组成燃烧室。
【任务学习】
1.1.2 活塞 活塞的作用是承受气体压力,并将此力传给连
杆,以推动曲轴旋转。活塞顶部与气缸盖下表 面、气缸壁共同组成燃烧室。 根据其作用,活塞可分为顶部、环槽部、裙部 和活塞销座四部分。
曲柄连杆机构的检测
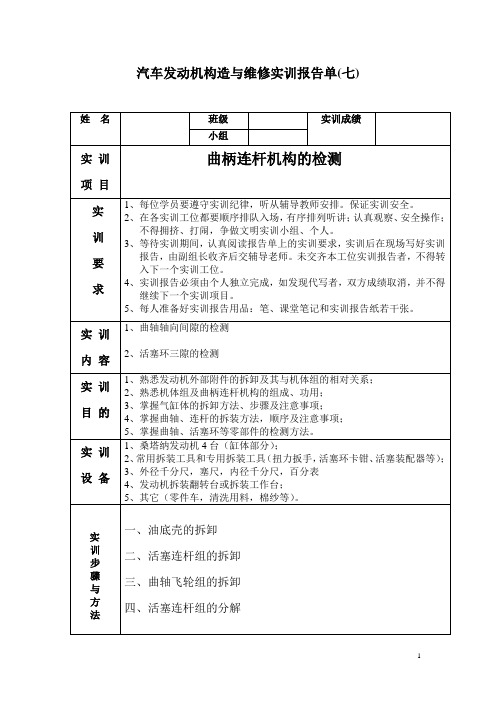
汽车发动机构造与维修实训报告单(七)
姓名
班级
实训成绩
小组
实训
项目
曲柄连杆机构的检测
实
训
要
求
1、每位学员要遵守实训纪律,听从辅导教师安排。保证实训安全。
曲轴轴向间隙实测值:
是否超限:(2)调整方法:源自曲轴轴向间隙一般为0.05~0.20mm。如轴向间隙过小,会使机件膨胀而卡着;轴向间隙过大,易形成轴向窜动,则给活塞连杆组的机件带来不正常的磨损。因此,当轴向间隙值逾限时,则应用更换或修整止推轴瓦或止推垫圈来进行调整。
(三)活塞环端隙的检验:
端隙又叫“开口间隙”。一般第一道环稍大,二、三道环稍小。组合环的刮片端隙可稍大。检验的方法是将环装在气缸内,用厚薄规测量其开口间隙值即可。
(四)活塞环侧隙的检验:
侧隙即活塞环的槽宽度尺寸与活塞环厚度之代数差。此间隙是保证活塞环正常工作,防止“卡死”,产生背压的条件。检验方法:将活塞环放在活塞的环槽内,围绕环槽滚动一周,应能自由滚动。用厚薄规检验其间隙应符合规定。
标准环槽间隙:
第一道环槽为0.03-0.08mm;
第二道环槽为0.03-0.07mm;
测量范围色别
0.025~0.076mm绿
0.050~0.150mm红
0.100~0.230mm蓝
②通用量具检验法:
用内径千分尺和外径千分尺分别测量轴颈的外径和轴承的内径,测得的这两个尺寸的差,就是它们之间的间隙。连杆轴承径向间隙的检查与曲轴轴承方法相似。
- 1、下载文档前请自行甄别文档内容的完整性,平台不提供额外的编辑、内容补充、找答案等附加服务。
- 2、"仅部分预览"的文档,不可在线预览部分如存在完整性等问题,可反馈申请退款(可完整预览的文档不适用该条件!)。
- 3、如文档侵犯您的权益,请联系客服反馈,我们会尽快为您处理(人工客服工作时间:9:00-18:30)。
0.025~0.076mm绿
0.050~0.150mm红
0.100~0.230mm蓝
②通用量具检验法:
用内径千分尺和外径千分尺分别测量轴颈的外径和轴承的内径,测得的这两个尺寸的差,就是它们之间的间隙。连杆轴承径向间隙的检查与曲轴轴承方法相似。
(二)
曲轴径向间隙
第一道
第二道
第三道
第四道
第五道
实测值
(二)曲轴轴向间隙的检查与调整
(1)检查方法:
①把带磁力底座的百分表固定在发动机前面或者后面的缸体上;
②把百分表杆部平行于曲轴中心线放置,调整表针;
③前后撬动曲轴,观察百分表读数。其最大值与最小值之差即为此曲轴的轴向间隙。
曲轴轴向间隙也可用另一方法进行检查:将曲轴定位轴肩和轴承的承推端面的一面靠合,用撬棒将曲轴挤向后端,然后用厚薄规在曲轴臂与止推轴瓦或止推垫圈之间测得。
4、掌握曲轴、连杆的拆装方法,顺序及注意事项;
5、掌握曲轴、活塞环等零部件纳发动机4台(缸体部分);
2、常用拆装工具和专用拆装工具(扭力扳手,活塞环卡钳、活塞装配器等);
3、外径千分尺,塞尺,内径千分尺,百分表
4、发动机拆装翻转台或拆装工作台;
5、其它(零件车,清洗用料,棉纱等)。
汽车发动机构造与维修实训报告单(七)
姓名
班级
实训成绩
小组
实训
项目
曲柄连杆机构的检测
实
训
要
求
1、每位学员要遵守实训纪律,听从辅导教师安排。保证实训安全。
2、在各实训工位都要顺序排队入场,有序排列听讲;认真观察、安全操作;不得拥挤、打闹,争做文明实训小组、个人。
3、等待实训期间,认真阅读报告单上的实训要求,实训后在现场写好实训报告,由副组长收齐后交辅导老师。未交齐本工位实训报告者,不得转入下一个实训工位。
4、实训报告必须由个人独立完成,如发现代写者,双方成绩取消,并不得继续下一个实训项目。
5、每人准备好实训报告用品:笔、课堂笔记和实训报告纸若干张。
实训
内容
1、曲轴轴向间隙的检测
2、活塞环三隙的检测
实训
目的
1、熟悉发动机外部附件的拆卸及其与机体组的相对关系;
2、熟悉机体组及曲柄连杆机构的组成、功用;
3、掌握气缸体的拆卸方法、步骤及注意事项;
(四)活塞环侧隙的检验:
侧隙即活塞环的槽宽度尺寸与活塞环厚度之代数差。此间隙是保证活塞环正常工作,防止“卡死”,产生背压的条件。检验方法:将活塞环放在活塞的环槽内,围绕环槽滚动一周,应能自由滚动。用厚薄规检验其间隙应符合规定。
标准环槽间隙:
第一道环槽为0.03-0.08mm;
第二道环槽为0.03-0.07mm;
实
训
步
骤
与
方
法
实
训
步
骤
与
方
法
实
训
步
骤
与
方
法
一、油底壳的拆卸
二、活塞连杆组的拆卸
三、曲轴飞轮组的拆卸
四、活塞连杆组的分解
五、曲轴轴承间隙的测量
六、连杆轴承间隙的测量
七、活塞环三隙的测量
(一)曲轴轴承径向间隙的检查与调整
(1)检查方法:
①专用塑料线规检验法(如桑塔纳)
拆下曲轴主轴承盖,清洁轴承及曲轴轴颈,将塑料间隙测量片放在轴颈上或主轴承中,将轴承盖装好,并用65N·m力矩拧紧轴承盖螺栓,但注意不要使曲轴转动。然后拆卸轴承盖,取出已压展的塑料间隙测量片,与附带有的不同宽度色标的量规相比对,测出轴承间隙值。
最大环槽间隙为0.2mm。
(五)活塞环背隙的检验:
背隙是指活塞环装在活塞上,再装入气缸内,活塞环内径与活塞环槽底径之代数差的1/2。检测的方法有两种:一是以槽深和环宽之差来表示,一般活塞环应低于环槽岸边0~0.35mm,以免在气缸内“卡死”。另一种方法是将活塞环放进气缸内,测量环的内径,再测量活塞的环槽底径后计算背隙。此方法较准确。
曲轴轴向间隙实测值:
是否超限:
(2)调整方法:
曲轴轴向间隙一般为0.05~0.20mm。如轴向间隙过小,会使机件膨胀而卡着;轴向间隙过大,易形成轴向窜动,则给活塞连杆组的机件带来不正常的磨损。因此,当轴向间隙值逾限时,则应用更换或修整止推轴瓦或止推垫圈来进行调整。
(三)活塞环端隙的检验:
端隙又叫“开口间隙”。一般第一道环稍大,二、三道环稍小。组合环的刮片端隙可稍大。检验的方法是将环装在气缸内,用厚薄规测量其开口间隙值即可。