废催化剂的回收利用
废催化剂的回收利用

废催化剂的回收利用废催化剂是工业生产中产生的一种废弃物,它通常由于使用寿命的结束、活性物质的耗尽以及污染物的堆积而成为废弃物。
催化剂废物的处理不仅对环境造成严重污染,而且对资源的浪费也非常严重。
因此,废催化剂的回收利用变得非常重要。
本文将介绍废催化剂的回收利用的方法以及其对环境和资源的重要意义。
1.再生:废催化剂通常含有一定量的活性物质,可以通过再生来恢复其催化性能。
再生的方法包括热处理和化学处理。
热处理是将废催化剂在高温下进行煅烧,以去除堆积的污染物和活性物质的耗尽。
化学处理包括酸碱洗涤、溶解和还原等方法,可以恢复催化剂的活性。
2.分离提取:废催化剂中通常含有可回收的金属成分,可以通过分离提取的方法将金属成分提取出来。
分离提取的方法包括溶液提取、离子交换和溶剂萃取等方法。
这些方法可以从废催化剂中提取出有价值的金属成分,使其得到有效利用。
3.粉碎回收:废催化剂通常是以颗粒或块状存在,可以通过粉碎的方式将其破碎成粉末状,再进行回收利用。
粉碎回收的方法包括机械粉碎和化学粉碎等。
这些方法可以将废催化剂转化成易于处理和回收利用的形态,提高资源利用效率。
废催化剂的回收利用对环境和资源都具有重要意义。
首先,废催化剂通常含有高浓度的有毒物质和重金属,如果直接丢弃或不加以处理,会对环境和人体健康造成严重污染。
因此,回收利用废催化剂可以有效减少对环境的污染,保护生态系统的健康。
其次,废催化剂通常含有一定量的金属成分,比如铂、镍等贵重金属。
这些金属成分在废催化剂中存在的形式通常是化合物或合金的形式,因此通过回收利用可以将这些金属成分提取出来,具有重要的资源利用价值。
此外,催化剂的再生还可以延长其使用寿命,延缓其冶炼成本,节约资源开采。
最后,废催化剂的回收利用还能降低废弃物的处理成本和对人力和物力资源的损耗,提高废弃物资源利用率。
在废催化剂的回收利用过程中,可以通过改进工艺和技术手段来降低能耗和废弃物的排放量,实现资源循环利用的目标。
催化剂的回收方法有哪些

催化剂的回收方法有哪些催化剂广泛应用于化学工业中,其作用在于加速反应速率,提高产品质量。
然而,随着反应的进行,催化剂会逐渐失活或受到污染,需要进行回收和再生。
催化剂的回收方法主要包括物理方法、化学方法和生物方法等。
物理方法是催化剂回收的一种常见方法。
其中的一种方法是通过沉积或离心等手段,将废弃的催化剂与反应物或产物分离。
这种方法的优点是简单易行,不会引入新的化学物质,对环境影响较小。
然而,物理方法回收的催化剂一般质量较低,需要进一步处理才能继续使用。
化学方法是催化剂回收的另一种常见方法。
例如,在某些反应中,使用可溶性络合剂来形成可溶性络合物,从而实现催化剂的回收。
通过控制条件,如温度、pH值等,可以使络合物与反应物或产物分离。
这种方法的优点是回收率较高,回收的催化剂质量较好。
然而,化学方法存在一定的化学废物产生,需要进行有效的处理和处理。
生物方法是近年来催化剂回收研究的新方向。
生物方法利用微生物或酶来催化反应,并实现催化剂的回收。
例如,利用微生物活化金属离子,使其转化成可溶性形态,从而实现催化剂的回收。
这种方法的优点是对环境友好,没有化学废物产生,可实现催化剂的高效回收。
然而,生物方法还处于研究阶段,需要进一步优化和实践。
除了上述方法之外,还有其他一些辅助方法可用于催化剂的回收。
例如,利用温度变化或压力变化等调节条件,将催化剂与反应物或产物分离。
利用化学吸附剂或材料来吸附催化剂,再通过适当的处理来实现回收。
这些方法虽然在催化剂回收中起到辅助作用,但需要根据具体情况选择合适的方法和条件。
总之,催化剂的回收是一项重要的工作,直接关系到反应效率和经济效益。
物理方法、化学方法、生物方法以及辅助方法等多种方法的结合应用,可以实现高效、环保的催化剂回收。
未来随着科学技术的不断发展和创新,相信催化剂回收方法会得到进一步改进和优化,为化学工业的可持续发展做出更大的贡献。
废催化剂回收利用提炼工艺有哪些

废催化剂回收利用提炼工艺有哪些废催化剂指的是在催化剂使用过程中变得无法再继续使用的残留物。
由于催化剂的高价值,从废催化剂中回收和利用其中的有用成分已成为一项重要的环保和资源节约措施。
废催化剂回收利用的提炼工艺主要包括以下几种:1. 焙烧方法焙烧法是一种常用的废催化剂回收利用工艺。
通过将废催化剂在高温下进行焙烧,将其中的有害物质和杂质烧除,得到高纯度的有用成分。
这种方法的优点是操作简单、成本较低,但同时也存在能耗高、排放污染物等问题。
2. 溶液浸取法溶液浸取法利用溶剂的选择性溶解性质,将废催化剂中的有用成分溶解出来。
常用的溶剂包括酸、碱和有机溶剂等。
通过对废催化剂的多次浸取和分离,可以逐步提取出目标成分。
这种方法的优点是选择性强、回收率高,但同时也需要处理大量的废液,对环境造成一定的影响。
3. 燃烧还原法燃烧还原法是一种通过高温气氛中的燃烧和还原反应,将废催化剂中的有害物质和杂质转化为无害物质,并回收利用有用成分的方法。
在高温还原气氛中,有害物质和杂质被还原为气体或金属等形式,而有用成分则以固体形式存在。
这种方法的优点是可回收高纯度的有用成分,但同时也需要高温和特殊的还原气氛条件。
4. 调整反应条件法调整反应条件法是一种通过改变反应条件来实现废催化剂回收利用的方法。
催化剂的活性往往与反应条件密切相关,通过调整反应温度、压力、气氛等条件,可以促使废催化剂中的有用成分重新表现出活性。
这种方法的优点是操作简单、成本低,但对于不同的废催化剂,需要找到最合适的反应条件。
5. 粉碎提取法粉碎提取法是一种通过机械碾磨废催化剂,再利用物理或化学方法提取有用成分的工艺。
通过细碎废催化剂,增加表面积,有利于后续的提取操作。
然后利用不同的提取剂、溶剂或分离技术,将有用成分从废催化剂中分离出来。
这种方法的优点是操作简便、废催化剂利用率较高,但对于废催化剂的破碎和提取过程会产生一定的能耗和环境污染。
6. 超声辅助提取法超声辅助提取法是一种利用超声波在液体中产生的空化效应,促进物质的溶解和扩散的技术。
炼油厂废催化剂回收利用
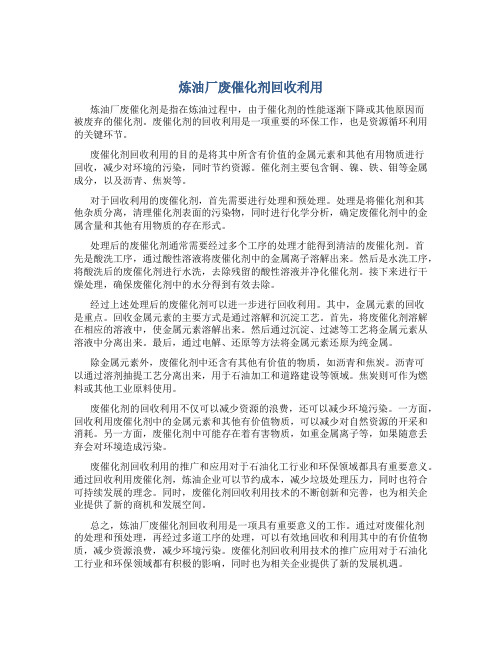
炼油厂废催化剂回收利用炼油厂废催化剂是指在炼油过程中,由于催化剂的性能逐渐下降或其他原因而被废弃的催化剂。
废催化剂的回收利用是一项重要的环保工作,也是资源循环利用的关键环节。
废催化剂回收利用的目的是将其中所含有价值的金属元素和其他有用物质进行回收,减少对环境的污染,同时节约资源。
催化剂主要包含铜、镍、铁、钼等金属成分,以及沥青、焦炭等。
对于回收利用的废催化剂,首先需要进行处理和预处理。
处理是将催化剂和其他杂质分离,清理催化剂表面的污染物,同时进行化学分析,确定废催化剂中的金属含量和其他有用物质的存在形式。
处理后的废催化剂通常需要经过多个工序的处理才能得到清洁的废催化剂。
首先是酸洗工序,通过酸性溶液将废催化剂中的金属离子溶解出来。
然后是水洗工序,将酸洗后的废催化剂进行水洗,去除残留的酸性溶液并净化催化剂。
接下来进行干燥处理,确保废催化剂中的水分得到有效去除。
经过上述处理后的废催化剂可以进一步进行回收利用。
其中,金属元素的回收是重点。
回收金属元素的主要方式是通过溶解和沉淀工艺。
首先,将废催化剂溶解在相应的溶液中,使金属元素溶解出来。
然后通过沉淀、过滤等工艺将金属元素从溶液中分离出来。
最后,通过电解、还原等方法将金属元素还原为纯金属。
除金属元素外,废催化剂中还含有其他有价值的物质,如沥青和焦炭。
沥青可以通过溶剂抽提工艺分离出来,用于石油加工和道路建设等领域。
焦炭则可作为燃料或其他工业原料使用。
废催化剂的回收利用不仅可以减少资源的浪费,还可以减少环境污染。
一方面,回收利用废催化剂中的金属元素和其他有价值物质,可以减少对自然资源的开采和消耗。
另一方面,废催化剂中可能存在着有害物质,如重金属离子等,如果随意丢弃会对环境造成污染。
废催化剂回收利用的推广和应用对于石油化工行业和环保领域都具有重要意义。
通过回收利用废催化剂,炼油企业可以节约成本,减少垃圾处理压力,同时也符合可持续发展的理念。
同时,废催化剂回收利用技术的不断创新和完善,也为相关企业提供了新的商机和发展空间。
废FCC催化剂的综合回收与利用

废FCC催化剂的综合回收与利用废FCC催化剂是指离子交换成分催化裂化(FCC)工艺中使用后,因其寿命结束或失效而产生的废弃催化剂。
废FCC催化剂的回收与利用是一项具有重要经济和环境意义的工作。
本文将介绍废FCC催化剂的来源、组成、综合回收与利用的方法以及对环境的影响。
废FCC催化剂来源主要有两个方面,一是自身寿命到期,没有再利用价值;二是因质量不合格而被替换。
废FCC催化剂包含的主要组成元素有铝、硅、钠、钙等。
这些元素是宝贵的资源,如果能够从废催化剂中回收利用,将对资源节约和环境保护起到积极的作用。
废FCC催化剂的综合回收与利用可以通过以下几个步骤来实现。
对废催化剂进行预处理,包括破碎、筛分、焙烧等,以便更好地进行后续处理。
采用物理方法进行分离,如磁选法、重液法等,将废催化剂中的铝、硅等有价值元素分离出来。
然后,采用化学方法进行进一步的提取和分离,如酸浸、碱浸等,将废催化剂中的有价值元素提取出来。
对废催化剂进行再生处理,使其再次成为可用的FCC催化剂。
废FCC催化剂的综合回收与利用对环境有着重要的影响。
废催化剂的回收利用可以减少对自然资源的开采,降低人类对环境的破坏。
通过回收废催化剂中的有价值元素,可以减少对矿产资源的消耗,降低生产成本,提高资源利用效率。
废催化剂的回收利用还可以减少废弃物的产生,降低对垃圾处理设施的负荷,减少环境污染。
废FCC催化剂的综合回收与利用是一项具有重要经济和环境意义的工作。
通过对废催化剂的回收利用,可以实现资源的节约和循环利用,减少对环境的破坏,为可持续发展做出贡献。
需要加强相关技术研究和政策的支持,推动废FCC催化剂的综合回收与利用工作的开展。
催化剂回收利用方法

催化剂回收利用方法催化剂是一种在化学反应中起催化作用的物质,广泛应用于化工、石油和环保等领域。
催化剂的使用可以提高反应速率、降低反应温度和降低能耗,但随着使用时间的增加,催化剂会逐渐失活,需要进行回收和再利用。
本文将介绍催化剂回收利用的方法。
1. 物理方法物理方法是指通过物理手段将催化剂从反应系统中分离出来进行回收。
常用的物理方法包括过滤、离心和萃取等。
过滤是一种将固体颗粒从液体中分离的方法,适用于颗粒较大的催化剂。
这种方法操作简单,成本较低,但对于颗粒较小的催化剂效果不佳。
离心是一种利用离心力将催化剂和反应物分离的方法,适用于颗粒较小且密度差异较大的催化剂。
这种方法回收效率较高,但设备成本较高且操作复杂。
萃取是一种利用溶剂将催化剂从反应溶液中提取出来的方法,适用于可溶于溶剂中的催化剂。
这种方法能够回收大部分催化剂,并可以进行后续的再利用。
2. 化学方法化学方法是指通过化学反应将催化剂还原或再生,以实现回收利用。
常用的化学方法包括还原、氧化和酸碱中和等。
还原是一种将催化剂中的活性组分从其氧化态还原为还原态的方法,可以恢复催化剂的活性。
常用的还原剂包括氢气、氨气和亚硫酸等。
氧化是一种将催化剂中的杂质氧化为可溶性物质,从而清除杂质的方法。
常用的氧化剂包括过氧化氢、高锰酸钾和浓硝酸等。
酸碱中和是一种通过酸碱反应将催化剂中的杂质转化为水和盐的方法。
通过酸碱中和可以有效地去除催化剂表面吸附的杂质。
3. 物化联合方法物化联合方法是指将物理方法和化学方法相结合,通过物理手段分离催化剂并使用化学方法进行还原或再生。
这种方法综合利用了物理和化学的优势,能够有效地回收利用催化剂。
常见的物化联合方法包括超声辅助还原、高温还原和酸碱联合处理等。
超声辅助还原利用超声波的机械振动作用,加速还原剂与催化剂的反应速率,提高回收效率。
高温还原利用高温条件加速还原反应,同样能够提高回收效率。
酸碱联合处理通过在酸碱条件下处理催化剂,可以去除表面的污染物并恢复催化剂的活性。
废催化剂回收
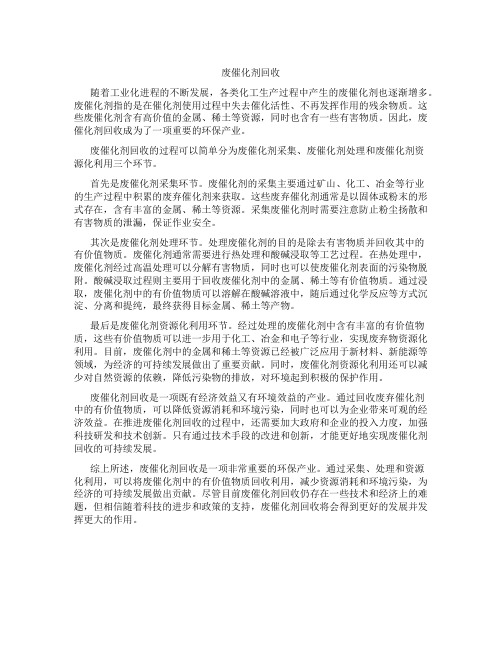
废催化剂回收随着工业化进程的不断发展,各类化工生产过程中产生的废催化剂也逐渐增多。
废催化剂指的是在催化剂使用过程中失去催化活性、不再发挥作用的残余物质。
这些废催化剂含有高价值的金属、稀土等资源,同时也含有一些有害物质。
因此,废催化剂回收成为了一项重要的环保产业。
废催化剂回收的过程可以简单分为废催化剂采集、废催化剂处理和废催化剂资源化利用三个环节。
首先是废催化剂采集环节。
废催化剂的采集主要通过矿山、化工、冶金等行业的生产过程中积累的废弃催化剂来获取。
这些废弃催化剂通常是以固体或粉末的形式存在,含有丰富的金属、稀土等资源。
采集废催化剂时需要注意防止粉尘扬散和有害物质的泄漏,保证作业安全。
其次是废催化剂处理环节。
处理废催化剂的目的是除去有害物质并回收其中的有价值物质。
废催化剂通常需要进行热处理和酸碱浸取等工艺过程。
在热处理中,废催化剂经过高温处理可以分解有害物质,同时也可以使废催化剂表面的污染物脱附。
酸碱浸取过程则主要用于回收废催化剂中的金属、稀土等有价值物质。
通过浸取,废催化剂中的有价值物质可以溶解在酸碱溶液中,随后通过化学反应等方式沉淀、分离和提纯,最终获得目标金属、稀土等产物。
最后是废催化剂资源化利用环节。
经过处理的废催化剂中含有丰富的有价值物质,这些有价值物质可以进一步用于化工、冶金和电子等行业,实现废弃物资源化利用。
目前,废催化剂中的金属和稀土等资源已经被广泛应用于新材料、新能源等领域,为经济的可持续发展做出了重要贡献。
同时,废催化剂资源化利用还可以减少对自然资源的依赖,降低污染物的排放,对环境起到积极的保护作用。
废催化剂回收是一项既有经济效益又有环境效益的产业。
通过回收废弃催化剂中的有价值物质,可以降低资源消耗和环境污染,同时也可以为企业带来可观的经济效益。
在推进废催化剂回收的过程中,还需要加大政府和企业的投入力度,加强科技研发和技术创新。
只有通过技术手段的改进和创新,才能更好地实现废催化剂回收的可持续发展。
废FCC催化剂的综合回收与利用

废FCC催化剂的综合回收与利用近年来,由于环境问题越来越受到人们的关注和重视,废弃催化剂的综合回收与利用也得到了越来越多的关注。
废弃催化剂是指在工业生产过程中由于达到活性失效、存在毒害、催化剂浓度过低等原因而被淘汰的催化剂。
废弃催化剂通常含有金属或者贵金属等高价值的成分,如果不能有效地回收和利用,不仅会造成资源的浪费,还会对环境造成污染和破坏。
废弃催化剂的综合回收与利用对于资源的节约和环境的保护具有重要的意义。
废弃催化剂的综合回收与利用可以采取多种方式,其中一个重要的方式是通过化学方法对催化剂进行回收。
可以采取酸溶法将催化剂中的金属等高价值成分溶解出来,然后通过沉淀、过滤、洗涤等步骤得到纯净的金属沉淀物。
接着,可采用还原法将金属沉淀物还原成金属颗粒,并通过过滤、洗涤等手段得到纯净的金属颗粒。
经过烧结或其他工艺处理,可以将金属颗粒制成金属材料或催化剂,实现催化剂资源的再利用。
废弃催化剂的综合回收与利用还可以采用物理方法,如磁选法、浮选法等,对催化剂中的贵金属进行回收和提取。
这些物理方法可以通过贵金属的特性,如磁性、密度等来实现对贵金属的分离和回收。
通过这些方法,可以实现对废弃催化剂中贵金属成分的高效回收和利用。
除了化学和物理方法,废弃催化剂的综合回收与利用还可以采用生物技术。
生物技术通过利用微生物对废弃催化剂中的有机物进行降解和分解,可以有效地降低催化剂中有机物的毒性和污染,从而实现对废弃催化剂的资源化利用。
在废弃催化剂的综合回收与利用过程中,还需要注意对环境污染的控制。
废弃催化剂中的某些成分可能对水、土壤和大气造成严重的污染和破坏。
在回收过程中,应该合理利用各种技术手段,控制和减少废弃催化剂对环境的污染。
废弃催化剂的综合回收与利用是一项重要的工作,对于节约资源和保护环境具有重要的意义。
只有通过各种有效的方法对废弃催化剂进行回收和利用,才能实现催化剂资源的再利用,减少资源的浪费和环境的污染,促进可持续发展的目标的实现。
- 1、下载文档前请自行甄别文档内容的完整性,平台不提供额外的编辑、内容补充、找答案等附加服务。
- 2、"仅部分预览"的文档,不可在线预览部分如存在完整性等问题,可反馈申请退款(可完整预览的文档不适用该条件!)。
- 3、如文档侵犯您的权益,请联系客服反馈,我们会尽快为您处理(人工客服工作时间:9:00-18:30)。
全球催化剂的销售额达到107亿美元。 其中炼油催化剂为24亿美元(占22.4 %),化工催化剂为43亿美元(占40.2 %),环保催化剂为40亿美元(占37.4 %)。 据世界市场研究机构福斯特与沙利文 公司的预测在今后的十年内炼油催化 剂将增长5%,化工催化剂将增长1 %-2%,而环保催化剂将增长13%。
废催化剂随日光的照射还会释放出有害 的气体如SO2、H2S、NDx、CO2及挥发 性有机物,从而污染大气。废催化剂随 风暴的吹扫则会增加大气中尘粒的悬浮 量而污染周围的环境。 因此开展废催化剂的回收利用, 因此开展废催化剂的回收利用,可 以使废催化剂的有害部分减量化, 以使废催化剂的有害部分减量化,甚至 无害化以达到清洁生产的目的, 无害化以达到清洁生产的目的,增强企 业的竞争能力。 业的竞争能力。
多相反应的特点是反应发生在两相界面上,表面 的几何形状、表面积的大小,表面形态等有关系 的。 废催化剂回收前,通过焙烧使其中金属晶粒长大, 变形;使其上吸附的水分、气体、有机物等挥发 掉以改变其表面的形态有利于溶解时溶剂在其表 面的吸附,和通过固体表面空位向固体体内进行 渗透。 溶解进行时,如若相界面表面积越大,固液接触 就越好。因此在废催化剂溶解前,若固体颗粒进 行磨碎的话,既可以增大溶解反应时接触的界面 面积,又可以增加金属晶格的缺陷从而大大提高 溶解的速率。
在扩散控制的溶解过程中,温度对溶解 速率的影响较小。但在此种情况下, 为了减少溶解产物扩散层的厚度,需 要提高搅拌的速度,溶解速率是搅拌 速度的函数,扩散层厚度随着搅拌速 度的提高而减小。 在化学反应控制的溶解过程溶解速率与 搅拌速度无关。
(2)溶剂的选择 废催化剂溶解时常用溶剂及分类见下表。
溶剂选择的原则是热力学上可行,反应速度快、 经济合理,来源容易。易于回收。对设备腐蚀性 小,对欲溶解组分的选择性好。主要应根据被溶 物的物理特性和化学特性而定。 碱性溶剂比酸性溶剂的反应能力弱,但其选择性 比酸性的高。 氯气浸出主要用于含贵金属的废催化剂原料。由 于氯气的电位高于除金以外的贵金属,并且氯在 水溶液中会水解生成盐酸和次氯酸,盐酸可以使 已氯化的贵金属呈氯络酸状态溶解;而次氯酸的 电极电位比氯更高,能使所有的贵金属氧化。
化工
化学工业
化 学 工 业 废 渣
行业和工艺过程分 : 无机盐工业废物(铬渣、氰渣、磷泥等) 氯碱工业废物(盐泥、电石渣等) 氮肥工业废物(主要是炉渣) 硫酸工业废物(主要是硫铁矿烧渣) 纯碱工业废物等。
按废物主要组成分: 废催化剂、硫铁矿烧渣、铬渣、氰渣、盐泥、炉渣、 各类炉渣、碱渣等
化 学 工 业 废 渣 种 类
环境效益: 环境效益: 因催化反应的需要,有些催化剂在制 作过程中不得不采用或添加了一些有 毒的组分,如As2O3、As2O5、CrO3等。 倘若对废催化剂不加处置随意堆放的 话,一方面堆积废催化剂需要占据大 量的场地;另一方面废催化剂中所含 的毒物会随雨水的冲刷而流失,造成 水质污染,又破坏土壤的结构及地面 上的植被。
4.1.4 废催化剂回收机理
主要涉及到废催化剂固体中金属和载体组分的溶 解与从溶液中分离出这些组分的两大过程。 一、组分的溶解 (1)溶解的机理:固—液系统,典型的多相反应过 程,平均溶解速率可用下式表示:
式中 C1——在时间t1时被溶组分的浓度; C2——在时间t2时被溶组分的浓度。 瞬时速率为v=dc/dt 按溶解进行的速率,溶解过程 可分为三种。
化 学 工 业 废 渣
急毒性、 急毒性、 反应性 及腐蚀 性
1~3t,8~12t, 0.4亿吨,6.16% 0.4亿吨 亿吨, 产生量大 金、银、 铂等 化学工业废 渣的特性
危险废物种 类多
资源化潜力 大
三、主要治理技术措施
改革化工生产工艺、设备、改进操作方式, 采用无废或低废工艺,尽可能把污染消除 在生产过程中。 采用蒸馏、结晶、萃取、吸附、氧化等方 法将废物转化为有用产品,加以综合利用。 通过焚烧、热解、化学氧化等方式将废物 安全有效处理或处置,使其无害化。
二、特点
废物产生量大:一般生产每吨产品产生1- 3吨的固体废物,有的产品可高达8-12吨/ 吨产品。若以产值计算,则一般为 7.16t/万 元产值; 危险废物种类多,有毒物质含量高,对人 体健康和环境危害大。如铬渣:致癌;氰 渣:直接中毒等; 废物再资源化可能性大。相当一部分是未 反应的原料和反应副产物。如废石膏等
化学工业固体废物简介
一、来源与分类 化学工业生产过程中产生的。 一般按废物产生的行业和工艺过程进行分 类。 按照固体废物对人体和环境的危害性分类。 按废物主要组成分类。
石油化工
石油炼制:酸、碱废液,废催化剂 石油化工:有机废液,废催化剂,污泥 石油化纤:有机废液,酸碱废液,聚酯废料 无机盐工业:铬渣,氰渣,磷渣等 氯碱工业:盐泥,电石渣等 磷肥工业:磷石膏等 纯碱工业:蒸馏废液 制酸工业:硫铁矿渣,氟石膏等 有机原料及合成工业:皂化废液及高浓度母液等 染料工业:废硫酸,废滤液等 感光工业:废胶片,乳剂和污泥等
每开发1吨有色金属,就中国的水准而 言,要开采出33吨的矿石,剥离26.6吨 的围岩,消耗成百吨的煤和约8吨水、 同时会产生90吨的固体废弃物及相应的 废气和废水。 因此将废催化剂作为二次矿源来利用, 从中回收金属及其他组分是有一定的经 济效益的。
资源效益: 资源效益: 我国人均资源拥有率相对较低。我国每单位国民 生产总值所消耗的矿物原料要比发达国家高出 3—4倍。全世界铂族金属的储量不过8.76万吨, 铂矿仅有2.46万吨,我国的铂矿资源更少,只有 世界的0.7%左右,每年的总产量不过500kg左右, 其缺口高达90%。据国家地矿部资料显示,我国 的铁、铜、铅、锌等矿产资源到2000年就已进 入了中、晚期阶段。 为子孙后代着想,将废催化剂作为二次资源加以 利用,有较强的现实意义还有深远的历史意义, 具有长久效益。
催化剂失活原因: (1)随着催化剂使用时间的增长,催化剂发生 热老化,因过热而导致活性组分晶粒的长大 甚至发生烧结而使催化活性下降; (2)因遭受某些毒物的毒害而部分或全部丧失 活性; (3)因一些污染物诸如油污、焦炭等积累在催 化剂活性表面上或堵塞催化剂孔道而降低活 性; (4)催化剂抗破碎强度欠佳,使用一段时间后 颗粒破碎而引起系统阻力上升而无法继续使 用。
催化剂寿命短的仅数月甚至几天,长的 则可达七八年。 废催化剂的处理方式主要有填埋/固化处 理法,焚化法和回收/再循环/再利用法。 回收/再循环/再利用法才是解决废催化 剂出路的好方法,它既节约天然资源, 又减少对环境的污染,在大多数情况下 还能获得可观的收益。
4.1.1 废催化剂回收利用的重要意义
经济效益: 经济效益: 催化剂在制备过程中,常常挑选一些有色 金属乃至贵金属作为其主要组分。废催化 剂仍然会含有数量不低的有色金属,如铜、 镍、钴、铬等有用物质。有的还含有较多 的稀贵金属铂、钯、钌等。有时它们的含 量远远高于贫矿中所含有的相应组分。 例如,冶炼金属镍的硅镍矿仅含2.8%的镍, 而一般废镍催化剂的含量可达6%-20%的 范围。
废催化剂的回收利用其针对性极强。 废催化剂的回收利用其针对性极强。 因此,针对某种废催化剂, 因此,针对某种废催化剂,具体究 竟应采用哪一种方法进行回收, 竟应采用哪一种方法进行回收,尚 需根据此种催化剂的组成, 需根据此种催化剂的组成,含量及 载体种类等加以选择, 载体种类等加以选择,根据企业拥 有的设备和能力及回收物的价值、 有的设备和能力及回收物的价值、 性能、收率, 性能、收率,最终回收费用等加以 比较而决定之。 比较而决定之。
由阿仑尼乌斯方程来表达:
K = A exp( − E / RT )
式中 K——反应速率常数; A——常数; E——活化能。 从上述方程可知溶解速率和温度的关系与 活化能的大小是密切相关的。为了加速溶 解速率,可以提高温度,但温度的升高往 往要受到水沸点的限制。在加压溶解过程 中,溶解的温度可以升到250—300℃或更 高温度。
三、干湿结合法
含两种以上组分的废催化剂很少单独 采用干法或湿法进行回收,多数采用 干湿结合法才能达到目的。 广泛地用于回收物的精制过程。 例如,铂-铼废重整催化剂回收时, 浸去铼后的含铂残渣需经干法煅烧后, 再次浸渍才将铂浸出。
四、不分离法
此法不将废催化剂活性组分与载体分离,或不将 其两种以上的活性组分分离处理。 由于不分离活性组分及载体,故能耗小,成本低、 废弃物排放少,不易造成二次污染。 例如,在回收铁铬中温变换催化剂时,往往不将 浸液中的铁铬组分各自分离开来,直接将其回收 重制新催化剂。 再如,回收生产DMT(苯二甲酸二甲酯)和TA(对 苯二甲酸)用的钴锰废催化剂时,往往不将钴锰 分离开来,调整其钴锰配比(按工艺要求)后直接 返回系统中重新启用。
4.1.3 废催化剂的常规回收方法
各类废催化剂的常规回收方法一般 可分为四种方法:
1. 干法 2. 湿法 3. 干湿结合法 4. 不分离法
一、干法
利用加热炉将废催化剂与还原剂及助熔剂一 起加热熔融,使金属组分经还原熔融成金属 或合金状回收,以作为合金或合金钢原料; 而载体则与助熔剂形成炉渣排去。 回收某些稀贵金属含量较少的废催化剂时, 往往加进一些铁之类的贱金属作为捕集剂共 同进行熔炼。 干法能耗较高。氧化焙烧法、升华法和氯化 挥发法也包括在干法之中。由于此法不用水, 一般谓之干法。
溶剂浓度对固体溶解速率影响较大。 固液比也是影响溶解过程的因素之一。 固体组分的溶解过程,主要由以下几个步骤所组成: ①溶剂离子向废催化剂固体表面扩散; ②溶剂离子在界面上的吸附; ③被吸附溶剂和废催化剂固体中被溶组分的相互反 应; ④反应产物解吸到扩散层内; ⑤反应产物在溶液中扩散。
固体溶解的过程一般可分为以下三种类型。 1 当固体表面的化学反应速率大大超过扩 散速率时,溶解过程为扩散控制过程。 此时活化能数值较低。 2 当固体表面的化学反应速率大大低于扩 散速率,属于化学反应控制步骤时、此 时活化能数值较高。 3 当固体表面的化学速率与扩散速率相等 时,其溶解过程为混合控制过程。