电子束焊接技术的应用
电子束焊接机原理及应用

电子束焊接机原理及应用电子束焊接机是一种高效、高精度的焊接设备,广泛应用于航空、航天、电子、医疗和汽车等多个领域。
本文将详细介绍电子束焊接机的原理和应用,以帮助读者更好理解该技术。
一、原理电子束焊接是利用高能电子束对工件进行熔化和连接的一种焊接方法。
其原理基于电子束产生、聚焦及作用于工件上的过程。
1. 电子束产生:电子束源通常采用热阴极发射电子束的方式。
热阴极经过加热后,发射出大量的自由电子,形成电子束。
2. 电子束聚焦:为了使电子束能够准确地作用于工件上,通常需要使用电磁场将电子束进行聚焦。
聚焦系统通常由电子枪和磁场组成,电子枪用于发射电子束,并通过磁场控制电子束的方向和聚焦程度。
3. 电子束作用:一旦电子束聚焦后,它将以高速冲击到工件上,产生巨大的能量。
电子束的高能量可以瞬间加热工件,使其熔化并与其他工件相融合。
二、应用电子束焊接机在各个领域都有广泛的应用,下面将分别就航空、航天、电子、医疗和汽车五个领域进行介绍。
1. 航空领域:航空工业对焊接质量和工艺的要求非常严格,因为焊接连接处需要承受极高的载荷和温度变化。
电子束焊接机由于能够提供高质量的焊接接头,被广泛应用于飞机结构的连接。
其优势在于焊缝小、熔深浅、热效应小、气体保护不需要。
2. 航天领域:航天器的结构必须具有很高的可靠性和强度,同时对结构的重量也有严格限制。
电子束焊接机可实现高质量、低热影响做工的焊接效果,广泛应用于航天器的结构连接,如推进器、燃气发生器等。
3. 电子领域:电子设备的焊接通常要求高度精确和可靠性。
电子束焊接机在电子领域可以实现高精度焊接,适用于焊接电子元件、连接电子线路板和封装器件等。
4. 医疗领域:医疗器械焊接需要保证焊接接头的无菌性和牢固性。
电子束焊接机可实现非接触式焊接,避免了杂质和气体污染,适用于不锈钢、钛合金、镍钴合金等医疗器械材料的焊接。
5. 汽车领域:汽车工业对焊接质量和强度要求较高。
电子束焊接机的高能量密度和精确性可以实现高质量、高强度的焊接,适用于汽车车身结构的焊接,如车架、车门、天窗等。
高能束焊接技术的发展和应用

高能束焊接技术的发展和应用高能束焊接技术(EBW)是一种先进的焊接方法,它利用高速电子束来熔化和连接金属材料。
这种焊接技术具有高能量密度、高焊接速度、优质的焊接效果和适用于各种金属材料等优点,因此在航空航天、汽车制造、核工业和电子行业等领域得到了广泛的应用。
本文将从高能束焊接技术的发展历程和原理、应用领域、优势和挑战等方面进行介绍。
一、高能束焊接技术的发展历程和原理高能束焊接技术最早是在20世纪50年代发展起来的,最初是用于核工业和航天航空领域。
1958年,美国杜邦公司开发出了第一台商用的电子束焊接机,这标志着电子束焊接技术开始走向工业化生产。
高能束焊接技术通过电子枪产生高速电子束,电子束击中工件表面时,产生的能量将工件表面瞬间加热到熔化温度,然后通过电子束辐照区域产生高温熔池,从而实现熔化和连接金属材料的目的。
高能束焊接技术的原理是利用高速电子束的能量瞬间加热金属材料,使其熔化并形成熔池,然后利用合适的焊接工艺来实现金属材料的连接。
与传统的焊接方法相比,高能束焊接技术具有能量密度高、焊接速度快、热影响区小、热输入低等优点,因此可以实现高质量的焊接效果。
二、高能束焊接技术的应用领域高能束焊接技术在航空航天、汽车制造、核工业和电子行业等领域得到了广泛的应用。
在航空航天领域,高能束焊接技术被广泛应用于飞机结构件、发动机零部件、航天器壳体等关键部件的焊接,以提高焊接质量和生产效率。
在汽车制造领域,高能束焊接技术通常应用于汽车车身焊接、汽车零部件焊接等工艺环节,以提高焊接强度和减少成本。
在核工业领域,高能束焊接技术被用于核反应堆压力容器、核燃料元件等核设备的焊接,以保证核设备的安全可靠性。
在电子行业领域,高能束焊接技术通常应用于电子器件的微细焊接和包装,以提高器件的性能和可靠性。
高能束焊接技术相对传统焊接方法有很多优势,主要包括以下几点:1. 高能量密度:高能束焊接技术的能量密度很高,可以实现瞬间加热和快速熔化金属材料,从而提高焊接速度和效率。
电子束焊接技术研究与应用

电子束焊接技术研究与应用随着工业的发展,焊接技术已经成为各行各业中不可或缺的一项技术。
而电子束焊接技术作为现代高新技术的代表之一,因其高效、高质、高稳定性等优点,已被广泛应用于飞航航空、船舶、化工、医疗器械、精密仪器等高科技行业。
本文将探讨电子束焊接技术的研究和应用。
一、电子束焊接技术的基本原理电子束焊接技术是一种将电子束在低压和真空的情况下进行的高速能量材料处理。
在电子束的作用下,焊材在极短时间内被快速加热并熔化,形成一道焊缝。
基本原理是通过高能电子束的能量转化为焊接材料内部的热能,使其熔化,并通过流动的铁水消除焊接材料中的气孔,从而实现焊接。
二、电子束焊接技术的优点与其他传统的焊接方式相比,电子束焊接技术具有以下几个优点:1. 焊接区域不受热影响区的影响,能够焊接极薄的材料。
2. 焊缝的孔洞率较低,焊接质量高。
3. 电子束焊接过程中,不需要添加任何助焊剂,无需后续清洗和处理焊渣等。
4. 可以实现对不同材料不同厚度的焊接并达到很高的焊接效率。
5. 由于焊接时使用的是真空环境,所以焊接零件表面的污染和氧化问题得到很好的解决,从而减少了热裂问题的产生。
三、电子束焊接技术的应用电子束焊接技术在精密结构的制造、高精度零件的加工等领域有了广泛的应用。
下面将从飞航航空、船舶、医疗器械等方面来介绍其应用:1. 飞航航空电子束焊接技术在飞航航空领域具有重要的应用价值。
早在上世纪60年代初,美国就已成功实现了航空发动机涡轮叶片的电子束焊接,并将其广泛应用。
目前,国内外的航空航天领域中,电子束焊接技术已经为创新提供了新的技术保障。
2. 船舶电子束焊接技术在造船领域有着广泛的应用。
船体结构件是船用焊接加工中最困难的焊接部位之一,特别是在船体的局部加强部位,常常需要进行多角度的焊接。
电子束焊接通过其高度的控制能力,可以有效保证焊接质量,并且减轻了焊接环境和操作者的安全风险。
3. 医疗器械电子束焊接技术在医疗器械领域中的应用,主要用于制造一些耐高压、耐高温、各种特殊环境下使用的设备。
电子束焊接技术的应用与发展趋势

电子束焊接技术的应用与发展趋势近年来,随着科技的不断进步和工业的快速发展,电子束焊接技术逐渐成为焊接领域的热门话题。
电子束焊接技术以其高效、高质、低能耗的特点,被广泛应用于航空航天、汽车制造、电子设备等领域,并且在未来的发展中有着巨大的潜力。
首先,电子束焊接技术在航空航天领域的应用前景广阔。
航空航天领域对焊接技术的要求非常高,需要确保焊接接头的强度和密封性。
而电子束焊接技术可以通过高能电子束的瞬间热量作用于焊接接头,实现高质量的焊接效果。
此外,电子束焊接技术还具有焊接速度快、热影响区小等优点,能够满足航空航天领域对焊接工艺的严格要求。
其次,电子束焊接技术在汽车制造领域的应用也非常广泛。
汽车制造领域对焊接接头的质量和可靠性要求较高,而传统的焊接方法往往难以满足这些要求。
电子束焊接技术通过高能电子束的集中加热作用,可以实现焊接接头的高强度和高密封性。
此外,电子束焊接技术还可以在焊接过程中实时监测焊接质量,提高焊接工艺的可控性和稳定性。
此外,电子束焊接技术在电子设备领域的应用也越来越广泛。
电子设备通常需要焊接小尺寸、高密度的焊接接头,而传统的焊接方法难以满足这些要求。
而电子束焊接技术可以通过高能电子束的精确控制,实现对小尺寸焊接接头的高精度焊接。
此外,电子束焊接技术还可以避免传统焊接方法中可能产生的电磁干扰和热应力,保证焊接接头的稳定性和可靠性。
随着科技的不断进步和工业的快速发展,电子束焊接技术也在不断发展和创新。
未来,电子束焊接技术的发展趋势主要体现在以下几个方面:首先,电子束焊接技术将更加智能化。
随着人工智能技术的快速发展,电子束焊接技术也将更加智能化。
通过引入人工智能算法和机器学习技术,可以实现焊接过程的自动化和智能化控制,提高焊接工艺的稳定性和可控性。
其次,电子束焊接技术将更加高效节能。
随着能源资源的日益紧张,高效节能已经成为焊接技术发展的重要方向。
电子束焊接技术以其高能量密度和高效热源的特点,可以实现焊接过程的快速加热和冷却,从而大大提高焊接效率和能源利用率。
电子行业电子束焊接

电子行业电子束焊接简介电子束焊接是一种常用于电子行业的高精度焊接技术。
它利用电子束的高能量特性,将焊接材料加热至高温,快速融化并连接在一起。
电子束焊接具有精度高、焊接速度快和热影响区小等优点,广泛应用于半导体、电子元件和电路板的制造过程中。
工艺流程电子束焊接的工艺流程包括以下几个步骤:1.准备工作:对焊接材料进行清洁处理,确保表面不含杂质和氧化物。
同时,需要根据焊接要求确定焊接参数,包括电子束功率、聚焦电压和聚焦电流等。
2.对焊接材料进行定位和夹持:将待焊接的材料放置在焊接台上,并使用夹具进行固定,以确保焊接过程中的稳定性和准确性。
3.开始焊接:启动电子束装置,将电子束聚焦并瞄准焊接位置。
电子束穿过电子枪并聚焦在工件上,加热焊接材料达到融化温度并实现焊接。
4.焊接结束:完成焊接后,关闭电子束装置,等待焊接区域冷却。
同时,对焊接区域进行检查,确保焊接质量符合要求。
特点和优势电子束焊接在电子行业中得到广泛应用,主要受益于以下几个特点和优势:•高精度:电子束焊接能够提供非常精确的焊接结果,焊接位置和焊缝的尺寸控制非常准确,有助于保证电子产品的稳定性和可靠性。
•焊接速度快:电子束焊接的加热速度非常快,因为电子束本身具有高能量,能够迅速将焊接材料加热至融化温度。
相比传统焊接方法,电子束焊接能够大大缩短焊接时间,提高生产效率。
•热影响区小:电子束焊接时,焊接区域受热的时间非常短,因此在焊接过程中产生的热量对材料周围的影响非常小。
这意味着电子束焊接可以避免或减少由于热应力引起的变形和损坏,提高焊接质量。
•适用范围广:电子束焊接可以应用于各种材料的焊接,包括金属、陶瓷和非金属材料。
它在不同类型的电子元件、半导体和电路板的制造过程中都有重要的应用价值。
•自动化程度高:电子束焊接可以与自动化设备相结合,实现工艺的自动化和智能化。
通过编程和机器控制,可以实现焊接参数的精确控制和焊接过程的自动化控制。
应用案例LED封装在LED封装过程中,电子束焊接被广泛应用于焊接LED芯片和良好导热性能的基座之间的连接。
电子束焊接技术在电子元器件制造中的应用案例

电子束焊接技术在电子元器件制造中的应用案例电子束焊接技术作为一种高精密、高效率的焊接方法,在电子元器件制造中发挥着重要的作用。
它通过利用电子束的能量来加热并融化焊接材料,以达到连接的目的。
本文将探讨电子束焊接技术在电子元器件制造中的几个具体应用案例。
首先,电子束焊接在电子元器件的封装中应用广泛。
封装是指将电子元器件芯片固定在外壳中,以保护芯片不受外界影响,并提供便于安装的结构。
传统的封装方式包括焊线与焊盘连接以及焊膏封装,然而这些方法往往需要在较高的温度下进行,容易引发电子元器件的损坏。
而电子束焊接技术能够在较低的温度下完成焊接过程,减少元器件的热损伤风险。
其次,电子束焊接技术在电子封装中的应用案例之一是主板焊接。
主板是电子设备的核心部件,它连接着各种电子器件,负责传递电流和信号。
传统的主板焊接方式往往采用热流风或回流焊接,但这些方法会产生过多的热量,容易导致主板变形和元器件热损伤。
而电子束焊接技术通过在焊接过程中准确控制焊接区域的加热范围,避免了热损伤和变形的风险,提高了焊接的质量和效率。
另外,电子束焊接技术在电子元器件的连接中也有广泛的应用。
电子设备中的连接往往需要高精度和高可靠性,而传统的焊接方法往往无法满足这些要求。
电子束焊接技术通过高能电子束的精确瞄准和控制,可以实现非接触式焊接,避免了传统焊接中可能出现的接触不良或者损伤的情况。
同时,电子束焊接技术还能够在焊接过程中实时监控焊接质量,提高了连接的可靠性。
最后,电子束焊接技术在印刷电路板(PCB)制造中也有广泛的应用。
PCB是电子器件的重要组成部分,它提供了电子元器件之间的电气连接和机械支撑。
传统的PCB制造方法包括贴片焊接和波峰焊接,但这些方法往往需要多个步骤和设备,工艺复杂且效率低下。
而电子束焊接技术可以直接在PCB上进行焊接,避免了多个步骤的耗时和设备的成本,提高了制造效率并降低了制造成本。
综上所述,电子束焊接技术在电子元器件制造中的应用具有广泛的前景。
电子束焊接技术在零部件制造中的应用案例

电子束焊接技术在零部件制造中的应用案例电子束焊接是一种高能电子束通过束缚电子与工件表面相互作用,将电子动能转化为热能,从而实现零件的熔化和焊接的先进技术。
这种焊接技术在零部件制造中具有广泛的应用,能够提高零部件的质量、效率和可靠性。
以下将介绍一些电子束焊接技术在不同领域的实际应用案例。
1. 航空航天领域航空航天领域对零部件的质量和可靠性要求极高,因此电子束焊接技术得到了广泛应用。
例如,飞机发动机零部件的制造中广泛采用电子束焊接技术。
该技术能够实现高强度、高质量的焊接,确保承受高温和高压的环境下的可靠性。
此外,电子束焊接还被用于制造航天器的燃烧室和液氢推进器等部件,确保其在极端环境下的工作性能和安全性。
2. 汽车制造领域汽车制造领域对零部件的质量和耐久性要求也很高,并且对于轻量化、高效能的需求也越来越大。
电子束焊接技术在汽车制造中起到了重要作用。
例如,汽车发动机的缸体焊接中,电子束焊接能够实现高强度、无瑕疵的焊接,提供可靠的密封性和耐用性。
此外,电子束焊接还在汽车零部件的连接件、车身结构和悬挂系统等方面得到了广泛应用,提高了整车的质量和安全性。
3. 电子设备制造领域电子设备制造领域对于高精度和高可靠性的需求很高,因此电子束焊接技术在该领域的应用也较为广泛。
例如,在半导体制造过程中,电子束焊接被用于连接不同层次的电子元件,确保其电气连接的稳定性和可靠性。
此外,电子束焊接还被用于连接液晶显示器的电子线路板,实现高精度的焊接和封装。
这些应用都极大地促进了电子设备的小型化、高性能化和可靠性。
4. 医疗器械制造领域医疗器械的制造对于材料的纯度、焊接的精确性和耐腐蚀性都有很高的要求。
电子束焊接技术在医疗器械的制造中得到了广泛应用。
例如,在人工关节的制造中,电子束焊接技术能够实现金属部件的高精度、无瑕疵的连接,确保关节的稳定性和耐久性。
此外,电子束焊接还被用于连接心脏起搏器和其他医疗器械的电子元件,提供可靠的电气连接。
电子束焊是什么焊接方法
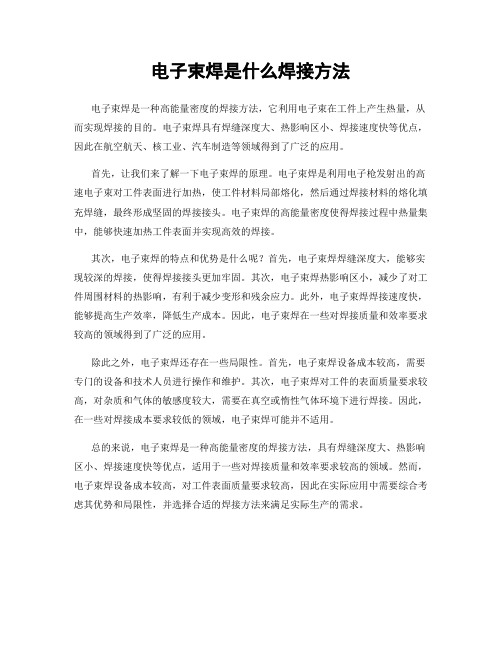
电子束焊是什么焊接方法
电子束焊是一种高能量密度的焊接方法,它利用电子束在工件上产生热量,从而实现焊接的目的。
电子束焊具有焊缝深度大、热影响区小、焊接速度快等优点,因此在航空航天、核工业、汽车制造等领域得到了广泛的应用。
首先,让我们来了解一下电子束焊的原理。
电子束焊是利用电子枪发射出的高速电子束对工件表面进行加热,使工件材料局部熔化,然后通过焊接材料的熔化填充焊缝,最终形成坚固的焊接接头。
电子束焊的高能量密度使得焊接过程中热量集中,能够快速加热工件表面并实现高效的焊接。
其次,电子束焊的特点和优势是什么呢?首先,电子束焊焊缝深度大,能够实现较深的焊接,使得焊接接头更加牢固。
其次,电子束焊热影响区小,减少了对工件周围材料的热影响,有利于减少变形和残余应力。
此外,电子束焊焊接速度快,能够提高生产效率,降低生产成本。
因此,电子束焊在一些对焊接质量和效率要求较高的领域得到了广泛的应用。
除此之外,电子束焊还存在一些局限性。
首先,电子束焊设备成本较高,需要专门的设备和技术人员进行操作和维护。
其次,电子束焊对工件的表面质量要求较高,对杂质和气体的敏感度较大,需要在真空或惰性气体环境下进行焊接。
因此,在一些对焊接成本要求较低的领域,电子束焊可能并不适用。
总的来说,电子束焊是一种高能量密度的焊接方法,具有焊缝深度大、热影响区小、焊接速度快等优点,适用于一些对焊接质量和效率要求较高的领域。
然而,电子束焊设备成本较高,对工件表面质量要求较高,因此在实际应用中需要综合考虑其优势和局限性,并选择合适的焊接方法来满足实际生产的需求。
- 1、下载文档前请自行甄别文档内容的完整性,平台不提供额外的编辑、内容补充、找答案等附加服务。
- 2、"仅部分预览"的文档,不可在线预览部分如存在完整性等问题,可反馈申请退款(可完整预览的文档不适用该条件!)。
- 3、如文档侵犯您的权益,请联系客服反馈,我们会尽快为您处理(人工客服工作时间:9:00-18:30)。
机械工艺师∞00.1051电子束焊接技术的应用
口尹夕兵
近几年,我厂开发出日本五十铃系列MSA、MSB数种汽车变速器及TCM叉车变速器,其产品的技术水平在国内处于领先地位。
在齿轴零件的制造过程中,有些零件考虑其结构及加工工艺性,大胆采用了国内先进的电子柬焊接技术,应用效果较为显著,既提高了产品质量,又降低了生产成本。
一、设备概况
1.我厂现采用的电子束焊机是北京中科电气高技术公司生产的低真空齿轮焊接专用设备,型号为EBW---4GC,焊接具有可靠的自动运行程序系统,操作方便、焊缝质量优良、重复精度高。
2.设备的电子束加工原理,是由灼热阴极所发射的电子流在阴、阳极高压作用下加速,经过磁透镜汇聚到工件上,并冲击工件,将动能转化为热能。
在功率密度高达1盯一1妒W/mF的条件下,使金属快速地加热、熔化完成焊接加工。
3.加工特点
1)因为电子束的能量密度高,在加速高压作用下,电子被加速至1/2—1/3倍光速。
使被轰击的工件焊缝处温度瞬间可达lO'℃以上,几乎可熔化各种金属如黑色、有色、耐熔、活性金属及其合金,实现其焊接的目的。
2)热影响区域小,焊缝的深宽比可达50:l,焊接变形较小(能量集中,产生高温时间短),当焊缝深度为3.4mm时,变形可控制在0.01。
0.02ram,可实施精加工后的焊接,即焊接后无需再进行加工。
3)由于焊接过程是在真空中进行,排除了大气中的有害气体(如氢、氧等)的影响,焊接缺陷少。
4)由于电子束能量密度高,焊接速度可以很高,生产率水平较高可达60件/d,时。
5)焊接完成后可采用着色探伤或采用超声波探伤仪进行探伤检查,我厂现采用uF眦A型智能超声波齿轮焊缝探伤机。
二、影响焊接质量的因素
1.材料的可焊性
根据钢的化学成份与焊接热影响区淬硬性的关系,把钢中的合金元素(包括C)的含量,按其作用折算成碳当量作为粗略地评定钢材焊接性的一种参考指
标。
碳当量计算公式如下:
nn.Mn.Cr+Mo+V.Ni+Cu
L冒2。
+百+——『_+—话一
当岛≥0.35时,可焊性较差。
因为碳当量越高,淬硬性越大,形成马氏体焊接时极易产生裂纹,导致焊接无效。
2.电子束焊缝处不需开坡口也不需大的倒角,且焊缝与凸起边缘应保持有0.7—1.5mm的距离。
避免边缘被电子柬熔化,使工件报废。
3.焊缝处配合间隙选用过渡配合H6,r6或HS/r7,以最大间隙≤0.03area,最大过盈≤0.03Ⅻ为宜。
焊后变形要求高时,应选择过盈较为合适。
4.压嵌深度相等,保持被焊面平整,以防焊偏或焊深减少。
5.焊接夹具的定位及焊件与夹具的配合精度应合适。
主要目的在于保证电子束准确地打在焊缝上。
6.焊接前应进行清洗,需去除焊接表面的油污、杂屑等,而后进行烘干,并在6h内实施焊接。
三、电子束焊接土艺实例
1.3t液力叉车输入轴总成零件的加工
该零件系叉车变速器中较为复杂的零件之一,从工艺上分析其最大直径≠138与最小直径处≯30差值很大,台阶长度较长,并且具有I/,126空腔。
从材料利用或从毛坯锻造角度出发,不宜采用整体设计,否则,既浪费材料,又浪费机加工工时;另外输入轴外圆上多环形槽,且轴体一端有细长深孔,另一端又有渐开线花键内齿,离台器壳内腔壁薄,两端均有8等分槽,不宜采用整体设计,否则将造成机加工困难,甚至影响加工质量(见图1)。
焊接部分进行防渗处理,输A轴热处
图2翰A轴总虞
52机械工艺师2000,10
雷达天线外导体的振动镗孔
口肖继明郑建明袁启龙李言李淑娟口付海军
摘要利用振动切削技术和一种集镗、饺和挤压于一体的深孔专用镗头,很好地解决了雷达天线外导体的深乳加工,效率高,刀具寿命长。
美键词:雷达天线外导体深孔加工振动镗削
雷达天线外导体是雷达的关键零件,其结构特点是薄壁长管件,内孔尺寸精度、形状精度和表面粗糙度要求高,材料强度、硬度较低,塑性较大,深孔加工是其生产中的一大难题。
采用振动切削深孔镗孔技术,结合研制的一种集镗、铰和挤压于一体的深孔专用镗头,一次镗孔即达到外导体深孔加工的技术要求。
一、雷达天线外导体工艺分析
图l所示为雷达天线规格中两种天线外导体简图,材料为黄铜管(H62一Y或Y2),直径上的镗孔加工余量1—4113TI;强度钆=340N,Ⅻn2,延伸率am=30畅,加工中易变形,断排屑困难,易粘结等;壁厚与孔径比8,D为1,2l一1t10,长度与孔径比L/D达32—74.5,属薄壁长管零件,加工工艺难点主要是深孔加工。
用普通的深孔镗刀加工,由于刀具的自导性和工作平稳性差,极易使孔镗偏或出现多边形(试验中常常是三角形)。
同时伴有孔径扩大和表面波纹产生。
因此,提高刀具在镗削过程中的白导性和工作平稳性是解决问题的关键。
试验研究表明,应从以下两方面提高刀具在镗孔过程中的自导性和工作平稳性,即一方面采用具有良好工艺效果的振动切削镗孔技术代替传统的镗孔方法,改善刀具的工作条件和切削性能,解决断排屑问题,提高加工质量;另一方面改进刀具结构,提高刀具的自导性和稳定性。
图1井导体零件简图
理后继续完成全部加工(主要指磨加工),离台器壳调质处理后完成全部加工,再实施电子束焊接。
焊后.着色法探伤检查。
在最初的试验中,由于离合器采用加cr材料,碳当量高,焊接后出现裂纹等缺陷,改用35钢,焊接性能明显改善。
该零件经长期使用证。
焊接部位质量稳定、可靠。
2.日本五十赞咖姒、MsB变速器二轴上的传动轮(采用接合齿齿轮本体的光轴电子束焊联接方式在开发产品的初期,此处采用的是花键联接方式(见
2)。
这种联接方式中,由于齿体外花键齿采用插削加工(齿厚尺寸公差不能过小,否则将不经济)而且经过热处理后产生变形。
压配前,齿环内花键齿(拉削加工)也已经过最终热处理,必然存在热处理变形,诸多的影响因素造成内、外花键齿齿厚的尺寸变动,压配时过盈量极难控制到设计的理想程度。
压配后可能随机出现压裂(过盈量过大)或松脱现象(过盈量过小,甚至出现间隙)。
而后采用电子柬焊接工艺(见图3),经过工艺验证、变速器台架试验以及整车道路试验,焊接后联接强度满足设计要求。
由花键过盈联接,改为光轴、图2传动齿轮的原设计圈3改进后的传动齿轮设计光孔电子束焊工艺,光轴、光孔加工精度易于保证,且不受热处理变形的影响(先焊接成总成后,再进行热处理).既保证了产品质量,提高了劳动效率,又降低了生产成本。
作者通讯地址:安簟省汽车齿轮葙甚厂(2,砷IO)
收稿日期:加哪27
电子束焊接技术的应用
作者:尹夕兵
作者单位:
1.林世昌.LIN Shi-chang影响电子束焊接质量的几个工艺因素[期刊论文]-电焊机2005,35(7)
2.尹夕兵电子束焊接技术的应用[期刊论文]-机械工艺师2000(10)
3.刘春飞.张益坤电子束焊接技术在航天工业中的应用[会议论文]-1999
4.张秉刚.冯吉才.吴林电子束焊接技术研发动态[会议论文]-2002
5.周广德.陶守林.ZHOU Guang-de.TAO Shou-lin电子束焊接在我国汽车零部件的应用与发展[期刊论文]-电焊机2005,35(7)
6.张毓新.王文成填丝电子束焊接工艺的应用[会议论文]-1999
7.陈芙蓉.霍立兴.张玉凤电子束焊接技术在工业中的应用与发展[期刊论文]-电子工艺技术2002,23(2)
8.何成旦.李鹤岐.李春旭.许启晋电子束焊接电子枪电子光学系统设计[期刊论文]-兰州理工大学学报2004,30(5)
9.刘春飞.张益坤电子束焊接技术发展历史、现状及展望(Ⅳ)[期刊论文]-航天制造技术2003(4)
10.曹树春.李中平.张子民.苏雅龙.王斌.杨春名.陈地红.景漪.袁平工业用电子加速器控制系统的研制[会议论文]-2008
本文链接:/Conference_233182.aspx。