套筒石灰竖窑工艺介绍
600TPD套筒石灰窑工艺简介
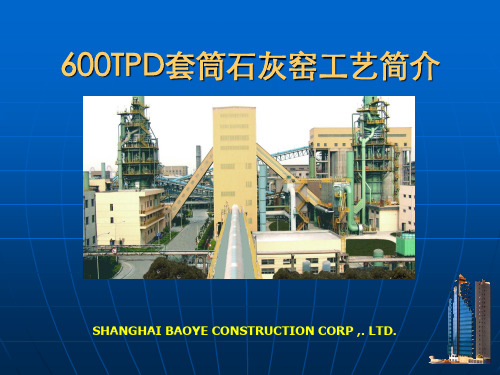
料
a.上料导轨为焊接H型钢 导轨,带防侧摆装置;
导
b.上料小车容积为3m3,额 轨
定载重2.5t;
c.配限位:下极限\翻转 极限。
下 极 限 设 置
翻转极限
石 料 路 由
功能说明:
a.均匀一致布料,防止
布
料面差异过大;
料
b.双液压马达驱动,保 证平稳;
装
c.定点卸料。
置
布 料 器 剖 面 图
旋转布料器
用
户 功 a.根能据说窑明的:工况进行燃气入窑流点量
的调节 b33.支% 进管上均烧匀嘴 分配燃67气% 的进下流烧量嘴比 c.实时监控燃气热值,进行入窑流
量的调节
煤 气 调 压 站
(3)、冷却风系统
主要设备: a.冷却风机(2台) b.管道、阀门(如图)
功能说明: a.冷却风机(工频),一用一备、互为备用 b.分两路冷却,最终点为上下内套筒
b.防雨作用。
窑顶结构: a.窑顶结构圆形密闭框架结构, 结构形式相对其他部位比较复 杂。
b.主要为支撑上内套筒,
窑 顶
上部窑体结构
平台(从下至上) 出灰平台 下烧嘴平台 上烧嘴平台 热交换器平台 窑顶平台 热交换器顶部平台
窑本体楼梯及平台
②、上、下内套筒
上 内 套 筒
下
内
套
功能说明:
筒
a.形成并流、逆流煅
600TPD套筒石灰窑工艺简介
组成:
①、窑壳及附属结构 ②、上、下内套筒 ③、燃烧设备
①、窑壳及附属件
石灰卸料槽
下 部 窑 体 底 座
下部窑体结构
石灰导料板
下
部
下
窑
内
石灰竖窑的工艺流程

石灰竖窑的工艺流程
石灰竖窑是一种传统的石灰生产方法,其工艺流程主要包括以下几个步骤:
1. 原料准备:将石灰石或石灰岩等石灰矿石经过破碎、研磨等处理,制成一定粒度的石灰石粉。
2. 下料装窑:将准备好的石灰石粉通过输送装置送入竖窑内,形成一定的料层。
3. 煅烧石灰:点燃竖窑下部的燃料,通过燃烧产生的高温将石灰石进行煅烧,使其分解生成生石灰。
4. 生石灰冷却:生石灰生成后,通过排烟筒排出炉内烟尘,然后经过冷却器等装置进行冷却,使其达到适宜的温度。
5. 石灰粉碾磨:经过冷却的生石灰通过研磨机械进行碾磨,制成石灰粉。
以上就是石灰竖窑的主要工艺流程,这种传统的石灰生产方法已经逐渐被新型石灰生产设备所替代,但在一些地区仍然有人继续使用这种方法进行石灰生产。
套筒窑生产工艺
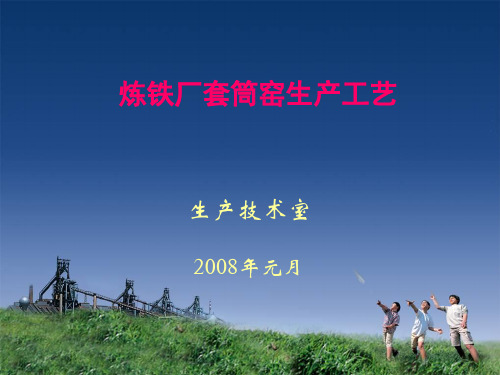
二、活性石灰煅烧过程 机理分析
生石灰的灼减
一般是指石灰在1000℃左右所失去的重量。石
灰灼减一是由于石灰未烧透,二是由于石灰在大气
中吸收了水分和CO2。
由于煅烧石灰的原料通常含有以二氧化钙为主的杂质,使 煅烧后石灰的组成中有游离氧化钙和结合氧化钙,游离氧 化钙中又分活性氧化钙和非活性氧化钙。
套筒窑同时又是负压生产,一是有利于环保;二容易操作;
三能随时查看石灰窑运行状况,利于检修等优点。
2、生石灰生产的目的与意义:
活性石灰是在炼钢造渣中性能活泼、反应能力强、 熔解能力高的优质材料。其主要特点是:体积密度小、 氧化钙矿物结晶细小、比表面积大、气孔率及活性度
高、残余CO2及有害杂质P、S低等特性。
石灰石中杂质的影响 原料石灰石的杂质其主要来源是天然石灰石自身含有的 杂质和矿体中夹杂带入的泥沙。杂质的主要成分为酸性 氧化物如:SiO2、Al2O3、Fe2O3等,这些酸性氧化物在 900℃即可与生石灰进行次生反应,石灰石在煅烧炉内
发生的反应有:
主反应:CaCO3 ⇋ CaO+CO2↑ 次生反应: 2CaO+SiO2→2CaO·SiO2(硅酸二钙) 3CaO+2SiO2→3CaO·2SiO2(二硅酸三钙) 3CaO+Al2O3→3CaO·Al2O3(铝酸三钙) CaO+Fe2O3→ CaO·Fe2O3(铁酸钙)
0.48 0.55 0.71 0.22
2.30 4.30 7.30 12.20
340 316 302 266
2.0
3.0 4.0
85.19
80.11 78.99
0.010
0.010 0.008
0.28
套筒式竖窑

焙烧石灰用套筒式竖窑1、套筒式竖窑焙烧的特点在各种竖窑中,焙烧的物料与燃烧气流存在两种流动换热方式,即燃烧气流与物料同向流动的并流(又称顺流)方式和燃烧气流与物料流动反向相反的逆流方式。
理论和实践证明,在活性石灰焙烧中,顺流换热、焙烧要优于逆流换热焙烧,其焙烧物料受热均勾,石灰活性度高,产品质量好;而逆流具有换热热效率高的特点。
套筒式竖窑通过其比较复杂的结构,使用了并流和逆流两种方式换热、培烧。
从结构上看,套筒式竖窑由窑外壳和内套筒组成,从上至下大致可分为四个区域,即石灰石预热带、上、下燃烧室之间逆流焙烧带、下燃烧室下部并流焙烧带和石灰冷却带,物料与气流就在内、外壳体之间流动。
在物料流动方向上,窑顶的横梁、上拱桥、下拱桥和出料门四部分结构,上下两两之间成60。
角交错分布,实现了物料在向下流动的过程中的自动再次分布,保证了不同粒度的物料在窑体内均能均匀受热焙烧。
物料在环形空间内自上而下,进行四次布料。
套筒式竖窑另一个结构特点是有独立的燃烧室,燃烧室沿圆周方向均匀布置,位于每个拱桥下面:燃料在燃烧室内充分燃烧后,均匀和稳定的高温气流进人物料层,避免火焰直接与物料接触,燃料变化对套筒式竖窑影响相对较小。
从气固流动方向来看,套筒式竖窑属于并流焙烧石灰窑。
利用从喷射管内喷出的高速流动热空气,在下燃烧室处产生低压区,使从下烧嘴进人的燃料和助燃空气与窑内的物料在下燃烧室下部同方向流动并与之反应,形成并流焙烧带。
在并流焙烧区域内,石灰石原料充分与高温气体接^!,反应生成石灰产品。
通过控制循环气体的温度,使焙烧过程得到控制并充分利用热量3套筒式竖窑内的循环气体是指从下烧嘴进人的燃料和助燃空气,在下燃烧室下部的并流焙烧带与石灰石原料充分反应后,与从窑底冷却带进人的冷却空气一起进人到下内套筒上段内,然后经过上拱桥内的循环气体通道管流入喷射器,与喷射管内的热空气混合后一起再次喷射进人下燃烧室。
循环气体的产生,在窑内形成了并流焙烧带;同时循环气体也使窑内的热量得到了充分的利用,降低了石灰产品的热耗。
套筒式竖窑工艺特点及其相关工艺配置[1]
![套筒式竖窑工艺特点及其相关工艺配置[1]](https://img.taocdn.com/s3/m/b6a1546c1eb91a37f1115ce6.png)
套筒式竖窑工艺特点及其相关工艺配置罗 琨(武钢设计研究院湖北武汉430080)摘 要 重点介绍了套筒式竖窑生产活性石灰的工艺特点及相关工艺配置,简要分析比较了几种活性石灰窑的优缺点,阐述了套筒式竖窑的应用条件。
关键词 套筒式竖窑 工艺 应用PR OCESS CHARACTERISTICS AN D ARRANGEMENT OF BECKENBACHANNU LAR SHAFT KI L NLuo K un(Design &Research Institute of WISC O Hubei Wuhan 430080)Abstract The present paper describes the process characteristics and arrangement of the BASK kiln ,briefly analyzes and com pares the advantages and disadvantages of several active lime shaft kilns and eluciates the prerequisite for application of the BASK kiln.K eyw ords BASK kiln process application罗 琨,女,工程师收稿日期:2001-07-191 前 言套筒式竖窑又名环形窑,起源于德国肯巴赫・威尔曼司特勒公司(BECKE NBACH W ARMESTE LLE G M BH ),世界上已有300余座套筒式竖窑投入使用。
欧洲和日本用这种窑型较为普遍。
近几年来,我国也逐渐引入这种窑型,先后有5座套筒式竖窑在梅钢、马钢、本钢等大型钢铁企业应用。
实践表明,套筒式竖窑设备简单,操作和维修方便,工作环境较好,产品质量优良,是一种很有发展前景的新型窑型。
2 套筒式竖窑的基本结构套筒式竖窑主要由窑体、上料装置、出料装置、燃烧室、换热器、喷射器以及风机系统等构成(见图1)。
套筒石灰窑的工作原理
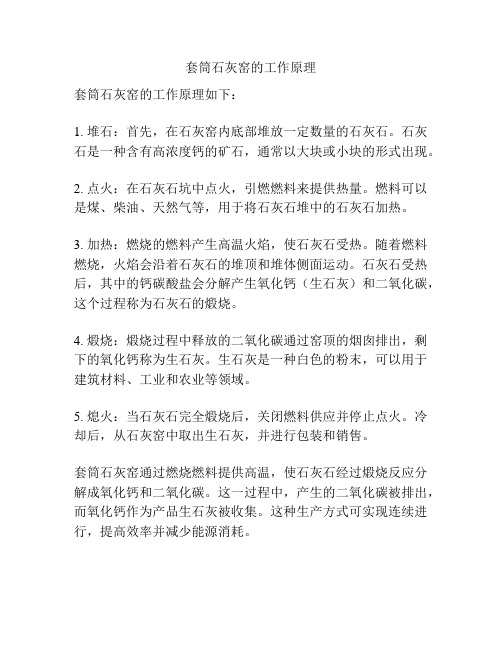
套筒石灰窑的工作原理
套筒石灰窑的工作原理如下:
1. 堆石:首先,在石灰窑内底部堆放一定数量的石灰石。
石灰石是一种含有高浓度钙的矿石,通常以大块或小块的形式出现。
2. 点火:在石灰石坑中点火,引燃燃料来提供热量。
燃料可以是煤、柴油、天然气等,用于将石灰石堆中的石灰石加热。
3. 加热:燃烧的燃料产生高温火焰,使石灰石受热。
随着燃料燃烧,火焰会沿着石灰石的堆顶和堆体侧面运动。
石灰石受热后,其中的钙碳酸盐会分解产生氧化钙(生石灰)和二氧化碳,这个过程称为石灰石的煅烧。
4. 煅烧:煅烧过程中释放的二氧化碳通过窑顶的烟囱排出,剩下的氧化钙称为生石灰。
生石灰是一种白色的粉末,可以用于建筑材料、工业和农业等领域。
5. 熄火:当石灰石完全煅烧后,关闭燃料供应并停止点火。
冷却后,从石灰窑中取出生石灰,并进行包装和销售。
套筒石灰窑通过燃烧燃料提供高温,使石灰石经过煅烧反应分解成氧化钙和二氧化碳。
这一过程中,产生的二氧化碳被排出,而氧化钙作为产品生石灰被收集。
这种生产方式可实现连续进行,提高效率并减少能源消耗。
石灰竖炉(石灰立窑)工艺流程

【河南中材水泥设备制造网】石灰竖炉(又名石灰立窑、石灰回转窑),主要包括炉壁和设在炉壁上的烧嘴,在竖炉的中央植入一个柱状炉芯,炉芯和炉壁之间有环形间隙。
【关键词】石灰竖炉,石灰立窑,石灰回转窑,工艺流程一、石灰竖炉工艺概述装载机将合格的原燃料分别装入石灰石仓和煤炭仓,然后通过输送皮带运至混配料仓。
原燃料按设定值用电子秤准确称量,通过振动绘料机均匀给料后进行混匀,然后由提升料车把混合料运至炉顶受料斗,通过炉顶蜗壳式布料器完成炉内布料。
炉料靠自重缓慢向下运动,相继通过予热带、锻烧带、冷却带。
炉料在下降过程中,与炽热的上升煤气流进行着复杂的热交换,并伴随着石灰石的分解和生石灰的晶粒的发育成长过程。
当全过程完成时,也被助燃空气冷却降温至4 0 -- 6 0℃,然后由卸料机在不漏气的情况下卸至炉外成品皮带上。
由多斗提升机将石灰运至成品料仓。
如果需要筛分,先进行筛分后装入块灰仓和粉灰仓。
2..工艺特点(1) 自动称量、均匀配料对入炉石灰石和煤炭准确称量和合理配比是石灰竖炉优质锻烧和节能降耗的关键环节之一。
(2)均匀给料、旋转布料炉顶加料系统由受料斗、传动和旋转布料器组成。
由料车向旋转布料器均匀而定量给料,促使物料在入炉前进一步混合。
旋转布料器是圆周式定点布料,可自动也可手动定点布料,炉内断面上石灰石和煤炭呈"点、网"状分布,料面呈"M"形状,从而使炉内气流分布均匀,对锻烧带稳定起到了关键性的作用。
(3)合理供风、密封出灰该部分由离心风机、风帽、卸灰机组成。
风机按要求定量供风。
风帽则是我们自行设计,风帽保证炉内供风均匀,有效地抑制了竖炉的偏烧和过烧现象。
卸灰机可使园周各处排料均匀,保证料柱均匀平稳下降和料柱异常时的及时排除,既保证了炉内气流稳定和防止炉气外泄,又提高了现场环境。
(4)自动控制,安全可靠该石灰炉系统采用了自动控制技术。
在布料、混配、供风和卸灰等关键设备上使用了以确保各个关键设备的安全运行。
立式套筒石灰窑施工技术
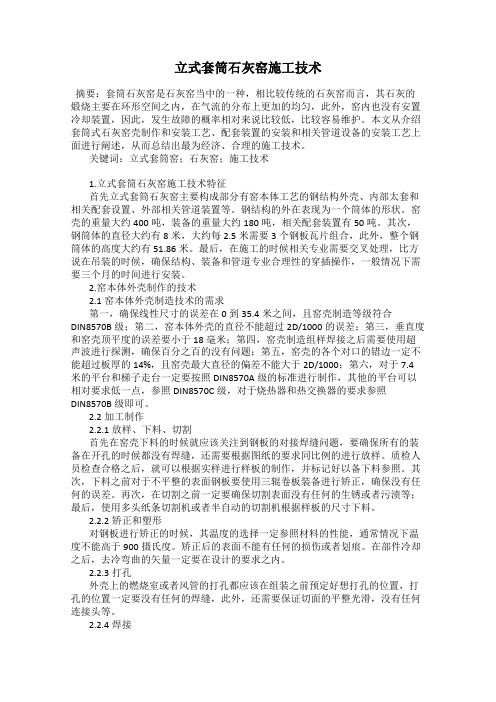
立式套筒石灰窑施工技术摘要:套筒石灰窑是石灰窑当中的一种,相比较传统的石灰窑而言,其石灰的煅烧主要在环形空间之内,在气流的分布上更加的均匀,此外,窑内也没有安置冷却装置,因此,发生故障的概率相对来说比较低,比较容易维护。
本文从介绍套筒式石灰窑壳制作和安装工艺、配套装置的安装和相关管道设备的安装工艺上面进行阐述,从而总结出最为经济、合理的施工技术。
关键词:立式套筒窑;石灰窑;施工技术1.立式套筒石灰窑施工技术特征首先立式套筒石灰窑主要构成部分有窑本体工艺的钢结构外壳、内部太套和相关配套设置、外部相关管道装置等。
钢结构的外在表现为一个筒体的形状。
窑壳的重量大约400吨,装备的重量大约180吨,相关配套装置有50吨。
其次,钢筒体的直径大约有8米,大约每2.5米需要3个钢板瓦片组合,此外,整个钢筒体的高度大约有51.86米。
最后,在施工的时候相关专业需要交叉处理,比方说在吊装的时候,确保结构、装备和管道专业合理性的穿插操作,一般情况下需要三个月的时间进行安装。
2.窑本体外壳制作的技术2.1窑本体外壳制造技术的需求第一,确保线性尺寸的误差在0到35.4米之间,且窑壳制造等级符合DIN8570B级;第二,窑本体外壳的直径不能超过2D/1000的误差;第三,垂直度和窑壳顶平度的误差要小于18毫米;第四,窑壳制造组样焊接之后需要使用超声波进行探测,确保百分之百的没有问题;第五,窑壳的各个对口的错边一定不能超过板厚的14%,且窑壳最大直径的偏差不能大于2D/1000;第六,对于7.4米的平台和梯子走台一定要按照DIN8570A级的标准进行制作,其他的平台可以相对要求低一点,参照DIN8570C级,对于烧热器和热交换器的要求参照DIN8570B级即可。
2.2加工制作2.2.1放样、下料、切割首先在窑壳下料的时候就应该关注到钢板的对接焊缝问题,要确保所有的装备在开孔的时候都没有焊缝,还需要根据图纸的要求同比例的进行放样。
- 1、下载文档前请自行甄别文档内容的完整性,平台不提供额外的编辑、内容补充、找答案等附加服务。
- 2、"仅部分预览"的文档,不可在线预览部分如存在完整性等问题,可反馈申请退款(可完整预览的文档不适用该条件!)。
- 3、如文档侵犯您的权益,请联系客服反馈,我们会尽快为您处理(人工客服工作时间:9:00-18:30)。
套筒石灰竖窑工艺介绍讲解人:刘林一、石灰窑的概况1、国内常见的石灰窑有:回转窑、竖窑、BASK套筒竖窑、麦尔兹窑(双膛细粒窑)等。
2、BASK套筒石灰竖窑几种石灰窑比较:(1).煅烧工艺合理:实现逆流和并流共存的煅烧工艺;(2).产品质量高:活性度达到350ml,一般炼钢对活性度的要求较高,化工行业(如电石)对活性度的要求不高,但对生/过烧率有要求;(3).环保安全,负压操作(窑内压力位-1000mm水柱,煤气压力位16KPa,可以在线检查);(4).节能,利用了换热器及二次循环空气;(5).对原料的粒度有要求(一般是30mm~80mm);(6).对原料的成分有要求(MgO的含量≤1.0),否则容易产生设备(换热器)的堵塞。
二、石灰窑的组成1、常见的套筒竖窑三大系统:(1).原料储运+筛分系统(2).竖窑本体焙烧(煅烧)系统(3).成品贮运+筛分系统2、三大系统的组成及工艺流程:(1).原料储运+筛分系统(2).竖窑本体焙烧(煅烧)系统a.套筒竖窑煅烧工艺及结构见下图工艺流程:石灰石原料经卷扬机上料小车(1)、漏斗及溜槽、密封闸门、旋转布料器及料钟(2),进入窑内装料槽(3)。
在窑顶入料口处设置密封闸门,以避免外界空气进入而影响套筒竖窑的负压操作。
窑内装石灰石的环形空间是由窑钢外壳(4)内部耐火墙和与其同心布置的上、下(5、6)内筒分割形成。
套筒竖窑有上、下两层烧嘴(7、8)并均匀错开布置,每层烧嘴有七个圆柱形燃烧室(9、10),每个燃烧室都有一个用耐火材料砌筑的从窑外壳到下内筒的过桥(16),高温气体从燃烧室内出来,经过过桥下面形成的空间进入料层。
两层烧嘴将套筒竖窑分成两个煅烧带,上煅烧带为逆流,下煅烧带为并流。
并流带下部为冷却带,在冷却带石灰将自身热量传递给冷却的空气,此处仍为逆流。
冷却石灰的空气由于废气风机作用向上抽,而石灰则在冷却带的底部通过液压推杆(11)及出灰装置(12)排出,排出的石灰进入到位于套筒竖窑底部的石灰料仓内(13),石灰料仓内的石灰通过振动给料机(14),经一定的时间间隔被排出。
上、下内筒钢壳体上都砌有耐火材料,钢壳体环隙通过内筒冷却风机产生的空气冷却。
冷却下内筒的空气预热后,经位于上、下层七个过桥内的十四个下内筒冷却空气扁平管(17)汇集到内筒冷却空气环管(一)(18)中,为了达到上、下排烧嘴均衡分配助燃空气,将其从内筒冷却空气环管(一)再分配到环管(二)、(三),然后分别送到各个烧嘴(20)。
冷却上内筒的空气又分为两部分:一部分冷却上内筒后排入大气,另一部分用于自动吹扫烧嘴和冷却火焰探测器观察孔。
二台驱动风机 (罗茨风机)将适量空气送到换热器被预热到350℃左右。
预热的驱动空气从换热器出来后进入驱动空气环管(18),并被送到七个喷射器(19),作为喷射器抽吸循环气体的动力气体。
下层燃烧室中由于加入了驱动空气和循环气体,因此供给过量空气,使燃料能够完全燃烧,燃烧后高温气体被分成两部分,一部分由废气风机抽到上部,进入位于上、下两层燃烧室间的中间煅烧带。
另一部分与冷却石灰预热空气通过循环气体入口(15)进入到下内筒,从位于上层七个过桥内的七个循环气体管道(21)中出来,由驱动空气在喷射器中产生的动力气体作用下送到下层六个燃烧室(10)中。
并流带高温气体和冷却石灰预热空气的混合气体称为循环气体(其中含有过剩空气可以作为燃烧二次空气),循环气体的温度为840~920℃。
并流带循环气体是整个煅烧工艺的关键,操作中通过检测循环气体的温度来控制整个窑的煅烧状况。
循环气体控制主要通过控制驱动空气来实现,循环气体是通过喷射器产生的作用力带动循环。
在上层燃烧室(9)中供给的空气量不足,只有50%左右,为不完全燃烧,进入料层的气体中还含有一定的燃料。
由于废气风机的作用,不完全燃烧的气体进入上部料层时与来自下方的含过剩空气的气流相遇,使不完全燃烧的气体得到完全燃烧。
完全燃烧的烟气在窑顶分成两部分:一部分70%经预热带到窑顶环形烟道(22)进入废气风机,另一部分30%经悬挂在窑顶的上内筒(5),进入到换热器预热驱动空气后再进入废气管道,窑内所有的废气都经废气风机引出,进入废气风机的温度为230~240℃左右,然后经流量调节阀混入冷风降到160~180℃进入布袋除尘器除尘后由烟囱排入大气。
窑体从上至下依次为预热带-上部煅烧带-中部煅烧带-下部煅烧带-冷却带,整个窑体无水冷。
(3).成品贮运+筛分系统三、套筒竖窑本体1、概况套筒竖窑是由德国杜塞尔多夫土石热源公司的卡尔、贝肯巴赫于1960年发明的,由于窑体是由内外两个圆形钢筒组成,因而得名“贝肯巴赫环形套筒竖窑”简称BASK。
第一座BASK窑于1962年建在德国威尔曼司特勒公司,至今尚在运行。
目前全世界已建有这种竖窑300多座。
2、组成及工艺流程套筒竖窑焙烧(煅烧)系统共分为四大区域(①窑本体区域、②除尘系统区域、③综合楼+电气楼区域、④燃气加压、调压区域)和十四个系统。
具体如下:(1).上料、布料系统【组成部分】a.称量料斗(2.5吨)b.上料小车(2.5吨)c.上料导轨d.导向滑轮(3个)e.卷扬机装置(4吨)f.旋转布料器(受料溜槽、旋转料仓、料钟、液压马达、旋转机构、配重等)【工艺流程】(2).冷却风系统【组成部分】a.冷却风机(2台、一用一备,属于核心设备,在供电系统断电的情况下,两台风机同时作业,持续给内套筒供冷却风,确保石灰窑内套不被烧坏。
)b.冷却风管、阀门及仪表等【工艺流程】a.冷却风出风机房后分为两路,一路(占风量的78%)进入到下内套筒,另外一路(占风量的22%)进入上段内套筒(分三路支管进入),其作用为冷却内套筒。
b.进入下内套筒的冷却风被预热后,经冷却空气扁平管进入第一层环管(为助燃空气)c.进入上内套筒的冷却风冷却内套后,被直接排放到大气中。
(3).驱动风系统【组成部分】a.驱动风机(又名罗茨风机:属泵系列,利用三片叶轮将空气挤压出去,特点是升压快,确定是噪音大。
一台变频,一台恒速,两台同时运转)b.驱动风管、阀门、仪表等【工艺流程】a.驱动风机出来的空气直接进入到换热器,经过烟气预热后,直接进去到第四层环管。
再分散到7个喷射器中。
b.注意:在进换热器前后的管道之间有一个旁通管,其作用是为了开窑时使用。
(4).助燃风系统【来源】a.冷却扁平管出来的热空气b.经过换热器预热后的驱动空气【去向】a.窑体上部共四圈环管,标号为1、2、3、4,其中1、2、3环管为并联相通。
第4层单独。
b.第1、2、3层环管中,第1层环管为进风口,第2、3层为出风口。
其中第2层环管的助燃风直接进入下烧嘴。
第3层环管的助燃风进入上烧嘴。
c.第4层环管的助燃风分散到7个喷射器,加速下燃烧室燃料的完全燃烧。
(5).二次空气回路系统【来源】a.进入下燃烧室的热空气中的30%随石灰石自上而下流动,与窑底冷却石灰的冷空气相混合后,经内套筒中段进入到上燃烧室循环管。
形成二次空气回路。
【去向】经过循环管到喷射器,进入下燃烧室,热量重复利用。
(6).燃气系统(含氮气吹扫)【组成部分】a.调压站(调节阀、过滤器、放散管、波纹管、排水器等)b.燃气管道、阀门、仪表、烧嘴【工艺流程】a.经过加压的煤气进入调压站后(调整压力)进入燃气主管,分两路:其中一路(67%)到下烧嘴,另外一路(33%)到上烧嘴。
(7)废气净化系统(本体除尘系统)【组成部分】a.烟箱、重力除尘管;b.废气风机(主排烟风机);c.液压三通阀d.除尘器(低压长袋脉冲除尘器)e.除尘风机f.排气筒(又名烟囱,事故烟囱+净化后的烟气)【工艺流程】a.废气的来源有两路:一路是上内套筒废气直接排出到换热器,预热驱动空气后,再回到重力除尘管。
另外一路为上部两处废气烟箱并联到重力除尘管。
b.经过重力除尘管的烟气经过废气风机(被废气风机抽出),通过液压三通阀门后分为两路:第一路(当除尘器正常工作),烟气直接经过除尘器,第二路(当除尘器检修时),烟气经过排气筒(事故烟囱)排放到大气。
c.在除尘器进风口前有一处调节阀,其作用为混风。
d.经过除尘器净化后的烟气,通过除尘风机的作用经过排气筒直接排放到大气。
e.开窑和烘窑时,烟气都由事故烟囱排出。
(8)液压系统【组成部分】a.液压站b.液压管(高压管)c.压力表、固定管卡d.油缸、金属软管e.高压球阀【工艺流程】a.液压站齿轮泵为双联齿轮泵。
b.主泵(Q1/Q2),副泵(Q3/Q4)及循环泵c.七个用户点:①.窑顶旋转布料器料钟、②窑顶旋转布料器液压马达、③窑顶旋转布料器翻板阀、④出灰装置、⑤液压三通阀、⑥称量料斗、⑦窑底振动出灰机。
d.其中Q1伺服①+②+③;Q2+Q4伺服④;Q3伺服⑤+⑥+⑦。
e.整个液压系统通过阀台控制,由PLC整体控制。
f.工作压力为11MPa(9)压缩空气【用途】a.气动调节阀b.平台、设备吹扫c.除尘器(10)水系统【用途】a.循环水(风机冷却)b.生活水c.平台清理(11)焙烧系统【组成部分】a.竖窑外壳b.上下内套筒c.上下燃烧室及喷射器d.窑内衬(耐材)(12)出灰系统【组成部分】a.出灰装置(7套,抽屉式)靠液压控制b.振动出灰机(靠电机激振,液压控制出灰阀门)【工艺原理】a.出灰装置的频率与旋转布料器的频率相同;b.成品石灰经出灰装置卸料后,储存在窑底石灰料斗中,石灰料斗设上下料位计,以防止石灰出现料面过低或者过高的现象。
c.窑底振动出灰机按一定频率卸料。
(13)出灰系统【组成及说明】a.现场仪表、PLC、MCC、现场操作箱等b.实现连锁、智能控制,通过对燃料、空气、废气中的流量、温度、压力等进行调节。
(14)润滑系统【组成及说明】a.分集中润滑和单点润滑b.集中润滑:润滑站、润滑管、用户点;单点润滑:润滑枪、油嘴等四、套筒竖窑施工总需要注意的地方(部分)1、钢结构(1)窑壳的垂直度(同心度)、椭圆度、周长、上口水平度及标高;(2)窑底环板与窑壳的焊接顺序(3)内套筒下部支撑梁的水平度及标高(4)上下燃烧室与窑壳之间的连接(现场依照实物开孔),要保证等分角度,确保循环管与喷射器的对接。
(5)V3系统上口水平度(法兰盘),直接影响到旋转布料器的安装。
(6)通廊的桡度(≥24mm的必须起拱)(7)通廊支架的中心线控制,确保通廊和皮带机的安装。
(8)所有焊缝的质量(内部、感官)2、设备(1)上料小车四个小车轮的平滑性、稳定性、与导轨的接触是否良好?(2)卷扬机(4T)a.地脚螺栓的牢固性(抗拉性能)b.设备的制动性能是否良好?(3)旋转布料器a.导向轮的小牛腿(支撑柱)上表面标高、水平度b.旋转布料器料仓的垂直度c.导向轮与导向槽(法兰盘)的配合度d.液压马达的传动轮与销轴盘的啮合度e.料钟与旋转料仓下部密封面的接触性(4)上下内套筒及冷却空气扁平管a.上下内套的椭圆度b.上下内套筒的气密性c.上内套筒安装时的水平角度d.冷却空气扁平管中伸缩节(波纹管)的焊接(要求设备厂家将碳钢圈在厂内焊接好)(5)上下燃烧室及喷射器a.上下燃烧室面板要平整,面板与法兰的螺栓孔要匹配b.喷射器面板要平整,面板与法兰的螺栓孔要匹配(6)出灰装置a.七套出灰装置面板的平整度(7)液压管道a.管线布置要在便于检修的部位b.为了防止液压油泄露,联结头改为焊接接头。