Molding Process Introduce 注塑工艺介绍
注塑工艺流程英文简介

注塑工艺流程英文简介Injection Molding Process Flow.Injection molding is a manufacturing process for producing parts by injecting molten plastic material into a mold. It is commonly used for mass-producing plastic products such as toys, containers, and automotive parts. The process involves several key steps:1. Mold Design and Construction:The first step is to design and construct the mold. The mold consists of two halves (a cavity and a core) that come together to form the desired shape of the part. The cavity is the negative form of the part, while the core creates any internal features or holes. The mold is typically made of steel or aluminum and is designed to withstand the high pressures and temperatures involved in the injection molding process.2. Material Selection:The next step is to select the plastic material to be used. There are a wide variety of plastic materials available, each with its own unique properties and applications. Some of the most common plastic materials used in injection molding include polyethylene (PE), polypropylene (PP), polystyrene (PS), and acrylonitrile butadiene styrene (ABS).3. Material Preparation:Once the plastic material has been selected, it is prepared for injection molding. This involves drying the material to remove any moisture, which can cause defects in the molded part. The material is then typically pelletized or granulated into small, uniform particles.4. Injection Molding Machine:The injection molding machine is the equipment used to inject the molten plastic material into the mold. Themachine consists of a hopper, a heating chamber, aninjection unit, a mold clamping unit, and a cooling system.5. Injection Process:The injection process begins by feeding the plastic pellets into the hopper. The pellets are then heated in the heating chamber until they melt. The molten plastic is then injected into the mold cavity by the injection unit. The injection unit is a plunger or screw that forces the molten plastic into the mold under high pressure.6. Molding:Once the molten plastic has been injected into the mold, it is held under pressure until it cools and solidifies.The cooling time varies depending on the size andcomplexity of the part, as well as the type of plastic material used.7. Ejection:After the part has cooled and solidified, it is ejected from the mold. This is typically done using ejector pins or a knockout mechanism.8. Finishing:The ejected part may require additional finishing operations, such as trimming, sanding, or painting. These operations are typically performed to remove any imperfections or to improve the appearance of the part.Advantages of Injection Molding:High production rates and short cycle times.Ability to produce complex and intricate parts.Precision and dimensional accuracy.Wide range of material options.Cost-effective for mass production.Disadvantages of Injection Molding:High initial investment costs for mold design and construction.Limited to thermoplastic materials.Potential for defects and rejects.Environmental concerns related to plastic waste.。
注塑成型工艺流程及条件介绍外文文献翻译、中英文翻译、外文翻译
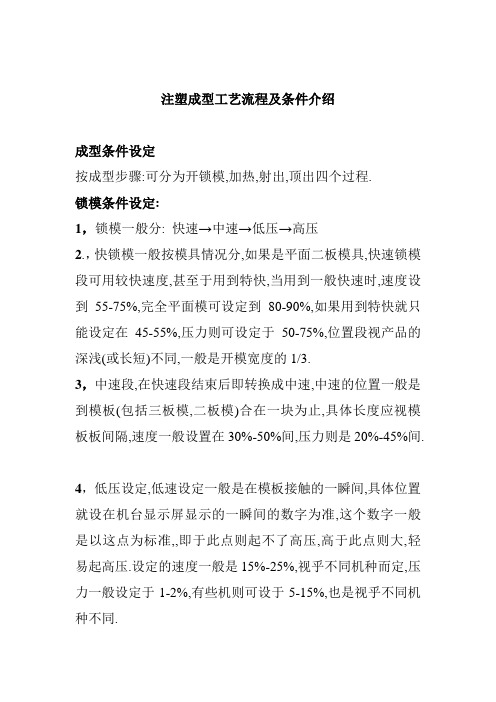
注塑成型工艺流程及条件介绍成型条件设定按成型步骤:可分为开锁模,加热,射出,顶出四个过程.锁模条件设定:1,锁模一般分: 快速→中速→低压→高压2.,快锁模一般按模具情况分,如果是平面二板模具,快速锁模段可用较快速度,甚至于用到特快,当用到一般快速时,速度设到55-75%,完全平面模可设定到80-90%,如果用到特快就只能设定在45-55%,压力则可设定于50-75%,位置段视产品的深浅(或长短)不同,一般是开模宽度的1/3.3,中速段,在快速段结束后即转换成中速,中速的位置一般是到模板(包括三板模,二板模)合在一块为止,具体长度应视模板板间隔,速度一般设置在30%-50%间,压力则是20%-45%间.4,低压设定,低速设定一般是在模板接触的一瞬间,具体位置就设在机台显示屏显示的一瞬间的数字为准,这个数字一般是以这点为标准,,即于此点则起不了高压,高于此点则大,轻易起高压.设定的速度一般是15%-25%,视乎不同机种而定,压力一般设定于1-2%,有些机则可设于5-15%,也是视乎不同机种不同.5.高压设定,按一般机台而言,高压位置机台在出厂时都已作了设定,相对来讲,是不可以随便更改的,比如震雄机在50P.速度相对低压略高,大约在30-35%左右,而压力则视乎模具而定,可在55-85%中取,比如完全平面之新模,模具排气良好,甚至于设在55%即可,如果是滑块较多,原来生产时毛边也较多,甚至于可设在90%还略显不足.加热工艺条件设定1.加热段温度设定必须按照产品所使用的原料的不同而不同,但却必须遵循一个这样的规则,即由射口筒到进科段温度是逐步递减的.且递减温度是以10.度为单位.2特殊情况下.如料头抽丝,则射口筒温度应降低,如果是比较特殊的原料冷凝比较快的.则射口筒温度则不止比第二节法兰温度高10度.比如PPS. 尼龙等.3.机台马达启动温度视乎机台不同而不同,一般出于对机台油路中的油封保护需要,油温最好能控制在40度-60度,以免油封长期高压而变化,缩短使用寿命,造成成型不稳定.注射是把塑料原料经加热后射进模腔的过程,它一般可分为第一级,第二级,第三级,第四级及保压几段:1 .第一级注射一般是注射料头段.具注射量一般可根据料头的轻重来估计其行程,当然也可以依据公式来计算,如公式L=Si=Vi/0.785Ds2:L:注射行程; Si: 注射行程;Vi:理论注射容积; Ds:螺杆直径;0.785:是Ω/4的值.当然,如果我们在成型时每设定一个参数都要计算一次,要成型出一个产品就要几个小时才能完成了.2. 第二级是注塑产品约2/3的阶段,当然,根据产品特殊需要,也允许成型不到2/3阶段,比如避免结合线问题,这一阶段的成型速度及压力一般是整个成型段的最大值段,如果排的产品与机台基本是相吻合的.模具结构合理,排气良好,这一段的压力一般也不会超过80%.速度侧视产品需变,可能大到95%也可,自然一般都是在55%-80%间.3. 第三段是注射余下的1/3段,其速度和压力根据产品的需要,一般是小于第二段,速度和压力存在于一个往下降的过程.主要是为了防止产品毛边的产生,但同时又必须把产品充填饱满.4.第四段:一般有机台还有第五,第六段,这段的成型速度和压力相同前,都存在两段一个递减过程.其作用都是起到一个再次充满的作用.5.保压段:不论成型什么产品,都存在一个保压过程.任何产品都不同程度的存在一个厚薄不一的问题,正常情况下,较厚的部分都可能存在一个收缩凹陷的现象,为了解决这种现象,就应应用到保压,保压一般来讲都应用较慢的射速,而压力的设置则应看缩水的情况如何,小到25%,大到80%都有可能.产品经冷却定型后则有一个开模的过程,开模基本上是合模的反过程.开模的未段则有一个慢速设置,开模完成后,产品必须顶出的过程.一.顶前:顶前最好分两个阶级,第一阶可分为中压慢速,即是把产品轻轻顶出一部分,然后是中压中速顶,中压中速一般指的是35%-55%,而低速则有可能低到5%,这需视产品不同而言,顶出行程设定是顶出长度稍比产品垂直深度大1-2cm即可. 二.退针顶退包括两个过程与顶落的过程基本一致,顶退的终点应预留1-3cm的空间,以保护顶针油管不被顶坏.三.顶针顶针方式还包括一个多次顶,单次顶及顶针停留的选择,机械手取产品,脱模顺利的情况都采取多项,为了顶针油缸寿命的延长,多次顶就以不超过三次为宜,顶针停留一般用在顶针带着产品退回有可能对增品产生损伤的模具,同时为配合机械手使用,有时也需要较短的顶针停留.Injection molding technical process and condition introductionSection Molding parameter Setting Molding steps: mold opening/closing, heating injection and knocking out.Mold closing parameter setting1.Mold closing: high-speed →low-speed →low pressure→high pressure2.In high-speed section, Mold closing speed depends on type of mold. For two –plate mold it can set quick and even especially quick usually, it set speed within 55-75%. For full-plate mold it set speed within80-90% while using especially high speed it set speed within 45-55% and pressure within 50-75% position distance setting differs depending on the volume of product and usually it can be set 1/3 of mold opening position.3.In mid-speed section: Mold closing speed changes into mid-speed after high-speed section finish. Mid-speed start position is where two plates meet (include three-plate mold and two-plate mold ) Distance of mid-speed is up to distance of two plates plate it speed within 30-50% and pressure 20-45%.4.Low-pressure section: Mold closing sets low-pressurewhen plates meeting. This position is set to the data of machine screen on this time. This point is the gage of the data. Data lower the point there is no high-pressure. Data higher the point there is high-pressure easily. It set speed within 15-25% and pressure within 1-2% depending on type within 1-2% depending on type of injection molding machine.5. High-pressure section: To normal injection molding machine, high-pressure position had been set before they were sent to customer. It can not be modified. For example high-pressure position of CHENHSONG machine is 50P.The speed of high-pressure section is about 30-35% and higher than that of low-pressure. The pressure is up to mold, it can set within 55-85% For full-plate mold, it’s eject air well, it can set pressure 55% .If mold has a lot of slides and flash rate high in production, pressure can set 90%.Heating technique parameter setting1.The proper temperature setting differs depending on type of resin material, but it must be abide by a rule that temperature setting should diminish in step 10.C from nozzle to feeding resin material position.2 Nozzle temperature setting should low if product line. If resin material such as PPS, PA, cool very soon , Nozzletemperature should higher more 10.C than the second cylinder temperature.3. Pump turning on temperature is different depending on type of injection molding machine. To protect oil seal of machine it set oil temperature within 40.C-60.C, If oil seal work on condition that high pressure and damaged It’s work time will be shorter, it can cause molding stable.Injection is a step which inject melt resin material into mold. It consists of stepl,step2 ,step3,step4 and holding pressure step:1. Step l injects usually tunnel material, Injection V olume can be estimated according to the weight of course it can be calculated by formula:L=Si=Vi/0.785Ds2L: injection stroke Si: injection strokeVi: injection volume of theoretical Ds: diameter of screw0. 785: value of Ω/4.But it cost a lot of time to produce one product if every time molding parameter is setting by calculation.2. Step 2 inject 2/3 of product. It can lower 2/3 of product according to requirement of product. For example to prevent weld line. Molding speed and pressure on this step is the maximum of whole molding section. If Mold suit the injectionmolding machine and mold structure reasonable and eject air well, pressure of this step should lower 80%. Molding speed setting within 55-80% but it may setting 95% for especial product.3. Step3 inject remain 1/3 of product. According to product molding speed and pressure lower than that of step2 To prevent flash speed and pressure should decrease but it can’t shot short. Step4 section: Some injection machines have step5,step6 which are same as former molding speed and pressure this step should diminish and inject once more.5. Holding pressure step: No matter what product there is a holding pressure step. Any product can’t molding a same thickness. Usually the deeper section may sink mark . To prevent this defect it should set holding pressure, The injection speed of holding pressure step is slow but holding pressure setting within 25-80% depending on sink mark.There is a mold opening step after product cooling taking shape. Mold opening is a reverse step of mold closing. The last step of mold opening speed set slow. Product should be knocked out after mold opened.one.Knocking outKnocking out includes two steps, Step1 section setting mid-speed, knocks product out partly step2 section setting mid-pressure and mid-speed . Depending on different product, mid-pressure and mid-speed sets within 35-55% but low-speed can set 5%. Distance of knocking out longer 1-2cm than the vertical thickness of product.two.BackThe same as knocking out, ejector back includes 2 steps. To protect the ejector oil jar, it should make a 1-3mm distance in the ending point of ejector back.Three. ThimbleThe way of knocking out includes knocking out once, Knocking out repeat and ejector delay. Take product by manipulator or take product easy, it should select knocking out once. To longer the work time of ejector oiljar, times of knocking out lower 3 times. Ejector delay used when product will be damaged if ejector back or suit manipulator.。
注塑工艺流程介绍
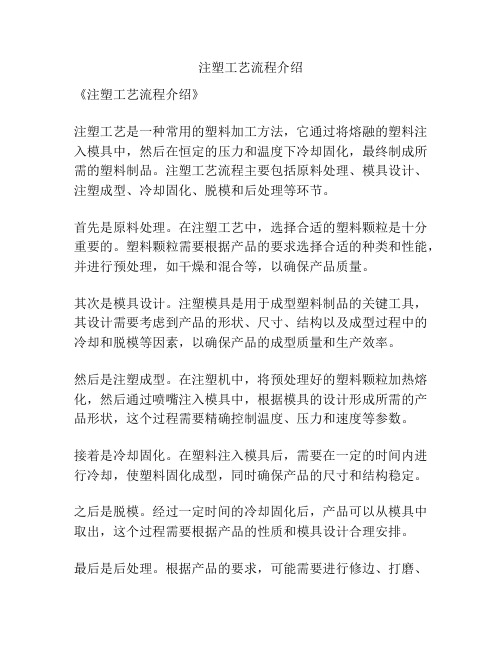
注塑工艺流程介绍
《注塑工艺流程介绍》
注塑工艺是一种常用的塑料加工方法,它通过将熔融的塑料注入模具中,然后在恒定的压力和温度下冷却固化,最终制成所需的塑料制品。
注塑工艺流程主要包括原料处理、模具设计、注塑成型、冷却固化、脱模和后处理等环节。
首先是原料处理。
在注塑工艺中,选择合适的塑料颗粒是十分重要的。
塑料颗粒需要根据产品的要求选择合适的种类和性能,并进行预处理,如干燥和混合等,以确保产品质量。
其次是模具设计。
注塑模具是用于成型塑料制品的关键工具,其设计需要考虑到产品的形状、尺寸、结构以及成型过程中的冷却和脱模等因素,以确保产品的成型质量和生产效率。
然后是注塑成型。
在注塑机中,将预处理好的塑料颗粒加热熔化,然后通过喷嘴注入模具中,根据模具的设计形成所需的产品形状,这个过程需要精确控制温度、压力和速度等参数。
接着是冷却固化。
在塑料注入模具后,需要在一定的时间内进行冷却,使塑料固化成型,同时确保产品的尺寸和结构稳定。
之后是脱模。
经过一定时间的冷却固化后,产品可以从模具中取出,这个过程需要根据产品的性质和模具设计合理安排。
最后是后处理。
根据产品的要求,可能需要进行修边、打磨、
组装或者其它特殊加工,使产品最终符合客户需求。
总的来说,注塑工艺流程是一个复杂的系统工程,需要各个环节精心设计和合理安排,以确保产品质量和生产效率。
通过不断的技术创新和工艺改进,注塑工艺在各个领域有着广泛的应用和发展前景。
Molding Process Introduce 注塑工艺介绍.ppt

Gas Assist Injection
Molded Shipping Container
24
Process Selection - Injection
Heat & Cool System
Mold Temperature
Vicat Softening point
plasticization open
high performance, tight tolerance parts with very little
4
secondary labor and minimal waste.
Pacific ADS Design Training November 2003
Process Selection - Injection
Injection Unit The Reciprocating Screw
Ready for Injection
9
Pacific ADS Design Training November 2003
Process Selection - Injection
Injection Unit The Reciprocating Screw
Process Selection - Injection
Gas Assist Injection Molding
Gas Introduced After Short Shot to Pack out Part
Advantages
Disadvantages
• Improved Aesthetics • Defect on Every Part
Mucell微孔发泡工艺的塑化单元
01
注塑模加工工艺流程

注塑模加工工艺流程英文回答:Injection molding is a widely used manufacturing process for producing plastic parts. It involves the use of an injection molding machine, which consists of a hopper, a heating unit, a mold, and an injection unit. The process begins with the melting of plastic pellets or granules in the heating unit. Once the plastic is melted, it isinjected into the mold cavity through a nozzle using high pressure. The plastic then cools and solidifies inside the mold, taking the shape of the desired part. Finally, the mold is opened and the finished part is ejected.The injection molding process can be divided into several stages. First, the mold is prepared by cleaning and lubricating it to ensure smooth operation. Next, theplastic material is loaded into the hopper, where it is fed into the heating unit. The plastic is heated to its melting point, which varies depending on the type of plastic beingused.Once the plastic is melted, it is injected into themold cavity under high pressure. The injection unitconsists of a screw or a plunger that pushes the melted plastic into the mold. The high pressure ensures that the plastic fills the entire cavity and creates a uniform part.After the plastic is injected into the mold, it beginsto cool and solidify. Cooling can be facilitated by the use of cooling channels within the mold or by external cooling methods. The cooling time depends on the thickness and complexity of the part, as well as the type of plasticbeing used. Once the plastic has solidified, the mold is opened and the finished part is ejected. The mold can then be closed again to start the next cycle.Injection molding offers several advantages over other manufacturing processes. It allows for the production of complex and intricate parts with high precision and repeatability. It also enables the use of a wide range of materials, including thermoplastics, thermosetting plastics,and elastomers. Additionally, injection molding is a highly efficient process, with minimal material waste and short cycle times.中文回答:注塑模加工是一种广泛应用于生产塑料零件的制造工艺。
Molding Process Introduction

R&D Internal Training
15
Eject Procedure
Mold Temperature 175degC
Tablet Preheat
-16 0 Transfer position
Clamp Force 30ton
Tablet Load Position
R&D Internal Training
To join ST/LF, chip and gold wire and form a IC package.
R&D Internal Training
2
塑封机器(Auto-molding System)
TOWA Y-Series
ASA Omega Series
R&D Internal Training
10
模具
下模(Bottom Chase)
Bottom Cavity Bar Bottom Cull Block Bottom Alignment Block Pot Plunger Location Pin Eject Pin Resin Stop Block
R&D Internal Training
R&D Internal Training
8
下料
Unloader/Cleaner 把塑封后的料从模具中取出送到Carrier Plate, 同时清洁模具表面。
Carrier Plate 塑封后的料运送至Gate Break处。 Gate Break(Degate) 吹风冷却,去处残胶(Cull)。 Pick&Place&Output Magazine 把料从Carrier上夹起,放入Staker Magazine。
注塑工艺介绍

注塑工艺介绍
注塑工艺是一种可以将塑料以液体熔体的形式注入到金属模具
之中,并在模具内凝固并成型的工艺。
这种工艺的核心是能够将原材料熔化和加工成特定形状的装置,并能够提供高精度的成型性能。
注塑工艺的应用范围极为广泛,从汽车、航空航天、仪器仪表、重工业到家用电器制造都有广泛的应用。
注塑工艺有几种不同的形式,其中最常见的有压力式注塑工艺、真空式注塑工艺和挤出式注塑工艺。
压力式注塑工艺在技术上要求最高,其特点是熔融塑料由压力泵维持在凝固模具内的一定压力,充分利用模具中的渗流和内部排气,使注塑部件完全按照设计图样结构和尺寸成型。
真空式注塑工艺是一种利用真空吸引熔融的塑料的技术,其特点是可以做出薄壁、复杂部件的塑件,多用于制造汽车零部件、塑料零件等内部腔体精密的部件。
最后,挤出式注塑工艺是通过滚筒式挤出压力机将熔融的塑料挤出来,形成管材和型材的工艺,大多用于制造管材和型材等。
注塑工艺很多时候与其他工艺联用,以获得更完美的产品质量。
比如,通过添加另一种加工工艺,如喷射塑料成型,可以使注塑工艺产品的表面更光滑、外形更美观。
另外,熔体注压工艺也可以很好地和加工技术配合,以提高产品的性能。
此外,注塑工艺也可以通过不同的材料结合而成,增加产品质量。
比如,通过熔体注塑工艺,可以将不同的材料注入到模具内,然后在高温环境下进行成型,从而使具有不同塑料性能的零件结合在一起,
为产品提供更为完美的外观和性能。
总之,注塑工艺在现代制造业中发挥着越来越重要的作用,能够制造出精度高、外形美观的零部件。
伴随着许多新材料和新技术的开发,注塑工艺的应用范围可能会进一步扩大,以满足制造业的需要。
注塑工艺流程 英文
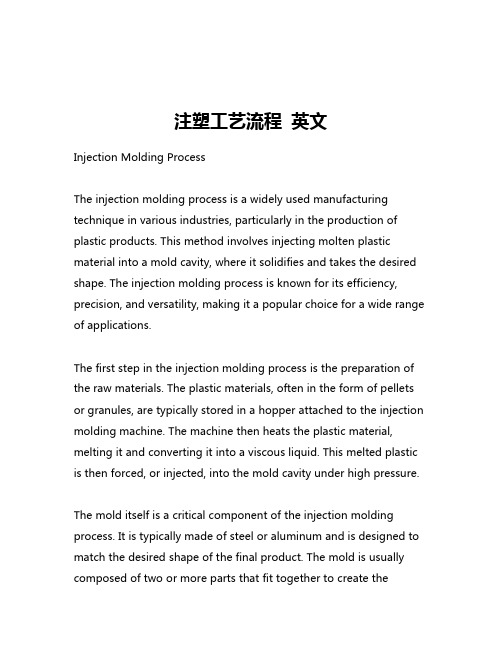
注塑工艺流程英文Injection Molding ProcessThe injection molding process is a widely used manufacturing technique in various industries, particularly in the production of plastic products. This method involves injecting molten plastic material into a mold cavity, where it solidifies and takes the desired shape. The injection molding process is known for its efficiency, precision, and versatility, making it a popular choice for a wide range of applications.The first step in the injection molding process is the preparation of the raw materials. The plastic materials, often in the form of pellets or granules, are typically stored in a hopper attached to the injection molding machine. The machine then heats the plastic material, melting it and converting it into a viscous liquid. This melted plastic is then forced, or injected, into the mold cavity under high pressure.The mold itself is a critical component of the injection molding process. It is typically made of steel or aluminum and is designed to match the desired shape of the final product. The mold is usually composed of two or more parts that fit together to create thedesired form. When the molten plastic is injected into the mold, it fills the cavity and takes on the shape of the mold.After the plastic has been injected into the mold, it is allowed to cool and solidify. This cooling process is essential to ensure that the plastic takes on the desired shape and structural integrity. The time required for cooling can vary depending on the size and complexity of the part, as well as the specific plastic material being used.Once the part has solidified, the mold is opened, and the finished product is ejected. This ejection process is often automated, with the use of ejector pins or other mechanical mechanisms to remove the part from the mold. The finished part may then undergo additional processing, such as trimming, finishing, or assembly, depending on the specific product requirements.One of the key advantages of the injection molding process is its ability to produce high-quality parts with a high degree of consistency and precision. The use of computer-controlled machinery and advanced mold design techniques allows for the creation of complex and intricate parts with tight tolerances. This consistency and precision are particularly important in industries where the quality and reliability of the final product are critical, such as in the automotive, medical, and electronics sectors.Another advantage of the injection molding process is its versatility. The process can be used to produce a wide range of plastic products, from simple household items to highly specialized industrial components. The choice of plastic material, mold design, and processing parameters can be tailored to meet the specific requirements of the application, making injection molding a highly flexible manufacturing method.In addition to its technical advantages, the injection molding process is also known for its efficiency and cost-effectiveness. The automated nature of the process, combined with the ability to produce large quantities of parts in a relatively short amount of time, makes it a highly efficient manufacturing method. This efficiency can translate into lower production costs, making injection-molded products more affordable for consumers and businesses alike.Despite its many advantages, the injection molding process is not without its challenges. One of the key challenges is the need to carefully control the processing parameters, such as temperature, pressure, and injection speed, to ensure the production of high-quality parts. Improper control of these parameters can lead to a variety of defects, such as warping, shrinkage, or flash, which can negatively impact the final product.Another challenge is the need for specialized equipment and tooling,which can represent a significant upfront investment for manufacturers. The design and fabrication of high-quality molds, in particular, can be a complex and costly process, requiring the expertise of skilled engineers and technicians.Despite these challenges, the injection molding process remains a highly valuable and widely used manufacturing technique. As technology continues to advance, it is likely that the process will become even more efficient, versatile, and cost-effective, further solidifying its position as a cornerstone of the modern manufacturing landscape.In conclusion, the injection molding process is a crucial component of the modern manufacturing industry. Its ability to produce high-quality, consistent parts at a relatively low cost has made it a popular choice for a wide range of applications. As the demand for plastic products continues to grow, the injection molding process will undoubtedly remain a vital and innovative manufacturing method for years to come.。
- 1、下载文档前请自行甄别文档内容的完整性,平台不提供额外的编辑、内容补充、找答案等附加服务。
- 2、"仅部分预览"的文档,不可在线预览部分如存在完整性等问题,可反馈申请退款(可完整预览的文档不适用该条件!)。
- 3、如文档侵犯您的权益,请联系客服反馈,我们会尽快为您处理(人工客服工作时间:9:00-18:30)。
Mold Temperature Vicat Softening point plasticization temperature rise plasticization
Process
Valve unit hot water hot water cold water cold water hot water
Advantages Improved Aesthetics Low Pressure Process Lower Part Weight Reduced CycleDefect on Every Part More Complex Process High Tooling Costs 23 Licensing Costs
Process Selection - Injection
Injection Unit The Reciprocating Screw
Ready for Injection
9
Pacific ADS Design Training November 2003
Process Selection - Injection
Pacific ADS Design Training November 2003
12
Process Selection - Injection
Standard Injection Molding
Advantages
•Fast Cycle Times •Complex Parts •High Volume •Aesthetics
Pacific ADS Design Training November 2003
Disadvantages • High Pressure Process • Limited Large Part Capability • High Tooling Cost
13
Co- Injection Molding
Disadvantages • Longer Cycle Time • Aesthetics • Blending Required
21
Process Selection - Injection
Structural Foam
SKIN CORE SKIN
• Increases the attainable wall thickness • Gas expands inside plasticized material to create foam core
22
Pacific ADS Design Training November 2003
Process Selection - Injection
Gas Assist Injection Molding
Gas Introduced After Short Shot to Pack out Part
• • • •
Injection Unit The Reciprocating Screw
Heating Coils (Filling) Throat
Rotation Injection Force Back Pressure
Nozzle
Screw Pushes Forward: Inject
Screw Slides Back: Feed, Melt
19
Mucell微孔发泡的产品表现形式
20
Pacific ADS Design Training November 2003
Process Selection - Injection
Structural Foam Injection Molding
Inert Gas Blowing Agent with Resin
2
Pacific ADS Design Training November 2003
Process Selection - Injection
Processing of Engineering Thermoplastics:
Materials Processing Processing
•Injection Molding •Extrusion •Compression Molding •Thermoforming •Blow Molding •Secondary Operations •Comparisons
Mucell微孔发泡工艺的塑化单元
01 04 02 03 05
01 Needle valve nozzle 02 Gas injector 03 MuCell®-plasticizing screw (L/D ratio: 22:1~24:1) 04 Homogenizing section for gas/melt mixture 05 Plastics granules without blowing agent Pacific ADS Design Training November 2003
Process Selection - Injection
Injection Unit The Reciprocating Screw
Pellets
Melt
Feed Section
6
Pacific ADS Design Training November 2003
Process Selection - Injection
Metering
Compression
Feed
Feed Section: Picks up pellets and carries them forward.
Transition Section: central portion of the screw with reduced channel depth which compresses plastic, eliminating air between pellets and heating and melting them. Metering Section: Final plasticizing of melt.
26
Need special equipment
Pacific ADS Design Training November 2003
LEXAN FOAMABLE RESIN Business Machine Chassis
High Strength and Rigidity in Larger Parts
17
Pacific ADS Design Training November 2003
Mucell微孔发泡设备
18
Pacific ADS Design Training November 2003
3
Pacific ADS Design Training November 2003
Process Selection - Injection
Injection Molding Introduction
Injection molding makes possible mass production of intricate, high performance, tight tolerance parts with very little secondary labor and minimal waste.
Pacific ADS Design Training November 2003
4
Process Selection - Injection
Injection Molding Machine
Mold
Hopper
Clamp
Extruder Barrel with Heating Bands
5
Pacific ADS Design Training November 2003
Co- Injection Molding
Co- Injection Molding
16
Pacific ADS Design Training November 2003
Four Component
Process Selection - Injection
Structural Foam Part
open
25
Pacific ADS Design Training November 2003
Process Selection - Injection
Heat & Cool Equipments
Part
Cooling Water
T2
T1
T3
Boiler
: Channel
Valve Unit
Cooling Channel
Co- Injection Molding
Two - Component
Pacific ADS Design Training November 2003
14
Co- Injection Molding
Co- Injection Molding
15
Three Component
Pacific ADS Design Training November 2003
11
Pacific ADS Design Training November 2003
Process Selection - Injection
Clamping System
Nozzle
Movable Platen
Mold
Stationary Platen
• Provides motion and force to open and close mold • Clamping Force: maximum holding force in tons that a machine can maintain