Ansys在复合材料结构优化设计中的应用_图文(精)
UG和ANSYS软件在结构分析及优化设计中的应用
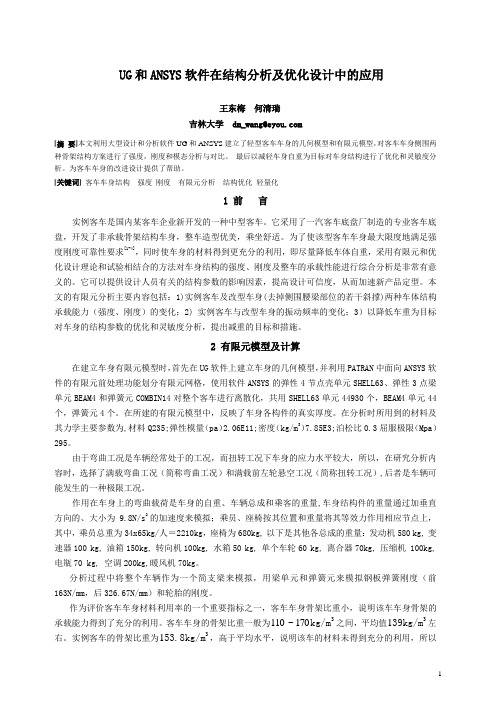
UG 和ANSYS 软件在结构分析及优化设计中的应用王东梅 何清瑞吉林大学 dm_wang@[摘 要]本文利用大型设计和分析软件UG 和ANSYS 建立了轻型客车车身的几何模型和有限元模型,对客车车身侧围两种骨架结构方案进行了强度,刚度和模态分析与对比。
最后以减轻车身自重为目标对车身结构进行了优化和灵敏度分析。
为客车车身的改进设计提供了帮助。
[关键词] 客车车身结构 强度 刚度 有限元分析 结构优化 轻量化1 前 言实例客车是国内某客车企业新开发的一种中型客车。
它采用了一汽客车底盘厂制造的专业客车底盘,开发了非承载骨架结构车身,整车造型优美,乘坐舒适。
为了使该型客车车身最大限度地满足强度刚度可靠性要求[1-4],同时使车身的材料得到更充分的利用,即尽量降低车体自重,采用有限元和优化设计理论和试验相结合的方法对车身结构的强度、刚度及整车的承载性能进行综合分析是非常有意义的。
它可以提供设计人员有关的结构参数的影响因素,提高设计可信度,从而加速新产品定型。
本文的有限元分析主要内容包括:1)实例客车及改型车身(去掉侧围腰梁部位的若干斜撑)两种车体结构承载能力(强度、刚度)的变化;2) 实例客车与改型车身的振动频率的变化;3)以降低车重为目标对车身的结构参数的优化和灵敏度分析,提出减重的目标和措施。
2 有限元模型及计算在建立车身有限元模型时,首先在UG 软件上建立车身的几何模型,并利用PATRAN 中面向ANSYS 软件的有限元前处理功能划分有限元网格,使用软件ANSYS 的弹性4节点壳单元SHELL63、弹性3点梁单元BEAM4和弹簧元COMBIN14对整个客车进行离散化,共用SHELL63单元44930个,BEAM4单元44个,弹簧元4个。
在所建的有限元模型中,反映了车身各构件的真实厚度。
在分析时所用到的材料及其力学主要参数为,材料Q235;弹性模量(pa )2.06E11;密度(kg/m 3)7.85E3;泊松比0.3屈服极限(Mpa )295。
Ansys复合材料结构分析总结
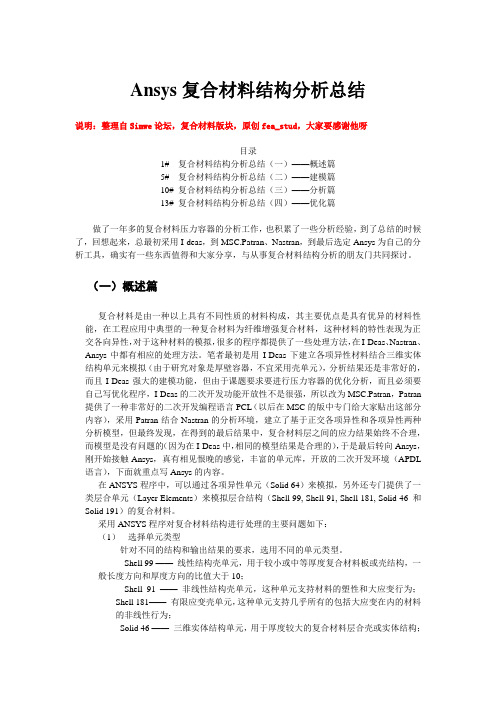
Ansys复合材料结构分析总结说明:整理自Simwe论坛,复合材料版块,原创fea_stud,大家要感谢他呀目录1# 复合材料结构分析总结(一)——概述篇5# 复合材料结构分析总结(二)——建模篇10# 复合材料结构分析总结(三)——分析篇13# 复合材料结构分析总结(四)——优化篇做了一年多的复合材料压力容器的分析工作,也积累了一些分析经验,到了总结的时候了,回想起来,总最初采用I-deas,到MSC.Patran、Nastran,到最后选定Ansys为自己的分析工具,确实有一些东西值得和大家分享,与从事复合材料结构分析的朋友门共同探讨。
(一)概述篇复合材料是由一种以上具有不同性质的材料构成,其主要优点是具有优异的材料性能,在工程应用中典型的一种复合材料为纤维增强复合材料,这种材料的特性表现为正交各向异性,对于这种材料的模拟,很多的程序都提供了一些处理方法,在I-Deas、Nastran、Ansys中都有相应的处理方法。
笔者最初是用I-Deas下建立各项异性材料结合三维实体结构单元来模拟(由于研究对象是厚壁容器,不宜采用壳单元),分析结果还是非常好的,而且I-Deas强大的建模功能,但由于课题要求要进行压力容器的优化分析,而且必须要自己写优化程序,I-Deas的二次开发功能开放性不是很强,所以改为MSC.Patran,Patran 提供了一种非常好的二次开发编程语言PCL(以后在MSC的版中专门给大家贴出这部分内容),采用Patran结合Nastran的分析环境,建立了基于正交各项异性和各项异性两种分析模型,但最终发现,在得到的最后结果中,复合材料层之间的应力结果始终不合理,而模型是没有问题的(因为在I-Deas中,相同的模型结果是合理的),于是最后转向Ansys,刚开始接触Ansys,真有相见恨晚的感觉,丰富的单元库,开放的二次开发环境(APDL 语言),下面就重点写Ansys的内容。
在ANSYS程序中,可以通过各项异性单元(Solid 64)来模拟,另外还专门提供了一类层合单元(Layer Elements)来模拟层合结构(Shell 99, Shell 91, Shell 181, Solid 46 和Solid 191)的复合材料。
ansys实例应用实验报告

结构线性静力分析一、问题描述分析如下图所示具有圆孔的矩形板在拉伸状态下的应力分布。
1.0 m×2.0 m的矩形板,厚度为0.03 m,中心圆孔直径为0.25 m,弹性模量为207GPa,泊松比0.3,端部受拉伸载荷600 N。
二、有限元分析步骤1)选用solid45单元。
2)定义材料系数。
弹性模量为207e9Pa,泊松比为0.3。
3)建立模型。
Modeling>create>volumes>block>by dimensions。
X1,x2;y1,y2;z1,z2分别取-1,1;-0.5,0.5;0,0.03,得到矩形板。
创建圆柱体:Modeling>create>volumes>cylinder>by dimensions,半径为0.125m,深度为0.03m。
进行布尔操作:Modeling>operate>booleans>subtruct>volumes,选择矩形板,点击apply,选择圆柱体,点击ok。
4)划分网格。
选择Utility Menu>WorkPlane>Display Working Plane,然后选择Utility>WorkPlane>Offset WP by Increments,在Offset WP对话框的Degrees框中输入:0,-90,0然后点击OK确定。
Modeling>Operate>Booleans>Divide>Volu byWrkPlane,选择Pick All,图形窗口中将显示模型被工作平面一分为二。
类似地,通过移动工作平面的位置,最后将几何模型剖分。
选择Modeling>Operate>Booleans> Glue>Volumes,在对话框中选择Pick All,将剖分开的各部分模型粘接在一起。
选择Size control>Lines>set,将圆孔周边的线段和中线小正方型的线段都设定为10段,厚度方向的线段设定为6段,然后选择Mesh处下拉菜单为volume,shape设定为sweep,点击sweep,然后点击select all,然后点击OK确定。
ANSYS在结构优化设计中的应用
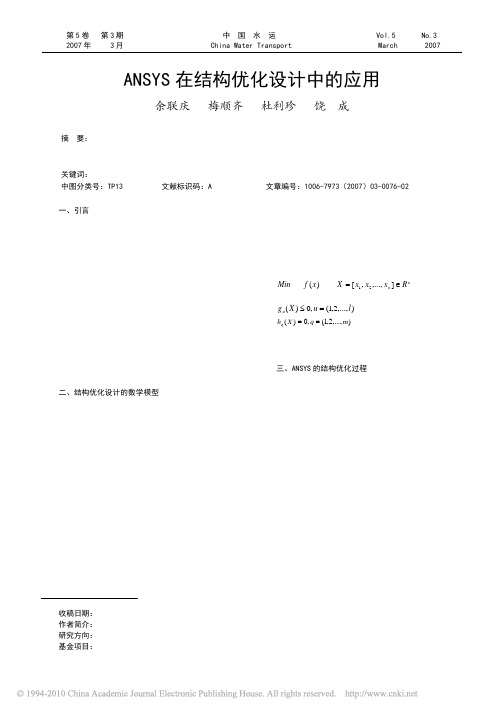
第5卷 第3期 中 国 水 运 Vol.5 No.3 2007年 3月 China Water Transport March 2007收稿日期:2007-3-15作者简介:余联庆 男(1972-) 武汉科技学院工业工程系 讲师 (430074) 研究方向:机械动力学、机械系统仿真技术基金项目:本文获湖北省教育厅教学研究项目“机械类计算机仿真技术课程体系与实践研究(20050326)”ANSYS 在结构优化设计中的应用余联庆 梅顺齐 杜利珍 饶 成摘 要:由于优化设计的基础理论涉及面较广,对设计人员的数学能力要求较高。
为了帮助设计人员更好地理解抽象的优化理论,提高其实际动手能力,本文介绍了如何利用有限元分析软件进行结构优化设计,建立了基于ANSYS 的结构优化设计流程图。
最后通过一个工程实例加以说明。
关键词:优化设计 ANSYS 有限元分析中图分类号:TP13 文献标识码:A 文章编号:1006-7973(2007)03-0076-02一、引言优化设计是在数学规划的基础上发展起来的一门交叉学科,随着电子计算机的引入,它已迅速发展成为一种有效的新型工程设计方法。
机械结构设计应用优化设计方法较传统的设计方法一般可节省材料7~40%,并可获得最佳的结构尺寸。
近年来,基因(遗传)算法、猴王算法及模拟退火算法等新型算法又相继引入优化设计领域,扩大了优化设计的基础理论涉及面,对学生的数学基础要求也越来越高。
当设计人员在面对这些种类繁多而且抽象的优化理论时,普遍出现困难情绪。
在优化设计中引入计算机和成熟的商品软件,使结构优化设计的求解程序化、可视化,激发设计人员的求解兴趣,使得传统的优化设计增添了新的活力。
本文介绍了有限元分析软件ANSYS 在结构优化设计中的应用,使概念更具体化和形象化,提高了设计人员分析问题的基本技能和计算机操作与软件应用的能力。
二、结构优化设计的数学模型一般说来,优化设计方法不仅要求设计人员要了解所求解问题的工程背景,将设计问题转化为某种优化模型,而且还要懂得利用一门计算机编程语言来实现某种算法,这样他才能够完成优化设计。
Ansys复合材料结构分析操作指导书---副本

第四章复合材料计算实例在有了前几章知识做铺垫,这一章我们来学习两个复合材料分析的例子,加深复合材料分析的理解,也希望读者能从中收获一些经验。
在这里将第二章的流程图再次拿出来,进一步熟悉ANSYS有限元分析的基本过程。
图7 Ansys 结构分析流程图4.1 层合板受压分析4.1.1 问题描述层合板指的是仅仅由FRP层叠而成的复合板材,中间不包含芯材,板材的性能不仅与纤维的弹性模量、剪切模量有关,还与纤维的铺层方向有着密切关系。
本例中的板材有4层厚度为0.025m的单元板复合而成,单元板的铺层方向为0°、90°、90°、0°,见图13所示。
单元板的材料属性见表4.1。
表 4.1 单元板材料属性EX/MP EY/MP EZ/MP GXY/MP GYZ/MP GXZ/MP PRXY PRYZ PRXZ12.5 300 300 50 20 50 0.25 0.25 0.01图13 复合材料板4.1.2 求解步骤根据问题描述,所要分析的问题为壳体结构的复合材料板,可以采用SOLID46单元建立3D有限元模型进行分析。
结合图7的一般步骤进行分析。
步骤一:选取单元类型,设置单元实常数⑴、在开始一个新分析前,需要指定文件保存路径和文件名。
文件保存路径GUI:【Utility Menu】|【File】|【Change Directory】见图14指定新的文件名GUI:【Utility Menu】|【File】|【Change Jobname】见图15所示图14 指定文件保存路径图15 修改文件名⑵、选取单元类型1)选取单元类型的GUI操作:【Main Menu】|【Preprocessor】|【Element Type】|【Add/Edit/Delete】,执行后弹出Element Types对话框。
2)在Element Types对话框点击Add定义新的单元类型,弹出“Library of Element Types”对话框,见图16所示,按图中所示选择,单元类型参考号输入框中输入数字1。
基于SolidWorks和ANSYS的复合支撑梁的优化设计

基于SolidWorks和ANSYS的复合支撑梁的优化设计摘要:铰链和支撑座相结合的复合支撑梁的结构,通常应用于大型钢结构平台中,传统的设计方法比较复杂。
借助SolidWorks软件方便快捷的三维建模能力和ANSYS软件强大的力学分析能力,并利用两种软件通用的数据交换格式,将两种软件结合使用,充分发挥各自软件的优势,大大提高了工程设计的工作效率和精度。
关键词:SolidWorks;ANSYS;复合支撑梁;优化设计引言ANSYS是一款以结构矩阵分析有限单元法(Finite Element Method)为理论基础的有限元分析软件,可应用于求解各种数学、物理问题。
如热传导、流体力学、电磁场以及结构力学等。
由于ANSYS具有度高、适应性强以及计算格式规范统一等优点,因此成为现代机械产品设计中的一种重要CAE工具。
SolidWorks软件是世界上第一个基于Windows 开发的三维CAD系统,目前广泛应用于机械设计制造业。
将CAE和CAD两种软件相结合使用,可充分发挥各自软件的优势,大大提高工程设计的工作效率和精度。
铰链和支撑座相结合的复合支撑梁的结构,通常应用于大型钢结构平台中,由于受力形式相对复杂,普通的分析设计手段不能满足其要求。
本文作者通过应用CAD/CAE技术,优化了符合支撑梁的结构,改善了符合支撑梁的目前较传统的设计状况。
1 设计流程本文作者结合SolidWorks和ANSYS两种软件的各自优势,形成了以下设计思路,具体流程[1]如下(图1所示):2 模型建立通常单独使用ANSYS软件建立复杂模型比较困难,而使用SolidWorks软件建模则简单很多。
SolidWorks为达索系统(Dassault Systemes S.A)下的子公司,专门负责研发与销售机械设计软件的视窗产品,该软件提供了当今市场上几乎所有CAD/CAE软件的输入/输出格式转换器,可进行不同文件格式的转换。
所以在使用SolidWork建模后,可方便的将模型文件转换成能被ANSYS软件识别使用的文件格式。
Ansys的复合材料分析
© 2005 ANSYS, Inc.
8
ANSYS, Inc. Proprietary
SHELL99 Linear Layered Structural Shell Element
• Element Definition
– 8node, 3D shell element with six degrees of freedom at each node – Thin to moderately thick plate and shell structures with a sideto thickness ratio of roughly 10 or greater
© 2005 ANSYS, Inc.
rietary
Benefits of Composites
• Stronger and stiffer than metals on a density basis • Capable of high continuous operating temperatures • Highly corrosion resistant • Electrically insulating/conducting/selectively conducting properties • Tailorable thermal expansion properties • Exceptional formability • Outstanding durability
基于ANSYS Workbench碳纤维复合材料综框的铺层分析与优化设计
o f t h e He al d Fr ame o f Car b o n Fi b er Co mp o s i t e
H AN Bi n b i n , W ANG Yi x u a n , REN S h u a n g n i n g , ZHA NG Qi u x i a
【8 1 ・1 4 0・
Tex t i l e
织器 。 Ac c e s s o r i e s
V O I . 4 4 N O 3
Ma y 201 7
基于 A NS Y S Wo r k b e n c h碳 纤 维 复 合 材 料 综 框 的 铺 层 分 析 与 优 化 设 计
a n d t he pe r f o r ma nc e wi t h a l u mi n i u m a l l o y h e a l d f r a me . I t i S p oi nt e d ou t t ha t t he he a l d f r a me
( 1 . Th e R& D Ce n t e r Be i j i n g Xi n g h a n g Me c h t r o n i c a l Eq u i p me n t Co . , Lt d . , Be i j i n g 1 0 0 0 7 4, Ch i n a ;
动 态特性 的影响 , 并进行 不 同参数 组合优化 , 可确定综框 结构的最佳参数 。
ANSYS软件在复合材料专业技能竞赛中的应用
行分析 、对应力的传递和承 载受 力破坏过程进行计算 机模拟 ,可 以获 竞赛规则要求 桥梁载荷 满足载荷 为 8kN的前 提下 ,按 照质量 的增加
得难以用传统设计获得 的一系列数据 ,且可以通过适 当的验证方 法来 排列名 次 ,质量越轻 的作 品获胜 。因此 ,采用 目标 函数最优设计方案进
水利 、日用家 电等领域有着广泛 的应用 。ANSYS功能强大 ,操作 简单 设计变量 的改变而有所改变 )的值最小。也就是说 ,在满足所有设计要
方便 ,现在 已成 为 目前应用最广的有限元分析软件之一 。
求的前提下 ,所需的方案最小 (如质 量 、面积 、体积 、应力 、费用 等 ),即
ANSYS有 限元分析软 件能够对 复合材料结 构进行优化 、性能进 目标函数值最/]'-,I3I。如第六届超轻复合材料桥梁竞赛中碳纤维桥梁组
与传统材料相比 ,复合材料 的可设计性主要体现在结构的设计和
材料 的设计 ,复合材料结构的多层次性为复合材料及其结构设计带来
了极大 的灵活性 ,复合材料的力学性能 和机械性能 ,都可按 照结构的
使用要求 和环 境条件要求 ,通过组分材料 的选 择匹配 、铺层设 计及界 面控制 等材料设计 手段 ,最大限度 的达 到预期 目的 ,以满 足工程设备
运算 和塑(弹)性理论 ,且只有少数简单结构才能得 出准确的结论。 轻 复合材料桥梁竞赛提供有一条非常有效 的途径 。
ANSYS软件 是美 国 ANSYS公 司研制 的 大型 通 用有 限元 分析
ANSYS有 限 元分 析 软 件 强 大 的优 化 设 计 主 要 体 现 在 “目标 函 数 最
通 常 ,复合材料结构的受力及应力应 变情况非常 复杂 ,并 要考虑 规 则是 :作 品按照载荷/重量 比值排名 ,即载荷,重 量的 比值 最大 者获 各种应力应变的耦合和相互影响。而传统复合材料的设计 主要采用等 胜 ,桥梁最大重量为 750克。
基于Matlab和Ansys的复合材料板的结构分析
基于Matlab 和Ansys 的复合材料板的分析本文通过使用MATLAB 和ansys 这两款软件对假设的复合材料层积板进行结构分析,对该材料同一点施加相同的力之后,观察比对其余相同节点的位移及和扭转角。
假定的复合材料分析的模型问题阐述:假设一个对称的、尺寸为4.04.0⨯的方形积层板,使用SI 单位的碳纤维(Gr70%-Epoxy30%)为复材,铺层角为︒45,共有4层,每层厚度为1mm 。
在底端约束固定,于顶端中央的节点上施加一个Z 方向(垂直于复合材料板平面的方向为Z 方向)的集中力N F z 100=,是对其进行静力分析。
基于MATLAB 的复合材料层合板的分析 复合材料板的刚度矩阵称为层积板。
常见的层积板是以正交材料堆叠而成。
层积板中各层的正交材料有,又是以高强度线状材料与基底材料压制而成。
在复合材料力学中,我们可以列出弹性剪切模量G 、泊松比ν、杨氏模量E 的关系方程式。
二维正交材料,各应变的关系式为:)(2121111σνσε-E = (1))(2121221σσνε+-E = (2)1212121τγG =(3) 若定义: {}}{T 1221γεεε= (4){}}{T 1221τσσσ= (5)则上式可写成:{}[]{}σεS = (6)其中[]⎥⎥⎥⎥⎥⎥⎥⎦⎤⎢⎢⎢⎢⎢⎢⎢⎣⎡--=12222111211000101G E E E E S νν (7) 现在假设刚度矩阵[]Q 为挠度矩阵[]S 的逆矩阵,也就是:[][]1-=S Q (8)第(8)式可改写成:{}[]{}εσQ = (9)其中刚度矩阵[]⎥⎥⎥⎥⎥⎥⎦⎤⎢⎢⎢⎢⎢⎢⎣⎡----=1221122211221121121222112100011011G E E E E Q νννννννννν (10) 又由于21ν和12ν的关系式121221E E νν=,因此2112Q Q =,也就是2112211211212211νννννν-=-E E ,刚度矩阵[]Q 为对称矩阵[][]TQ Q =。
- 1、下载文档前请自行甄别文档内容的完整性,平台不提供额外的编辑、内容补充、找答案等附加服务。
- 2、"仅部分预览"的文档,不可在线预览部分如存在完整性等问题,可反馈申请退款(可完整预览的文档不适用该条件!)。
- 3、如文档侵犯您的权益,请联系客服反馈,我们会尽快为您处理(人工客服工作时间:9:00-18:30)。
A一13玻璃钢学会第十六届玻璃钢/复合材料学术年会论文集2006年
Amys在复合材料结构优化设计中的应用
覃海艺,邓京兰
(武汉理工大学材料科学与工程学院,武汉430070
摘要:优化设计方法在复合材料结构设计中起着十分重要的作用。
本文详细介绍了Ansys两种优化设计方法.目标函数最优设计和拓扑优化设计的过程,并运用目标函数最优设计方法对复合材料夹层结构进行了最优结构层合设计和运用拓扑优化设计方'法对玻璃钢圆凳进行了最佳形状设计。
结果证明Ansys优化设计方法在复合材料结构设计中的有效性。
关键词:Ansys;优化设计方法;目标函数最优设计;拓扑优化设计;复合材料
l前言
复合材料是由两种或多种性质不同的材料组成,具有比强度、比刚度高、耐疲劳性能好及材料与性能可设计强等特点,广泛应用于汽车、建筑、航空、卫生等领域。
复合材料通过各相组分性能的互补和关联获得优异的性能,因此复合材料各组分之间及材料整体结构的合理布置,充分发挥复合材料的性能已成为设计的关键所在…。
Ansys软件是融结构、流体、电场、磁场、声场分析于一体的大型通用有限元分析软件。
优化设计是一种寻找确定最优设计方案的技术,Ansys强大的优化设计功能已广泛地应用于复合材料制品的结构设计心J。
2Ansys中的优化设计方法【3娟j
2.1目标函数最优设计
“最优设计”是指满足所有的设计要求,而且所需(如重量、面积、体积、应力、费用等的方案最小,即目标函数值最小。
也就是说,最优设计方案是一个最有效率的方案。
在Ansys中设计方案的任何方面都是可以优化的,如尺寸(如厚度、形状(如过
渡圆角的大小、支撑位置、制造费用、自然频率、材料特性等。
实际上,所有可以参数化的Ansys选项都可以作优化设计。
目标函数最优设计是通过改变设计变量(自变量的数值,使状态变量(设计变量的函数,因变量在满足一定条件时,目标函数(因设计变量的改变而有所改变的值最小。
目标函数最优设计的一般步骤为①生成循环所用的分析文件,该文件须包括整个分析的过程,并满足以下条件:参数化建立模型(PREIy7,对模型进行初次求解(SOLUTION,对初次求解的结果提取并指定状态变量和目标函数(POSTl/POST26;②在Ansys数据库里建立与分析文件中变量相对应的参数,这一步是标准的做法,但不是必须的(BEGIN或OPT;③进入OPT优化处理器,指定要进行优化设计循环的分析文件(oPT;④声明优化变量:指定哪些参数是设计变量,哪些参数是状态变量,哪个参数是目标函数;⑤选择优化工具或优化算法:优化算法是使单个函数(目标函数在控制条件下达到最小值的传统算法,包括零阶算法和一阶算法;⑥指定优化循环控制方式,每种优化方法和工具都有相应的循环控制参数,比如最大迭代次数等;⑦进行优化分析;⑧查看设计序列结果(OPT和后处理(POSTl/POST26。
2.2拓扑优化设计
拓扑优化是指形状优化,有时也称为外型优化。
拓扑优化的目标是寻找承受单载荷或多作者简介:覃海艺(1980・,男,在读硕士。
49
载荷的物体的最佳材料分配方案。
与目标函数最优设计不同的是,拓扑优化不需要给出参数和优化变量的定义。
目标函数、状态变量和设计变量是程序内部预定义好的。
用户只需给出结构的参数(材料特性、模型、载荷等和要省去的材料百分比,即可通过优化计算得到结构的最佳外形设计。
拓扑优化的目标是在满足结构约束的情况下减少结构的变形能,从而提高结构的刚度,所以在优化中表现为“最大刚度”设计。
拓扑优化设计主要步骤为①定义拓扑优化包括定义材料特性(杨氏模量和泊松比,选择合适的单元类型生成有限元模型,施加载荷和边界条件做单载荷步或多载荷步分析;②选择单元类型,Ansys中可用于拓扑优化的单元有二维实体单元(SOLID2和SOLID82、三维实体单元(SOLID92和SOLID95、壳单元(SHELL93;③指定要优化和不优化的区域,只有单元类型号为1的单元才能做拓扑优化,使用这种限制控制模型优化和不优化的部分;④定义和控制载荷工况,可以在单个载荷工况和多个载荷工况下做拓扑优化;⑤定义和控制优化过程:定义优化参数和进行拓扑优化;⑥查看结果。
拓扑优化结束后,ANSYS将优化结果存储于结果文件(Jobname.RST供通用后处理器使用。
3复合材料结构优化设计[3侧
3.1目标函数最优设计实例
3.1.1问题的提出
玻璃钢夹层结构已广泛应用于玻璃钢制品中,生产一款夹层结构的玻璃钢汽车顶盖,长3000ram,宽1500mm,厚25ram。
初步计算,生产中夹层结构单位体积费用为玻璃钢的1/5,顶盖设计最大面载荷为1000N/m2。
材料力学性能为(E为弹性模量,盯为许用应力,恤为泊松比,G为剪切弹性模量,8为许用应变,U为最大允许挠度:
玻璃钢(视为板结构,正交各向异性材料
El_16GPa,E:=12GPa,G:2=4.5GPa,斗112=o.30
盯1=150MPa,£1=0.2%,U1=8.0mm
夹层为泡沫材料(视为各向同性材料
Ei=E;=o.1GPa,斗212=o.30,盯2=1.0MPa,82=0.15%,U2=8.0mm 问:夹层材料厚度为多少较合适。
3.1.2生成优化循环分析文件
(1参数化建模
由已知,把汽车顶盖视为平板模型,尺寸不变,四边简支,顶部受最大面载荷
1000N/m2。
设计平板上下层为玻璃钢材料,厚度均为T。
,中间层为泡沫材料,厚度为T2形状如图1,且T2=25—2×T。
用有限元软件Ansy8建立参数化模型,采用99号单元进行网格划分,如图2所示。
图1平板截面示意
图2有限元网格模型
3.2拓扑优化设计实例
3.2.1问题的提出
如设计一复合材料圆凳,采用短切纤维增强材料和SMC模压成型工艺,上部圆直径为500ram,下部圆直径为700mm,高为600ram,圆凳上部设计最大面载荷为
10000N/m2。
视短切纤维增强复合材料为各向同性材料∽J,经样板试验测得玻璃钢材料力学性能为弹性模量E= 15GPa,泊松比斗=0.32,许用应变8=O.2%,许用应力
or=150MPa。
按设计经验,初步设计圆凳形状如图5(有限元网格图所示。
为了防止圆凳因受压失稳而破坏,其壁加厚为10ram,由此经Ansys静力分析得结果,如表2。
其中,8一为最大应变,盯一为最大应力,u~为最大位移。
表2初步设计的计算结果
由表2的计算结果发现,所设计的产品力学安全性能远远大于使用要求,按这样的设计,材料没有得到充分的发挥,造成浪费。
在基本尺寸(长宽高及壁厚不变的情况下,对圆凳下部侧边进行材料缩减(即挖空,以合理使用材料和减少生产成本。
3.2.2拓扑优化分析
按设计要求,选取solid95优化单元进行网格划分(如图5,对凳脚中间部分节点施加固定约束,圆凳上表面施加面载荷,初步设定缩减参数为(圆凳总体积的40%。
经拓扑优化分析,可得优化结果,如图6。
图5初步设计有限元模型图6拓扑优化结果图7重新设计的模型
3.2.3形状重新设计
按形状优化设计结果(图6,对模型形状进行重新设计如图7,并对其进行有限元静力分析校核,分析结果见表3。
表3形状重新设计后的计算结果
由表3数据可知,按图7的设计方案,模型在满足使用性能的条件下,材料用量比初步设计结果(图5少了许多,是一种较理想的设计方案。
仔细观察表3数据可知,按图7的设计方案,模型的安全系数仍然相当高。
按图6拓扑优化结果所示,还可以酌情对模型进行一部分材料缩减,如再次挖空减料、减小截面厚度等,再次进行分析校核,直到得出最合理最经济的设计方案。
值得注意的是凳脚太细或截面太薄时,需对模型进行屈曲分析校核,以防止圆凳在满足52。