模具加热及冷却系统设计
模具设计指南-模温控制

第十章模温控制模具温度对胶件的成型质量、成型效率有着较大的影响。
在温度较高的模具里,熔融胶料的流动性较好,有利于胶料充填型腔,获取高质量的胶件外观表面,但会使胶料固化时间变长,顶出时易变形,对结晶性胶料而言,更有利于结晶过程进行,避免存放及使用中胶件尺寸发生变化;在温度较低的模具里,熔融胶料难于充满型腔,导致内应力增加,表面无光泽,产生银纹、熔接痕等缺陷。
不同的胶料具有不同的加工工艺性,并且各种胶件的表面要求和结构不同,为了在最有效的时间内生产出符合质量要求的胶件,这就要求模具保持一定的温度,模温越稳定,生产出的胶件在尺寸形状、胶件外观质量等方面的要求就越一致。
因此,除了模具制造方面的因素外,模温是控制胶件质量高低的重要因素,模具设计时应充分考虑模具温度的控制方法。
10.1模具温度控制的原则和方式10.1.1模具温度控制的原则为了保证在最有效的时间内生产出高外观质量要求、尺寸稳定、变形小的胶件,设计时应清楚了解模具温度控制的基本原则。
(1)不同胶料要求不同的模具温度。
参见10.1.3节(2)不同表面质量、不同结构的模具要求不同的模具温度,这就要求在设计温控系统时具有针对性。
(3)前模的温度高于后模的温度,一般情况下温度差为20~30º左右。
(4)有火花纹要求的前模温度比一般光面要求的前模温度高。
当前模须通热水或热油时,一般温度差为40º左右。
(5)当实际的模具温度不能达到要求模温时,应对模具进行升温。
因此模具设计时,应充分考虑胶料带入模具的热量能否满足模温要求。
(6)由胶料带入模具的热量除通过热辐射、热传导的方式消耗外,绝大部分的热量需由循环的传热介质带出模外。
铍铜等易传热件中的热量也不例外。
(7)模温应均衡,不能有局部过热、过冷。
10.1.2模具温度的控制方式模具温度一般通过调节传热介质的温度,增设隔热板、加热棒的方法来控制。
传热介质一般采用水、油等,它的通道常被称作冷却水道。
第9章 压铸模加热和冷却系统设计

温金属液预热。 4)预热后的压铸模应进行必要的清理和润滑。 5)冷却液应该在压铸模预热之前此时通入,否
则将因激冷而引起压铸模产生裂纹甚至破裂。
9.2 模具的冷却 一、压铸模的冷却方法 压铸模的冷却方法主要有风冷和水冷两种形式. (一)风冷
通入成型镶缺或型芯内从而实现冷却,因此水冷模 具结构较风冷复杂。水冷速度比风冷速度快得多, 它能有效地提高生产效率。一般可以通过测定进水 口和出水口的温度以及模具型腔表面温度,据此控 制水流量,从而调节冷却效率。大中型铸件或厚壁 铸件以及大批量连续操作时为了保证散热员较大的 要求,通常采用水冷。
二、冷却通道的设计计算
2.熔融金属传给模具的热流量 熔融金属传给模具的热流量Q可 按下式计算
Q=qNm 式中 q——凝固热量(J/k g);
N——压铸机生产率(次/h); m——每次压铸的合金重量(kg/次)。 不同合金的凝固热量q 值,见表。
3.模具自然传走的热流量 模具自然传走的热量Q1是通 过周围辐射和传导而散发的。 其计算式可表示为
三、冷却系统的布置 (一)冷却通道的设计要点 设计冷却通道时应注意下述几点: ‘
1)冷却水道要求布置在型腔内温度最高、热量比较 集中的区域,流路要通畅,无堵塞现象。
2)模具镶拼结构上有冷却水通过时要求采取密封措 施,防止泄漏。
3)水管接头尽可能设置在模具下面或操作者的对面 一侧,其外径尺寸应统一,以便接装输水胶管。
活动型芯或者推杆发生干涉。加热孔径与电热元 件的壳体外径的配合间隙不应太大,以免降
低传热率。在动模和定模的套板上可以布置供安 装热电偶的测温孔,以便控制模温,其配合 尺寸应按照所选用的热电偶的规格而定。
典型注塑模设计-项目1-模块三

1.排气系统
大多数情况下可利用模具分型面或模具零件间的配合间隙自然地排气 ,其间隙值通常为0.01~0.03mm,以不产生溢料为限。
排气与引气系统的设计
相关理论知识
2.引气系统的设计 大型深壳形制品包紧型芯形成真空,难以脱模,需要引气装置。 镶拼式侧隙引气 气阀式引气 相关理论知识
能合理地设计浇注系统
能合理地进行成型零件设计
能正确地绘制模具装配图和零件工作图
1.能设计合理的冷却系统 2.能设计合理的排气系统 3.能绘制合理的冷却水道布置图
学习目标
工作任务
根据图示的塑件零件图以及已确定的总体结构方案,设计本模具的冷却系统和排气系统,并绘制冷却水道布置图。
冷却系统设计
低粘度-低模温
单击此处添加正文,文字是您思想的提炼,为了演示发布的良好效果,请言简意赅地阐述您的观点。您的内容已经简明扼要,字字珠玑,但信息却千丝万缕、错综复杂,需要用更多的文字来表述;但请您尽可能提炼思想的精髓,否则容易造成观者的阅读压力,适得其反。正如我们都希望改变世界,希望给别人带去光明,但更多时候我们只需要播下一颗种子,自然有微风吹拂,雨露滋养。恰如其分地表达观点,往往事半功倍。当您的内容到达这个限度时,或许已经不纯粹作用于演示,极大可能运用于阅读领域;无论是传播观点、知识分享还是汇报工作,内容的详尽固然重要,但请一定注意信息框架的清晰,这样才能使内容层次分明,页面简洁易读。如果您的内容确实非常重要又难以精简,也请使用分段处理,对内容进行简单的梳理和提炼,这样会使逻辑框架相对清晰。
根据图示的塑件零件图以及已确定的总体结构方案,设计本模具的冷却系统和排气系统并绘制冷却水道布置图。
练习
高粘度-高模温
对模具加热或冷却

第10章模温控制模具温度对胶件的成型质量、成型效率有着较大的影响。
在温度较高的模具里,熔融胶料的流动性较好,有利于胶料充填型腔,获取高质量的胶件外观表面,但会使胶料固化时间变长,顶出时易变形,对结晶性胶料而言,更有利于结晶过程进行,避免存放及使用中胶件尺寸发生变化;在温度较低的模具里,熔融胶料难于充满型腔,导致内应力增加,表面无光泽,产生银纹、熔接痕等缺陷。
不同的胶料具有不同的加工工艺性,并且各种胶件的表面要求和结构不同,为了在最有效的时间内生产出符合质量要求的胶件,这就要求模具保持一定的温度,模温越稳定,生产出的胶件在尺寸形状、胶件外观质量等方面的要求就越一致。
因此,除了模具制造方面的因素外,模温是控制胶件质量高低的重要因素,模具设计时应充分考虑模具温度的控制方法。
概念:对模具加热或冷却,将模温控制在合理的范围内。
——模具冷却介质:水、油、铍铜、空气等;——模具的加热方式:热水,蒸气,热油、电热棒加热等。
温度控制的重要性模温对不同塑料的影响1.对流动性较好的塑料(PE、PP、HIPS、ABS等),降低模温可减小应力开裂(模温通常为60°左右);2.对流动性较差的塑料(PC、PPO、PSF等),提高模温有利于减小塑件的内应力(模温通常在80°至120°之间)。
模温对塑件成型质量的影响(1)过高:脱模后塑件变形率大,还容易造成溢料和粘模;(2)过低:则熔胶流动性差,表面会产生银丝、流纹、啤不满等缺陷;(3)不均匀:塑件收缩不均匀,导致翘曲变形。
模具温度直接影响注塑周期模具冷却时间约占注塑周期的80%。
10.1模具温度控制的原则和方式10.1.1模具温度控制的原则为了保证在最有效的时间内生产出高外观质量要求、尺寸稳定、变形小的胶件,设计时应清楚了解模具温度控制的基本原则。
(1)不同胶料要求不同的模具温度。
(2)不同表面质量、不同结构的模具要求不同的模具温度,这就要求在设计温控系统时具有针对性。
SMC模具结构设计(SMC_Mold)

SMC模具结构设计SMC制品模压模具制作流程一、接受任务书成型SMC制件的任务书通常由制件设计者提出,其内容如下: 1. 经过审签的正规制件图纸,并注明采用产品的牌号、技术参数等。
2. SMC制件说明书或技术要求。
3. 生产产量。
4. SMC制件样品。
通常模具设计任务书由SMC 制件工艺员根据成型SMC制件的任务书提出,模具设计人员以成型SMC制件任务书、模具设计任务书为依据来设计模具。
二、收集、分析、消化原始资料收集整理有关制件设计、成型工艺、成型设备、机械加工及特殊加工资料,以备设计模具时使用。
1. 消化SMC制件图,了解制件的用途,分析SMC制件的工艺性,尺寸精度等技术要求。
例如SMC制件在外表形状、颜色透明度、使用性能方面的要求是什么,SMC件的几何结构、斜度、嵌件等情况是否合理,熔接痕、缩孔等成型缺陷的允许程度,有无涂装、电镀、胶接、钻孔等后加工。
选择塑料制件尺寸精度最高的尺寸进行分析,看看估计成型公差是否低于SMC制件的公差,能否成型出合乎要求的SMC制件来。
此外,还要了解SMC产品的固化及成型工艺参数。
2. 消化工艺资料,分析工艺任务书所提出的成型方法、设备型号、材料规格、模具结构类型等要求是否恰当,能否落实。
成型材料应当满足SMC制件的强度要求,具有好的流动性、均匀性和各向同性、热稳定性。
根据SMC制件的用途,成型材料应满足染色、镀金属的条件、装饰性能、必要的弹性和塑性、透明性或者相反的反射性能、胶接性或者焊接性等要求。
3. 确定成型方法采用直压法、铸压法还是注射法。
4、选择成型设备根据成型设备的种类来进行模具,因此必须熟知各种成型设备的性能、规格、特点。
例如对于模压机来说,在规格方面应当了解以下内容:模压容量、模压力、速度、模具安装尺寸、顶出装置及尺寸、开模方式、喷嘴孔直径及喷嘴球面半径、浇口套定位圈尺寸、模具最大厚度和最小厚度、模板行程等,具体见相关参数。
要初步估计模具外形尺寸,判断模具能否在所选的模压机上安装和使用。
模具加热与冷却系统设计
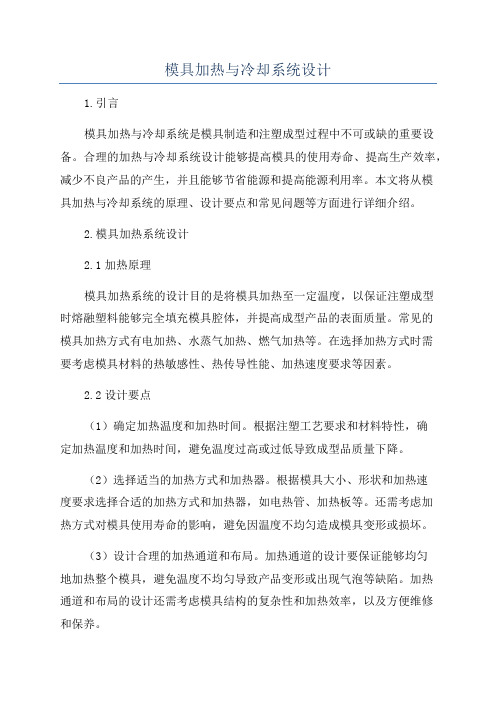
模具加热与冷却系统设计1.引言模具加热与冷却系统是模具制造和注塑成型过程中不可或缺的重要设备。
合理的加热与冷却系统设计能够提高模具的使用寿命、提高生产效率,减少不良产品的产生,并且能够节省能源和提高能源利用率。
本文将从模具加热与冷却系统的原理、设计要点和常见问题等方面进行详细介绍。
2.模具加热系统设计2.1加热原理模具加热系统的设计目的是将模具加热至一定温度,以保证注塑成型时熔融塑料能够完全填充模具腔体,并提高成型产品的表面质量。
常见的模具加热方式有电加热、水蒸气加热、燃气加热等。
在选择加热方式时需要考虑模具材料的热敏感性、热传导性能、加热速度要求等因素。
2.2设计要点(1)确定加热温度和加热时间。
根据注塑工艺要求和材料特性,确定加热温度和加热时间,避免温度过高或过低导致成型品质量下降。
(2)选择适当的加热方式和加热器。
根据模具大小、形状和加热速度要求选择合适的加热方式和加热器,如电热管、加热板等。
还需考虑加热方式对模具使用寿命的影响,避免因温度不均匀造成模具变形或损坏。
(3)设计合理的加热通道和布局。
加热通道的设计要保证能够均匀地加热整个模具,避免温度不均匀导致产品变形或出现气泡等缺陷。
加热通道和布局的设计还需考虑模具结构的复杂性和加热效率,以及方便维修和保养。
3.1冷却原理模具冷却系统的设计目的是将模具迅速冷却至一定温度,使注塑成型的产品迅速凝固,以便顺利脱模。
冷却系统一般采用水冷或油冷方式。
水冷却系统又可分为内冷和外冷两种形式。
选择合适的冷却方式和冷却介质需考虑模具的形状、材料及成型周期等因素。
3.2设计要点(1)冷却通道的设计。
冷却通道的设计要保证能够覆盖整个模具,使冷却介质能够充分接触模具表面,实现快速冷却。
通道的布局要合理,避免对产品的冷却时产生热死区。
(2)冷却介质选择。
根据模具的要求,选择合适的冷却介质,如自来水、循环水或特殊的冷却液等。
应考虑冷却介质的对模具材料的腐蚀性、冷却效果和成本等因素。
压缩模设计说明书1

学校:北华航天工业学院姓名:学号:指导老师:完成日期:2011年6月23日摘要近年来,我国家电工业的高速发展对模具工业,尤其是塑料模具提出了越来越高的要求,2004年,塑料模具在整个模具行业中所占比例已上升到30%左右,据有关专家预测,在未来几年中,中国塑料模具工业还将持续保持年均增长速度达到10%以上的较高速度的发展。
国内塑料模具市场以注塑模具需求量最大,其中发展重点为工程塑料模具。
压缩成型是塑料成型的一种重要方法,它主要适用于热塑性塑料的成型,可以一次成型形状复杂的精密塑件。
本章就是将绝缘类零件作为设计模型,将压缩模具的相关知识作为依据,阐述塑料压缩模具的设计过程。
关键词:压缩模一模二腔上模下模推杆推出前言塑料是20世纪才发展起来的新材料,目前世界上塑料的体积产量已经赶上和超过了钢材,成为当前人类使用的一大类材料。
我国的塑料工业正在飞速发展,塑料制品的应用已深入到国民经济的各个部门。
塑料工程通常是指塑料制造与改性,塑料成型与制品加工。
塑料制品与模具设计是塑料工程中的重要部分,是塑料工业中不可少的环节。
模具是工业生产的重要工艺装备,它被用来成型具有一定形状和尺寸的各种制品。
在各种材料加工工业中广泛地使用着各种模具,如金属制品成型的压铸模,锻压模,浇铸模,非金属模制品成型的玻璃模,陶瓷模,塑料模等。
塑料成型模具是成型塑料制品的工具。
塑料成型模具应能生产并满足给定的形状、尺寸、外观和内在性能要求的制品。
要求模具能被高效率的应用,且操作简便,并达到自动化水平。
要求模具有合理的结构,制造容易且成本低廉。
也要求模具有足够的使用寿命。
近年来塑料成型模具的产量和水平发展十分迅速,高效率,自动化,大型,精密,长寿命模具总产量中所占比例越来越大,在各种塑料模具中来看,压缩模具在生产中占的比例是越来越大。
一、塑件的技术要求与工艺分析1 塑件的技术要求2 塑件结构图材料为塑造11—1,小批量生产。
3 工艺性分析①对制品的原材料分析塑件的工艺分析对塑件的原料分析。
模具设计原理及考虑

制件设计的一般考虑工程塑料制品大部分是用注射成型方法加工而成的,制件的设计必须在满足使用要求和符合塑料本身的特性前提下,尽可能简化结构和模具、节省材料、便于成型。
制件设计中应分别考虑如下因素:一、制件的形状应尽量简单、便于成型。
在保证使用要求前提下,力求简单、便于脱模,尽量避免或减少抽芯机构,如采用下图例中(b)的结构,不仅可大大简化模具结构,便于成型,且能提高生产效率。
二、制件的壁厚确定应合理。
塑料制件的壁厚取决于塑件的使用要求,太薄会造成制品的强度和刚度不足,受力后容易产生翘曲变形,成型时流动阻力大,大型复杂的制品就难以充满型腔。
反之,壁厚过大,不但浪费材料,而且加长成型周期,降低生产率,还容易产生气泡、缩孔、翘曲等疵病。
因此制件设计时确定制件壁厚应注意以下几点:1.在满足使用要求的前提下,尽量减小壁厚;2.制件的各部位壁厚尽量均匀,以减小内应力和变形;3.承受紧固力部位必须保证压缩强度;4.避免过厚部位产生缩孔和凹陷;5.成型顶出时能承受冲击力的冲击。
国外的一些常用塑料的推荐壁厚如下表:三、必须设置必要的脱模斜度为确保制件成型时能顺利脱模,设计时必须在脱模方向设置脱模斜度,其大小与塑料性能、制件的收缩率和几何形状有关,对于工程塑料的结构件来说,一般应在保证顺利脱模的前提下,尽量减小脱模斜度。
下表为根据不同材料而推荐的脱模斜度:具体确定脱模斜度时应考虑以下几点:1.对于收缩率大的塑料制件应选用较大的脱模斜度;2.对于大尺寸制件或尺寸精度要求高的制件应采用较小的脱模斜度;3.制件壁厚较厚时,成型收缩增大,因此脱模斜度应取大;4.对于增强塑料脱模斜度宜取大;5.含自润滑剂等易脱模塑料可取小;6.一般情况下脱模斜度不包括在制件公差范围内。
四.强度和刚度不足可考虑设计加强筋为满足制件的使用所需的强度和刚度单用增加壁厚的办法,往往是不合理的,不仅大幅增加了制件的重量,而且易产生缩孔、凹痕等疵病,在制件设计时应考虑设置加强筋,这样能满意地解决这些问题,它能提高制件的强度、防止和避免塑料的变形和翘曲。
- 1、下载文档前请自行甄别文档内容的完整性,平台不提供额外的编辑、内容补充、找答案等附加服务。
- 2、"仅部分预览"的文档,不可在线预览部分如存在完整性等问题,可反馈申请退款(可完整预览的文档不适用该条件!)。
- 3、如文档侵犯您的权益,请联系客服反馈,我们会尽快为您处理(人工客服工作时间:9:00-18:30)。
注:在Re=10000和水温10°C的条件下(Re为雷诺系数)。
一般水孔直径可根据塑件的平均壁厚来确定。平均壁厚 为2mm时,水道直径可取10~14mm。
无论多大的模具,水孔的直径不能大于14mm,否则冷却 水难以处于最佳流动状态,以致降低热交换效率。
02.06.2019
3)冷却水道导热总面积的计算
02.06.2019
4.冷却通道的形式
02.06.2019
02.06.2019
02.06.2019
02.06.2019
02.06.2019
练习: 零件B 的质量为200g(已考虑浇注系统凝料),成型
周期时间t=40s,材料低压聚乙烯,在出口处水温400, 入口处冷却温度200, C=4183 J/kg·k, ρ=998.203 kg/m3。
由上述计算可知,因为模具每分钟所需 的冷却水体积流量较小,故可不设冷却系 统,依靠空冷的方式冷却模具即可。
3.冷却装置的形式
02.06.2019
细型芯的冷却装置
02.06.2019
大型芯的冷却装置
3
A
3
2
5
2
剖面A-A
4A
5
1
1
a)
b)
02.06.2019
隔板式冷却装置
02.06.2019
水管喷流式冷却装置
210.00 285.85
塑料
尼龙 聚甲醛 醋炭纤维素 丁酸-醋炭纤维素
ABS AS
Δi
700.14~816.48 420.00 289.38 259.14
326.76~396.48 280.14~349.85
ቤተ መጻሕፍቲ ባይዱ
求出所需冷却水体积后,可根据处于湍流状态的流速、流量与管道直径的关系,确定 模具上的冷却水道孔径。
02.06.2019
4)冷却水道总长度的计算
5)冷却水道数目的计算
由于受模具尺寸的限制,每根水路的长度由模具尺寸决定。设 每条水路的长度为l,则冷却水道的数目n=L/l。
02.06.2019
例:零件A 的质量为20g(已考虑浇注系统凝料),成型 周期时间t=50s,材料ABS,在出口处水温400,入口 处冷却温度200, C=4183 J/kg·k, ρ=998.203 kg/m3,
型芯型腔温差过大,塑件收缩不均、内应力增大、 塑件变形、尺寸不稳定。
二、模具加热装置的设计
1.模具加热的方法有
气体加热(蒸汽) 工频感应加热:设备复杂 电阻加热:最常用
2.电阻加热元件
02.06.2019
3.电阻加热的计算
1)理论计 算
02.06.2019
2)近似计算
加热模具所需的电功率(P)可按模具的重量(m)近似计算: P=0.24m(T2-T1)
02.06.2019
60° C
图冷却水道冷 却数水量道传数热量 与关传系热 关 系
⑶冷却孔要避开塑件的熔接痕部位
02.06.2019
⑷水孔排列与型腔形状吻合
图 冷 (5)浇口附近与壁厚处加强冷却 却 水 道 布 局
02.06.2019
(6)定模与动模要分别冷却,保证冷却平衡。
02.06.2019
第13讲模具加热与冷却系统设计
目的与要求: 1.要求掌握加热与冷却装置设计计算 2.掌握设计原则
02.06.2019
重点和难点: 理论与实际相结合
一、模具加热与冷却的目的
1.加热 ※热固性塑料需要较高的模具温度促使交联反应进行 ※某些热塑性塑料也需维持80度以上的模温,如聚甲
醛、聚苯醚等 ※大型模具要预热 ※热流道模具的广泛使用
02.06.2019
2)冷却水孔直径的确定
表10-3 冷却流道的稳定湍流速度、流量、流道直径
冷却流道直径d
8 10 12
速度v
1.66 1.32 1.10
V
冷却流道直径d
5.0×10-3
15
6.2×10-3
20
7.4×10-3
25
速度v
0.87 0.66 0.53
V
9.2×10-3 12.4×10-3 15.5×10-3
2.冷却
模塑周期主要取决于冷却定型时间(约占80%),通过 降低模温来缩短冷却时间,是提高生产效率的关键。
02.06.2019
02.06.2019
模具温度与塑件质量的关系
模温过低
塑料流动性差,塑件轮廓不清晰,表面无光泽; 热固性塑料则固化不足,性能严重下降。
模温过高 易造成溢料粘模,塑件脱模困难,变形大;热固 性塑料则过熟。 模温不均
① 电热环加热 小型模具:Pu=40W/kg; 大型模具:Pu=60W/kg;
② 电热棒加热 小型模具(40kg以下):Pu=35W/kg; 中型模具(40~100kg);Pu=30W/kg; 大型模具(100kg以上):Pu=20W/kg。
02.06.2019
三、模具冷却装置的设计
冷却介质:水、压缩空气、冷冻水、油
凹模与型芯的冷却
⑺冷却通道应密封且不应通过镶块接缝,以免漏水。 ⑻进出水温差不宜过大 (9)节约用水原则
02.06.2019
2.冷却回路的尺寸确定
1)所需冷却水体积的计算
表10-2 常用塑料在凝固时所放出的热焓量 (KJ/kg)
塑料
高压聚乙烯 低压聚乙烯
聚丙烯 聚苯乙烯 聚氯乙烯 有机玻璃
Δi
583.33~700.14 700.14~816.48 583.33~700.14 280.14~349.85
02.06.2019
冷却通道设计原则 冷却装置的形式
冷却回路的尺寸确定 冷却通道的形式
1.冷却通道设计原则 ⑴冷却水孔相对位置尺寸
A—型腔底面
Lmin=D
02.06.2019
从型腔表面到冷却水孔的距离
⑵模具结构允许,冷却孔尽量大、多,使 冷却更均匀。
445585.°1553C.683660.°16°3C.°C8°6CC6° C° C
解:所需冷却水体积的计算
G=20(60×60)/50 =1440=1.44kg/h
Δi=4×105J/KG
V=(1.44×4×105)/(60 ×4183 × 998(40-20))
=576000/5009560800 =1.15 × 10-4m3/min < 5.0×10-3 m3/min
02.06.2019
其中:T2-T1—模具加热前后的温度差
例题 已知:模具总重量:m=50Kg 模具成型温度 T2=155℃ 室温T1=20℃ ,计算所需电功率。
02.06.2019
P=0.24×50(155-20)=1620W
结论:可以取400W的电热棒4根
3)经验法
可以根据加热方式和模具的大小,采用下面经验数据计 算单位质量模具的电加热功率Pu 。