磷化处理技术条件
磷化处理影响因素及常见问题

一、磷化工艺参数的影响1、总酸度————总酸度过低、磷化必受影响,因为总酸度是反映磷化液浓度的一项指标。
控制总酸度的意义在于使磷化液中成膜离子浓度保持在必要的范围内。
2、游离酸度————游离酸度过高、过低均会产生不良影响。
过高不能成膜,易出现黄锈;过低磷化液的稳定性受威胁,生成额外的残渣。
游离酸度反映磷化液中游离H+的含量。
控制游离酸度的意义在于控制磷化液中磷酸二氢盐的离解度,把成膜离子浓度控制在一个必须的范围。
磷化液在使用过程中,游离酸度会有缓慢的升高,这时要用碱来中和调整,注意缓慢加入,充分搅拌,否则碱液局部过浓会产生不必要的残渣,出现越加碱,游离酸度越高的现象。
单看游离酸度和总酸度是没有实际意义的,必须一起考虑。
3、酸比————酸比即指总酸度与游离酸度的比值。
一般的说酸比都在5~30 的范围内。
酸比较小的配方,游离酸度高,成膜速度慢,磷化时间长,所需温度高。
酸比较大的配方,成膜速度快,磷化时间短,所需温度低。
因此必须控制好酸比。
4、温度————磷化处理温度与酸比一样,也是成膜的关键因素。
不同的配方都有不同的温度范围,实际上,他在控制着磷化液中的成膜离子的浓度。
温度高,磷酸二氢盐的离解度大,成膜离子浓度相应高些,因此可以利用此种关系在降低温度的同时提高酸比,同样可达到成膜,其关系如下:70℃60 ℃50 ℃40 ℃30 ℃20 ℃1/5 1/7 1/10 1/15 1/20 1/25生产单位确定了某一配方后,就应该严格控制好温度,温度过高要产生大量沉渣,磷化液失去原有平衡。
温度过低,成膜离子浓度总达不到浓度积,不能生成完整磷化膜。
温度过高,磷化液中可溶性磷酸盐的离解度加大,成膜离子浓度大幅度提高,产生不必要的沉渣,白白浪费了磷化液中的有效成分,原有的平衡被迫坏,形成一个新的温度下的平衡,如,低温磷化液在温度失控而升高时,H2PO4→H++PO43- 的离解反应向右进行,从而使磷酸根浓度升高,产生磷酸锌沉淀,使磷化液的酸比自动升高。
磷化工艺及检验
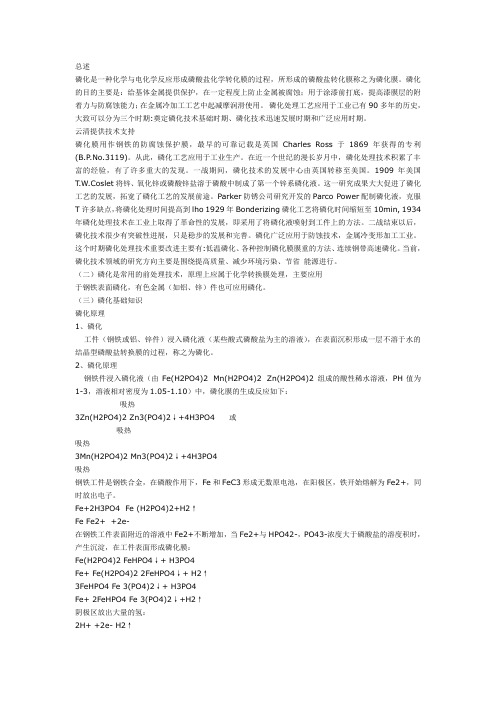
总述磷化是一种化学与电化学反应形成磷酸盐化学转化膜的过程,所形成的磷酸盐转化膜称之为磷化膜。
磷化的目的主要是:给基体金属提供保护,在一定程度上防止金属被腐蚀;用于涂漆前打底,提高漆膜层的附着力与防腐蚀能力;在金属冷加工工艺中起减摩润滑使用。
磷化处理工艺应用于工业己有90多年的历史,大致可以分为三个时期:奠定磷化技术基础时期、磷化技术迅速发展时期和广泛应用时期。
云清提供技术支持磷化膜用作钢铁的防腐蚀保护膜,最早的可靠记载是英国Charles Ross于1869年获得的专利(B.P.No.3119)。
从此,磷化工艺应用于工业生产。
在近一个世纪的漫长岁月中,磷化处理技术积累了丰富的经验,有了许多重大的发现。
一战期间,磷化技术的发展中心由英国转移至美国。
1909年美国T.W.Coslet将锌、氧化锌或磷酸锌盐溶于磷酸中制成了第一个锌系磷化液。
这一研究成果大大促进了磷化工艺的发展,拓宽了磷化工艺的发展前途。
Parker防锈公司研究开发的Parco Power配制磷化液,克服T许多缺点,将磷化处理时间提高到lho 1929年Bonderizing磷化工艺将磷化时间缩短至10min, 1934年磷化处理技术在工业上取得了革命性的发展,即采用了将磷化液喷射到工件上的方法。
二战结束以后,磷化技术很少有突破性进展,只是稳步的发展和完善。
磷化广泛应用于防蚀技术,金属冷变形加工工业。
这个时期磷化处理技术重要改进主要有:低温磷化、各种控制磷化膜膜重的方法、连续钢带高速磷化。
当前,磷化技术领域的研究方向主要是围绕提高质量、减少环境污染、节省能源进行。
(二)磷化是常用的前处理技术,原理上应属于化学转换膜处理,主要应用于钢铁表面磷化,有色金属(如铝、锌)件也可应用磷化。
(三)磷化基础知识磷化原理1、磷化工件(钢铁或铝、锌件)浸入磷化液(某些酸式磷酸盐为主的溶液),在表面沉积形成一层不溶于水的结晶型磷酸盐转换膜的过程,称之为磷化。
酸洗磷化喷涂标准
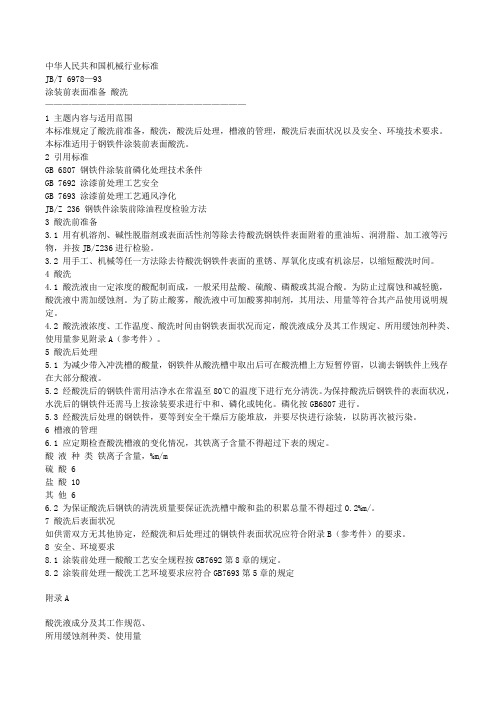
中华人民共和国机械行业标准JB/T 6978—93涂装前表面准备酸洗———————————————————————1 主题内容与适用范围本标准规定了酸洗前准备,酸洗,酸洗后处理,槽液的管理,酸洗后表面状况以及安全、环境技术要求。
本标准适用于钢铁件涂装前表面酸洗。
2 引用标准GB 6807 钢铁件涂装前磷化处理技术条件GB 7692 涂漆前处理工艺安全GB 7693 涂漆前处理工艺通风净化JB/Z 236 钢铁件涂装前除油程度检验方法3 酸洗前准备3.1 用有机溶剂、碱性脱脂剂或表面活性剂等除去待酸洗钢铁件表面附着的重油垢、润滑脂、加工液等污物,并按JB/Z236进行检验。
3.2 用手工、机械等任一方法除去待酸洗钢铁件表面的重锈、厚氧化皮或有机涂层,以缩短酸洗时间。
4 酸洗4.1 酸洗液由一定浓度的酸配制而成,一般采用盐酸、硫酸、磷酸或其混合酸。
为防止过腐蚀和减轻脆,酸洗液中需加缓蚀剂。
为了防止酸雾,酸洗液中可加酸雾抑制剂,其用法、用量等符合其产品使用说明规定。
4.2 酸洗液浓度、工作温度、酸洗时间由钢铁表面状况而定,酸洗液成分及其工作规定、所用缓蚀剂种类、使用量参见附录A(参考件)。
5 酸洗后处理5.1 为减少带入冲洗槽的酸量,钢铁件从酸洗槽中取出后可在酸洗槽上方短暂停留,以滴去钢铁件上残存在大部分酸液。
5.2 经酸洗后的钢铁件需用洁净水在常温至80℃的温度下进行充分清洗。
为保持酸洗后钢铁件的表面状况,水洗后的钢铁件还需马上按涂装要求进行中和、磷化或钝化。
磷化按GB6807进行。
5.3 经酸洗后处理的钢铁件,要等到安全干燥后方能堆放,并要尽快进行涂装,以防再次被污染。
6 槽液的管理6.1 应定期检查酸洗槽液的变化情况,其铁离子含量不得超过下表的规定。
酸液种类铁离子含量,%m/m硫酸 6盐酸 10其他 66.2 为保证酸洗后钢铁的清洗质量要保证洗洗槽中酸和盐的积累总量不得超过0.2%m/。
7 酸洗后表面状况如供需双方无其他协定,经酸洗和后处理过的钢铁件表面状况应符合附录B(参考件)的要求。
高温锰系磷化处理

高温锰系磷化处理简介磷化(Phosphating)是将金属表面形成一层有机磷化合物的防锈涂层的技术。
钢铁材料通过磷化处理产生的膜层是不光滑的,由于不同材料的表面情况不同,因此其结构也有所不同。
磷化原理磷酸盐是磷化反应的主要原料。
在酸性条件下,含有磷酸盐的物质与金属表面产生反应。
在磷化反应中,磷酸盐对金属表面发生氧化-还原反应,生成以磷酸盐为主的磷化膜,从而起到防锈和增加摩擦力等作用。
高温锰系磷化处理高温锰系磷化处理是一种特殊的磷化技术,它一般都运用在高温、高压并且有化学反应的重载条件下,使金属表面生长出一层坚韧耐磨、抗磨损、防腐蚀、不导电、耐碱强、化学稳定的无机膜层。
该技术的处理方法:在弱酸性溶液中加入适量的金属磷化剂和与其同步脱氢的金属盐类、金属离子和某些添加剂,并将金属工件浸泡在这种溶液中,通入适量的氧气,反应温度控制在 200~350℃(取决于所需要的磷化层的厚度,温度越高越容易形成较厚的磷化层),处理时间一般为 1 ~ 3 小时。
经这种磷化处理后,金属表面形成了磷化膜层,该膜层是由金属磷化剂与金属表面磷化共生成的金属磷化物,其基本成分为 Mn2O3、Fe2O3、Zn3(P(PO4)2)2和Mn3(PO3)2等物质,具有橙红、灰色或黑色外观。
该膜层能够很好地保护基体金属,提高了金属的耐腐蚀性、耐磨损性、防滑性和润滑性等性能。
应用领域高温锰系磷化处理技术的应用范围很广,主要用于制造重载机械设备、精密电子部件、汽车零部件、石化设备和液压元件等需要具备高度耐磨和耐腐蚀性的领域。
此外,该技术还可以应用在制造其他具有耐磨、耐腐蚀、不导电、化学稳定等要求的物品上,如医疗器械、太阳能电池、半导体材料、水处理设备等。
结论高温锰系磷化处理是一种特殊的磷化技术,对金属材料的防锈和增加摩擦力等性能方面有很好的提升。
该技术的应用领域很广泛,包括制造以及其他需要具备高度耐磨和耐腐蚀性的领域。
虽然该技术的处理方法较为复杂,但是其优点显而易见,具有广泛的应用前景和发展空间。
磷化作业指导书

磷化作业指导书1 范围《接箍磷化作业指导书》规定了《API Spec 5CT 套管和油管规范》中所包含的各类油管、套管接箍的磷化工艺规程及为保证其可追溯性在生产过程中需要填写的质量表格。
2 规范性参考标准API Spec 5CT 第九版套管和油管规范GB/T 11376—1997 金属的磷酸盐转化膜GB 6807-2001<<钢铁工件涂前磷化处理技术条件>>GB 2828-2003<<逐批检查计数抽样程序及抽样表>>3 磷化工艺公司采用钢铁用锰系覆膜剂 RD-3601 是使钢铁表面形成高耐蚀性磷酸锌覆膜的药剂,适用于浸渍法。
经RD-3601处理得到的覆膜均匀、粘着性好。
由于是吸油性的覆膜,加之涂以防锈油,上蜡或施行涂装,能够得到非常理想的防锈性。
3.1 工艺方案如下:3.1.1工艺流程:→→→→→→→本工艺流程规定了金属前处理的内容:1、材料的选择;2、工艺条件及工艺参数;3、槽液配制方法(以1000 L计);4、槽液的检测方法;5、槽液调整与添加;6、对生产工艺的要求。
3.1.1.1材料的选择:选用:(1)FC-4360S除油剂(2)RD-3601磷化液(3)SJ1901硬模防锈油3.1.1.2工艺条件及工艺参数:(1)除油(浸渍法)产品型号: FC-4360S除油剂配比: 2%碱度: 15~18pt温度: 50~65℃时间: 5~15min(视工件表面油污程度而定)(2)水洗(溢流)产品型号: 新鲜自来水PH 值: 6~8温度: 常温时间: 1~3min(3)除锈产品型号: 工业盐酸(HCL含量30-33%)使用配比:13-17%,即55%工业盐酸(HCL含量30-33%)﹢新鲜自来水45%(配槽按各组分液体重量、比例进行添加)使用温度: 常温处理时间: 10-30min(视工件锈蚀程度及氧化皮而定)(4)水洗(溢流)产品型号: 新鲜自来水PH 值: 6~8温度: 常温时间: 30 S~1min(5)磷化产品型号: RD-3601磷化液配比: 4.7%总酸度: 12Pt~27Pt游离酸度: 5~10pt酸比:4~6温度: 70~99℃时间: 10~20min(视膜的厚度与颜色而定)(6)水洗(溢流)产品型号:新鲜自来水PH 值:6~8温度:常温时间:30 S~1min(7)脱水防锈油封(浸渍)产品型号:SJ1901硬模防锈油配比:原液温度:常温时间:10~30 S油封处理时要抖动,使盲孔充分得到处理3.1.1.3槽液配制方法1、除油槽(按1000 L计):(1)在除油槽中加水至配槽液总量的4/5体积刻度线,加温到约40℃;(2)将FC-4360S除油剂20Kg慢慢加入,边搅拌边溶解;(3)补充水至1000 L,同时搅拌均匀槽液;(4)加温到50~65℃;(5)浸渍5~15 min2、除锈槽(按1000 L计):(1)在除锈槽中加水450 L;(2)将450 L的工业盐酸(含量为30-33%)缓缓加入槽中,使其充分稀释,将槽液缓缓搅拌20min左右(搅拌过程中应严防酸液外溅),30min后即可使用。
汽车行业金属表面处理油箱磷化工艺技术条件
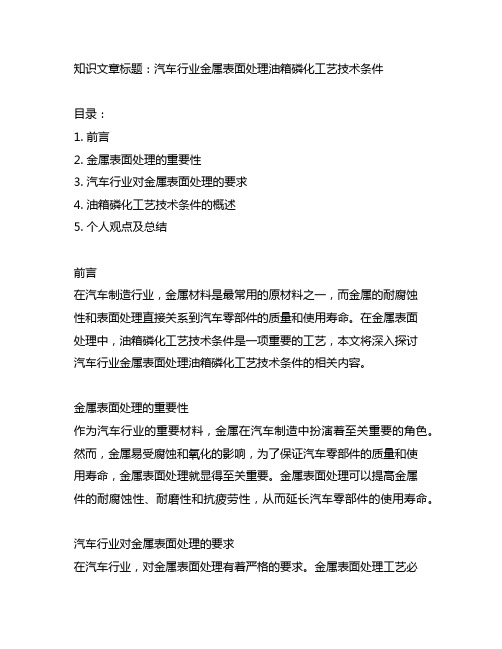
知识文章标题:汽车行业金属表面处理油箱磷化工艺技术条件目录:1. 前言2. 金属表面处理的重要性3. 汽车行业对金属表面处理的要求4. 油箱磷化工艺技术条件的概述5. 个人观点及总结前言在汽车制造行业,金属材料是最常用的原材料之一,而金属的耐腐蚀性和表面处理直接关系到汽车零部件的质量和使用寿命。
在金属表面处理中,油箱磷化工艺技术条件是一项重要的工艺,本文将深入探讨汽车行业金属表面处理油箱磷化工艺技术条件的相关内容。
金属表面处理的重要性作为汽车行业的重要材料,金属在汽车制造中扮演着至关重要的角色。
然而,金属易受腐蚀和氧化的影响,为了保证汽车零部件的质量和使用寿命,金属表面处理就显得至关重要。
金属表面处理可以提高金属件的耐腐蚀性、耐磨性和抗疲劳性,从而延长汽车零部件的使用寿命。
汽车行业对金属表面处理的要求在汽车行业,对金属表面处理有着严格的要求。
金属表面处理工艺必须符合环保要求,不能对环境造成污染。
金属表面处理后的零部件要符合汽车整车的设计要求,既保证产品的性能,又要符合美观要求。
金属表面处理必须能够提高零部件的耐腐蚀性,延长产品的使用寿命。
油箱磷化工艺技术条件的概述油箱磷化是指将金属表面以磷酸盐的形式进行钝化处理,形成一层致密、均匀、规则的磷化膜。
这种薄膜具有良好的耐蚀性和耐磨性,并且对燃料有一定的阻隔作用,可以有效地保护油箱不受腐蚀。
油箱磷化工艺技术需要满足一定的工艺条件,包括磷化溶液的配方、工艺温度、磷化时间等方面的要求。
个人观点及总结通过本文的了解,我对汽车行业金属表面处理油箱磷化工艺技术条件有了更深入的理解。
在汽车制造中,金属表面处理不仅关系到产品的质量和使用寿命,还关系到环境保护和消费者的安全。
油箱磷化工艺技术条件作为金属表面处理的重要一环,必须满足环保要求、产品性能要求和设计要求,才能在汽车行业得到广泛应用。
总结回顾:本文深入探讨了汽车行业金属表面处理油箱磷化工艺技术条件的重要性和相关要求,使我对这一主题有了全面、深刻和灵活的理解。
磷化简介

磷化简介磷化是金属材料防腐蚀的重要方法之一,其目的在于给基体金属提供防腐蚀保护、用于喷漆前打底、提高覆膜层的附着力与防腐蚀能力及在金属加工中起减摩润滑作用等。
按用途可分为三类:1、涂装性磷化 2、冷挤压润滑磷化 3、装饰性磷化。
按所用的磷酸盐分类有:磷酸锌系、磷酸锌钙系、磷酸铁系、磷酸锌锰系、磷酸锰系。
根据磷化的温度分类有:高温(80 ℃以上)磷化、中温(50~70 ℃)磷化、低温磷化(40 ℃左右)和常温磷化( 10~30 ℃)。
一、磷化成膜机理磷化主要有以下过程:(1)金属的溶解过程即金属与磷化液中的游离酸发生反应:M+H3PO4 = M(H2PO4)2+H2↑(2)促进剂的加速过程为:M(H2PO4)2+Fe+[O]→M3(PO4)2+FePO由于氧化剂的氧化作用,加速了不溶性盐的逐步沉积,使金属基体与槽液隔离,会限制甚至停止酸蚀的进行。
(3)磷酸及盐的水解磷化液的基本成分是一种或多种重金属的酸式磷酸盐, 其分子式为Me(H2PO4)2,这些酸式磷酸盐溶于水,在一定浓度及pH值下发生水解,产生游离磷酸:Me(H2PO4)2=MeHPO4+H3PO43MeHPO4=Me3(PO4)2+H3PO4H3PO4=H2PO4-+H+= HPO2-4 + 2H+ =PO3-4 + 3H+由于金属工件表面的H+浓度急剧下降,导致磷酸根各级离解平衡向右移动,最终成为磷酸根。
(4 ) 磷化膜的形成当金属表面离解出的PO3-4与磷化槽液中的金属离子Zn2+、Mn2+、Fe2+达到饱和时,即结晶沉积在金属工件表面,晶粒持续增长,直到在金属工件表面生成连续不溶于水的牢固的磷化膜:3M2 + + 2PO3 -4 + 4H2O = M3 ( PO4 ) 2·4H2O ↓2 M2 + + Fe2 + + 2PO3 -4 + 4H2O= M2 Fe ( PO4 ) 2· 4H2O金属工件溶解出的Fe2+一部分作为磷化膜的组成部分被消耗掉,而残留在磷化槽液中的Fe2+则氧化成Fe3+,生成FePO4沉淀,即磷化沉渣的主要成分之一。
紧固件磷化处理一般性技术条件

紧固件磷化处理技术条件1 磷化处理目的磷化处理目的是改善螺栓(螺柱)与螺母、螺母与垫圈间的摩擦,防止螺栓(螺柱)与螺母咬死。
磷化处理还能形成保护层,但必须涂油存放。
2 工艺规程的制定螺栓(螺柱)、螺母和垫圈的基体材料应为碳钢或低合金钢。
螺栓(螺柱)、螺母和垫圈的内外表面均应采用磷酸锰进行磷化处理。
磷化处理前应制定相应的工艺规程,规程中包含冲洗、活化、磷化、钝化、检查以及重新磷化时应进行脱磷处理等过程,并在操作中严格实施。
3 磷化处理前的准备在磷化处理以前,零件应紧密衔接地进行除油、去除氧化物和热水冲洗。
冲洗热水的温度为60~80℃。
4 磷化处理4.1 零件磷化前应进行表面活化处理。
4.2 磷化处理后,螺栓(螺柱)、螺母和垫圈的所有表面应形成5~10μm的磷化层。
零件磷化处理后,应立即进行冲洗和钝化:——在流动冷水中冲洗;——在磷酸铬中钝化1~2min,钝化温度为50~70℃;——用热空气吹干,或在80~110℃的烘箱中干燥,最少5分钟。
5 检验5.1 外观检查零件干燥后,应对所有零件进行100%目视检查,灯光照明度应≥500勒克司。
磷化膜应具有均匀、完整、光洁、致密(细小结晶组织)的灰黑色外观,不允许有裸点、过磷化或表面疏松存在。
5.2 抗腐蚀性检验用指示剂滴于磷化膜上,当温度在15~20℃时,指示剂由天蓝变成浅绿、黄色或红色的时间在3分钟以上为合格。
每槽抽查5%,但不少于1件。
如检验不合格,允许加倍抽检,如再不合格,则该槽零件视为不合格。
指示剂配方为:硫酸铜(0.4N的溶液)40毫升,氯化钠(10%溶液)20毫升,盐酸(0.1N 的溶液)0.8毫升。
5.3 结合力检验用白布擦拭零件表面,如无落灰,即认为膜表面层不存在疏松。
5.4 厚度检验对同一批磷化处理的螺栓(螺柱)、螺母和垫圈各设一个见证件,用显微检验的方法在非螺纹处检查磷化层厚度。
5.5 脱氢处理目视检查合格后,极限抗拉强度大于1450MPa的钢件应在100℃±5℃的温度下保温8小时进行脱氢处理。
- 1、下载文档前请自行甄别文档内容的完整性,平台不提供额外的编辑、内容补充、找答案等附加服务。
- 2、"仅部分预览"的文档,不可在线预览部分如存在完整性等问题,可反馈申请退款(可完整预览的文档不适用该条件!)。
- 3、如文档侵犯您的权益,请联系客服反馈,我们会尽快为您处理(人工客服工作时间:9:00-18:30)。
钢铁工件涂漆前磷化处理技术条件本标准适用于钢铁工件涂漆前的磷化处理•经处理所形成的磷化膜用作油漆底层,以增强漆膜与钢铁基体的附著力及防护性,提高钢铁工件的涂漆质量•1.磷化膜分类磷化膜按其重量及用途的分类见表1.分类膜重G/M2膜的组成用途次轻量级0.2〜1.0主要由磷酸铁,磷酸钙或其他金属的磷酸盐所组成.用作较大形变钢铁工件的油漆底层.轻量级1.1〜4.5主要由磷酸锌和(或)他金属的磷酸盐所组成.用作油漆底层次重量级4.6〜7.5主要由磷酸铁和(或)其他金属的磷酸盐所组成.可用作基本不发生形变钢铁工件的油漆底层重量级>7.5主要由磷酸铁,磷酸锰和(或)其他金属的磷酸盐所组成.不作油漆底层2.技术要求2.1待处理的工件应符合下列要求:2.1.1无特别规定时,工件的机械加工,成型,焊接和打孔应在处理前完成.2.1.2工件的表面质量应符合技术文件的规定.2.2工件的热处理特殊用途的零件,应在磷化处理前消除应力及处理后消除氢脆.2.3前处理2.3.1工件表面的油污,锈及氧化皮可用一枫中国庶科人]或几种方法清理.2.3.2脱脂后的工件,不应有油脂,乳浊液等污物,其表面应能被水完全润湿.2.3.3酸洗后工件,不应有目视可见的氧化物,锈及过腐蚀现象,其表面应色泽均匀.2.3.4喷抛丸清理后的工件,不应有漏喷,磨料粘附,锈蚀及油污,其表面应露出金属本色2.4磷化处理2.4.1磷化处理的主要施工方法可采用浸渍法, 喷淋法或浸喷组合的方法进行.2.4.2对于轻度油污或锈蚀的工件, 可以采用前处理和磷化或采用脱脂, 除锈, 磷化和钝化一步法进行.2.4.3磷化处理可以在以锌, 锰, 锌钙, 碱金属, 其他金属或氨的磷酸二氢盐为主要成分的溶液中进行.2.4.4磷化槽液的配制, 调整及管理应按工艺规定的要求进行.2.4.5盛装磷化液的槽体材料或衬里材料应耐磷酸盐腐蚀, 所有制作磷化设备的材料或接触槽液的材料应不影响磷化液及损害磷化膜质量.2.4.6工件表面生成的磷化膜应符合2.6, 2.7, 2.8 ,2.9条的技术要求.2.5 后处理2.5.1为了提高磷化膜的耐腐蚀性能, 水洗后磷化工件建议在铬酸, 重铬酸盐或其他类型的钝化液中进行钝化.2.5.2磷化或钝化后的工件, 一般情况下应进行水洗, 为了提高工件表面的清洗质量, 可采用脱离子水作最终水洗.2.5.3最终水洗后的工件, 一般需干燥后方可涂漆.2.5.4为了防止工件表面被污染或重新锈蚀, 干燥后应尽快的涂漆.2.5.5磷化与涂漆间隔一般不超过16H, 对特殊的加工工序及特殊的零件可适当延长间隔时间, 但此期间的工件表面不得被污染或重新锈蚀.2.6磷化膜外观2.6.1磷化后工件的颜色应为浅灰色到深灰色或彩色, 膜层应结晶致密, 连续和均匀.2.6.2磷化后的工件具有下列情况或其中之一时, 均为允许缺陷.2.6.2.1轻微的水迹, 重铬酸盐的痕迹, 擦白及挂灰现象.2.6.2.2由于局部热处理, 焊接以及表面加工状态的不同而造成颜色和结晶不均匀.2.6.2.3在焊缝的气孔和夹渣处无磷化膜.2.6.3磷化后的工件具有下列情况之一时, 均为不允许缺陷.2.6.3.1疏松的磷化膜层.2.6.3.2有锈蚀或绿斑.2.6.3.3局部无磷化膜(焊缝的气孔和夹渣处除外).2.6.3.4表面严重挂灰.2.7磷化膜重量按附录A(补充件)测定的磷化膜重量,应符合表1•所列数值,磷化膜厚度与重量的换算关系参考附录C(参考件).2.8磷化膜耐蚀性能按3.3条规定的方法检验磷化膜耐蚀性能时:2.8.1浸渍法: 经1H, 基体金属不应现出锈蚀(棱边, 孔, 角及焊缝处除外).2.8.2点滴法: 可作为工序间磷化膜质量的快速检验.2.9漆膜耐蚀性能按3.4 条规定的方法检验漆膜耐蚀性能时: 锌盐, 锰盐, 锌钙盐磷化膜涂漆试样经24H 耐盐雾试验后, 铁盐磷化膜的涂漆试样8H 耐盐雾试验收后, 除划痕部位处, 漆膜应无起泡, 脱落及生锈等现象.注: 划痕部位系指划痕任何一测的附近宽度0.5MM 内.3.检验方法3.1外观检验在天然光或混合照明条件下, 用目视检查, 天然光照度要求不小于100lx, 采光系数最低值为2%, 混合照明的光照度要求不小于500lx.3.2磷化膜重量测定法经过2.3, 2.4条及2.5.1 款处理并干燥的试样, 按附录A 规定的方法测定膜层重量.3.3磷化膜耐蚀性能检验331浸渍法:将工件或试样(已降至室温)浸入3%的氯化钠(NaCl)的水溶液中,在15-25E 下, 保持规定的时间, 取出工件或试样, 随时之洗净, 吹干, 目视检查磷化表面是否出现锈蚀.333点滴法:磷化膜耐蚀性能的点滴法检验见附录D(参考件)3.4漆膜耐蚀性能检验.3.4.1经2.3 2.4条及2.5.1款处理并干燥后的磷化试样,按GB1765-79<<测定耐湿热,耐盐雾, 耐候性(入工加速)的漆膜制备法>>中第3 条制板方法的规定, 喷涂一层厚度为25-35um 的A04-9 白色氨基烘漆, 室温干燥30min, 再放入恒温鼓风烘箱中, 要温度102-107C下烘2h,干燥后的试样,用石蜡和松香1:1的混合物或性能较好的自干漆封边, 封孔, 在室外温下置放24h, 待试.3.4.2制备后的试样, 用18 号缝纫机针将漆膜划成长2cm 的交叉对角线(划痕深至钢铁基体, 对角线不贯穿对角, 对角线端点与对角成等到距离), 取试样三片, 划痕面朝上, 而后的将试样置于符合GB-1771-79V<漆膜耐盐雾测定法>>的盐雾试验箱中,按其规定的试验条件连续试验.3.4.3检查时, 取出试样, 用自来水冲净试样表面上所沉积的盐分, 冷风快速吹干(或毛巾, 滤纸吸干), 目视检查试样表面.4 验收规则4.1工件磷化后的质量检验包括外观, 磷化膜重量, 磷化膜耐蚀性能及漆膜耐蚀性能检验.4.2外观检验验收按下列规定:4.2.1大工件和重要工件应100%进行检验并逐一验收.4.2.2一般工件(包括小工件或小零件)可按GB 2828-81<逐批检查度数抽样程序及抽样表>抽样检验验收,检验规则见附录B(补充件).4.3测定磷化膜重量时, 在受试的三个平行试样的平均值不合格, 则再取三件进行复验, 若其平均值仍不合格, 则该批产品为不合格.4.4磷化工件由于数量, 尺寸及形状不能按规定的方法进行耐蚀性能检验时, 应按下列方法之一制作试样.4.4.1从实际工件切取一部分.4.4.2用与工件相同的材料长宽为70*150mm 的试样与工件同时进行处理.4.5磷化膜耐蚀性检验时,应从每批工件中抽取三件试样进行检验, 其中有一件不合格则再取双倍试样进行复验.若仍有一件不合格, 则采用4.7 条的规定进行检验并以其结果为准4.6磷化膜重量及漆膜耐蚀性能检验为抽验,应在下列情况之一时进行:4.6.1新设计投产的产品.4.6.2企业规定的周期检验.4.6.3设备, 工艺或槽液配方改变.4.6.4其他认为必要时的检验.4.7漆膜耐蚀性能检验时, 在受试的三个试样中, 其中有一个试样不合格, 则再取双倍试样复验,若仍有一个试样不合格, 则该批产品为不合格.附录A磷化膜重量测定法(补充件)本方法适用于钢铁表面生成的磷化膜单位面积重量的测定A.1 一般规定A.1.1 仪器1.容器: 玻璃的或其他适当材料的容器.2.分析天平: 感量为0.1mg.3.加热设备: 用于控制退膜液的温度.A.1.2 试样试样的总表面积应尽可能的大, 膜重小于1g/m2 的试样的总表面积不应小于300cm2, 膜重1-10g/m2 的试样的总表面积不应小于200cm2.A.1.3 试剂退膜溶液, 应由分析纯试剂和蒸馏水制备.A.2 测定方法将试样用分析天平称量准确0.1mg, 再浸入下表规定的退膜溶液中, 取出后立即用自来水冲洗, 然后用蒸馏水冲洗, 迅速干燥再称重.重复本操作, 直至得到一个稳定的重量为止.磷化膜类型退膜液组成分工作条件材料名称含量时间温度磷酸锌膜氢氧化钠乙二胺四乙酸四钠盐三乙醇胺100904 15 65-75磷酸铁膜, 磷酸锰膜, 磷酸锌膜及磷酸锌钙膜等. 三氧化铬50 15 70-80注: 配制退膜液时, 先用少量水将试剂溶解, 财用水稀释至1L.A.3 计算方法磷化膜单位面积膜层重量W 按下式计算: W={(P2-P1)/S}*10 式中: W 膜重量,g/m2.P1 ----- 退除磷化膜后试样的重量, mg.--- 磷化后试样的重量,mg.P2S ------ 磷化试样的总表面积, cm2.取三个平行测定试样的平均值.附录B磷化膜外观检验规则(补充件)本规则适用于一般工件磷化后外观检验.B.1 磷化膜的外观检验应符合GB 2828-81<<逐批检查计数抽样程序及抽样表>>的有关规定.B.2 缺陷分类: 磷化膜的外观缺陷分为轻缺陷及重缺陷. 2.6.2 款中允许缺陷属于轻缺陷而2.6.3 款式中的缺陷属于重缺陷.B.3 外观检查时, 一般根据磷化膜的外观颜色及膜层质量进行验收, 以有无重缺陷来判断合格或不合格, 轻缺陷一般不用于判断合格或不合格.B.4 逐批检查采用一次抽样方案, 初次检查为正常检查, 其缺陷类型, 合格质量水平及检查水平接下表的规定:缺陷类型重缺陷检查项目第2.6.3.1, 2.6.3.2, 2.6.2.3, 及2.6.3.4项合格质量水平(APL)0.25检查水平n附录C磷化膜厚度和单位面积膜层重量的换关系(参考件)磷化膜厚度(um)和单位面积膜层重量(g/m2)的换算关系见下表厚度,um单位面积膜层重.g/m21-213 3-65 5-1510 10-3015 15-45注: 1. 次轻量级磷化膜重量与厚度之比约为1.2.轻量级磷化膜重量与厚度之比1-2.3.磷化膜重量与厚度之比一般在1-3 之间.附录D点滴法(参考件)本方法适用于稳定性生产中, 工序间磷化膜耐蚀性能的快速检验D.1'检验溶液的成份和含量硫酸铜CuSO4.5H2O 41g/l.氯化钠NaCl 35g/l0.1N 盐酸HCl 13ml/l注: 1. 检验溶液应使用化学纯试剂和蒸馏水配制.2.溶液在5-35C下有效期限为一周.D.2 检验方法在15-23E下,磷化表面滴一滴检验溶,同时启动秒表,观察滴液从天兰变为浅黄色或淡红色的时间.D.3 验收标准点滴法用作工序间磷化膜质量的快速检验, 其变色时间由供需双方商定.。