硫酸法烷基化装置腐蚀机理与防腐对策研究
硫酸烷基化工艺腐蚀分析及应对措施研究

硫酸烷基化工艺腐蚀分析及应对措施研究
硫酸烷基化工艺是一种重要的化工生产方法,但同时也存在着一些腐蚀问题。
本文将分析硫酸烷基化工艺中可能存在的腐蚀问题,并提出相应的解决措施。
硫酸烷基化工艺涉及到硫酸的使用,硫酸具有很强的腐蚀性。
在生产过程中,硫酸可能会与设备和管道内壁接触,导致设备和管道的腐蚀。
硫酸还可能与其他金属离子或化合物形成酸性环境,加速设备和管道的腐蚀。
针对硫酸的腐蚀问题,可以采取以下应对措施:
1. 选择耐腐蚀材料:在设计和选择设备和管道时,应优先选择耐腐蚀材料,例如高合金钢,不锈钢等。
这些材料具有较强的抗硫酸腐蚀能力,可以有效延长设备和管道的使用寿命。
2. 强化涂层保护:在设备和管道内壁涂覆一层耐腐蚀的涂层,可以防止硫酸直接接触设备和管道的金属表面,减少腐蚀的发生。
常用的涂层材料包括聚氨酯涂层、环氧涂层等。
3. 控制工艺条件:在硫酸烷基化工艺中,通过控制工艺条件,如温度、压力和流速等参数,可以减少硫酸对设备和管道的腐蚀。
降低硫酸的浓度和温度,减少腐蚀的程度。
4. 定期维护和检修:对设备和管道进行定期的维护和检修,及时清除设备和管道内的污垢和腐蚀产物,可以减少腐蚀的发生。
定期检查设备和管道的腐蚀情况,及时更换受损的部件,保证设备和管道的正常运行。
针对硫酸烷基化工艺中的腐蚀问题,可以通过选择耐腐蚀材料、强化涂层保护、控制工艺条件和定期维护和检修等措施来解决。
这些措施可以有效降低腐蚀的发生,延长设备和管道的使用寿命,保障硫酸烷基化工艺的安全生产。
硫酸烷基化工艺腐蚀分析及应对措施研究

硫酸烷基化工艺腐蚀分析及应对措施研究
硫酸烷基化工艺是一种重要的有机合成工艺,广泛应用于合成烷基酸、烷基磺酸盐、烷基苯、烷基醚等有机化合物。
在硫酸烷基化过程中,腐蚀问题一直是一个困扰工艺安全和设备寿命的难题。
本文将从腐蚀分析与应对措施两个方面进行研究。
进行腐蚀分析是理解和解决腐蚀问题的关键。
硫酸烷基化过程中常使用的材料有不锈钢、碳钢、玻璃钢等。
这些材料在硫酸烷基化过程中都可能受到腐蚀的影响。
常见的腐蚀形式有酸蚀、缝隙腐蚀、应力腐蚀等。
酸蚀是硫酸烷基化过程中最常见的腐蚀形式之一。
硫酸可以与金属表面形成一层氧化膜,但在酸性条件下,硫酸可以侵蚀金属表面,导致金属损失、设备破损甚至泄漏。
缝隙腐蚀是指在金属板与密封垫之间形成的缝隙处,硫酸能够渗入缝隙中,引起金属表面的腐蚀破坏。
应力腐蚀是指金属在应力作用下发生腐蚀,导致金属的破裂。
由于硫酸的强腐蚀性,上述腐蚀形式在硫酸烷基化过程中可能同时存在。
在腐蚀问题出现之后,应采取相应的应对措施来解决问题。
选择耐腐蚀的材料是最基本的应对措施。
如使用耐酸不锈钢或陶瓷材料制造设备,可以有效防止腐蚀。
对设备进行防腐处理也是一种有效的手段。
如对设备表面进行涂层处理,形成一层保护膜来抵御硫酸的腐蚀。
定期进行设备维护和检修也是重要的措施。
及时发现设备表面的腐蚀问题,采取修复措施,可以延长设备的使用寿命。
硫酸烷基化工艺中的材料腐蚀问题是一个需要引起重视的难题。
通过腐蚀分析、选择耐腐蚀材料、设备防腐、定期维护等措施可以有效应对这一问题,保障工艺安全和设备寿命。
烷基化装置硫酸腐蚀与措施
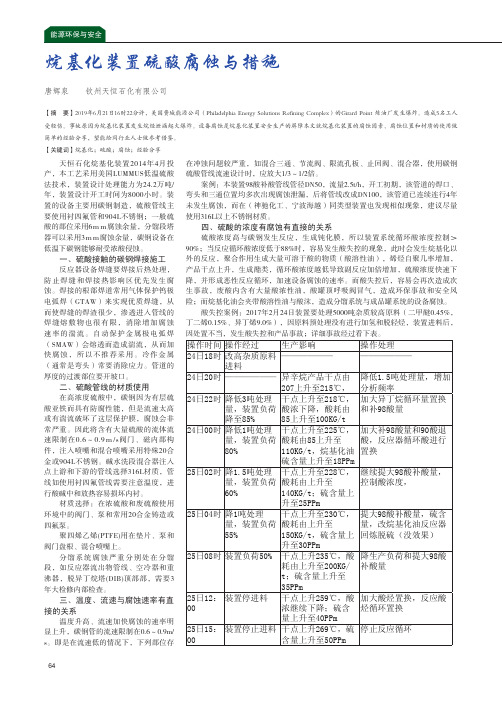
64天恒石化烷基化装置2014年4月投产,本工艺采用美国LUMMUS低温硫酸法技术,装置设计处理能力为24.2万吨/年,装置设计开工时间为8000小时。
装置的设备主要用碳钢制造,硫酸管线主要使用衬四氟管和904L不锈钢;一般硫酸的部位采用6mm腐蚀余量,分馏段塔器可以采用3mm腐蚀余量,碳钢设备在低温下碳钢能够耐受浓酸侵蚀。
一、硫酸接触的碳钢焊接施工反应器设备焊缝要焊接后热处理,防止焊缝和焊接热影响区优先发生腐蚀。
焊接的根部焊道常用气体保护钨极电弧焊(GTAW)来实现优质焊缝,从而使焊缝的焊渣很少,渗透进入管线的焊缝熔敷物也很有限,消除增加腐蚀速率的湍流。
自动保护金属极电弧焊(SMAW)会熔透而造成湍流,从而加快腐蚀,所以不推荐采用。
冷作金属(通常是弯头)常要消除应力。
管道的厚度的过渡部位要开坡口。
二、硫酸管线的材质使用在高浓度硫酸中,碳钢因为有层硫酸亚铁而具有防腐性能,但是流速太高或有湍流破坏了这层保护膜,腐蚀会非常严重。
因此将含有大量硫酸的流体流速限制在0.6~0.9m/s阀门、磁内部构件,注入喷嘴和混合喷嘴采用特殊20合金或904L不锈钢。
碱水洗段混合器注入点上游和下游的管线选择316L材质,管线如使用衬四氟管线需要注意温度,进行酸碱中和放热容易损坏内衬。
材质选择:在浓硫酸和废硫酸使用环境中的阀门、泵和常用20合金铸造或四氟泵。
聚四烯乙烯(PTFE)用在垫片、泵和阀门盘根、混合喷嘴上。
分馏系统腐蚀严重分别处在分馏段,如反应器流出物管线、空冷器和重沸器,脱异丁烷塔(DIB)顶部部,需要3年大检修内部检查。
三、温度、流速与腐蚀速率有直接的关系温度升高、流速加快腐蚀的速率明显上升,碳钢管的流速限制在0.6~0.9m/s。
即是在流速低的情况下,下列部位存烷基化装置硫酸腐蚀与措施唐辉泉 钦州天恒石化有限公司【摘 要】2019年6月21日16时22分许,美国费城能源公司(Philadelphia Energy Solutions Refining Complex)的Girard Point 炼油厂发生爆炸。
硫酸烷基化工艺腐蚀分析及应对措施研究

硫酸烷基化工艺腐蚀分析及应对措施研究硫酸烷基化工艺是工业生产中常见的一种化工生产工艺,其在石化、化肥、农药等行业有着广泛的应用。
在硫酸烷基化过程中,常常会遇到腐蚀问题,腐蚀严重影响了设备的使用寿命和生产效率。
对硫酸烷基化工艺腐蚀分析及应对措施的研究具有重要意义。
一、硫酸烷基化工艺腐蚀分析1. 腐蚀原因分析在硫酸烷基化工艺中,腐蚀主要是由于以下几个原因引起的:(1)介质腐蚀:硫酸烷基化反应中使用的介质中含有大量的硫酸、酸性离子等腐蚀性物质,这些物质可能对设备材料产生腐蚀作用。
(2)温度腐蚀:硫酸烷基化反应需要在一定的温度下进行,高温环境会加剧设备的腐蚀情况。
(1)表面腐蚀:设备表面出现腐蚀斑点、锈蚀等现象。
(2)局部腐蚀:设备的某些局部受到腐蚀,出现孔洞、腐蚀凹陷等情况。
(3)材料疲劳:长期腐蚀会导致设备材料疲劳、脆化,降低了设备的使用寿命。
针对硫酸烷基化工艺中的腐蚀问题,需要进行腐蚀评价分析,根据设备材料、反应条件等因素进行腐蚀风险评估,确定腐蚀程度和影响范围,为后续的防腐措施提供重要依据。
1. 材料选择在硫酸烷基化工艺中需要选择耐酸性能好的材料,如不锈钢、镍基合金、耐酸塑料等,以提高设备的耐腐蚀性能。
2. 表面处理对设备进行表面处理,如镀锌、喷涂耐酸涂料等,提高设备表面的抗腐蚀能力。
3. 设备设计在设备设计过程中,考虑对腐蚀性介质的隔离,减少介质对设备的腐蚀作用。
4. 防腐涂层5. 监测与维护定期对设备进行腐蚀情况的监测和维护,发现问题及时进行修复和更换,延长设备的使用寿命。
6. 新技术应用引进新技术,如防腐蚀合金材料、防腐蚀涂料等,提高设备的耐腐蚀性能。
三、结语硫酸烷基化工艺腐蚀问题是工业生产中常见的难题,为了保证生产设备的安全运行和生产效率的提高,必须加强对硫酸烷基化工艺腐蚀分析及应对措施的研究。
针对硫酸烷基化工艺中的腐蚀问题,必须做好材料选择、设备设计、防腐涂层等工作,同时加强对设备腐蚀情况的监测和维护,引进新技术应用,从源头上预防腐蚀问题的发生。
硫酸法烷基化装置腐蚀及防护分析
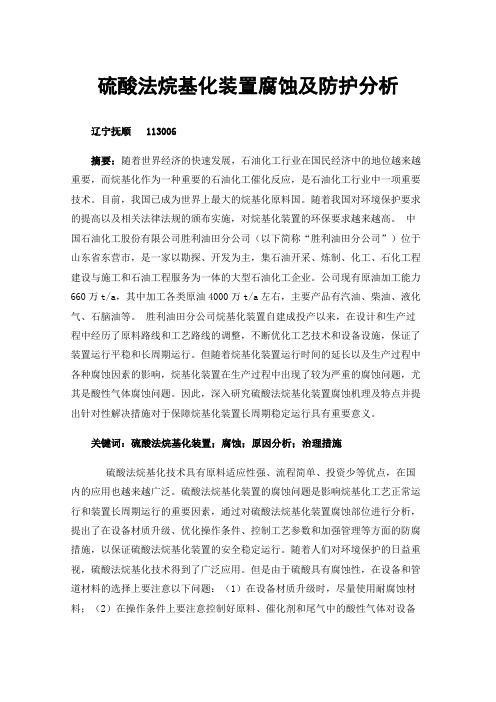
硫酸法烷基化装置腐蚀及防护分析辽宁抚顺 113006摘要:随着世界经济的快速发展,石油化工行业在国民经济中的地位越来越重要,而烷基化作为一种重要的石油化工催化反应,是石油化工行业中一项重要技术。
目前,我国已成为世界上最大的烷基化原料国。
随着我国对环境保护要求的提高以及相关法律法规的颁布实施,对烷基化装置的环保要求越来越高。
中国石油化工股份有限公司胜利油田分公司(以下简称“胜利油田分公司”)位于山东省东营市,是一家以勘探、开发为主,集石油开采、炼制、化工、石化工程建设与施工和石油工程服务为一体的大型石油化工企业。
公司现有原油加工能力660万t/a,其中加工各类原油4000万t/a左右,主要产品有汽油、柴油、液化气、石脑油等。
胜利油田分公司烷基化装置自建成投产以来,在设计和生产过程中经历了原料路线和工艺路线的调整,不断优化工艺技术和设备设施,保证了装置运行平稳和长周期运行。
但随着烷基化装置运行时间的延长以及生产过程中各种腐蚀因素的影响,烷基化装置在生产过程中出现了较为严重的腐蚀问题,尤其是酸性气体腐蚀问题。
因此,深入研究硫酸法烷基化装置腐蚀机理及特点并提出针对性解决措施对于保障烷基化装置长周期稳定运行具有重要意义。
关键词:硫酸法烷基化装置;腐蚀;原因分析;治理措施硫酸法烷基化技术具有原料适应性强、流程简单、投资少等优点,在国内的应用也越来越广泛。
硫酸法烷基化装置的腐蚀问题是影响烷基化工艺正常运行和装置长周期运行的重要因素,通过对硫酸法烷基化装置腐蚀部位进行分析,提出了在设备材质升级、优化操作条件、控制工艺参数和加强管理等方面的防腐措施,以保证硫酸法烷基化装置的安全稳定运行。
随着人们对环境保护的日益重视,硫酸法烷基化技术得到了广泛应用。
但是由于硫酸具有腐蚀性,在设备和管道材料的选择上要注意以下问题:(1)在设备材质升级时,尽量使用耐腐蚀材料;(2)在操作条件上要注意控制好原料、催化剂和尾气中的酸性气体对设备和管道的影响;(3)在保证原料和催化剂纯度的同时,减少尾气中酸性气体对设备和管道的腐蚀。
硫酸烷基化工艺腐蚀分析及应对措施研究

硫酸烷基化工艺腐蚀分析及应对措施研究硫酸烷基化是一种重要的化工生产工艺,但也存在一定的腐蚀问题。
本文就硫酸烷基化工艺的腐蚀问题进行分析,并提出相应的应对措施。
1. 腐蚀症状硫酸烷基化过程中,腐蚀主要表现为设备内部的腐蚀和管道的腐蚀。
设备内部的腐蚀主要表现为反应釜内壁和底部的腐蚀,而管道的腐蚀则表现为管道内壁的腐蚀和管道连接处的腐蚀。
腐蚀症状主要包括:(1)设备内壁和底部出现磨损、毛刺和凸起。
(2)管道内壁出现腐蚀坑和凹陷,管道连接处出现漏气现象。
(3)设备和管道表面出现斑点、腐蚀颜色不同等。
2. 腐蚀原因硫酸烷基化过程中,腐蚀主要是由于以下原因所引起的:(1)化学腐蚀:硫酸极具腐蚀性,因此在硫酸烷基化过程中难免产生化学腐蚀。
(2)机械磨损:在反应釜内部,由于反应物之间的剧烈反应以及搅拌器的搅拌作用,会导致设备内部的机械磨损,从而产生腐蚀。
(3)温度和压力:硫酸烷基化需要在高温高压下进行,高温和高压会使设备产生应力变形,从而大大降低了设备的抗腐蚀能力。
3. 应对措施为了解决硫酸烷基化过程中的腐蚀问题,需要采取相应的应对措施,包括:(1)选择合适的材料:在原材料的选择上,应尽量选用耐腐蚀的材料。
例如,采用不锈钢、玻璃钢等材料制造设备和管道,这些材料可以有效提高设备和管道的耐腐蚀性能。
(2)合理的维护保养:对设备和管道进行定期的维护保养,使用防腐材料进行修补和涂层处理,有效延长设备和管道的使用寿命。
同时,应注意设备和管道的清洗,避免在清洗过程中对设备和管道造成二次损伤。
综上所述,硫酸烷基化工艺腐蚀问题的解决需要采取一系列的应对措施,包括选择合适的材料、合理的维护保养和严格控制温度和压力等。
通过这些措施,可以有效保护设备和管道,延长设备和管道的使用寿命。
低温硫酸法烷基化装置设备防腐对策
低温硫酸法烷基化装置设备防腐对策摘要:本文结合装置实际设计和生产,针对低温硫酸法烷基化工艺进行了介绍,根据工艺中所产生的硫酸腐蚀、碱腐蚀、硫腐蚀、垢下腐蚀、保温层下腐蚀进行了原因分析,并根据腐蚀原因和腐蚀机理制定相对应的设备选型策略及工艺防腐措施。
关键词:低温法硫酸烷基化、硫酸腐蚀、碱腐蚀、硫腐蚀、保温层下腐蚀乌鲁木齐石化公司炼油厂烷基化装置是由烷基化单元与废酸再生单元两部分构成的联合装置,由中国石油工程建设有限公司华东设计分公司设计。
烷基化单元采用鲁姆斯公司的 CDAlky 低温硫酸法烷基化技术。
主要是以MTBE装置提供的未反应碳四馏分、加氢裂化液化气、轻烃分离液化气为原料,主要利用液化气中的碳四烯烃和异丁烷,在浓硫酸催化剂的作用下,烯烃与异丁烷反应,生成烷基化油。
烷基化油的特点是辛烷值高,调和性能好,蒸汽压低,有理想的挥发性和燃烧性能,是理想的高辛烷值调和组分,其不含烯烃和芳烃,是清洁燃料。
1 低温硫酸法烷基化工艺介绍烷基化装置是以MTBE装置提供的未反应碳四馏分、加氢裂化液化气、轻烃分离液化气为原料,主要利用液化气中的碳四烯烃和异丁烷,在浓硫酸(98%浓度的硫酸)催化剂的作用下,烯烃与异丁烷反应,生成烷基化油;副产正丁烷和丙烷。
装置主要由原料聚结脱水、烷基化反应、产物聚结分离、压缩制冷、脱丙烷塔、烷基化产品分馏和含酸尾气洗涤等几部分组成。
其中反应部分主要是在催化剂的作用下,异丁烷和丁烯反应生成烷基化油,制冷部分是在压缩机的作用下,利用反应产物中大量的异丁烷减压汽化吸收热量,维持反应在低温液相下进行,同时为反应系统提供足够的循环冷剂,保证低温进料和反应器的分子比;流出物经过聚结器将反应生成的烷基化油与酸分离,脱酸后的烷基化油经过脱异丁烷塔、脱正丁烷塔和再蒸馏塔分离出异丁烷、正丁烷和最终产物异辛烷的过程。
2 低温硫酸法烷基化装置产生腐蚀的原因分析根据上面的烷基化工艺介绍,可以看出,硫酸法烷基化装置的腐蚀形态会非常复杂,存在多种样式,被腐蚀风险较大的设备较多,主要表现在酸腐蚀、亚硫酸腐蚀、碱应力腐蚀、氢腐蚀、硫腐蚀、垢下腐蚀、冲刷腐蚀、露点腐蚀以及保温层下腐蚀等。
硫酸烷基化工艺腐蚀分析及应对措施研究
硫酸烷基化工艺腐蚀分析及应对措施研究【摘要】本文针对硫酸烷基化工艺中常见的腐蚀问题进行了深入分析和研究,通过对腐蚀机理、影响因素及应对措施进行论述,总结了现有研究进展。
在腐蚀问题日益凸显的情况下,对腐蚀控制和预防提出了有效的解决方案。
通过本文的研究,可以更好地认识硫酸烷基化工艺中腐蚀问题的本质和特点,为相关行业提供技术支持和参考。
未来的研究方向包括进一步探索腐蚀机理、开发新型抗腐蚀材料以及提高腐蚀控制技术水平,以实现对硫酸烷基化工艺腐蚀问题的更好预防和处理。
【关键词】硫酸烷基化工艺、腐蚀、分析、应对措施、研究背景、研究意义、腐蚀机理、影响因素、常见问题、研究进展、成果总结、未来展望。
1. 引言1.1 研究背景硫酸烷基化工艺是一种常见的化工生产方法,广泛应用于石油化工、合成染料、医药和农药等领域。
随着生产规模的不断扩大和生产条件的复杂化,硫酸烷基化工艺在实际生产中面临着严重的腐蚀问题。
在硫酸烷基化工艺中,金属设备受到硫酸和烷基物所引起的腐蚀威胁,容器、管道和阀门等设备往往存在着腐蚀的风险。
腐蚀不仅会降低设备的使用寿命,还会导致设备的安全隐患和生产事故的发生。
研究硫酸烷基化工艺腐蚀问题及应对措施具有重要意义。
通过对硫酸烷基化工艺腐蚀机理的深入分析,可以更好地了解腐蚀过程中的原理和规律,为腐蚀问题的预防和控制提供科学依据。
探讨硫酸烷基化工艺中常见的腐蚀问题及应对措施,可以有效减少生产中的腐蚀损失,提高设备的稳定性和可靠性。
对硫酸烷基化工艺腐蚀问题的研究具有重要的现实意义和应用价值。
1.2 研究意义硫酸烷基化工艺在化工生产中具有重要的应用价值,能够实现烷基化反应,提高产物的附加值。
随着工艺规模的扩大和生产条件的变化,硫酸烷基化工艺腐蚀问题逐渐凸显出来。
腐蚀问题不仅会影响设备的正常运行,还会危及生产安全,导致生产事故的发生。
研究硫酸烷基化工艺腐蚀分析及应对措施具有重要的意义。
通过对硫酸烷基化工艺腐蚀进行深入研究,可以更好地了解腐蚀机理,找出影响腐蚀的因素,提出有效的应对措施,为化工生产提供技术支撑和保障。
硫酸烷基化工艺腐蚀分析及应对措施研究
硫酸烷基化工艺腐蚀分析及应对措施研究硫酸烷基化工艺是一种在精细化学品生产中广泛使用的化学反应过程,但随着工艺的推广应用,其腐蚀问题日益显著。
针对硫酸烷基化工艺的腐蚀问题,本文进行了相关分析并提出了相应的应对措施。
硫酸烷基化反应过程中存在着许多影响腐蚀的因素,如进料质量、反应温度、反应物浓度、气体流量、反应容器材质等。
其中,温度是影响腐蚀的最主要因素。
反应温度高于170℃时,硫酸烷基化反应会产生大量的硫酸酰烷基,硫酸酰烷基能形成极具腐蚀性的硫酸。
此外,硫酸烷基化反应中的反应物也会影响腐蚀性。
含有醇类反应物的硫酸烷基化反应会产生较高浓度的氯化氢,而氯化氢对不锈钢等材质很容易产生腐蚀作用。
此外,不同反应物的比例也会对腐蚀性产生影响,比如甲苯与氯化硫酸反应的比例过高,会使腐蚀速度加快。
针对硫酸烷基化工艺的腐蚀问题,我们可以从以下方面采取应对措施:1、选择合适材质在硫酸烷基化反应中,由于反应物的不同组合会导致生成的化学物质不同,其对材质的腐蚀程度也不同。
因此,在选择精细化学品生产中的反应容器时,应根据化学反应类型与条件来选用适应性良好的材质,如碳钢、316L不锈钢、锆合金等。
2、控制反应温度反应温度是影响硫酸烷基化反应腐蚀的最主要因素。
降低反应温度可以减少产生的硫酸酰烷基浓度,进而减缓腐蚀的速度。
因此,在生产过程中应控制反应温度在170℃以下。
同时,将硫酸酰烷基排放到处理设备中,在排放前进行稀释也可以减轻腐蚀问题。
3、加入缓蚀剂在反应中加入适当的缓蚀剂,能起到减缓、抑制腐蚀的作用。
常用的缓蚀剂有咪唑类缓蚀剂和卡宾类缓蚀剂等。
4、加强清洗与维护及时清洗反应容器、保养设备,以及设立检测系统进行监测,都能帮助尽早发现、处理反应容器内壁存在的腐蚀问题。
此外,设立防腐涂层也是一种有效的预防措施。
5、规范生产操作生产操作的规范化,能最大程度地避免人为因素引发的安全事故。
在硫酸烷基化反应中,要求合格的操作技术员、表明化学物质的标识、采用个人防护措施等,也有助于减少潜在风险。
硫酸烷基化工艺腐蚀分析及应对措施研究
硫酸烷基化工艺腐蚀分析及应对措施研究硫酸烷基化工艺是一种重要的有机合成工艺,在某些化工行业中得到广泛应用。
这种工艺在实际应用中容易出现腐蚀问题,特别是对于设备和管道,导致设备寿命缩短、工作效率下降以及生产安全风险增加。
对硫酸烷基化工艺的腐蚀进行分析和研究,并采取相应的应对措施,对于提高工艺的稳定性和安全性具有重要意义。
对硫酸烷基化工艺的腐蚀进行分析。
硫酸烷基化过程中常用的反应物是硫酸和烷基化剂,这些反应物具有一定的腐蚀性。
在硫酸溶液中,一些金属如铁、铜、镍等容易发生腐蚀反应,导致设备和管道的金属材料受损。
硫酸的酸性也使得设备和管道的非金属材料受到侵蚀,例如橡胶密封件、塑料管道等。
腐蚀是硫酸烷基化工艺中无法忽视的一个重要问题。
针对硫酸烷基化工艺的腐蚀问题,可以采取如下的应对措施:1.材料选择:选择具有良好耐腐蚀性的材料用于设备和管道的制作,例如不锈钢、玻璃钢、聚丙烯等。
避免选用容易受腐蚀的金属材料。
2.涂层保护:在金属表面涂覆一层抗腐蚀涂层,如橡胶、聚酯等材料的涂层,可以起到防腐蚀的作用。
涂层的选择应根据具体的工艺条件和腐蚀介质进行合理选择。
3.防腐措施:加入适量的缓蚀剂或者缓蚀剂体系,如硝酸铜、碳酸钠等,可以减少腐蚀速率,提高设备和管道的抗腐蚀性能。
定期进行设备和管道的维修和检测,及时发现和处理腐蚀问题。
4.工艺改进:通过改进硫酸烷基化工艺,减少腐蚀介质的作用时间和浓度,可以降低腐蚀风险。
优化反应条件、改变反应器结构等,可以减少腐蚀反应的发生。
需要强调的是,腐蚀分析和应对措施的研究是一个多方面的工作,需要综合考虑工艺条件、设备材料、腐蚀介质等因素的影响。
只有在腐蚀分析的基础上制定出科学合理的防腐措施,才能提高硫酸烷基化工艺的安全性和可靠性,保障生产过程的顺利进行。
- 1、下载文档前请自行甄别文档内容的完整性,平台不提供额外的编辑、内容补充、找答案等附加服务。
- 2、"仅部分预览"的文档,不可在线预览部分如存在完整性等问题,可反馈申请退款(可完整预览的文档不适用该条件!)。
- 3、如文档侵犯您的权益,请联系客服反馈,我们会尽快为您处理(人工客服工作时间:9:00-18:30)。
硫酸法烷基化装置腐蚀机理与防腐对策研究摘要硫酸法烷基化装置腐蚀问题是困扰装置长周期安全稳定运行的重要因素。
本文从硫酸腐蚀出发,研究硫酸腐蚀机理、碳钢在硫酸条件下腐蚀曲线等方面,结合装置现场腐蚀及防腐情况,对现场重点腐蚀部位及腐蚀原因进行分析,提出防腐措施并对部分已实施防腐措施进行评估论述,提出系统的防腐措施建议。
关键词硫酸;烷基化;腐蚀机理;防腐中图分类号TE986文献标识码 A烷基化油由于其具有高辛烷值,不含硫、氮、芳烃或烯烃等优点,是一种环保、清洁的组分汽油。
硫酸法烷基化装置是目前较成熟的生产工艺,在硫酸法烷基化装置中,烯烃和异丁烷在浓硫酸催化下生成烷基化油,但其硫酸腐蚀问题一直是困扰装置长周期安全稳定运行的制约条件。
某石化硫酸法烷基化装置自2013年10月检修投产后,装置始终面临着硫酸系统腐蚀问题。
因此,研究硫酸法烷基化酸系统的腐蚀机理,找出相应防腐策略是一项急需解决的问题。
1硫酸的理化特性及腐蚀机理1.1 硫酸的主要理化性质及腐蚀特点纯硫酸是一种无色油状液体,密度1.84g/ml,结晶温度为10.36℃,能与水任意比互溶,形成不同浓度的硫酸溶液,而不同浓度的硫酸表现不同特性。
浓硫酸同时具备酸性、强氧化性、吸水性等特性;稀硫酸主要表现为其酸性,能与多数金属与金属氧化物发生反应。
硫酸腐蚀环境几乎包含所有位置,在大部分环境中硫酸起腐蚀主导作用,也有部分环境中硫酸起加剧腐蚀作用。
硫酸的腐蚀伴随着温度、浓度的变化呈现出不同的性质,不同杂质的组分与含量对腐蚀的影响也有所不同。
1.2 影响硫酸腐蚀的主要因素影响硫酸腐蚀速率的主要因素包括硫酸的浓度、温度与杂质的含量,与其他酸腐蚀不同的是,流速对于腐蚀速率也有很大的影响[1]。
1.2.1 硫酸浓度对腐蚀的影响稀硫酸中有大量H+,大多数工业金属或合成金属在H+环境中发生化学腐蚀与电化学腐蚀,表面迅速被均匀的溶解并生成相应金属离子与H2。
稀硫酸腐蚀表现仅为其酸性,而浓硫酸不仅仅具有酸性特征,同时还具有强氧化性特征,对于金属腐蚀表现出不同的特性。
由于硫酸不同浓度表现出不同性质,因此硫酸浓度对于腐蚀的影响巨大,一般而言,中等浓度硫酸酸性最强,同时还有一定的氧化性,因而对金属的腐蚀性最强。
98%以上的发烟硫酸腐蚀性要弱的多,硫酸浓度每升高1%,腐蚀速率可降低约10倍。
而不同材质在硫酸环境中的腐蚀速率也不尽相同,通常使用等腐蚀速率曲线来表示其腐蚀特性。
因此,根据不同材质腐蚀特性来控制硫酸浓度是防腐蚀的一项重要举措。
1.2.2 温度对腐蚀的影响一般情况下,硫酸对金属的腐蚀随着温度的提高而加剧,但也有一些例外,一些金属在极浓硫酸中、某些温度范围内的腐蚀速率最小,本文主要讨论硫酸烷基化装置中的硫酸腐蚀,没有这种例外条件,故不做讨论。
因此,控制硫酸的温度是降低硫酸腐蚀的一条重要措施,但由于浓硫酸在低温时易出现结晶现象,所以控制防腐温度需进行考虑。
1.2.3 杂质对腐蚀的影响硫酸中的不同杂质对于其腐蚀性有较大的影响。
硫酸中含有SO32-和Cl-等还原性物质时,对材料的腐蚀一般是有害的,尤其是氯化物和氟化物会使金属在硫酸中钝化变得异常困难。
硫酸中含Cl-后,即使是耐腐蚀性能较强的哈氏合金,其耐腐蚀性也呈现较明显的降低。
硫酸中含有Na2SO4、K2SO4等硫酸盐可提高其导电性,使腐蚀速率略有增强。
由此可见,控制硫酸中杂质的含量,对控制腐蚀速率也较为重要。
1.2.4 流速对腐蚀的影响硫酸流速对腐蚀的影响较为复杂,取决于不同材料的性能与其所处的环境,与酸浓度、温度、杂质含量等有极为重要的联系。
一般而言,硫酸流速对金属的腐蚀影响本质是材料表面保护膜耐冲刷能力的强弱,在表面膜破坏之前,流速增加对腐蚀速率影响较小;当流速达到一定速度,可以使保护膜破坏时,腐蚀速率将会随着流速的增加急速加剧。
硫酸在低速环境中呈现均匀腐蚀状态,而在高速环境中,腐蚀加剧,且呈现局部腐蚀特性。
不同介质中高低速分界点如表1。
表1 不同介质中高低速分界点序号材质低速高速1碳钢<0.6m/s≥0.6m/s2不锈钢<1.2m/s≥1.2m/s3较高合金钢<1.8m/s≥1.8m/s同时,温度对于保护膜破坏起到至关重要的作用,通常随着温度的升高,使金属保护膜破坏的酸流速会有明显的下降;因此,讨论流速对腐蚀的影响时,要充分考虑温度等条件的影响。
在相同条件下,奥氏体不锈钢耐冲刷性能要比碳钢好得多。
2 硫酸对碳钢的腐蚀特性由于装置酸系统目前材质为碳钢(20#钢),因此本文主要研究硫酸对碳钢的腐蚀机理。
根据碳钢在硫酸中腐蚀曲线可知,碳钢在97%浓度的硫酸中腐蚀较慢,随着硫酸浓度降低,腐蚀速率呈现加快态势,在酸浓度87%左右时,腐蚀速率又随着酸浓度的下降逐渐降低。
在浓硫酸环境中,浓度为83%-90%的硫酸对碳钢的腐蚀速率最快。
硫酸对碳钢的腐蚀速率随着温度的升高呈现明显的升高状态,在50℃,85%浓度硫酸条件下,碳钢的腐蚀速率接近1.3mm/a,在75℃条件下,各浓度硫酸腐蚀速率均超过1.3mm/a。
硫酸对碳钢的腐蚀随着流速的加快腐蚀加剧,NACE的权威资料认为,碳钢用于98%的浓硫酸时,在常温下,流速要限制在0.6m/s以下,在实际生产操作时,一般流速要限制在0.4m/s以下。
根据碳钢在硫酸中腐蚀特性,在烷基化装置中需要控制硫酸的温度不能超过50℃、浓度尽可能高于90%、流速低于0.4m/s等条件。
同时,温度与流速对腐蚀速率的影响较大,在有条件的前提下尽可能降低硫酸温度与流速,但不能低于其结晶温度,可以根据等腐蚀曲线腐蚀速率0.5mm/a线来控制操作温度,从而控制腐蚀速率。
3 装置典型腐蚀位置及防腐措施根据API571及装置流程图,绘制装置腐蚀回路图,见图1。
根据腐蚀回路图及现场运行腐蚀情况,烷基化装置腐蚀主要是硫酸及酸脂分解产生的亚硫酸腐蚀[3],运行过程中常见腐蚀包括加酸、排酸系统腐蚀,进料、冷剂、流出物系统腐蚀,分馏系统腐蚀等几方面。
图1 某石化烷基化装置腐蚀回路图3.1 新酸、排酸系统腐蚀烷基化酸线系统腐蚀严重,主要有加酸线、排酸线及其酸系统阀门。
烷基化装置小流量加酸线腐蚀减薄严重,16年11月小流量加酸泵出口管线先后出现两次泄漏,其中泵出口缓冲器管段减薄严重,测厚计算腐蚀速率约为1mm/a。
小流量排酸线,酸包排酸线多次出现腐蚀泄漏,仅16年一年就先后出现3次泄漏,一次漏点为三通位置、两次漏点为弯头位置。
同时酸系统阀门内漏严重。
原因分析:(1)现场使用小流量加酸泵为隔膜柱塞泵,加酸线内硫酸流动不稳定,在往复压缩过程中有部分介质流速较快、腐蚀较严重。
泵出口缓冲器管段由于介质反复冲刷,减薄严重。
计算泵出口管线硫酸流速约为0.32m/s,由于泵为隔膜柱塞泵,判断实际局部流速有可能超过0.6m/s,导致腐蚀加剧。
(2)酸线伴热为热水伴热,温度过高,局部位置高温会加剧腐蚀。
(3)排酸线酸浓度较低,一般排酸浓度为90%左右,由于工艺操作等原因,部分时间排酸浓度会低于88%,酸腐蚀性加剧。
(4)排酸线局部冲刷加剧腐蚀:局部流速过快、湍流会加剧腐蚀速率。
从三次排酸线漏点判断,2次为弯头处,一次为三通处。
弯头与三通位置面临直接冲刷腐蚀,同时,弯头等位置存在焊口,管道内壁不平或存在焊渣等因素会导致焊口后部腐蚀急剧升高。
(5)部分阀门由于流量控制要求,闸阀开度小,流经闸阀的酸流速快、且存在局部湍流,对阀板、密封面腐蚀较严重针对此系统腐蚀情况,逐步对重点腐蚀位置进行优化改进:(1) 18年装置优化改造,加酸量由原1-1.2m3/h降低至0.7-0.8m3/h,硫酸流速降低至0.22 m/s,有效减缓腐蚀速率。
(2)将部分酸线伴热改为电伴热,降低局部高温可能性,进一步降低腐蚀可能性。
(3)对经常性泄漏的排酸线及阀门进行材质升级,材质升级为较为耐酸的904L不锈钢材质,耐蚀性能显著提高[4]。
(4)加强施工焊接质量控制,减少焊口内部存在局部不平整情况,减少局部湍流引起的腐蚀加剧。
(5)酸系统阀门改为无冲刷的全通径球阀,或更换为更加耐冲刷磨损的合金钢阀门,如904L,Alloy 20[5]。
3.2 反应进料、冷剂、流出物系统腐蚀烷基化进料管线由于结构设计问题,冷剂与进料线使用三通直接混合,存在冲刷与局部湍流,导致三通背部冲刷位置多次腐蚀泄漏。
通过在三通内部增加一个90度弯头,降低直接冲刷、减少湍流;同时装置优化操作,减少冷剂系统酸夹带。
改进后此位置腐蚀明显降低,管段自15年5月后至今未出现泄漏情况。
装置碱洗混合三通位置腐蚀,既有碱液冲刷导致的腐蚀,同时由于流出物夹带酸较多,又有酸碱中和过程中的局部稀酸腐蚀,同时由于循环碱液温度高,腐蚀难以避免。
针对此位置增加一个90度弯头后,腐蚀位置后移且腐蚀稍有减弱,但改造后仍出现三次腐蚀泄漏。
针对此位置,惠州炼化材质升级为Alloy20,但使用一年后也出现泄漏,后续材质升级为哈氏合金C276[6]。
碱洗混合三通位置腐蚀问题目前并没有好的彻底解决的办法,但减少流出物中酸夹带毫无疑问能直接降低此位置的腐蚀。
3.3 分馏系统腐蚀烷基化装置分馏系统腐蚀主要为塔底结垢与塔顶的腐蚀。
2016年烷基化装置检修时,塔底外送泵与塔底重沸器内部积垢严重,塔顶回流系统腐蚀较为严重,腐蚀状态为硫酸均匀腐蚀。
由于分馏系统塔底温度较高,正常操作120℃左右,塔底不含水,高温下硫酸、烷基化油以及反应产生的酸脂等发生分解和聚合,导致塔底重沸器积垢较严重,易产生垢下腐蚀情况[7],但分解产生的SO2将会对塔顶系统造成一定的腐蚀[8]。
对塔底重沸器垢样进行分析,其Fe、Na、SO42-含量分别仅有3.6%、0.074%与0.24%,结垢主要成分为有机聚合物。
分馏塔顶回流系统由于操作条件的原因,不可避免会有少量水与硫酸以及酸脂分解产生的SO2结合产生稀酸环境,导致顶回流系统均匀腐蚀。
分馏系统的腐蚀与结垢原因根本上是由于上游碱洗后流出物仍夹带少量酸、酸脂与水进入系统导致。
2018年烷基化优化改造,增加原料脱水、脱甲醇设施,改善反应物酸烃分离设备,增加碱洗后碱烃分离设备,流出物夹带酸量显著降低[9],至目前运行良好,未发现分馏系统有明显腐蚀迹象。
因此,避免酸夹带进入分馏系统是解决腐蚀的根本举措。
4 总结与展望根据硫酸腐蚀机理及影响腐蚀速率的条件,控制腐蚀应主要从酸浓度、温度、流速和杂质含量等方面进行,结合碳钢的等腐蚀曲线,目前烷基化装置酸系统的防腐应着重注意以下几点:(1)保证酸浓度,在同等条件下,浓度87%-97%的硫酸,随着酸浓度的升高腐蚀速率降低,尽可能提高操作酸浓度能有效防止酸腐蚀;(2)降低温度,在同等条件下,随着温度的升高,腐蚀速率急剧升高。
装置内部热水伴热改为电伴热,控制其操作温度在50℃以内,有条件的情况可以降低至20-30℃,能较大程度减缓腐蚀。