加氢裂化反应系统操作因素分析
加氢裂化装置反应器径向温差原因分析与探讨
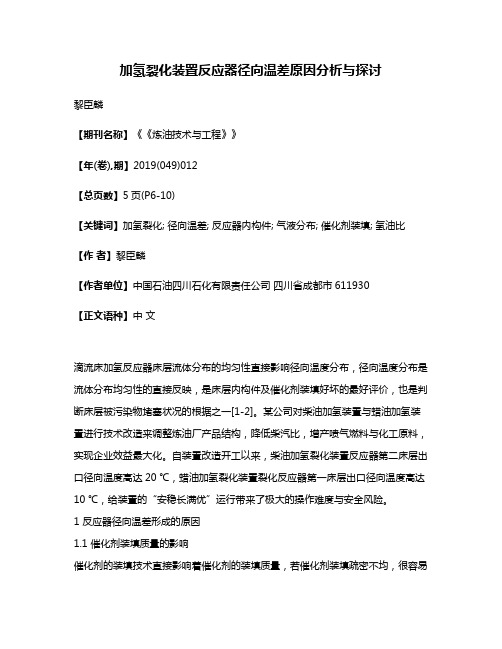
加氢裂化装置反应器径向温差原因分析与探讨黎臣麟【期刊名称】《《炼油技术与工程》》【年(卷),期】2019(049)012【总页数】5页(P6-10)【关键词】加氢裂化; 径向温差; 反应器内构件; 气液分布; 催化剂装填; 氢油比【作者】黎臣麟【作者单位】中国石油四川石化有限责任公司四川省成都市611930【正文语种】中文滴流床加氢反应器床层流体分布的均匀性直接影响径向温度分布,径向温度分布是流体分布均匀性的直接反映,是床层内构件及催化剂装填好坏的最好评价,也是判断床层被污染物堵塞状况的根据之一[1-2]。
某公司对柴油加氢装置与蜡油加氢装置进行技术改造来调整炼油厂产品结构,降低柴汽比,增产喷气燃料与化工原料,实现企业效益最大化。
自装置改造开工以来,柴油加氢裂化装置反应器第二床层出口径向温度高达20 ℃,蜡油加氢裂化装置裂化反应器第一床层出口径向温度高达10 ℃,给装置的“安稳长满优”运行带来了极大的操作难度与安全风险。
1 反应器径向温差形成的原因1.1 催化剂装填质量的影响催化剂的装填技术直接影响着催化剂的装填质量,若催化剂装填疏密不均,很容易造成物料“短路”或床层下陷,从而导致反应器内物料和温度分布不均匀、物料与催化剂接触时间不均匀[3]、反应器压力降不均匀,影响产品质量和催化剂寿命。
某蜡油加氢裂化装置反应器各床层出口温度分布见表1。
表1 某加氢裂化装置反应器各床层出口温度Table 1 Temperature distribution at the bed outlet of hydrocracking react or ℃项目中心点温度内圈直径1 600 mm温度中圈直径3 225 mm温度外圈直径4 040 mm温度温升径向温度径向温度/轴向温升精制反应器第一层378.0376.4375.4378.0377.2377.5376.1378.3377.7376.6375.1378.1376.4374. 220.54.10.2 第二层377.7378.4379.8380.6378.2379.2378.4381.1379.1378.3377.8379.4378.5378.48.13.30.41 第三层387.1388.1386.0387.8385.2386.2383.1389.8387.3388.6385.8382.9386.8388. 615.46.90.45续表1 ℃项目中心点温度内圈直径1 600 mm温度中圈直径3 225 mm温度外圈直径4 040 mm温度温升径向温度径向温度/轴向温升裂化反应器第一层378.5382.4382.0385.4379.3377.6381.4385.5379.3377.6381.4376.5378.5375. 31210.20.85 第二层382.2381.7379.3383.1383.0381.7380.9384.1382.2382.1382.1380.8379.7378. 512.75.60.44 第三层381.3380.2378.5379.9381.0379.7380.4382.6379.7379.3380.8381.1380.8380. 011.34.10.36 第四层382.9383.7382.1385.0386.6384.3384.2386.6388.0384.1382.6386.8383.0383. 316.25.90.36注:红色标注为最高温度,黄色标注为最低温度,精制反应器与裂化反应器直径都为4 800 mm从表1可以看出,精制反应器各床层出口最高温度都在反应器中心位置,第一、第二床层出口最低温度在直径4 040 mm位置,靠近反应器器壁;裂化反应第一、第二、第三床层出口最高温度在反应器中心位置,各床层出口最低温度在直径4 040 mm位置,靠近反应器器壁。
石油化工技术《加氢裂化主要影响因素》

我们知道,加氢裂化反响总体是个放热反响,而放出热量的多少与反响温度是有直接关系的。因为前面我们介绍过,提高反响温度,将会使反响速度加快,而加氢裂化反响又是个放热反响,因此释放出的反响热也会增加。如果这些反响热不能够及时的移走,将会进一步导致反响器内温度的升高,如此下去,将会形成恶性循环,导致催化剂床层温度骤然升高,也即工业上所说的飞温,其后果那么会使催化剂的寿命缩短,严重时可能会引起设备或管线的爆炸事故。因此,反响温度是加氢裂化过程须严格控制的操作参数。
一、反响压力的影响
〔小组讨论:压力增加对反响有何影响?教师总结〕
具体讲授:它是一个重要的操作参数,在加氢裂化过程中,反响压力的影响是通过氢分压来表达的。系统中的氢分压取决于操作压力、氢油比、循环氢纯度以及原料的汽化率。
提高氢分压有利于加快加ห้องสมุดไป่ตู้裂化的反响速度,提高反响物的转化率。同时,保持一定的反响压力,有利于提高催化剂对原料中多环芳烃和硫、氮、氧等非烃类化合物的氢解活性,从而改善产品的质量。另外,提高氢分压还有利于抑制不饱和烃的缩合反响,从而减缓催化剂的积炭速度,延长催化剂的使用周期。
但是,提高氢油比并不总是对反响有利的,比方氢油比增大,会使得单位时间内流过催化剂床层的气体量增加,流速加快,反响物在催化剂床层里的停留时间缩短,反响时间减少,不利于加氢反响的进行。同时,氢油比过大会导致系统的压降增大,动力消耗和投资就增加。所以氢油比并不是越大越好。
蜡油的加氢裂化反应
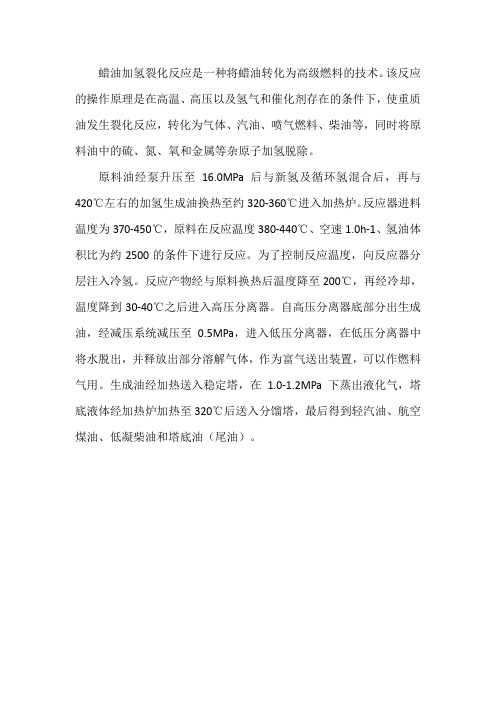
蜡油加氢裂化反应是一种将蜡油转化为高级燃料的技术。
该反应的操作原理是在高温、高压以及氢气和催化剂存在的条件下,使重质油发生裂化反应,转化为气体、汽油、喷气燃料、柴油等,同时将原料油中的硫、氮、氧和金属等杂原子加氢脱除。
原料油经泵升压至16.0MPa后与新氢及循环氢混合后,再与420℃左右的加氢生成油换热至约320-360℃进入加热炉。
反应器进料温度为370-450℃,原料在反应温度380-440℃、空速1.0h-1、氢油体积比为约2500的条件下进行反应。
为了控制反应温度,向反应器分层注入冷氢。
反应产物经与原料换热后温度降至200℃,再经冷却,温度降到30-40℃之后进入高压分离器。
自高压分离器底部分出生成油,经减压系统减压至0.5MPa,进入低压分离器,在低压分离器中将水脱出,并释放出部分溶解气体,作为富气送出装置,可以作燃料气用。
生成油经加热送入稳定塔,在1.0-1.2MPa下蒸出液化气,塔底液体经加热炉加热至320℃后送入分馏塔,最后得到轻汽油、航空煤油、低凝柴油和塔底油(尾油)。
加氢裂化催化剂反应机理

加氢裂化过程是在较高压力下,烃类分子与氢气在催化剂表面进行裂解和加氢反应生成较小分子的转化过程,同时也发生加氢脱硫、脱氮和不饱和烃的加氢反应。
其化学反应包括饱和、还原、裂化和异构化。
加氢裂化的反应机理是正碳离子机理,遵循β-断裂法则。
在双功能催化剂上,正碳离子的生成主要是通过不饱和烃在催化剂的酸性位获取质子而生成正碳离子;烷烃失去负离子生成正碳离子,当烷烃与正碳离子反应时,发生负氢离子转移,生成新的正碳离子。
此外,加氢裂化催化剂上的反应主要包括活性金属和酸性载体上的化学反应。
具体来说,活性金属表面上的硫化物和氮化物的氢解、芳烃加氢饱和、烯烃加氢饱和,以及在酸性载体上的环状化合物的开环、裂化、脱烷基、异构化反应。
至于具体的反应细节和步骤,建议查阅化学专业书籍或咨询化学专家,以获取更深入的了解。
同时,也应注意,在进行加氢裂化反应时,应严格遵守相关安全规定,确保人员安全和设备稳定。
加氢裂化反应影响因素
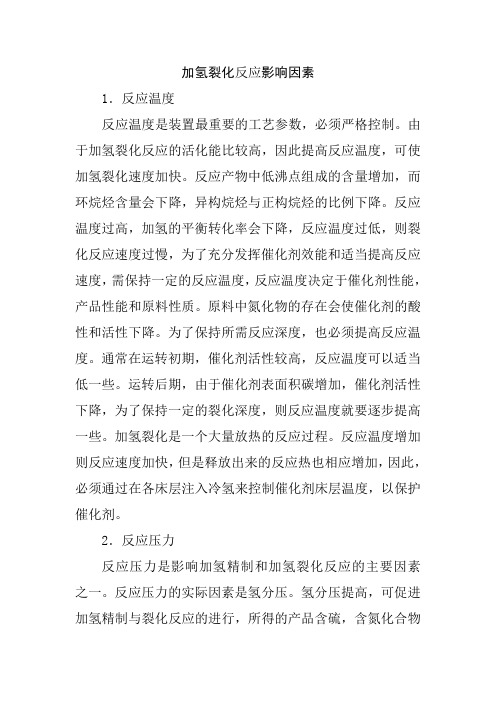
加氢裂化反应影响因素1.反应温度反应温度是装置最重要的工艺参数,必须严格控制。
由于加氢裂化反应的活化能比较高,因此提高反应温度,可使加氢裂化速度加快。
反应产物中低沸点组成的含量增加,而环烷烃含量会下降,异构烷烃与正构烷烃的比例下降。
反应温度过高,加氢的平衡转化率会下降,反应温度过低,则裂化反应速度过慢,为了充分发挥催化剂效能和适当提高反应速度,需保持一定的反应温度,反应温度决定于催化剂性能,产品性能和原料性质。
原料中氮化物的存在会使催化剂的酸性和活性下降。
为了保持所需反应深度,也必须提高反应温度。
通常在运转初期,催化剂活性较高,反应温度可以适当低一些。
运转后期,由于催化剂表面积碳增加,催化剂活性下降,为了保持一定的裂化深度,则反应温度就要逐步提高一些。
加氢裂化是一个大量放热的反应过程。
反应温度增加则反应速度加快,但是释放出来的反应热也相应增加,因此,必须通过在各床层注入冷氢来控制催化剂床层温度,以保护催化剂。
2.反应压力反应压力是影响加氢精制和加氢裂化反应的主要因素之一。
反应压力的实际因素是氢分压。
氢分压提高,可促进加氢精制与裂化反应的进行,所得的产品含硫,含氮化合物减少,更重要的是可减少结焦,保持催化剂活化,提高催化剂的稳定性。
反应器中的氢分压等于油汽加上循环氢的总压与氢气占全部气体分子数的乘积。
本装置补充氢纯度确定为99.9%。
从经济角度出发,不采用提高补充氢纯度的办法来提高氢分压。
3.氢油比氢油体积比有两种,其一是反应器入口的氢油比,其二是总冷氢油比。
反应器入口氢油比是每小时通过反应器内氢气(循环氢气+新氢)体积与每小时通过的原料油体积之比。
(单位为Nm3 /m3)。
总冷氢油体积比是每小时通入反应器的总冷氢气体积总和与每小时通过的原料油体积之比。
在加氢反应器中只有一部分氢气起反应。
大部分氢气仍以自由状态存在。
采用高氢油比,可提高氢分压,有利于传质和加氢反应的进行,在一定范围内防止油料在催化剂表面结焦。
蜡油加氢裂化装置氢耗的影响因素分析及措施

蜡油加氢裂化装置氢耗的影响因素分析及措施摘要:在炼油企业降耗增效的大形势下,降低氢耗对于降低加工成本尤为重要。
蜡油加氢处理装置的氢耗在加工成本中占很大比例。
为了降低蜡油加氢处理装置的氢耗,有必要分析其影响因素并提出改进建议,为车间节能生产提供参考。
基于此,对蜡油加氢裂化装置氢耗的影响因素分析及措施进行研究,以供参考。
关键词:新氢;反应温度;原料组分;溶解损失;转化率引言加热炉的燃料气消耗在炼油装置能耗中占有相当大的比例,少则20%~30%,多则80%~90%,加热炉技术水平及操作性能极大地影响着炼油装置的能源消耗水平。
因此,提高加热炉热效率,降低燃料气消耗,对降低能耗具有十分重要的意义。
1氢耗的影响因素1.1溶解损失在氢气循环过程中,一部分氢气会溶解在热高压分离器(简称热高压分离器)和冷高压分离器(简称冷高压分离器)的液相中,称为溶解损失。
相关研究文献指出,180℃和240℃的高温是两个拐点。
在80℃左右,循环氢的体积分数最低。
当温度高于180℃时,循环氢的体积分数随着温度的升高而逐渐增加。
当温度超过240℃时,循环氢体积分数的增加趋势减缓。
考虑到循环氢浓度和设备的承受能力,装置的高温应为240℃~260℃。
对于高冷含量,降低操作温度有利于提高氢气纯度,但温度过低和高压空冷器、高压换热器负荷过重会导致能耗过高。
综合考虑,冷高分操作温度应控制在45℃~55℃。
1.2压力控制装置的压力控制采用循氢机入口的压力控制器控制新氢返回量和循氢机入口分液罐顶排放循环氢来控制,这样可以有效控制系统压力,又可以对临氢系统的氢分压进行调节,这种方式避免了循环氢连续排放造成的氢气浪费。
1.3浓度一般钢材在水溶液中,浓度越高,越容易产生硫化物应力腐蚀开裂。
有日本资料报导:当水溶液中的浓度低于50~60ppm时,应力腐蚀开裂的可能性很低。
对任何一种钢,都存在一个浓度的门限值,超过此门限值都可发生应力腐蚀开裂。
Troiano曾对16Mn钢试样进行研究,考察常温下浓度对裂纹扩展的影响,试验结果表明,常温条件下,钢材内部裂纹扩展非常缓慢。
加氢裂化装置提高石脑油收率

加氢裂化装置提高石脑油收率1. 引言1.1 背景介绍近年来,随着能源需求的不断增长和石油资源的日益枯竭,石油加工技术的研究逐渐成为石油工业的热点之一。
石脑油是石油加工中重要的产品之一,其在化工、能源等领域有着广泛的应用。
传统的加工方法在提取石脑油方面存在着效率低、能耗高等问题,导致石脑油的收率较低。
为了解决这一问题,研究人员提出了利用加氢裂化技术来提高石脑油的收率。
加氢裂化是一种通过加氢作用对石油原料进行裂化反应的技术,可有效提高石脑油的产率和质量。
通过调整加氢裂化装置的参数和优化操作流程,可以最大限度地提高石脑油的收率,提高石油加工的效率和经济效益。
本文旨在探讨加氢裂化技术在提高石脑油收率方面的应用,分析加氢裂化装置的操作原理和影响因素,并提出针对性的优化方法,以期为石油加工行业提供有益的参考和借鉴。
【2000字】1.2 研究意义石脑油是一种重要的石油炼制产品,广泛应用于化工、能源等领域。
石脑油的产出对国家经济具有重要意义,因此提高石脑油收率一直是炼油行业的研究重点之一。
加氢裂化技术是提高石脑油收率的有效途径之一,通过在高温、高压、催化剂存在的条件下将重质石油馏分转化为轻质产品,提高石脑油的产量和质量。
研究加氢裂化装置对石脑油收率的影响具有重要的意义。
加氢裂化技术对石脑油收率的影响因素包括温度、压力、催化剂种类和加氢裂化装置参数等。
优化这些参数可以有效提高石脑油的收率,降低生产成本,提高经济效益。
本文旨在研究加氢裂化装置对石脑油收率的影响因素,并探讨加氢裂化技术在提高石脑油收率方面的应用前景,为炼油行业的发展提供理论支持和实践指导。
1.3 研究目的研究目的是通过加氢裂化技术提高石脑油的收率。
石脑油是一种重要的石油产品,其收率直接影响着炼油厂的经济效益。
目前,石脑油的生产面临着一些挑战,如原料质量不稳定、设备老化等问题,导致产量和质量波动较大。
研究加氢裂化装置技术,优化工艺参数,提高石脑油收率,具有重要的意义。
影响高压加氢裂化尾油质量因素分析

烃量越高, 碳原子相近 的多环烷烃 的加氢裂化速 度低 于 带烷 基 芳烃 , 同时 , 料油 馏 分 越重 , 子 原 分
结构 复 杂的芳香 杂 环 氮化 物 比例增 加 , 响芳 烃 影 加氢 饱 和反应 和加 氢 裂化 性 能 , 出的 尾油 质 量 产 下 降 。所 以对加 氢裂化 原料 油馏分 范 围的控 制是 控制 尾油 质量 的一个重 要手 段 。 表 1 高压加 氢裂化 原料 油不 同窄馏 分对
烃在进行加氢裂化反应 时经选择断环后 , 主要集
收稿 日期 :09一I 2 。 20 I一 0 作者简介 : 春林 , 师,97年毕业于江苏石油化学院化 蒋 工程 1 9 工工艺专业, 现在扬子石油化工有限公 司生产技术 和运行调 度部从事技术管理工作 。
率越高 。因此 , 探讨 调节加氢裂化尾油质量的方 法也就是探讨调节尾油 B C 值的方法。 MI
l 8
A VN D A A
细
石
油
化
工
进
展
CES I F NE E OCH EM I AL N I P TR C S
… 1一… … 第 l 卷第 3期
中在石 脑 油 馏 分 和 中 间 馏 分 中 , 响 尾 油 B 1 影 MC
系, 可直接 影响尾 油 的族组 成 , 6 当3 0℃ 以上馏 分
况, 需要同时兼顾 生产高芳潜 石脑油 和低 B C MI
值 的乙烯裂 解原 料 , 尽可 能选 择 中间基 原油 。 应
2 1 2 原料 油馏分 范 围的控 制 ..
式中, t 平 均沸 点 ; ——
d —相 对密 度 。 —
- 1、下载文档前请自行甄别文档内容的完整性,平台不提供额外的编辑、内容补充、找答案等附加服务。
- 2、"仅部分预览"的文档,不可在线预览部分如存在完整性等问题,可反馈申请退款(可完整预览的文档不适用该条件!)。
- 3、如文档侵犯您的权益,请联系客服反馈,我们会尽快为您处理(人工客服工作时间:9:00-18:30)。
加氢裂化反应系统操作因素分析
1.1反应系统
1.1.1反应温度
反应温度是控制脱S脱N率和生成油转化率的主要手段。
在己选定催化剂和原料油的情况下,温度的影响最为重要,因为在正常的生产条件下,系统压力、新H2纯度变化不会很大,氢油比也是基本恒定的,所以温度也就成为最有效的控制手段。
对于R1001,加氢精制段平均反应温度按照精制油中氮含量要求加以控制调整,要求调整到R1001流出油中有机氮≤1Oppm。
提高反应温度,加快加氢速度,可提高脱S脱N 率,烯烃的饱和程度亦提高,产品安定性好。
为裂化反应创造条件。
催化剂床层温升控制在25-30℃以寻求在提高催化剂的整体利用效率和降低炉子负荷、节省装置能耗上的平衡,达到装置的操作成本最低化。
对于R1002,加氢裂化段平均反应温度按照单程转化率要求加以控制调整,提高反应温度可使裂化反应速度加快,原料的裂化程度加深,生成油中低沸点组分含量增加,气体产率增高。
提高反应温度对产品化学组成有明显影响,正构烷烃含量增加,异构烷烃含量降低,异烷/正烷的比值下降。
催化剂床层温升控制在8-12℃以寻求在产品分布合理、装置温度
操作安全方面的平衡。
另外,从减少冷氢用量,从而减少循环氢压缩机负荷、减低装置投资和操作成本考虑,加氢精制反应器出口温度与加氢裂化反应器入口温度之差应尽量减小,从装置操作安全性上考虑,此温度差不得高于20℃。
反应温度的提高会使催化剂表面积炭结焦速度加快,影响其寿命。
所以,温度条件的选择一般受催化剂活性、操作温度限定值、产品分布等诸多因素的影响。
通常在催化剂活性允许的条件下,采用尽可能低的反应温度,为补偿催化剂结垢的影响,反应温度随开工周期的延长将逐步提高。
催化剂床层温度是反应部分最重要的工艺参数。
其它工艺参数对反应的影响,可用调整催化剂床层温度来补偿。
R1001的温度催化剂活性下降时,所有反应器需要较高的温度。
(稳定状态)操作参数的相互关系。
这些数据对均衡情况下温度调整时判断某些参数的变化是十分有用的。
本装置是按60万吨/年的生产能力设计的(如果改为一次通过,可达80万吨/年的规模),每台反应器装有符合装置能力所要求的催化剂量。
因此,在与设计进料率相应的同一条件下,当进料量减少时,则催化剂的用量就显得富裕,工艺参数也就不能在这同一条件下操作,我们把这种情况称做低空速。
为了避兔过量转化,在这种条件下需要降低催化剂床层温度。
我装置在实际生产中,可能存在低空速问题,要
根据转化率变化,及时调整催化剂床层温度。
1.1.2.反应压力
反应压力的实际因素是氢分压。
反应压力的选择与处理和原料性质有关,原料中含多环芳烃和杂质越多,则所需的反应压力越高。
在确定装置压力等级时主要从原料油性质、转化率、预计的反应温度和体积空速的匹配、产品质量要求等方面加以综合考虑;由于装置进料中含减四线和DAO,而且减四和DAO两股物料占总进料的26~38m%,混合原料馏程的50%馏出温度高达469︒C,95%馏出温度已达577︒C,干点超过600︒C。
这种原料油已经不是我们通常认为的“常规高压加氢裂化装置原料”,如果要求在70%以上的高转化率下运转,宜在高压下操作。
提高系统的氢分压,可促使加氢反应的进行,烯烃和芳烃的加氢速度加快,脱S、脱N率提高,对胶质、沥青质的脱除有好处。
故所得产品的溴价低,含S、含N化合物少,油品安定性好,同时还可防止或减少结焦,有利于保持催化剂活性。
反应器入口H2分压用下式求得:
[循环气中氢分子数+新氢中分子数]
氢分压(Mpa)=反应器入口压力*
[循环气中氢分子数+新氢中分子数+进料分子数]
反应部分的操作压力是在V1012入口压力PIC1118保持1.7MPa(157公斤/厘米2)(表),此压力在整个操作周期都必须保持基本恒定。
为了维持压力恒定,在冷高压分离器装有一个压力调节器与新氢机系统的逐级递反配合调节,控制反应系统新氢补充量,实现反应系统压力稳定。
1.1.3 氢油比
氢油比的大小或循环气量大小直接关系到氢分压和油品的停留时间,并且还影响油的汽化率。
循环气量的增加可以保证系统有足够的氢分压,有利于加氢反应。
此外,过剩的H2可起到保护催化剂表面的作用,在一定的范围内可防止油料在催化剂表面缩合结焦,同时,氢油比增加可及时地将反应热从系统带出,有利于反应床层的热平衡,从而使反应器内温度容易控制平稳。
但过大的氢油比会使系统的压降增大,油品和催化剂接触的时间缩短,从而会导致反应深度下降,循环机负荷增大,动力消耗增大。
循环氢气量(标米3/时)
氢油比=
进料量(米3/时)
通常循环氢流量在催化剂整个运转周期内应保持恒定,因为经常改变压缩机的操作是不可能的。
为适应设计进料率到反应器入口的循环氢流量,必须维持下面的数值:
对精制反应器:
R1001入口混氢标米3/时
=900
(新鲜原料十循环油) 标米3/时
对裂化反应器:
(R1001入口混氢十R1001急冷氢十R1002入口冷氢)标米3/时
=900
(新鲜原料十循环油)米3/时在设计进料流率时,采用上述氢油比,在低于设计进料流,采用高一些的氢/油比。
在比设计进料流率高时,不要使循环氢的循环量大于设计数字,因为这会影响保留的急冷氢,所以高于设计进料流率时,氢/油比将小于上述数值。
1.1.4空速
降低空速,则原料反应的时间延长,深度加大,转化率提高。
但空速过低,二次裂解反应加剧,虽然这时总转化率可以提高。
但生成的气态烃也会相应的增加。
同时,由于油分子在催化剂中的停留时间延长,在一定的温度下,缩合结焦的机会也随之增加,因此,长期的低空速对催化剂活性不利,空速的选择随原料油性质和催化剂活性的不同而不同,空速的增大意味着处理能力的增大,为达到合适的转化率,
必须提高反应温度。
故在不影响原料转化深度的前提下,应尽量提高空速。
但空速的增加受到设备设计负荷的限制和相应的温度限制。
1.1.5催化剂活性
催化剂活性对加氢裂化操作条件、产品收率和产品性质有着显著的影响,提高活性可以降低反应器温度和压力,提高空速或降低氢油比。
提高催化剂选择性,则可以生产更多的目的产品,减少不必要的副反应,增加催化剂的抗毒能力。
随着开工周期延长,催化剂活性逐渐下降,此时必须相应提高反应温度,以保持达到设计的转化率。
应当指出,在生产过程,操作水平的高低及各种不正确的操作方法,均对催化剂活性有较大影响,必须引起有关人员注意。
1.1.6循环氢流量和纯度
a. 循环氢流量
循环氢主要作用是:使反应系统保持高的氢分压;作为热传递载体,在催化剂床层之间加入足够的急冷氢,把热量及时带走,以控制催化剂床层的温升;促使液体进料均匀分布在整个催化剂床层,以抑制热点形成,从而提高反应性能。
当循环氢的流量较高时,上述作用较为明显,而这些作用都有利于抑制催化剂的结焦。
因此,在整个运转期内,应使循环氢的流量保持在允许的最高值上。