催化加氢总结
总结氢化反应

总结氢化反应氢化反应概述氢化反应是一种广泛应用于有机合成领域的重要反应类型。
它主要通过在有机化合物中加入氢气来实现,从而将不饱和化合物转化为饱和化合物。
氢化反应广泛用于制备醇、醛、酮和胺等有机化合物,具有高效、环境友好、选择性好等优点。
氢化反应分类氢化反应可以根据催化剂的类型分为催化氢化反应和非催化氢化反应。
催化氢化反应催化氢化反应是氢化反应中最常用的类型,它需要添加合适的催化剂来促进反应的进行。
常见的催化剂有铂、钯、铑等贵金属催化剂,它们具有高催化活性和选择性。
催化氢化反应可以分为三个主要类型:1.加氢还原反应:将不饱和化合物转化为饱和化合物,常用于将烯烃转化为烷烃的反应;2.加氢裂解反应:将长链烷烃裂解为短链烷烃,常用于石油化工领域的反应;3.加氢脱氧反应:将含氧官能团的化合物转化为饱和化合物,常用于制备醇、醛、酮等化合物。
非催化氢化反应非催化氢化反应是指在没有外加催化剂的情况下,利用高温和高压条件下的氢气来进行氢化反应。
这种反应条件较为苛刻,但在一些特定的情况下,非催化氢化反应仍然具有一定的应用价值。
氢化反应的实施条件氢化反应的实施条件是反应成功的关键之一。
通常需要考虑以下几个方面:1.催化剂的选择:选择合适的催化剂对于提高反应效率和选择性非常重要。
不同类型的氢化反应需要不同的催化剂,并且催化剂的载体和配体的选择也会影响反应结果。
2.反应温度和压力:反应温度和压力对于氢化反应的进行有重要影响。
一般情况下,较高的温度和压力可以促进反应的进行,但过高的条件可能导致产物副反应和催化剂失活。
3.反应溶剂选择:反应溶剂可以帮助提供反应环境,促进反应的进行。
合适的溶剂选择有助于催化剂的溶解和反应物的溶解,从而提高反应效率和选择性。
4.反应时间和摇床速度:反应时间和摇床速度对于氢化反应的控制也非常重要。
反应时间太短可能导致反应不完全,而反应时间太长可能造成产物的副反应。
氢化反应的应用领域氢化反应在有机合成领域具有广泛的应用价值,常见的应用领域包括:1.药物合成:氢化反应是制备药物中间体和活性成分的重要手段。
烷基酸的催化加氢反应

烷基酸的催化加氢反应是一种在化学生产中广泛应用的反应。
该反应可以将烯烃和炔烃转化为烷烃,得到较高纯度的产物,具有重要的经济价值。
本文将对进行介绍,分析反应机理和影响反应效果的因素,并总结该反应的应用前景。
一、反应原理是一种通过加氢作用将烯烃和炔烃转化为烷烃的反应。
通常使用铜、镍、钯等金属和烷基酸作为催化剂,常见的烷基酸有硫酸、磷酸、酒石酸等。
在反应中,烷基酸作为质子供体,能够与烯烃或炔烃形成复合物。
当催化剂表面存在吸附氢原子,这些氢原子可以被烷基酸上的质子引导,与烯烃或炔烃的双联键或三联键发生加成反应,产生相应的烷烃。
二、反应机理通常分为两个步骤:质子化和加氢。
质子化是指烯烃或炔烃在烷基酸上发生吸附形成质子化物质,这种物质更稳定,对反应发挥重要作用。
加氢是指发生在质子化物质上的加氢反应,最终得到相应的烷烃产物。
催化剂中的过渡金属与小分子气态氢在反应中的作用是:将氢分子裂解成两个氢原子(其H-H键能为436 kJ/mol),根据对应配位基的强弱,通过过渡金属负载的催化剂上的反应质子,与烯烃或炔烃的双键或三键形成复合物,然后又被氢原子进一步还原得到烷烃。
三、影响反应效果的因素在实际应用中,其效果往往受到多种因素的影响。
以下是几个主要的因素:1.反应温度:反应温度是影响效果的主要因素之一。
通常情况下,反应温度越高,反应速率越快,但是温度过高会引起不必要的副反应,影响产物纯度。
2.催化剂的种类:不同的催化剂在催化加氢反应中具有不同的反应活性和选择性。
常见的铜、镍、钯等金属可以作为催化剂,不同催化剂的适用范围和效果不同,需要在实验中进行测试。
3.反应物的种类:不同的反应物在烷基酸催化加氢反应中产生的产物不同,需要根据具体情况选择合适的反应物。
通常来说,烯烃和炔烃是常见的反应物。
四、应用前景在石油、化工等领域都有广泛的应用。
常见的应用领域有:1.烷烃的合成:可以通过将烯烃和炔烃转化为烷烃,实现高纯度的烷烃合成。
有机合成中的催化加氢与氧化反应

有机合成中的催化加氢与氧化反应有机合成是一门复杂而又具有重要意义的化学科学,催化加氢和氧化反应作为其中的两种重要反应类型,在有机合成过程中扮演着重要的角色。
催化加氢反应是将氢气加入有机物中,使其发生氢化反应,而催化氧化反应则是将氧气加入有机物中,使其氧化为更高的价态。
本文将详细介绍有机合成中的催化加氢与氧化反应。
一、催化加氢反应催化加氢反应广泛应用于有机合成中,它可以将不饱和键或者不稳定官能团加氢,得到稳定的饱和化合物。
常见的催化剂包括贵金属催化剂(如铂、钯、铑等)、非贵金属催化剂(如镍、铁等)以及配位催化剂(如氢化钯、氢化铂等)。
催化剂的选择取决于反应底物的性质以及反应条件。
催化加氢反应的机理一般可分为两步:吸附和反应。
吸附是指底物或者底物与催化剂之间发生化学结合,形成活性吸附物种;反应则是指催化剂表面上的吸附物种发生变化,生成产物。
催化加氢反应的速率受到多种因素的影响,如反应温度、催化剂的种类和形态、底物的结构等。
催化加氢反应在有机合成中有着广泛的应用。
例如,将不饱和烯烃加氢合成饱和烃;将酮、醛、酸等官能团还原为醇;将炔烃加氢合成烯烃等。
这些反应在有机合成中起到了至关重要的作用,为合成目标产物提供了重要的中间体和建模原料。
二、催化氧化反应催化氧化反应是将氧气加入有机物中,使有机物中的原子发生氧化反应,从而形成更高的价态。
常见的催化剂包括贵金属催化剂(如铑、铱、钌等)、氧化剂(如过氧化氢、高锰酸钾等)以及配位催化剂(如六氟合铀酸银、高铁素酸钾等)。
催化剂的选择取决于反应底物的性质以及反应条件。
催化氧化反应的机理较为复杂,常见的反应机理包括单电子转移机制、氢移机制、氧进攻机制等。
催化氧化反应的速率同样受到多种因素的影响,如反应温度、催化剂的种类和形态、底物的结构等。
催化氧化反应同样在有机合成中发挥着重要的作用。
例如,将醇氧化为醛或酮;将醚氧化为醛、酮或醚羧酸;将烯烃氧化为醇或酮等。
这些反应在有机合成中起到了重要的作用,为合成复杂化合物提供了关键的步骤和途径。
加氢脱氢过程知识点总结

加氢脱氢过程知识点总结1. 加氢脱氢的基本概念加氢脱氢反应是指在催化剂的作用下,有机物中的饱和键(C=C)被氢气加成形成饱和烃,或者烃分子中的部分氢原子被去除,形成不饱和烃。
加氢脱氢过程通常在高压、高温、催化剂存在的条件下进行,反应物可以是烃类、醇类、醛酮类化合物等。
这种反应是一种重要的烃转化反应,对于有机合成、燃料改性、化工产品提纯等具有重要意义。
2. 加氢脱氢的催化剂加氢脱氢反应中的催化剂是反应过程中至关重要的一环。
常见的加氢脱氢催化剂包括贵金属催化剂(如铂、钯、钌等)和非贵金属催化剂(如镍、铁等)。
其中,贵金属催化剂具有活性高、选择性好的特点,但成本较高;而非贵金属催化剂成本较低,但活性和选择性相对较差。
催化剂的选择涉及到反应物的性质、采用工艺条件等因素,是影响加氢脱氢反应效率的关键因素之一。
3. 加氢脱氢的反应机理加氢脱氢反应的机理主要分为两种:加氢反应和脱氢反应。
在加氢反应中,有机物分子中的双键处的氢原子被加成,生成饱和烃;在脱氢反应中,有机物分子中的氢原子被去除,生成不饱和烃。
这些反应都是在催化剂的表面上进行的,催化剂通过提供活性位点促进反应进行。
在加氢脱氢反应机理研究中,理论计算、实验验证和催化剂设计都是重要的研究方向,对于深入理解反应机理和提高反应效率具有重要意义。
4. 加氢脱氢的应用领域加氢脱氢反应在化工领域有着广泛的应用。
在石油炼制工业中,加氢脱氢反应用于烃类的转化,包括重油加氢脱硫脱氮、汽油、柴油的加氢精制等;在有机合成领域,加氢脱氢反应用于醇醛酮的加氢制备醇类、醚类、醚醛类化合物等;在生物制药领域,加氢脱氢反应用于生产抗生素、维生素等药物。
加氢脱氢反应在这些领域中发挥着重要的作用,为生产高质量产品和提高生产效率做出贡献。
5. 加氢脱氢的发展趋势随着化工工业的发展,加氢脱氢反应也在不断地得到改进和优化。
一个重要的发展趋势是催化剂的设计和改进。
通过设计新型的催化剂结构和组成,可以提高催化剂的活性、选择性和稳定性,从而提高反应效率。
汽柴油加氢技术总结汇报
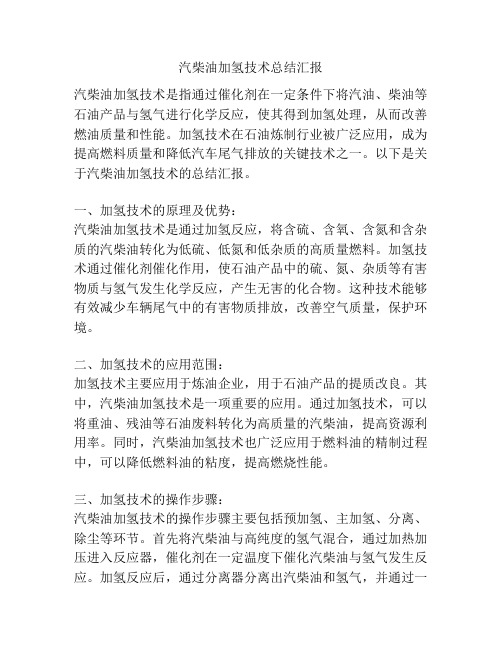
汽柴油加氢技术总结汇报汽柴油加氢技术是指通过催化剂在一定条件下将汽油、柴油等石油产品与氢气进行化学反应,使其得到加氢处理,从而改善燃油质量和性能。
加氢技术在石油炼制行业被广泛应用,成为提高燃料质量和降低汽车尾气排放的关键技术之一。
以下是关于汽柴油加氢技术的总结汇报。
一、加氢技术的原理及优势:汽柴油加氢技术是通过加氢反应,将含硫、含氧、含氮和含杂质的汽柴油转化为低硫、低氮和低杂质的高质量燃料。
加氢技术通过催化剂催化作用,使石油产品中的硫、氮、杂质等有害物质与氢气发生化学反应,产生无害的化合物。
这种技术能够有效减少车辆尾气中的有害物质排放,改善空气质量,保护环境。
二、加氢技术的应用范围:加氢技术主要应用于炼油企业,用于石油产品的提质改良。
其中,汽柴油加氢技术是一项重要的应用。
通过加氢技术,可以将重油、残油等石油废料转化为高质量的汽柴油,提高资源利用率。
同时,汽柴油加氢技术也广泛应用于燃料油的精制过程中,可以降低燃料油的粘度,提高燃烧性能。
三、加氢技术的操作步骤:汽柴油加氢技术的操作步骤主要包括预加氢、主加氢、分离、除尘等环节。
首先将汽柴油与高纯度的氢气混合,通过加热加压进入反应器,催化剂在一定温度下催化汽柴油与氢气发生反应。
加氢反应后,通过分离器分离出汽柴油和氢气,并通过一系列的脱硫、脱氮、脱杂等工艺处理,最终得到高质量的汽柴油产品。
四、加氢技术的优势与不足:加氢技术具有以下优势:1. 改善燃料质量:通过加氢处理,汽柴油的硫含量、氮含量和杂质含量得到有效降低,提高了燃料的质量。
2. 降低尾气排放:加氢技术能够减少燃料中的有害物质含量,从而降低了汽车尾气中的污染物排放,改善环境质量。
3. 提高能源利用率:通过将废料油转化为汽柴油,提高了资源利用效率,减少了能源浪费。
不足之处:1. 技术要求高:加氢技术对催化剂稳定性、反应条件、操作参数等要求较高,需要专业技术人员掌握和操作。
2. 设备投资大:加氢技术需要投入大量设备和催化剂,投资成本较高。
石化加氢工作总结

石化加氢工作总结
石化加氢是炼油工业中非常重要的工艺之一,它通过加氢反应将重质石油产品
转化为轻质产品,提高产品的质量和减少环境污染。
在过去的一段时间里,我们团队在石化加氢工作中取得了一定的成绩,现在我将对我们的工作进行总结。
首先,我们在石化加氢工作中注重了安全生产。
加氢反应是高温高压下进行的,一旦发生事故后果将不堪设想。
因此,我们严格执行安全操作规程,定期进行设备检修和维护,确保设备运行的安全可靠。
同时,我们也加强了员工的安全培训,提高了员工的安全意识和应急处理能力,有效地保障了生产安全。
其次,我们在工艺优化方面取得了一些进展。
我们对加氢反应的工艺参数进行
了优化调整,提高了产品的收率和质量。
通过改进催化剂的配方和制备工艺,我们成功地降低了生产成本,提高了生产效率。
此外,我们还引进了先进的自动化控制系统,实现了设备的智能化运行,进一步提高了生产的稳定性和可靠性。
最后,我们在环保方面也做出了一些努力。
石化加氢工艺会产生大量的硫化氢
和硫化物等有害气体,对环境造成严重污染。
为了减少排放,我们加强了废气处理设施的建设和运行,有效地净化了废气排放。
同时,我们还对废水处理系统进行了改造升级,减少了废水排放对水环境的影响。
总的来说,我们在石化加氢工作中取得了一些成绩,但也存在一些问题和不足。
未来,我们将继续努力,不断改进工艺,提高生产效率和产品质量,同时加强安全生产和环保工作,为炼油工业的可持续发展做出更大的贡献。
白油加氢催化剂长周期运行总结及使用寿命预测
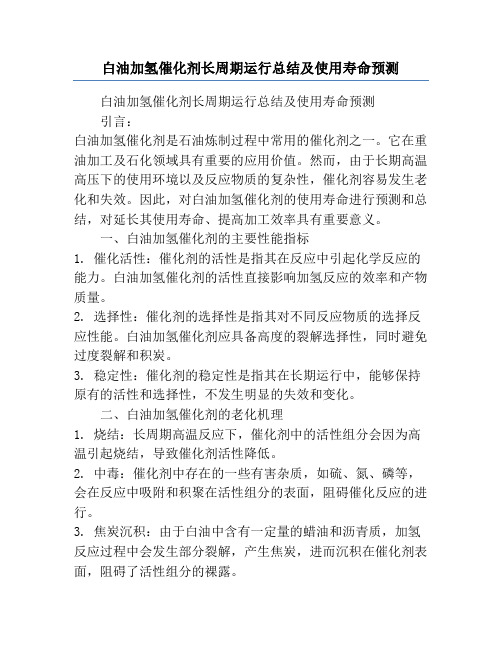
白油加氢催化剂长周期运行总结及使用寿命预测白油加氢催化剂长周期运行总结及使用寿命预测引言:白油加氢催化剂是石油炼制过程中常用的催化剂之一。
它在重油加工及石化领域具有重要的应用价值。
然而,由于长期高温高压下的使用环境以及反应物质的复杂性,催化剂容易发生老化和失效。
因此,对白油加氢催化剂的使用寿命进行预测和总结,对延长其使用寿命、提高加工效率具有重要意义。
一、白油加氢催化剂的主要性能指标1. 催化活性:催化剂的活性是指其在反应中引起化学反应的能力。
白油加氢催化剂的活性直接影响加氢反应的效率和产物质量。
2. 选择性:催化剂的选择性是指其对不同反应物质的选择反应性能。
白油加氢催化剂应具备高度的裂解选择性,同时避免过度裂解和积炭。
3. 稳定性:催化剂的稳定性是指其在长期运行中,能够保持原有的活性和选择性,不发生明显的失效和变化。
二、白油加氢催化剂的老化机理1. 烧结:长周期高温反应下,催化剂中的活性组分会因为高温引起烧结,导致催化剂活性降低。
2. 中毒:催化剂中存在的一些有害杂质,如硫、氮、磷等,会在反应中吸附和积聚在活性组分的表面,阻碍催化反应的进行。
3. 焦炭沉积:由于白油中含有一定量的蜡油和沥青质,加氢反应过程中会发生部分裂解,产生焦炭,进而沉积在催化剂表面,阻碍了活性组分的裸露。
三、白油加氢催化剂使用寿命预测方法1. 富集曲线法:通过催化剂的催化活性数据建立不同周期下的活性曲线,根据曲线趋势预测催化剂的使用寿命。
2. 表面积比法:分析催化剂表面具体活性组分的含量变化情况,根据活性组分的降解率进行预测。
3. 物化校正法:通过对比不同白油加氢催化剂,根据化学成分和物化性质的对比,综合评估催化剂的使用寿命。
四、白油加氢催化剂长周期运行总结1. 催化剂表面的烧结和焦炭沉积会导致催化剂活性降低,周期性的再生和烧烤等操作能够有效延长催化剂的使用寿命。
2. 白油加氢催化剂的稳定性对反应产物质量有重要影响,催化剂的选择和控制反应条件可提高稳定性。
加氢脱硫催化剂总结
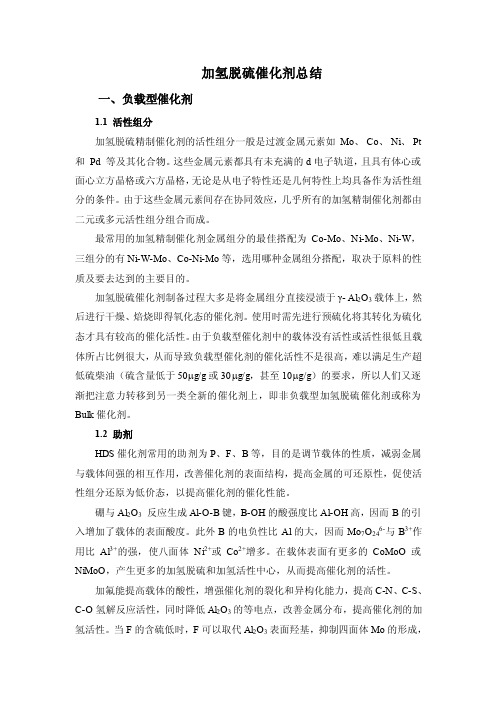
加氢脱硫催化剂总结一、负载型催化剂1.1 活性组分加氢脱硫精制催化剂的活性组分一般是过渡金属元素如Mo、Co、Ni、Pt 和Pd 等及其化合物。
这些金属元素都具有未充满的d电子轨道,且具有体心或面心立方晶格或六方晶格,无论是从电子特性还是几何特性上均具备作为活性组分的条件。
由于这些金属元素间存在协同效应,几乎所有的加氢精制催化剂都由二元或多元活性组分组合而成。
最常用的加氢精制催化剂金属组分的最佳搭配为Co-Mo、Ni-Mo、Ni-W,三组分的有Ni-W-Mo、Co-Ni-Mo等,选用哪种金属组分搭配,取决于原料的性质及要去达到的主要目的。
加氢脱硫催化剂制备过程大多是将金属组分直接浸渍于γ- Al2O3载体上,然后进行干燥、焙烧即得氧化态的催化剂。
使用时需先进行预硫化将其转化为硫化态才具有较高的催化活性。
由于负载型催化剂中的载体没有活性或活性很低且载体所占比例很大,从而导致负载型催化剂的催化活性不是很高,难以满足生产超低硫柴油(硫含量低于50μg/g或30μg/g,甚至10μg/g)的要求,所以人们又逐渐把注意力转移到另一类全新的催化剂上,即非负载型加氢脱硫催化剂或称为Bulk催化剂。
1.2 助剂HDS催化剂常用的助剂为P、F、B等,目的是调节载体的性质,减弱金属与载体间强的相互作用,改善催化剂的表面结构,提高金属的可还原性,促使活性组分还原为低价态,以提高催化剂的催化性能。
硼与Al2O3反应生成Al-O-B键,B-OH的酸强度比Al-OH高,因而B的引入增加了载体的表面酸度。
此外B的电负性比Al的大,因而Mo7O246-与B3+作用比Al3+的强,使八面体Ni2+或Co2+增多。
在载体表面有更多的CoMoO或NiMoO,产生更多的加氢脱硫和加氢活性中心,从而提高催化剂的活性。
加氟能提高载体的酸性,增强催化剂的裂化和异构化能力,提高C-N、C-S、C-O氢解反应活性,同时降低Al2O3的等电点,改善金属分布,提高催化剂的加氢活性。
- 1、下载文档前请自行甄别文档内容的完整性,平台不提供额外的编辑、内容补充、找答案等附加服务。
- 2、"仅部分预览"的文档,不可在线预览部分如存在完整性等问题,可反馈申请退款(可完整预览的文档不适用该条件!)。
- 3、如文档侵犯您的权益,请联系客服反馈,我们会尽快为您处理(人工客服工作时间:9:00-18:30)。
4加氢裂化:260〜400C。温度提高,裂解反应速度加快,因而反应产物中低沸点
组分增多、烷烃含量增加而环烷烃含量降低、异构烷/正构烷比值下降。根据催化剂
性能、原料性质和产品的要求来定,一般不超过400〜420C。
3加氢裂化:600〜1200(体)
1、具有绿色化的化学反应,原子经济性。
催化加氢一般生成产物和水,不会生成其它副产物(副反应除外),具有很好的
原子经济性。绿色化学是当今科研和生产的世界潮流,我国已在重大科研项目研究的 立项上向这个方向倾斜。
2、产品收率高、质量好
普通的加氢反应副反应很少,因此产品的质量很高。
3、反应条件温和;
4、设备通用性
处于气相时,提高反应压力使汽油的反应时间延长,因此加氢精制深度提高。
但在有液相存在时,提高压力将会使精制效果变差。氢通过液膜向催化剂表面扩散 的速度往往是影响反应速度的控制因素, 提高反应压力会使催化剂表面的液层加厚, 从而降低了反应速度。如果总压不变,提高氢分压,可以得到最佳的精制效果。一 般在压力4.5〜5.0MPa时,采用氢油比150〜600Nm3/m3可以得到最适宜的氢分压。
三、国内外几家主要公司的馏分油加氢裂化催化剂
催化剂牌号
原料油
产品
酸性载体
金属组分
Chevro n ICR-106
VGO、AGO
柴油、航煤、石脑 油
SQ2-AI2O3
W-Ni-Ti-P
Chevron ICR-117
VGO
石脑油、柴油、航 煤
—
W-Ni
UOP DHC-100
VGO、DAO
航煤
含沸石
—
UOP HC-14
VGO
LPG、汽油、石脑 油
Y
Mo-Ni
Shell S424
—
—
—
Mo-Ni-P
中石化3825
VGO
石脑油、航煤、柴 油
USY-AI2O3
Mo-Ni-P
中石化3903
VGO
航煤、柴油
—
W-Ni
四、加氢过程的主要影响因素
1反应压力
反应压力的影响往往是通过氢分压来体现的,系统的氢分压取决于操作压力、 氢油比、循环氢纯度和原料的汽化率等
催化加氢学习知识总结
、概述
催化加氢是石油馏分在氢气的存在下催化加工过程的通称。
炼油厂的加氢过程主要有两大类:
加氢处理(加氢精制)
加氢裂化
加氢精制/加氢处理
产品精制
原料预处理
润滑油加氢
临氢降凝
加氢裂化
馏分油加氢裂化
重(渣)油加氢裂化
根据其主要目的或精制深度的不同有:
加氢脱硫(HDS)
加氢脱氮(HDN)
1—加热炉;2—反应器;3—分离器;
4-稳定塔;5-循环压缩机
加氢裂化:在较高的反应压力下,较重的原料在氢压及催化剂存在下进行裂解和加 氢反应,使之成为较轻的燃料或制取乙烯的原料。可分为:
馏分油加氢裂化
渣油加氢裂化
加氢精制与加氢裂化的不同点:在于其反应条件比较缓和,因而原料中的平均分 子量和分子的碳骨架结构变化很小。
3、空速
空速反映了装置的处理能力。
根据催化剂活性、原料性质和要求的反应深度不同而定,一般在0.5〜10h-1。
重的原料和二次加工得到的原料加氢时通常采用较低的空速。
4、氢油比
提高氢油比可以氢分压,一般情况下对加氢反应有利。加氢精制氢油比可较低,而 加氢裂化的要较高。
1汽油精制:50〜150(体)
2柴油精制:150〜600(体)
3重馏分油加氢精制和加氢裂化
大于350C的重馏分油在加氢精制条件下经常是处于气液混相,因此提高氢分压能 显著提高反应速度而提高精制效果。
芳烃加氢反应的转化率随着反应压力升高而显著提高,同时也加快了反应速度。在 压力低时,即使反应速度很快,也不可能有高压下的高转化率。
加氢裂化原料一般都是较重的馏分油,其中含有较多的多环芳烃。多环芳烃的裂解 是通过芳香环的加氢来进行的,因此,在给定的催化剂和反应温度条件下,选用的 压力要能保证环数最多的芳烃有足够的平衡转化率。
2、反应温度
提高反应温度会使加氢精制和加氢裂化的反应速度加快。在常用的压力范围内,加
氢精制的反应温度一般在250〜420C,超过420C时会发生较多的裂解和脱氢反应。
1重整原料精制:400〜420C。温度较高,脱氢的反应没有什么关系。
2航煤加氢精制:350〜360C。温度超过370C时,四氢萘脱氢生成萘的平衡转化 率急速上升(在5.0MPa条件下)。
1汽油加氢精制
氢分压在2.5MPa〜3.5PMa后,汽油加氢精制反应的深度不受热力学控制,而是取 决于反应速度和反应时间。
在气相条件下进行,提高反应压力使汽油的反应时间延长,压力对它的反应速度影 响很小,因此加氢精制深度提高。
如果压力不变,通过氢油比来提高氢分压,则精制深度下降。
2柴油加氢精制
在精制条件下,可以是气相也可是气液混相。