加氢裂化工艺流程概述
加氢裂化工艺流程介绍
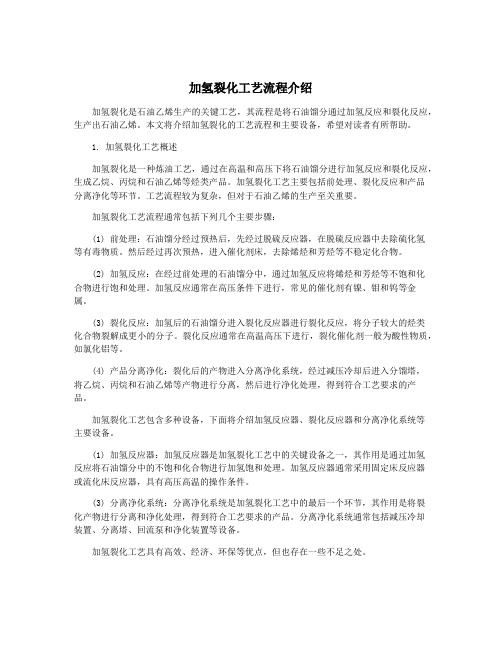
加氢裂化工艺流程介绍加氢裂化是石油乙烯生产的关键工艺,其流程是将石油馏分通过加氢反应和裂化反应,生产出石油乙烯。
本文将介绍加氢裂化的工艺流程和主要设备,希望对读者有所帮助。
1. 加氢裂化工艺概述加氢裂化是一种炼油工艺,通过在高温和高压下将石油馏分进行加氢反应和裂化反应,生成乙烷、丙烷和石油乙烯等烃类产品。
加氢裂化工艺主要包括前处理、裂化反应和产品分离净化等环节。
工艺流程较为复杂,但对于石油乙烯的生产至关重要。
加氢裂化工艺流程通常包括下列几个主要步骤:(1) 前处理:石油馏分经过预热后,先经过脱硫反应器,在脱硫反应器中去除硫化氢等有毒物质。
然后经过再次预热,进入催化剂床,去除烯烃和芳烃等不稳定化合物。
(2) 加氢反应:在经过前处理的石油馏分中,通过加氢反应将烯烃和芳烃等不饱和化合物进行饱和处理。
加氢反应通常在高压条件下进行,常见的催化剂有镍、钼和钨等金属。
(3) 裂化反应:加氢后的石油馏分进入裂化反应器进行裂化反应,将分子较大的烃类化合物裂解成更小的分子。
裂化反应通常在高温高压下进行,裂化催化剂一般为酸性物质,如氯化铝等。
(4) 产品分离净化:裂化后的产物进入分离净化系统,经过减压冷却后进入分馏塔,将乙烷、丙烷和石油乙烯等产物进行分离,然后进行净化处理,得到符合工艺要求的产品。
加氢裂化工艺包含多种设备,下面将介绍加氢反应器、裂化反应器和分离净化系统等主要设备。
(1) 加氢反应器:加氢反应器是加氢裂化工艺中的关键设备之一,其作用是通过加氢反应将石油馏分中的不饱和化合物进行加氢饱和处理。
加氢反应器通常采用固定床反应器或流化床反应器,具有高压高温的操作条件。
(3) 分离净化系统:分离净化系统是加氢裂化工艺中的最后一个环节,其作用是将裂化产物进行分离和净化处理,得到符合工艺要求的产品。
分离净化系统通常包括减压冷却装置、分离塔、回流泵和净化装置等设备。
加氢裂化工艺具有高效、经济、环保等优点,但也存在一些不足之处。
加氢裂化工艺流程介绍

加氢裂化工艺流程介绍加氢裂化是一种重要的石油加工工艺,可以将高沸点石油馏分转化为低沸点馏分,同时提高汽油和润滑油基础油的数量和质量。
本文将介绍加氢裂化的工艺流程。
1. 原料引入原料通常是经过预处理的石油馏分或重油,经过加热后进入加氢裂化反应器。
通常预处理过程包括脱蜡、脱硫、脱氮、脱水等步骤,以保证原料质量达到反应器的要求。
2. 加氢在反应器中,原料与氢气混合,压力一般在20到70大气压之间。
加氢操作是为了提供反应所需的氢气,并将部分反应产物中产生的芳烃和不饱和化合物氢化,达到减少积碳和减少杂质的目的。
3. 热解在反应器中,加热的原料和氢气混合物进入热解区域,受热后发生热解反应。
热解反应是原料中分子裂解成较小分子的过程,该过程有利于提高汽油和基础油的数量和质量。
裂解反应产生的芳烃、烯烃、脂肪烃等不饱和物质,进一步参与裂解反应。
4. 转化原料中分子的热解不仅分解了大分子化合物,而且还通过转化产生了新的分子,这是加氢裂化的重要特点。
转化反应相当于将一种化合物转化成另一种化合物。
该过程对于提高工艺效率和提高产品质量有重要意义。
5. 冷凝加氢裂化的反应产物中包含大量的不同碳数的烃烃类化合物。
从反应器中出来的气体混合物在经过冷却后,其中的液态混合物进入分离器进行进一步的分离。
尤其是汽油和润滑油基础油在冷凝后可以直接由分离器分离出来,经过蒸馏后得到最终产品。
6. 氢气回收由于反应过程需要大量的氢气,因此需要对反应后剩余的氢气进行回收。
在回收前,需要将氢气先进行压缩,进而进行氢气的回收和再利用。
7. 产品储存和输送从分离器中分离出来的产品由输送系统输送到储罐中进行储存。
对于汽油和润滑油基础油需要进行进一步的精制,以提高其纯度和质量,最终得到优质的成品。
总之,加氢裂化工艺流程具有较高的生产效率和制品质量,可以为石油化工行业提供具有重要价值的产品。
加氢裂化工艺流程

加氢裂化工艺流程1. 简介加氢裂化是一种常用的炼油工艺,用于将重质石油馏分转化为高辛烷值的汽油。
该工艺通过在高温和高压下将长链烃分子分解为较短链的烃类,同时加入氢气来抑制烃类的进一步裂解和脱氢反应。
加氢裂化工艺流程包括预热、加氢裂化反应、分离和再生等步骤。
2. 步骤和流程2.1 预热首先,原料石油馏分经过预热过程,将其加热到适宜的温度。
预热有助于提高反应速率和转化率,并减少催化剂的热损失。
预热的温度和时间根据具体的石油馏分和工艺条件来确定。
2.2 加氢裂化反应预热后的石油馏分进入加氢裂化反应器,与催化剂和氢气一起进行反应。
催化剂通常采用铝硅比较高的沸石催化剂,具有较好的活性和选择性。
反应器内的温度和压力控制在适宜的范围内,以提高反应速率和转化率。
在加氢裂化反应中,长链烃分子发生裂解和氢化反应,生成较短链的烃类和饱和烃。
裂解产物中的短链烃类主要是高辛烷值的汽油组分,而饱和烃主要是石蜡。
2.3 分离反应器出口的混合物进入分离器,通过分馏和其他分离操作将产物分离。
分离过程主要包括汽油、石蜡、烯烃和气相的分离。
其中,石蜡可以作为工业原料或进一步加工成蜡烛、润滑油等产品。
2.4 再生经过分离的催化剂进入再生器,通过加热和氢气的作用将吸附在催化剂上的碳杂质和焦炭燃烧掉,再生催化剂的活性。
再生后的催化剂回流到加氢裂化反应器中,继续参与反应。
3. 工艺优化和改进为了提高加氢裂化工艺的效果和经济性,可以采取以下措施进行优化和改进:3.1 催化剂的选择和改进选择具有较高活性和选择性的催化剂,通过改变催化剂的物理和化学性质来提高其性能。
例如,改变催化剂的孔径大小、比表面积和酸性等,可以调节反应的速率和产物分布。
3.2 反应条件的优化通过调整反应器的温度、压力和氢气的用量等参数,优化反应条件,提高反应速率和转化率。
同时,可以采用多级反应器和换热器等装置,提高能量利用率和催化剂的利用率。
3.3 废气处理加氢裂化过程中产生的废气中含有大量的硫化物、氮化物和有机物等污染物,需要进行适当的处理。
加氢裂化工艺流程介绍

加氢裂化工艺流程介绍加氢裂化是一种重要的石油化工工艺,主要用于将重质石油馏分或原油中的长链烃类分子切割成较短链烃类分子,以提高产品的转化率和降低其粘度,从而达到提高产品质量和增加产品产量的目的。
该工艺主要包括催化剂的选择、反应装置的设计、反应条件的控制等几个方面,下面将对加氢裂化工艺的流程进行详细介绍。
一、催化剂的选择加氢裂化反应的催化剂通常为金属催化剂,如镍、钴、铂、钒等。
这些金属催化剂能够在合适的条件下催化烃类分子的裂解反应,生成较短链烃类分子和氢气。
通常还需在催化剂中加入一定量的活性组分,如氧化物、氧化钠、氧化铝等,以增加催化剂的活性和稳定性。
二、反应装置的设计加氢裂化反应通常在催化裂化装置中进行。
这种反应装置通常由裂化炉、加氢装置、冷却装置和分离装置等组成。
裂化炉是反应装置的核心部件,是将原料石油馏分或原油送入裂化反应器进行加热和裂化的地方。
加氢装置用于向裂化反应器中注入氢气,以提高裂化反应的效率和选择性。
冷却装置用于冷却反应产物,并将其中的气态产物液化。
分离装置则用于将反应产物中的各种组分进行分离,并提取所需的产品。
三、反应条件的控制加氢裂化反应的温度、压力、空速、氢油比等条件对反应的效率和选择性具有重要影响。
通常情况下,加氢裂化反应的温度为400-500℃,压力为2-8 MPa,空速为1-10 h-1,氢油比为1000-2000 Nm3/m3。
在这些条件下,可获得较高的产品转化率和较好的产品选择性。
加氢裂化工艺通常包括以下几个步骤:1. 原料处理:原料石油馏分或原油经过脱盐、脱硫等处理后,送入加氢裂化装置进行加热和裂化。
在这个过程中,通过加热将原料加热至裂化反应所需温度,并将其中的一部分烃类分子裂解成较短链烃类分子和氢气。
3. 冷却和分离:经过加氢裂化反应后,产生大量的气态产物和液态产物需要进行冷却和分离。
通过冷却装置将气态产物冷却成液态产物,并通过分离装置将其中的各种组分进行分离,提取所需的产品。
加氢裂化工艺流程介绍
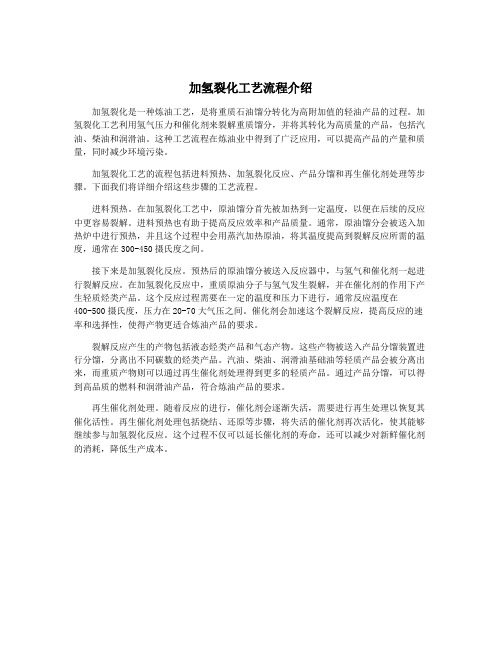
加氢裂化工艺流程介绍加氢裂化是一种炼油工艺,是将重质石油馏分转化为高附加值的轻油产品的过程。
加氢裂化工艺利用氢气压力和催化剂来裂解重质馏分,并将其转化为高质量的产品,包括汽油、柴油和润滑油。
这种工艺流程在炼油业中得到了广泛应用,可以提高产品的产量和质量,同时减少环境污染。
加氢裂化工艺的流程包括进料预热、加氢裂化反应、产品分馏和再生催化剂处理等步骤。
下面我们将详细介绍这些步骤的工艺流程。
进料预热。
在加氢裂化工艺中,原油馏分首先被加热到一定温度,以便在后续的反应中更容易裂解。
进料预热也有助于提高反应效率和产品质量。
通常,原油馏分会被送入加热炉中进行预热,并且这个过程中会用蒸汽加热原油,将其温度提高到裂解反应所需的温度,通常在300-450摄氏度之间。
接下来是加氢裂化反应。
预热后的原油馏分被送入反应器中,与氢气和催化剂一起进行裂解反应。
在加氢裂化反应中,重质原油分子与氢气发生裂解,并在催化剂的作用下产生轻质烃类产品。
这个反应过程需要在一定的温度和压力下进行,通常反应温度在400-500摄氏度,压力在20-70大气压之间。
催化剂会加速这个裂解反应,提高反应的速率和选择性,使得产物更适合炼油产品的要求。
裂解反应产生的产物包括液态烃类产品和气态产物。
这些产物被送入产品分馏装置进行分馏,分离出不同碳数的烃类产品。
汽油、柴油、润滑油基础油等轻质产品会被分离出来,而重质产物则可以通过再生催化剂处理得到更多的轻质产品。
通过产品分馏,可以得到高品质的燃料和润滑油产品,符合炼油产品的要求。
再生催化剂处理。
随着反应的进行,催化剂会逐渐失活,需要进行再生处理以恢复其催化活性。
再生催化剂处理包括烧结、还原等步骤,将失活的催化剂再次活化,使其能够继续参与加氢裂化反应。
这个过程不仅可以延长催化剂的寿命,还可以减少对新鲜催化剂的消耗,降低生产成本。
加氢裂化工艺流程介绍

加氢裂化工艺流程介绍加氢裂化工艺是炼油(石油加工)领域中的一种常用工艺,主要用于将重质石油馏分转化为较轻质的高附加值产品,如汽油和润滑油等。
以下是对加氢裂化工艺流程的介绍。
加氢裂化工艺是一种在高温高压下进行催化裂化反应的技术。
该工艺可以将重质石油馏分分解成轻质零部件,其中包括液化气、汽油、柴油和润滑油等。
在加氢裂化过程中,石油馏分首先经过预热,使其达到反应温度(通常为500-550摄氏度)。
然后,经过高压氢气的加氢作用,将石油分子中的一些碳链断裂成更短的碳链,从而产生较轻质的产品。
加氢裂化的反应器通常采用催化剂床,催化剂床中放置着由金属氧化物和酸性氧化物组成的催化剂。
加氢裂化反应器中的催化剂具有催化裂化反应的活性,能够促进碳链断裂和氢气的加氢反应。
催化剂床中的催化剂能够在高温高压下,将石油分子中的碳链断裂成较轻质的碳链,并捕获并催化裂化反应中产生的不稳定的分子中间体。
在加氢裂化过程中,石油馏分经过反应器后,会进入分离器进行分离。
分离器用于将产物中的不同组分进行分离和纯化。
在分离器中,液相产物被分离出来,并通过蒸汽冷凝器进行冷却,得到液体产品。
而气相产物则通过气体分离装置进行分离,得到液化气等产品。
加氢裂化工艺的设备通常还包括氢气压缩装置、再生装置和废气处理装置等。
氢气压缩装置用于将氢气压缩到加氢裂化过程所需的高压,并输送至反应器中。
再生装置用于再生催化剂,以维持催化剂的活性。
废气处理装置用于处理加氢裂化过程中产生的废气,以达到环保要求。
加氢裂化工艺是一种重要的炼油工艺,可将重质石油馏分转化为较轻质的高附加值产品。
这种工艺通过在高温高压下进行催化裂化反应,将石油分子的碳链断裂成较轻质的碳链。
这种工艺在提高石油利用率、改善燃料质量和减少环境污染方面具有重要意义。
加氢裂化工艺流程介绍
加氢裂化工艺流程介绍加氢裂化是一种石油加工工艺,用于将长链烃分子转化为较短的、易于加工的烃分子。
该工艺使用了高压和高温,使长链烃分子在催化剂的作用下通过裂解和氢化反应产生较小的烃分子,并且烃分子之间的化学键成为饱和状态。
在这里,我们将介绍该加氢裂化工艺的详细流程。
1. 加氢裂化反应器加氢裂化反应器是整个工艺流程的核心部分。
该反应器通常包括反应器本身、进料口、出料口、催化剂和氢气供应系统等。
反应器内的催化剂通常由一系列金属氧化物和酸性氧化物组成,并且需要经过预处理和活化才能使用。
此外,反应器中的氢气供应系统可以确保反应中的加氢过程得以顺利进行。
2. 进料预处理在加氢裂化反应之前,原油或其他烃类物质需要在进料预处理过程中进行预处理。
此过程包括严格的催化剂活性检测、沉积和分离重质杂质等,以确保进料的纯度和化学组成符合加氢裂化反应的要求。
预处理过程通常采用加热、加压、过滤、油品加氢和添加一些化学试剂来保证进料的净化和活化。
4. 分离和净化加氢裂化反应结束后,反应物中产生的烯烃和烷烃被分离和净化,以获得所需的目标产品。
分离器包括循环油分离器、蜡油分离器和气相分离器,这些分离器用于将产物分离和净化。
除此之外,产生的催化剂残留需要进行处理和再生,以加快催化剂的消耗和提高反应效率。
5. 尾气处理加氢裂化过程中产生的尾气是一种有害的废气,需要通过处理来减少对环境的污染。
尾气处理系统包括燃烧器、废气冷却器、氧化还原反应器和气体净化器等,这些装置用于清除尾气中的有害物质,并确保经过处理后的尾气排放符合环保要求。
加氢裂化工艺
加氢裂化工艺一、引言加氢裂化工艺是一种重要的炼油工艺,主要用于将重质石油馏分转化为高级汽油和柴油。
本文将详细介绍加氢裂化工艺的流程和设备组成。
二、加氢裂化工艺流程1. 原料预处理原料先经过蒸馏分离出各个馏分,然后将需要进行加氢裂化的重质馏分送入预处理装置。
预处理装置主要包括加热器、换热器和精密过滤器等设备,其作用是将原料加热至适宜温度,去除杂质和水分。
2. 加氢反应预处理后的原料进入反应器,与催化剂在高压下进行反应。
催化剂通常由铝酸盐、硅酸盐或钼酸盐等组成。
反应器内的温度通常在400-500℃之间,压力在20-30MPa之间。
加氢反应会使原料中的大分子链断裂,并与氢气发生反应生成较轻的烃类物质。
3. 分离和净化经过反应后的产物进入分离塔,塔内通过不同温度和压力的分离区间,将产物分为不同的组分。
其中,高级汽油和柴油是主要产品,其余产物可用于其他工艺或作为燃料。
产物中可能含有少量杂质和催化剂残留,需要通过净化装置进行处理。
4. 催化剂再生反应器中使用的催化剂在一定时间后会失效,需要进行再生。
催化剂再生主要包括焙烧、酸洗和还原等步骤。
焙烧将催化剂中的碳积聚物烧掉,酸洗去除催化剂表面的杂质,还原则是将氧化态的金属还原成金属原子。
三、加氢裂化工艺设备组成1. 反应器反应器是加氢裂化工艺中最重要的设备之一。
反应器通常由钢制成,内部涂有耐高温、耐腐蚀的陶瓷材料。
反应器通常具有自动控制系统和安全保护系统。
2. 分离塔分离塔是将产物分离为不同组分的关键设备。
分离塔通常由钢制成,内部涂有耐高温、耐腐蚀的陶瓷材料。
分离塔通常具有自动控制系统和安全保护系统。
3. 加热器加热器是将原料加热至适宜温度的设备。
加热器通常由钢制成,内部涂有耐高温、耐腐蚀的陶瓷材料。
加热器通常具有自动控制系统和安全保护系统。
4. 换热器换热器是将反应产生的废气或废水与进料进行换热的设备。
换热器通常由钢制成,内部涂有耐高温、耐腐蚀的陶瓷材料。
换热器通常具有自动控制系统和安全保护系统。
加氢裂化工艺流程概述
加氢裂化工艺流程概述加氢裂化工艺流程概述全装置工艺流程按反应系统(含轻烃吸收、低分气脱硫)、分馏系统、机组系统(含PSA系统)进行描述。
1.1反应系统流程减压蜡油由工厂罐区送入装置经原料升压泵(P1027/A、B)后,和从二丙烷罐区直接送下来的轻脱沥青油混合,在给定的流量和混合比例下原料油缓冲罐V1002液面串级控制下,经原料油脱水罐(V1001)脱水后,与分馏部分来的循环油混合,通过原料油过滤器(FI1001)除去原料中大于25微米的颗粒,进入原料油缓冲罐(V1002),V1002由燃料气保护,使原料油不接触空气。
自原料油缓冲罐(V1002)出来的原料油经加氢进料泵(P1001A,B)升压后,在流量控制下与混合氢混合,依次经热高分气/混合进料换热器(E1002)、反应流出物/混合进料换热器(E1001A,B)、反应进料加热炉(F1001)加热至反应所需温度后进入加氢精制反应器(R1001),R1001设三个催化剂床层,床层间设急冷氢注入设施。
R1001反应流出物进入加氢裂化反应器(R1002)进行加氢裂化反应,两个反应器之间设急冷氢注入点,R1002设四个催化剂床层,床层间设急冷氢注入设施。
R1001反应流出物设有精制油取样装置,用于精制油氮含量监控取样。
由反应器R1002出来的反应流出物经反应流出物/混合进料换热器(E1001)的管程,与混合原料油换热,以尽量回收热量。
在原料油一侧设有调节换热器管程出口温度的旁路控制,紧急情况下可快速的降低反应器的入口温度。
换热后反应流出物温度降至250℃,进入热高压分离器(V1003)。
热高分气体经热高分气/混合进料换热器(E1002)换热后,再经热高分气空冷器(A1001)冷至49℃进入冷高压分离器(V1004)。
为了防止热高分气在冷却过程中析出铵盐堵塞管路和设备,通过注水泵(P1002A,B)将脱盐水注入A1001上游管线,也可根据生产情况,在热高分顶和热低分气冷却器(E1003)前进行间歇注水。
加氢裂化工艺流程
加氢裂化工艺流程
《加氢裂化工艺流程》
加氢裂化是一种炼油工艺,用于将较重的石油馏分转化为更轻的产品,如汽油和柴油。
该工艺利用催化剂和氢气将高分子量的烃类分子裂解成低分子量的烃类,从而提高产品的附加值和燃烧效率。
加氢裂化工艺流程通常包括以下几个步骤:
1. 原料预处理:石油原料经过蒸馏、加氢处理等预处理工序,去除杂质和硫化物,以保证加氢裂化反应的高效进行。
2. 加氢反应器:预处理后的原料与氢气混合后进入加氢反应器,其中有催化剂的存在。
在高温高压下,长链烃类分子被裂解为较短的链烃,并与氢气发生加氢反应,生成更轻的产品。
3. 分离装置:经过加氢裂化反应后的产物混合物进入分离装置,通过蒸馏、提取等工艺将不同碳数的烃类分离出来,得到目标产品,如汽油、柴油等。
4. 催化剂再生:经过一段时间的运行,加氢裂化的催化剂会被炭积物和杂质堵塞,需要定期进行再生。
再生工艺一般包括焙烧、酸洗等步骤,以恢复催化剂的活性和选择性。
加氢裂化工艺可以提高汽油和柴油的产量,提高产品的品质,并减少环境污染。
然而,该工艺也需要消耗大量的氢气和催化
剂,并且对原料的要求较高,因此需要精细的工艺控制和运行管理。
随着石油工业的不断发展,加氢裂化工艺也在不断完善和优化,以适应市场的需求和环保的要求。
- 1、下载文档前请自行甄别文档内容的完整性,平台不提供额外的编辑、内容补充、找答案等附加服务。
- 2、"仅部分预览"的文档,不可在线预览部分如存在完整性等问题,可反馈申请退款(可完整预览的文档不适用该条件!)。
- 3、如文档侵犯您的权益,请联系客服反馈,我们会尽快为您处理(人工客服工作时间:9:00-18:30)。
加氢裂化工艺流程概述
全装置工艺流程按反应系统(含轻烃吸收、低分气脱硫)、分馏系统、机组系统(含PSA系统)进行描述。
1.1反应系统流程
减压蜡油由工厂罐区送入装置经原料升压泵(P1027/A、B)后,和从二丙烷罐区直接送下来的轻脱沥青油混合,在给定的流量和混合比例下原料油缓冲罐V1002液面串级控制下,经原料油脱水罐(V1001)脱水后,与分馏部分来的循环油混合,通过原料油过滤器(FI1001)除去原料中大于25微米的颗粒,进入原料油缓冲罐(V1002),V1002由燃料气保护,使原料油不接触空气。
自原料油缓冲罐(V1002)出来的原料油经加氢进料泵
(P1001A,B)升压后,在流量控制下与混合氢混合,依次经热高分气/混合进料换热器(E1002)、反应流出物/混合进料换热器(E1001A,B)、反应进料加热炉(F1001)加热至反应所需温度后进入加氢精制反应器(R1001),R1001设三个催化剂床层,床层间设急冷氢注入设施。
R1001反应流出物进入加氢裂化反应器(R1002)进行加氢裂化反应,两个反应器之间设急冷氢注入点,R1002设四个催化剂床层,床层间设急冷氢注入设施。
R1001反应流出物设有精制油取样装置,用于精制油氮含量监控取样。
由反应器R1002出来的反应流出物经反应流出物/混合
进料换热器(E1001)的管程,与混合原料油换热,以尽量回收热量。
在原料油一侧设有调节换热器管程出口温度的旁路控制,紧急情况下可快速的降低反应器的入口温度。
换热后反应流出物温度降至250℃,进入热高压分离器(V1003)。
热高分气体经热高分气/混合进料换热器(E1002)换热后,再经热高分气空冷器(A1001)冷至49℃进入冷高压分离器(V1004)。
为了防止热高分气在冷却过程中析出铵盐堵塞管路和设备,通过注水泵(P1002A,B)将脱盐水注入A1001上游管线,也可根据生产情况,在热高分顶和热低分气冷却器(E1003)前进行间歇注水。
冷却后的热高分气在V1004中进行油、气、水三相分离。
自V1004底部出来的油相在V1004液位控制下进入冷低压分离器(V1006)。
自V1003底部出来的热高分油在V1003液位控制下进入热低压分离器(V1005)。
热低分气气相与冷高分油混合后,经热低分气冷却器(E1003)冷却到40℃进入冷低压分离器(V1006)。
自V1005底部出来的热低分油进入分馏部分的脱丁烷塔第29层塔盘。
自V1006底部出来的冷低分油分成两路,一路作为轻烃吸收塔(T1011)的吸收油,吸收完轻烃的富吸收油品由T-1011的塔底泵P-1016再打回进冷低分油的进脱丁烷塔线。
依次经冷低分油/柴油换热器(E1004)、冷低分油/减一线换热器(E1005A,B)、冷低分油/减二线换热器(E1014)和冷低分油/减底油换热器(E1015),分别与柴油、减一线油、减二
线油和减底油换热后进入脱丁烷塔第22层塔盘。
V1004底部排出的含硫污水、V1006底部排出的含硫污水及分馏部分V1007、V1008排出的含硫污水合并,送至装置外。
V1006气相先进入低分气缓冲罐(V1022)后,进入低分气脱硫塔(T1010)底部。
脱硫使用的贫胺液由干气脱硫装置提供,外来贫胺液与柴油在套管换热器(E1024)换热后,进入缓冲罐(V1024),经贫胺液泵(P1017/A、B)加压后,进入低分气脱硫塔(T1010)上部,T1010内装三层填料,贫胺液与低分气在填料塔内逆流接触,脱除低分气中的硫化氢,塔顶脱硫低分气在压控条件下去PSA装置,塔底富胺液靠自压返回干气脱硫装置再生后,返回加氢裂化装置循环使用。
轻烃吸收塔(T1011)内装两层填料,来自脱丁烷塔、脱乙烷塔的两股塔顶气混合后进入塔底空间,来自反应部分的冷低分油作为吸收油进入塔顶空间,在填料内进行汽液接触,完成吸收过程。
塔顶气体在压力控制下去装置外脱硫,塔底富吸收油经富吸收油泵(P1016A,B)升压后与冷低分油混合进入脱丁烷塔。
1.2分馏系统流程
自反应部分来的热低分油和换热后的冷低分油分别进入脱丁烷塔(T1001)第28、22层塔盘,T1001共有40层浮阀塔盘。
塔顶气经脱丁烷塔顶空冷器(A1002)、脱丁烷塔顶后冷
器(E1009)冷却至40℃后进入脱丁烷塔顶回流罐(V1007)进行油、水、气三相分离。
罐中分离出的塔顶干气在压力控制下至轻烃吸收塔(T1011);V1007的油相分两路,一路经脱丁烷塔顶回流泵(P1003A,B)升压后在流量和塔顶温度串级控制下作为T1001回流。
另一路经脱乙烷塔进料泵
(P1004A,B)升压后在V1007液位和流量串级控制下进入脱乙烷塔(T1002)的第二段填料上部;V1007分水包排出的含硫污水与反应部分含硫污水一起排出装置。
脱丁烷塔底油在流量及T1001液位控制下作为常压塔(T1003)的进料。
T1001热量由塔底重沸炉(F1002)提供,脱丁烷塔底油经脱丁烷塔底重沸炉泵(P1006A,B)升压后分两路在流量控制下进入F1002加热后返回到T1001底部。
F1002的出口温度由调节F1002燃料气量来控制。
脱乙烷塔(T1002)设置3段散堆填料。
塔顶气相经脱乙烷塔顶冷凝冷却器(E1010)冷却至40℃后进入脱乙烷塔顶回流罐V1008,V1008的压力通过调节塔顶气的排出量来控制,塔顶气体去轻烃吸收塔(T1011)回收液态烃。
V1008液体经脱乙烷塔顶回流泵(P1005A,B)升压后全部作为塔顶回流。
脱乙烷塔采用重沸器(E-1013)汽提,汽提热源为航煤。
塔底物流经液化石油气冷却器(E1016)冷却至40℃作为液化气送出装置。
脱丁烷塔底油分四路在流量控制下进入常压塔进料加热
炉(F1003)加热至350℃进入T1003第53层塔盘,T1003设置60层浮阀塔盘,炉出口的温度由调节F1003燃料气量来控制。
塔顶气相经常压塔顶空冷器(A1003)冷却至54℃后进入常压塔顶回流罐(V1009),V1009的压力通过调节燃料气的进入或排出量来控制,从而使T1003的操作压力恒定。
由V1009排出的低压燃料气体引至火炬系统。
由V1009底部抽出的塔顶液经常压塔顶回流泵(P1007A,B)升压后在流量和塔顶温度串级控制下作为T1003的塔顶回流;V-1009内多余的油品经轻石脑油泵(P-1026)升压后经轻石脑油冷却器(E1011)冷却至40℃,在流量及V1009液位控制下作为轻石脑油产品出装置。
V1009分水包排出的污水进入装置内的含油污水系统。
重石脑油馏份自T1003第15块板抽出,自流进入有10块浮阀塔盘的重石脑油汽提塔(T1004),该塔的进料流率由塔底液位来控制,T1004顶油气返回到T1003第14块塔板。
T1004热量由重石脑油汽提塔底重沸器(E1007)提供,其热源为航煤,重沸器的换热量由热源的旁路和进口调节阀控制。
汽提后的重石脑油产品由T1004底抽出,经重石脑油泵(P1008A,B)升压后经重石脑油空冷器(A1004)冷却至60℃,再进重石脑油冷却器(E1012)冷却至40℃后在流量控制下送出装置。
航煤馏份自T1003第29块板抽出,自流进入有10块浮。