加氢裂化工艺的进展和发展趋势
《加氢裂化工艺概况》课件
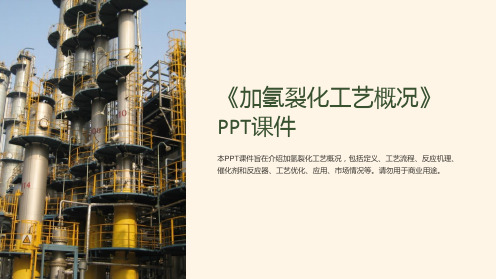
市场情况
加氢裂化工艺的发展趋势
未来加氢裂化工艺将需求更高的能量稳定性 较好的催化剂,以提高催化剂的使用寿命和 降低成本。
市场规模及前景
由于加氢裂化技术的广泛应用,市场规模不 断扩大,前景良好。
结论
1 加氢裂化工艺的优势
可以将低成本原材料转化为高价值产品,特别是汽油产量较大。
2 发展前景及挑战
随着市场不断变化与技术进步,加氢裂化工艺将面临更多新的挑战和机遇。
《加氢裂化工艺概况》 PPT课件
本PPT课件旨在介绍加氢裂化工艺概况,包括定义、工艺流程、反应机理、 催化剂和反应器、工艺优化、应用、市场情况等。请勿用于商业用途。
加氢裂化定义
1 概念
加氢裂化是一种石油加工工艺,通过将石油原料加热、加压和加氢在催化剂作用下裂解 成较短的碳链烷烃和高芳烃,以改善其性能。
Байду номын сангаас
在加氢裂化过程中,催化剂经过反应
后受到磨损、污染等影响。因此,再
生催化剂是保证工艺效果的一项重要
措施。
应用
加氢裂化在石油化工中的应用
广泛应用于石油化工、炼油厂、石化企业等行业 中,具有重要的战略地位。
原料来源及产品种类
石油加工厂获取的原材料主要是来自于油田的原 油,产品种类涵盖了汽油、柴油等多种石化产品。
•等
固定床反应器原理及分类
• 原理:石油原料从上面输入,反应产物 由下面输出;催化剂填充在反应器床内, 氢气从反应器底部输入,避免了反应模
• 型分类变:化横。通流固定床反应器、纵向通流 固定床反应器等。
工艺优化
1
温度及压力的影响
加氢裂化反应处于高温、高压条件下
催化剂的再生
2
进行的,因此温度和压力的掌握对工 艺效果影响很大。
有关加氢裂化技术的应用现状与趋势分析

有关加氢裂化技术的应用现状与趋势分析摘要为了生产清洁燃料油品,我们通常会把劣质馏分油轻质化,该过程便是加氢裂化技术。
面对日益严格化的运输燃料环境法规,加氢裂化技术不仅受到了重视,而且有着非常光明的发展前景。
本文着重分析了加氢裂化技术的应用现状,并对加氢裂化技术的发展趋势进行展望。
关键词加氢裂化技术;应用现状;发展趋势;分析0引言加氢裂化技术诞生于上个世纪的五十年代,经过六十多年的发展,该技术不仅日臻完善,而且更加符合当前石油工业的要求。
在不同的发展时间段,加氢裂化技术也体现出了不同的技术特征,特别是在工艺方面、催化剂均有自己时代特色。
例如,在以往,加氢裂化技术主要是两段加工工艺,而现在,加氢裂化技术主要是单段工艺、单段串联供工艺。
目前,人们对于油品的清洁程度要求越来越高,加氢裂化原料原料重量也相应地提高,其技术设备同样呈现出了大型化的发展趋势。
今天的石油产业面临着巨大的市场需求,为了提高石油产业的节能生产、高效生产,面对不断提高重量的原料加工状况,更加节能、更加高效的加氢裂化技术得到了广泛应用。
1 加氢裂化技术的应用现状不断攀升的汽车保有量需要消耗大量的石油产品,石油产品的市场需求十分巨大,这使得今天的炼油商往往希望能够利用对渣油与HVGO等较重原料油的加工来获得更高的利润水平,但是,由此导致的加氢裂化设备运转时间短、产品收率低以及氢耗相对较高等问题始终无法得到较为有效的解决。
由此可见,能效高、成本低的加氢裂化技术是当前全球炼油行业的迫切需求,应该成为今后催化剂生产企业和工艺设计企业的关注重点。
石油化工协会对2020年之前现有与将建的加氢裂化装置和制氢装置生产能力的增长情况进行了分析与预测(具体见表1),具有重要参考价值。
2 渣油的加氢裂化技术现状由于目前全世界范围存储着数量非常巨大渣油这种非常规超重原油资源,因此,我们可以预见渣油的加氢裂化技术必然会在未来的数十年内保持高速的增长状态。
渣油的加氢裂化技术能够把渣油这种原料转变成为市场价值非常高的石油产品,HSFO(高硫燃料油)、柴油和重油(储量非常大)之间的价格差异非常大,将重油转变为市场所需要的石油产品,可以帮助炼油商获得巨额的经济利益,因此,在巨大经济利益的驱动之下,必然会有越来越多的炼油商越来越青睐于渣油的加氢裂化技术。
《加氢裂化工艺》课件
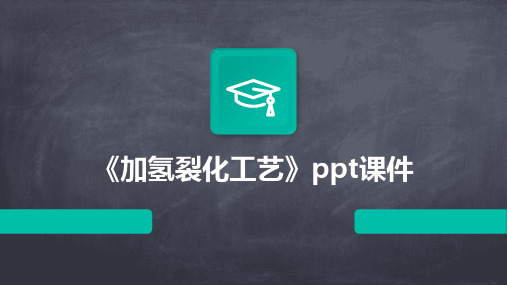
反应器的设计应考虑压力降、温度分布、催化剂装填量等因素,以确 保原料油在最佳条件下进行反应。
04
反应器的操作应控制适当的反应温度和压力,以获得所需的加氢裂化 产物。
加热炉
加热炉是加氢裂化工艺中用于 加热原料油的关键设备。
加热炉通常采用管式加热炉, 炉管内通过原料油,炉管外燃 烧燃料油或天然气,通过热传 导和热辐射将热量传递给原料
技术发展趋势与展望
高效催化剂
研发高效、稳定的催化剂是加氢裂化工艺的重要 发展方向。新型催化剂可提高反应活性和选择性 ,降低能耗和原料消耗,提高产品收率和质量。
智能化控制
智能化控制技术可以提高加氢裂化工艺的安全性 和稳定性。通过实时监测、自动控制和优化操作 ,可降低人工操作成本和事故风险,提高生产效 率。
压缩机的设计应考虑压缩比、 输送能力、机械效率等因素, 以确保气体和液体能够被顺利 压缩和输送。
压缩机的操作应控制适当的入 口和出口压力,以防止气体和 液体在压缩过程中发生泄漏和 堵塞。
分离器
分离器是加氢裂化工艺中用 于分离液体和气体的关键设
备。
1
分离器通常采用立式或卧式 分离器,通过重力或离心力 的作用将液体和气体进行分
绿色低碳发展
随着环保意识的提高,低碳、环保的加氢裂化工 艺成为未来的发展趋势。通过优化反应条件、降 低能耗和减少废物排放,实现加氢裂化工艺的绿 色低碳发展。
拓展应用领域
随着市场需求的变化,加氢裂化工艺的应用领域 也在不断拓展。例如,在生产高品质润滑油、石 蜡、高纯度溶剂等化学品方面,加氢裂化工艺具 有广阔的应用前景。
环保要求与处理措施
01
02
03
04
加氢裂化工艺应符合国家和地 方环保法规要求,确保排放的 废气、废水等污染物达到标准
加氢裂化技术发展现状及展望

加氢裂化技术发展现状及展望摘要:近些年,随着社会的发展,带动了我国科学技术水平的进步。
在加氢裂化生产清洁油品过程中,煤油馏分和柴油馏分中有许多可以通过创新工艺,生产出清洁特色产品。
为适应清洁化的发展趋势,综合利用系列加氢技术,开发了系列高端、特种、专用和差异化的特种油生产技术,并逐步实现工业应用,进一步增加产品效益。
关键词:加氢裂化技术;改造;发展趋势引言加氢裂化技术是在原油的基础上通过二次改造的方式来更好的提高石油质量,通过此种技术所研发生产出来的石油化工产品具有清洁性的特征。
特别是在当前现代科学技术不断创新的时代背景下,我国加氢裂化技术逐渐与世界水平接轨,逐渐朝着绿色节能、高效科学的方向转变。
对此,笔者以加氢裂化技术为主要研究内容,对其改造及其发展趋势进行简要分析与着重探讨。
1加氢裂化技术的改造在现代科学技术创新的驱动之下,加氢裂化技术装置得到了跨越式发展,并且进一步加快与国际化的接轨进程。
在应用原有加氢裂化装置的基础上,采用了加氢裂化改造技术,应用“延迟焦化+加氢处理+催化裂化”方案,对原有的250万吨/常年减压装置予以改造,常压分馏出的175℃石油脑送入下游重整装置的预加氢加工;175~220℃的轻柴油调和组分;220~350℃的重柴油送下游加氢装置进行进一步精制;常压重油经减压分馏,生产的减压渣油将会去延迟焦化装置进一步加工处理,分出的直流蜡油、焦化蜡油去催化原料预处理装置。
最初所使用的加氢裂化装置以串联尾油全循环工艺为主,严格按照4:1的比例调配加工原料油,进而形成了具有混合性特征的减一线、减二线和减三线混合蜡油。
后期对设备进行进一步检修,增设航煤汽提塔,从而研发了航煤产品,其中所需要的氢气均来自与氢气管网、渣油加氢装置中的PSA部分。
在检修工作完成后,要定期更换催化剂,通常为FF-46、FC-16B,加工方案由此前的整体循环调整为一次性通过的方式。
2改造后加氢裂化技术的优势2.1原料适应性沸腾床加氢裂化原料适应性强,能够加工瓦斯油、常压渣油、减压渣油、煤液化产品、沥青、页岩油和油砂等。
加氢裂化工艺的进展和发展趋势
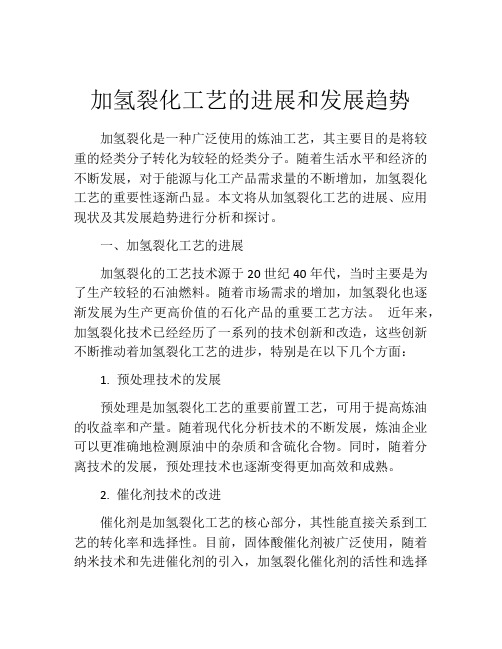
加氢裂化工艺的进展和发展趋势加氢裂化是一种广泛使用的炼油工艺,其主要目的是将较重的烃类分子转化为较轻的烃类分子。
随着生活水平和经济的不断发展,对于能源与化工产品需求量的不断增加,加氢裂化工艺的重要性逐渐凸显。
本文将从加氢裂化工艺的进展、应用现状及其发展趋势进行分析和探讨。
一、加氢裂化工艺的进展加氢裂化的工艺技术源于20世纪40年代,当时主要是为了生产较轻的石油燃料。
随着市场需求的增加,加氢裂化也逐渐发展为生产更高价值的石化产品的重要工艺方法。
近年来,加氢裂化技术已经经历了一系列的技术创新和改造,这些创新不断推动着加氢裂化工艺的进步,特别是在以下几个方面:1. 预处理技术的发展预处理是加氢裂化工艺的重要前置工艺,可用于提高炼油的收益率和产量。
随着现代化分析技术的不断发展,炼油企业可以更准确地检测原油中的杂质和含硫化合物。
同时,随着分离技术的发展,预处理技术也逐渐变得更加高效和成熟。
2. 催化剂技术的改进催化剂是加氢裂化工艺的核心部分,其性能直接关系到工艺的转化率和选择性。
目前,固体酸催化剂被广泛使用,随着纳米技术和先进催化剂的引入,加氢裂化催化剂的活性和选择性都得到了显著提高。
例如,高选择性诱导合成制备的催化剂在加氢裂化过程中表现出了优异的性能,同时也推动了合成技术的发展。
3. 堆积结构和反应器设计的优化根据加氢裂化工艺的不同工艺特点,不同的堆积结构和反应器设计都对工艺的转化率和选择性有着不同的影响。
例如,堆积结构越松散,反应热能扩散越强,反应能力也更强,但同时也会降低选择性。
因此,工艺中的堆积结构和反应器设计的优化是持续发展的重要方向。
二、加氢裂化工艺的应用现状目前,加氢裂化广泛应用于炼油和化工生产领域,尤其是石油化工和煤油化工行业。
在炼油工艺中,加氢裂化常用于生产高辛烷值汽油、航空煤油等高附加值产品。
而在化工生产领域,加氢裂化则应用于制备丙烯、苯乙烯、乙烯等一系列的重要合成原料。
加氢裂化工艺在炼油和化工工艺中的应用还存在一些问题。
渣油加氢裂化技术应用进展,值得关注!

渣油加氢裂化技术应用进展,值得关注!【本期内容,由上海神农冠名播出】随着国家对于环境保护、发展质量以及资源节约的重视逐渐加强,石油炼化工业也面临新的挑战,本文就为大家深度解读一下渣油深度加氢裂化技术的应用现状和研究新进展,希望七友们与小七一起探讨这个美妙的领域!渣油加氢裂化技术应用进展当前我国经济发展进入“新常态”,更加注重发展质量、环境保护和资源节约。
实现能源清洁生产与高效利用是我国炼油工业绿色清洁可持续发展面临的主要难题。
目前,国际油价低位运行,炼厂加工重劣质原油不再具备明显经济性。
但长远来看,原油重劣质化的发展趋势不可避免,包含减黏、焦化、渣油加氢等技术在内的重油加工技术依然是未来需要重点应用和持续开发改进的关键技术。
相比减黏、焦化等热加工过程,渣油加氢技术因其具有很强的原料适用性和加工灵活性,能够实现渣油的清洁高效利用,是应对原油重劣质化这一挑战的关键技术手段。
渣油加氢技术按用途主要分为加氢处理和加氢裂化两种。
渣油加氢处理技术主要是固定床加氢处理,工艺成熟,用于渣油改质作为催化裂化装置的原料,转化率通常只有15%~20%。
渣油加氢裂化技术主要分为沸腾床和悬浮床两种,用于劣质渣油转化生产动力燃料。
沸腾床加氢裂化技术可用来加工高残碳、高金属含量的劣质渣油,兼有裂化和精制双重功能,转化率(60%~80%)和精制深度高;但氢压较高(>15MPa),对催化剂也有特殊要求。
渣油悬浮床加氢裂化技术首要标志就是转化率高、排出的尾油量少。
相比于沸腾床加氢裂化,悬浮床加氢裂化的转化率普遍可达到90%以上,体现出明显的优势,但在工业化应用方面尚不如沸腾床成熟和普遍。
技术应用现状和对比分析1渣油沸腾床加氢裂化技术>>>>应用现状世界上渣油沸腾床加氢裂化技术主要有Axens公司的H-Oil技术、CLG(ChevronLummusGlobal)公司的LC-Fining技术以及中国石化集团公司的STRONG技术。
加氢裂化技术的新进展
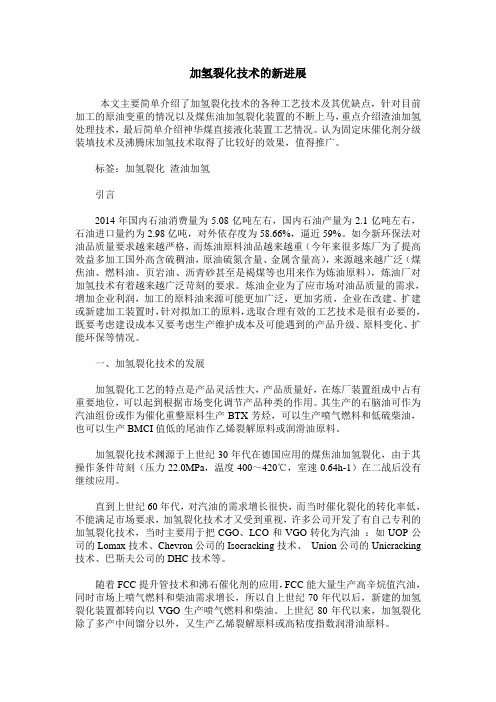
加氢裂化技术的新进展本文主要简单介绍了加氢裂化技术的各种工艺技术及其优缺点,针对目前加工的原油变重的情况以及煤焦油加氢裂化装置的不断上马,重点介绍渣油加氢处理技术,最后简单介绍神华煤直接液化装置工艺情况。
认为固定床催化剂分级装填技术及沸腾床加氢技术取得了比较好的效果,值得推广。
标签:加氢裂化渣油加氢引言2014年国内石油消费量为5.08亿吨左右,国内石油产量为2.1亿吨左右,石油进口量约为2.98亿吨,对外依存度为58.66%,逼近59%。
如今新环保法对油品质量要求越来越严格,而炼油原料油品越来越重(今年来很多炼厂为了提高效益多加工国外高含硫稠油,原油硫氮含量、金属含量高),来源越来越广泛(煤焦油、燃料油、页岩油、沥青砂甚至是褐煤等也用来作为炼油原料),炼油厂对加氢技术有着越来越广泛苛刻的要求。
炼油企业为了应市场对油品质量的需求,增加企业利润,加工的原料油来源可能更加广泛,更加劣质,企业在改建、扩建或新建加工装置时,针对拟加工的原料,选取合理有效的工艺技术是很有必要的,既要考虑建设成本又要考虑生产维护成本及可能遇到的产品升级、原料变化、扩能环保等情况。
一、加氢裂化技术的发展加氢裂化工艺的特点是产品灵活性大,产品质量好,在炼厂装置组成中占有重要地位,可以起到根据市场变化调节产品种类的作用。
其生产的石脑油可作为汽油组份或作为催化重整原料生产BTX芳烃,可以生产喷气燃料和低硫柴油,也可以生产BMCI值低的尾油作乙烯裂解原料或润滑油原料。
加氢裂化技术渊源于上世纪30年代在德国应用的煤焦油加氢裂化,由于其操作条件苛刻(压力22.0MPa,温度400~420℃,室速0.64h-1)在二战后没有继续应用。
直到上世纪60年代,对汽油的需求增长很快,而当时催化裂化的转化率低,不能满足市场要求,加氢裂化技术才又受到重视,许多公司开发了有自己专利的加氢裂化技术,当时主要用于把CGO、LCO和VGO转化为汽油:如UOP公司的Lomax技术、Chevron公司的Isocracking技术、Union公司的Unicracking 技术、巴斯夫公司的DHC技术等。
加氢裂化原料

加氢裂化的趋势及原料相关说明
1. 加氢裂化的趋势
燃料油、润滑油及化工原料正朝着更加符合环保要求及高使用性能的情节油料方向发展,追求低硫、低烯烃和低芳烃含量及异构化性能强的产品目标,加氢及加氢裂化在炼油行业中的地位日益突出。
2.加氢裂化的原料范围非常宽,最轻的石脑油直至渣油或煤,产品则有液态烃直至润滑油。
加氢裂化可以生产汽油、煤油、柴油、轻芳烃、乙烯原料、润滑油基础油等。
由于催化剂等技术的革新,高压力降至10-15MPa。
3.加氢裂化对原料的要求:
加氢裂化反映的特点是异构化能力很强,基本不发生环化反应,不能制取环数更多和正构烃较多的产品,可生产性能优异具有大量异构烷烃的石脑油、煤油、柴油及润滑油等产品;若用断环选择性强的催化剂,可制取环状烃比例较大的轻质产品,如催化重整原料,煤油、柴油等。
原料组分或馏分对加氢裂化制取不同目的产品影响不大,但为了制取某种产品,在选择原料时还以采用接近目的产品要求的族组成的油料为佳。
影响加氢裂化装置长周期运行的主要因素是采用的原料,但在讨论对原料指标要求时不能脱离催化剂及工艺,因为三者是相互关联又相互制约的。
由于进料性质对整个加氢反应影响很大,所以在操作时应尽量保证进料符合要求,以确保催化剂能有较长的寿命。
- 1、下载文档前请自行甄别文档内容的完整性,平台不提供额外的编辑、内容补充、找答案等附加服务。
- 2、"仅部分预览"的文档,不可在线预览部分如存在完整性等问题,可反馈申请退款(可完整预览的文档不适用该条件!)。
- 3、如文档侵犯您的权益,请联系客服反馈,我们会尽快为您处理(人工客服工作时间:9:00-18:30)。
辽宁石油化工大学中文题目加氢裂化工艺的进展和发展趋势教学院研究生学院专业班级化学工程0904学生姓名张国伟学生学号 01200901030412完成时间 2010 年6月20日加氢裂化工艺的进展和发展趋势张国伟(辽宁石油化工大学抚顺113001)摘要:加氢裂化是油料轻质化的有效方法之一,且原料适应性强,他可以将馏分油到渣油的各种油料转化为更轻的油品,随世界范围内原油变重,重油加氢裂化技术发展较快。
本文主要介绍了重油高压和中压加氢裂化技术的特点,阐述了固定床、沸腾床、移动床、悬浮床重油加氢裂化技术在世界范围内工艺发展趋势。
关键字:加氢裂化;工艺;技术特点; 发展趋势Hydrocracking process of development and trendsZhang guowei(Liaoning petrochemical industry university fushun 113001)Abstract:The hydrocracking is one of effective methods which transfer fuel oils to light one , and raw material is uncompatible.Tt may transform range from the fraction oil to residual oil of each kinds of fuel oils to a lighter oil quality. Accompanying with the crude oil change heavy ,the heavy oil hydrocracking technological development is pretty quick.This article mainly introduce the characteristics of the heavy oil hydrocracking technology in high pressure and mid-presses, The article elaborates the fixed bed, the ebullition bed, the moving bed, hang the floating floor heavy oil hydrocracking technology in the worldwide scale and the craft trend of development. Key word:hydrocracking; artwork; tech- characteristic; development tendency重油加氢裂化工艺是重质油轻质化的重要手段之一,其最大优势在于可以根据加工原料油类型的不同和市场对各类产品需求的变化, 通过在高温、氢气、催化剂和高压或中压的条件下, 调整工艺条件使重油发生裂化反应, 转化为气体、汽油、煤油、柴油等各种清洁马达燃料和优质化工原料,最大限度满足市场的不同需求。
按反应压力为7. 0~10. 5 MPa 和> 10.5 MPa的划分标准,加氢裂化工艺可以分为中压加氢裂化或高压加氢裂化。
可加氢裂化的原料主要有减压馏分油、常压渣油、减压渣油、脱沥青油等重质油。
1高压和中压加氢工艺选择在较高压力条件下操作可以得到各种优质产品,尤其可以得到多种中压加氢裂化得不到的产品,但建设投资及操作费用明显增加。
若在中压下操作,将直接影响到原料油中的杂质脱除、芳烃饱和及开环等反应效果,但装置的建设投资及操作费用均较高压降低30 %[1 ] 。
在工业上采用何种加氢裂化技术,应根据企业的原料来源,对目的产品的需求及对建设装置的投资来选用,这样才能为企业带来更大的经济效益。
1.1 重油高压加氢裂化技术的特点重油高压加氢裂化技术使用的催化剂有加氢和裂化2 种作用, 因此具有原料适应性强、操作灵活性大、转化率高、产品质量好等特点。
原料适应性强: 高压加氢裂化的原料可以是催化裂化循环油、焦化馏分油、脱沥青油、常减压渣油等。
此外还能有效的处理含金属、硫、氮、残炭等杂质含量高的劣质原料油。
操作灵活性大: 重油高压加氢裂化技术一般分为一段加氢裂化和二段加氢裂化, 还有介于二者之间的串联流程。
从操作方式来分, 有一次通过流程和循环流程。
选择哪种流程, 由原料油的性质、产品结构、装置规模来确定, 其经济效益是决定因素。
转化率高: 如果采用固定床二段流程, 以减压馏分油和循环油为原料生产汽油和航煤, 其转化率可以达到90 %以上; 而采用固定床一段流程, 转化率也可达80 %以上; 沸腾床加氢裂化重油的转化率为65 %~90 %; 悬浮床加氢裂化重油的转化率为90 %以上; 移动床加氢裂化重油的转化率为60 %~90 %。
产品质量好[2]: 由于加氢裂化过程存在氢气, 因而抑制了叠合和缩合反应, 避免了大量焦炭和低价值产物的生成, 加氢裂化产物中不含烯烃, 氮、硫的含量也非常少, 所以产品的色泽、胶质及安定性都很好, 产品中异构烷烃高于平衡比例, 因此喷气燃料的冰点和柴油的凝点都很低。
总的来看, 重油加氢裂化产品的质量好。
1.2中压加氢裂化裂化技术的特点对于中压加氢裂化不论是加氢裂化所得重整原料,喷气燃料馏分、柴油馏分、还是尾油馏分,其主要性质的优劣,均与原料油中的环状烃含量有关。
重石脑油芳潜以石蜡基原料较低,中间基原料则较高;轻柴油的十六烷值虽然较高,但中间基原料生产的喷气燃料馏分的芳烃含量和烟点均不合格。
属环烷基原料油的中东油更是如此,除沙中、伊轻VGO2 外,其余几种原料所得喷气燃料馏分的烟点都不合格。
除石蜡基原料油外,中压加氢裂化生产的喷气燃料达不到规格指标烟点> 25 mm ,芳烃< 20 %的要求。
造成芳烃含量高、烟点低的主要原因是原料馏分较重,环状烃含量高且结构较为复杂,而在中压下受热力学条件限制,致使芳烃饱和深度不够,不宜裂解所致。
当压力升高,热力学条件得到改善。
反应温度也可适当提高,有利于芳烃转化。
压力增加化主要产品质量均得到优化。
随着压力的提高,重石脑油的芳潜含量上升;喷气燃料的芳烃含量降低、烟点提高、完全满足了规格指标;柴油的硫含量降低、十六烷值明显提高,均达到了欧Ⅳ清洁柴油排放标准。
2 重油加氢裂化技术的发展趋势重油加氢裂化技术属UOP 和CLG这两大加氢裂化技术比较成熟,在世界范围内进行生产适用最多,同时此技术也比较先进。
2. 1 HyCycle Unicracking 技术[3]2001 年,UOP 公司推出了HyCycle Unicracking工艺。
该技术最初是为完全转化的加氢裂化而设计的。
HyCycle Unicracking 工艺的某些方面也可用于现有装置的技术改造,使炼厂在现有的操作压力下生产优质产品。
HyCycle Unicracking 工艺通过针对性加氢的优化措施,使加氢裂化装置的裂化功能与加氢功能分离开来,分别优化,在得到最大收率的同时提高产品质量。
在较低压力下操作时,通过重烃的选择性裂解和细致的氢气管理,可比传统的加氢裂化过程降低氢耗20 %。
工艺装置包括一台HyCycle 分离/ 补充精制反应器、反向串联的反应器和设计构造新颖的分馏塔。
工艺的主要优点是生产较重产品时氢耗低、选择性高。
与其他全转化工艺相比,中间馏分油收率可提高5 %以上。
氢耗的下降和过程热的更有效利用,使总操作成本下降15 %。
另一个重要的工艺特征是操作压力可以降低。
与通常情况相比, HyCycle Unicracking 的设计压力一般低25 %。
设备的改进使总成本下降10 %之多。
主要设备和流程见图12. 2 改进的部分转化Unicracking( APCU) 技术[4]APCU 工艺是UOP 专利技术HyCycle Uni2cracking 工艺的延伸。
与缓和加氢裂化相比,APCU技术在低转化率(20 %~50 %) 和中等压力( < 10MPa) 下,以比全转化装置低得多的投资在产品质量上实现了跨跃。
工艺设计独特,可独立控制最终柴油和FCC 进料的质量,为炼油厂提供灵活有利的清洁燃料生产方案。
在APCU 流程中,低转化率加氢裂化装置和FCC 装置一起运转,可生产满足最严格的汽油和柴油产品规范的清洁燃料。
新工艺可达到以下目的:(1) 处理减压瓦斯油(VGO) 不需对FCC 汽油进行后处理便可直接生产超低硫汽油(ULSG) 调合组分; (2) 生产高十六烷值的超低硫柴油调合组分,提高出厂柴油质量的灵活性; (3) 同时加工其他柴油馏分进料,生产符合调合要求的超低硫柴油; (4) 同时生产能够满足重整装置进料要求的石脑油; (5)优化氢气的利用(避免产品的过度处理) ;APCU 工艺流程如图2 所示。
高硫进料与热循环氢混合,从上部连续穿过高活性预处理催化剂和馏分油选择性加氢裂化催化剂床层。
这种组合催化剂可脱除难分解的硫、氮等杂质, 饱和多环芳烃(PNA) ,并且把一部分FCC 进料转化为超低硫燃料。
在反应器压力下,离开反应器的加氢裂化产品和脱除硫的FCC 进料立即在强化热分离器( EHS)中被分离。
EHS 塔顶产品有时和共同进料一起迅速进入集成APCU 补充精制反应器进行加氢。
在给定的设计压力下,通过这种独特的连续加工过程可生产出质量最佳的馏分油产品。
FCC 进料中的芳烃避免了过度饱和,加工过程中的氢耗降至最低。
通过调整催化剂的类型、反应器的体积和反应器的温度,可调整FCC 进料质量而不损害加氢裂化馏分油的质量。
EHS 底部物流不经冷却而直接进入分离单元,避免了重质产品在高压条件下的冷却,从而更加充分地利用热能。
APCU 工艺与HyCycle Unicracking 工艺类似,采用了低单程转化率设计,可使生成气体和催化剂积炭的副反应减少到最低限度。
在较低的操作压力下,选择性开环反应使平衡向更有利于生产高质量柴油燃料的方向移动。
苛刻度低的条件下,单程转化有利于较重产品的分布。
在较低转化率模式下操作时的脱硫效果见图3 。
2.3加氢裂化加氢组合工艺[5]加氢裂化-加氢处理组合工艺是UOP公司针对加拿大Northen Lights公司特定需要提出的其流程图如图4,该工艺可以同时加工DAO、VGO和AGO进料。
由于设备台数少,氢气和反应热等可以得到充分利用,因此装置投资和操作费用明显降低。
图4UOP加氢裂化-加氢处理组合工艺2.4 CLG公司的加氢裂化工艺[6]CLG公司是是由Clevron公司和ABB lummus Global合资的一家公司,它是第一家开展馏分油催化裂化的公司,在技术工艺方面CLG公司有SSOT,SSREC和两端加氢的基础上又研发了优化部分转化,分部进料和反法续串联两段进料工艺。