加氢裂化装置生产原理及工艺流程
两段加氢裂化工艺流程
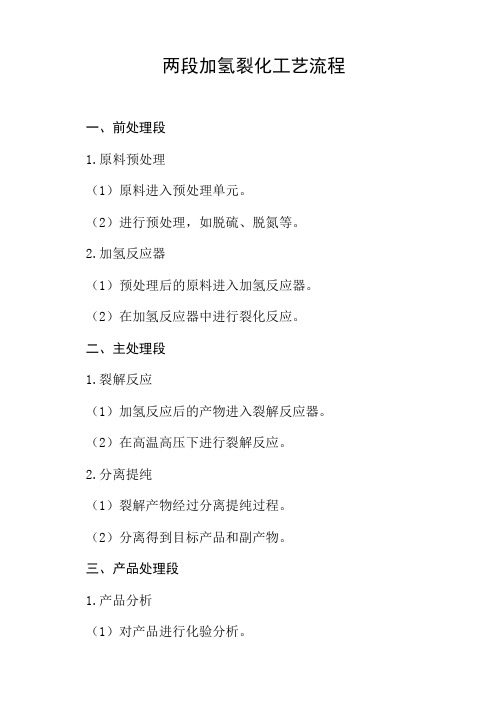
两段加氢裂化工艺流程
一、前处理段
1.原料预处理
(1)原料进入预处理单元。
(2)进行预处理,如脱硫、脱氮等。
2.加氢反应器
(1)预处理后的原料进入加氢反应器。
(2)在加氢反应器中进行裂化反应。
二、主处理段
1.裂解反应
(1)加氢反应后的产物进入裂解反应器。
(2)在高温高压下进行裂解反应。
2.分离提纯
(1)裂解产物经过分离提纯过程。
(2)分离得到目标产品和副产物。
三、产品处理段
1.产品分析
(1)对产品进行化验分析。
(2)确定产品质量和组分。
2.产品储存
(1)合格产品进行储存。
(2)设立储罐或储存设施。
四、废料处理段
1.副产物处理
(1)对副产物进行处理。
(2)如废水处理、废气处理等。
2.资源回收
(1)尽可能回收废料中的有用物质。
(2)减少废料对环境的影响。
五、安全环保措施
1.安全生产
(1)加强生产安全管理。
(2)实施安全防护措施。
2.环保措施
(1)配备污染治理设施。
(2)确保废料处理符合环保标准。
加氢装置介绍

加氢裂化装置原理、流程及特点
加氢裂化是将大分子的重质油转化为广泛使用的小分子 的轻质油的一种加工手段。可加工直馏柴油、催化裂化循环 油、焦化馏出油,也可用脱沥青重残油生产汽油、航煤和低 凝固点柴油。加氢裂化装臵是炼油厂最重要的的生产装臵之 一,在高温、高压、临氢状态下操作。 加氢裂化装臵的工艺流程主要有三种类型方法: ⑴ 一次通过法:所产尾油不参加循环。 ⑵ 部分循环法:所产尾油一部分参加循环,一部分排出 装臵。 ⑶ 全部循环法:所产尾油全部参加循环,不排尾油。 加氢裂化装臵主要设备有加氢精制反应器、加氢裂化反 应器、加热炉、高压热交换器、高压空冷器、高、低压分离 器、高温高压临氢管道、高温阀门等。详见图1、图2、图3、 图4。
2013-8-17 12
H1
H2
H3
凸台
H4
H5
s-k H6
1
图5
2013-8-17
热壁加氢反应器
13
加氢裂化装置常用材料
设备名称
加氢精制、裂化反应器 (设计温度≤ 450 ℃/设 计压力8~20MPa) 高压热交换器(温度≤ 260 ℃)
选用材质
板2.25Cr-1Mo(SA387Gr22CL2) +6.5mm(Tp309+347) 堆焊层 或+4mm(TP347)单层浅熔深堆焊 锻2.25Cr-1Mo(SA336F22CL2) + 6.5mm(Tp309+347) 堆焊层或+4mm(TP347)单层浅熔深堆焊 管程:反应流出物:管箱(碳钢、碳钼钢+4~6mm CA;铬钼钢+3mm CA)管板(碳钢、碳钼钢、铬钼钢 + 8mmTP309+347) 壳程:循环氢、原料:壳体(碳钢、碳钼钢、铬钼 钢+ 3mm CA) 管程:反应流出物:管箱(铬钼钢+3mm 1Cr18Ni9Ti 复合板 或 +6.5mm Tp309+347堆焊层 或 +4mmTP347) 管板(铬钼钢+8mmTP309+347或铬 钼钢+8mmTP410) 壳程:循环氢、原料:壳体(铬钼钢+4mm CA;或 +3mm 1Cr18Ni9Ti 复合板;或+4mmTP347;或 +6.5mm Tp309+347堆焊层) 14
HCR工艺

脱氮反应的反应热大约为2608 kJ/Nm3氢耗。
17
加氢脱氮(HDN)反应
18
加氢脱氮(HDN)反应
氮化物按其氮原子在分子中是否有孤对电子而分为碱性氮化物和非 碱性氮化物二大类,由于碱性氮化物中氮杂原子存在有自由的孤对电子 如一些胺类、二氢吲哚类和六员环杂环氮化合物,这些碱性氮化物更容 易吸附在酸性活性中心,因此对催化剂的毒性更大。但是,碱性氮化物 与非碱性氮化物之间并非有不可逾越的界限,在反应过程中非碱性氮化 物可能会转变为碱性氮化物。
处理能力401Biblioteka 0万吨/年;7加氢裂化的定义
加氢裂化定义:
在有氢气、催化剂存在以及适当的温度、压力 条件下,油料分子中的C——C键断裂,生成较小 分子的过程称为加氢裂化。
8
正碳离子反应机理
烷烃的加氢裂化是通过正碳离子反应机理进行的。 烷烃大分子首先在加氢裂化催化剂的金属中心脱氢形成
烯烃分子,烯烃分子再在催化剂的酸性中心得到氢质子而形成 正碳离子, 正碳离子进行β位 C-C 键断裂而生成较小的正碳离 子和烯烃。形成的小分子烯烃可以继续上述反应裂化成更小的 分子,也可以在金属中心上加氢后成为烷烃分子;形成的正碳 离子既可以进行断链反应,也可以在酸性中心上失去一个氢质 子而变成烯烃,并经加氢反应成为烷烃。
通常在运转初期,催化剂活性较高,反应温度可以适当低一些。运 转后期,由于催化剂表面积碳增加,催化剂活性下降,为了保持一定的 裂化深度,则反应温度就要逐步提高一些。加氢裂化是一个大量放热的 反应过程。反应温度增加则反应速度加快,但是释放出来的反应热也相 应增加,因此,必须通过在各床层注入冷氢来控制催化剂床层温度,以 保护催化剂。
加氢裂化装置优化运行生产航煤技术攻关

加氢裂化装置优化运行生产航煤技术攻关为了提高航煤的品质,同时降低其生产成本,加氢裂化装置的优化运行成为了一项具有重要意义的技术攻关。
针对这一问题,本文将从以下三个方面进行探讨:加氢裂化装置的工艺原理和流程;装置优化运行的必要性和挑战;装置优化运行中的关键技术和应用方法。
一、加氢裂化装置的工艺原理和流程加氢裂化是利用催化剂和氢气使长链烃分子在高温下断裂成短链分子的工艺。
加氢裂化装置的主要部件包括加氢反应器、分馏塔、冷却器等。
其工艺流程如下图所示:[插入图片]在这一工艺中,原料油进入加氢反应器后,在氢气的存在下,经过高温高压的加氢反应,长链烃分子被断裂成短链烃分子。
随着反应的进行,反应器中不断有新的短链分子生成,同时也有短链分子进一步加氢,生成更短的分子。
这时,分馏塔将反应产物分为轻质和重质两部分,轻质部分包含甲烷、乙烷、丙烷等气态产品,重质部分则包含乙烯、丙烯、苯等液态产品。
最后,这些产品经过冷却器冷却,通过分选装置分离出不同产品。
二、装置优化运行的必要性和挑战加氢裂化装置的优化运行主要是为了提高产品的催化裂化效率和产品品质,同时降低生产成本。
具体来说,装置优化运行的必要性体现在以下几个方面:1.提高产品的品质。
通过优化反应的温度、压力、质量比等因素,可以使产物中不同组分的含量得到有效控制,从而提高产品的品质和附加值。
2.降低生产成本。
装置优化运行可以帮助企业在提高产品品质的同时,尽可能降低生产成本,提高经济效益和市场竞争力。
3.优化反应系统的安全性。
优化加氢裂化装置的运行参数,可以有效减少一些不必要的反应失控和事故风险,保证生产过程的稳定性和安全性。
然而,装置优化运行所面临的挑战也不容忽视。
首先,加氢裂化反应机理较为复杂,其反应产物不仅涉及到烃类气体和液体,还可能出现其他非烃类物质,例如硫化物、酸性物等。
其次,不同反应物质的加工条件和要求也不尽相同,因此在不同的工作状态下对不同反应物质进行加工还需要进行针对性的优化。
加氢裂化工艺及过程 ppt课件

中国石油化工股份有限公司
CHINA PETROLEUM & CHEMICAL CORPORATION
金陵石化分公司炼油运行一部
PPT课件
1
催化加氢技术
1.0 概述 1.1 加氢裂化的沿革 1.2 国内加氢裂化技术发展历程 1.3 加氢裂化的基本原理及特点 1.4 加氢裂化原料油及产品 2.0 加氢裂化工艺流程 2.1 两段法加氢裂化 2.2 单段加氢裂化 2.3 一段串联(单程通过,未转化油全循环、部分循环)
PPT课件
12
催化加氢技术
1.2 国内加氢裂化技术的发展
◎ 50年代, 恢复了页岩粗柴油高压加氢, 发展了页岩油全馏分固定
床加氢裂化, 以及低温干馏煤焦油的高压三段加氢裂化技术。
◎ 60年代中期, 开发了107、219无定型加氢裂化催化剂和H-06沸石
催化剂;
◎ 1966年在大庆炼厂建成了40万吨/年加氢裂化装置, 加工大庆常三
为现代渣油悬浮床加氢以及馏分油固定加氢的基本模式奠定了基 础。
PPT课件
8
催化加氢技术
◎ 二战以后, 可多方获得中东油, 催化裂化技术的发展, 为重瓦斯 油(HVGO)转化生产汽油提供了更经济的手段, 加氢裂化的重要 性曾一度有所降低。
◎ 40年代末50年代初的“相关事件”, 铁路运输由蒸汽机车向柴油 机车驱动的转变,廉价天然气的供应使燃料油用量减少, FCC 发展导致富含芳烃难转化的循环油过剩, 汽车压缩比的提高和 高辛烷值汽油标准的实施等, 都迫切需要将难转化的原料加工 成汽油、柴油,导致对新的烃类转化技术需求的增产。
PPT课件
9
催化加氢技术
◎ 1959年Chevron研究公司宣布“加氢异构裂化工艺”在里蒙炼 厂
电子教案与课件:《石油加工生产技术》 04010113加氢处理工艺原理
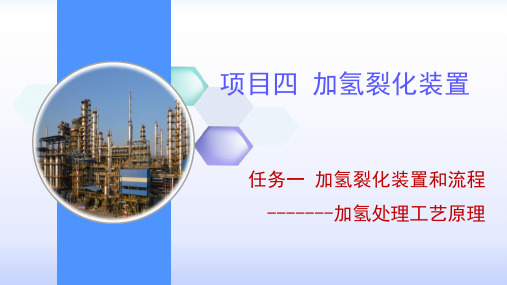
• 加氢裂化是重质原料在催化剂和氢气存在下进行的催 化加工,生产各种轻质燃料油的工艺过程。
• 用重质原料油生产轻质燃料油最基本的工艺原理就是 改变重质原料油的分子量和碳氢比,而改变分子和碳 氢比往往是同时进行的。改变碳氢比有两个途径;一 是脱碳,二是加氢。热加工过程,如热裂化、焦化以 及催化裂化工艺属于脱碳,它们的共同特点是要加大 一部分油料的碳氢比,因此,不可避免地要产生一部 分气体烃和碳氢比较高的缩合产物焦炭和渣油。
项目四 加氢裂化装置
任务一 加氢裂化装置和流程 -------加氢处理工艺原理
提出问题
燃料生产中一个重要的问题:如何合理利用石油 资源,改善产品质量,提高轻质油收率及减少大 气污染?
催化加氢为石油加工的一个重要过程,对提高原 油加工深度,合理利用石油资源,改善产品质量, 提高轻质油收率及减少大气污染都具有重要意义。 现今随着原油质量日益变差,市场和环境对优质 的中间馏分油需求越来越多,催化加氢更显重要。
4、芳烃
单环芳烃的加氢裂化不同于单环环烷烃,若侧链上有三个 碳原子以上时,首先不是异构化而是断侧链,生成相应的 烷烃和芳烃。除此之外,少部分芳烃还可能进行加氢饱和 和生成环烷烃然后再按环烷烃的反应规律继续反应。双环、 多环和稠环芳烃加氢裂化是分步进行的,通常一个芳香环 首先加氢变为环烷烃,然后环烷环断开变成单烷基芳烃, 再按单环芳烃规律进行反应。在氢气存在下,稠环芳烃的 缩合反应被抑制,因此不易生成焦炭产物。
➢六元环烷相对比较稳定,一般是先通过异构化反应转 化为五元环烷烃后再断环成为相应的烷烃。
➢ 双六元环烷烃在加氢裂化条件下往往是其中的一个六 元环先异构化为五元环后再断环,然后才是第二个六 元环的异构化和断环。这两个环中,第一个环的断环 是比较容易的,而第二个环则较难断开。
加氢精制和加氢裂化介绍
加氢精制和加氢裂化介绍加氢精制和加氢裂化介绍一、加氢精制加氢精制主要用于油品精制,其目的是除掉油品中的硫、氮、氧杂原子及金属杂质,改善油品的使用性能。
由于重整工艺的发展,可提供大量的副产氢气,为发展加氢精制工艺创造了有利条件,因此加氢精制已成为炼油厂中广泛采用的加工过程,也正在取代其它类型的油品精制方法。
㈠加氢精制的主要反应加氢精制的主要反应有:1、加氢脱硫2、加氢脱氮3、加氢脱氧4、重质油加氢脱金属5、在各类烃中,环烷烃和烷烃很少发生反应,而大部分的烯烃与氢反应生成烷烃。
在加氢精制中,加氢脱硫比加氢脱氮反应容易进行,在几种杂原子化合物中含氮化合物的加氢反应最难进行。
例如,焦化柴油加氢精制时,当脱硫率达到90%的条件下,脱氮率仅为40%。
加氢精制产品的特点:质量好,包括安定性好,无腐蚀性,以及液体收率高等,这些都是由加氢精制反应本身所决定的。
㈡加氢精制工艺装置加氢精制的工艺流程因原料而异,但基本原理是相同的,如图3-10所示,包括反应系统、生成油换热、冷却、分离系统和循环氢系统三部分。
1、反应系统原料油与新氢、循环氢混合,并与反应产物换热后,以气液混相状态进入加热炉,加热至反应温度进入反应器。
反应器进料可以是气相(精制汽油时),也可以是气液混相(精制柴油时)。
反应器内的催化剂一般是分层填装,以利于注冷氢来控制反应温度(加氢精制是放热反应)。
循环氢与油料混合物通过每段催化剂床层进行加氢反应。
加氢反应器可以是一个,也可以是两个。
前者叫一段加氢法,后者叫两段加氢法。
两段加氢法适用于某些直馏煤油的精制,以生成高密度喷气燃料。
此时第一段主要是加氢精制,第二段是芳烃加氢饱和。
2、生成油换热、冷却、分离系统反应产物从反应器的底部出来,经过换热、冷却后进入高压分离器。
在冷却器前要向产物中注入高压洗涤水,以溶解反应生成的氨和部分硫化氢。
反应产物在高压分离器中进行油气分离,分出的气体是循环氢,其中除了主要成分氢外,还有少量的气态烃(不凝气)和未溶于水的硫化氢。
【分享】加氢裂化工艺流程图
【分享】加氢裂化工艺流程图加氢裂化,是一种石化工业中的工艺,即石油炼制过程中在较高的压力的温度下,氢气经催化剂作用使重质油发生加氢、裂化和异构化反应,转化为轻质油(汽油、煤油、柴油或催化裂化、裂解制烯烃的原料)的加工过程。
它与催化裂化不同的是在进行催化裂化反应时,同时伴随有烃类加氢反应。
加氢裂化实质上是加氢和催化裂化过程的有机结合,能够使重质油品通过催化裂化反应生成汽油、煤油和柴油等轻质油品,又可以防止生成大量的焦炭,还可以将原料中的硫、氮、氧等杂质脱除,并使烯烃饱和。
加氢裂化具有轻质油收率高、产品质量好的突出特点。
目录概念加氢裂化的化学反应加氢裂化催化剂石油馏分加氢的影响因素加氢裂化工艺流程概念加氢裂化的化学反应加氢裂化催化剂石油馏分加氢的影响因素加氢裂化工艺流程展开编辑本段概念定义类型:石化工业术语拼音:jiaqingliehua英文名称:hydrocracking条件10-15兆帕(100-150大气压),400℃左右。
优缺点加氢裂化的液体产品收率达98%以上,其质量也远较催化裂化高。
虽然加氢裂化有许多优点,但由于它是在高压下操作,条件较苛刻,需较多的合金钢材,耗氢较多,投资较高,故没有像催化裂化那样普遍应用。
编辑本段加氢裂化的化学反应烃类在加氢裂化条件下的反应方向和深度,取决于烃的组成、催化剂性能以及操作条件,主要发生的反应类型包括裂化、加氢、异构化、环化、脱硫、脱氮、脱氧以及脱金属等。
加氢裂化①烷烃的加氢裂化反应。
在加氢裂化条件下,烷烃主要发生C-C键的断裂反应,以及生成的不饱和分子碎片的加氢反应,此外还可以发生异构化反应。
②环烷烃的加氢裂化反应。
加氢裂化过程中,环烷烃发生的反应受环数的多少、侧链的长度以及催化剂性质等因素的影响。
单环环烷烃一般发生异构化、断链和脱烷基侧链等反应;双环环烷烃和多环环烷烃首先异构化成五元环衍生物,然后再断链。
③烯烃的加氢裂化反应。
加氢裂化条件下,烯烃很容易加氢变成饱和烃,此外还会进行聚合和环化等反应。
加氢裂化
第十章加氢裂化第一节概述随着近代工业的迅速发展,要求石油炼制工业不但在数据上,而且在质量上提供更多更好的燃料油和润滑油,因而也就促进和要求对炼油技术的不断革命和改造。
催化加氢过程正是在这个前提下,为了完成石油的深度加工,最大限度的提高轻质油收率和产品质量而发展起来的新型工艺。
催化加氢过程包括为提高汽油、煤油、柴油质量的馏分油加氢精制;生产优质柴油、航空煤油、汽油或润滑油的重馏分油加氢裂化;用含碳或高含硫原油生产低硫燃料油的渣油加氢脱硫等。
石油馏分的加氢裂化是六十年代发展起来的新工艺,是近十多年来炼油技术发展的一个重要成就。
它是在较高压力(80-175大气压)、较高温度(260-480℃)和小号外部供应氢气(轻油体积比1::1000-2500)的情况下,在催化剂上进行不同的化学反应,将烃类原料转化为较低沸点生成油的催化加工过程。
加氢裂化催化剂是一种双功能催化剂,功能之一是将原料中的高沸点化合物裂化和异构化,功能之二是将原料和反应物中的烯烃等不饱和烃进行加氢使其变成饱和物。
目前以分子筛为担体或在担体上加入大量分子筛的催化剂多用于生产汽油和煤油,例如以Pd-Y型催化剂生产汽油和航空煤油有较好的活性、选择性和稳定性。
以无定型SiO2-Al2O3或SiO2-MgO为担体的非金属催化剂可用来生产低点柴油而保持较长的使用寿命。
加氢裂化过程是用加氢的办法来改变原料的碳氢比,在外界引入氢气并保持一定的氢压下,可抑制高分子缩合物和焦炭的生成;可使产品中不含烯烃而具有较好的安定性;可使原料中所含的硫、氮、氧等杂质除去;另外加氢裂化过程改变聊原料分子的结构,其产品中富有异构烃。
基于这些变化,就决定了加氢裂化过程有原料范围广、产品质量好的特点。
这对加工含硫特别是高含硫原料油,并从中制取优质产品具有十分重要的意义。
实际上加氢裂化原料油的范围极广,从粗汽油到重柴油,各种重油,甚至丙烷脱沥青油都可以加工,并生产出不同的优质产品。
《加氢裂化技术讲座》课件
03
原料性质
原料的性质对加氢裂化反应的影响较大,不同原料的化学组成、分子结
构、硫、氮等杂质含量都会影响反应的进行。因此,需要根据原料的性
质选择适宜的催化剂和操作条件。
03
加氢裂化工艺流程
加氢裂化工艺流程简述
原料油进入预处理系统,去除 杂质和水分。
预处理后的原料油进入加氢裂 化反应器,在高温高压和催化 剂的作用下进行裂化反应。
保障石油产品质量
加氢裂化技术能够提高石油产品质量 ,满足环保要求,降低油品中的硫、 氮等杂质含量,提高油品的清洁度和 稳定性。
提高轻质油收率
促进石油资源的有效利用
加氢裂化技术能够充分利用石油资源 ,提高资源的利用率,延长石油资源 的经济寿命。
通过加氢裂化技术,能够将重质油转 化为轻质油,提高轻质油收率,增加 经济效益。
催化剂活性与选择性
催化剂的活性与选择性是影响 加氢裂化技术的重要因素,需 要不断研发新型催化剂以提高
其性能。
加氢裂化技术的未来发展趋势与研究方向
高效催化剂的研发和应用
研发新型高效催化剂,提高加氢裂化反应的 转化率和选择性。
反应工艺的优化和改进
优化和改进加氢裂化反应工艺,降低能耗和 物耗,提高经济效益。
加大技术研发和创新投入,提高加氢裂化 技术的核心竞争力和经济效益。
推进智用
加强智能化和自动化技术在加氢裂化领域 的应用,提高生产效率和安全性,降低生 产成本。
加大环保技术的研发和应用,降低加氢裂 化技术的环境影响,提高企业的社会责任 感和形象。
06
结论
加氢裂化技术的重要地位与作用
多产高附加值产品的研发
研发多产高附加值产品的加氢裂化技术,以 满足市场需求。
- 1、下载文档前请自行甄别文档内容的完整性,平台不提供额外的编辑、内容补充、找答案等附加服务。
- 2、"仅部分预览"的文档,不可在线预览部分如存在完整性等问题,可反馈申请退款(可完整预览的文档不适用该条件!)。
- 3、如文档侵犯您的权益,请联系客服反馈,我们会尽快为您处理(人工客服工作时间:9:00-18:30)。
大庆石化公司炼油厂加氢裂化装置
装置特点和危险特性
加氢裂化装置生产特点和危险特性:具有炼油企 业之高温,高压,易燃易爆,高噪声且介质含H2-S,工业 粉尘,汽油等.加氢裂化工艺属高温、高压、临氢工艺 过程。技术要求高,操作难度大,危险因素多。物料 介质中含有浓度较高的硫化氢等有毒有害物质,而硫 化氢在潮湿、低温的环境下,容易产生湿硫化氢腐蚀, 容器及管线设备容易被腐蚀穿孔,或者有管线爆裂、 法兰垫片撕裂等情况,都可能发生硫化氢泄漏事故。 因此,防爆防毒是车间安全工作的重点。 装置内高温高压法兰、分馏塔、塔底热油泵、高温 高压循环油泵、产品泵,压缩机管线等部位容易着火。
注:粗线为主流程
2013年10月23日
大庆石化公司炼油厂加氢裂化装置
反应系统 自装置外来的原料油进入原料缓冲罐(D-3101),由 原料油泵(P-3101)送至原料油/柴油换热器(E3212)、原料油/尾油换热器(E-3100)加热后,再经过 自动反冲洗过滤器(SR-3101)过滤,进入滤后原料油缓 冲罐(D-3102)。滤后原料油经反应进料泵(P-3102) 升压后与氢气混合,在混氢油/反应产物换热器(E3101)与反应产物换热后,通过反应进料加热炉(F3101)加热到反应所需温度(344℃),先后进入加氢精 制反应器(R-3101)和加氢裂化反应器(R-3102),混 氢油在反应器中催化剂的作用下,进行加氢精制和加氢
2013年10月23日
大庆石化公司炼油厂加氢裂化装置
二、生产方法及反应机理
加氢裂化指在加氢反应过程中,原料油的分子有 10% 以上变小的那些加氢技术。烷烃(烯烃)在加氢 裂化过程中主要进行裂化、异构化和少量环化的反应。 烷烃在高压下加氢反应而生成低分子烷烃,包括原料 分子某一处C—C键的断裂,以及生成不饱和分子碎片 的加氢。烯烃加氢裂化反应生成相应的烷烃,或进一 步发生环化、裂化、异构化等反应。 典型的化学反应有以下:
出 方
重石脑油
航煤 柴油 尾油 合计
14.09
15.81 21.44 43.91 101.54
21135
23715 32160 65865 152314
507.24
569.16 771.84 1580.76 3655.537
16.91
18.97 25.73 52.69 121.85
2013年10月23日
除盐水自动力站 注水罐
氢气分液罐
注水泵 高压空冷器 冷高分 反应进料加热炉 滤后原料缓冲罐 冷低分 冷低分去制氢
将原料中大于 25μ以上的固 体颗粒过滤掉
循环氢换热器
冷低分油去脱气塔
过滤器
含硫污水出装置
热低分气空冷器 滤前原料缓冲罐 反应产物换热器 热高分
热低分油去脱气塔 尾油及柴油换热器 原料升压泵 反应进料泵 液力透平
加氢裂化装置培训课件
2013年10月23日
大庆石化公司炼油厂加氢裂化装置
前沿:装置简单流程介绍
2013年10月23日
大庆石化公司炼油厂加氢裂化装置
前沿:装置简单流程介绍
2013年10月23日
大庆石化公司炼油厂加氢裂化装置
一、加氢裂化装置介绍 二、生产方法及反应机理 三、工艺技术路线及流程 四、装置开停工过程中的关键操作 五、装置关键设备介绍 六、装置技术经济水平 七、装置生产中存在问题及解决措施 八、装置实际操作条件介绍 九、加氢裂化装置实际操作注意事项
2013年10月23日
大庆石化公司炼油厂加氢裂化装置
一、装置简介
加氢裂化装置于2002年10月开始筹建,2004 年6月1日工程正式中交,并于同年8月28日19时37 分实现装置一次投料成功,并生产出合格产品。由中 油第一建筑公司、大庆石化工程公司、大庆市建安集 团共同承建。装置总投资为59672.32万元,总占地 面积8479平方米。 装置的基础设计部分由中国石化工程建设公司北京 设计院完成,详细设计部分由大庆石化设计院完成。 由反应、分馏、热工和公用工程等部分组成. 加氢裂化装置承担着大庆石化公司的成品油质量, 改善产品结构,并为乙烯提供优质裂解原料的重任。
2013年10月23日
大庆石化公司炼油厂加氢裂化装置
装置特点
催化剂采用器外再生方案。 分馏塔设中段回流,回收热量,降低能耗。 蒸汽凝结水、分流塔顶冷凝水、及污水汽提净化 水回用,节省除盐水。 本装置运行条件苛刻,采用DCS进行实时控制。 为确保装置安全运行,设置紧急停车系统ESD。
2013年10月23日
2013年10月23日
大庆石化公司炼油厂加氢裂化装置
装置特点
选用抚顺石油化工研究院开发的FC-16和大庆石化究院 开发的DZN单段双剂串联一次通过工艺。 反应部分采用炉前混氢流程。 采用热高分流程,降低能耗,节省换热面积。 分馏设置脱气塔,采用分馏进料加热炉和常压塔出柴油 方案。 原料油缓冲罐采用低压燃料气保护,防止其与空气接 触。 防止原料中固体杂质带入反应床层,采用原料自动反冲 洗过滤器。 催化剂采用干法硫化工艺。 选用低氮油注氨的催化剂钝化方案。
2013年10月23日
大庆石化公司炼油厂加氢裂化装置
反应系统
冷低分气去制氢装置。冷低分油在航煤/冷低分 油换热器(E-3208)和航煤产品换热后与热低分 油混合进入脱气塔。
2013年10月23日
大庆石化公司炼油厂加氢裂化装置
3、分馏系统
航煤空冷 航煤 干气去制氢 柴油 塔顶水冷器
脱除硫化氢及C4 以下轻烃组分
2013年10月23日
大庆石化公司炼油厂加氢裂化装置
反应系统 从冷高压分离器(D-3105)分离出来的气体(循环 氢),在循环氢分液罐(D-3107)中分液后,液体 进入冷低压分离器(D-3106),气体经循环氢压缩 机(K-3102)升压后,一路作为急冷氢注入催化剂 床层;一路作为吹扫用循环气去反应进料泵(P3102)出口后路;一路与自新氢压缩机 (K-3101)来的补充新氢混合,经氢气/热高分气换 热器(E-3102)与热高分气换热后与原料油混合, 进入混氢油/反应产物换热器(E-3101),返回反 应系统。冷高分油经减压后进入冷低压分离器(D3106),继续气、油、水三相分离。热低分气相经 过热低分气空冷器(A-3102)冷却后也进入冷低压 分离器(D-3106)。冷高压分离器(D-3105)界控 脱除的含硫污水减压后与冷低压分离器(D-3106) 脱除的含硫污水汇合出装置至污水汽提装置处理,
2013年10月23日
大庆石化公司炼油厂加氢裂化装置
二、生产方法及反应机理
加氢脱硫(HDS):
R
S
+ 6H2
R
CH3+ H S 2
加氢脱氮(HDN):
R
NH + 6H2
R
CH3+ NH 3
2013年10月23日
大庆石化公司炼油厂加氢裂化装置
二、生产方法及反应机理
烯烃加氢饱和:
H3 C
CH3 + H 2 CH3
H3C
CH3 CH3
2013年10月23日
大庆石化公司炼油厂加氢裂化装置
二、生产方法及反应机理
单环芳烃加氢饱和:
R
多环芳烃加氢饱和:
+ 3H2
+ 2H2 R R
R
R
+ 3H2
R
+ 2H2
R
2013年10月23日
大庆石化公司炼油厂加氢裂化装置
二、生产方法及反应机理
芳烃加氢脱烷基:
R
+ H2
+ RH
柴油成品罐区
尾油产品52.69(43.91%)
工业氢1.85
乙烯裂解
2013年10月23日
大庆石化公司炼油厂加氢裂化装
原料加热至344℃进入精 制反应器进行脱硫、脱 氮、脱氧、脱金属反应, 以及烯烃、芳烃饱和反应
裂化反应器 循环氢分液罐
精制反应产物进 入裂化反应器进 行裂化反应
冷低分油 换热器 脱气塔 汽提蒸汽
原料油 换热器
尾油蒸汽 发生器
二中蒸汽 发生器 石脑油 重沸器 尾油空冷 尾油缓冲罐
汽提蒸汽 脱气塔底油 换热器 尾油换热器 分馏进料 加热炉 汽提蒸汽 重石脑油 柴油汽提塔 重石脑 油空冷 尾油泵 脱气塔底泵 柴油泵 航煤泵 重石脑油泵 尾油接力泵 重石脑 油水冷 尾油
2013年10月23日
大庆石化公司炼油厂加氢裂化装置
装置简介
装置设计年开工时间为8000小时,设计能力为 120万吨/年,最大生产能力140万吨/年,设计低 转化率工况下的能耗为32.43千克油/吨。 2006年装置实际生产负荷142万吨,创装置加 工能力的最大历史水平。 2008年装置全年综合能耗累计24.71千克油/ 吨,创装置历史最好能耗水平。
制氢装置
乙烯裂解
催化重整 航煤成品罐区
二套常减 压装置
减一线油4.81 减二线油13.85 减三线油2.45
加 氢 裂 化 装 置
重石脑油产品16.91(14.09%)
航煤产品18.97(15.81)
一制蜡 装置 蜡脱油 装置 制氢装 置
发汗蜡下油4.43 溶济脱蜡油4.14
柴油产品25.73(21.44%)
大庆石化公司炼油厂加氢裂化装置
1、装置物料平衡
装置物料平衡表 物料 原料油 入 方 工业氢 合计 气体 轻石脑油 W% 100 1.54 101.54 3.35 2.94 Kg/h 150000 2314 152314 5024 4415 t/d 3600 55.536 3655.537 120.5784 105.96 104t/a 120 1.85 121.85 4.02 3.53
注:粗线为主流程
2013年10月23日
大庆石化公司炼油厂加氢裂化装置
分馏系统 冷低分油在航煤/冷低分油换热器(E-3208)和航 煤产品换热后与热低分油混合进入脱气塔(C3201)第26层塔板,在脱气塔中脱除轻烃和硫化氢。 塔顶气相经脱气塔顶空冷器(A-3201)和脱气塔 顶水冷器(E-3201)冷却后进入脱气塔顶回流罐 (D-3201),回流罐顶气体去制氢装置,液体经 脱气塔顶回流泵(P-3202)打回脱气塔做塔顶回 流。脱气塔底油经泵(P-3201)送至柴油/分馏进 料换热器(E-3211)和尾油/分馏进料换热器(E3202)分别与柴油和尾油产品换热后,去分馏塔进 料加热炉(F-3201)加热至要求的温度 (346℃),之后进入主分馏塔(C-3202)第8 层塔板,在主分馏塔内实现分馏过程。分馏塔顶