ERPII-3.3物料需求计划
ERP第9讲-物料需求计划1

5. 下达订单的开始日期?
5. 提前期
物料需求计划-系统目的
使订单、预测订单、采购、委外、自制之数 量需求能达到刚好而及时的效果 由成品→半成品→原料逐阶计算真正的需求 量,以降低库存 考虑在单量、预约量的精确数量及时间,避 免造成停工待料 提供购标识码 制造/采购标识码属于库存文件中的一个项目,通常用 字母P或M来表示某物料是采购或是制造。当运行 MRP时, 这个码决定是做采购订单还是做制造订单。如果是采购项目 ,无须产生项目组件的需求;而对于制造项目,就必须利用 BOM来决定由哪些零件、部件或材料来制造这个项目。 2. 批量政策
把MPS传送给MRP
计算毛需求
计算净需求
净需求>0?
否
生成订单计划
下达订单计划
是
还处理其他项目?
结束
计划投入时间=计划产出时间-提前期
MRP编制案例
1、已知MPS为在第8个计划周期内产出 100件A产品,A产品BOM结构树如下,试 计算各物料的毛需求和计划投入量
A TL=4 C(2) TL=2 D(1) TL=1 B(1) TL=3 E(2) TL=1
1
2
3
4
5
6
7
8
100
3
1
B
毛需求量 计划投入量 毛需求量 计划投入量 毛需求量
2
1
C
1
2
D
计划投入量 毛需求量
1
2
E 计划投入量
各物料的需求量是由上至下层层分解得到的 一种物料的“计划投入量”的时间比“毛需 求”提前的时间量是由该物料的提前期决定 的 上一层物料“计划投入量”的时间即为下一 层物料的“毛需求”时间
JSERP3物料需求计划操作手册
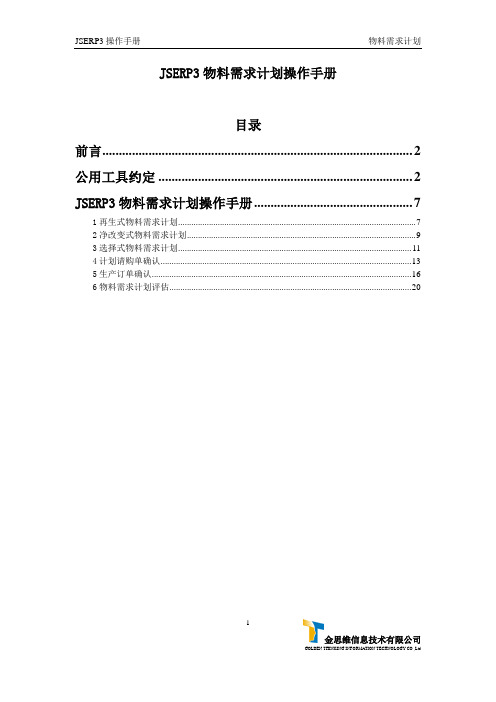
JSERP3物料需求计划操作手册目录前言 (2)公用工具约定 (2)JSERP3物料需求计划操作手册 (7)1再生式物料需求计划 (7)2净改变式物料需求计划 (9)3选择式物料需求计划 (11)4计划请购单确认 (13)5生产订单确认 (16)6物料需求计划评估 (20)12 前言物料需求计划(MRP )是计划管理子系统中核心的计划层次,物料需求计划是在主生产计划(MPS )的基础上,根据产品结构、物料计划信息、库存信息,计算出父物料对子物料的相关需求,并制定出所需子物料的生产计划和采购计划,并明确最终计划的品种、数量和加工时间进度。
公用工具约定工具图标打印点击该按钮可将当前界面显示的数据内容在打印机上打印出来。
打印预览在您打印系统资料之前,可通过点击该按钮,将当前屏幕显示的数据内容按打印格式显示在屏幕上,先查看打印效果后决定是否打印。
报表样式定义通过该按钮提供的功能,可以根据您的需要自行定义各种样式的需要输出和打印的报表3栏目设置栏目设置是用来调整界面所显示的栏目的顺序剔除不需要的栏目或自行设置栏目的标题。
第一条记录在浏览状态下,点击按钮或使用快捷键Ctrl+Home 将光标直接跳到表中的第一条记录,即将表中的第一条记录变为当前记录。
前一条记录在浏览状态下,点击按钮或使用快捷键Ctrl+Up 将光标跳到表中的上一条记录,即将表中的上一条记录变为当前记录。
查找在浏览状态下,点击按钮或使用快捷键Ctrl+F ,界面将变成编辑状态,你可在界面上的任何一个编辑框中输入您所知道的信息,也可以同时输入几个编辑框内容,输入完毕后点击“保存编辑内容”按钮,系统将根据您输入的信息进行快速查找和定位。
若只存在一条满足条件的记录,记录指针将直接跳转到该条记录上;若存在多条满足条件的记录,系统将显示一个列表对话框,你可从中选择一条您所需要的记录;否则系统将提示你没有找到您要的记录,记录指针位置不变。
后一条记录在浏览状态下,点击按钮或使用快捷键Ctrl+Down 将光标跳到表中的下一条记录,即将表中的下一条记录变为当前记录。
MRPⅡ-ERP之第6章物料需求计划ppt课件
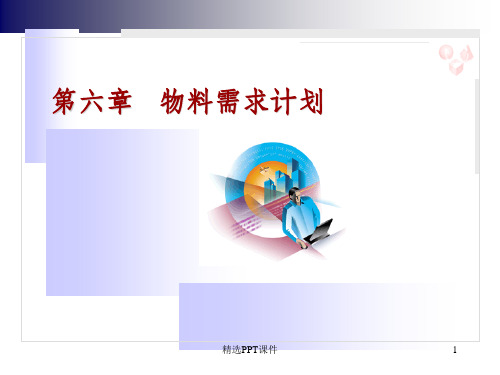
26
Gross Requirements Plan
Week
12345678
Toy Car
Required Date
100
Order release data
100
Wheel assembly Required Date
200
Order release data
200
Body
Required Date
1 week
Toy
Car
4
5
6
7
8
Time in Weeks
精选PPT课件
17
Time-Phased Product Structure
1 week
Wheel Assembly
2 weeks
1 week
Toy
Car
Body
4
5
6
7
8
Time in Weeks
精选PPT课件
18
Time-Phased Product Structure
– Body – Axles (2)
W heel A sse m b ly(2 )
Body
– Wheels (4)
A x le (1)
W he e ls (2 )
精选PPT课件
14
Cooperstown Cars, Inc.
B ill o f M a t e r ia ls f o r T o y C a r
精选PPT课件
4
A零件 实际制造周期
库存时间
附加库存时间
计划制造周期
B零件 计划制造周期
实际制造周期
外购配套 零件库存时间
第6章 ERP物料需求计划

感谢您的关注
www.第一课件网.com
计划接收量 库存量
计划订单下达 毛需求量(B) 计划接收量 库存量 计划订单下达 毛需求量 计划接收量 库存量 计划订单下达
14
1 20 20 1 9 9 5 15 15 11
5
0
21
0
0
原理: A对一项物料的计划订货的下达就同时产生了其 直接下属项目的毛需求 B他们在时间上完全一致,在数量上有确定的对 应关系 C此过程沿BOM的各个分支进行,直到所有的分 解路线都达到外购件为止。
6.2.2MRP的运算方法
1.如何确定低层物料的毛需求(生产100个X需要几个 D?) 产品 X
库存量 毛需求量 净需求量
总成 组件
A
2
100 98
98 83
B
C
15
7 46
零件
零件半 成品
83
76
76
30
D
原理: A只有在确定了上一级层次的净需求以后,才能确 定下属层次的净需求量,因为下一层次物料的需 求量取决于上一层次的需求量 B毛需求量是为了满足上一级项目的订货要求而产 生的,而不是最终产品所消耗的数量,这两个量 不一定相同。 C在物料需求计划中,下属项目的毛需求量取决于 上一级项目的净需求量,而不取决于最终产品或 主生产计划最终项目的需求量。
第十一章ERP之物料需求计划
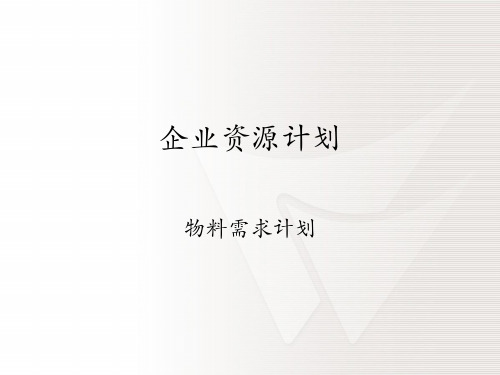
X(LT=4)
Y(LT=6)
A(1)
B(1)
A(1)
产品X、Y的BOM图(物料X的需求关系〕
C(1)
物料A的毛需求计算表
周
1 2 3 4 5 6 7 8 9 10 11 12 13
2.独立需求
当一个项目的需求不能直接从另一个项目的需求计划得到时 ,这种需求称为独立需求;否则,为相关需求。 ➢ 独立需求与相关需求的概念是相对的。例如,若生产园
珠笔,则笔的需求是独立需求,其需求数量是由预测 得 到的,而对构成笔的笔芯和弹簧之类的项目而言便是相 关需求。其需求数量是通过计划 得到的。但是,若想单 独销售笔芯,则笔芯又是独立需求。 ➢ 在编制物料需求计划时,必须认真地分析与收集独立需 求与相关需求。
5.其它因素
(1)低阶码(low level code,LLC)
➢ 低阶码,又称层次码或低层码,是系统分配给物料清单 上的每个物品一个从0至N的数字码。在产品BOM结构 中,最上层的层级码为0,下一层部件的层级码则为l, 依此类推。
➢ 一个物品只能有一个MRP低阶码,当一个物品在多个产 品中所处的产品结构层次不同或即使处于同一产品结构 中但却处于不同产品结构层次时,则取处在最低层的层 级码作为该物品的低阶码,也即取层次最低的、数字最 大的层级码。
• MRP的概念 • MRP的工作原理 • MRP处理过程 • MRP的编制案例 • MRP的更新方法 • 能力需求计划 • MRP和LRP
MRP的编制案例
例1 求毛需求及发出订货计划
• 例1 求毛需求及发出订货计划:已知MPS为在第8个计划周 期时产出100件A产品,其中A产品的BOM图见下图。
即一个项目是采购件还是制造件的标识码。采购或制造标识 码通常用一个字母(P或M)表示。当MRP运行时,该码决定 做采购订单或制造订单计划。
第九章-物料需求计划及ERP《运营管理》ppt课件

A
L=4 , 0层
12 34 5 6 78
B(1) L=3
C(2)
L=2 1层
D(1) L=1
E(2) L=1 2层
注:L:提前期 ()中数值为该零件在上层产品中的件数。
MRP的输入与输出
MRP 输入
MRP 过程
MRP 输出
主生产计划 物料清单
MRP 计算机程序
变更
订货
主报告
订货计划 时间安排
例外报告
MRP的逻辑
基本假设:
• 所有物料均经过中央库存处理,库存信息及时更新; • 订单(采购/生产)完工即为入库量; • 需求量即为库存系统的输出量;
制造 采购
库存系统
需求
MRP的处理流开程始n=0 t=1
第0层的Gt由MPS推算
推算各周期.第n层所有项目的毛需求量G(t)
确定n层次,t期净需求量N(t)
MRP-II的局限性
• 不能做到整个资源集成管理; • 企业规模扩大化,多集团、多工厂要求
协同作战,统一部署; • 整个供应链的管理;
企业资源规划 ERP
• 企业内部资源 → 系统整体资源。
• ERP是在MRP-Ⅱ的基础上扩展了管理范 围,给出了新的系统结构。
ERP的形成
ERP是建立在信息技术基础上,利用现代企业的先进管理 思想,全面地集成了企业所有资源信息,为企业提供决
二级报告
计划报告 业绩控制报告
存货记录
存货处理
物料需求计划的主要输入
(1)主生产计划 MPS Master Production Schedule
• MPS是确定每一具体的独立需求项目在每 一具体时间段内(一般为一周)的生产 数量。
ERP原理与应用-物料需求计划(MRP)

0层 X 产品(卡车) 1层 A 总成(传动器)
库存 毛需求 100
2 100
2层 B 组件(齿轮箱) 15
98
3层 C 零件(齿轮)
7
83
4层
14:17
D 毛坯(锻坯)
46 76
净需求 100 98 83 76 30
16
6. 低层码
▪ 低层码(Low Level Code)是指某个物料在所有产 品结构树中所处的最低层数,因此可以通过零部 件所在产品结构树中的层次来决定它的低层码。
可供货量 30 10 10 -25 0 0 0 0 0 -10
14:17
13
5. MRP的数据处理逻辑
时段 毛需求量
1 2 3 4 56 7 8
20
25 15 12
预计入库量
30
库存量 23 23 3 33 8 8 -7 -19 -19
净需求量
7 12
计划订货量
7 12
计划订货下达
7 12
提前期=4
ERP原理与应用
物料需求计划(MRP)
14:17
1
主要内容
1. 制造业基本方程 2. MRP能够做什么 3. 物料需求计划理论 4. MRP逻辑流程 5. MRP的数据处理逻辑 6. 关于低层码和损耗率 7. MRP运行条件及运行方式
14:17
2
1. 制造业基本方程--MRP概念公式
A*B-C=D
14:17
12
MRP的基本方法---时间分段法
例:某物料的库存状态数据为:
库存量:30 已订货量:25 需求量:65 可供货量:-10
1 2 3 4 5 6 7 8 9 10
库存量
2020年(ERPMRP管理)物料需求计划(MRP)作业细则

(ERPMRP管理)物料需求计划(MRP)作业细则PM111101文件制(修)訂履歷表文件名稱:物料需求計劃(MRP)作業細則文件編號:PM111101目錄一.物料需求計劃作業關聯 (1)二.物料需求計劃作業細則 (2)第一章總則 (2)第二章物料需求計劃(MRP)作業細則 (3)第三章實施與修訂 (4)三.附表附表124weeksRequired/ManufactureShippingPlan (5)附表2SummaryofShippingQuantity (7)四.附件附件1MRP (8)附件2MRPParameters (10)附件3MRPDemandReview (12)附件4MRPSupplyDemandSummary (14)附件5MRPRe port (16)附件6MPSbyplaningBill (17)附件7MRPReport (18)附件8MRPControlsMaintenance (20)附件9ItemMasterMaintenance (22)附件10ItemMaintenance-ProductionControl (24)第一章總則1.目的將出貨需求進行MRP展開,以取得是否需要進行物料采購的訊息。
2.指導原則1.1.滿足客戶需求,做到客戶要貨時有貨,不要貨時零庫存。
1.2依據客戶需求變更修改計劃,使計劃更具可靠性。
1.3合理利用制造資源,節約成本,增加產出。
3.范圍適合于PCE事業處各單位。
4.參考文件4.1.組裝周生產排配計劃作業系統(SM214120)。
第二章物料需求計劃(MRP)作業1.需求受入1.1交管人員將經簽核的24周出貨計劃Copy一份給企劃部,並在Lotus Notes的交管訊息公布欄內予以公布,同時通知組裝采購部門,交管公布的出貨需求表為「24wksRequired&ManufactureShipping Plan」(24周需求和制造出貨計劃)(附表1)和「Summaryof ShippingQuantity」(出貨明細表)(附表2)。
- 1、下载文档前请自行甄别文档内容的完整性,平台不提供额外的编辑、内容补充、找答案等附加服务。
- 2、"仅部分预览"的文档,不可在线预览部分如存在完整性等问题,可反馈申请退款(可完整预览的文档不适用该条件!)。
- 3、如文档侵犯您的权益,请联系客服反馈,我们会尽快为您处理(人工客服工作时间:9:00-18:30)。
2 MRP工作原理 • • • • • 逐层计算原则 MRP的输入、处理和输出 MRP中的基本数量概念 MRP的运行方式 MRP的开环和闭环
逐层计算原则 • 逐层计算原则是指MRP在计算物料需求时,应该 采用自顶向下按照产品结构层次逐层计算物料需 求量的方式。 • 逐层计算原则是MRP工作原理的重要组成部分, 它揭示了MRP计算物料需求量的基本过程形式, 是理解MRP工作原理的基础。 • 逐层计算涉及的四个方面:提前期、需求展开、 偏移和计划订单。
第3章第3节 物料需求计划
1 概述 • MRP是一种物料管理和生产方式,是ERP系统的 重要组件,它建立在MPS的基础上,根据产品的 BOM、工艺路线、批量政策和提前期等技术和管 理特征,生成原材料、毛坯和外购件的采购作业 计划和零部件生产加工、装配的生产作业计划, 从而达到有效管理和控制企业物料流动的微观计 划。
MRP应该回答的问题 [A] 生产什么?生产多少?何时生产? [B] 要用到什么?用到多少?何时用到? [C] 已经有了什么?有多少?何时使用? [D] 还缺少什么?缺少多少?何时需要? [E] 何时安排?
MRP是ERP系统的核心内容 • MRP是ERP系统的核心内容,它把ERP系统中的 许多重要组件组合在一起。 • MRP把MPS作为其基础和输入,是MRP要达到 的最终目标。 • BOM是MRP把最终产品分解成各种物料的工具, 是最终产品与物料编码和物料数量相关联的方法。 • 毫无疑问,作为一种重要的基础数据,物料编码 是整个ERP系统包括MPS和MRP组件识别和使用 物料的依据。
MRP中的基本数量概念
计划接收量
物料号 动作 毛需求 计划接收量 D 预计可用库存量 净需求 计划订单接受 计划订单下达 毛需求 计划接收量 E 预计可用库存量 净需求 计划订单接受 计划订单下达 0 20 20 0 0 0 周 1 2 20 20 0 0 3 4 5
MRP中的基本数量概念 • 订单下达(续)
逐层计算原则
• 如果第6周需 要100个A,各 物料计划订单 接受和计划订 单下达又如何?
D
LT:1周
ALT:1周B来自LT:2周CLT:1周
E
LT:1周
A:B:C 1:1:1 B:D:E 1:1:1
逐层计算原则
物料需求展开和偏臵
物料号
A B C D E 周 1 2 3 4 5 100 6 100
动作
示例 • 下面通过一个例子来介绍低层码的作用。 • 在如图4-3所示的自行车产品的BOM结构示意图 中,最终产品项目是ZXC,由2个零件A和1个组 件B组成,1个组件B由1个零件A和2个零件C组成。 • 在这里,零件A既出现在阶层1又出现在阶层2, 因此,零件A的低层码是2。
自行车产品的BOM结构示意图
MRP中的基本数量概念 • 订单下达(续)
– 订单下达之前,必须检查子项的可用性。计算机程 序检查子项的库存纪录,以确保有足够的物料可供 使用,并且如果有物料可供使用,则为特定的生产 订单分配必需的数量。如果物料不够使用,计算机 程序就会告知计划人员物料短缺的状况。 – 当采购或制造的授权下达之后,计划订单量被取消, 取而代之的是计划接收量。计划接收量是已经发给 制造部门或供应商的订单,表示制造或者采购的承 诺。
再生式MRP • 在再生式MRP运算中,MPS中列出的每一个最终 产品项目的需求都进行分解,每一个需要的BOM 文件都被访问,每一个相关物料的库存状态记录 都要更新,每一个物料的毛需求量和净需求量都 要重新计算,每一项作业计划的日程需要重新安 排,系统输出大量的相关报告。 • 这种方法的优点是数据的处理效率高,因为总是 提供最新的计划数据。 • 但是,这种方法存在的主要问题是运算量大,两 次运算之间的MPS变化、BOM变化和作业计划因 素变化等不能及时反映到MRP中。
闭环MRP原理图
生产规划 主生产计划(MPS) 粗能力需求计划(RCCP) N 是否可行? Y 物料需求计划(MRP) 库存状况 MRP 的分时段需求 工艺路线 工作中心 能力需求计划(CRP) N
BOM
是否可行? Y 作业计划管理和控制 (采购、生产作业计划) 执行能力计划(投入/产出计划)
3 低层码的作用
MRP中的基本数量概念 • 前例,假设A产品库存有20个,则只有30个A需 要生产,那么对子项的需求也相应减少。
– – – – 毛需求=50 现有库存=20 净需求=毛需求-现有库存=50-20=30 父项的计划订单下达30,因此对B和C的毛需求也 只有30
假设库存有20个A产品及10个B物料,那么对子项D和E的需求 都将发生变化。
分时段的优先计划管理方式 • MRP是一种分时段的优先计划管理方式。为了理 解这个概念,需要理解以下两点:
– 第一,物料需求量和物料需求时间之间的关系; – 第二,传统生产计划管理方式中采用的缺料计划。
缺料表 • 缺料表是传统手工管理方式下的缺料计划的表现 形式。 • 在传统的手工管理方式下,由于计算效率低、计 算误差大等原因,某些物料的缺乏往往在生产加 工过程和装配过程中才能被发现和记录。 • 缺料表往往是这种缺料现象的具体表现形式。根 据缺料表来进行采购作业安排和生产作业安排的 计划被称为缺料计划。
ZXC
0
A(2)
B(1)
1
A(1)
C(2)
2
计划形式:MPS 物料名称:ZXC 时段 需求量 计划形式:MRP 加工提前期:1 时段 毛需求量 1 装配提前期:1 2 50 物料名称:A(1 层) 批量规则:30 当期 1 100 2 安全库存:20 3 160 4 180 5 3 4 80 5 90 计划形式:MRP 装配提前期:1 时段 毛需求量 计划收到量 预计库存量 净需求量 计划产出量 计划投入量 50 20 物料名称:B(1 层) 批量规则:50 当期 1 50 100 70 70 40 30 50 100 50 70 100 50 2 安全库存:20 3 80 4 90 5
计划订单下达 E
20 ………….
MRP中的基本数量概念 • 订单下达
– 在很多情况下,需求每天都在变化。以计算机为基 础的物料需求计划系统自动重新计算对子项物料的 需求,而且编织出新的计划订单下达,以满足需求 的变化。 – 计划订单下达仍然是计划并没有下达,正式下达计 划订单是物料计划人员的责任,而不是计算机。订 单下达要等到计划订单下达的时区成为当前时区 (第1周)才能下达。 – 订单下达意味着授权采购部门购买所需要的物料, 或者授权生产部门制造子项部件。
开环MRP • 最初提出MRP是在20世纪60年代中期,MRP的结 构如图4-1所示。 • 根据可行的MPS,在BOM、库存状态信息和工艺路 线等基础数据的支持下,由计算机编制出分时间段 的物料需求计划,从而可以下达执行采购作业的采 购订单和执行生产作业的加工订单。显然,采用 MRP可以快速、准确地制定采购作业计划和生产作 业计划,从而可以确保得到准确的物料需求,为最 终实现物料管理的精细化打下物资基础。 • 但是,这种MRP计算方式有一些前提条件,例如, MPS存在且可行、采购作业计划可行且执行过程顺 利以及生产作业计划可行且生产过程不受其他外界 因素的影响。
MRP中的基本数量概念
• 例如:完成下表。某物料的毛需求如表,提前期是2周, 批量200单位,应该采取什么行动?
周 毛需求 计划接收量 预计可用量 150 净需求 1 50 2 250 200 3 100 4 50
计划订单接受
计划订单下达
MRP的运行方式 • 再生式MRP表示每次计算时,都会覆盖原来的 MRP数据,生成全新的MRP。再生式MRP是周 期性运算MRP,通常的运算周期是1周。 • 净改变式MRP表示只会根据指定条件而变化,例 如MPS变化、BOM变化等,经过局部运算更新原 来MRP的部分数据。净改变式MRP是一种连续性 的操作,当指定数据改变时就需要立刻运行。
• 低层码是指同一种物料项目由于位于同一个BOM的不同阶层中或不 同的BOM的不同层次中而有多个阶层码时,取最低层码作为计算该 项物料需求量的一种方法。 • 这种方法的目的是确保时间上最先需求的物料在计划上最先得到库存 量,避免最后需求的物料提前下达而在计划上占用有限的库存量。 • 低层码的引入是对逐层计算原则的一个补充,低层码指定了对同一物 料位于不同BOM阶层时的处理方式。 • 合理安排作业计划、简化作业管理、降低库存量和减少企业流动资金 积压
– 制造订单下达时,计算机将给该订单分配父项所需 要的子项数量。但并不意味着子项物料已经从仓库 取走,而是意味着预期可供子项数量的减少。 – 在MRP记录中的计划接受量是工厂或供应商的未 完成订单,属于采购部门和生产活动控制的管辖范 围。但产品验收入库可供使用时,订单完成了。计 划接受量将成为现有库存量的一部分。 – 因此对净需求量的计算进行修改: 净需求量=毛需求-计划接受量-可用库存 如果考虑安全库存: 净需求量=毛需求-计划接受量-可用库存+安全库存量
计划订单接受 计划订单下达 计划订单接受 计划订单下达
计划订单接受 计划订单下达 计划订单接受
计划订单下达 计划订单接受 计划订单下达
MRP的输入、处理和输出
• MRP最主要的输入数据是3个,即MPS、 BOM和库存状况。 • MRP的处理过程主要包括读取MPS数据、 分解BOM、计算物料毛需求、计算物料净 需求和下达作业计划。 • MRP的输出主要是可以用于管理和控制的 各种计划和报告。
MRP是一种物料管理方式 • 物料管理包括物料的库存管理、物料需求的计划 管理、企业各个部门中物料数量的协调和控制以 及物料的采购和运输管理等。 • 一般情况下,物料管理有两个目的,一是保证整 个生产过程连续进行,不能因物料供应不足而出 现生产中断的现象;二是尽可能减少库存量,不 应该出现因物料库存数量过多造成占用过多的流 动资金、过多的仓库位臵和物料浪费等现象。
闭环MRP • 例如,采购作业计划可能因为供货能力或运输能力不 足而不能按期或按量执行,生产作业可能会受到加工 设备能力不足、人力资源缺乏和废品率过大的影响而 不能按期、按量完成计划的生产作业。 • 怎样解决这种MRP计算方式存在的问题呢?可以基 于控制原理采取一些适当的措施,例如,在MRP计 算过程中考虑到企业的生产加工能力问题、供货企业 的供货能力问题,确保制定的物料需求计划(包括采 购作业计划、生产作业计划)是可行的;在采购作业 计划、生产作业计划的执行过程中,通过增加采购管 理和车间管理功能而增强计划跟踪和反馈功能,确保 物料需求计划可以及时地得到更新。 • 采取这些措施之后得到的MRP被称为闭环MRP,而 把以前的MRP计算方式称为开环MRP