铝合金熔体的熔剂精炼
论述铝合金的熔体处理

论述铝合金的熔体处理1 前言铝及铝合金因其优异的性能被广泛应用于航天、航空、交通运输、建筑、包装、电子、印刷、装饰等众多国防和民用领域。
在金属材料中,铝合金的应用范围和用量仅次于铁,约占有色金属用量的1/3,随着铝及铝合金的大范围应用,对其性能要求也越来越高、越来越多样,而铝及铝合金的良好性能与其熔炼铸造是分不开的。
熔铸是铝加工的第一道工序,为后序的轧制、锻造、挤压等生产提供锭坯,铸锭质量的好坏直接与各种铝材的最终质量紧密相关,故要获得良好的构件,必须从熔体处理开始。
铝合金熔体净化处理是生产高质量的铝铸件的基本保证措施之一,也是提高铝合金综合性能的主要手段之一,对疏松、气孔、夹杂等的形成有重要影响,而且直接影响铝铸件的物理性能、机械性能以及使用性能。
2 熔体净化方法所谓净化处理就是就是采用各种措施使铝熔体中不希望存在的气体与固态物质降到所允许的范围以内,以确保材料的性能符合标准或某些特殊要求。
铝合金净化方法按其作用机理可分为吸附净化和非吸附净化两大基本类型。
2.1 吸附净化吸附净化主要是利用精炼剂的表面作用,当精炼剂(如各种气体、液体、固体精炼剂及过滤介质)在铝熔体中与氧化物夹杂或气体相接触时,杂质或气体被精炼剂吸附在其表面上,从而改变杂质的物理性质,随精炼剂一起被除去,以达到除气除杂的目的。
吸附净化的方法主要有:浮游法、熔剂法、过滤法等。
(1)浮游法浮游法也叫气体吹洗法,它是将气体通入到铝熔体内部,形成气泡,熔体中的氢在分压差的作用下扩散进这些气泡中,并随气泡的上浮而被排除,达到除气的目的。
浮游法主要包括惰性气体吹洗、活性气体吹洗混合气体吹洗以及氯盐净化等。
无毒精炼剂主要由硝酸盐等氧化剂和碳组成,在高温下反映生成氮气和二氧化碳都能起到精炼作用,由于其不产生刺激性气味的气体且精炼效果也好从而得到广泛应用。
(2)溶剂法熔剂法是在铝合金熔炼过程中,将熔剂加入到熔体内部,通过一系列物理化学作用,达到除气除杂的目的。
铝镁精炼剂介绍

铝镁精炼剂
Al—Mg合金在熔化过程中,熔体表面氧化膜结构为Mgo+Al2O3,在熔炼过程中该氧化膜结构不致密容易被破坏,产生新的氧化膜,因此含镁铝合金熔体含渣量多、流动性差,铸锭在铸造时补缩差。
易造成铝镁合金铸锭,在轧制过程中裂边,最终产品性能达不到要求。
重庆云岭金属材料有限公司开发的铝镁精炼剂是专门为铝镁合金量身定做的一种精炼剂,能有效减少上述铝镁合金铸锭缺陷。
该精炼剂能促进铝熔体与渣子分离,并将渣子溶解到熔剂中上浮带出。
该精炼剂中添加了一种还原剂,能有效地阻止铝熔体的进一步氧化,同时该精炼剂对熔体的碱金属有较好的除去作用。
该精炼剂还能改善渣子的性质,将“马粪渣”变成松散的薄层渣子,易于扒出,带出的金属少,产品在西南铝周边企业使用后,对含镁铝合金铸造质量有了较大的改善,减少了热轧铸锭裂边。
该产品在铸轧料生产中效果更佳,由于流量少、流程长,温降大,熔体粘度大,铸轧板表面易产生较多的裂口,废品率高。
通过使用铝镁精炼剂,有效地减少了生产中熔体夹渣多、粘度大、表面张力小等问题,使铸轧料表面裂纹得到有效的解决,成品率达90%以上。
重庆云岭金属材料有限公司地处中国铝加工之都-----重庆西彭,从事过多年的铝熔铸技术研究,解决过许多较为棘手的熔铸问题,热诚欢迎各铝加工企业来电咨询,联系人:王先生,电话:(023)65805776,013808350456。
精炼助熔剂氟化钙

精炼助熔剂氟化钙
氟化钙是一种常用的精炼助熔剂。
在冶金和金属加工过程中,它被广泛用作铝、镁等金属的熔炼和精炼剂。
氟化钙具有降低金属的熔点、改善熔体流动性和脱氢能力的特点,对于去除金属中的杂质和夹杂物也有一定的效果。
氟化钙作为助熔剂的主要作用之一是提高熔体的流动性。
在金属的熔炼和铸造过程中,熔体的流动性对于填充模具和得到良好的铸件形态非常重要。
氟化钙可以降低金属的表面张力,使熔体更容易流动,减少铸件中的缺陷。
另外,氟化钙还可以降低金属的熔点。
在金属加工过程中,通过添加适量的氟化钙,可以使金属的熔点降低,有利于金属的熔化和熔炼操作。
这对于金属的精炼和合金的调整非常重要。
此外,氟化钙还能够在金属熔炼过程中起到脱氢的作用。
氟化钙可以与金属中的氢反应生成氢氟化物,从而有效地去除金属中的氢气,防止气孔和夹杂物的产生。
总之,氟化钙作为精炼助熔剂在金属加工过程中有着重要的作用,能够提高金属的流动性,降低熔点,并有效地净化金属。
铝及铝合金的熔炼
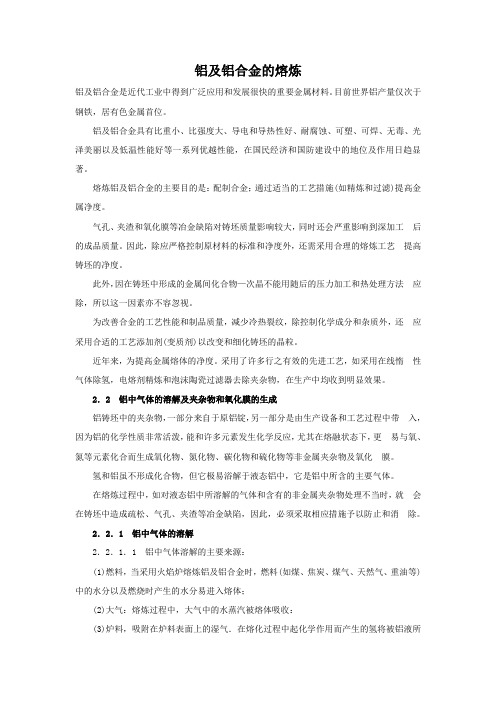
铝及铝合金的熔炼铝及铝合金是近代工业中得到广泛应用和发展很快的重要金属材料。
目前世界铝产量仅次于钢铁,居有色金属首位。
铝及铝合金具有比重小、比强度大、导电和导热性好、耐腐蚀、可塑、可焊、无毒、光泽美丽以及低温性能好等一系列优越性能,在国民经济和国防建设中的地位及作用日趋显著。
熔炼铝及铝合金的主要目的是:配制合金;通过适当的工艺措施(如精炼和过滤)提高金属净度。
气孔、夹渣和氧化膜等冶金缺陷对铸坯质量影响较大,同时还会严重影响到深加工后的成品质量。
因此,除应严格控制原材料的标准和净度外,还需采用合理的熔炼工艺提高铸坯的净度。
此外,因在铸坯中形成的金属间化合物—次晶不能用随后的压力加工和热处理方法应除,所以这一因素亦不容忽视。
为改善合金的工艺性能和制品质量,减少冷热裂纹,除控制化学成分和杂质外,还应采用合适的工艺添加剂(变质剂)以改变和细化铸坯的晶粒。
近年来,为提高金属熔体的净度。
采用了许多行之有效的先进工艺,如采用在线惰性气体除氢,电熔剂精炼和泡沫陶瓷过滤器去除夹杂物,在生产中均收到明显效果。
2.2 铝中气体的溶解及夹杂物和氧化膜的生成铝铸坯中的夹杂物,一部分来自于原铝锭,另一部分是由生产设备和工艺过程中带入,因为铝的化学性质非常活泼,能和许多元素发生化学反应,尤其在熔融状态下,更易与氧、氮等元素化合而生成氧化物、氮化物、碳化物和硫化物等非金属夹杂物及氧化膜。
氢和铝虽不形成化合物,但它极易浴解于液态铝中,它是铝中所含的主要气体。
在熔炼过程中,如对液态铝中所溶解的气体和含有的非金属夹杂物处理不当时,就会在铸坯中造成疏松、气孔、夹渣等冶金缺陷,因此,必须采取相应措施予以防止和消除。
2.2.1 铝中气体的溶解2.2.1.1 铝中气体溶解的主要来源:(1)燃料,当采用火焰炉熔炼铝及铝合金时,燃料(如煤、焦炭、煤气、天然气、重油等)中的水分以及燃烧时产生的水分易进入熔体;(2)大气:熔炼过程中,大气中的水蒸汽被熔体吸收:(3)炉料,吸附在炉料表面上的湿气.在熔化过程中起化学作用而产生的氢将被铝液所溶解;如果炉料放置过久,且表面有油污者,对熔体的吸气量尤有影响;(4)耐火材料:烘炉不彻底时,耐火材料表面吸附的水分,以及砌制时泥浆中的水分在熔炼头几个熔次时,对熔体中气体含量将有明显影响;(5)熔剂;使用保存不当而发生了潮解的溶剂,也能增加熔体的含气量;(6)熔铸工具:在倒炉及铸造时,如果熔铸工具干燥不好,易使熔体的吸气量增加;(7)倒炉及浇铸过程中,如果熔体落差大,或液流翻滚过急时,也会使气体及氧化膜卷入熔体;(8)润滑油脱水不好。
铸造铝合金的熔炼工艺
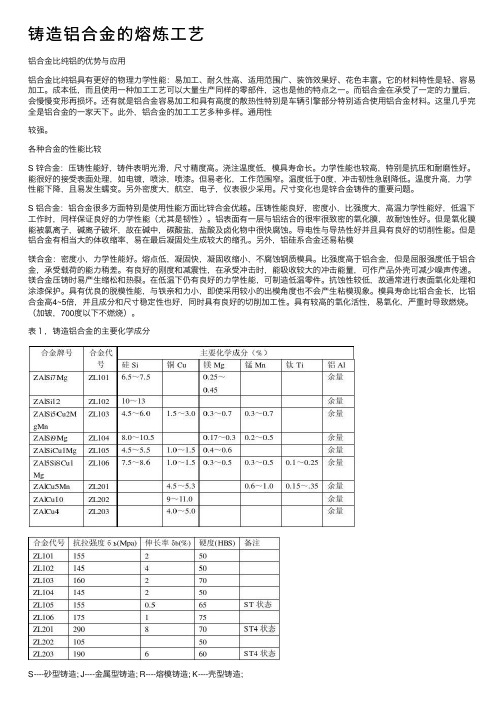
铸造铝合⾦的熔炼⼯艺铝合⾦⽐纯铝的优势与应⽤铝合⾦⽐纯铝具有更好的物理⼒学性能:易加⼯、耐久性⾼、适⽤范围⼴、装饰效果好、花⾊丰富。
它的材料特性是轻、容易加⼯。
成本低,⽽且使⽤⼀种加⼯⼯艺可以⼤量⽣产同样的零部件,这也是他的特点之⼀。
⽽铝合⾦在承受了⼀定的⼒量后,会慢慢变形再损坏。
还有就是铝合⾦容易加⼯和具有⾼度的散热性特别是车辆引擎部分特别适合使⽤铝合⾦材料。
这⾥⼏乎完全是铝合⾦的⼀家天下。
此外,铝合⾦的加⼯⼯艺多种多样。
通⽤性较强。
各种合⾦的性能⽐较S 锌合⾦:压铸性能好,铸件表明光滑,尺⼨精度⾼。
浇注温度低,模具寿命长。
⼒学性能也较⾼,特别是抗压和耐磨性好。
能很好的接受表⾯处理,如电镀,喷涂,喷漆。
但易⽼化,⼯作范围窄。
温度低于0度,冲击韧性急剧降低。
温度升⾼,⼒学性能下降,且易发⽣蠕变。
另外密度⼤,航空,电⼦,仪表很少采⽤。
尺⼨变化也是锌合⾦铸件的重要问题。
S 铝合⾦:铝合⾦很多⽅⾯特别是使⽤性能⽅⾯⽐锌合⾦优越。
压铸性能良好,密度⼩,⽐强度⼤,⾼温⼒学性能好,低温下⼯作时,同样保证良好的⼒学性能(尤其是韧性)。
铝表⾯有⼀层与铝结合的很牢很致密的氧化膜,故耐蚀性好。
但是氧化膜能被氯离⼦,碱离⼦破坏,故在碱中,碳酸盐,盐酸及卤化物中很快腐蚀。
导电性与导热性好并且具有良好的切削性能。
但是铝合⾦有相当⼤的体收缩率,易在最后凝固处⽣成较⼤的缩孔。
另外,铝硅系合⾦还易粘模镁合⾦:密度⼩,⼒学性能好。
熔点低,凝固快,凝固收缩⼩,不腐蚀钢质模具。
⽐强度⾼于铝合⾦,但是屈服强度低于铝合⾦,承受载荷的能⼒稍差。
有良好的刚度和减震性,在承受冲击时,能吸收较⼤的冲击能量,可作产品外壳可减少噪声传递。
镁合⾦压铸时易产⽣缩松和热裂。
在低温下仍有良好的⼒学性能,可制造低温零件。
抗蚀性较低,故通常进⾏表⾯氧化处理和涂漆保护。
具有优良的脱模性能,与铁亲和⼒⼩,即使采⽤较⼩的出模⾓度也不会产⽣粘模现象。
模具寿命⽐铝合⾦长,⽐铝合⾦⾼4~5倍,并且成分和尺⼨稳定性也好,同时具有良好的切削加⼯性。
高性能铝合金精炼剂论文

高性能铝合金精炼剂的探讨摘要:对于铝合金来说,由于al的化学活性很强,在熔炼过程中容易产生夹杂、气体等缺陷,它们在熔体凝固后会分布在合金内部,对材料性能产生很大影响。
因此,要提高铸造铝及其合金的性能,必须充分除去熔体中的氧化夹杂和气体,避免铸件中缺陷的产生。
关键词:铝合金精炼剂氧化物夹杂1 氧化物夹杂的类型熔融金属液在精炼处理以及运输过程中,氧化皮、金属间化合物、炉膛碎片等异质物容易被带入到金属液中,形成非金属夹杂,这些非金属夹杂主要是氧化物夹杂。
根据其在熔化和浇铸过程中形成时期的不同,可以分为一次氧化物夹杂和二次氧化物夹杂。
一次氧化物夹杂主要是指铝液浇注前形成的所有氧化物夹杂。
一次氧化物夹杂按其形状可分两类:一类是宏观组织中分布不均匀的大块夹杂物,这类夹杂物,使合金组织不连续,降低工件的气密性能,成为腐蚀的根源,明显降低铝合金的强度和塑性,也往往成为零件的裂纹源,第二类氧化物夹杂是指细小的、弥散的夹杂物,即使经过仔细净化也不能全除去,它使金属液粘度增大,降低凝固时铝液的补缩能力,易造成铸件的缩松。
二次氧化物夹杂,又称为内生夹杂物,主要是在浇注过程中形成的。
内生夹杂物一般来说分布比较均匀,颗粒也比较小。
铝液在浇注过程中的飞溅、紊流是二次氧化物夹杂的主要来源。
铝液在砂型中,与型砂中的水分作用,经水分解为氧和氢,氧与铝作用形成氧化物夹杂,氢溶于铝液。
2 杂质去除方法铝熔体中的有害杂质元素可用真空处理去除和精炼剂法化学去除。
真空处理就是在真空条件下,利用杂质元素的沸点低于铝(沸点为1800℃)和铝合金主要成分的沸点,通过蒸发使之去除。
真空处理可以将钙、锌等的量降低到lppm以下,但是还未获得工业应用。
有害杂质元素可与精炼剂发生化学反应而生成能够与铝分离的化合物,并通过精炼剂的吸附作用而被带入精炼渣中排出。
其它金属与氧、按和硫的生成热大小排列如下:氧化物:镁、铝、钠、硅、锰、锌、铁、镍、铅、铜;氯化物: 钠、镁、铝、锰、锌、铅、铁、镍、铜、硅;硫化物:钠、镁、锰、锌、铝、铁、铜、铅、硅、镍以去除氧化物夹杂为主的方法主要有:电熔剂法、过滤法和精炼剂法。
铝合金熔铸工艺
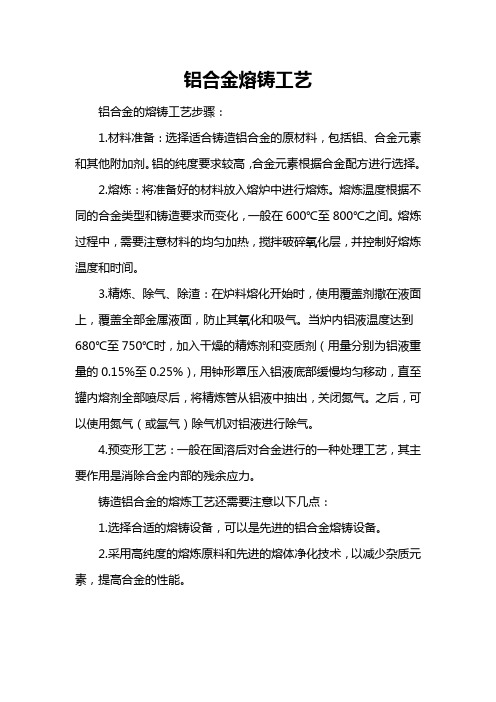
铝合金熔铸工艺
铝合金的熔铸工艺步骤:
1.材料准备:选择适合铸造铝合金的原材料,包括铝、合金元素和其他附加剂。
铝的纯度要求较高,合金元素根据合金配方进行选择。
2.熔炼:将准备好的材料放入熔炉中进行熔炼。
熔炼温度根据不同的合金类型和铸造要求而变化,一般在600℃至800℃之间。
熔炼过程中,需要注意材料的均匀加热,搅拌破碎氧化层,并控制好熔炼温度和时间。
3.精炼、除气、除渣:在炉料熔化开始时,使用覆盖剂撒在液面上,覆盖全部金属液面,防止其氧化和吸气。
当炉内铝液温度达到680℃至750℃时,加入干燥的精炼剂和变质剂(用量分别为铝液重量的0.15%至0.25%),用钟形罩压入铝液底部缓慢均匀移动,直至罐内熔剂全部喷尽后,将精炼管从铝液中抽出,关闭氮气。
之后,可以使用氮气(或氩气)除气机对铝液进行除气。
4.预变形工艺:一般在固溶后对合金进行的一种处理工艺,其主要作用是消除合金内部的残余应力。
铸造铝合金的熔炼工艺还需要注意以下几点:
1.选择合适的熔铸设备,可以是先进的铝合金熔铸设备。
2.采用高纯度的熔炼原料和先进的熔体净化技术,以减少杂质元素,提高合金的性能。
3.可以采用先进的铸造工艺,如压铸、挤压铸等,以减少合金内部的缺陷,提高合金性能。
4.注意工具和熔炉的清理、预热和涂料喷刷,以及铝料配比(铝锭与回炉料的比例应不大于50%)等。
铝合金熔炼过程中除渣及精炼除气的分析
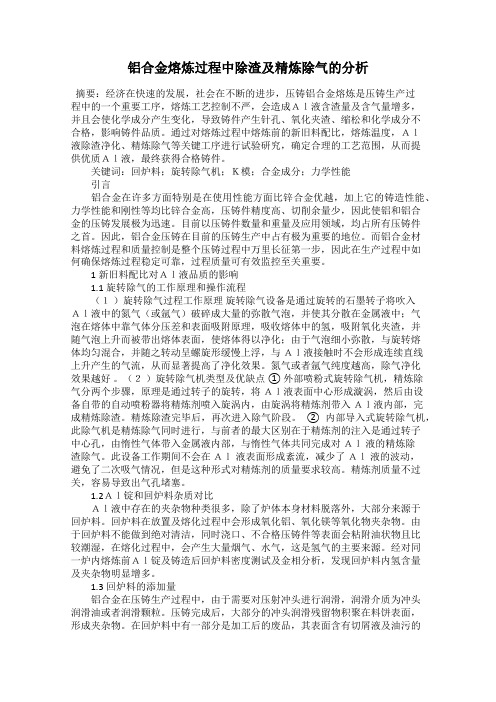
铝合金熔炼过程中除渣及精炼除气的分析摘要:经济在快速的发展,社会在不断的进步,压铸铝合金熔炼是压铸生产过程中的一个重要工序,熔炼工艺控制不严,会造成Al液含渣量及含气量增多,并且会使化学成分产生变化,导致铸件产生针孔、氧化夹渣、缩松和化学成分不合格,影响铸件品质。
通过对熔炼过程中熔炼前的新旧料配比,熔炼温度,Al液除渣净化、精炼除气等关键工序进行试验研究,确定合理的工艺范围,从而提供优质Al液,最终获得合格铸件。
关键词:回炉料;旋转除气机;K模;合金成分;力学性能引言铝合金在许多方面特别是在使用性能方面比锌合金优越,加上它的铸造性能、力学性能和刚性等均比锌合金高,压铸件精度高、切削余量少,因此使铝和铝合金的压铸发展极为迅速。
目前以压铸件数量和重量及应用领域,均占所有压铸件之首。
因此,铝合金压铸在目前的压铸生产中占有极为重要的地位。
而铝合金材料熔炼过程和质量控制是整个压铸过程中万里长征第一步,因此在生产过程中如何确保熔炼过程稳定可靠,过程质量可有效监控至关重要。
1新旧料配比对Al液品质的影响1.1旋转除气的工作原理和操作流程(1)旋转除气过程工作原理旋转除气设备是通过旋转的石墨转子将吹入Al液中的氮气(或氩气)破碎成大量的弥散气泡,并使其分散在金属液中;气泡在熔体中靠气体分压差和表面吸附原理,吸收熔体中的氢,吸附氧化夹渣,并随气泡上升而被带出熔体表面,使熔体得以净化;由于气泡细小弥散,与旋转熔体均匀混合,并随之转动呈螺旋形缓慢上浮,与Al液接触时不会形成连续直线上升产生的气流,从而显著提高了净化效果。
氮气或者氩气纯度越高,除气净化效果越好。
(2)旋转除气机类型及优缺点① 外部喷粉式旋转除气机,精炼除气分两个步骤,原理是通过转子的旋转,将Al液表面中心形成漩涡,然后由设备自带的自动喷粉器将精炼剂喷入旋涡内,由旋涡将精炼剂带入Al液内部,完成精炼除渣。
精炼除渣完毕后,再次进入除气阶段。
② 内部导入式旋转除气机,此除气机是精炼除气同时进行,与前者的最大区别在于精炼剂的注入是通过转子中心孔,由惰性气体带入金属液内部,与惰性气体共同完成对Al液的精炼除渣除气。
- 1、下载文档前请自行甄别文档内容的完整性,平台不提供额外的编辑、内容补充、找答案等附加服务。
- 2、"仅部分预览"的文档,不可在线预览部分如存在完整性等问题,可反馈申请退款(可完整预览的文档不适用该条件!)。
- 3、如文档侵犯您的权益,请联系客服反馈,我们会尽快为您处理(人工客服工作时间:9:00-18:30)。
铝合金熔体的熔剂精炼 Revised as of 23 November 2020
铝合金熔体的熔剂精炼
本文介绍了熔剂精炼在铝合金熔体净化过程中的作用,熔剂的分类和要求,常用熔剂的组成,适用范围及使用方法等。
在铝及铝合金熔炼过程中,氢及氧化夹杂是污染铝熔体的主要物质。
铝极易与氧生成A1202或次氧化铝(Al2O及A10).同时也极易吸收气体(H)其含量占铝熔体中气体总量的70—90%,而铸造铝合金中的主要缺陷——气孔和夹渣,就是由于残留在合金中的气体和氧化物等固体颗粒造成的。
因此,要获得高质量的熔体,不仅要选择正确合理的熔炼工艺,而且熔体的精炼净化处理也是很重要的。
铝及铝合金熔体的精炼净化方法较多,主要有浮游法、熔剂精炼法、熔体过滤法、真空法和联合法。
本文介绍熔剂精炼法在铝合金熔炼中的应用。
1熔剂的作用
熔盐熔剂广泛地用于原铝和再生铝的生产,以提高熔体质量和金属铝的回收率[]。
熔剂的作用有四个:其一,改变铝熔体对氧化物(氧化铝)的润湿性,使铝熔体易于与氧化物(氧化铝)分离,从而使氧化物(氧化铝)大部分进入熔剂中而减少了熔体中的氧化物的含量。
其二,熔剂能改变熔体表面氧化膜的状态。
这是因为它能使熔体表面上那层坚固致密的氧化膜破碎成为细小颗粒,因而有利于熔体中的氢从氧化膜层的颗粒空隙中透过逸出,进入大气中。
其三,熔剂层的存在,能隔绝大气中水蒸气与铝熔体的接触,使氢难以进入铝熔体中,同时能防止熔体氧化烧损。
其四,熔剂能吸附铝熔体中的氧化物,使熔体得以净化。
总之,熔剂精炼的除去夹杂物作用主要是通过与熔体中的氧化膜及非金属夹杂物发生吸附,溶解和化学作用来实现的。
2熔剂的分类和选择
2.1熔剂的分类和要求
铝合金熔炼中使用的熔剂种类很多,可分为覆盖剂(防止熔体氧化烧损及吸气的熔剂)和精炼剂(除气、除夹杂物的熔剂)两大类,不同的铝合金所用的覆盖剂和精炼剂不同。
但是,铝合金熔炼过程中使用的任何熔剂,必须符合下列条件[]。
①熔点应低于铝合金的熔化温度。
②比重应小于铝合金的比重。
③能吸附、溶解熔体中的夹杂物,并能从熔体中将气体排除。
④不应与金属及炉衬起化学作用,如果与金属起作用时,应只能产生不溶于金属的惰性气体,且熔剂应不溶于熔体金属中。
⑤吸湿性要小,蒸发压要低。
⑥不应含有或产生有害杂质及气体。
⑦要有适当的粘度及流动性。
⑧制造方便:价格便宜。
2.2熔剂的成分及熔盐酌作用
铝合金用熔剂一般由碱金属及碱土金属的氯化物及氟化物组成,其主要成分是KCl、NaCl、NaF.CaF,.、Na3A1F6、Na2SiF6等。
熔剂的物理、化学性能(熔点、密度、粘度、挥发性、吸湿性以及与氧化物的界面作用等)对精炼效果起决定性作用.
2.2.1.氯盐:
氯盐是铝合金熔剂中最常见的基本组元,而45%NaCl+55%KCl的混合盐应用最广。
由于它们对固态Al2O3,夹杂物和氧化膜有很强的浸润能力(与Al2O3,的润湿角为20多度)且在熔炼温度下NaCl和KCl的比重只有1.55g/cm3和l.50g /cm3,显着小于铝熔体的比重,故能很好地铺展在铝熔体表面,破碎和吸附熔体表面的氧化膜。
但仅含氯盐的熔剂,破碎和吸附过程进行得缓慢,必须进行人工搅拌以加速上述过程的进行。
氯化物的表面张力小,润湿性好,适于作覆盖剂,其中具有分子晶型的氯盐如CCl4,SiCl4,A1C13,等可单独作为净化剂,而具有离子晶型的氯盐如LiCl、NaCl毛KCl、MgC12:等适于作混合盐熔剂。
2。
2.2.氟盐:
在氯盐混合物中加入NaF.Na3A1F6、CaF2。
等少量氟盐,主要起精炼作用,如吸附、溶解Al2O3,。
氟盐还能有效地去除熔体表面的氧化膜,提高除气效果。
这是因为:a)氟盐可与铝熔体发生化学反应生成气态的A1F,、SiF4,、BF3,等,它们以机械作用促使氧化膜与铝熔体分离,并将氧化膜挤破,推入熔剂中;
b)在发生上述反应的界面上产生的电流亦使氧化膜受“冲刷”而破碎。
因此,氟盐的存在使铝熔体表面的氧化膜的破坏过程显着加速,熔体中的氢就能较方便的逸出;c)氟盐(特别是CaF2:)能增大混合熔盐的表面张力,使已吸附氧化物的熔盐球状化,便于与熔体分离,减少固熔渣夹裹铝而造成的损耗,而且由于熔剂——熔体表面张力的提高,加速了熔剂吸附夹杂的过程。
3铝合金熔炼中常用熔剂
熔剂精炼法对排出非金属夹杂物有很好的效果,但是清除熔体中非金属夹杂物的净化程度,除与熔剂的物理、化学性能有关外,在很大程度上还取决于精炼工艺条件,如熔剂的用量,熔剂与熔体的接触时间、接触面积、搅拌情况、温度等。
3.1常用熔剂
为精炼铝合金熔体,人们已研制出上百种熔剂,以钠、钾为基的氯化物熔剂应用最广。
对含镁量低的铝合金广泛采用以钠钾为基的氯化物精炼剂,含镁量高的铝合金为避免钠脆性则采用不含钠的以光卤石为基的精炼熔剂。
铝合金熔炼过程中常用熔剂的成分及作用如表1(4-7)。
表1常用熔剂的成分及应用
溶剂种类组分含量,%
NaClKClMgCl2Na3AlF6其它成分适用的合金
覆盖剂3950CaF2Al-Cu系,Al-Cu-Mg系,Al-Cu-Si系Al-Cu-Mg-Zn系
一般铝合金
5050一般铝合金
KCl,MgCl280CaF220Al-Mg系Al-Mg-Si系合金
3114CaF210CaCL244Al-Mg系合金
867CaF210,MgF215Al-Mg系合金
精炼剂25-3540-5018-26除Al-Mg系,Al-Mg-Si系以外的其它合金
867MgF215,CaF210Al-Mg系合金
KCl,MgCl260,CaF240Al-Mg系Al-Mg--Si系合金
4246Bacl26(2号熔剂)Al-Mg系合金
225622一般铝合金
503515一般铝合金
4050NaF10一般铝合金
50355CaF210一般铝合金
60CaF220,NaF20一般铝合金
36-4550-553-7CaF一般铝合金
Na2SiF630-50,C2Cl650-70一般铝合金
KF10易拉罐合金
从上表中可以看出,有些熔剂组分的含量变化范围较大,可以根据实际情况来确定。
首先要根据合金元素的含量来确定[8],因为大多数铝合金中主要元素含量都可在一定范围内变化,其次要根据所除杂质成分及含量来确定。
因此,使用厂家除使用熔剂厂生产的熔剂外,最好根据所熔炼铝合金的成分调正熔剂组分比例,以找出最佳熔剂组成。
综合以上各种熔剂不难看出,当要熔制的铝合金成分确定后,熔剂成分的设计首先是主要成分(如氯化物)用量配比的选择,其次是添加组分(如氟化物)的选择。
熔剂配好后,最好是经熔炼、冷凝成块、再粉碎后使用,因为机械混合状态的效果不好。
熔剂用量.
熔炼铝合金废料时,废料质量不同,覆盖剂及精炼剂的用量也不同。
3.2.1.主覆盖剂用量
a)熔炼质量较好的废料,如块状料、管、片时覆盖剂用量(见表2)。
表2覆盖剂种类及用量
炉料及制品覆盖剂用量(占投料量的%)覆盖剂种类
电炉熔炼:一般制品特殊制品-%-%普通粉状溶剂普通粉状溶剂
煤气炉熔炼:原铝锭废料1-2%2-4%KC1:NaC1按1:1混合
KC1:NaC1按1:1混合
注:对高镁铝合金,应一律用不含钠盐的熔剂进行覆盖,避免和含钠的熔剂接触。
b)熔炼质量较差的废料,如由锯、车、铣等工序下来的碎屑及熔炼扒渣等时,覆盖剂用量(见表3)。
表3:覆盖剂用量
类别用量(占投料量的%)
小碎片碎屑号外渣子6-810-1515-20
3.2.2精炼剂用量
不同铝合金、不同制品,精炼剂用量也各不相同(见表4)。
表4精炼剂用量
合金及制品熔炼炉静置炉
高镁合金2号熔剂5-6kg/t2号熔剂5-6kg/t
特殊制品除高镁合金普通熔剂5-6kg/t普通熔剂6-7kg/t
LT66、LT62、LG1、LG2、LG3、LG4出炉时用普通熔剂、叠熔剂坝
其它合金普通熔剂5-6kg/t
注:
①在潮湿地区和潮湿季节,熔剂用量应有所增加
②对大规格的圆锭,其熔剂用量也应适当增加。
熔剂使用方法
熔剂精炼法熔炼铝合金生产中常用以下几种方法:
①熔体在浇包内精炼。
首先在浇包内放入一包熔剂,然后注入熔体,并充分搅拌,以增加二者的接触面积。
②熔体在感应炉内精炼。
熔剂装入感应炉内,借助于感应磁场的搅拌作用使熔剂与熔体充分混合,达到精炼的目的。
③在浇包内或炉中用搅拌机精炼,使熔剂机械弥散于熔体中。
④熔体在磁场搅拌装置中精炼。
,该法依靠电磁力的作用,向熔剂——
金属界面连续不断地输送熔体,以达到铝熔体与熔剂间的活性接触,熔体旋转速度越高,其精炼效果越好。
⑤电熔剂精炼。
此法是使熔体通过加有电场(在金属——熔剂界面上)的熔剂层,进行连续精炼。
在这五种方法中,电熔剂精炼效果最好。