铝合金精炼
铸造铝合金的浮游法精炼工艺.pdf

中国铸造装备与技术5/2007式。
铸造专家系统涉及到许多的专业知识,单单依靠某一位专家解决困难比较大,需要多位专家协同合作,这就要求专家系统能够适应分布协同发展的要求,这将是专家系统的一个主要发展方向。
支持数据通信,网络和集成的新一代领域专家系统开发工具将不断地涌现。
(4)专家系统将越来越多的实现自我管理。
随着计算机技术数据库的知识发现(KDD)和人工智能技术的发展,挖掘数据库中有价值的知识,对知识中对知识库中的知识进行智能化的精益求精,专家系统特别是知识库的更新、解释机构将一改目前手动或者半自动的方式从而越来越多的实现自我管理。
(5)实用性和可操作性将越来越强。
随着面向对象的高级开发程序的进一步发展,专家系统必然向着更加人性化和模块化的方向发展,将会为越来越多的人所使用和操作。
参考文献1J.L.Hilletal.Knowledge-BasedDesignofRiggingSystemsforInvest-mentCastings,AFCTransactions,1993.2吕建国,张方,张希俊.专家系统在铸造中的应用.有色金属设计,2003(1).3李俊,钱翰诚,等.铸件缺陷分析专家系统的研究.现代机械,第2期.4RudolfSillen.UsingArtificialIntelligenceinthefoundry.ModernCasting,December1991,pp.33-37.5K.Nyamekye,etal.ExpertSystermforDesigningGatingSystemforpermanentMoldTilt-PourCastingProcess.AFSTransaction,1994.6H.Kulkarni,G.A.Stone.CastingDefectAnalysisExpertSystem,AFSTranslaction,1992.7周丹晨,蒋玉明,等.铸造合金选择专家系统的研究和应用.特种铸造及有色金,2000(6).8李日,李梅娥,等.铸造方法选择的专家系统研究与开发.西北工业大学学报,1998(8):Vol.16No.3.9黄天佑,等.铸造工业的计算机专家系统.铸造,1989(8).10熊守美,等.球墨铸铁铸件缺陷分析专家系统.铸造,1994(5).11熊守美,等.大断面球铁件生产技术及缺陷分析知识库的建立.铸造,1995(1).12卢宏远,李荣彬.DCES压铸缺陷及对策专家系统构造原理.铸造,2001(4).13金传伟,毛宗源.用于航空铝镁铸件缺陷分析的智能专家系统.华南理工大学学报:自然科学版,2000,28(3).14刘旭麟,刘顺,王霞.铸造缺陷分析专家系统的研究.计算机应用技术特种铸造及有色合金,2000(4).15曾怡丹,等.铸件孔、洞类缺陷分析的CCDAI专家系统.特种铸造及有色合金,1993(1):25-27.铸造铝合金以其密度小、比强度高、塑性好、导电导热性好、耐蚀性好、资源丰富,容易加工等优点,已广泛应用于航空、航天、汽车、机械、电子等各个领域。
《汽车轮毂用A356铝合金的精炼及净化》范文
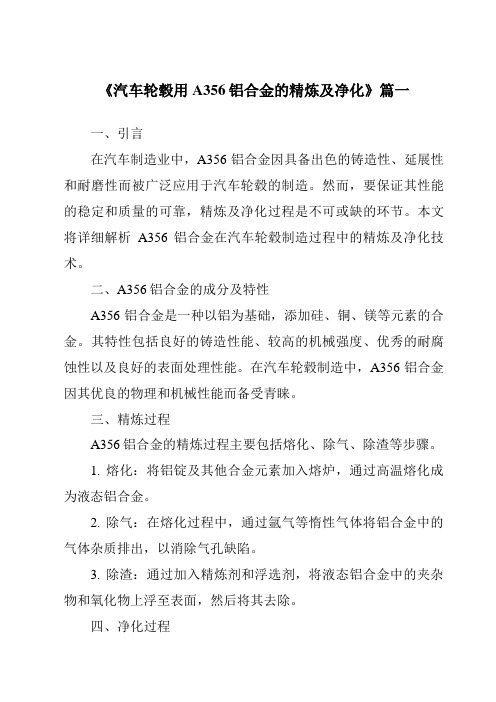
《汽车轮毂用A356铝合金的精炼及净化》篇一一、引言在汽车制造业中,A356铝合金因具备出色的铸造性、延展性和耐磨性而被广泛应用于汽车轮毂的制造。
然而,要保证其性能的稳定和质量的可靠,精炼及净化过程是不可或缺的环节。
本文将详细解析A356铝合金在汽车轮毂制造过程中的精炼及净化技术。
二、A356铝合金的成分及特性A356铝合金是一种以铝为基础,添加硅、铜、镁等元素的合金。
其特性包括良好的铸造性能、较高的机械强度、优秀的耐腐蚀性以及良好的表面处理性能。
在汽车轮毂制造中,A356铝合金因其优良的物理和机械性能而备受青睐。
三、精炼过程A356铝合金的精炼过程主要包括熔化、除气、除渣等步骤。
1. 熔化:将铝锭及其他合金元素加入熔炉,通过高温熔化成为液态铝合金。
2. 除气:在熔化过程中,通过氩气等惰性气体将铝合金中的气体杂质排出,以消除气孔缺陷。
3. 除渣:通过加入精炼剂和浮选剂,将液态铝合金中的夹杂物和氧化物上浮至表面,然后将其去除。
四、净化过程净化过程主要是通过化学和物理方法进一步去除A356铝合金中的杂质,提高其纯度和性能。
1. 化学净化:通过添加特定的化学试剂,与合金中的杂质发生化学反应,生成无害或低害的化合物,并通过精炼和浮选将其去除。
2. 物理净化:利用离心分离、真空蒸馏等技术,通过物理方法去除合金中的杂质和气体。
五、工艺控制及优化为了确保A356铝合金的精炼及净化效果,需要对整个过程进行严格的工艺控制及优化。
这包括控制熔炼温度、精炼剂和浮选剂的添加量、除气和除渣的时间和频率等。
此外,还需要定期对设备进行维护和检修,确保其正常运行和良好的工作状态。
六、结论A356铝合金的精炼及净化过程是汽车轮毂制造中不可或缺的环节。
通过精炼和净化,可以有效地去除合金中的杂质和气体,提高其纯度和性能,从而保证汽车轮毂的质量和性能。
在未来的汽车制造业中,随着对材料性能和质量的不断要求提高,A356铝合金的精炼及净化技术将不断得到优化和发展。
《2024年汽车轮毂用A356铝合金的精炼及净化》范文
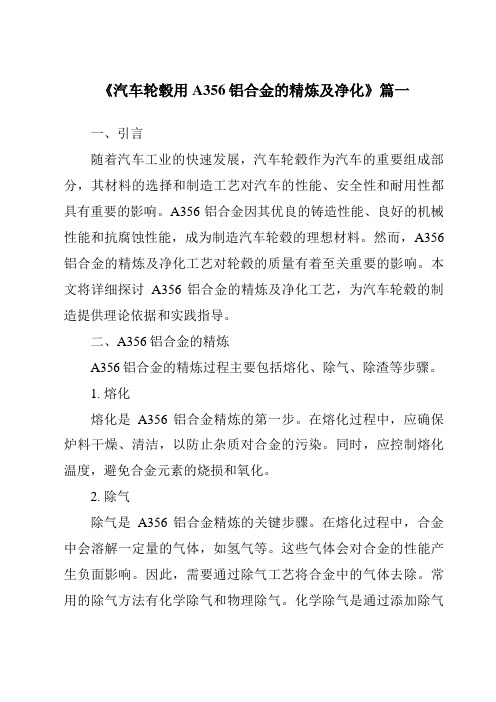
《汽车轮毂用A356铝合金的精炼及净化》篇一一、引言随着汽车工业的快速发展,汽车轮毂作为汽车的重要组成部分,其材料的选择和制造工艺对汽车的性能、安全性和耐用性都具有重要的影响。
A356铝合金因其优良的铸造性能、良好的机械性能和抗腐蚀性能,成为制造汽车轮毂的理想材料。
然而,A356铝合金的精炼及净化工艺对轮毂的质量有着至关重要的影响。
本文将详细探讨A356铝合金的精炼及净化工艺,为汽车轮毂的制造提供理论依据和实践指导。
二、A356铝合金的精炼A356铝合金的精炼过程主要包括熔化、除气、除渣等步骤。
1. 熔化熔化是A356铝合金精炼的第一步。
在熔化过程中,应确保炉料干燥、清洁,以防止杂质对合金的污染。
同时,应控制熔化温度,避免合金元素的烧损和氧化。
2. 除气除气是A356铝合金精炼的关键步骤。
在熔化过程中,合金中会溶解一定量的气体,如氢气等。
这些气体会对合金的性能产生负面影响。
因此,需要通过除气工艺将合金中的气体去除。
常用的除气方法有化学除气和物理除气。
化学除气是通过添加除气剂与合金中的气体反应,从而将气体从合金中排出。
物理除气则是利用真空泵将合金中的气体抽出。
3. 除渣除渣是A356铝合金精炼的另一重要步骤。
在熔化和除气过程中,会生成一些浮渣和夹杂物。
这些浮渣和夹杂物会降低合金的机械性能和抗腐蚀性能。
因此,需要通过除渣工艺将这些杂质去除。
常用的除渣方法有静置沉淀法、离心除渣法等。
三、A356铝合金的净化A356铝合金的净化主要包括固溶处理、晶粒细化及人工时效等步骤。
1. 固溶处理固溶处理是将合金加热到一定温度,使合金元素充分溶解在基体中,然后迅速冷却,使合金元素以过饱和固溶体的形式存在于基体中。
这一过程可以消除合金中的偏析、成分不均等问题,提高合金的性能。
2. 晶粒细化晶粒细化是通过添加晶粒细化剂来改善合金的晶粒结构。
晶粒细化可以显著提高合金的机械性能和抗腐蚀性能。
常用的晶粒细化剂有钛、硼等元素。
《2024年汽车轮毂用A356铝合金的精炼及净化》范文

《汽车轮毂用A356铝合金的精炼及净化》篇一一、引言随着汽车工业的飞速发展,对汽车零部件的性能和轻量化要求越来越高。
其中,汽车轮毂作为承载整车重量和传输动力的重要部件,其材料的选择至关重要。
A356铝合金以其优异的铸造性能、力学性能以及良好的可加工性成为汽车轮毂的首选材料。
然而,其在使用前需要进行严格的精炼及净化处理,以保证其性能的稳定性和可靠性。
本文将详细探讨汽车轮毂用A356铝合金的精炼及净化工艺。
二、A356铝合金的成分及特性A356铝合金是一种常用的铸造铝合金,具有优良的铸造性能、良好的加工性能和较高的强度。
其主要成分包括铝、硅、铜等元素。
其中,硅元素可以提高合金的流动性,有利于铸造;铜元素可以提高合金的强度和硬度。
此外,A356铝合金还具有良好的耐腐蚀性和可回收性,符合环保要求。
三、精炼工艺A356铝合金的精炼工艺主要包括熔化、除气、除渣等步骤。
首先,将原材料按照一定比例加入炉中熔化。
在熔化过程中,需要严格控制温度和时间,以防止合金元素的氧化和烧损。
其次,通过除气工艺去除熔体中的气体杂质。
常用的除气方法包括气体喷吹法、真空除气法等,这些方法可以有效地去除熔体中的氢气和氧化物。
最后,通过除渣工艺去除熔体中的夹杂物和浮渣。
除渣方法包括机械除渣和化学除渣等,这些方法可以有效地去除熔体中的夹杂物和浮渣,提高合金的纯净度。
四、净化工艺A356铝合金的净化工艺主要包括精炼剂添加和炉内精炼两步。
首先,在精炼过程中加入适量的精炼剂,如氯化物等,这些精炼剂可以与熔体中的杂质元素发生化学反应,生成易于浮出熔体的化合物,从而达到净化合金的目的。
其次,在炉内进行精炼处理,使合金在高温下充分熔解和均匀混合,进一步去除合金中的杂质元素。
在净化过程中,还需要对合金进行充分的搅拌和静置处理,以使杂质元素充分上浮并去除。
五、结论通过对A356铝合金进行严格的精炼及净化处理,可以有效地去除合金中的杂质元素和气体杂质,提高合金的纯净度和性能稳定性。
铸造铝合金的熔炼工艺
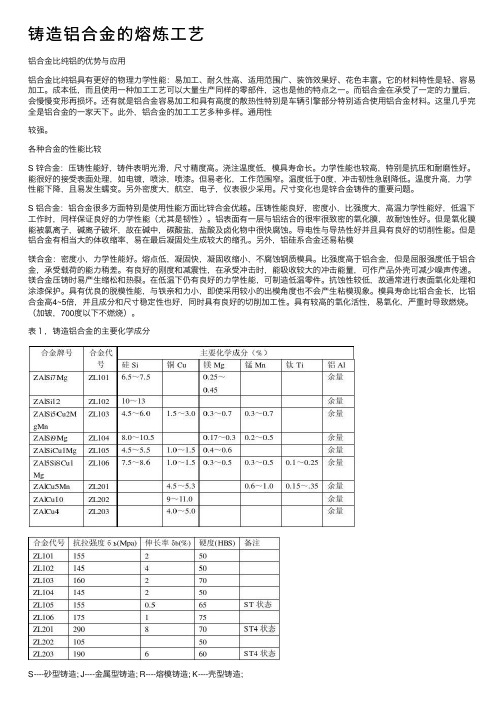
铸造铝合⾦的熔炼⼯艺铝合⾦⽐纯铝的优势与应⽤铝合⾦⽐纯铝具有更好的物理⼒学性能:易加⼯、耐久性⾼、适⽤范围⼴、装饰效果好、花⾊丰富。
它的材料特性是轻、容易加⼯。
成本低,⽽且使⽤⼀种加⼯⼯艺可以⼤量⽣产同样的零部件,这也是他的特点之⼀。
⽽铝合⾦在承受了⼀定的⼒量后,会慢慢变形再损坏。
还有就是铝合⾦容易加⼯和具有⾼度的散热性特别是车辆引擎部分特别适合使⽤铝合⾦材料。
这⾥⼏乎完全是铝合⾦的⼀家天下。
此外,铝合⾦的加⼯⼯艺多种多样。
通⽤性较强。
各种合⾦的性能⽐较S 锌合⾦:压铸性能好,铸件表明光滑,尺⼨精度⾼。
浇注温度低,模具寿命长。
⼒学性能也较⾼,特别是抗压和耐磨性好。
能很好的接受表⾯处理,如电镀,喷涂,喷漆。
但易⽼化,⼯作范围窄。
温度低于0度,冲击韧性急剧降低。
温度升⾼,⼒学性能下降,且易发⽣蠕变。
另外密度⼤,航空,电⼦,仪表很少采⽤。
尺⼨变化也是锌合⾦铸件的重要问题。
S 铝合⾦:铝合⾦很多⽅⾯特别是使⽤性能⽅⾯⽐锌合⾦优越。
压铸性能良好,密度⼩,⽐强度⼤,⾼温⼒学性能好,低温下⼯作时,同样保证良好的⼒学性能(尤其是韧性)。
铝表⾯有⼀层与铝结合的很牢很致密的氧化膜,故耐蚀性好。
但是氧化膜能被氯离⼦,碱离⼦破坏,故在碱中,碳酸盐,盐酸及卤化物中很快腐蚀。
导电性与导热性好并且具有良好的切削性能。
但是铝合⾦有相当⼤的体收缩率,易在最后凝固处⽣成较⼤的缩孔。
另外,铝硅系合⾦还易粘模镁合⾦:密度⼩,⼒学性能好。
熔点低,凝固快,凝固收缩⼩,不腐蚀钢质模具。
⽐强度⾼于铝合⾦,但是屈服强度低于铝合⾦,承受载荷的能⼒稍差。
有良好的刚度和减震性,在承受冲击时,能吸收较⼤的冲击能量,可作产品外壳可减少噪声传递。
镁合⾦压铸时易产⽣缩松和热裂。
在低温下仍有良好的⼒学性能,可制造低温零件。
抗蚀性较低,故通常进⾏表⾯氧化处理和涂漆保护。
具有优良的脱模性能,与铁亲和⼒⼩,即使采⽤较⼩的出模⾓度也不会产⽣粘模现象。
模具寿命⽐铝合⾦长,⽐铝合⾦⾼4~5倍,并且成分和尺⼨稳定性也好,同时具有良好的切削加⼯性。
高性能铝合金精炼剂论文

高性能铝合金精炼剂的探讨摘要:对于铝合金来说,由于al的化学活性很强,在熔炼过程中容易产生夹杂、气体等缺陷,它们在熔体凝固后会分布在合金内部,对材料性能产生很大影响。
因此,要提高铸造铝及其合金的性能,必须充分除去熔体中的氧化夹杂和气体,避免铸件中缺陷的产生。
关键词:铝合金精炼剂氧化物夹杂1 氧化物夹杂的类型熔融金属液在精炼处理以及运输过程中,氧化皮、金属间化合物、炉膛碎片等异质物容易被带入到金属液中,形成非金属夹杂,这些非金属夹杂主要是氧化物夹杂。
根据其在熔化和浇铸过程中形成时期的不同,可以分为一次氧化物夹杂和二次氧化物夹杂。
一次氧化物夹杂主要是指铝液浇注前形成的所有氧化物夹杂。
一次氧化物夹杂按其形状可分两类:一类是宏观组织中分布不均匀的大块夹杂物,这类夹杂物,使合金组织不连续,降低工件的气密性能,成为腐蚀的根源,明显降低铝合金的强度和塑性,也往往成为零件的裂纹源,第二类氧化物夹杂是指细小的、弥散的夹杂物,即使经过仔细净化也不能全除去,它使金属液粘度增大,降低凝固时铝液的补缩能力,易造成铸件的缩松。
二次氧化物夹杂,又称为内生夹杂物,主要是在浇注过程中形成的。
内生夹杂物一般来说分布比较均匀,颗粒也比较小。
铝液在浇注过程中的飞溅、紊流是二次氧化物夹杂的主要来源。
铝液在砂型中,与型砂中的水分作用,经水分解为氧和氢,氧与铝作用形成氧化物夹杂,氢溶于铝液。
2 杂质去除方法铝熔体中的有害杂质元素可用真空处理去除和精炼剂法化学去除。
真空处理就是在真空条件下,利用杂质元素的沸点低于铝(沸点为1800℃)和铝合金主要成分的沸点,通过蒸发使之去除。
真空处理可以将钙、锌等的量降低到lppm以下,但是还未获得工业应用。
有害杂质元素可与精炼剂发生化学反应而生成能够与铝分离的化合物,并通过精炼剂的吸附作用而被带入精炼渣中排出。
其它金属与氧、按和硫的生成热大小排列如下:氧化物:镁、铝、钠、硅、锰、锌、铁、镍、铅、铜;氯化物: 钠、镁、铝、锰、锌、铅、铁、镍、铜、硅;硫化物:钠、镁、锰、锌、铝、铁、铜、铅、硅、镍以去除氧化物夹杂为主的方法主要有:电熔剂法、过滤法和精炼剂法。
《2024年汽车轮毂用A356铝合金的精炼及净化》范文

《汽车轮毂用A356铝合金的精炼及净化》篇一一、引言随着汽车工业的快速发展,汽车轮毂作为汽车的重要组成部分,其材料的选择和制造工艺对汽车的性能和使用寿命具有重要影响。
A356铝合金因其良好的铸造性能、较高的强度以及优良的机械加工性能,成为制造汽车轮毂的理想材料。
本文将重点介绍A356铝合金的精炼及净化工艺,以确保汽车轮毂的高质量制造。
二、A356铝合金的特性A356铝合金是一种铝-硅系合金,具有优异的铸造性能、良好的机械加工性能和较高的强度。
此外,其优良的耐腐蚀性能和良好的表面处理性能也使其成为汽车轮毂制造的理想选择。
然而,A356铝合金在铸造过程中易产生气孔、夹杂物等缺陷,因此需要进行精炼和净化处理。
三、精炼及净化工艺1. 原料准备:选用高质量的A356铝合金锭作为原料,确保原料的纯度和成分符合要求。
同时,对原料进行严格的检查和筛选,去除杂质和不良品。
2. 熔炼:将选定的A356铝合金锭放入熔炉中,加热至合金完全熔化。
在熔炼过程中,需严格控制温度和时间,以防止合金元素的烧损和氧化。
3. 精炼:在合金熔化后,加入精炼剂进行精炼处理。
精炼剂可以去除合金中的气体、夹杂物等杂质,提高合金的纯净度和密度。
精炼过程中需注意控制精炼剂的添加量和时间,以确保精炼效果。
4. 净化:经过精炼处理后,还需进行进一步的净化处理。
通过真空吸气和过滤等方法,去除合金中的气体、夹杂物和氧化物等杂质。
净化处理可以提高合金的机械性能和耐腐蚀性能。
5. 铸造:经过精炼和净化处理的A356铝合金可以铸造成各种形状的汽车轮毂。
在铸造过程中,需控制好温度、压力和速度等参数,以获得高质量的轮毂产品。
四、工艺优势采用A356铝合金的精炼及净化工艺制造汽车轮毂具有以下优势:1. 提高合金的纯净度和密度,减少气孔、夹杂物等缺陷的产生;2. 提高合金的机械性能和耐腐蚀性能,延长汽车轮毂的使用寿命;3. 优化铸造过程,提高生产效率和产品质量;4. 降低生产成本,提高企业的经济效益和市场竞争力。
铝合金熔炼过程中除渣及精炼除气的分析
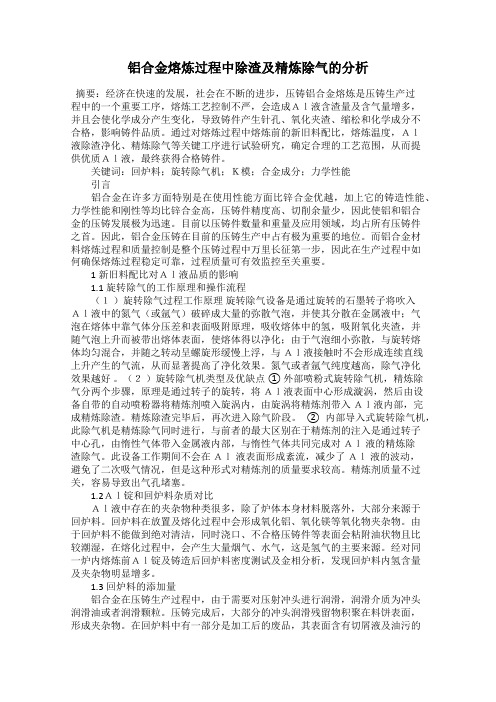
铝合金熔炼过程中除渣及精炼除气的分析摘要:经济在快速的发展,社会在不断的进步,压铸铝合金熔炼是压铸生产过程中的一个重要工序,熔炼工艺控制不严,会造成Al液含渣量及含气量增多,并且会使化学成分产生变化,导致铸件产生针孔、氧化夹渣、缩松和化学成分不合格,影响铸件品质。
通过对熔炼过程中熔炼前的新旧料配比,熔炼温度,Al液除渣净化、精炼除气等关键工序进行试验研究,确定合理的工艺范围,从而提供优质Al液,最终获得合格铸件。
关键词:回炉料;旋转除气机;K模;合金成分;力学性能引言铝合金在许多方面特别是在使用性能方面比锌合金优越,加上它的铸造性能、力学性能和刚性等均比锌合金高,压铸件精度高、切削余量少,因此使铝和铝合金的压铸发展极为迅速。
目前以压铸件数量和重量及应用领域,均占所有压铸件之首。
因此,铝合金压铸在目前的压铸生产中占有极为重要的地位。
而铝合金材料熔炼过程和质量控制是整个压铸过程中万里长征第一步,因此在生产过程中如何确保熔炼过程稳定可靠,过程质量可有效监控至关重要。
1新旧料配比对Al液品质的影响1.1旋转除气的工作原理和操作流程(1)旋转除气过程工作原理旋转除气设备是通过旋转的石墨转子将吹入Al液中的氮气(或氩气)破碎成大量的弥散气泡,并使其分散在金属液中;气泡在熔体中靠气体分压差和表面吸附原理,吸收熔体中的氢,吸附氧化夹渣,并随气泡上升而被带出熔体表面,使熔体得以净化;由于气泡细小弥散,与旋转熔体均匀混合,并随之转动呈螺旋形缓慢上浮,与Al液接触时不会形成连续直线上升产生的气流,从而显著提高了净化效果。
氮气或者氩气纯度越高,除气净化效果越好。
(2)旋转除气机类型及优缺点① 外部喷粉式旋转除气机,精炼除气分两个步骤,原理是通过转子的旋转,将Al液表面中心形成漩涡,然后由设备自带的自动喷粉器将精炼剂喷入旋涡内,由旋涡将精炼剂带入Al液内部,完成精炼除渣。
精炼除渣完毕后,再次进入除气阶段。
② 内部导入式旋转除气机,此除气机是精炼除气同时进行,与前者的最大区别在于精炼剂的注入是通过转子中心孔,由惰性气体带入金属液内部,与惰性气体共同完成对Al液的精炼除渣除气。
- 1、下载文档前请自行甄别文档内容的完整性,平台不提供额外的编辑、内容补充、找答案等附加服务。
- 2、"仅部分预览"的文档,不可在线预览部分如存在完整性等问题,可反馈申请退款(可完整预览的文档不适用该条件!)。
- 3、如文档侵犯您的权益,请联系客服反馈,我们会尽快为您处理(人工客服工作时间:9:00-18:30)。
精炼:从熔体中除去气体(对于铝熔体主要是氢气,占70-90%,主要来源见《铝合金熔铸
生产技术问答》-p77)、夹杂物和有害元素,以获得优良金属液对的工艺方法和操作过程称
为精炼,也称为净化。按作用原理可分为:吸附精炼和非吸附精炼。按精炼部位可分为炉内
精炼、浇包精炼和在线式精炼(或炉外连续精炼)。
铝合金精炼剂
从熔体中除去气体、夹杂物和有害元素的物质称为精炼剂。按常温物态分:固态精炼剂
(块状和粉末、液态精炼剂和气态精炼剂。按作用分:覆盖剂、除气剂、精炼剂(又称复合
净化剂)、打渣剂(又称渣铝分离剂)、清炉剂、除镁剂、除钠剂、除钙剂等。
气体精炼剂
◎惰性气体:不与铝熔体反应且在熔体中不溶解或溶解极微的气体,如氩气、氮气等
◎活性气体(能与熔体产生化学反应但不对铝熔体造成污染的气体,如氯气、氟利昂、六氟
化硫等)
◎混合气,如氮-氩、氩-氯、氮-氟利昂、氩-六氟化硫、氮-氯-一氧化氮等。
基本要求:保证达到预期精炼效果所必需的气体纯度。
固态和液态精炼剂
(1)按组分:
◎单组分溶剂:主要指氯盐精炼剂。氯盐精炼剂通常具有挥发性大、沸点较低、精炼处理时
反应比较激烈的特点;但氯盐一般都有吸湿性,反应最终产物氯化铝有一定毒性,污染环境。
对于某些氯盐还会增加金属杂质含量,其使用受到限制。
◎复合溶剂:指有两种或两种以上的单盐经混合或融合而成的盐类混合物。只是铝材行业目
前使用最广泛的一类精炼剂。
复合溶剂的基本要求:在加工温度范围内不产生有害于铝液的化学反应;有良好的精炼性,
或覆盖性,或打渣性,或要求的去除金属杂质的性能;熔点应低于熔炼温度,并在液态下保
持良好的流动性,不论哪种复合溶剂,都应便于铝液分离,且不黏附于炉壁和工具;密度应
小于工作温度下铝液的密度;彻底干燥;来源充足,供应方便,价格便宜。
复合溶剂的配方原理:(1)表面张力与溶剂成分的关系;(2)熔点与溶剂成分的关系;(3)
各成分的作用
(2)按使用目的:
◎防止氧化和吸气用的覆盖剂(要求小的表面张力和低的熔点)
◎除氢脱气的除气剂
◎除去氧化物夹杂用的净化剂
◎除去钠、镁、钾、钙等杂质元素的元素清除剂
◎清炉分离铝液用的除渣剂(对铝液有大的表面张力而对氧化渣要有较小的表面张力)
◎细化变质用的变质剂
铝及其合金中气体的来源
氢在液态铝合金和固态铝合金的饱和溶解度相差近17倍,因此即使合金液含氢量很低,
凝固时也会有大量的氢析出,在铸件中形成针孔和夹杂等缺陷。从而严重影响铝合金的力学
性能。熔入铝熔体中气体氢占85%以上,因而铝熔体中的“含气”可以近似地视为“含氢量”。
在熔体中铝与水汽发生下列反应:
可见,在一般熔体温度下,炉料、工具、熔剂、炉墙、炉底、和大气中的水汽都足于和铝
熔体产生反应而形成氢因此。在铝熔体中曾、是含有一定数量的氢。
铝及其合金熔体中非金属夹杂物的来源
铝熔体中的非金属夹杂物(主要为氧化夹杂物),绝大多数来源于熔炼和浇铸,按照化学
反应原理,铝与炉气中的𝑂2与、𝑁2、𝐻2𝑂 (汽)、𝐶𝑂2、CO、𝐶𝑛、𝐻𝑛、𝐻2等反应最终都生成𝐴𝑙
2𝑂3
与夹杂物,特别是铝熔体与水汽反应既生成氢又生成Al2O3,反应生成物都是对产品有害的
物质。
铝及其合金熔体中气体和非金属夹杂物的相互作用
r−𝐴𝑙2𝑂
3
与铝熔体接触的一面是致密的,与空气接触的一面是疏松的,吸附有水汽和氢,
当r−𝐴𝑙2𝑂3被卷入铝熔体时,所吸附的水汽和氢一起进入铝熔体,产生化学反应生成氢和氧
化杂物。因此.铝熔体中氧化夹杂物愈多,则铝熔体中的含氢量也愈高,溶解及吸附的氢也愈
多。同时,氧化夹杂物的存在,阻碍铝熔体脱氢,要脱氢必须同时除去氧化夹杂物。清除夹杂
物是除氢的基础。