两级圆柱齿轮减速器精度分析
机械类专业二级圆锥圆柱齿轮减速器设计说明书

二级圆锥-圆柱齿轮减速器摘要减速器是各类机械设备中广泛应用的传动装置。
减速器设计的优劣直接影响机械设备的传动性能。
减速器是原动机和工作机之间的独立的闭式传动装置,用来降低转速和增大转矩,以满足工作需要,在某些场合也用来增速,称为增速器。
选用减速器时应根据工作机的选用条件,技术参数,动力机的性能,经济性等因素,比较不同类型、品种减速器的外廓尺寸,传动效率,承载能力,质量,价格等,选择最适合的减速器。
减速器的类别、品种、型式很多,目前已制定为行(国)标的减速器有40余种。
减速器的类别是根据所采用的齿轮齿形、齿廓曲线划分;减速器的品种是根据使用的需要而设计的不同结构的减速器;减速器的型式是在基本结构的基础上根据齿面硬度、传动级数、出轴型式、装配型式、安装型式、联接型式等因素而设计的不同特性的减速器。
齿轮传动是现代机械中应用最广的一种传动形式。
它的主要优点是:○1瞬时传动比恒定,工作平稳,传动准确可靠,可传递空间任意两轴间的运动和动力○2适用的功率和速度范围广○3传动效率高○4工作可靠,使用寿命长○5外轮廓尺寸小,结构紧凑。
1绪论随着社会的发展和人民生活水平的提高,人们对产品的需求是多样化的,这就决定了未来的生产方式趋向多品种、小批量。
在各行各业中十分广泛地使用着齿轮减速器,它是一种不可缺少的机械传动装置. 它是机械设备的重要组成部分和核心部件。
目前,国内各类通用减速器的标准系列已达数百个,基本可满足各行业对通用减速器的需求。
国内减速器行业重点骨干企业的产品品种、规格及参数覆盖范围近几年都在不断扩展,产品质量已达到国外先进工业国家同类产品水平,承担起为国民经济各行业提供传动装置配套的重任,部分产品还出口至欧美及东南亚地区,推动了中国装配制造业发展。
1.1 本设计的目的及意义目的:A 通过设计熟悉机器的具体操作,增强感性认识和社会适应能力,进一步巩固、深化已学过的理论知识,提高综合运用所学知识发现问题、解决问题的能力。
二级减速齿轮

摘要齿轮传动是现代机械中应用最广的一种传动形式。
它的主要优点是:①瞬时传动比恒定、工作平稳、传动准确可靠;②适用的功率和速度范围广;③传动效率高,η=0.92-0.98;④工作可靠、使用寿命长;⑤外轮廓尺寸小、结构紧凑。
由齿轮、轴、轴承及箱体组成的减速器,用于原动机和工作机或执行机构之间,起匹配转速和传递转矩的作用,在现代机械中应用极为广泛。
国内的减速器多以齿轮传动、蜗杆传动为主,但普遍存在着功率与重量比小,或者传动比大而机械效率过低的问题。
另外,材料品质和工艺水平上还有许多弱点,特别是大型的减速器问题更突出,使用寿命不长。
国外的减速器,以德国、丹麦和日本处于领先地位,特别在材料和制造工艺方面占据优势,减速器工作可靠性好,使用寿命长。
但其传动形式仍以定轴齿轮传动为主,体积和重量问题,也未解决好。
当今的减速器是向着大功率、大传动比、小体积、高机械效率以及使用寿命长的方向发展。
减速器与电动机的连体结构,也是大力开拓的形式,并已生产多种结构形式和多种功率型号的产品。
近十几年来,由于近代计算机技术与数控技术的发展,使得机械加工精度,加工效率大大提高,从而推动了机械传动产品的多样化,整机配套的模块化,标准化,以及造型设计艺术化,使产品更加精致,美观化。
在21世纪成套机械装备中,齿轮仍然是机械传动的基本部件。
CNC机床和工艺技术的发展,推动了机械传动结构的飞速发展。
在传动系统设计中的电子控制、液压传动、齿轮、带链的混合传动,将成为变速箱设计中优化传动组合的方向。
在传动设计中的学科交叉,将成为新型传动产品发展的重要趋势。
关键字:减速器轴承齿轮机械传动目录毕业设计任务书 (2)摘要 (7)前言 (8)1机械传动装置的总体设计1.1分析和拟定传动装置的运动简图1.2电动机的选择…………………………………………1.2.1 已知条件及其它数据…………………………1.2.2 选择电动机………………………………………2计算总的传送比及分配各级的传动比………………3计算各轴的功率,转数及转矩………………………3.1 电动机轴的功率P,转速n及转矩T……………3.2 Ⅰ轴的功率P,转速n及转矩T…………………3.3 Ⅱ轴的功率P,转速n及转矩T…………………….3.4 Ⅲ轴的功率P,转速n及转矩T………………….4齿轮的设计计算………………………………………….4.1齿轮传动设计准则……………………………………4.2 直齿1、2齿轮的设计………………………………4.3 直齿3、4齿轮的设计………………………………5轴的设计及低速轴的强度校核……………………………5.1 概述……………………………………………………5.1.1轴的作用5.1.2 轴的类型5.1.3轴的形状和名称5.1.4影响轴技术参数和形状的因素5.1.5轴的设计应掌握的条件5.1.6轴的强度、刚度5.1.7轴的设计原则5.1.8零件在轴上的固定5.2 Ⅰ轴的设计………………………………………………5.3 Ⅱ轴的设计………………………………………………….5.4 Ⅲ轴的设计…………………………………………………6键联接的选择及其校核计算………………………………………6.1 键的选择……………………………………………………6.2 键的设计……………………………………………………7滚动轴承的选择及其校核计算…………………………………7.1概述…………………………………………………………7.2 滚动轴承的选择及有关计算………………………………8设计减速器箱体,箱壳及其附件………………………………9润滑方式的确定…………………………………………………总结…………………………………………………………………………致谢…………………………………………………………………………参考文献……………………………………………………………………前言机械(machine),源自于希腊语之mechine及拉丁文mecina,原指“巧妙的设计”,作为一般性的机械概念,可以追溯到古罗马时期,主要是为了区别与手工工具。
两级圆柱齿轮减速器精度分析

机械精度课程大作业两级圆柱齿轮减速器装配分析2014年12月目录一、减速器的工作原理及实际应用二、减速器的主要组成部件精度及配合选用分析三、相关零件图四、装配图(部分)一、减速器的工作原理和实际应用1、两级圆柱齿轮减速器的工作原理2、减速器的实际应用减速机是国民经济诸多领域的机械传动装置,食品轻工、电力机械、建筑机械、冶金机械、水泥机械、环保机械、电子电器、筑路机械、水利机械、化工机械、矿山机械、输送机械、建材机械、橡胶机械、石油机械等行业领域对减速机产品都有旺盛的需求。
二、减速器的组成部件精度及配合选用分析(部分装配图)1、轴的精度和配合选用1)确定尺寸精度如图,输出轴上Φ32mm轴径与一个轴承的内圈配合,Φ60mm的轴颈与齿轮基准孔配合,Φ45mm轴头与减速器外开始齿轮传动主动齿轮(图中未画出)基准孔配合,Φ68mm轴肩的两端面分别为齿轮和滚动轴承内圈的轴向定位基准面。
(轴装配图)该轴转速不高,承受载荷不大,有轴向力,故轴承采用7211 GB/T 297-1994圆锥滚子轴承,其额定动载荷为52800N。
经计算,该轴承的当量动载荷为3036N,与额定动载荷的比值小于0.07,则该轴承的负荷状态属于轻负荷。
轴承工作时承受定向负荷的作用,内圈与轴颈一起转动,外圈与箱体固定不旋转,因此轴承内圈属于负荷方向旋转。
根据以上计算,查表6.2可知,轴颈公差带代号为Φ55k6。
(表6.2)选取安装在Φ60mm轴颈上的从动轮的最高精度等级为7级,查表10.10(表10.10)确定齿轮内孔尺寸公差为IT7,轴比孔高一级,取IT6。
同理安装在该轴端部Φ45mm轴颈上的开式齿轮精度等级为9级,该轴头尺寸公差为IT7Φ60mm轴颈与齿轮基准孔的配合采用基孔制,齿轮基准孔公差带代号为Φ60H7。
(表3.10)查表3.10,考虑输出轴上齿轮传递扭矩较大,采用过盈配合,轴颈的尺寸公差带为Φ60r6,齿轮与轴配合代号为Φ58H7/r6。
机械设计课程设计二级展开式直齿圆柱齿轮减速器(全套图纸三维)
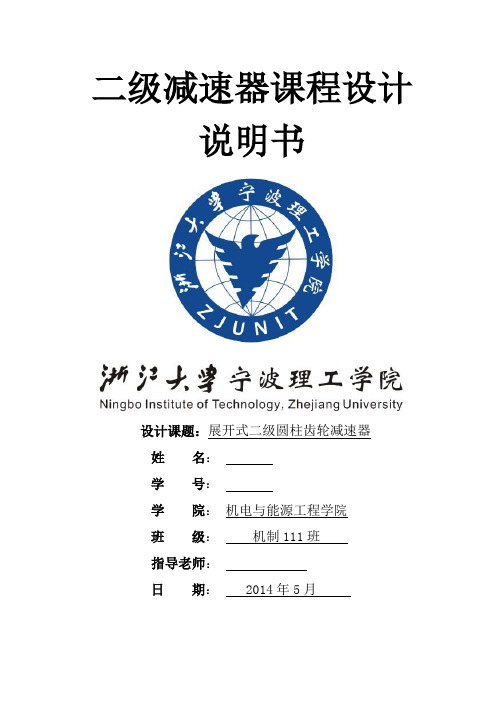
(1). 传动 装置总传动 比 (2). 分配 传动装置各 传动比
由[1]327 页中表 8-184 选常用的同步转速为1000 r min 的 Y 系列电动 Υ132Μ1− 6 ,
其满载转速为 nω = 960 r min 。
nω =960r min
总传动比: i = nm = 960 = 13.40 nω 71.62
对于两级展开式圆柱齿轮减速器,一般按齿轮浸油润滑要求,即各级大齿轮直径相近
i = 13.40 i1 = 4.19
的条件分配传动比,因此,速器高速级和低速级的传动比分别取 i1 = 4.19 ,i2 = 3.2 。 i2 = 3.2
3. 计 算 传 动装置的 运动和动 力参数
(1). 各轴 转速的计算
(3). 确定 电动机转速
卷筒轴作为工作轴,其转速为:
nω
=
6 × 10 4Vm πD
=
6 ×104 ×1.5 π × 400
= 71.62 r
min
nω = 71.62r min
-4-
2. 计算传 动装置的 总传动比 和分配各 级传动比
传动装置总传动比:按[1]11 页中表 2-3 推荐的各传动机构传动比的二级展开式圆柱齿
×
0.97 2
=
0.89
故 Ρo = Ρω KW = 4.63KW = 5.20KW
η
0.89
Ρo = 5.20KW
因载荷平稳,电动机额定功率 Ρm 只需略大于 Ρ o 即可。按[1]327 页中表 8-184Y 系列
闭式三相异步电动机技术数据,选电动机的额定功率为 Ρm =5.5kw
Ρm =5.5kw
= 9550 ΡI nI
= 9950 5.07 = 50.44N ⋅ m 960
二级斜齿圆柱齿轮减速器中间轴强度校核方法研究

二级斜齿圆柱齿轮减速器中间轴强度校核方法研究二级斜齿圆柱齿轮减速器是一种常用的传动装置,广泛应用于工业生产中。
中间轴作为该减速器的重要组成部分,其强度校核是保证减速器正常运转的关键之一。
本文将从中间轴的强度校核方法入手,探讨二级斜齿圆柱齿轮减速器中间轴的强度校核方法。
一、中间轴的作用与结构中间轴是二级斜齿圆柱齿轮减速器的一个重要组成部分,其作用是将输入轴和输出轴之间的转矩传递给输出轴,起到减速作用。
中间轴的结构一般为圆柱形,其两端分别与输入轴和输出轴相连,中间部分则为齿轮的支撑部分。
二、中间轴的强度校核方法中间轴的强度校核是保证减速器正常运转的关键之一。
其校核方法主要有以下几种:1. 极限强度法极限强度法是一种传统的中间轴强度校核方法。
其基本思想是根据中间轴的材料和几何形状,计算其承受最大转矩时的强度,然后与实际工作转矩进行比较,判断其是否足够强度。
这种方法简单易行,但忽略了中间轴在工作过程中的实际应力状态,容易导致误判。
2. 应力分析法应力分析法是一种综合考虑中间轴在工作过程中应力状态的强度校核方法。
其基本思想是根据中间轴的几何形状和工作条件,采用有限元分析等方法计算其在工作过程中的应力状态,然后根据材料的应力应变关系,计算出中间轴的应力和应变,进而判断其是否足够强度。
这种方法比较精确,但计算量较大,需要一定的计算机技术支持。
3. 经验公式法经验公式法是一种基于实验数据和经验公式的强度校核方法。
其基本思想是根据中间轴的几何形状和工作条件,结合实验数据和经验公式,计算出中间轴的强度,并判断其是否足够强度。
这种方法简单易行,但准确性较差,容易产生误差。
三、中间轴的强度校核注意事项在进行中间轴的强度校核时,需要注意以下几点:1. 中间轴的材料应选择高强度、高韧性的材料,并考虑其疲劳寿命和可焊性等因素。
2. 中间轴的几何形状应尽量简单,避免出现过多的几何结构,以减少应力集中和裂纹的产生。
3. 中间轴的强度校核应综合考虑其在工作过程中的应力状态,采用合适的强度校核方法,以确保其足够强度。
二级展开式斜齿圆柱齿轮减速器设计说明

机械设计课程设计计算手册设计题目:两级圆锥圆柱齿轮减速机一、设计数据及要求1.1 传输方案示意图图 1 传输方案示意图1.2 原始数据表 1:原始数据输送带张力 F(N) 输送带速度 V(m/s) 滚筒直径 D (mm)1000 2.6 4001.3 工作条件二班制,使用寿命10年,连续单向运转,负载相对稳定,小批量生产,输送链速允许误差为链速的5%。
2、电机选型及传动运动动态参数计算、齿尖高度系数0、等位。
输送机为通用工作机,速度不高,故选用佛商学院大齿轮:45质)3.初步确定轴的最小直径 初步估计轴的最小直径。
所选轴的材料为45钢(调质),根据《机械设计(第八版)》表15-3,0112A =得mm 4.141440061.3112n P A d 33I I 0min === 输入轴的最小直径是安装联轴器的直径12d 。
为了使所选12d 的轴径与联轴器的直径相适应,需要同时选择联轴器型号。
联轴器的计算扭矩见2ca A T K T =《机械设计(第八版)》表14-1。
由于扭矩变化很小,因此将5.1A=K 其视为m 4515.30203015.12ca ⋅=⨯==N T K T A查阅《机械设计课程设计》表14-1,选用Lx2型弹性销联轴器,其工作扭矩为560N.m ,电机轴径为28mm ,联轴器直径不宜过小。
Take 12d = 20mm ,半联轴器长度L = 112mm ,半联轴器与轴配合的轮毂孔长度为62mm 。
4、轴结构设计(1) 拟定轴上零件的装配图(见图2)图 3 输入轴上的零件组装(2)根据轴向定位的要求确定轴各段的直径和长度1)为了满足半联轴器的轴向定位,需要在12段轴的右端做一个台肩,所以取23段的直径mm 23d 23=。
左端与轴端挡圈定位,12段长度应适当小于L ,取12L =60mm2)滚动轴承的初步选择。
由于轴承同时承受径向力和轴向力,单列找到圆锥滚子轴承,参考工作要求,根据mm 23d 23=《机械设计课程设4.14d min =2ca A T K T ==30.45m ⋅N12d =20L=112N F F N F F Nd T F t a nt r t 58.577tan 79.868cos tan 73.231521======I Iββα已知锥齿轮的平均节圆直径()mm 10.1585.01d d 22m =-=R ϕNF F N F F N F n t a n t r t 20.250sin tan 38.83cos tan 59.724d 22222222m 2=====T =δαδα圆周力1t F , 2t F , 径向力1r F ,2r F 和轴向力1a F ,2a F 如下图所示:25.22=ca σ57279min/48088.2===I I I I I I T r n kw Pmm d 47.49= NF NF N F a r t 58.57779.86873.2315===mm10.158d 2m =图 4. 弯矩和扭矩图3.初步确定轴的最小直径初步估计轴的最小直径。
机械设计课程设计 双级圆柱齿轮减速器
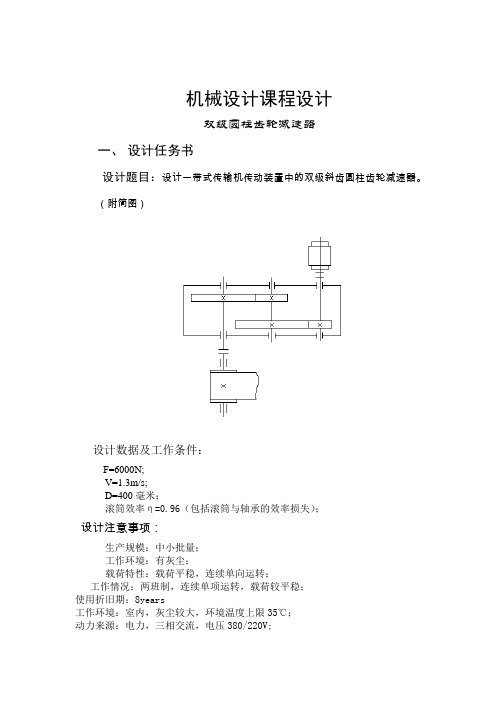
机械设计课程设计双级圆柱齿轮减速器一、设计任务书设计题目:设计一带式传输机传动装置中的双级斜齿圆柱齿轮减速器。
(附简图)设计数据及工作条件:F=6000N;V=1.3m/s;D=400毫米;滚筒效率η=0.96(包括滚筒与轴承的效率损失);设计注意事项:生产规模:中小批量;工作环境:有灰尘;载荷特性:载荷平稳,连续单向运转;工作情况:两班制,连续单项运转,载荷较平稳;使用折旧期:8years工作环境:室内,灰尘较大,环境温度上限35℃;动力来源:电力,三相交流,电压380/220V;检修间隔期:四年一大修,二年一中修,半年一小修;制造条件及成产批量:一般机械厂制造,小批量生产。
设计由减速器或其它机械传动装配图1张。
零件图2张,及设计计算说明书一份组成。
设计中所有标准均按我国标准采用。
二.传动方案的分析与拟定Nw=60×1000V/πD=62.1 r/min一般选用同步转速为1000r/min 或者1500r/min 的电动机作原动机,则可估算出传动装置的总传动比i 约为70或47。
根据这个传动比及工作条件可有三种方案,对这三种传动方案进行分析比较可知:选择链传动,减速器的尺寸小,链传动的尺寸较紧凑。
三、电动机的选择3.1.电动机类型的选择根据工作条件及工作环境,选用卧式封闭型Y(IP44)系列三相交流异步电动机。
3.2.电动机容量1)工作所需功率Pw=F ·V ·nw/9550=6000×1.3/9550=8.125Kw2)电动机输出功率Pd为了计算电动机所需功率Pd ,先要确定从电动机到工作机之间的总功率η。
设1η、2η、3η、4η、5η分别为弹性联轴器、闭式齿轮传动(设齿轮精度为8级)、滚动轴承、开式滚子链传动、滚筒的效率,由表查的: 1η=0.99;2η=0.97; 3η=0.99; 4η=0.92; 5η=0.96 则传动装置的总效率为225····0.99*0.97*0.99*0.92*0.96=0.7745 22512345η=ηηηηη电动机所需功率为Pd= Pw/η=(8.1/0.7745)Kw=10.46Kw 由表选取电动机的额定功率为11 Kw 。
同轴式二级圆柱齿轮减速器

目录1. 题目及总体分析 (2)2. 各主要部件选择 (2)3. 选择电动机 (3)4. 分配传动比 (3)5. 传动系统的运动和动力参数计算 (4)6. 设计高速级齿轮 (5)7. 设计低速级齿轮 (10)8. 减速器轴及轴承装置、键的设计 (14)1轴(输入轴)及其轴承装置、键的设计 (15)2轴(中间轴)及其轴承装置、键的设计 (21)3轴(输出轴)及其轴承装置、键的设计 (27)9. 润滑与密封 (32)10. 箱体结构尺寸 (32)11. 设计总结 (33)12. 参考文献 (33)一•题目及总体分析题目:设计一个带式输送机的减速器给定条件:由电动机驱动,运输带工作拉力为4000N,运输带速度为1.6m/s,运输机滚筒直径为400mm。
自定条件:工作寿命10年(设每年工作300天),三年一大修,连续单向运转,载荷平稳,室内工作,有粉尘生产批量:10台减速器类型选择:选用同轴式两级圆柱齿轮减速器。
整体布置如下:图示:1为电动机,2及6为联轴器,3为减速器,4为高速级齿轮传动,5为低速级齿轮传动,7为输送机滚筒。
辅助件有:观察孔盖,油标和油尺,放油螺塞,通气孔,吊环螺钉,吊耳和吊钩,定位销, 启盖螺钉,轴承套,密封圈等.0二•各主要部件选择三.选择电动机四•分配传动比五•传动系统的运动和动力参数计算第5页共44页第7页共44页第10页共44页第12页共44页第14页共44页六•设计高速级齿轮目的过程分析(8)计算弯曲疲劳许用应力取弯曲疲劳安全系数S= 1.4,由式10 —12得K FN1 FE1[F]1——s0.85 500303.57MPa1.4K FN2 FE2[F】2——s0.88-380238.86MPa1.4Y Fa Y sa(9)计算大小齿轮的[F]Y Fa1Y Sa1 2.592结论齿数乙26Z2 94按齿根弯曲强度设计[F ]1Y Fa 2Y Sa2[F ]2大齿轮的数据大2)设计计算303.5715960.013632194 17830.01638238.86m n 32 2.08 6.3 £ 0.88 曲14。
- 1、下载文档前请自行甄别文档内容的完整性,平台不提供额外的编辑、内容补充、找答案等附加服务。
- 2、"仅部分预览"的文档,不可在线预览部分如存在完整性等问题,可反馈申请退款(可完整预览的文档不适用该条件!)。
- 3、如文档侵犯您的权益,请联系客服反馈,我们会尽快为您处理(人工客服工作时间:9:00-18:30)。
机械精度课程大作业两级圆柱齿轮减速器装配分析2014年12月目录一、减速器的工作原理及实际应用二、减速器的主要组成部件精度及配合选用分析三、相关零件图四、装配图(部分)一、减速器的工作原理和实际应用1、两级圆柱齿轮减速器的工作原理2、减速器的实际应用减速机是国民经济诸多领域的机械传动装置,食品轻工、电力机械、建筑机械、冶金机械、水泥机械、环保机械、电子电器、筑路机械、水利机械、化工机械、矿山机械、输送机械、建材机械、橡胶机械、石油机械等行业领域对减速机产品都有旺盛的需求。
二、减速器的组成部件精度及配合选用分析(部分装配图)1、轴的精度和配合选用1)确定尺寸精度如图,输出轴上Φ32mm轴径与一个轴承的内圈配合,Φ60mm的轴颈与齿轮基准孔配合,Φ45mm轴头与减速器外开始齿轮传动主动齿轮(图中未画出)基准孔配合,Φ68mm轴肩的两端面分别为齿轮和滚动轴承内圈的轴向定位基准面。
(轴装配图)该轴转速不高,承受载荷不大,有轴向力,故轴承采用7211 GB/T 297-1994圆锥滚子轴承,其额定动载荷为52800N。
经计算,该轴承的当量动载荷为3036N,与额定动载荷的比值小于0.07,则该轴承的负荷状态属于轻负荷。
轴承工作时承受定向负荷的作用,内圈与轴颈一起转动,外圈与箱体固定不旋转,因此轴承内圈属于负荷方向旋转。
根据以上计算,查表6.2可知,轴颈公差带代号为Φ55k6。
(表6.2)选取安装在Φ60mm轴颈上的从动轮的最高精度等级为7级,查表10.10(表10.10)确定齿轮内孔尺寸公差为IT7,轴比孔高一级,取IT6。
同理安装在该轴端部Φ45mm轴颈上的开式齿轮精度等级为9级,该轴头尺寸公差为IT7Φ60mm轴颈与齿轮基准孔的配合采用基孔制,齿轮基准孔公差带代号为Φ60H7。
(表3.10)查表3.10,考虑输出轴上齿轮传递扭矩较大,采用过盈配合,轴颈的尺寸公差带为Φ60r6,齿轮与轴配合代号为Φ58H7/r6。
同理,Φ45mm轴与开式齿轮孔的配合亦采用基孔制,轴的尺寸公差带为Φ45n7,齿轮公差带为Φ45H8,配合代号为Φ45H8/n7,过渡配合。
④Φ55k6、Φ60r6、Φ45n7的极限偏差由表3.2和表3.4查出Φ60r6和Φ45n7两个轴径和轴上零件的固定采用普通平键联结,键槽宽度分别为18mm和14mm。
键槽公差带由表8.1中正常联结分别确定为18N9(0043.-)和14N9(0043.-),键槽深度极限偏差由表8.1分别确定为53(02.-)和39.5(02.-)。
2)确定几何精度为保证选定的配合性质,对轴颈Φ55k6、轴Φ60r6、轴Φ45n7都采用包容要求。
按0级滚动轴承要求,查表6.6选取轴颈的圆柱度公差为0.005mm 。
(表6.6)为保证输出轴的使用要求,轴颈Φ55、Φ60和Φ45的轴线应分别与安装基准的公共轴线通州。
由齿轮精度为8级,由式10.15确定轴颈对公共基准轴线A-B 的径向跳动公差值为r t =0.3, p F =0.3*0.07=0.021Φ60mm 轴对公共基准轴线A-B 的径向圆跳动公差值为0.022mm ,Φ45mm 轴头对基准轴线的径向圆跳动公差为0.017mm (类比法)。
轴颈的键槽相对于这个轴的轴线对称度公差值查表 4.16按8级确定为0.02mm 。
3)确定表面粗糙度参数值查表6.7选取Φ55k6轴颈表面粗糙度参数Ra的上限值为0.8μm(表6.7)查表5.7选取Φ45n7和Φ60r6两轴径表面粗糙度参数Ra的上限值都为0.8μm。
(表5.7)Φ60mm轴段的表面与密封件接触,此轴径表面粗糙度参数Ra的上限值一般取为1.6μm。
键槽配合表面的表面粗糙度参数Ra的上限值取为3.2μm;非配合表面的Ra 的上限值取为6.3μm。
输出轴其它表面粗糙度参数Ra的上限值取为152.5μm。
4)确定未注尺寸公差等级与未注几何公差等级输出轴上未注公差及几何公差分别按GB/T1804-m和GB/T1184-K给出,并在装配图“技术要求”中加以说明。
三、相关零件图①确定齿轮精度等级一级从动轮转速和分度圆直径则查表10.5确定减速器从动轮平稳性精度为8级(表10.5)②确定齿轮必检偏差项目及其允许值查表10-1得02.0,017.0,069.0α=±==F f F pt P(表10-1)查表10-2得021.0β F(表10-2)确定齿轮的最小法向侧隙和齿厚上、下偏差 (1)最小法向侧隙确定查表10-6,a=117介于100与200之间,用插值法(式10-2)得(2)齿厚上、下偏差的计算查表10.1、10.2得L=62,b=45查表10.8得则齿原上偏差为94.0)tan cos 2(min -=++-=n a n bn bn sns f J j E αα查表10.1和表10.7得145.0926.1055.0===IT b P r r因此齿厚公差为613.020tan 2055.0145.020tan 22222=︒⋅+=︒⋅+=r r sn F b T齿厚下偏差为207.0113.0094.0-=--=-=sn sns sni T E E(3)公法线长度及其上、下偏差的计算()[]nn n k inv Z K m w απα'5.0cos +-=3770.0cos tan tan ==βααn t 端面分度圆压力角为 "18'3920︒=t α在 kw 的计算式中引用齿数58.100014904.0016473.091'=⨯==n t inv inv ZZ αα当量齿数)12(68.115.09'取=+=Z K则716.70)]'5.0([cos =+-=n n n k inv z k m w απα按式10.8和Fr=0.055可得 102.0sin 72.0cos -=-=n r n sns bns F E E αα 181.020sin 72.0cos -=+=︒n sni i bn E E α 102.0181.0716.70--=k w④确定尺寸公差和几何公差(1)基准孔的尺寸公差和几何公差查表10.10得基准孔Φ38的公差为IT7,采用包容要求,即025.0038738+Φ=ΦH取按式10.12、10.13计算值中较小者069.0069.01.01.00016.0)(04.0=⨯==p F F bL β取 t =0.0016(2)齿顶圆的尺寸公差和几何公差查表10.10得齿顶圆的尺寸公差为IT8,即072.05.19285.192-Φ=Φh齿顶圆的圆柱度公差值t =0.0616(同基准孔)按式10.15得齿顶圆对基准孔的径向圆跳动公差0207.0069.03.03.0=⨯==p r F t(3)基准端面的圆跳动公差 按式10.14的基准面对基准孔的轴向跳动公差017.0021.0455.1832.02.0=⨯⎪⎭⎫ ⎝⎛⨯=⋅⎪⎭⎫ ⎝⎛=βF b D t d i⑤确定齿轮副精度(1)齿轮副中心距极限偏差查表10.8得027.0±=a f则图上标注为mma 027.0117±=(2)轴线平行度偏差的最大029.0=⎪⎪⎭⎫ ⎝⎛=∑βδF b L f014.05.0=⎪⎪⎭⎫ ⎝⎛=∑ββF b L f⑥确定内孔键槽尺寸及基极限偏差采用平键联结,根据齿轮孔直径D=Φ38mm ,参照机器中采用的尺寸,选键槽宽度b=10mm ,正常联结,查表8.1得键槽宽度的公差带10JS9(±0.018),轮毂槽mmt 3.32=mmt D 8.413.3382=+=+上下偏差为+0.2和0,查表4.16得对称度公差为0.015mm 。
⑦确定齿轮各部分的表面粗糙度参数值由表10.11,按7级精度查得齿轮表面的粗糙度Ra 的上限值为1.25um 。
由表10.12查得基准孔表面粗糙度Ra 的上限值为1.25—2.5um ,取2um ;基准端面和顶圆端面粗糙度Ra 上限值为2.5—5um ,取3.2um 。
键槽配合表面Ra 的上限值取 3.2um ,非配合表面Ra 的上限值取 6.3um ,齿轮其余表面Ra 的上限值取12.5um 。
(表10.11) ⑧确定齿轮上未注尺寸及几何公差等级齿轮上未注尺寸公差按GB/T 1804——2000给出,这里取中等级m;未注几何公差按GB/T 1184——1996给出,这里取K 级。
轴零件图齿轮零件图2、减速器中重要结合面的配合尺寸1)圆锥滚子轴承与轴颈、箱体轴承孔的配合对滚动轴承内圈、外圈分别与轴颈、轴承孔相配合的尺寸只标注轴颈和轴承孔尺寸的公差带代号。
齿轮轴、输出轴的轴颈的公差带代号分别为Φ45n7和Φ55k6。
箱体轴承孔的公差带代号分别为Φ62H7和Φ100H7。
2)轴承端盖与箱体轴承孔的配合尺寸轴承端盖用于轴承外圈的轴向定位。
它与轴承孔的配合要求为装配方便且不产生较大的偏心。
因此,该配合宜采用间隙配合。
由于轴承孔的公差带已经按轴承要求确定,故应以轴承孔公差带为基准来选择轴承端盖软煮面的公差带,由表12.2所示为其基本偏差代号,此处结合配合性质要求,所以轴承端盖圆柱面的标准公差等级比轴承孔低2——3级。
由表12.2可确定四处轴承孔与轴承端盖圆柱面的配合尺寸分别为Φ62H7/f9和Φ100H7/f9。
3)套筒孔与轴颈配合尺寸套筒用于从动齿轮与轴承内圈的轴向定位。
套筒孔与轴颈的配合要求与轴承端盖圆柱面与箱体轴承孔的配合要求类似,由轴颈基本偏差确定套筒的基本偏差,如表12.2所示。
套筒孔的标准公差等级比轴颈低2~3级。
又轴颈的基本偏差代号为k,故套筒孔与轴颈的配合代号为Φ55D9/k6。
(表12.2)4)从动齿轮基准孔与输出轴轴颈的配合考虑到输出轴上齿轮传递的扭矩较大,应采用过盈配合,应加键链接。
根据齿轮和输出轴精度设计的结果,基准孔公差带代号为Φ60H7,轴公差带代号为Φ60r6,故齿轮与轴配合的配合代号为Φ60H7/r6。
四、装配图(部分)。