影响塑料制品收缩率的因素
塑料制品收缩及其措施分析
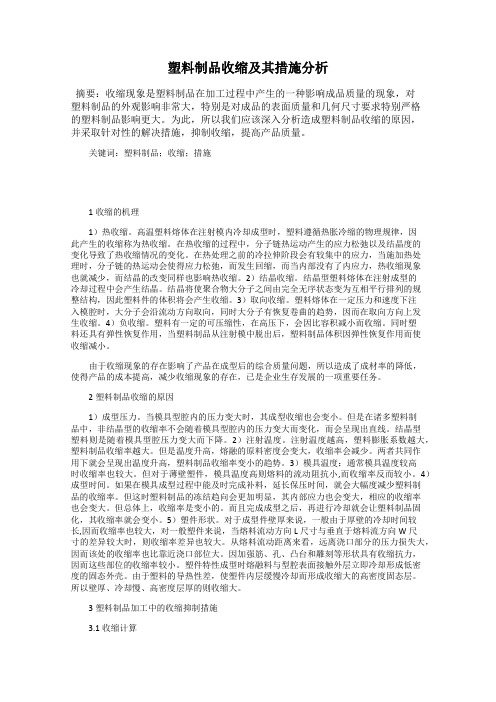
塑料制品收缩及其措施分析摘要:收缩现象是塑料制品在加工过程中产生的一种影响成品质量的现象,对塑料制品的外观影响非常大,特别是对成品的表面质量和几何尺寸要求特别严格的塑料制品影响更大。
为此,所以我们应该深入分析造成塑料制品收缩的原因,并采取针对性的解决措施,抑制收缩,提高产品质量。
关键词:塑料制品;收缩;措施1收缩的机理1)热收缩。
高温塑料熔体在注射模内冷却成型时,塑料遵循热胀冷缩的物理规律,因此产生的收缩称为热收缩。
在热收缩的过程中,分子链热运动产生的应力松弛以及结晶度的变化导致了热收缩情况的变化。
在热处理之前的冷拉伸阶段会有较集中的应力,当施加热处理时,分子链的热运动会使得应力松弛,而发生回缩,而当内部没有了内应力,热收缩现象也就减少,而结晶的改变同样也影响热收缩。
2)结晶收缩。
结晶型塑料熔体在注射成型的冷却过程中会产生结晶。
结晶将使聚合物大分子之间由完全无序状态变为互相平行排列的规整结构,因此塑料件的体积将会产生收缩。
3)取向收缩。
塑料熔体在一定压力和速度下注入模腔时,大分子会沿流动方向取向,同时大分子有恢复卷曲的趋势,因而在取向方向上发生收缩。
4)负收缩。
塑料有一定的可压缩性,在高压下,会因比容积减小而收缩。
同时塑料还具有弹性恢复作用,当塑料制品从注射模中脱出后,塑料制品体积因弹性恢复作用而使收缩减小。
由于收缩现象的存在影响了产品在成型后的综合质量问题,所以造成了成材率的降低,使得产品的成本提高,减少收缩现象的存在,已是企业生存发展的一项重要任务。
2塑料制品收缩的原因1)成型压力。
当模具型腔内的压力变大时,其成型收缩也会变小。
但是在诸多塑料制品中,非结晶型的收缩率不会随着模具型腔内的压力变大而变化,而会呈现出直线。
结晶型塑料则是随着模具型腔压力变大而下降。
2)注射温度。
注射温度越高,塑料膨胀系数越大,塑料制品收缩率越大。
但是温度升高,熔融的原料密度会变大,收缩率会减少。
两者共同作用下就会呈现出温度升高,塑料制品收缩率变小的趋势。
聚丙烯注塑加工成型收缩率的影响因素

来源于:注塑塑料网/聚丙烯注塑加工成型收缩率的影响因素塑料制品的质量取决于材料(树脂、加工助剂等)的选择和注塑加工条件。
塑料成型加工是一门科学与工程紧密结合的交叉学科,其任务是:了解材料的特性,确定最适宜加工条件,制取最佳性能产品。
热塑性塑料注塑制品成型时收缩率与结晶度及球晶大小密切相关,球晶与聚合形式及助剂有关,而结晶直不仅取决于化学结构而且还受到加工过程中冷却速率、熔体温度、模具温度、制品厚度等的影响,给模具设计确定型腔尺寸和控制制品尺寸精度带来困难。
生产中迫切需要了解注塑工艺对各种塑料收缩率的影响规律。
聚丙烯具有较高的结晶性,给产品带来较好的刚性,但也决定了其较大的制品成型收缩率,给其在注塑领域的应用带来了不少的限制,通常,PP的结晶度通常为40~70%,其它为非定形区,由此它的成型收缩率会出现在1~2.5%范围内。
在与一些下游应用厂家的交流中经常碰到需要解决降低PP的成型收缩率的问题。
因此不少石化研究院所对在PP 的生产和加工两个过程中如何降低其收缩率等问题进行了研究。
2 常用聚丙烯加工技术聚丙烯作为增长最为强劲的通用塑料,与其具有较宽的成型加工适应性有很大关系。
如PP可注塑、吹塑、真空热成型、涂覆、旋转成型,也可熔接、机加工、电镀和发泡等,并可在金属表面喷涂。
目前,常用的聚丙烯成型加工技术有注塑、挤塑、薄膜、发泡等。
常用聚丙烯按聚合方式及其链段结构的不同,可分为均聚、无规共聚以及嵌段共聚,通常注塑采用均聚和嵌段共聚PP,挤塑三种都可以使用,吹塑和薄膜(如 BOPP)可采用均聚和无规共聚PP。
目前市场上注塑成型和挤出PP使用量较大。
一般注塑温度在180~210℃之间,注塑压力在65~140MPa,模具温度为40~70℃。
预干燥温度在80℃左右[1]。
3 聚丙烯的成型收缩性与注塑工艺聚丙烯的成型收缩率一直是注塑厂家所关心的指标,成型收缩率包括结晶收缩,取向收缩、热收缩、负收缩和后收缩。
通常,PP从注射温度降低到室温时,体积收缩较大,收缩率一般在1%~2.5%,且具有各向异性,并存在占总收缩宰10%-15%的后收缩[2]。
吹塑收缩率

吹塑收缩率吹塑收缩率是指塑料制品在冷却后与模具的尺寸差异程度,它是衡量塑料制品尺寸稳定性的重要指标。
收缩率的大小直接影响到塑料制品的精度和质量。
在塑料加工过程中,吹塑收缩率的控制是至关重要的。
需要明确的是,塑料在加工过程中会因为温度变化而发生收缩。
在吹塑过程中,塑料被加热到熔融状态后,通过气流吹气将其吹到模具的壁厚上。
随着塑料冷却,它会逐渐收缩,与模具壁厚形成一定的尺寸差异。
吹塑收缩率的大小与塑料材料的种类、成分、加工温度、冷却速度等因素有关。
不同种类的塑料具有不同的收缩率。
一般来说,聚乙烯(PE)的收缩率约为1.5%至2%,聚丙烯(PP)的收缩率约为1%至2%,聚氯乙烯(PVC)的收缩率约为0.3%至1%。
此外,根据不同的加工温度和冷却速度,收缩率也会有所变化。
控制吹塑收缩率的关键在于合理调整加工温度和冷却速度。
在吹塑加工过程中,温度的控制非常重要。
过高的温度会导致塑料熔融过度,收缩率增大;而过低的温度则会导致塑料不充分熔融,收缩率减小。
此外,冷却速度也是影响收缩率的重要因素。
快速的冷却速度会使塑料收缩率增大,而慢速的冷却速度则会使收缩率减小。
为了控制吹塑收缩率,可以采取以下措施:1. 合理选择塑料材料:不同种类的塑料具有不同的收缩率,根据产品要求选择合适的塑料材料。
2. 控制加工温度:根据塑料材料的熔点和加工要求,合理控制加工温度,避免温度过高或过低。
3. 控制冷却速度:通过调整冷却介质的温度和流量,控制冷却速度,避免过快或过慢的冷却。
4. 设计合理的模具结构:模具的结构对塑料制品的收缩率有一定影响。
合理设计模具,减少塑料制品的收缩率。
5. 进行试模和调试:在实际生产前,进行试模和调试工作,通过不断优化参数,控制塑料制品的收缩率。
吹塑收缩率的控制对于塑料制品的尺寸精度非常重要。
合理调整加工温度和冷却速度,选择合适的塑料材料,设计合理的模具结构,可以有效控制吹塑收缩率,提高塑料制品的质量和稳定性。
ms塑料收缩率

MS塑料收缩率1. 什么是MS塑料?MS塑料是一种特殊的塑料材料,全称为Methyl Methacrylate Styrene Copolymer,中文名为甲基丙烯酸甲酯苯乙烯共聚物。
它是一种透明、坚韧、耐候性好的塑料,具有优异的物理和化学性能。
2. 塑料收缩率的定义塑料收缩率是指塑料制品在冷却过程中产生的尺寸变化。
塑料在加热过程中会膨胀,而在冷却过程中会收缩。
塑料收缩率是衡量塑料收缩程度的指标,通常用百分比表示。
3. MS塑料的收缩率特点MS塑料具有较低的收缩率,这是由于其分子结构的特殊性所决定的。
相比其他塑料材料,MS塑料的收缩率较小,这使得它在制造精度要求较高的产品时具有优势。
4. 影响MS塑料收缩率的因素MS塑料的收缩率受多种因素的影响,包括温度、冷却速度、厚度等。
4.1 温度温度是影响MS塑料收缩率的重要因素之一。
一般来说,温度越高,塑料的收缩率就越大。
因此,在制造MS塑料制品时,需要控制好加热和冷却的温度,以使得塑料的收缩率能够满足产品的尺寸要求。
4.2 冷却速度冷却速度也是影响MS塑料收缩率的重要因素之一。
一般来说,冷却速度越快,塑料的收缩率就越大。
因此,在制造MS塑料制品时,需要控制好冷却速度,以使得塑料的收缩率能够得到控制。
4.3 厚度塑料制品的厚度也会影响其收缩率。
一般来说,厚度越大,塑料的收缩率就越小。
因此,在设计和制造MS塑料制品时,需要考虑到其厚度对收缩率的影响。
5. 如何控制MS塑料的收缩率?为了控制MS塑料的收缩率,可以采取以下措施:5.1 优化模具设计模具设计是影响塑料制品尺寸的重要因素。
通过优化模具设计,可以减小塑料制品的收缩率。
例如,可以增加冷却通道,提高冷却效果,从而减小塑料的收缩率。
5.2 控制加热和冷却温度加热和冷却温度的控制对于控制塑料收缩率至关重要。
通过合理控制加热和冷却温度,可以使得塑料的收缩率在合理范围内。
5.3 选择合适的冷却速度冷却速度对于塑料收缩率的控制也非常重要。
pc材料收缩率

pc材料收缩率PC材料收缩率。
PC材料是一种常用的工程塑料,具有优良的物理性能和化学性能,被广泛应用于电子、汽车、家电等领域。
在使用PC材料进行注塑成型时,我们需要了解其收缩率,以便在设计模具和制定工艺参数时进行合理的补偿,保证最终产品的尺寸精度。
本文将介绍PC材料的收缩率及其影响因素。
首先,我们需要了解PC材料的收缩率是什么意思。
收缩率是指塑料制品在冷却过程中由于温度变化而产生的尺寸变化比例。
一般来说,塑料制品在冷却过程中会出现收缩现象,这是由于材料分子在冷却过程中重新排列导致的。
PC材料的收缩率一般在0.5%~0.7%之间,具体数值会受到材料配方、注塑工艺、模具结构等因素的影响。
其次,影响PC材料收缩率的因素有哪些呢?首先是材料配方。
PC材料的配方中包含了树脂、增塑剂、填充剂等多种成分,不同的配方会导致不同的收缩率。
其次是注塑工艺参数。
注塑工艺中的料温、模温、压力、注射速度等参数都会对收缩率产生影响。
最后是模具结构。
模具的结构设计、冷却系统的设置都会对收缩率产生影响。
因此,在实际生产中,需要综合考虑这些因素,通过合理的工艺设计和模具调试来控制PC材料的收缩率。
针对PC材料的收缩率,我们需要采取哪些措施来进行补偿呢?首先是在模具设计阶段就考虑收缩率的影响。
通过模具结构设计、冷却系统的设置等方式来预先补偿收缩率,以减小最终产品的尺寸偏差。
其次是在制定注塑工艺参数时考虑收缩率的影响。
合理地调整料温、模温、压力等参数,以达到最终产品尺寸的精确控制。
最后是在实际生产中通过试模、调试来验证和修正工艺参数,保证产品尺寸的精度。
总之,PC材料的收缩率是影响最终产品尺寸精度的重要因素,了解其收缩率及影响因素,并采取合理的补偿措施,对于保证产品质量具有重要意义。
在实际生产中,我们需要综合考虑材料配方、工艺参数、模具结构等因素,通过科学的方法和严格的控制,来实现PC材料的收缩率精确控制,为客户提供高质量的塑料制品。
塑料模具收缩率表

塑料模具收缩率表一、引言在塑料模具的制造过程中,收缩率是一个非常重要的参数。
塑料模具收缩率表是用来指导模具制造过程中的尺寸设计和修正的参考依据。
本文将围绕塑料模具收缩率表展开讨论,介绍塑料模具收缩率的概念、影响因素以及如何使用收缩率表进行尺寸修正。
二、塑料模具收缩率的概念塑料模具收缩率是指塑料制品在冷却过程中由于温度变化而引起的尺寸变化率。
塑料模具收缩率是一个相对值,通常以百分比表示。
例如,如果一个塑料制品在冷却过程中尺寸缩小了2%,那么它的收缩率就是2%。
三、影响塑料模具收缩率的因素1. 塑料材料的种类:不同种类的塑料具有不同的收缩率。
一般来说,热塑性塑料的收缩率比热固性塑料高。
2. 温度:温度是影响塑料模具收缩率的重要因素。
一般来说,温度越高,塑料的收缩率越高。
3. 压力:在注塑过程中,注射机施加的压力也会影响塑料模具收缩率。
一般来说,施加较高的压力可以减小塑料的收缩率。
4. 模具结构:模具的结构也会对塑料模具收缩率产生影响。
例如,模具中的冷却系统设计不合理,会导致塑料冷却不均匀,进而影响塑料模具的收缩率。
四、塑料模具收缩率表的使用塑料模具收缩率表是模具制造过程中的重要参考工具。
使用收缩率表可以帮助工程师在设计模具尺寸时考虑到塑料的收缩,从而减少制品在冷却过程中的尺寸误差。
使用塑料模具收缩率表的步骤如下:1. 确定所使用的塑料材料的种类。
2. 根据塑料材料种类,找到对应的塑料模具收缩率表。
3. 根据模具尺寸和设计要求,在收缩率表中找到相应的收缩率数值。
4. 根据收缩率数值,计算修正尺寸。
修正尺寸= 原始尺寸× (1 + 收缩率)。
5. 在模具设计过程中,将修正尺寸应用于模具尺寸设计。
五、总结塑料模具收缩率是塑料模具制造中不可忽视的重要参数。
通过合理使用塑料模具收缩率表,可以减小塑料制品在冷却过程中的尺寸误差,提高模具制品的质量。
在实际应用中,工程师们应注意选择合适的塑料材料和合理的工艺参数,以保证模具制品具有准确的尺寸和优良的性能。
模具收缩率

模具收缩率模具收缩率是指熔融状态下的塑料材料在冷却固化过程中所发生缩小的比例,这种收缩是不可避免的,因为任何物质在温度变化时都会发生相应的体积变化。
在塑料制品生产过程中,模具收缩率是一个非常重要的参数,因为它会直接影响到最终成品的尺寸和质量。
若不了解材料的收缩率,容易产生尺寸偏差,甚至可能导致退货和返修等质量问题。
因此,准确控制模具收缩率是制造高品质塑件的关键,也是保证产品符合客户需求的重要保证。
塑料的收缩率受许多因素影响,如材料种类、加工参数、模型结构、冷却方式等。
以下是介绍主要影响因素:1. 材料种类不同种类的塑料材料对于温度变化的反应是不同的,因此它们的收缩率也不同。
例如,普通ABS 塑料的收缩率大约为0.4-0.8%,而尼龙材料的收缩率则为1.2-2.0%。
2. 温度和时间温度是塑料收缩率的主要影响因素之一。
在注塑加工中,模具温度或熔融物料的温度过高或过低都会导致收缩率异常。
此外,塑料材料在冷却过程中需要一定的时间来固化,因此时间也是模具收缩率的另一个因素。
3. 模具结构模具结构中的设计和改善对模具收缩率具有直接的影响。
例如,设计合理的送风系统可以控制模具温度分布,从而减少塑料的变形和收缩。
4. 模具表面在模具制造过程中,模具表面的抛光和处理也可能影响到收缩率。
如果表面不平滑,会影响塑料流动和冷却,从而影响收缩率。
在实际生产中,为了准确控制模具收缩率,需要根据材料性能和实际生产情况,进行科学合理的工艺参数设置和模具设计。
以下是一些从生产实践中总结的几个实用技巧:1. 降低温度通过降低熔融温度或模具温度,可以有效地降低收缩率。
但需要注意,温度过低会影响注塑品质。
2. 增加模压适当增加模具压力可以增强模内料流的稳定性,从而减少收缩率。
3. 设计合理的模具结构在模具设计中,可以通过改变注塑序列、优化模型设计和加强冷却系统等手段,实现收缩率的控制。
4. 加强管理加强人员操作的规范性和标准化程度,避免不必要的操作失误,从而保证注塑品质的稳定性和一致性。
ABS注塑成型收缩率的几点关系

来源于:注塑塑料网/ABS注塑成型收缩率的几点关系塑料收缩率直接关系到制品的形状和尺寸精度。
塑料制品特性、模具设计、工艺条件控制等影响成型收缩率和后收缩的各因素,对注塑制品及其稳定性影响极大[门。
目前模具尺寸的设计通常运用公差带或平均收缩率的方法计算,模具在试模后,根据试制出的制品尺寸来修正模具,然而一些高硬度。
低粗糙度模具的表面尺寸修正起来相当困难,且费工费时,有时甚至无法修正,造成巨大的损失。
所以,要得到所需尺寸的精密注塑件,同时又能尽量减少对模具的修正,就需要充分了解成型收缩率随工艺条件的变化规律,预先精确测定成型收缩率。
(丙烯膨丁二惭苯乙烯)三元共聚物(ABS)塑料综合了丙烯睛的耐化学药品性、耐油性、刚度和硬度,丁二烯的韧性和耐寒性及苯乙烯的电性能,被广泛应用于汽车、电器仪表和机械工业中,是目前通用工程塑料中应用最广泛的品种之一[z]。
国外对塑料成型收缩率的研究开始得较早,且取得了比较丰富的研究成果「3-7],国内专门从事塑料成型收缩率研究的并不多[8-11]。
因此,笔者采用xsrn n oss-so标准测定了^ss塑料在不同工艺条件下注射模塑的成型收缩率,得出了ABS塑料的成型收缩率随工艺条件的变化规律,为制订合理的工艺条件进行正确的工艺控制和模具设计从而生产出合格尺寸的制品提供了重要依据。
一、实验部分(一)主要原材料ABS:IH-100,上海高桥石化公司。
(二)主要设备干燥料斗:FNH-A型,日本日永化工株式会社;模温调节机:NT-55型,日本日永化工株式会社;注塑机:PS40SESASE型,日本日精树脂l业株式会社;模具:按ASTM D 955-89制造,长条模、圆片模,自制。
(三)测试方法试样分别为长条门27.045 mm x 10•000 mm X3.200 mm)和圆片(o101.975 mm)。
测试时运用带百分表的靠模,精度为0.of mm,测试长条形试样在平行于流动方向及圆片形试样在平行和垂直于流动方向上的尺寸变化。
- 1、下载文档前请自行甄别文档内容的完整性,平台不提供额外的编辑、内容补充、找答案等附加服务。
- 2、"仅部分预览"的文档,不可在线预览部分如存在完整性等问题,可反馈申请退款(可完整预览的文档不适用该条件!)。
- 3、如文档侵犯您的权益,请联系客服反馈,我们会尽快为您处理(人工客服工作时间:9:00-18:30)。
影响塑料制品收缩率的因素:1.成型工艺对塑料制品收缩率的影响(1)成型温度不变,注射压力增大,收缩率减小;(2)保持压力增大,收缩率减小;(3)熔体温度提高,收缩率有所降低;(4)模具温度高,收缩率增大;(5)保压时间长,收缩率减小,但浇口封闭后不影响收缩率;(6)模内冷却时间长,收缩率减小;(7)注射速度高,收缩率略有增大倾向,影响较小;(8)成型收缩大,后收缩小。
后收缩在开始两天大,一周左右稳定。
柱塞式注射机成型收缩率大。
2、塑料结构对制品收缩率的影响(1)厚壁塑件比薄壁塑件收缩率大(但大多数塑料1mm薄壁制件反而比2mm收缩率大,这是由于熔体在模腔内阻力增大的缘故);(2)塑件上带嵌件比不带嵌件的收缩率小;(3)塑件形状复杂的比形状简单的收缩率要小;(4)塑件高度方向一般比水平方向的收缩率小;(5)细长塑件在长度方向上的收缩率小;(6)塑件长度方向的尺寸比厚度方向尺寸的收缩率小;(7)内孔收缩率大,外形收缩率小。
3、模具结构对塑料制品收缩率的影响(1)浇口尺寸大,收缩率减小;(2)垂直的浇口方向收缩率减小,平行的浇口方向收缩率增大;(3)远离浇口比近浇口的收缩率小;(4)有模具限制的塑件部分的收缩率小,无限制的塑件部分的收缩率大。
4、塑料性质对制品收缩率的影响(1)结晶型塑料收缩率大于无定形塑料;(2)流动性好的塑料,成型收缩率小;(3)塑料中加入填充料,成型收缩率明显下降;(4)不同批量的相同塑料,成型收缩率也不相同。
流动取向是塑料在模塑过程中由于流动而产生的分子链取向。
拉伸取向是塑料在外力作用下分子链被强制拉伸产生的取向。
淬火是塑料成型过程中为了减小结晶度而进行的快速冷却。
异相成核,是结晶过程中结晶在相界面,或者杂质表面发生。
膨胀比:塑料在挤出过程中,挤出后材料径向膨胀,膨胀比就是挤出后材料的直径和出口孔径的比。
离模膨胀又叫出口膨胀,在挤出过程中,挤出物离开模后,其横截面尺寸因弹性回复而大于口模尺寸的现象。
收缩是塑料加工商们面临的大敌,特别是对于表面质量要求较高的大型塑料制品,收缩更是一个顽疾。
因此人们开发了各种技术,以最大限度地减少收缩,提高产品质量。
在注塑塑料部件较厚位置,如筋肋或突起处形成的收缩要比邻近位置更严重,这是由于较厚区域的冷却速度要比周围区域慢得多。
冷却速度不同导致连接面处形成凹陷,即为人们所熟悉的收缩痕。
这种缺陷严重限制了塑料产品的设计和成型,尤其是大型厚壁制品如电视机的斜面机壳和显示器外壳等。
事实上,对于日用电器这一类要求严格的产品上必须消除收缩痕,而对于玩具等一些表面质量要求不高的产品允许有收缩痕的存在。
形成收缩痕的原因可能有一个或多个,包括加工方法、部件几何形状、材料的选择以及模具设计等。
其中几何形状和材料选择通常由原材料供应商决定,且不太容易改变。
但是模具制造商方面还有很多关于模具设计的因素可能影响到收缩。
冷却流道设计、浇口类型、浇口尺寸可能产生多种效果。
例如,小浇口如管式浇口比锥形的浇口冷却得快得多。
浇口处过早冷却会减少型腔内的填充时间,从而增加收缩痕产生的几率。
对于成型工人,调整加工条件是解决收缩问题的一种方法。
填充压力和时间显著影响收缩。
部件填充后,多余的材料继续填充到型腔中补偿材料的收缩。
填充阶段太短将会导致收缩加剧,最终会产生较多或较大的收缩痕。
这种方法本身也许并不能将收缩痕减少到满意的水平,但是成型工人可以调整填充条件改善收缩痕。
还有一种方法是修改模具,有一种简单的解决方法就是修改常规的型芯孔,但是并不能指望这一方法适用于所有的树脂。
另外,气体辅助方法同样值得一试。
柱、气体和泡沫GE聚合物加工研究中心(PPDC)进行了一项12个月的研究,来评估8种不同的旨在减少收缩痕的方法。
这些技术代表了减少收缩痕的一些最新思路。
这些方法可以分为两类:一类可以称为取代材料法,另一类为去除热量法。
取代材料法是通过增加或减少可能收缩区域的材料用量来减少收缩痕。
去除热量法旨在快速地将可能产生收缩的区域的热量去除,从而减少较薄区域和较厚区域产生的冷却不均的可能性。
在本次研究中,共评估了5种取代材料法:伸出式凸柱、圆头凸柱、带弹簧凸柱、气体辅助成型和化学发泡。
三种去除热量法:铍-铜凸柱、铍-铜嵌件以及特殊设计的热活动凸柱。
评估的对象是待试部件中产生的收缩痕的数量,待试部件为带有三角形凸起的制品。
所有方法比较的标准为标准工具——不锈钢凸柱。
该测试工具能产生壁厚为2.5mm的圆盘,凸柱高为22.25mm,直径为4.5mm,壁厚为1.9mm,在底盘上有2mm的三角铁。
该研究所用的成型设备为350t的水平触动液压机,材料为日用电子产品中常用的材料,也是收缩问题严重的材料,即GE的PC/ABS、CycoloyCU6800和PPE/PS、NorylPX5622。
这两种材料的加工范围均在产品技术参数建议范围的中间点。
如果收缩痕处于最小状态,可以下调填充量来引发更多收缩痕,以方便度量并与经验方法进行比较。
尽管收缩痕通常都是通过肉眼来观察的,但是这些试验采用了一种机器对收缩痕的深度进行了定量测量。
试验内容试验的标准技术之一是伸出式凸柱,即标准凸柱伸出进入凸柱底部的壁里,从而减小壁厚并补偿凸柱中多余材料造成的效果。
试验中采用了两种伸出深度,分别为壁厚的25%和50%。
另外一个试验采用了一种圆头而不是尖头的凸柱。
这个方法不是去除凸柱区域的材料,而是使得各区域的过渡更加连贯。
还有一种方法在顶出板和凸柱之间使用弹簧。
弹簧使得部件冷却后凸柱底下的材料仍处于压力状态,以使材料获得补偿收缩的效果。
结果会受到弹簧初始压力以及弹簧“刚性”的影响,试验评估了这两种因素的影响。
使用了两种不同刚度的弹簧,对每种刚度的弹簧都施加了多种不同的初始压力。
化学发泡剂也在本次试验的评估内容里,因为化学发泡剂的优势在于不用对工具进行任何改变。
该方法的理论依据是在较厚的区域也就是最可能产生收缩的区域发泡,发泡过程会产生足够的局部压力以阻止收缩。
当然,在发泡过程中只能使用少量(0.25%)的发泡剂(SafoamRPC-40),以免形成裂纹损伤部件表面。
通过加工过的凸柱注射氮气来试验气体辅助成型,氮气在通常容易出现收缩的区域形成气泡,这样就可以去除该区域的材料用气泡里的气体来填充该区域。
为了实现热量快速转移,使用了一种由铍-铜构成的凸柱,热传导速度远远超过不锈钢材料。
该技术同样要求凸柱的后端与巨大的热池连接,使得热量能够完全从凸柱的区域去除。
该方法的另一种方式是利用标准的不锈钢凸柱但是在凸柱周围区域安装铍-铜的插件。
这就要求对模具型腔进行充分的修改,在该区域加工出一个小槽安装筋肋/凸柱结构。
筋肋/凸柱结构加工成独立的铍-铜型腔插件,安装在小槽里。
热传导速率高的插件会将凸柱区域的热量完全吸收并导入到工具中。
前两种方法采用的是被动的热去除方法,“热活动凸柱”包含了一种流体将热区域的热量带走并分散到冷却装置。
结果的比较采用PC/ABS材料时,五个试验方法产生的收缩比标准凸柱产生的收缩少。
所有的去除热量的方法效果很好,取代材料的方法中只有加载弹簧的凸柱的方法比标准凸柱效果好,而弹簧的预加载压力对性能的影响尤为突出。
气体辅助方法的结果不是决定性的:使用该种模具和材料,由于制品壁太薄,熔融-冷却速度太快,从而气体渗透很难保持一致。
发泡试验也没有决定性的影响。
部件表面明显的裂纹表明,在本方法还不能与其他方法相提并论之前,应该减少发泡剂的数量。
使用PPE/PS树脂时,加载弹簧的凸柱同样表现出色。
其他三种取代材料方法,包括伸出式凸柱法和气体辅助成型法效果也比标准凸柱的效果好。
对于去除热量法,只有铍-铜凸柱方法比标准凸柱方法的效果好。
而圆头凸柱方法对于两种材料的效果都不好。
意外的是伸出式凸柱方法对于PC/ABS材料而言效果很不好,而二十年来,伸出式凸柱一直是推荐的方法。
这些试验结果表明这些方法对于不同材料而言效果并不是相同的。
最有趣的结果还是来自加载弹簧式凸柱的方法。
对于两种材料而言,适当使用弹簧的预压力,制品收缩性均得到了50%的改善。
弹簧钢性的影响似乎不如弹簧预压力的影响大。
预压力过小,塑料熔体将凸柱的背端推得太远,导致凸柱区域太多材料滞留,从而导致收缩。
弹簧预压力过大,在熔体的压力下不会被压缩,效果和标准凸柱一样。
测量筋肋结构附近的收缩痕时,弹簧加载方法还显示了惊人的结果。
尽管该方法旨在将凸柱附近的收缩最小化,加工PPE/PS材料时,相连的筋肋结构处的收缩也得到了惊人的改善。
可能是凸柱压缩时有效地将材料填充进筋肋结构,从而减少了收缩。
不管结果如何,人们也不应就此低估气体辅助成型方法和化学发泡剂方法。
对于气体辅助成型,模具没有得到优化,有望在较大尺寸部件中起到很好的效果,因为它能覆盖的区域比加载弹簧凸柱覆盖的范围更大。
而且,如前所述,这些试验中发泡剂的配方也没有得到优化。
影响成型收缩率的因素影响成型收缩率的因素影响热塑性塑料成型收缩的因素有以下几点:一、塑料品种热塑性塑料成型过程中由于还存在结晶化形成的体积变化,内应力强,冻结在塑件产品的残余应力大,分子取向强等因素,因此与热固性塑料相比则成型收缩率较大,收缩率范围宽,方向性明显,另外成型后的收缩、退火或者调湿度处理后的收缩一般也都比热固性塑料大。
二、塑件特性成型时熔料与型腔表面接触外层立即冷却形成低密度的固态外壳。
由于塑料的导热性差,使塑件内层缓慢冷却形成收缩率大的高密度固态层。
所以壁厚、冷却慢、高密度层厚的则收缩大。
另外,有无嵌件布局、数量都直接影响料流方向,密度分布及收缩阻力大小等,所以塑件的特性对收缩大小,方向性影响极大。
三、浇口尺寸、形式、分布这些因素直接影响料流方向、密度分布、保压补缩作用及成型时间,直接进料口、浇口截面积大则收缩小但方向性大,浇口宽及长度短的则方向性小。
距进料口近的或与料流方向平行的则收缩率大。
四、成型条件模具温度高,熔料冷却慢、密度高、收缩大,尤其对结晶性料则结晶度高,体积变化左,故收缩更大。
模具温度分布与塑件内外冷却及密度均匀性也有关,直接影响到各部分收缩量大小及方向性。
另外,保压压力及时间对收缩影响较大,压力大,时间长的则收缩小但方向性大。
注射压力高,熔料粘度差小,脱模后弹性回跳大,故收缩也可适量的减小,料温高、收缩大,但方向性小。
因此在成型时调整模具温度、压力、注射速度及冷却时间等诸多因素也可适当改变塑件产品收缩情况。
注塑制品的成型是一个非常复杂的多因素耦合作用的动态加工过程,成型过程的每个因素都对制品的成型质量产生重要影响,其中成型收缩是影响制品质量的关键因素之一。
影响注塑制品收缩的因素很多,成型材料包括高聚物的分子链结构、结晶度、力学性能、流变性能等)、制品结构包括制品厚度、嵌件结构等)、工艺条件;包括注射速度、保压压力、保压时间、冷却时间等);和模具设计;包括浇口位置和数量、冷却回路分布等);等都影响其收缩行为。