低货台半挂车车架有限元分析报告
低货台半挂车车架静强度有限元分析
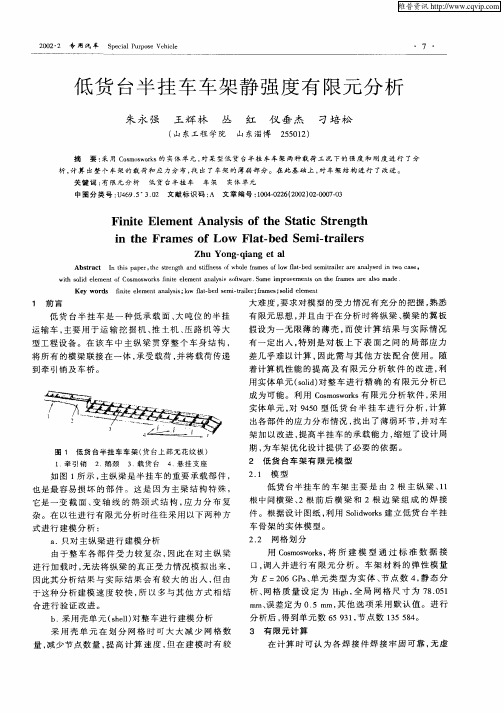
1 前 言
大难 度 , 求对 模 型 的受力 情 况 有充 分 的把握 , 悉 要 熟
有 限元 思想 , 且 由于在 分析 时 将纵 梁 、 梁 的翼 板 并 横
低 货 台半 挂 车 是 一 种 低 承 载 面 、 吨位 的 半 挂 大 运输 车 , 要 用于 运 输 挖 掘 机 、 土机 、 路 机 等 大 主 推 压
假设 为 一无 限薄 的 薄壳 , 使 计 算 结 果 与 实 际 情 况 而
有一 定 出入 。 别 是 对 板 上 下 表 面 之 间 的 局 部 应 力 特
型工 程设 备 。在 该 车 中 主 纵 梁 贯 穿 整 个 车 身 结 构 ,
将 所有 的横 梁 联 接 在一 体 , 受 载荷 , 承 并将 载 荷 传递
( 东 工 程 学 院 山 东淄 博 山 25 1 ) 5 0 2
摘 要 : 用 C s ow r s 实 体 单 元 , 某 型 低 货 台 半 挂 车 车 架 两 种 载 荷 工 况 下 的 强 度 和 刚 度 进 行 了 分 采 om s o 的 k 对
析 , 算 出整 个 车 架 的 载 荷 和 应 力 分 布 , 出 了 车 架 的 薄 弱 部 分 。在 此基 础 上 , 车 架 结 构 进 行 了改 进 。 计 找 对
到 牵 引销 及 车桥 。
差几 乎 难 以计 算 , 此 需 与 其 他 方 法 配 合 使 用 。随 因
着计 算 机性 能 的 提 高 及 有 限元 分 析 软 件 的 改 进 , 利 用 实体 单元 (o d 对 整 车 进 行 精确 的有 限元 分 析 已 sl ) i
成 为可 能 。利 用 C s ow rs 限元 分 析 软件 , 用 om s o 有 k 采
载货汽车车架拓扑优化设计及有限元分析的开题报告

载货汽车车架拓扑优化设计及有限元分析的开题报告一、研究背景随着物流业的快速发展,货车需求也不断增加。
而车辆的持久稳定性和安全性是货车发展的基础,因此在设计过程中车架的优化设计和有限元分析尤为重要。
从材料及制造工艺角度来看,目前较为成熟的结果是焊接结构,但是这种结构重量较重、成本高、制造周期长、不环保等问题日益凸显,因此要求综合考虑设计材料、拓扑结构、工艺等多方面因素,通过优化设计来提高车辆的质量、性能、经济性和可靠性。
二、研究内容1.车架结构拓扑优化设计。
在满足安全性和结构强度的前提下,结合实际的工作条件和载荷特点,通过最优化设计方法寻找最佳的车架结构形式,减轻车身质量,实现经济性和环保性。
2.车架有限元分析。
采用有限元分析方法,对拓扑优化设计后的车架进行有限元模拟分析,验证其强度和刚度的可靠性,进行有限元分析计算,为车辆的改进提供依据。
3.材料选择及加工工艺的分析。
车架材料的选择及加工工艺直接影响着车体的质量、成本、环保性等方面,以现代先进制造工艺,适当选择适合的材料,实现车体质量的低成本、高品质。
三、研究意义与价值根据研究内容,主要达到以下目的:1.提高载货汽车的安全性和可靠性,减少事故数量和损失,同时提高企业的经济效益。
2.减少我国的能源和环境负担,优化设计和改进制造工艺,避免资源的浪费和环境污染。
3.积累相关技术和经验,在相应领域做出贡献,并推动该领域技术的进步。
四、研究方法1.车架结构拓扑优化设计。
综合考虑载荷、强度、刚度等因素,采用最优化模拟设计方法,缩短设计周期,降低制造成本。
同时,为了防止优化设计过程中出现失控情况,我们建立了一套预警机制来发现和纠正问题。
2.车架有限元分析。
建立标准分析模型,通过有限元分析计算车架的应力、位移和应变,以确定车架的强度和刚度,在改进设计过程中应用结果。
3.材料选择及加工工艺的分析。
在选择材料的过程中,我们将考虑性能、成本等各方面因素。
在加工工艺的选择过程中,我们将专注于工艺稳定性、效率和成本。
半挂牵引车车架强度的有限元分析
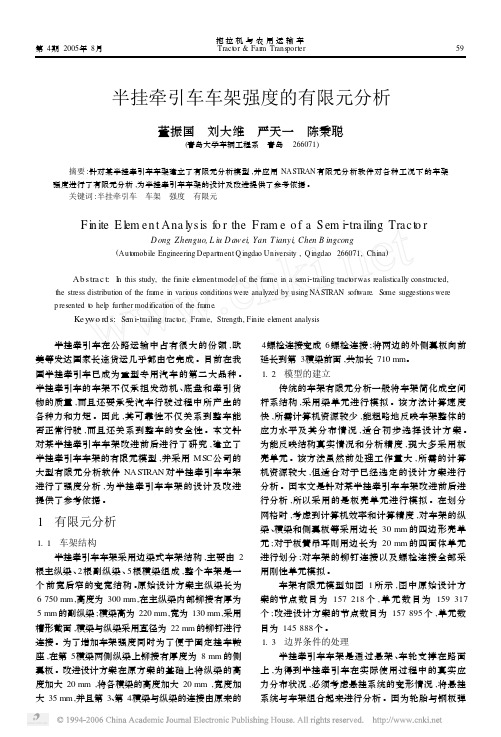
2 邓楚南 ,何天明. 半挂车车架有限元强度分析. 武汉汽车工业大学 学报 , 1997 ( 2) : 10~13
3 李德信 ,吕江涛 ,应锦春. SX360 自卸车车架异常断裂原因分析. 汽车工程 , 2002 (4) : 348~352
4 周志革 ,王金刚. 轻型货车车架纵梁异常开裂原因的分析. 汽车工 程 , 2004 ( 2) : 229~232
97
99. 5
97. 5
99
表 5 ZH1110 柴油机消声器台架试验对比数据
项 目
无消声器 原消声器 新消声器
测点 ③处总的声压级 / dB (A ) 消声器的衰减量 ΔL / dB (A )
功率损失 / kW
功率损失百分比 / %
标定工况燃油消耗率 /〔g· ( kW ·h) - 1 〕 燃油消耗率增加值 /〔g· ( kW ·h) - 1 〕 燃油消耗率增加百分数 /% 整机噪声 5 点 加 权 平 均 声压级 / dB (A )
2 载荷与工况的确定
2. 1 载荷条件的确定 车辆满载时作用于车架上的载荷包括动力总成
和驾驶室及乘员以及来自于挂车鞍座处的挂车载荷 。 在计算过程中 ,将车架质量平均分配到各单元上 ;其 中动力总成为 5 000 N、驾驶室及乘员共重 5 000 N ,这 两个力分别按照安装位置分配到相应的支承节点上 ; 挂车载荷为 227 500 N,此载荷通过挂车鞍座施加给 牵引车车架 ,应将其分解为两个集中力和力矩分别作 用到鞍座左右两孔中心处 ,如图 2所示。
由图3可知原始设计方案和改进设计方案在不同工况下主要应力集中部位都在侧翼板前部的螺栓连接处危险位置i和前钢板弹簧后吊耳固定处危险位置并且改进设计中侧翼板前部螺栓连接处的应力集中部位随着侧翼板向前的延伸而前移图3b
半挂车有限元车架挠度和模态分析
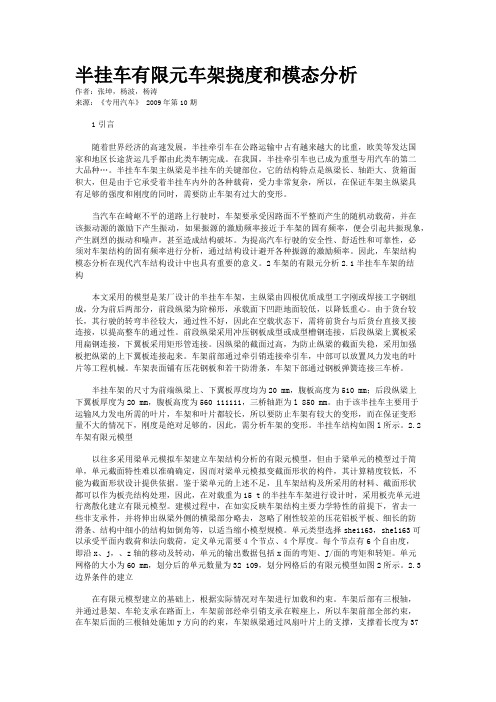
半挂车有限元车架挠度和模态分析作者:张坤,杨波,杨涛来源:《专用汽车》 2009年第10期1引言随着世界经济的高速发展,半挂牵引车在公路运输中占有越来越大的比重,欧美等发达国家和地区长途货运几乎都由此类车辆完成。
在我国,半挂牵引车也已成为重型专用汽车的第二大品种…。
半挂车车架主纵梁是半挂车的关键部位,它的结构特点是纵梁长、轴距大、货箱面积大,但是由于它承受着半挂车内外的各种载荷,受力非常复杂,所以,在保证车架主纵梁具有足够的强度和刚度的同时,需要防止车架有过大的变形。
当汽车在崎岖不平的道路上行驶时,车架要承受因路面不平整而产生的随机动载荷,并在该振动源的激励下产生振动,如果振源的激励频率接近于车架的固有频率,便会引起共振现象,产生剧烈的振动和噪声,甚至造成结构破坏。
为提高汽车行驶的安全性、舒适性和可靠性,必须对车架结构的固有频率进行分析,通过结构设计避开各种振源的激励频率。
因此,车架结构模态分析在现代汽车结构设计中也具有重要的意义。
2车架的有限元分析2.1半挂车车架的结构本文采用的模型是某厂设计的半挂车车架,主纵梁由四根优质成型工字刚或焊接工字钢组成,分为前后两部分,前段纵梁为阶梯形,承载面下凹距地面较低,以降低重心。
由于货台较长,其行驶的转弯半径较大,通过性不好,因此在空载状态下,需将前货台与后货台直接叉接连接,以提高整车的通过性。
前段纵梁采用冲压钢板成型或成型槽钢连接,后段纵梁上翼板采用扁钢连接,下翼板采用矩形管连接。
因纵梁的截面过高,为防止纵梁的截面失稳,采用加强板把纵梁的上下翼板连接起来。
车架前部通过牵引销连接牵引车,中部可以放置风力发电的叶片等工程机械。
车架表面铺有压花钢板和若干防滑条,车架下部通过钢板弹簧连接三车桥。
半挂车架的尺寸为前端纵梁上、下翼板厚度均为20 mm,腹板高度为510 mm;后段纵梁上下翼板厚度为20 mm,腹板高度为560 111111,三桥轴距为l 850 mm。
铝合金半挂车车架结构设计及有限元分析

铝合金半挂车车架结构设计及有限元分析摘要:现阶段,在各地进行物资交换的运输过程中,半挂车具有高效、灵活的优点,在运输领域发挥着重要的作用。
半挂车不仅可进行滚装运输、区间运输和甩挂运输,而且具有装卸方便,运输效率高、可靠、安全,运输成本低廉的优点。
半挂车将向节油环保、轻量化、专业化、多样化以及标准化未来的发展方向,对于不同半挂车生产厂家而言,半挂车车架在满足刚度以及强度的同时,半挂车车架的轻量化不仅会为企业自身带来更大的利润,也会提升企业自身的市场竞争力。
因此对半挂车车架进行有限元分析与轻量化问题的研究有着十分重要的意义。
关键词:铝合金;半挂车车架结构设计;有限元分析引言随着我国经济的快速发展,电商、快递业爆发式增长,货物运输量剧增,导致商用物流车需求加大,物流运输行业竞争加剧。
为控制成本,增加货运量,各物流企业对车辆的性能、油耗、载质量利用率要求越来越高,而解决上述问题的最佳方案莫过于减重。
轻量化对传统燃油汽车可显著降低油耗,对新能源汽车可增加续航能力,对于商用物流车最明显的优势是多拉货物,空载降低油耗,从而在相同运费情况下降本增效。
车架是半挂车最关键的部件,承载着整车载荷。
因此,车架轻量化要充分考虑其强度和刚度,目前钢制半挂车车架纵梁、横梁普遍采用高强钢板冲压、折弯成型,再焊接而成。
相对于低碳钢车架,高强钢车架在钢板壁厚上做了一定程度的减薄,因其材料屈服和抗拉强度高,也能满足使用要求,轻量化效果也不错。
但因钢板壁厚薄,工作环境恶劣,容易锈蚀,影响车架强度,使用寿命很短。
铝合金密度仅为钢的三分之一,其表面有一层致密的氧化膜,可隔绝空气与铝的接触,作为车架材料永不生锈。
通过合理的结构设计,将铝合金应用于该领域,实现轻、强、耐用的效果,对半挂车的轻量化很有意义。
1半挂车车架有限元分析1.1有限元法概念有限元法是用简单的问题替换复杂的问题并进行求解,具有计算精度较高的优点,可对不同复杂形状的工程问题进行科学有效的分析以及计算。
某型号矿用半挂牵引车车架的有限元分析

某型号矿用半挂牵引车车架的有限元分析杨扬(神东煤炭集团责任有限公司,榆林719315)摘要:对某型号矿用半挂牵引车车架进行了有限元分析,建立了以壳单元为基本单元并采用多点约束MPC)单元模拟铆钉传力的有限元计算模型。
通过静态分析表明了车架在满载弯曲工况与满载扭转工况下的应力及变形分布情况。
经过模态分析,获得了车架的固有频率和振形特征。
综合分析结果,对车架结构的改进提供了一些建议。
关键词:牵引车;车架;静态分析;模态中图分类号:U463.320.2文献标识码:A0引言矿用半挂牵引车车架作为非承载式车身结构的主要部件,其主要功能是固定汽车的大部分部件的相对位置,还要承载半挂牵引车车身包含的各种载荷。
汽车在行驶时,要承受来自路面的弯曲、扭转载荷以及由路面、悬架等各部件所产生的振动。
车架在设计时,不仅要保证有足够的强度和弯曲及扭转刚度,还要避免车架由外部激振频率所引发的共振导致车架使用寿命的下降。
本文建立了某型号矿用半挂牵引车车架的有限元模型,对其刚度和强度以及模态进行了有限元分析,为以后的结构改进设计提供理论依据。
1半挂牵引车车架有限元模型的建立车架有限元模型建立是采用的壳单元模型,有效避免了横梁连接点不易确定和梁单元模型纵的等一些问题,尤其是能明确展示出连接点位置的变化和加强板以及支架的一些情况,经过与实验数据的比较其计算精度也比较高。
此外,在车架有限元分析中还需要考虑汽车悬架的因素和各种约束模拟。
首先,我们应该在分析的过程中在solidworks或在UG软件里进行建立模型,可以依据其中关联的原则性简单化操作,实体模型如图1所示,接下来把模型快速导入ANSYS里,再采用shell63单元将半挂牵引车架采用整体网格分划,一定要在所有连接点和形状有明显突变的区域进行网格多次细化,在铆接处采取mpc184单元连接,这样半挂牵引车车架就形成了一个新的建模整体。
接下来利用mass21单元和combine14单元以及beam4单元对悬架和轮胎分别进行模拟。
半挂牵引车车架有限元分析的开题报告

半挂牵引车车架有限元分析的开题报告题目:半挂牵引车车架有限元分析一、选题背景和意义:半挂牵引车是一种常用的运输工具,其安全稳定性对于交通运输行业至关重要。
车架是半挂牵引车的主体结构,负责承载车身和所装载物品的重量和力量,因此其结构安全性是半挂牵引车运行安全的重要保障。
有限元分析是一种理论计算方法,可以模拟实际的结构受力情况,对于车架的结构设计和优化具有重要的意义。
二、研究内容和方法:本研究将以一辆半挂牵引车的车架为研究对象,利用有限元分析软件进行车架的有限元建模,通过加载不同的载荷,分析车架的受力情况,找出车架的薄弱环节,并提出相应的优化方案。
研究方法主要包括以下几个步骤:1.车架有限元建模采用有限元分析软件对半挂牵引车的车架进行建模,选择合适的单元类型和网格划分,构建数值分析模型。
2.载荷分析根据实际情况,确定车架承受的载荷情况,在有限元分析软件中加载各种载荷,如静载荷、动载荷等。
3.应力分析利用有限元分析软件分析车架的应力分布情况,得出车架的最大应力和应力集中点位置。
4.应变分析利用有限元分析软件分析车架的应变分布情况,得出车架的最大应变和应变集中点位置。
5.结构优化根据有限元分析结果,找出车架的薄弱环节,提出结构优化方案。
采用有限元分析软件对优化方案进行验证和优化。
三、预期结果和意义:通过本研究,可以建立半挂牵引车车架的有限元模型,分析车架在不同载荷作用下的受力情况,找到车架的薄弱环节,提出优化方案,最终得到经过优化的车架结构。
这些结果可以为半挂牵引车车架结构设计和优化提供参考,提高其安全性和稳定性,减少车辆事故的发生,为国家交通运输事业的发展做出贡献。
117468_赵坤_自卸式半挂车车架建模及有限元分析_前期报告_1428238022999

河北工业大学城市学院毕业设计(论文)前期报告学生姓名:赵坤学号: 117468 系别:机械工程系专业:车辆工程设计(论文)题目:自卸式半挂车车架建模及有限元分析设计(论文)地点:河北工业大学城市学院指导教师:王金刚职称:教授2015年 04 月 03 日一、文献综述(不少于2000字)1.课题背景随着社会的发展,自卸车在二十世纪五十年代应运而生,自卸车的问世是一场重大的技术革新,是有效节省劳动力、降低劳动强度、提高生产效率的特色产品。
自卸车又称翻斗车,是指通过液压或机械举升而自行卸载货物的车辆,是应用较多、环境适应能力强的一种专用车,可以运输绝大部分的散货,由于运输货物相对比较固定,所以具有均衡性强的特点,在粮食、采矿、建筑、矿粉运输、电厂、钢厂的许多行业都有广泛的应用[1]。
目前国内自卸车主要用于能源物流运输(煤碳、砂石、矿石等)和工地道路施工作业,其中煤碳、砂石料、铁粉运输比例占有相当大的比重。
半挂车,是车轴置于车辆重心(当车辆均匀受载时)后面,并且装有可将水平或垂直力传递到牵引车的联结装置的挂车[2]。
其设计结构合理,且外型美观,制动效果好,可靠性高。
其次,半挂车设计符合人体工程学,具有装载质量大,装载物品稳当、结实的特点。
缩短了汽车的总长,提高了整车的行驶稳定性和机动性,更重要的是它的区段运输、甩挂运输、滚装运输还能对我国物流的组织形式起到一定程度的促进作用[3]。
与汽车相比,半挂车更能够提高公路运输的综合经济效益。
运输效率可提高30-50%,油耗下降20-30%,成本降低30-40%[4]。
正因为自卸车和半挂车各自特点和优势,所以二者的结合更是绝佳的配合,节省了劳动力、提高了运输效率、降低了成本,成为汽车行业的一枝独秀。
2.项目的国内外发展情况自卸半挂车最早源于国外,日本、北美、西欧的技术比较先进,在发达国家随着基础设施的日趋完善,自卸半挂车市场品种齐全、产品技术含量高,一些新材料诸如高强度钢板、新型铝合金材料、塑料等的使用,使车身的重量变得更轻,在降低了能耗的同时,更增加了美感和抗变形能力[5]。
- 1、下载文档前请自行甄别文档内容的完整性,平台不提供额外的编辑、内容补充、找答案等附加服务。
- 2、"仅部分预览"的文档,不可在线预览部分如存在完整性等问题,可反馈申请退款(可完整预览的文档不适用该条件!)。
- 3、如文档侵犯您的权益,请联系客服反馈,我们会尽快为您处理(人工客服工作时间:9:00-18:30)。
低货台半挂车车架有限元
分析报告
设计:张平霞
张平霞
zpx164@
低货台半挂车车架有限元分析报告
摘要
低货台半挂车车架几何结构特殊,各构件应力分布也很特殊,难以用常用的计算公式加以计算,其中主纵梁是该半挂车的主要承载部件,本文采用COSMOSWORKS 有限元分析软件对某低货台半挂车车架进行两种载荷工况荷的强度、刚度分析,计算出车架的载荷和应力分布,为设计提供了准确的理论依据,同时可指导进一步改进整个车架结构,实现车身的优化设计。
一、项目介绍
低货台半挂车是一种低承载面、大吨位的半挂运输车,主要用于运输挖掘机、推土机、压路机等大型工程设备。
在该车中主纵梁贯穿整个车身结构,将所有的横梁联接成一体,共同承受载荷,并将载荷传递到牵引销及车桥,是半挂车的重要承载部件(见图1)。
也是半挂车最容易破坏的部件。
因此对其进行强度分析,并加以 改进,可大大提高半挂车的承载能力,满足用户的使用要求。
但由于该纵梁几何结构特殊,为一变截面变轴线的鹅颈式结构,并且应力分布非常复杂,所以在以往设计时多采用经验公式进行计算,或待试验后根据实验结果进行修正,不能准确地计算出各部分的受力情况,并且周期较长,给合理设计造成了一定的难度。
本文采用COSMOSWORKS 有限元分析软件,可精确地计算出各部分的应力分布情况,找出薄弱环节,为车架的优化设计提供了理论依据。
图1低货台半挂车车架(挂车载货台上部无花纹板)
1.牵引销,2.鹅颈,3.载货台,4.悬挂支座。
1 2 3 4
图2右主纵梁
二、低货台车架有限元模型的建立及网格划分
模型的建立
低货台半挂车的车架主要是由2根主纵梁、11根中间横梁、2根前后横梁和2根边梁组成的焊接件。
根据设计图纸,利用Solidworks三维模型设计软件建立低货台半挂车骨架的实体模型(如图1),图2为右主纵梁。
网格划分
打开COSMOSWORKS有限元分析软件,将所建模型通过接口调入并进行有限元分析工作。
车架的材料参数为:弹性模量E=206Gpa。
单元类型选为Solid(实体),节点数为4,分析类型为Static(静态),Quality (网格质量)为High(优),Global(全局网格尺寸)为78.051mm,Tolerance(误差)为0.5mm,其他选项采用软件的默认值,单元划分结果为:单元数65931,节点数135584,如图3所示。
计算机配置为:CPU主频600MHz,内存为256MB,计算时间为30分钟,网格划分结果如下图。
图3 车架网格图
三、有限元计算
模型假设:在计算时假设各焊接件焊接牢固可靠,无虚焊松脱现象,焊接后残余应力较小,不足以影响车架的承载能力;所载货物按要求均匀分布在挂车载货台上。
工况1:车架静载荷有限元分析
此时半挂车全部车轮均与路面接触,牵引销支撑在牵引车的牵引座上,半挂车的载货台承受56吨的静载荷,半挂车处于静止状态,所以可将车架模型约束如下:将8个悬挂支座及2个主纵梁前下翼板的下平面进行全约束(如图4所示)。
主纵梁
与横梁上平面承受均布载荷为73212N/m2(如图5所示)。
图4车架约束图
图5车架加载图
模型计算结果:
加载完毕后即可进行计算,整个计算过程历时大约5个小时。
由分析图形可知车架最大应力为1.095×108N/m2,位于主纵梁前面变截面处以及悬挂前支座处,如图6所示,车架最大位移变形为2.13mm,如图13所示。
应力最大处
图6车架侧俯视应力图
图8车架悬挂
支座局部视图
图7车架侧仰视应力图
图8车架悬挂支座局部视应力图
图9车架前视应力图
图10右纵梁局部应力分布视图
图11车架前部应力分布局部视图
位移最大处
图12车架侧视位移分布图
图14车架前视位移分布图
工况2:车架左前轮悬空时静载荷有限元分析
此时半挂车左前车轮悬空,其余车轮与路面接触,牵引销支撑在牵引车的牵引座上,半挂车的载货台承受56吨的静载荷,半挂车处于静止扭曲状态,所以可将车架模型约束如下:将6个悬挂支座及2个主纵梁前下翼板的下平面进行全约束(如
图15所示)。
主纵梁与横梁上平面承受均布载荷为73212N/m2(如图5)所示:
图15车架约束图
模型计算结果:
车架最大应力为 1.047×108N/m2,位于主纵梁前面变截面处以及悬挂前支座
处,如图25所示,车架最大位移变形为6.207mm,如图26所示。
图16车架后视应力图
图17车架前视应力图
图18车架侧俯视应力图
应力最大处
图19车架侧俯视应力图
图21车架鹅颈处应力分布局部视图
图22车架主纵梁中部应力分布局部视图
图23车架悬挂前支座处应力分布局部视图
图24车架悬挂前支座处应力分布局部视图
图25车架侧仰视应力分布图
图26车架侧仰视位移分布图
图27车架侧视位移分布图
四、结论
1.从以上分析结果可以看出,在两种工况下,纵梁在悬挂前支座部分处以及与牵引
板相靠近的纵梁前半部分的下翼板,由于纵梁截面尺寸变化较大,所以出现最大的应力,但在第二种工况时最大应力小于第一种工况的最大应力,这是因为在左前轮悬空时,承载力与第一种工况相同而约束改变的结果;对变形量而言第二种工况的最大位移大于第一种工况的最大位移,所以低货台是抗压而不抗扭,如果扭力在继续加大,破坏将会更厉害,车架结构必须改进。
2.在两种工况下,边梁前半部分出现最大的位移变形,其原因是:由于边梁只受横
梁和边梁自身的变形约束,所以导致位移约束较弱,出现最大变形,这也是与实际情况基本相吻合的,因此边梁的扭弯刚度需加强。
存在的问题及改进
该模型在建立时,为了简化模型加快计算速度,忽略了钢板弹簧和牵引销的影响,而对相关部件(悬挂支座及主纵梁前部下翼板的下平面)进行了全约束,但在半挂车的实际使用中半挂车是可以绕牵引销作前后、左右方向的旋转运动的,并且纵梁上的悬挂支座也可以
绕车轴作一定的旋转运动,
所以在实际中这两处的约
束会减弱,因此主纵梁在这
两处所承受的应力会减弱,
但边梁的变形会增大。
基于
此应在半挂车鹅颈后部加
一横向拉板,以减少边梁前
部的变形(如图28);在边
梁中部与纵梁下部之间加
斜撑以减少边梁中部的变
形,并增大整车骨架的刚
度。
图28 改进后低货台半挂车车架模型
总之,通过该软件进行分析可明显看出整车的最大变形量,以及刚度薄弱的部位,并可以找到最大应力区,验证强度是否满足要求,以加以改进。
张平霞
zpx164@。