车架有限元分析
基于ANSYS的自行车车架结构有限元分析

基于ANSYS的自行车车架结构有限元分析自行车车架是自行车的核心组成部分,它承载着骑手的重量和外界的力量,直接影响着自行车的性能和稳定性。
为了确保自行车车架的可靠性和安全性,有限元分析被广泛应用于自行车车架结构设计。
有限元分析是一种应用于工程领域的数值计算方法,通过将实际结构离散为若干个小单元,近似计算每个小单元的力学特性和应力分布,从而得到整体结构的力学性能。
在进行自行车车架的有限元分析时,需要先对车架进行几何建模。
通常可使用计算机辅助设计软件或三维建模软件进行建模,将车架几何形状、尺寸和连接方式等细节进行精确描述。
接下来,将车架模型导入ANSYS软件中进行分析。
在分析过程中,需要先对车架进行网格划分,将其离散为数个小单元,以便进行后续的力学计算。
划分网格时需要考虑车架各处应力分布的均匀性和准确性。
进行有限元分析时,需要对车架施加相应的边界条件和载荷。
边界条件包括固定支撑或约束,以模拟车架与其他部分的连接方式。
载荷可以是骑手的重力、外界风阻、不平坦路面等因素,通过合理选择载荷类型和大小来模拟实际使用条件。
在进行有限元分析时,需要定义适当的材料参数,包括车架的弹性模量、泊松比、材料屈服强度等。
这些参数直接影响着车架的刚度和性能。
通过对车架进行有限元分析,可以得到车架各处的应力、应变分布情况。
基于分析结果,可以对车架进行优化设计,以满足强度和刚度的要求。
例如,在高应力处添加加强结构或材料,以提高车架的强度和稳定性。
此外,有限元分析还可以在车架结构设计阶段进行疲劳寿命预测。
通过加载一定的循环载荷,可以计算出车架在特定循环次数下的疲劳损伤情况,从而评估车架结构的可靠性和耐久性。
总之,基于ANSYS的有限元分析在自行车车架结构设计中扮演着至关重要的角色。
它可以帮助设计师评估车架的强度、刚度和耐久性,并优化设计以提高车架的性能和稳定性。
通过有限元分析,可以减少设计过程中的试错成本,提高设计效率,为自行车车架的可靠性和安全性提供保障。
基于ANSYS的FSAE赛车车架的有限元分析
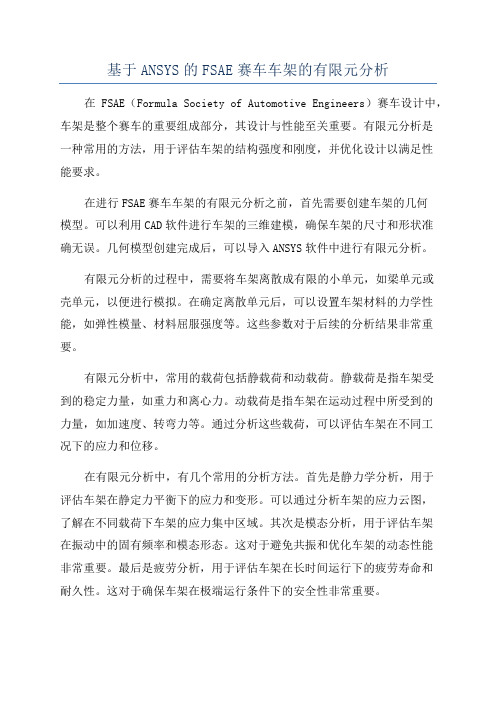
基于ANSYS的FSAE赛车车架的有限元分析在FSAE(Formula Society of Automotive Engineers)赛车设计中,车架是整个赛车的重要组成部分,其设计与性能至关重要。
有限元分析是一种常用的方法,用于评估车架的结构强度和刚度,并优化设计以满足性能要求。
在进行FSAE赛车车架的有限元分析之前,首先需要创建车架的几何模型。
可以利用CAD软件进行车架的三维建模,确保车架的尺寸和形状准确无误。
几何模型创建完成后,可以导入ANSYS软件中进行有限元分析。
有限元分析的过程中,需要将车架离散成有限的小单元,如梁单元或壳单元,以便进行模拟。
在确定离散单元后,可以设置车架材料的力学性能,如弹性模量、材料屈服强度等。
这些参数对于后续的分析结果非常重要。
有限元分析中,常用的载荷包括静载荷和动载荷。
静载荷是指车架受到的稳定力量,如重力和离心力。
动载荷是指车架在运动过程中所受到的力量,如加速度、转弯力等。
通过分析这些载荷,可以评估车架在不同工况下的应力和位移。
在有限元分析中,有几个常用的分析方法。
首先是静力学分析,用于评估车架在静定力平衡下的应力和变形。
可以通过分析车架的应力云图,了解在不同载荷下车架的应力集中区域。
其次是模态分析,用于评估车架在振动中的固有频率和模态形态。
这对于避免共振和优化车架的动态性能非常重要。
最后是疲劳分析,用于评估车架在长时间运行下的疲劳寿命和耐久性。
这对于确保车架在极端运行条件下的安全性非常重要。
通过有限元分析,可以得到车架的应力、位移、变形等结果。
根据这些结果,可以对车架进行优化设计,以提高其结构强度和刚度。
优化设计的方法包括增加材料的厚度和强度,改变车架的结构形式等。
此外,还可以通过有限元分析,评估不同配置和材料对车架性能的影响,以选择最佳的设计方案。
总之,基于ANSYS的有限元分析是FSAE赛车车架设计的重要工具。
通过分析车架的结构强度和刚度,可以优化设计,提高赛车的性能。
车架有限元分析

以ANSYS软件为分析工具对从国外引进的某重型车的车架进行了有限元分析、模态分析和以路面谱为输入的随机振动分析,通过用壳单元离散车架及MPC单元模拟铆打传力建立计算模型,研究该车架静、动态性能,了解该车架的优缺点。
车架是汽车的重要组成部分,在汽车整车设计中占据着重要位置,车架结构设计历来为广大汽车厂商所重视。
本文以某汽车公司从欧洲引进的某重型车车架为研究对象,对该车架结构的动、静态特性进行分析计算,消化、吸收欧洲的先进技术并在此基础上进行自主创新设计。
分析手段主要是通过建立正确的有限元分析模型,对车架进行典型工况的静态分析、模态分析和路面不平度引起的随机振动分析,以此了解车架的静态和动态特性,了解该车架的优越性能及其不足之处,为新车架的改型设计提供依据。
1 有限元分析模型的建立该车架为边梁式,由两根位于两边的纵梁和若干根横梁组成,用铆接或焊接方式将纵梁和横梁联接成坚固的刚性结构,纵梁上有鞍座,其结构如图1所示。
由于车架是由一系列薄壁件组成,有限元模型采用壳单元离散能详细分析车架应力集中问题,可以真实反映车架纵、横梁联接情况,是目前常采用的一种模型。
该车架是多层结构,纵梁断面为槽形,各层间用螺栓或铆钉联接,这种结构与具有连续横截面的车架不同,其力的传递是不连续的。
该车架长7m,宽约0.9 m,包括双层纵梁、横梁、外包梁、背靠梁、鞍座、飞机板、铸铁加强板、发动机安装板、三角支撑板和后轴等部分。
考虑到车架几何模型的复杂性,可在三维CAD软件UG里建立车架的面模型,导人到Hypermesh 软件中进行网格划分等前置处理,然后提交到ANSYS解算。
车架各层之间的铆钉联接,可以用Hypermesh-connectors中的bar单元来模拟铆钉联接,对应的是ANSYS的MPC单元,因车架各层间既有拉压应力,又有剪应力,故MPC的类型应选择Rigid Beam方式。
由于该车是多轴车,为超静定结构,为了得到车架结构的真实应力分布,必须考虑悬挂系统的变形情况。
车架有限元分析

1前言车架是汽车的主要部件。
深人解车架的承载特性是车架结构设计改进和优化的基础。
过去汽车设计多用样车作参考,这种方法不仅费用大,试制周于精确解。
因此,正确建立结构的力学模型,是分析期长,而且也不可能对多种方案进行评价。
现代车架设计已发展到包括有限元法、优化、动态设计等在内的计算机分析、预测和模拟阶段。
计算机技术与现代电子测试技术相结合已成为汽车车架研究中十分行之有效的方法。
实践证明,有限元法是一种有效的数值计算方法,利用有限元法计算得到的结构位移场、应力场和低阶振动频率可作为结构设计的原始判据或作为结构改进设计的基础。
2车架的静态分析力学模型的选择有限元分析的基本思想,是用一组离散化的单元组集,来代替连续体机构进行分析,这种单元组集体称之为结构的力学模型;如果已知各个单元体的力和位移(单元的刚度特性),只需根据节点的变形连续条件与节点的平衡条件,来推导集成结构的特性并研究其性能。
有限元的特点是始终以矩阵形式来作为数学表达式,便于程序设计,大量工作是由电子计算机来完成,只要计算机容量足够,单元的剖分可以是任意的,对于任何复杂的几何形状,多样化的载荷和任意的边界条件都能适应。
然而,由于有限元是一种数值分析方法,计算结果是近似解,其精度主要取决于离散化误差。
如果结构离散化恰当,单元位移函数选取合理,随着单元逐步缩小,近似解将收敛于精确解。
因此,正确建立结构的力学模型,是分析工作的第一步目前采用有限元分析模型一般有如下两种:梁单元模型和组合模型等。
梁单元模型是将车架结构简化为由一组两节点的梁单元组成的框架结构,以梁单元的截面特性来反映车架的实际结构特性。
其优点是:划分的单元数目和节点数目少,计算速度快而且模型前处理工作量不大,适合初选方案。
其缺点是:无法仔细分析车架应力集中问题,因而不能为车架纵、横梁连接方案提供实用的帮助。
组合单元模型则是既采用梁单元也采用板壳单元进行离散。
在实际工程运用中,由于车架是由一系列薄壁件组成的结构,且形状复杂,宜离散为许多板壳单元的组集,其缺点是前处理工作量大,计算时间长,然而随着计算机技术的不断发展,这个问题已得到了较好的解决,而且由于有大型有限元软件支撑,巨大的前处理工作量绝大部分可由计算机完成,也不是制约板壳元模型实际运用的困难了。
某型号矿用半挂牵引车车架的有限元分析

某型号矿用半挂牵引车车架的有限元分析杨扬(神东煤炭集团责任有限公司,榆林719315)摘要:对某型号矿用半挂牵引车车架进行了有限元分析,建立了以壳单元为基本单元并采用多点约束MPC)单元模拟铆钉传力的有限元计算模型。
通过静态分析表明了车架在满载弯曲工况与满载扭转工况下的应力及变形分布情况。
经过模态分析,获得了车架的固有频率和振形特征。
综合分析结果,对车架结构的改进提供了一些建议。
关键词:牵引车;车架;静态分析;模态中图分类号:U463.320.2文献标识码:A0引言矿用半挂牵引车车架作为非承载式车身结构的主要部件,其主要功能是固定汽车的大部分部件的相对位置,还要承载半挂牵引车车身包含的各种载荷。
汽车在行驶时,要承受来自路面的弯曲、扭转载荷以及由路面、悬架等各部件所产生的振动。
车架在设计时,不仅要保证有足够的强度和弯曲及扭转刚度,还要避免车架由外部激振频率所引发的共振导致车架使用寿命的下降。
本文建立了某型号矿用半挂牵引车车架的有限元模型,对其刚度和强度以及模态进行了有限元分析,为以后的结构改进设计提供理论依据。
1半挂牵引车车架有限元模型的建立车架有限元模型建立是采用的壳单元模型,有效避免了横梁连接点不易确定和梁单元模型纵的等一些问题,尤其是能明确展示出连接点位置的变化和加强板以及支架的一些情况,经过与实验数据的比较其计算精度也比较高。
此外,在车架有限元分析中还需要考虑汽车悬架的因素和各种约束模拟。
首先,我们应该在分析的过程中在solidworks或在UG软件里进行建立模型,可以依据其中关联的原则性简单化操作,实体模型如图1所示,接下来把模型快速导入ANSYS里,再采用shell63单元将半挂牵引车架采用整体网格分划,一定要在所有连接点和形状有明显突变的区域进行网格多次细化,在铆接处采取mpc184单元连接,这样半挂牵引车车架就形成了一个新的建模整体。
接下来利用mass21单元和combine14单元以及beam4单元对悬架和轮胎分别进行模拟。
摩托车车架的有限元分析及结构优化研究的开题报告

摩托车车架的有限元分析及结构优化研究的开题报告
一、选题背景及意义
摩托车是一种重要的交通工具,其车架是整个车辆结构中至关重要的组成部分。
车架的结构设计和优化对于摩托车稳定性、操控性、安全性等方面有着重要的影响。
有限元分析是一种常用的分析方法,能够对复杂的结构进行有效的分析和优化,因此可以用于摩托车车架的有限元分析及结构优化。
本研究旨在通过有限元分析和优化技术,提高摩托车车架的结构强度、刚度、减轻重量,达到优化设计的目的。
二、研究内容和方法
本研究的主要内容包括以下几个方面:
1. 摩托车车架有限元模型的建立
2. 车架在不同工况下的有限元分析
3. 车架结构的优化设计
4. 优化设计后的性能测试与对比分析
研究方法主要采用有限元分析软件进行模型建立和分析,并结合优化算法进行车架结构的优化设计。
三、预期成果和意义
本研究的预期成果主要包括以下几个方面:
1. 摩托车车架的有限元模型和分析结果
2. 车架结构的优化设计方案
3. 优化设计后的车架结构重量减轻和强度等性能指标的提升
该研究对于摩托车车架结构的优化设计和改进具有重要意义,能够提供相应的指导和参考,为更好地提高汽车的性能和可靠性提供有力的支持。
基于ANSYS的自行车车架结构有限元分析
基于ANSYS的自行车车架结构有限元分析自行车车架是连接自行车各个部件的重要结构,其设计优化对于提高整车性能和骑行舒适度至关重要。
有限元分析是一种常用的工程分析方法,可以用来评估自行车车架的结构强度、刚度和耐久性等特性。
在ANSYS软件中进行自行车车架有限元分析可以帮助设计师更好地理解和改进车架的设计。
首先,进行自行车车架有限元分析的第一步是建立几何模型。
可以使用ANSYS中的建模工具来创建车架的三维几何模型。
在建模过程中,需要考虑车架各个部件的几何形状、连接方式和材料参数等。
接下来,需要为车架模型分配材料属性。
车架材料的选择对于整体结构的强度和刚度具有重要影响。
可以利用ANSYS中的材料库来选择合适的材料,并为车架的不同部件分配相应的材料属性。
然后,需要进行约束和加载设置。
在真实的使用条件下,车架会受到各种力的作用,如骑行时的重力、路面不平和操控力等。
在有限元分析中,应根据实际工况和设计要求来设置适当的约束和加载。
例如,在车架的连接点设置约束,模拟骑行时的力加载。
随后,进行网格划分和网格质量检查。
网格划分是将车架模型离散化为有限元网格的过程。
在ANSYS中,可以使用自动划网工具或手动划网。
划分好网格后,还需要进行网格质量的检查和优化,以确保计算结果的准确性和可靠性。
然后,进行有限元分析求解。
有限元分析是通过将车架模型离散化为多个有限元单元,并根据材料特性、加载条件和边界条件来计算结构的应力、变形和刚度等参数。
在ANSYS中,可以选择不同的分析类型和求解器来进行分析。
根据需要,可以进行静力学、动力学、热力学和疲劳分析等。
最后,进行结果评估和优化。
通过有限元分析,可以得到车架在各个部件的应力分布图、变形图和刚度分析结果。
根据这些结果,可以评估车架的结构强度和刚度,并进行优化设计。
例如,可以优化车架的几何形状、材料选用和连接方式,以提高车架的性能。
总结起来,基于ANSYS的自行车车架结构有限元分析是一种重要的工程分析方法,可以帮助设计师评估和改进车架的设计。
汽车底盘车架设计中的有限元分析技术应用
汽车底盘车架设计中的有限元分析技术应用对于汽车制造商和设计师来说,设计一款坚固、耐用且安全的底盘车架是至关重要的。
在现代汽车设计过程中,有限元分析技术(Finite Element Analysis, FEA)被广泛应用于底盘车架设计中,以保证其结构的可靠性和性能。
本文将探讨有限元分析技术在汽车底盘车架设计中的应用,并介绍其在结构优化、材料选择和碰撞安全等方面的重要作用。
有限元分析技术是一种计算求解结构力学问题的数值分析方法,通过将底盘车架分割成有限个小单元(有限元),借助计算机进行离散化求解,从而得到车架在外力作用下的应力、应变、位移等力学响应。
这一计算模型可以准确描述车架的力学特性,并预测其结构行为。
首先,有限元分析技术在汽车底盘车架设计中的应用之一是结构优化。
通过对车架的有限元模型进行各种负载条件和约束条件的分析,设计师可以确定哪些局部区域受到最大的应力,从而确定哪些地方需要加强或重新设计。
例如,在汽车底盘车架的连接点和受力集中的区域,可以使用有限元分析来评估应力分布情况,以确保其强度和刚度满足设计要求。
此外,有限元分析还可以帮助设计师优化车架的减重设计,在保证结构安全性和刚度的前提下最大限度地降低车重,提高燃油经济性。
其次,有限元分析技术在材料选择方面也发挥着重要作用。
通过在有限元模型中引入不同材料的特性参数,设计师可以比较不同材料组合的效果,选取最佳材料以满足设计要求。
例如,比较不同材料的强度、刚度、耐腐蚀性等特性,以在保证结构安全性的前提下选择最轻最强的材料。
这种材料选择的优化可以有效地提高整个车架的性能,并且在节约成本的同时提高车辆的可靠性和可维护性。
最后,有限元分析技术在碰撞安全方面也具有重要意义。
通过对车架在碰撞事故时的有限元分析,设计师可以模拟和预测车辆受到冲击后的结构变形、应力分布和吸能能力等。
这对于汽车碰撞安全的设计和评估非常重要。
通过有限元分析的结果,设计师可以根据不同碰撞力的作用方式,合理设计车架吸能结构,以保护车辆内部乘客的安全。
某车型车架的有限元分析。开通一报告
开题报告某车型车架的有限元仿真分析一、选题的目的及研究意义车架也称大梁,车架是汽车各总成的安装基体,它将发动机、底盘和车身等总成连成一个整体,即将各总成组成为一辆完整的汽车。
同时,车架还承受汽车各总成的质量和有效载荷,并承受汽车行驶时所产生的各种力和力矩,即车架要承受各种静载荷和动载荷。
一般由两根纵梁和几根横梁组成,经由悬挂装置﹑前桥﹑后桥支承在车轮上。
具有足够的强度和刚度以承受汽车的载荷和从车轮传来的冲击。
车架在实际环境下要面对4种压力即:负载弯曲、非水平扭动、横向弯曲、水平棱形扭动。
要评价车架设计和结构的好坏,首先应该清楚了解的是车辆在行驶时车架所要承受的各种不同的力。
如果车架在某方面的韧性(stiffness)不佳,就算有再好的悬挂系统,也无法达到良好的操控表现。
汽车车架静力学分析主要包括弯曲和扭转两种工况,这是评价车架质量最重要的指标。
采用牵性力学理论及有限元原理,利用大型通用有限元分析软件ANSYS 对某车型车架在弯曲、扭转两种工况下进行力学分析,得出了在弯曲和扭转工况下某轿车车架的刚度变化。
并对不同荷载情况下的车架不同部位的应力、位移进行较为全面的数值模拟,为对车架的强度分析提供参考和依据。
由此可见车架对汽车的重要性,采用ANSYS对汽车车架进行结构优化设计,可以对结构的动态特性作出评价。
同时对车架的模态分析结果进行验证,使车架结构在原有基础上得以分析并优化,以保证车架的安全性精简性等。
二、综述与本课题相关领域的研究现状、发展趋势及研究方法等.1.研究现状:目前,国内对汽车车架的设汁与研究已经从主要依靠传统的经验分析设汁方法逐渐发展到有限元等现代设计方法,但是尚未像汽车整车和主要零部件的参数确定那样广泛应用优化设计方法。
所以汽车车架结构参数化设计与优化仍是近些年的重要研究领域。
2.发展趋势:有限元分析技术能够满足用户对车架的应力分布的需要,结构优化技术能够为车架的设计提供更合理的设计尺寸。
基于UG的某电动三轮车车架有限元分析
基于UG的某电动三轮车车架有限元分析【摘要】本研究基于UG软件对某电动三轮车车架进行有限元分析。
文章首先介绍了研究背景和研究意义,然后详细讨论了车架结构设计、有限元分析模型建立、载荷及边界条件设置、应力分析和变形分析。
通过对车架的有限元分析,得出了应力和变形的分布情况。
结论部分总结了分析结果,提出了优化建议,并展望了未来研究方向。
本研究为提高电动三轮车的结构强度和稳定性提供了理论指导,对于优化设计和改进性能具有重要意义。
【关键词】关键词:UG、电动三轮车、车架、有限元分析、结构设计、载荷、边界条件、应力分析、变形分析、优化建议、研究背景、研究意义、分析结果、展望未来。
1. 引言1.1 研究背景目前,关于电动三轮车车架的有限元分析研究还比较有限,大部分研究都是基于传统的车架设计理念,缺乏针对电动三轮车特殊结构和载荷的分析。
本研究旨在基于UG软件对某电动三轮车车架进行有限元分析,探讨其在不同载荷条件下的应力分布和变形情况,为其优化设计提供可靠的理论依据。
通过对电动三轮车车架的有限元分析,可以深入了解其受力情况,找出潜在的弱点和改进空间,提高车辆的安全性和稳定性。
也可以为今后电动三轮车车架的设计和研究提供一定的参考和借鉴。
这一研究具有重要的理论和实践意义。
1.2 研究意义电动三轮车作为新型交通工具,其车架结构设计对车辆性能和安全性有着至关重要的影响。
通过有限元分析方法对电动三轮车车架进行研究,可以为车辆设计和制造提供重要的参考和指导。
具体来说,有限元分析可以帮助分析车架在不同载荷下的受力情况,预测车架在运行中可能发生的应力和变形情况,进而优化车架结构,提高车辆的安全性和稳定性。
通过有限元分析还可以对电动三轮车车架在不同条件下的性能进行比较,找出潜在的问题并及时加以解决。
这对于提升电动三轮车整体性能、降低生产成本具有重要意义。
对电动三轮车车架进行有限元分析研究具有重要的理论和现实意义,对推动电动车行业的发展和进步具有积极作用。
- 1、下载文档前请自行甄别文档内容的完整性,平台不提供额外的编辑、内容补充、找答案等附加服务。
- 2、"仅部分预览"的文档,不可在线预览部分如存在完整性等问题,可反馈申请退款(可完整预览的文档不适用该条件!)。
- 3、如文档侵犯您的权益,请联系客服反馈,我们会尽快为您处理(人工客服工作时间:9:00-18:30)。
目录
一结构简介 (1)
二计算载荷工况 (2)
三有限元模型 (5)
四静强度分析结果 (10)
一、结构简介
本次作业以某转向架构架为几何模型,进行静强度分析,下图为本次计算针对的某型转向架几何模型,结构上由侧架、摇枕、转臂座、齿轮箱吊挂、轴箱吊挂、一系减震器座等组成。
整个计算主要分为网格划分和静强度计算两个过程。
图1 某型转向架几何模型(a)
图2 某型转向架几何模型(b)
二、计算载荷工况
根据要求,对转向架采取如下的加载方式: 1、约束
图3 约束要求
如下的局部视图中圈出处即为所加的约束之一;
图4 模型中所加约束之一
在此点出建立Z 方向的
位移约束
在此点出建立X 、Z 方
向的位移约束
在此点出建立X 、Y 、Z 方向的位
移约束
在此点出建立Y 、Z 方
向的位移约束
2、载荷
图5 受力要求
模型中加载作用力的局部视图如下(注:图中坐标系中红色为X 轴,绿色为Y 轴,蓝色为Z 轴);
图6 Z 轴正向26.2kN 的力
在此处加26.2KN 的力,力的方向为Z 轴负方向
在此处加26.2KN 的力,力的方向为Z 轴正方向
在此处加45.6KN 的力,力的方向为X 轴正方向中心销半圆内部分(Z 方向距上盖板80mm,距下盖板131mm ,X 方向距离圆心7mm )
图7 Z轴负向26.2kN的力
图8 中心处加载X轴正向45.6kN的力计算工况如下表1所示
表1 工况
工况
横向
(X向)
纵向
(Y 向)
垂向
(Z向)
1 -- --
+
整个模型由两类网格组成:构架采用壳网格单元建立模型,转臂座构件采用六面体网格建立模型;其中壳网格单元以四边形网格为主。
有限元模型重量为1422.015kg,结点总数为81382,单元总数为74991。
有限元模型如图9~12所示。
图9 壳单元模型(1/4模型)
图10 转臂座实体网格模型
图11 整体网格(a)
图12 整体网格(b)
需考虑对各个连接处的连接方式,根据工厂要求,具体连接处及连接方式可参考如下要求。
1、用Beam188单元来模拟轴向吊挂上的螺栓连接,通过Rbe3固定;
2、在图中相应位置建立一系弹簧,此处弹簧具有X、Y、Z三个方向的刚度;通过Rbe3连接到上盖板;
3、转臂座上面作用四根二系弹簧单元,通过Rbe3单元固定在转臂座上;
4、实体单元和壳单元之间采用CP_STRUC单元连接,一系弹簧和二系弹簧之间用刚性元连接,限制六个自由度。
为了保证计算精度,此处刚性元保证垂直于下盖板和转臂座底面;
5、为了便于ANSYS 计算,在图中相应位置建立质量点Mass 单元,质量点质量非常微小,只用于计算,对整体结构质量不起到影响。
具体在Hypermesh 软件中的连接方式,如下图13所示。
(a)
(b)
此处采用beam 单元模拟螺栓连接(梁截面直径d=30mm)即图中蓝色单元
此处采用rbe3单元模拟,即图中黄色单元
此处采用rbe3单元模拟,即图中黄色单元
一系弹簧采用弹簧单元模拟(此处共需建立三根弹簧单元,弹簧高度为226mm ,分别考虑X 、Y 、Z 三个方向刚度)
质量点Mass 单元
质量点Mass 单元
(c)
(d)
图13 连接处及连接方式
对于模型所附属性,其中材料属性及弹簧刚度见下表2
二系弹簧采用弹簧单元模拟(建立时需要建4根弹簧单元,以图中红色线均分成两段,每段建建立两根弹簧单元,分别考虑X 、Y 两个方向的刚度)
此处采用rbe3单元模拟,即图中黄色单元
两处的弹簧单元采用刚性元模拟连接
此处的实体网格与壳单元的连接采用刚性元模拟(单元类型选择CP_STRUC )
四、静强度分析结果(一)综合位移结果
使用ANSYS软件对模型进行静强度计算,得出:综合位移最大值13.696mm,出现在一系弹簧附近,大小符合标准,综合位移云图如下图所示;
综合位移最
大点
图14综合位移计算云图
(二)最大Von.mises应力结果
使用ANSYS软件对模型进行静强度计算,得出:最大Von.mises应力为66.843Mpa,应
力最大点出现在其中一个转臂座的底部位置,大小符合应力围,应力云图如下图所示;
Von.mises应力最大点
图15 Von.mises应力计算云图
图16 最大Von.mises应力局部视图。