铝合金压铸脱模剂之回收再利用技术探讨
再生铝合金铸造工艺中的热处理与表面改性技术

再生铝合金铸造工艺中的热处理与表面改性技术在现代工业制造中,铝合金是一种广泛应用的材料,其具有良好的强度、导电性和导热性等特性,成为许多行业的首选材料之一。
然而,在铝合金生产过程中,往往需要通过热处理和表面改性技术来提高其性能和应用领域。
本文将就再生铝合金铸造工艺中的热处理与表面改性技术进行探讨。
一、再生铝合金铸造工艺再生铝合金铸造工艺是指利用废旧铝材料进行加工,经过熔炼与铸造等过程,再生为新的铝合金制品的一种生产方式。
再生铝合金铸造工艺具有环保、节能、资源循环利用等优点,因而备受关注。
二、热处理技术热处理技术是指通过加热和冷却等过程,改变铝合金的组织结构和性能的一种方法。
再生铝合金铸造工艺中,热处理技术常用于优化铝合金的力学性能和耐腐蚀性能,提高其塑性和强度。
1. 固溶处理固溶处理是再生铝合金铸造工艺中常用的热处理技术之一。
在该工艺中,铝合金经过加热至固溶温度,使合金元素溶解在基体中,然后通过快速冷却固定组织结构,以达到强化合金的目的。
固溶处理可以显著提高铝合金的强度和硬度,同时改善其耐腐蚀性能。
在再生铝合金铸造工艺中,固溶处理可通过合理控制加热和冷却速度,实现理想的组织结构和性能。
2. 淬火处理淬火处理是再生铝合金铸造工艺中另一重要的热处理技术。
该技术通过将铝合金迅速冷却至室温,使其组织结构发生相变,从而使铝合金获得更高的强度和硬度。
淬火处理不仅可以改善铝合金的力学性能,还可以提高其耐腐蚀性能和磨损性能。
在实际应用中,再生铝合金铸造工艺中的淬火处理通常与固溶处理相结合,以达到最佳效果。
三、表面改性技术除了热处理技术外,表面改性技术也是再生铝合金铸造工艺中不可忽视的一环。
通过改变铝合金表面的物理、化学性质,可以增强其耐腐蚀性、耐磨性和装饰性,提高其使用寿命和颜值。
1. 防腐蚀处理铝合金容易受到氧化、腐蚀等影响,因此在再生铝合金铸造工艺中,防腐蚀处理是必不可少的。
常见的防腐蚀处理方法包括阳极氧化、电镀和化学处理等。
废铝合金回收处理及再利用技术

料及 其 它污染 杂 质等 。 1 2废 铝合 金 的回收处 理现 状 . 废铝 合金 ( 里主要 指 铝及 铝合 金 产 品 生产 加 工 这 过程 中所 产 出的工 艺废 料 总 称 , 不包 括 从 社会 上 回收 的各 类废 铝合 金 ) 有 合 金 化 学 成 分 相对 清楚 、 表 具 外
投入 研究 较 多 , 术 相 对 先 进 成 熟 , 先 走 出 了 一 条 技 率
经济 、 环保 、 用 的路子 , 实 与发 展 中国家 我们提 供 了学 习和借 鉴极 好范 例 。
1 3当前 企业 面 临的难题 与 研发 着力点 . 山东南 山轻 合 金 有 限公 司是 一 个 具 有 当今 世 界
先 进水 平 的现 代 化 大 型铝 合 金 轧 制 企 业 , 产 2 年 5万
铝箔 料 打 包 压 块 , 们 共 同 的特 点 是 金 属 比表 面 积 它
关 键 词 : 铝合 金 ; 废 回收 处 理 ; 利 用 ; 能 减 排 再 节
中图分类号 :76 X 5 文 献 标 识 码 : A 文 章 编 号 :6 1 6 9 ( 0 1 0 1 7 — 7 5 2 1 ) 4—0 0 — 4 0 1 0
进入 2 1世 纪 后 , 国 的铝 工 业 随 着 中 国宏 观 经 中
大、 容重 小 、 状 不 规 则 、 含有 较 多 的 油 污 、 学 涂 形 并 化
济 的快 速发 展也 得 到 了超 常规 的迅猛 发 展 ,0 9年 中 20 国的 电解 原 铝 产 量 已达 18 . 2 4 6万 吨 , 生 铝产 量 达 再 到 3 0万 吨 , 1 铝加 工 材 的产 量 已达 1 5 6 0万 吨 , 国 目 中 前 不仅 是全 球铝 的生 产 大 国 , 时 已成 为世 界 最 大 的 同 铝 产 品消 费 国。但 到 目前为 止 , 国铝加 工 材 产 品结 我 构 和布局 极 不合 理 , 型材 产 量所 占 比例 较 大 , 板 、 铝 铝 带、 箔材 所 占比例 相 对 较 低 , 因此 各 种 铝 合 金 板 、 、 带 箔材 的加 工生 产 已成 为重 点 发 展 方 向 , 其 是 各 种高 尤
废铝铸造再利用

废铝铸造再利用废铝铸造再利用废铝是指无法直接使用的废弃铝制品或铝合金制品,例如废旧铝制品、废旧铝罐、废旧铝框和铝合金废料等。
随着社会经济的快速发展和现代工业的不断进步,废铝的产量也越来越大。
然而,废铝对环境造成的污染和浪费也日益引起人们的关注。
因此,废铝铸造再利用成为了解决废铝问题的一种有效途径。
废铝铸造再利用是将废铝材料通过铸造工艺加工成新的铝制品。
废铝在经过回收和处理后,可以重新提炼成铝合金,在铸造过程中制造各种形状和尺寸的铝制品。
废铝铸造再利用具有以下几个优势。
首先,废铝铸造再利用能够有效减少资源的消耗。
铝是一种可再生的资源,通过废铝回收再利用,可以最大限度地节约和利用铝的资源。
同时,废铝的再利用也有助于减少对原生铝的需求,降低铝的生产成本。
其次,废铝铸造再利用有利于减少环境污染。
作为一种金属材料,废铝在自然界中降解的时间很长,且容易污染土壤和水源。
通过废铝铸造再利用,可以有效减少废铝对环境的污染,并减少废铝的处理和处置对环境造成的负担。
再次,废铝铸造再利用对于节约能源也有积极作用。
相比于生产原生铝,回收利用废铝能够在能源消耗方面节约约80%以上。
废铝的再利用也有助于减少能源供应的压力,促进可持续发展。
最后,废铝铸造再利用对于促进经济发展有重要意义。
废铝铸造再利用不仅可以创造就业机会,提升人们的生活水平,还能够促进相关产业链的发展,并为社会经济做出积极贡献。
然而,废铝铸造再利用面临着一些挑战。
首先,废铝回收利用的技术和设备需要不断改进和提升,以提高回收利用效率和质量。
其次,要加强废铝的回收和管理,增强全社会的环保意识和责任感。
再次,要加强政府的政策支持和资金投入,推动废铝回收再利用的发展。
针对上述挑战,我们可以采取以下措施。
一是加强技术研发和创新,提高废铝回收再利用的技术水平和效率。
二是加强废铝回收的宣传和教育,提高社会的环保意识和责任感。
三是加强产业链的建设和合作,形成废铝回收利用的闭环循环体系。
铝合金挤压模具报废后再利用的研究

尺寸进行切削,改造后模具型腔尺寸如图 4 所示。
改造前
改造后
退火温度/℃
保温时间/h
图 2 模具退火工艺图
将退火后的报废模具进行机加工操作。每片模 具的改造前后对比情况如图 3 所示。因该报废模具 的外形尺寸已满足要求,本次机加工只对模具型腔
图 3 模具改造前后对应图
· 57 ·
Copyright©博看网 . All Rights Reserved.
改造后的模具与内嵌块相配合便形成一套完整的模具。经现场生产的使用情况表明:废改模具+内嵌块的模式具有降低生
产成本、更换迅速、蚀洗方便等优点。
关键词:铝挤压;报废模具;内嵌块;再利用
中图分类号:TG375+.41
文献标识码:B
文章编号:1005-4898 (2021) 01-0056-04
doi:10.3969/j.issn.1005-4898.2021.01.14
(c) 剖面视图
新模具交付挤压生产时的硬度一般在洛氏硬度 HRC 46~50 之间,经历服役到报废后其硬度值变化 往往不会很大。机加工设备只适合在该硬度的模具 上进行小加工量的修模,并不利于大工作量的切削 加工,所以需将选取的报废模具进行退火处理,使 其硬度降到合适的加工范围,为后续的机加工做准 备。退火工艺曲线如图 2 所示。工艺流程为:迅速 升温至 860~890 ℃→860~890 ℃保温 2 h→降温至 740~760 ℃→740~760 ℃保温 4 h→炉冷至 500 ℃出 炉。
《铝加工》
2021 年第 1 期总第 258 期
深加工及其它
铝合金挤压模具报废后再利用的研究
毛一帆,赵茂密,姜小龙,赵斌斌,班米扁,零妙然
(吉利百矿集团有限公司,百色 533000)
铝合金压铸脱模剂研究报告

铝合金压铸脱模剂研究报告一、引言铝合金压铸是一种常用的铝合金成型方法,其能够快速、高效地制造各种形状复杂的铝合金零件。
在铝合金压铸过程中,脱模是一个关键步骤,直接影响到产品的质量和表面光洁度。
因此,研究并选择合适的铝合金压铸脱模剂对于提高铝合金压铸工艺的稳定性和产品质量具有重要意义。
二、铝合金压铸脱模剂的作用及分类铝合金压铸脱模剂是一种在铝合金压铸过程中涂覆在模具表面的物质,其作用是降低铝合金与模具之间的摩擦力,以便于零件的脱模。
根据脱模剂的成分和使用方式,可以将其分为涂覆型和喷雾型两类。
涂覆型脱模剂一般以溶液或涂料的形式涂覆在模具表面,而喷雾型脱模剂则通过喷雾的方式将脱模剂均匀地覆盖在模具表面。
三、铝合金压铸脱模剂的性能要求1. 良好的涂敷性:脱模剂应具有良好的涂敷性,能够均匀地涂覆在模具表面,以确保脱模效果的一致性。
2. 优异的脱模性:脱模剂应具有良好的脱模性能,能够降低铝合金与模具之间的摩擦力,使零件易于脱模。
3. 高温稳定性:铝合金压铸过程中,模具表面会受到高温的影响,脱模剂应具有较高的耐高温性能,以确保在高温条件下仍然能够保持良好的脱模效果。
4. 环境友好性:脱模剂应尽可能避免使用对环境有害的化学物质,以减少对环境的污染。
四、铝合金压铸脱模剂的研究进展1. 涂覆型脱模剂的研究进展:目前,涂覆型脱模剂主要以水基脱模剂为主,其具有环境友好、易于涂敷等优点。
同时,通过添加一定的表面活性剂和抗氧化剂,可以进一步提高涂覆型脱模剂的性能。
2. 喷雾型脱模剂的研究进展:喷雾型脱模剂能够更加均匀地覆盖在模具表面,提高脱模效果。
目前,研究人员通过改变喷雾剂的成分和喷雾方式,进一步改善喷雾型脱模剂的性能。
五、铝合金压铸脱模剂的应用案例1. 某公司针对铝合金压铸工艺的要求,选择了一种环境友好型的涂覆型脱模剂,并对其进行了实验测试。
结果表明,该脱模剂具有良好的涂敷性和脱模性能,能够有效提高铝合金压铸工艺的稳定性和产品质量。
再生铝合金铸造工艺中的科研项目与成果转化

再生铝合金铸造工艺中的科研项目与成果转化在当今工业领域,环境保护和资源可持续利用已经成为全球关注的重要问题。
再生铝合金铸造工艺作为一项新兴技术,旨在通过回收再利用废旧铝制品,实现资源的有效利用,降低环境污染。
为了促进再生铝合金铸造工艺的发展,科研项目与成果转化起到了至关重要的作用。
一、再生铝合金铸造工艺的意义再生铝合金铸造工艺是将废旧铝制品进行熔炼再生,并进行铸造成新的铝合金制品的工艺。
与传统的炼铝工艺相比,再生铝合金铸造工艺具有以下几个显著的优势:1. 节约资源:采用再生铝合金铸造工艺,可以将废旧铝制品进行回收再利用,避免了资源的浪费。
同时,与传统的炼铝工艺相比,再生铝合金铸造工艺所需的能量和原料更少,进一步节约了资源。
2. 降低污染:在再生铝合金铸造工艺中,通过废旧铝制品的熔炼再生,可以减少对环境的污染。
与传统的炼铝工艺相比,再生铝合金铸造工艺排放的废气和废水更少,减少了大气和水体的污染。
3. 提升经济效益:再生铝合金铸造工艺具有较低的生产成本,可以降低铝制品的生产成本,提升企业的竞争力。
同时,再生铝合金铸造工艺还可以创造更多的就业机会,促进经济的发展。
二、科研项目推动再生铝合金铸造工艺的发展科研项目是促进再生铝合金铸造工艺发展的重要推动力量。
通过开展科研项目,研究人员可以深入挖掘再生铝合金铸造工艺的潜力,解决其中的关键问题,提高工艺的稳定性和生产效率。
以下是一些与再生铝合金铸造工艺相关的科研项目:1. 再生铝合金铸造工艺的熔炼技术研究:通过对再生铝合金的熔炼过程进行研究,优化熔炼工艺参数,提高铝合金的质量和成品率。
2. 再生铝合金铸造工艺的模具设计研究:在再生铝合金铸造过程中,模具起到了至关重要的作用。
通过对模具的结构和材料进行研究,提高模具的耐热性和耐磨性,以提高产品的制造精度和寿命。
3. 再生铝合金铸造工艺的表面处理技术研究:通过对再生铝合金表面处理技术的研究,可以提高产品的表面质量和耐腐蚀性,提升产品在市场上的竞争力。
再生铝合金铸造工艺技术的能耗分析与优化
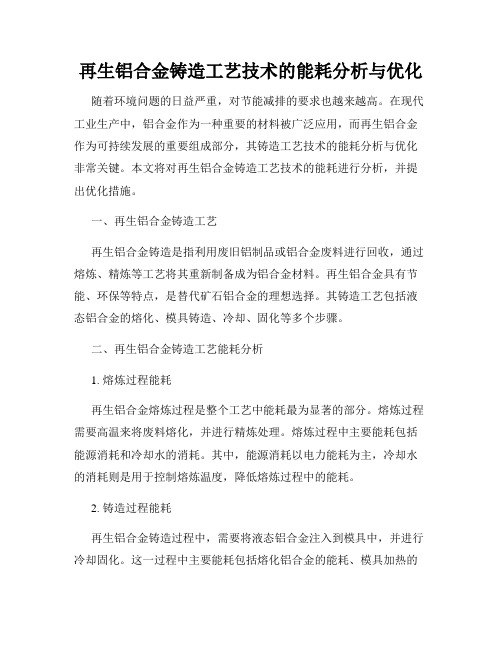
再生铝合金铸造工艺技术的能耗分析与优化随着环境问题的日益严重,对节能减排的要求也越来越高。
在现代工业生产中,铝合金作为一种重要的材料被广泛应用,而再生铝合金作为可持续发展的重要组成部分,其铸造工艺技术的能耗分析与优化非常关键。
本文将对再生铝合金铸造工艺技术的能耗进行分析,并提出优化措施。
一、再生铝合金铸造工艺再生铝合金铸造是指利用废旧铝制品或铝合金废料进行回收,通过熔炼、精炼等工艺将其重新制备成为铝合金材料。
再生铝合金具有节能、环保等特点,是替代矿石铝合金的理想选择。
其铸造工艺包括液态铝合金的熔化、模具铸造、冷却、固化等多个步骤。
二、再生铝合金铸造工艺能耗分析1. 熔炼过程能耗再生铝合金熔炼过程是整个工艺中能耗最为显著的部分。
熔炼过程需要高温来将废料熔化,并进行精炼处理。
熔炼过程中主要能耗包括能源消耗和冷却水的消耗。
其中,能源消耗以电力能耗为主,冷却水的消耗则是用于控制熔炼温度,降低熔炼过程中的能耗。
2. 铸造过程能耗再生铝合金铸造过程中,需要将液态铝合金注入到模具中,并进行冷却固化。
这一过程中主要能耗包括熔化铝合金的能耗、模具加热的能耗以及冷却水的能耗。
熔化铝合金的能耗主要与炉温、熔炼时间以及炉具的设计有关,而模具加热和冷却水的能耗则需要在工艺中进行合理的控制。
三、再生铝合金铸造工艺能耗优化措施1. 提高熔炼效率提高熔炼效率可以有效降低能耗。
可以通过改进炉具设计,提高炉体的密封性,减少能量的散失。
同时,合理选择熔炼温度和熔炼时间,避免能量浪费。
此外,选择合适的回炉比例,确保熔炼过程中的温度稳定,进一步降低能耗。
2. 优化铸造工艺针对铸造过程能耗,可以采取一些措施进行优化。
首先,在模具加热方面,可以采用预热手段,将冷模具提前加热至一定温度,减少能耗。
其次,在冷却固化方面,根据铝合金的特点,选择合适的冷却介质和冷却时间,以提高工艺的效率,减少能耗。
3. 循环利用能源再生铝合金铸造工艺中,可以通过循环利用能源来降低能耗。
废铝铸造再利用
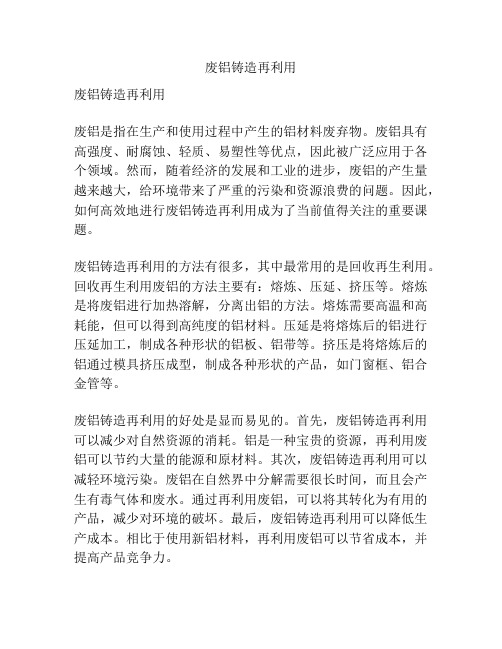
废铝铸造再利用废铝铸造再利用废铝是指在生产和使用过程中产生的铝材料废弃物。
废铝具有高强度、耐腐蚀、轻质、易塑性等优点,因此被广泛应用于各个领域。
然而,随着经济的发展和工业的进步,废铝的产生量越来越大,给环境带来了严重的污染和资源浪费的问题。
因此,如何高效地进行废铝铸造再利用成为了当前值得关注的重要课题。
废铝铸造再利用的方法有很多,其中最常用的是回收再生利用。
回收再生利用废铝的方法主要有:熔炼、压延、挤压等。
熔炼是将废铝进行加热溶解,分离出铝的方法。
熔炼需要高温和高耗能,但可以得到高纯度的铝材料。
压延是将熔炼后的铝进行压延加工,制成各种形状的铝板、铝带等。
挤压是将熔炼后的铝通过模具挤压成型,制成各种形状的产品,如门窗框、铝合金管等。
废铝铸造再利用的好处是显而易见的。
首先,废铝铸造再利用可以减少对自然资源的消耗。
铝是一种宝贵的资源,再利用废铝可以节约大量的能源和原材料。
其次,废铝铸造再利用可以减轻环境污染。
废铝在自然界中分解需要很长时间,而且会产生有毒气体和废水。
通过再利用废铝,可以将其转化为有用的产品,减少对环境的破坏。
最后,废铝铸造再利用可以降低生产成本。
相比于使用新铝材料,再利用废铝可以节省成本,并提高产品竞争力。
然而,废铝铸造再利用也面临一些挑战。
首先,废铝的回收收集工作需要投入大量的人力和物力。
目前,我国废铝的回收率还比较低,很多废铝都被随意丢弃或者乱倒。
其次,废铝铸造再利用的技术还不够成熟。
虽然有一些企业已经开始进行废铝的再利用,但是由于技术和设备的限制,废铝的再利用效率还不高。
此外,废铝铸造再利用所需的能耗也比较大,如果不能合理利用能源,对环境造成的影响可能会加剧。
针对废铝铸造再利用的问题,我们可以采取一系列的措施。
首先,加强废铝的回收管理工作,提高回收率。
政府可以出台相应的政策和法规,鼓励和支持企业和个人参与废铝回收。
其次,应加大对废铝再利用技术的研发和推广。
鼓励企业增加对废铝再利用技术的投资,提高废铝铸造再利用的效率和质量。
- 1、下载文档前请自行甄别文档内容的完整性,平台不提供额外的编辑、内容补充、找答案等附加服务。
- 2、"仅部分预览"的文档,不可在线预览部分如存在完整性等问题,可反馈申请退款(可完整预览的文档不适用该条件!)。
- 3、如文档侵犯您的权益,请联系客服反馈,我们会尽快为您处理(人工客服工作时间:9:00-18:30)。
铝合金压铸脱模剂之回收再利用技术探讨
于春生
浦东高科上海山益公司上海
铝合金压铸用的脱模剂(或称离型剂)产品,在90年代初,伴随着东洋压铸机进入中国市场,作为合同的附属合同供货给客户的,价格昂贵,当时经销品牌有积架,克鲁勃,十年后众多的进口、国产的脱模剂产品,如雨后春笋般向企业推销,你会感到有点不知所措,我们对产品的了解,都是听业务员忽悠的,在这里我们总结一下压铸的企业对脱模剂产品的质量需求:
1. 压铸的企业对脱模剂产品的质量需求的总结
1) 脱模剂效果,脱模效果好可以节省模具的顶针,滑块的维修与更换;
2) 铸件表面光亮,零件的表面缺陷更容易发现,长期储存可防止霉变;
3) 铸件气孔少,铸件产生气孔的原因较多,如果脱模剂不耐高温及附着力不足,在铝水冲型瞬间,会将“气化”的脱模剂卷入铝料内部而形成气孔;
4) 低表面张力(即脱模剂没有粘稠感);当员工喷水时,即使喷不好,脱模剂也可以浸润整个模具表面而完成脱模,对员工的喷水技术要求不高,避免了新员工制造粘模或废品的可能;
5) 脱模剂在模具表面成膜薄,低至0.2微米以下,这样可以经受住铝水的冲击,并能使模具快速降温,节约喷涂时间及成型周期,因膜厚的不同,每台机每天生产误差10%左右;
6) 模具无积碳,积碳是脱模剂“燃烧”时留下的碳与耐高温润滑剂,严重时,在模具表面形成厚0.1-0.3毫米的薄膜,影响了模具的热传递,导致零件成型周期延长或烧模频繁,如果采用洗模,省模的方法去除,都会影响工作效率及模具寿命;
7) 烟气少,无黑烟,否则车间的钢铁类结构,将受到污染或锈蚀加速,员工的健康受到伤害,特别是冬季车间的污染更严重;
8) 脱模剂成分要求无腐蚀,无毒,否则喷水时产生的蒸气或多或少会吸入员工体内或吸附在人的皮肤上,导致员工感染肺炎或皮肤红诊等疾病;
9) 脱模剂乳化液具有储存稀释,冷冻,解冻的稳定性,降低储存条件,节约电能;
10) 要求有明确的物性特征,符合环保的要求,可以通过第三方验证;
11) 脱模剂可回收性,做到不向外排放,象切削液一样使用,即节约了成本,又避免了污染河流的可能性;
12) 对后工序如电镀,阳极氧化,涂漆/喷粉等质量不受影响,这是很重要的,这是产品出货前的最后一道工艺,报废的成本较高。
2. 针对质量需求部分脱模剂制造商设计的办法
以上总结是从企业的需求出发的,这也将是考查脱模剂质量要求的重要条件,脱模剂制造商为达到或部分地满足客户要求,利用对硅油及矿物油乳化后溶于水中而制成水性脱模剂,但是此成分不能完成分模时的润滑,造成脱模困难或不能脱模,因此部分脱模剂制造商设计了以下办法,来满足脱模时的润滑:
1) 亚销酸盐与废机油复合;
2) 三乙醇铵与硼酸复合;
3) 膨润土与二氧化硅、氮化硼或二硫化钼等润滑类粉剂复合;
4) 石蜡或凡士林乳化复合;
5) 卤化物
用以上办法复合的脱模剂并不能完全满足客户的需求,或多或少地存在这样那样的问题,如发黄、发黑或影响电镀等,但能够增加脱模的润滑,而此类脱模剂是不能回收的,如回收时不能剔除,将打破了脱模剂配方的平衡,再利用时质量问题加剧。
上海山益脱模剂厂设计的耐高温矿物油,可以在5秒内耐高温650~700℃,如下图所示,解决了铸件脱模润滑问题。
图1 上海山益脱模剂厂设计的耐高温矿物油性能参数
上海山益公司生产的脱模剂产品,不添加以上耐高温润滑物料,只是将特殊的聚硅氧烷及特殊处理的矿物油乳化,按比例复配而成,利用特制的分散剂分散,回收时不会被破坏配方比例,回收方法简单而有效。
3. 脱模的危害
3.1 脱模剂对人类的危害(如图2)
图2 脱模剂对人类的危害3.2 脱模剂对模具的损害
图3 脱模剂对模具的损害
3.3 脱模剂对产品零件的损害
图四脱模剂对产品零件的损害
对图四的说明:尺寸不稳定、黑斑、后工序不良品、变形、发黑、拉伤、气孔等
现在我们来讨论一下压铸车间排出的废水的组份都有那些及存在的方式:
1. 被乳化的硅油或矿物油等乳液存在于废水中有三种型式
a. 油滴表面无乳化剂,在静置的情况下,因自身比重的关系会与水分层
b. 油滴乳化颗粒,是可以完全溶于水中,在静置的状态下,粘附的油滴会分离
c. 油滴处于半乳化状态,在静置的状态下,亦可以混入水中,不能分层。
2. 车间液压油,机油等废油流入废水,如a 的形式存在。
3. 脱模剂中溶于水的分散剂,抗氧剂,耦连剂,湿润剂,乳化剂,增滑剂等,分散于水中。
4. 极细小的油滴,尺寸小于0.5微米的油滴。
针对以上分析,如果我们采用静置的方法,可以去除较大的油滴,界面油水分离,那么细小的,半乳化状态的油并不能去除,如果我们采用气浮二次乳化法,使废水中的细小油滴聚合,就可以去除大部分油滴。
山益公司客户废水之静置方法除油试验结果:
2小时后油水界面清晰形成。
山益公司客户废水之气浮二次乳化法除油试验试验结果
30分钟后,5~12mm球状物出现
依以上实验结果,我们设计了一套废水循环系统,见下图。
图五自行设计的废水循环系统
利用连通器原理做地埋式的三个水池静置滤油,再将静置滤油后的废水吸入气浮乳化池,经30分钟通气后,流入储水池为脱模剂配水机使用,经客户三个月使用,节约脱模剂31%。
4. 总结
以上我们从压铸企业的需求出发,分析了脱模剂回收困难存在的原因——润滑成分的处理不当造成的,例如:石蜡的加入,因石蜡内含氧气,在铝水充型时即可汽化燃烧,由于模具的连续降温而不能完全燃烧,形成了碳黑润滑膜,但是石蜡含量小,是不会产生碳黑的,脱模剂制造商为了应对各种模具的脱模,只好过量使用石蜡从而污染了零件及模具。
过去,曾经有企业利用静置的方法回收,因回收废水发臭、烧手,生产的产品发黑、发黄等原因而荒废,在这里,我希望大家看了以上介绍后,能够与脱模剂制造商检讨,实现物料回收,或者直接与上海山益公司合作,为社会环保及员工健康奉献爱心。