金属压铸脱模剂原理
压铸脱模剂作用

压铸脱模剂作用压铸脱模剂是一种在压铸生产过程中使用的化学剂,其作用是帮助铸件顺利脱模,提高生产效率和产品质量。
本文将从压铸脱模剂的定义、作用原理、使用方法以及注意事项等方面进行阐述,以期对读者更加深入地了解压铸脱模剂。
定义部分。
压铸脱模剂是一种能够降低铸件与模具表面摩擦力、减少粘附和提高脱模性能的化学剂。
它通常是以液体或固体的形式存在,并且在铸件与模具接触面上形成一层薄膜,以减少接触面的摩擦力,从而使铸件能够顺利脱离模具。
作用原理部分。
压铸脱模剂的作用原理主要包括两个方面:一是降低摩擦力,二是减少粘附。
在压铸过程中,铸件与模具之间的接触面会产生摩擦力,而压铸脱模剂的存在可以有效地减少这种摩擦力,使得铸件能够更加顺利地脱模。
同时,压铸脱模剂还能够降低铸件与模具表面的粘附力,减少铸件粘附在模具上的现象,从而进一步提高脱模性能。
接下来,使用方法部分。
使用压铸脱模剂的方法一般有两种:涂覆法和喷雾法。
涂覆法是将压铸脱模剂均匀地涂覆在模具表面,可以使用刷子或喷枪进行涂覆。
喷雾法则是将压铸脱模剂以喷雾的形式均匀地喷洒在模具表面。
在使用压铸脱模剂之前,需要先将模具表面清洁干净,以确保脱模效果的良好。
另外,需要根据具体的生产情况和要求,选择适合的压铸脱模剂,并按照使用说明进行正确的使用。
注意事项部分。
在使用压铸脱模剂时,需要注意以下几个方面:一是要选择适合的脱模剂。
不同的铸件材料和模具材料对脱模剂的要求不同,需要根据具体情况选择适合的脱模剂。
二是要控制使用量。
使用过量的脱模剂会导致脱模剂在铸件表面残留过多,影响产品的质量。
三是要保持模具表面的清洁。
模具表面的污垢会影响脱模剂的附着性和脱模效果,因此需要定期清洁模具表面。
四是要注意脱模剂的保存。
脱模剂应存放在阴凉干燥的地方,避免阳光直射和高温环境,以免影响其性能和使用寿命。
压铸脱模剂在压铸生产中起着重要的作用。
通过降低摩擦力和减少粘附,它能够帮助铸件顺利脱离模具,提高生产效率和产品质量。
脱模剂的研究及应用
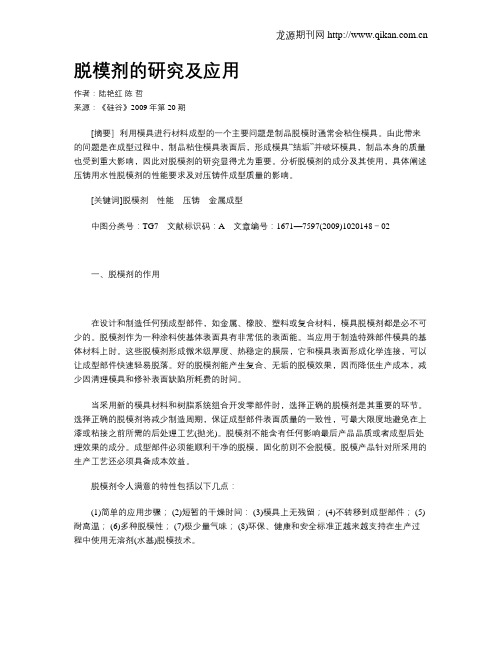
脱模剂的研究及应用作者:陆艳红陈哲来源:《硅谷》2009年第20期[摘要]利用模具进行材料成型的一个主要问题是制品脱模时通常会粘住模具。
由此带来的问题是在成型过程中,制品粘住模具表面后,形成模具“结垢”并破坏模具,制品本身的质量也受到重大影响,因此对脱模剂的研究显得尤为重要。
分析脱模剂的成分及其使用,具体阐述压铸用水性脱模剂的性能要求及对压铸件成型质量的影响。
[关键词]脱模剂性能压铸金属成型中图分类号:TG7文献标识码:A文章编号:1671—7597(2009)1020148-02一、脱模剂的作用在设计和制造任何预成型部件,如金属、橡胶、塑料或复合材料,模具脱模剂都是必不可少的。
脱模剂作为一种涂料使基体表面具有非常低的表面能。
当应用于制造特殊部件模具的基体材料上时。
这些脱模剂形成微米级厚度、热稳定的膜层,它和模具表面形成化学连接,可以让成型部件快速轻易脱落。
好的脱模剂能产生复合、无垢的脱模效果,因而降低生产成本,减少因清理模具和修补表面缺陷所耗费的时间。
当采用新的模具材料和树脂系统组合开发零部件时,选择正确的脱模剂是其重要的环节。
选择正确的脱模剂将减少制造周期,保证成型部件表面质量的一致性,可最大限度地避免在上漆或粘接之前所需的后处理工艺(抛光)。
脱模剂不能含有任何影响最后产品品质或者成型后处理效果的成分。
成型部件必须能顺利干净的脱模,固化前则不会脱模。
脱模产品针对所采用的生产工艺还必须具备成本效益。
脱模剂令人满意的特性包括以下几点:(1)简单的应用步骤; (2)短暂的干燥时间: (3)模具上无残留; (4)不转移到成型部件; (5)耐高温; (6)多种脱模性; (7)极少量气味; (8)环保、健康和安全标准正越来越支持在生产过程中使用无溶剂(水基)脱模技术。
二、脱模剂的分类传统的脱模剂一般为外用型,即涂敷在模腔表面,习惯上也有称作隔离剂的。
脱模剂涂在型腔表面,目的是方便脱模,外用脱模剂可以分为无机、有机及聚合物三类。
脱模剂的应用原理
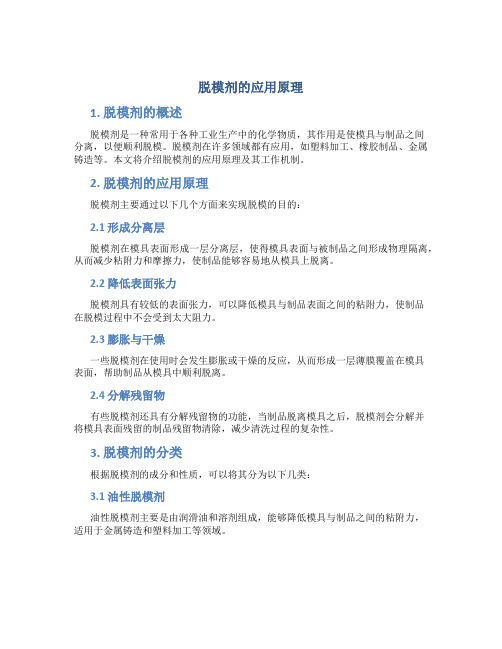
脱模剂的应用原理1. 脱模剂的概述脱模剂是一种常用于各种工业生产中的化学物质,其作用是使模具与制品之间分离,以便顺利脱模。
脱模剂在许多领域都有应用,如塑料加工、橡胶制品、金属铸造等。
本文将介绍脱模剂的应用原理及其工作机制。
2. 脱模剂的应用原理脱模剂主要通过以下几个方面来实现脱模的目的:2.1 形成分离层脱模剂在模具表面形成一层分离层,使得模具表面与被制品之间形成物理隔离,从而减少粘附力和摩擦力,使制品能够容易地从模具上脱离。
2.2 降低表面张力脱模剂具有较低的表面张力,可以降低模具与制品表面之间的粘附力,使制品在脱模过程中不会受到太大阻力。
2.3 膨胀与干燥一些脱模剂在使用时会发生膨胀或干燥的反应,从而形成一层薄膜覆盖在模具表面,帮助制品从模具中顺利脱离。
2.4 分解残留物有些脱模剂还具有分解残留物的功能,当制品脱离模具之后,脱模剂会分解并将模具表面残留的制品残留物清除,减少清洗过程的复杂性。
3. 脱模剂的分类根据脱模剂的成分和性质,可以将其分为以下几类:3.1 油性脱模剂油性脱模剂主要是由润滑油和溶剂组成,能够降低模具与制品之间的粘附力,适用于金属铸造和塑料加工等领域。
3.2 水性脱模剂水性脱模剂主要是由水和一些表面活性剂组成,能够在模具表面形成分离层,水性脱模剂具有绿色环保的特点,适用于食品包装和医药领域。
3.3 硅油脱模剂硅油脱模剂主要由聚硅氧烷组成,具有很高的耐温性和耐化学性,在高温环境下也能保持较好的脱模效果,适用于高温塑料模具和橡胶制品。
3.4 焊接脱模剂焊接脱模剂主要用于焊接过程中,能够在焊接后顺利脱模,并且对焊接接头不会产生不良影响。
4. 脱模剂的选择与使用在选择和使用脱模剂时,需要考虑以下几个因素:4.1 制品材料不同的制品材料对脱模剂有不同的要求,例如一些塑料对油性脱模剂更为适用,而一些金属铸件则需要使用耐高温的硅油脱模剂。
4.2 加工工艺加工工艺的不同也会影响脱模剂的选择,例如在高温塑料模具的注塑过程中,需要使用耐高温的硅油脱模剂。
铝合金脱模剂
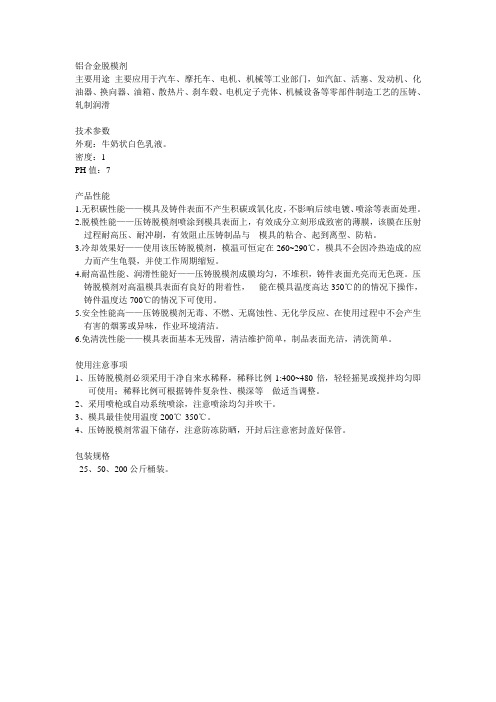
铝合金脱模剂
主要用途主要应用于汽车、摩托车、电机、机械等工业部门,如汽缸、活塞、发动机、化油器、换向器、油箱、散热片、刹车毂、电机定子壳体、机械设备等零部件制造工艺的压铸、轧制润滑
技术参数
外观:牛奶状白色乳液。
密度:1
PH值:7
产品性能
1.无积碳性能——模具及铸件表面不产生积碳或氧化皮,不影响后续电镀、喷涂等表面处理。
2.脱模性能——压铸脱模剂喷涂到模具表面上,有效成分立刻形成致密的薄膜,该膜在压射过程耐高压、耐冲刷,有效阻止压铸制品与模具的粘合、起到离型、防粘。
3.冷却效果好——使用该压铸脱模剂,模温可恒定在260~290℃,模具不会因冷热造成的应力而产生龟裂,并使工作周期缩短。
4.耐高温性能、润滑性能好——压铸脱模剂成膜均匀,不堆积,铸件表面光亮而无色斑。
压铸脱模剂对高温模具表面有良好的附着性,能在模具温度高达350℃的的情况下操作,铸件温度达700℃的情况下可使用。
5.安全性能高——压铸脱模剂无毒、不燃、无腐蚀性、无化学反应、在使用过程中不会产生有害的烟雾或异味,作业环境清洁。
6.免清洗性能——模具表面基本无残留,清洁维护简单,制品表面光洁,清洗简单。
使用注意事项
1、压铸脱模剂必须采用干净自来水稀释,稀释比例1:400~480倍,轻轻摇晃或搅拌均匀即
可使用;稀释比例可根据铸件复杂性、模深等做适当调整。
2、采用喷枪或自动系统喷涂,注意喷涂均匀并吹干。
3、模具最佳使用温度200℃-350℃。
4、压铸脱模剂常温下储存,注意防冻防晒,开封后注意密封盖好保管。
包装规格
25、50、200公斤桶装。
铝合金高压铸造介绍
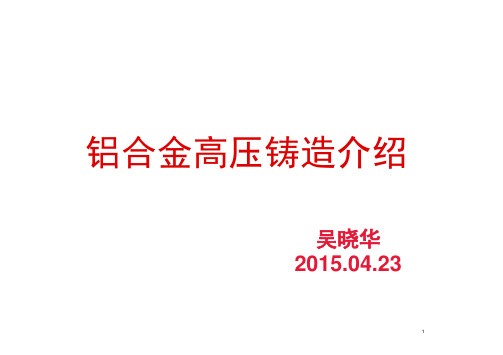
压铸模具和方案
三、产品开发—分型方案
2、产品滑块方案
Slide 2
Slide 1
Slide 3
Slide 4
Slide 5
Slide 7
Slide 6 模具共有7个滑块
22
压铸模具和方案
三、产品开发—顶出方案
1、产品顶针位置
EP Φ8 (Φ10台座)(×7)
23
压铸模具和方案
三、产品开发—刻字方案
成品率 充填率 充填时间(理论计算) 充填时间(经验值计算) 高速速度 高速区间+10mm 浇口截面积 冲头浇口截面积比
1578g 1509g 550g 3637g
43% 38.9%(20%-48%)
0.076s
0.06s(选用) 2.3m/s 146.6mm 470.7mm2
13.5 :1
高速速度 2.0m/s 2.5m/s 3.0m/s 3.5m/s 浇口速度 27m/s 33.75m/s 40.5m/s 47.25m/s
三、产品开发—产品铸造难点
②产品表面气孔要求
A区域
C区域
B区域
如图所示,产品A 区域表面气孔要求 为0.8mm,较为严 格,浇口排布是应 考虑此部位优先充 填
具体表面气孔标准客户另行提 供,双方将再次进行技术检讨
14
压铸模具和方案
三、产品开发—产品铸造难点 ③产品变型情况
素材图尺寸 要求
此部位 尺寸要求
5・限位柱固定 板
10
压铸模具和方案
二、产品介绍
汤饼
分流子 (湯道)
产品部
真空浇道
浇道部
推出顶针痕
盗肉
浇口 浇口
真空浇道头
金属压铸耐高温脱模剂技术
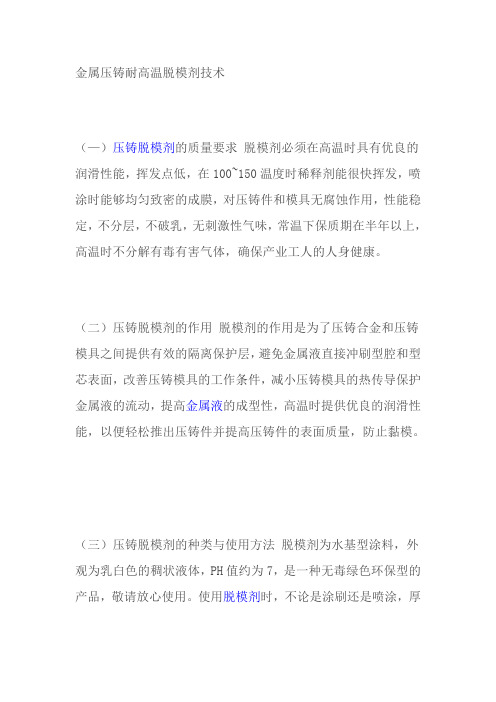
金属压铸耐高温脱模剂技术(—)压铸脱模剂的质量要求脱模剂必须在高温时具有优良的润滑性能,挥发点低,在100~150温度时稀释剂能很快挥发,喷涂时能够均匀致密的成膜,对压铸件和模具无腐蚀作用,性能稳定,不分层,不破乳,无刺激性气味,常温下保质期在半年以上,高温时不分解有毒有害气体,确保产业工人的人身健康。
(二)压铸脱模剂的作用脱模剂的作用是为了压铸合金和压铸模具之间提供有效的隔离保护层,避免金属液直接冲刷型腔和型芯表面,改善压铸模具的工作条件,减小压铸模具的热传导保护金属液的流动,提高金属液的成型性,高温时提供优良的润滑性能,以便轻松推出压铸件并提高压铸件的表面质量,防止黏模。
(三)压铸脱模剂的种类与使用方法脱模剂为水基型涂料,外观为乳白色的稠状液体,PH值约为7,是一种无毒绿色环保型的产品,敬请放心使用。
使用脱模剂时,不论是涂刷还是喷涂,厚薄应均匀,且不宜太厚,涂后应待涂料中的水份挥发后才能合模浇注,以避免成型困难。
选用脱模剂时应注意使用的型号: (1)对一般的产品,外表因为还有经过喷砂,车床,铣床等金加工,最后表面还有喷油漆,所以对压铸件的外观要求并不是很高。
我们建议您选用价格便宜A型脱模剂。
(2)对比较大的压铸件,对脱模剂的要求它需要更高的耐高温性,更高的隔离性,外表也需更好看,我们建议您选用脱模效果更佳的B型压铸脱模剂。
(3)对大型,外表要求更高,结构复杂的压铸件,我们建议您选用C型压铸脱模剂。
BD-257系列具有360度以上的耐高温性,优质的脱模性,并且克服一些国产高档脱模剂虽然脱模效果较好,却在后续加工中喷不上油漆或油漆表面起壳的缺点,用脱模剂压铸件表面易清洗,不流痕迹,可以轻松上油漆。
(4)使用时,如果是较难脱模的产品,一般加水为脱模剂的100倍,如果是小的产品容易脱模的产品最大可以加水150倍,具体到某一个产品请各用户酌情配比。
铝合金压铸,包括铝、镁、锌合金系列压铸产品,广泛应用于汽车、电信、摩托车、家电等行业。
脱模剂的介绍及应用原理

脱模剂的介绍及应用原理一、脱模剂的定义脱模剂是一种在模具表面形成一层分离膜,以减少模具与成型物表面之间的摩擦力,使成品容易脱离模具的材料。
脱模剂能够改善成品表面质量,提高生产效率,减少模具磨损,是现代工业生产不可或缺的重要助剂。
二、脱模剂的应用原理1. 降低摩擦力脱模剂在模具与成型物的接触面形成一层薄膜,减少模具与成型物之间的黏附力和摩擦力,使成品容易脱离模具。
这种分离膜不仅能够降低摩擦力,还能够保护模具表面不受损伤,延长模具使用寿命。
2. 改善成品表面质量脱模剂能够使成品表面更加光滑,减少模具表面与成型物之间的接触,避免成品表面出现划痕、刮痕等缺陷。
3. 提高生产效率使用脱模剂可以使成品容易从模具中脱离,减少成品脱模时间,提高生产效率。
同时,脱模剂还能够减少模具的清洗次数,节省时间和成本。
4. 减少模具磨损脱模剂可以降低模具与成品的摩擦力,减少模具磨损,延长模具的使用寿命。
这对于大批量生产的企业来说,可以减少模具更换的频率,节约成本。
三、脱模剂的分类脱模剂根据其成分和用途的不同,可以分为几种不同的类型:1. 润滑脱模剂润滑脱模剂主要是由润滑剂和添加剂组成,可以减少模具与成品之间的摩擦力,提高成品的脱模性能。
这种脱模剂常用于金属、塑料等成型工艺中。
2. 分离脱模剂分离脱模剂主要是通过在模具表面形成一层薄膜来实现成品与模具的分离。
这种脱模剂常用于注塑、压铸等成型工艺中。
3. 抗粘脱模剂抗粘脱模剂主要是通过添加一些抗粘剂和消泡剂等成分来实现对成品的保护和脱离。
这种脱模剂常用于橡胶等粘性物料的成型工艺中。
4. 防锈脱模剂防锈脱模剂主要是通过在模具表面形成一层防锈膜,防止模具受到潮湿空气的侵蚀。
这种脱模剂常用于金属模具的防锈和保养。
四、脱模剂的应用领域脱模剂广泛应用于以下几个领域:1. 塑料制品成型在塑料注塑、挤出、吹塑等成型过程中,使用脱模剂能够减少模具与塑料的粘附,帮助成品顺利脱模。
2. 金属制品成型在金属压铸、锻造、冲压等成型过程中,脱模剂可以降低模具与金属的摩擦,减少成品与模具的接触,有利于成品从模具中脱离。
铝合金压铸脱模剂研究报告

铝合金压铸脱模剂研究报告一、引言铝合金压铸是一种常用的铝合金成型方法,其能够快速、高效地制造各种形状复杂的铝合金零件。
在铝合金压铸过程中,脱模是一个关键步骤,直接影响到产品的质量和表面光洁度。
因此,研究并选择合适的铝合金压铸脱模剂对于提高铝合金压铸工艺的稳定性和产品质量具有重要意义。
二、铝合金压铸脱模剂的作用及分类铝合金压铸脱模剂是一种在铝合金压铸过程中涂覆在模具表面的物质,其作用是降低铝合金与模具之间的摩擦力,以便于零件的脱模。
根据脱模剂的成分和使用方式,可以将其分为涂覆型和喷雾型两类。
涂覆型脱模剂一般以溶液或涂料的形式涂覆在模具表面,而喷雾型脱模剂则通过喷雾的方式将脱模剂均匀地覆盖在模具表面。
三、铝合金压铸脱模剂的性能要求1. 良好的涂敷性:脱模剂应具有良好的涂敷性,能够均匀地涂覆在模具表面,以确保脱模效果的一致性。
2. 优异的脱模性:脱模剂应具有良好的脱模性能,能够降低铝合金与模具之间的摩擦力,使零件易于脱模。
3. 高温稳定性:铝合金压铸过程中,模具表面会受到高温的影响,脱模剂应具有较高的耐高温性能,以确保在高温条件下仍然能够保持良好的脱模效果。
4. 环境友好性:脱模剂应尽可能避免使用对环境有害的化学物质,以减少对环境的污染。
四、铝合金压铸脱模剂的研究进展1. 涂覆型脱模剂的研究进展:目前,涂覆型脱模剂主要以水基脱模剂为主,其具有环境友好、易于涂敷等优点。
同时,通过添加一定的表面活性剂和抗氧化剂,可以进一步提高涂覆型脱模剂的性能。
2. 喷雾型脱模剂的研究进展:喷雾型脱模剂能够更加均匀地覆盖在模具表面,提高脱模效果。
目前,研究人员通过改变喷雾剂的成分和喷雾方式,进一步改善喷雾型脱模剂的性能。
五、铝合金压铸脱模剂的应用案例1. 某公司针对铝合金压铸工艺的要求,选择了一种环境友好型的涂覆型脱模剂,并对其进行了实验测试。
结果表明,该脱模剂具有良好的涂敷性和脱模性能,能够有效提高铝合金压铸工艺的稳定性和产品质量。
- 1、下载文档前请自行甄别文档内容的完整性,平台不提供额外的编辑、内容补充、找答案等附加服务。
- 2、"仅部分预览"的文档,不可在线预览部分如存在完整性等问题,可反馈申请退款(可完整预览的文档不适用该条件!)。
- 3、如文档侵犯您的权益,请联系客服反馈,我们会尽快为您处理(人工客服工作时间:9:00-18:30)。
金属压铸脱模剂原理讲解了压铸脱模的原理以及压铸脱模剂中不同的蜡添加剂种类的功能。
金属压铸添加剂(金属压铸脱模剂)中蜡的不同功能
1、高熔融粘度产生脱模作用
由于蜡的高熔融粘附性,模具金属表面的蜡添加剂流速高于流动的液态氧化铝。
该流体流动界面层的稠度与离型膜的粘度成正比。
常用高密度聚乙烯蜡或改性聚丙烯蜡。
高密度聚乙烯蜡
改性聚丙烯蜡
推荐型号
Ultralube产品蜡的类型熔点粘度
E-1058 高密度聚乙烯120-125°C 1100 mPas/140°C
E-846A 高密度聚乙烯138°C 1100 mPas (140°C)
E-912 高密度聚乙烯146°C >8000 mPas (140°C)
E-660 改性聚丙烯150°C 800 mPas (170°C)
E-XP08060604 改性聚丙烯156°C 1100 mPas(170°C)
2、化学结构产生的脱模/润滑作用
一般用改性聚酯或聚酰胺蜡。
改性聚酯和金属表面相互作用
改性聚酯蜡的极性酯基团和线性分子,使得它与金属表面有很好的附着力和亲和力。
这种附着力在金属加工时提供了离型/润滑效果。
推荐型号:D-840
聚酰胺和金属表面相互作用
由于氮的自由电子与模具金属表面电子相互作用,所以这种酰胺蜡的分子结构让它与金属表面有很好的附着力,这种附着力在金属加工时提供了离型/润滑效果。
推荐型号:E-7098
不同蜡种类离型效果对比
Ultralube® 产品蜡的类型离型效果
E-7098 改性聚酯
D-840 聚酰胺
对金属表面的高亲和性产生离型效果
D-8400 改性聚酯/ 聚酰胺
E-912 高密度聚乙烯
E-1058 高密度聚乙烯
高熔融粘度产生离型效果
E-846A 高密度聚乙烯
E-660 改性聚丙烯
E-XP08060604 改性聚丙烯高熔融粘度产生离型效果+ 对金属表面的高亲和性
SE-112 改性聚二甲基硅氧烷可涂布离型剂
金属脱模剂中高密度聚乙烯与初级聚乙烯的性能对比
型号蜡的类型粘度固含熔点
Ultralube® E-912 高密度聚乙烯>8000 mPas 140°C 35 146°C PE 02 初级聚乙烯无数据40 95°C
残留率[%]
型号
200°C 300°C 400°C 500°C 600°C
Ultralube® 912 98 96 83 6 3,8
PE02 98 97 86 3 2,8
两种蜡都没有“莱顿弗罗斯特”现象
型号蜡的类型粘度固含熔点pH值离子类型Ultralube® E-912 高密度聚乙烯>8000 mPas 140°C 35 146°C 9,5 非离子
PE 02 初级聚乙烯无数据40 95°C 11 阴离子
PE 03 初级聚乙烯无数据40 95°C 9 阴离子/非离子
型号蜡的类型固含熔点pH值离子类型残留情况
PE 34 初级聚乙烯+ 添加剂38 95°C 9 阴离子/非离子
T XP -19021096 高密度聚乙烯+ 添加剂37 146°C/70°C 9 阴离子/非离子添加额外的助剂以避免模具中的残留物T XP-19021097 高密度聚乙烯+ 添加剂38 146°C 9 阴离子/非离子与PE34比较
金属脱模剂中不同蜡种类使用后的残留物与稳定性对比
模具上的残留问题
在压铸过程中我们发现模具中不同空间位置的温度不同。
热的铝被压进模具并且在里面冷却,导致模具不均匀的温度分布。
在模具中温度低的部分会时常出现蜡堆积后产生的残渣。
这些残渣会带来铸造过程中模具最大压力的降低和尺寸偏差。
冷区域里温度不足以燃烧掉所有的蜡,导致蜡容易堆积需要用机械外力清除。
尽管聚硅氧烷在模具的高温部位形成的是玻璃状残余物。
这些残留物也必须通过机械方法除去(例如用干冰清洗)
压铸工艺的温度
合金压铸温度[°C] 模具温度[°C]
锌合金390-410 80-170
镁合金650-680 190-250
铝合金650-720 150-340
铜合金900-960 460-600
案例:液体铝压铸过程的温度区间与残留物
残留率[%] 残留物型号蜡的种类
200°C300°C400°C500°C 600°C 80% Ultralube® E-7098 改性聚酯99,8 99 6 1 0,6 382°C Ultralube® D-840 聚酰胺100 99,8 52 1,5 0,5 382°C Ultralube® D-8400 改性聚酯/ 聚酰胺100 99,5 22 4 1,1 355°C Ultralube E-1058 高密度聚乙烯100 98 54 2 0,9 372°C Ultralube® E-846A 高密度聚乙烯100 98 58 8 1,2 355°C Ultralube® E-660 改性聚丙烯99 96 50 1 0,3 352°C Ultralube® E-XP08060604 改性聚丙烯99 98 50 1 0,2 375°C Ultralube® E-912 高密度聚乙烯98 96 83 6 3,8 408°C Ultralube SE-112 改性聚二甲基硅氧烷100 98 36 14 11,6 365°C
蜡残留一般发生在400℃以下。
案例:含有D-840和E-660的无硅脱模剂9000次喷射后没有脱模剂堆积
- UltralubeE-7098能提供更好的稳定性
-UltralubeE-7098/UltralubeE-8400在最终应用上提供良好的润湿性和硬水稳定性;由于对模具表面的高附着力,提供良好的离型效果
-UltralubeE-7098 / Ultralube E-8400做为配方中使用的低粘度蜡,对热模具有喷砂效果
-UltralubeE-7098 / UltralubeE-8400在模具低温部位的残留物能够在下一次喷洒脱模剂时再乳化。
这也避免一定次数的额外清洁
-乙氧基化酯蜡在模具表面上可稳定至380℃(热失重分析)。
在较高温度下,蜡很快分解。
分散体可无限制地与水混合而不分离
金属压铸添加剂(金属压铸脱模剂、水性脱模剂)推荐型号Ultralube 产品蜡的类型作用
E-7098 改性聚酯
对金属表面的高亲和性产生离型效果;
D-840 聚酰胺
其中E-7098对模具有额外的清理作用
D-8400 改性聚酯/ 聚酰胺
E-912
T-XP19021096
高密度聚乙烯类似“PE02/PE03/PE34”的离型效果
T-XP19021097
E-1058 高密度聚乙烯
E-846A 高密度聚乙烯
高熔融粘度产生离型效果
E-660 改性聚丙烯
E-XP08060604 改性聚丙烯
SE-112 改性聚二甲基硅氧烷可涂布离型剂。