第10章PCB生产剖析
PCB制造工艺流程详解课件
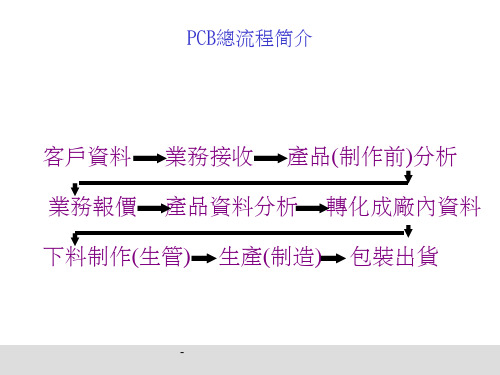
-
钻孔介绍(3)
I. 钻孔:
目的:
➢ 在板面上钻出层与层之间线路 连接的导通孔
主要原物料:钻头;鋁盖板;紙垫板
➢
钻头:碳化钨,钴及有机黏着剂组合而成
➢
盖板:主要为铝片,在制程中起钻头定位;
散热;减少毛头;保護基板的作用
➢
垫板:主要为紙漿墊板,在制程中起保护
钻机台面;清洁钻针沟槽胶渣作用.
➢ 下PIN:
铆钉
➢ 利用铆钉将多张内层板钉在一
2L
起,以避免后续加工时产生层间
3L
滑移
4L
• 主要原物料:铆钉;P/P
5L
➢ P/P(PREPREG):由树脂和玻璃纤
维布组成,据玻璃布种类可分为
1060;1080;2116;7628等几种
2L
➢ 树脂据交联状况可分为:
3L
A阶(液態);B阶(半固態);C阶(固態)
毛頭形成原因:鑽孔後孔邊緣的未切斷的銅絲及未切斷 的玻璃布
Deburr之目的:去除孔邊緣的毛邊,防止鍍孔不良 重要的原物料:刷輪
-
鍍銅介紹(3)
☺ 去膠渣(Desmear):
smear形成原因: 鑽孔時造成的高溫超過玻璃化轉移溫度
(Tg值),而形成膠糊狀,產生膠渣 Desmear之目的:裸露出各層需互連的銅環,另膨松劑可
-
防焊流程简介(5)
I. 印刷
目的:利用丝网上图案,将防焊油墨准确的 印在板子上。
主要原物料:油墨 常用的印刷方式:
A 印刷型(Screen Printing) B 淋幕型 (Curtain Coating) C 喷涂型 (Spray Coating) D 滚涂型 (Roller Coating)
PCB生产过程与技术(DOC 16)
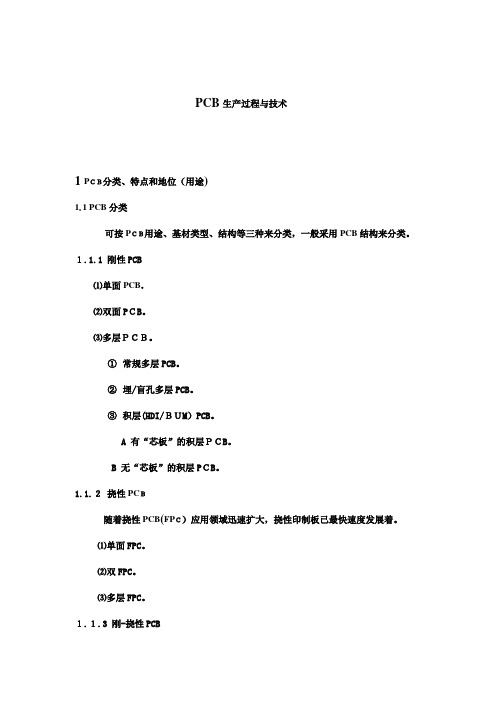
PCB生产过程与技术1 PCB分类、特点和地位(用途)1.1 PCB分类可按PCB用途、基材类型、结构等三种来分类,一般采用PCB结构来分类。
1.1.1 刚性PCB⑴单面PCB。
⑵双面PCB。
⑶多层PCB。
①常规多层PCB。
②埋/盲孔多层PCB。
③积层(HDI/BUM)PCB。
A 有“芯板”的积层PCB。
B 无“芯板”的积层PCB。
1.1.2挠性PCB随着挠性PCB(FPC)应用领域迅速扩大,挠性印制板已最快速度发展着。
⑴单面FPC。
⑵双FPC。
⑶多层FPC。
1.1.3 刚-挠性PCB这是指由刚性部分和挠性部分共同组成的PCB。
刚性部分主要用于焊接或组装元器件,而挠性部分主要起着刚性部分之间的连接、信号传输和可挠曲性机械安装的作用。
⑴刚性部分主要为刚性多层板结构,但中间夹入挠性部分,通过层压、钻孔和孔化与电镀等形成刚性部分与挠性部分之间连接。
⑵挠性部分由挠性板组成。
为了保持可挠曲性机械安装,挠性部分大多为单、双面挠性板或多组的单、双面挠性板等组成。
1.1.4 特种PCB这是指高频微波PCB、金属基(芯)PCB和某些特殊PCB而言的。
⑴高频微波PCB。
这是指应用于高频(频率大于300MHZ或波长小于1米)与微波(频率大于3G 或波长小于0.1米)领域的PCB。
其主要要求如下。
①低介电常数εr的基材。
A 聚四氟已烯(PTFE)又称Teflon,其εr=2.1,形成CCL的εr为2.6左右。
B “空气珠”或“微泡”结构的CCL材料,其εr为1.15∽1.35之间(Arlon公司)。
②低介质损耗角正切tanδ。
PTFE基材的tanδ为0.002,仅为FR-4的1/10。
⑵金属基(芯)PCB。
在组装有大功率组件的PCB内埋入金属板,以提高导热或散热为主要目的(还有改善CTE和尺寸稳定性等)的PCB。
所采用的金属材料有:薄Al板;薄Fe板;薄Cu板;殷钢;钨钼合金。
还有非金属的炭素板等。
⑶其它特殊PCB。
如厚铜箔PCB、复合材料PCB和特大尺寸(面积或厚度等)PCB。
PCB线路板基础知识讲义

制作流程
准备材料
01 根据设计要求,准备所需的铜
板、绝缘材料、导电材料等。
制作线路
02 根据设计图纸,使用各种制板
设备在铜板上制作线路。
添加阻焊剂
03 在PCB表面涂覆一层阻焊剂,
以保护线路和元器件免受损坏 。
表面处理
04 对线路板表面进行电镀、喷涂
等处理,以提高其导电性能和 耐腐蚀性。
组装元器件
机械应力
PCB在组装和使用过程中受到的机械应力可能导致线路断裂或焊 点脱落。
PCB的机械性能分析
01
02
03
耐冲击性
PCB应能承受一定程度的 冲击而不损坏。
耐弯曲性
PCB应能在一定程度的弯 曲后恢复原状,不发生断 裂或变形。
尺寸稳定性
PCB应能在温度和湿度变 化下保持稳定的尺寸和形 状。
PCB的热性能分析
设计原则
功能性原则
确保线路板实现所需的功能,满足电路连接 和信号传输的要求。
可靠性原则
保证线路板的稳定性和可靠性,能够承受一 定的机械和环境应力。
经济性原则
在满足功能和可靠性的前提下,尽量降低制 造成本。
维护性原则
设计应便于线路板的维修和保养,易于检测 和更换元件。
元件布局
按照电路功能分区布局
将电路中的元件按照功能划分区域,使布局更加清晰和易于管理。
环境适应性测试
模拟不同温度、湿度、盐雾等环境条件,检测 PCB的性能稳定性。
机械强度测试
对PCB进行振动、冲击、扭曲等试验,以评估其 在恶劣条件下的可靠性。
寿命测试
通过加速老化等方法检测PCB在不同使用条件下 的寿命。
THANKS FOR WATCHING
第10章PADS Layout的元器件的布局

第10章PADS Layout的元器件的布局第10章 PADS Layout的元器件的布局PADS Layout是复杂的、高速印制电路板的设计环境。
它是一个强有力的基于形状化(shape-based)、规则驱动(rules-driven)的布局设计方案。
PADS Layout的布局可以通过自动和手工两种方式来进行。
本章将从布局规则开始,对如何利用PADS2021软件实现元件布局进行详细的介绍,使读者对手动布局和自动布局有一个比较全面的了解。
10.1 布局规则介绍在PCB设计中,PCB布局是指对电子元器件在印刷电路上如何规划及放置的过程,它包括规划和放置两个阶段。
合理的布局是PCB设计成功的第一步,布局结果的好坏将直接影响到布线的效果和可制造性。
不恰当的布局可能导致整个设计的失败或生产效率降低。
在PCB设计中,关于如何合理布局应当考虑PCB的可制性、合理布线的要求、某种电子产品独有的特性等。
10.1.1 PCB的可制造性与布局设计PCB的可制造性是说设计出的PCB要符合电子产品的生产条件。
如果是试验产品或者生产量不大需要手工生产,可以较少考虑;如果需要大批量生产,需要上生产线生产的产品,则PCB布局就要做周密的规划。
需要考虑贴片机、插件机的工艺要求及生产中不同的焊接方式对布局的要求,严格遵照生产工艺的要求,这是设计批量生产的PCB应当首先考虑的。
当采用波峰焊时,应尽量保证元器件的两端焊点同时接触焊料波峰。
当尺寸相差较大的片状元器件相邻排列,且间距很小时,较小的元器件在波峰焊时应排列在前面,先进入焊料池。
还应避免尺寸较大的元器件遮蔽其后尺寸较小的元器件,造成漏焊。
板上不向组件相邻焊盘图形之间的最小间距应在1mm以上。
元器件在PCB板上的排向,原则上是随元器件类型的改变而变化,即同类元器件尽可能按相同的方向排列,以便元器件的贴装、焊接和检测。
布局时,DIP封装的汇摆放的方向必须与过锡炉的方向垂直,不可平行,如图10-1所示。
PCB制板工艺操作手册

PCB制板工艺操作手册第1章基础知识 (3)1.1 PCB概述 (3)1.2 制板工艺流程简介 (4)第2章材料准备 (5)2.1 基材选择 (5)2.2 覆铜板处理 (5)2.3 干膜制备 (6)第3章设计与布线 (6)3.1 PCB设计规范 (6)3.1.1 设计原则 (6)3.1.2 设计要求 (6)3.1.3 设计工具 (7)3.2 布线技巧 (7)3.2.1 布线规则 (7)3.2.2 层叠设计 (7)3.2.3 焊盘和过孔设计 (7)3.3 设计审查 (7)3.3.1 审查内容 (7)3.3.2 审查方法 (8)3.3.3 审查流程 (8)第4章制板前处理 (8)4.1 覆铜板切割 (8)4.1.1 材料准备 (8)4.1.2 切割操作 (8)4.1.3 质量检查 (8)4.2 钻孔与孔金属化 (8)4.2.1 钻孔 (8)4.2.2 孔金属化 (8)4.2.3 质量检查 (8)4.3 黑化处理 (8)4.3.1 材料准备 (9)4.3.2 黑化处理操作 (9)4.3.3 清洗与干燥 (9)第5章光绘与显影 (9)5.1 光绘工艺 (9)5.1.1 设备准备 (9)5.1.2 光绘参数设置 (9)5.1.3 光绘操作步骤 (9)5.1.4 注意事项 (9)5.2 显影工艺 (9)5.2.1 显影设备准备 (9)5.2.3 显影操作步骤 (10)5.2.4 注意事项 (10)5.3 质量检查 (10)5.3.1 检查方法 (10)5.3.2 检查内容 (10)5.3.3 处理措施 (10)第6章化学镀与电镀 (10)6.1 化学镀铜 (10)6.1.1 原理概述 (10)6.1.2 化学镀铜溶液组成 (10)6.1.3 操作步骤 (11)6.1.4 注意事项 (11)6.2 电镀铜 (11)6.2.1 原理概述 (11)6.2.2 电镀铜溶液组成 (11)6.2.3 操作步骤 (11)6.2.4 注意事项 (11)6.3 电镀锡铅 (11)6.3.1 原理概述 (11)6.3.2 电镀锡铅溶液组成 (12)6.3.3 操作步骤 (12)6.3.4 注意事项 (12)第7章蚀刻与去膜 (12)7.1 蚀刻工艺 (12)7.1.1 蚀刻原理 (12)7.1.2 蚀刻前准备 (12)7.1.3 蚀刻操作 (12)7.1.4 蚀刻后处理 (12)7.2 去膜工艺 (13)7.2.1 去膜原理 (13)7.2.2 去膜前准备 (13)7.2.3 去膜操作 (13)7.2.4 去膜后处理 (13)7.3 质量检查 (13)7.3.1 蚀刻质量检查 (13)7.3.2 去膜质量检查 (13)7.3.3 异常处理 (13)第8章表面处理 (13)8.1 热风整平 (13)8.1.1 工艺简介 (14)8.1.2 工艺流程 (14)8.1.3 注意事项 (14)8.2 沉金处理 (14)8.2.2 工艺流程 (14)8.2.3 注意事项 (14)8.3 阻焊油墨印刷 (15)8.3.1 工艺简介 (15)8.3.2 工艺流程 (15)8.3.3 注意事项 (15)第9章焊接与组装 (15)9.1 表面贴装技术 (15)9.1.1 表面贴装概述 (15)9.1.2 焊膏印刷 (15)9.1.3 贴片 (16)9.1.4 回流焊接 (16)9.2 通孔焊接 (16)9.2.1 通孔焊接概述 (16)9.2.2 焊料选择 (16)9.2.3 焊接过程 (16)9.3 检验与返修 (16)9.3.1 检验 (16)9.3.2 返修 (17)第10章质量控制与验收 (17)10.1 制板过程质量控制 (17)10.1.1 制程参数监控 (17)10.1.2 在线检测 (17)10.1.3 抽样检测 (17)10.1.4 工艺优化与改进 (17)10.2 成品验收标准 (17)10.2.1 外观检查 (17)10.2.2 尺寸测量 (17)10.2.3 功能性测试 (17)10.2.4 无铅焊接适应性测试 (18)10.3 故障分析与排除方法 (18)10.3.1 故障分类 (18)10.3.2 故障原因分析 (18)10.3.3 故障排除方法 (18)10.3.4 预防措施 (18)第1章基础知识1.1 PCB概述印刷电路板(Printed Circuit Board,简称PCB)是电子设备中用于支撑和连接电子元件的一种基础组件。
Altium Designer 14原理图与PCB设计第10章 综合实例

第10章 综合实例 图10-4 Messages(消息)对话框
第10章 综合实例
10.1.3 绘制印刷电路板图 1. 准备工作 绘制印刷电路板图之前,需要做一些准备工作,保证绘
制工作顺利进行,减少返工的概率。 (1) 需要核查所选的元件封装是否符合项目的要求或者
工程应用要求。在原理图编辑环境下,执行菜单命令Tools >> Footprint Manager,系统将弹出Footprint Manager(封装管 理)对话框,如图10-5所示。
第10章 综合实例 图10-5 Footprint Manager(封装管理)对话框
第10章 综合实例
在该对话框中查看每个元件的封装信息,如封装名,对 应的封装库,二维图形等。如果封装不符合要求,可以进行 修改或新增。点击Edit按钮,系统将弹出如图10-6所示的 PCB Model对话框。在PCB Model对话框去选择一个合适的 封装,也可以点击Add按钮,弹出PCB Model对话框,选择 一个封装作为元件封装的一种选择。
VR5 AXIAL-0.4 AXIAL-0.4 AXIAL-0.4
DIP-8 DIP-20
R38
第10章 综合实例
10.1.2 绘制原理图 1. 创建工程 执行菜单命令File >> New >> Project, 在New Project 对
话框中选择Project Type为PCB Project,Project Templates为 <Default>,将该工程命名为频率计.PrjPcb。
第10章 综合实例 图10-1 频率计电路原理图
Lib Ref Cap Cap2
D Zener DPY_8_4 Header 3
第10章 电源的印制板设计
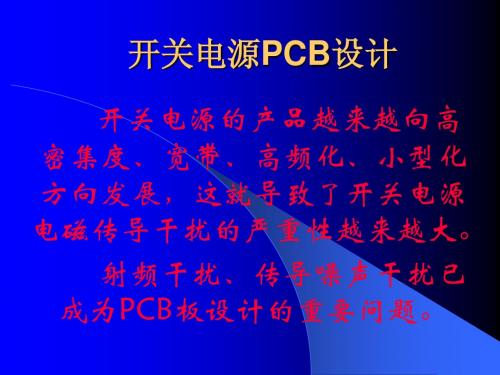
多层板(Multi多层板(Multi-Layer Boards) Boards)
我们刚刚提到的导孔(via),如果应用在双面 板上,那么一定都是打穿整个板子。不过在多层板当 中,如果您只想连接其中一些线路,那么导孔可能会 浪费一些其它层的线路空间。埋孔(Buried vias)和 盲孔(Blind vias)技术可以避免这个问题,因为它 们只穿透其中几层。盲孔是将几层内部PCB与表面 PCB连接,不须穿透整个板子。埋孔则只连接内部的 PCB,所以光是从表面是看不出来的。 在多层板PCB中,整层都直接连接上地线与电源。 所以我们将各层分类为信号层(Signal),电源层 (Power)或是地线层(Ground)。如果PCB上的零 件需要不同的电源供应,通常这类PCB会有两层以上 的电源与电线层。
PCB板的分类 PCB板的分类
PCB板有桡性绝缘板和刚性绝缘板两种 (详见课本244页)。 一般的PCB元器件安装有3种方式: 1、插入是安装(一般是dip); 2、表面安装(smd); 3、芯片直接安装。
Pcb板面说明 Pcb板面说明
为了将零件固定在PCB上面,我们 将它们的接脚直接焊在布线上。在最基 本的PCB(单面板)上,零件都集中在 其中一面,导线则都集中在另一面。这 么一来我们就需要在板子上打洞,这样 接脚才能穿过板子到另一面,所以零件 的接脚是焊在另一面上的。因为如此, PCB的正反面分别被称为零件面 (Component Side)与焊接面 (Solder Side)。Leabharlann 电磁兼容问题1 电磁兼容问题1
没有照EMC(电磁兼容)规格设计的电子设备, 很可能会散发出电磁能量,并且干扰附近的电器。EMC 对电磁干扰(EMI),电磁场(EMF)和射频干扰(RFI) 等都规定了最大的限制。这项规定可以确保该电器与附 近其它电器的正常运作。EMC对一项设备,散射或传导 到另一设备的能量有严格的限制,并且设计时要减少对 外来EMF、EMI、RFI等的磁化率。换言之,这项规定的 目的就是要防止电磁能量进入或由装置散发出。这其实 是一项很难解决的问题,一般大多会使用电源和地线层, 或是将PCB放进金属盒子当中以解决这些问题。电源和 地线层可以防止信号层受干扰,金属盒的效用也差不多。 对这些问题我们就不过于深入了。
学习入门-学习入门-Altium-Designer第10章-信号完整性分析优选全文

1.互阻抗模型 PCB上两根走线之间的互阻抗模型如图10.1.3所示。
图10.1.3 PCB上两根走线之间的互阻抗模型
2. 电容耦合产生的串扰(容性串扰)
所有两相邻导线之间都存在电容。当在一条线(攻击线或主
动线)加上一个脉冲信号(vs)时,脉冲信号会通过电容Cm
向另一条线(受害线或被动线)耦合一个窄脉冲。也就是两
上升时间,用tr表
示。
图10.1.1 非理想的脉冲(数字)信号波形
2. 带宽(频宽)
对于高速数字电路,决定其所需之带宽(频宽)的是时钟脉冲信
号上升时间tr,而不是时钟脉冲信号的频率。对于频率相同的时 钟信号,如果它们的上升时间tr不同,所需电路的带宽(频宽)
也是不同的[24]。
带宽(频宽)与信号的上升时间tr有关。一个有价值的经验法则 ,信号的带宽(频宽)与上升时间tr的关系[51]可以用下式表示:
信号的传播速度Vp与材料的介电常数εr之间的关系如下所示:
(10.1.3)
式中:C为光速(3×108m/s);εr为材料的介电常数。
10.1.3 反射
1. 反射的产生 反射(Reflection)就是传输线上的回波,信号功率的一部分
经传输线传给负载,另一部分则向源端反射。 信号沿传输线传播时,如果阻抗匹配(源端阻抗、传输线阻
SI、PI和EMI设计紧密关联,而PDN(Power Distribution Network,电源分配网络)是 SI、PI和EMI的公共基础互连,相 互关系[22,25]如图10.1.6所示。而SI、PI和EMI协同设计是高速数字 系统设计的唯一有效途径。
图10.1.6 SI、PI和EMI与PDN的相互关系
EMI到达EMI接收器的路径。
- 1、下载文档前请自行甄别文档内容的完整性,平台不提供额外的编辑、内容补充、找答案等附加服务。
- 2、"仅部分预览"的文档,不可在线预览部分如存在完整性等问题,可反馈申请退款(可完整预览的文档不适用该条件!)。
- 3、如文档侵犯您的权益,请联系客服反馈,我们会尽快为您处理(人工客服工作时间:9:00-18:30)。
≤400mm,长≥100mm;刷板厚度:0.5mm~6mm可通过手轮调节;各部件的作用见
表3-1。
第10章PCB生产剖析
图3-14 Create-BFM3200抛光机的实物照片
第10章PCB生产剖析
表10-1 抛光机各部件的作用
序号 1 2
部件名称 电源开关 控制面板
3
速度调节旋钮
4
急停
5
入板口
向主扫描,光学记录系统横移作副扫描,两个扫描运动合成,实现将计算机
内部图形信息以点阵形式还原在胶片上。其原理与电视机显像管中电子枪扫
描屏幕上的荧光物质相似。
第10章PCB生产剖析
内圆筒式激光光绘机
第10章PCB生产剖析
外滚筒式激光光绘机
第10章PCB生产剖析
•
1.激光光绘机
•
简称光绘机,是集激光光学技术、微电子技术和超精密机械于一体的照排设备,
第10章PCB生产剖析
10.2.3 裁板
•
裁板又称下料,在PCB制作前,应根据设计好的PCB图的大小来确定
所需PCB覆铜板的尺寸规格。
•
1.裁板机
•
一般裁板机可分为:脚踏式(人力)、机械式、液压摆式、液压闸式。
一般的中小企业常用的裁板设备有两种,一种是手动裁板的基本原理是借助于运动的上刀片和固定的下刀片,采用合理的刀
10.2.5钻孔
•
1.工艺描述
•
钻孔是在镀铜板上钻通孔或盲孔,建立PCB层与层之间以及元件与线路
6
上刷调节旋钮
7
下刷调节旋钮
8
顶部钢化玻璃盖
9
出板口
10
脚轮
功能 控制总机电源 人机界面为触摸式操作,液晶显示,设置
机器工作参数,控制机器运行 调节传动速度 紧急停止按钮 待抛光板材的入口 调节上刷的抛光力度 调节下刷的抛光力度 防止水溢出 抛光后板材的出口 便于移动机器,带刹车可固定位置
第10章PCB生产剖析
片间隙,对各种厚度的板材施加剪切力,使板材按所需要的尺寸断裂分离。
剪切工艺应能保证被剪覆铜板剪切表面的直线性和平行度要求,并尽量减少
板材扭曲,以获得高质量的工件。图3-13所示为手动裁板机外形图。
第10章PCB生产剖析
图10-13手动裁板机
第10章PCB生产剖析
•
2.手动裁板机操作方法
•
1)板材固定。根据用户所需裁剪尺寸大小,首先移动定位尺来确定裁剪尺寸,并
件设计的PCB图形数据文件送入激光光绘机的计算机系统,控制光绘机利用
光线直接在底片上绘制图形;然后经过显影、定影得到胶片底版。激光光绘
机采用He—Ne激光器作为光源,声光调制器作为扫描激光的控制开关,由计
算机发送的图像信息经RIP处理后进入驱动电路控制声光调制器工作,被调制
的衍射激光,经物镜聚焦在滚筒吸附的胶片(菲林)上,滚筒高速旋转作纵
10.2 PCB线路形成
PCB线路形成在中小规模PCB制造企业中主要涵盖了 PCB10个工艺流程,即:制片;裁板;抛光;钻孔;金属过 孔;线路感光层制作;图形曝光;图形显影;图形电镀;图形 蚀刻。
第10章PCB生产剖析
10.2.1 激光光绘
•
制片主要有两个步骤:光绘和冲片。光绘是直接将在计算机中用CAD软
•
4)定影槽:完成感光胶片图像定影(配定影泵)。
•
5)烘干槽:采用热风循环吹干胶片(配热风烘干机)。
•
6)出板口:成像后的干胶片输出口。
•
工业生产均采用自动工艺,全自动高温水平传动冲洗,胶片底片从前端输入,从
后端输出,中间过程不需要任何人工操作。
第10章PCB生产剖析
图10-10 冲片机的实物照片
用于在感光照相胶片上绘制各种图形,图像,文字或符号。首先,将印制电路板的图
面映像到一个大存储阵列中,然后使激光束按照存储阵列中相应单元的值被打开或关
闭(调制),从而得到所需要的工艺照片。激光光绘机采用激光做光源,有容易聚焦、
能量集中等优点,对瞬间快速的底片曝光非常有利,绘制的底片边缘整齐、反差大、
不虚光。曝光采用扫描式,无论密度多大,均能在最短时间内完成曝光,绘制一张底
片只需几分钟。因此成为当今光绘行业的主流。激光光绘机的光源多采用气体激光器, 如氩、氦和氖等。气体激光器的光源强度大,但寿命却有限,约6000~10000h,因此 使用一年多就需要更换光源,现在一些光绘机生产厂家采用了半导体激光器作为光源。
第10章PCB生产剖析
图10-9 光绘机的实物照片
第10章PCB生产剖析
提起压杆,再将待裁剪的板材置于裁板机底板上,并且将板材移至刀头部分,(靠近
压杆根部位置)对齐对位标尺和定位尺,使其裁剪尺寸更加精确。
•
2)裁板。板材固定完毕后,在裁板过程中,为避免板材的移动导致裁剪倾斜,应
先左手压住板材,右手再将压杆压下,压下压杆即完成一条边的裁板;重复上述步骤
就可以完成多边或多块板的裁剪。由于弯刀型裁板机弯刀受力支点靠首端,在确定好
程。
•
1.抛光机
•
线路板抛光磨刷清洗处理机(抛光机),是PCB生产工艺中不可缺少的专业设备,
可对PCB板进行刷磨、清洗、吸干等表面处理,集进料、磨刷、水洗、吸干、出料诸
多功能于一体。图3-14是Create-BFM3200抛光机的实物照片,该机可进行PCB表面
全自动抛光处理;刷板方式:独立单面抛光、双面同时抛光;配有双丝杆调节轮;具
有电气自动控制进水功能和排水功能以及传动导轨拆卸、双面吸水辊吸干、自动传送
自动烘干、不锈钢链式传送等功能;控制系统:高性能嵌入式处理器+嵌入式操作系统,
人机界面:大屏幕彩色液晶显示屏+触摸屏;能在触摸显示屏内阅读电子版抛光制作工
艺说明书;能在触摸显示屏内播放抛光工艺制作后的线路板效果图;刷板尺寸:宽
10.2.2 冲片
•
1.冲片机
•
胶片(菲林)冲片机又称显影机,与光绘机连接,属印前处理设备。冲片机用药
水显影,定影,经水洗、烘干,把胶片冲洗出来。
• 设备部件及功能:
•
1)入板口:激光照排(光绘)后的胶片进入口。
•
2)液晶显示面板:各工艺参数设置及工艺流程显示。
•
3)显影槽:完成感光胶片图像显影(配显影泵)。
覆铜板尺寸并固定好定位尺后,将覆铜板往前端移动再裁剪可更省力。刀片在使用中,
可以使用刀距调节旋钮使其距离编紧,使得裁板更加精确。
•
3)在使用时,严禁将手或身体的任何一个部位放入刀片下,手握压杆时,尽量靠
后,以免造成不必要的伤害。
第10章PCB生产剖析
10.2.4 抛光
•
抛光是除去PCB铜面的油污和氧化层,增加铜面的粗糙度,以利于后续的压膜制