线路板厂碱性蚀刻液铜回收工艺
碱性蚀刻液循环再生技术2013215

碱性蚀刻液循环再生系统建议计划书2013年2月15日一、项目背景近20年来,中国的PCB行业一直保持10-00%的年增长速度,目前有多种规模的PCB企业3500多家,月产量达到1.2亿平方米。
蚀刻是PCB生产中耗药水量较大的工序,也是产生废液和废水最大的工序,一般而言,每生产一平方米正常厚度(18μm)的双面板消耗蚀刻液约为2~3升,并产出废蚀刻液2~3升。
我国PCB行业每月消耗精铜6万吨/月以上,产出的铜蚀刻废液中总铜量在5万吨/月以上,对社会尤其是PCB厂周边地区的水资源和土壤造成了严重污染。
铜是一种存在于土壤及人畜体内的重金属元素,土壤中含量一般在0.2ppm左右,过量的铜会与人畜体内的酶发生沉淀/络合反应,发生酶中毒而丧失生理功能。
自然界中的铜通过水体、植物等转移至人畜体内,使人畜体内的微量元素平衡遭到破坏,导致重金属在体内的不正常积累,产生致病变性、致癌性等结果。
探索铜蚀刻过程的清洁生产技术,使铜蚀刻废液消除在生产过程中,实现在线循环再生,以彻底杜绝污染源及其污染扩散,实现真正意义上的源头治理,既是环境保护部门强制执法的第一选择,也是PCB行业降低生产成本,走可持续发展之路的必然选择。
二、项目运作模式2.1系统设备的提供1)我公司免费提供一成套碱性蚀刻液循环再生设备,废液处理能力100吨/月,设备造价200万元/套。
2)贵公司负责免费提供设备安装运作所需要的场地和相关水电接入到循环再生设备生产车间等条件。
2.2系统设备运作1)设备运作由我公司派专人和工程师24小时配合贵公司运作管理;2)设备运作费用由我公司自行负责;3)再生子液的化学药剂等费用由我公司负责;4)贵公司负责设备和我公司现场工作人员的基本安全,为我公司驻厂工作人员提供食宿。
2.3系统设备维护1)设备维护由我公司负责;2)设备维护费用由我公司自行负责;3)设备日常管理记录由我公司负责。
2.4收益共享分配1)设备运作所产生的效益实现共享原则;2)回收铜贵公司享有按合同的分配比例分配;3)回收铜由我公司回收、处理,每次回收将邀请贵公司人员到场记账互签;4)铜销售价格以当期上海金属交易所价格为准,每次提取铜后我公司7天内将贵公司所得汇入贵公司账户;三、设备工艺原理碱性蚀刻液在线循环技术采用溶剂萃取膜处理—电解还原法,从失效蚀铜液中分离回收铜,同时通过补加药剂,使失效蚀铜液得到有效回收并循环使用,废液回收率利用率100%,铜回收率100%。
线路板微蚀液回收方法

线路板生产微蚀液废液回收利用办法线路板行业在生产中会产生大量的微蚀废液,为了降低生产成本和环保处理成本,如果把微蚀液回收利用,可以大大降低成本并减少废液排放,下面以H2O2+H 2SO4为例介绍一下微蚀液的回收处理方法。
一、微蚀液量与排放频率二、小试:1、取沉铜磨板线排放时的微蚀液,测得CU 2+浓度是25g/l.H 2SO 4浓度是1.5%,H 202浓度是1.1%,置冰箱冷冻至结冰,后取出待冰溶化完全(温度10℃),未见有沉淀2、取排放时沉铜微蚀液,测得CU 2+浓度是20g/l.H 2SO 4浓度是1.3%,H 202浓度是1.2%,置冰箱冷冻至结冰,后取出待冰溶化完全(温度10℃),未见有沉淀3、取250mlOSP 微蚀液,测得CU 2+浓度22g/l,H 2O 2浓度:4%,搅拌加热至80℃,冷却后放入冰箱冷冻,待冰全部融化后测温度为16℃,瓶底有蓝色沉淀,此沉淀为CUSO 4.5H 2O 分析溶液CU 2+20g/l ,H 2O 2浓度3%,微蚀液排放频率排放体积(L)Cu 2+含量(g/l)H 2SO 4浓度H2O2浓度OSP 线一月一次400255%4%沉铜线一班一次100019 1.2% 1.1%沉铜磨板线一千块板一次400221.3%1.3%4、取250mlOSP 微蚀液,测得铜离子浓度为22g/l,H 2SO 4浓度是4.3%,H 2O 2是4%Cu 2++C 2H 4O 2→CuC 2H 2O 2↓+2H +6490152根据计算,加入草酸7.7g ,取上清液测得Cu 2+浓度为8g/l.又称取2.5g 草酸加入,测Cu 2+浓度为2.6g/l ,H 2SO 4浓度是5%,H2O2浓度是4%。
根据试验数据,在Cu 2+和草酸质量比为1:2时,铜回收率可达88%,原液中的H 2SO 4,H 2O 2的浓度变化不大,说明草酸的加入量是适量的。
三、小结通过以上试验,倾向说实验四,化学沉淀法沉铜,虽然化学沉淀法沉淀分离的速率慢,还会引入别的物质,草酸易分解,在80℃时就会分解生成水和CO 2,微蚀液老化速率可以大大降低,且草酸中的-COOH 官能团对微蚀液中的双氧水起到一定的保护作用,轻微过量的草酸可以降低双氧水的自身消耗。
碱性蚀刻液铜回收工艺
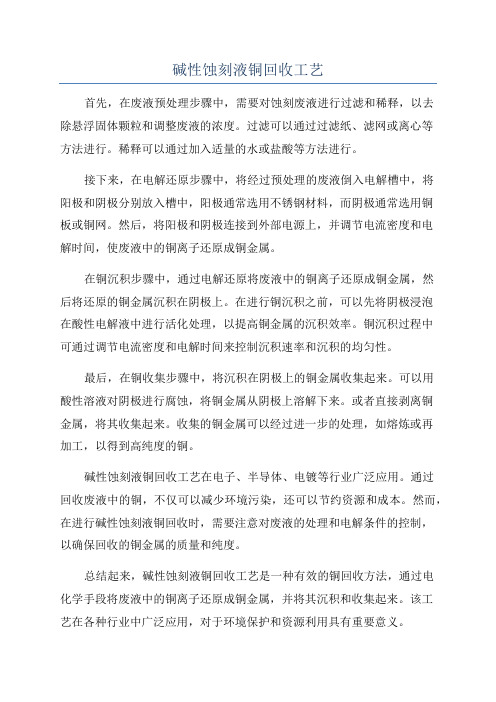
碱性蚀刻液铜回收工艺首先,在废液预处理步骤中,需要对蚀刻废液进行过滤和稀释,以去除悬浮固体颗粒和调整废液的浓度。
过滤可以通过过滤纸、滤网或离心等方法进行。
稀释可以通过加入适量的水或盐酸等方法进行。
接下来,在电解还原步骤中,将经过预处理的废液倒入电解槽中,将阳极和阴极分别放入槽中,阳极通常选用不锈钢材料,而阴极通常选用铜板或铜网。
然后,将阳极和阴极连接到外部电源上,并调节电流密度和电解时间,使废液中的铜离子还原成铜金属。
在铜沉积步骤中,通过电解还原将废液中的铜离子还原成铜金属,然后将还原的铜金属沉积在阴极上。
在进行铜沉积之前,可以先将阴极浸泡在酸性电解液中进行活化处理,以提高铜金属的沉积效率。
铜沉积过程中可通过调节电流密度和电解时间来控制沉积速率和沉积的均匀性。
最后,在铜收集步骤中,将沉积在阴极上的铜金属收集起来。
可以用酸性溶液对阴极进行腐蚀,将铜金属从阴极上溶解下来。
或者直接剥离铜金属,将其收集起来。
收集的铜金属可以经过进一步的处理,如熔炼或再加工,以得到高纯度的铜。
碱性蚀刻液铜回收工艺在电子、半导体、电镀等行业广泛应用。
通过回收废液中的铜,不仅可以减少环境污染,还可以节约资源和成本。
然而,在进行碱性蚀刻液铜回收时,需要注意对废液的处理和电解条件的控制,以确保回收的铜金属的质量和纯度。
总结起来,碱性蚀刻液铜回收工艺是一种有效的铜回收方法,通过电化学手段将废液中的铜离子还原成铜金属,并将其沉积和收集起来。
该工艺在各种行业中广泛应用,对于环境保护和资源利用具有重要意义。
碱性蚀刻液循环再生系统

碱性蚀刻液循环再生系统
一、技术简介
碱性蚀刻液循环再生系统是专门针对PCB印制线路板厂生产中产生的碱性蚀刻废液而设计的,采用先进的封闭式自体循环和平行式无损分离技术(CSC-PLS)进行金属铜的分离和蚀刻液的回用,经严格有效的工艺过程,实现了溶液的长期循环再生和100%铜回收率的目标,同时将生产运行成本控制到最低。
该系统与蚀刻机在线闭环连接,自动循环运作。
二、设备说明
1、工艺流程
蚀刻机中溢流出的碱性蚀刻废液进入母液罐,再用泵送入电解槽。
调整主机内铜离子浓度、氯离子浓度和碱度至规定标准,然后通电电解。
取出产品电解铜,将溶液泵至再生子液罐,并检测溶液各离子浓度、pH值,根据检测结果调整各成分含量,调整完毕再次检测,合格后泵入子液罐中待PCB厂家使用。
三、环保指标
◆该系统采用封闭式自体循环和无损分离技术(CSC-PLS)实现了废液的100%回用
◆在整个过程中无固体废弃物、废液、废气产生
◆完全符合国家清洁生产、节能减排的环保要求
四、特点及优势
◆本系统采用PLS平行式无损分离技术,整个过程无需使用任何萃取剂、添加剂,真正实现了对废蚀刻液的无损分离,保证了蚀刻液回用的质量。
◆本系统采用CSC封闭式自体循环技术对废蚀刻液进行循环再生,整个过程既不带入其他外来物质,也没有产生有害物质,更不会破坏溶液成分,再生蚀刻液性能可以与新购子液相媲美,特别适用于高精度PCB 板制作。
◆该系统稳定性强,设备操作简便,便于维护。
采用一站式闭环控制系统,使设备运行更加可靠,运行成本为同行业最低。
印制板蚀刻废液循环利用及铜回收新技术及设备
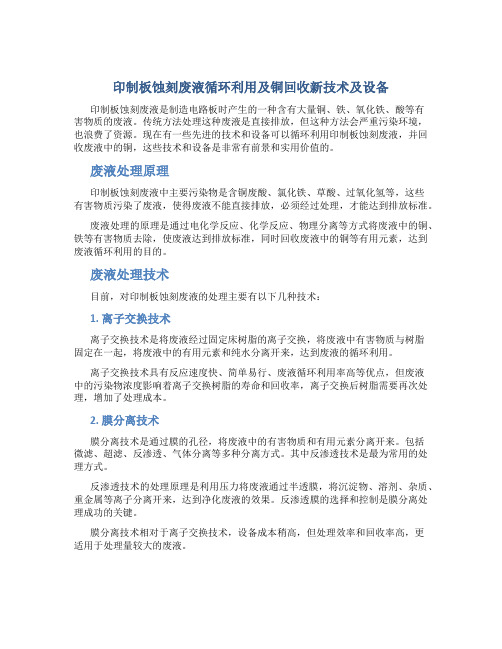
印制板蚀刻废液循环利用及铜回收新技术及设备印制板蚀刻废液是制造电路板时产生的一种含有大量铜、铁、氧化铁、酸等有害物质的废液。
传统方法处理这种废液是直接排放,但这种方法会严重污染环境,也浪费了资源。
现在有一些先进的技术和设备可以循环利用印制板蚀刻废液,并回收废液中的铜,这些技术和设备是非常有前景和实用价值的。
废液处理原理印制板蚀刻废液中主要污染物是含铜废酸、氯化铁、草酸、过氧化氢等,这些有害物质污染了废液,使得废液不能直接排放,必须经过处理,才能达到排放标准。
废液处理的原理是通过电化学反应、化学反应、物理分离等方式将废液中的铜、铁等有害物质去除,使废液达到排放标准,同时回收废液中的铜等有用元素,达到废液循环利用的目的。
废液处理技术目前,对印制板蚀刻废液的处理主要有以下几种技术:1. 离子交换技术离子交换技术是将废液经过固定床树脂的离子交换,将废液中有害物质与树脂固定在一起,将废液中的有用元素和纯水分离开来,达到废液的循环利用。
离子交换技术具有反应速度快、简单易行、废液循环利用率高等优点,但废液中的污染物浓度影响着离子交换树脂的寿命和回收率,离子交换后树脂需要再次处理,增加了处理成本。
2. 膜分离技术膜分离技术是通过膜的孔径,将废液中的有害物质和有用元素分离开来。
包括微滤、超滤、反渗透、气体分离等多种分离方式。
其中反渗透技术是最为常用的处理方式。
反渗透技术的处理原理是利用压力将废液通过半透膜,将沉淀物、溶剂、杂质、重金属等离子分离开来,达到净化废液的效果。
反渗透膜的选择和控制是膜分离处理成功的关键。
膜分离技术相对于离子交换技术,设备成本稍高,但处理效率和回收率高,更适用于处理量较大的废液。
3. 微生物处理技术微生物处理技术是利用微生物的去除能力,将有害物质降解为无害物质,是一种较为有潜力的处理技术。
这种技术存在工艺简单、处理成本低等优点。
目前,微生物处理技术主要包括好氧微生物法、厌氧微生物法和真菌生物法等,其中好氧微生物法的效果较好。
1137.印制线路板含铜蚀刻废液的综合利用技术

印制线路板含铜蚀刻废液的综合利用技术印制线路板含铜蚀刻废液的综合利用技术适用范围印制线路板制造业发达地区集中开展含铜蚀刻废液综合利用。
主要技术内容一、基本原理将印制线路板碱性蚀刻废液与酸性氯化铜蚀刻废液进行中和沉淀,生成的碱式氯化铜沉淀用于生产工业级硫酸铜;沉淀压滤母液用于生产碱性蚀刻液;其余废水经金属铝屑置换去除铜离子,进行蒸发浓缩生产混合铵盐。
另将三氯化铁蚀刻废液投铁提铜后通入氯气并蒸发浓缩,生成三氯化铁回用于线路板蚀刻。
二、关键技术硫酸铜、碱性蚀刻液、混合铵盐、三氯化铁综合利用生产技术及生产线。
典型规模1、利用碱性、酸性蚀刻废液10000吨/年,生产工业级硫酸铜4000吨/年,碱性蚀刻液4000吨/年,混合铵盐1200吨,硫酸铜废水处理铜粉50吨;2、利用三氯化铁蚀刻废液3000吨/年,生产三氯化铁蚀刻液4000吨/年,三氯化铁废液处理铜粉150吨。
主要技术指标及条件一、技术指标(一)废液资源利用率1、铜利用率碱性、酸性蚀刻废液 99.5%;三氯化铁蚀刻废液:95%2、氨(铵)利用率:100%。
3、三氯化铁利用率:100%。
(二)产品指标及性能硫酸铜(CuSO4•5H2O)、碱性蚀刻液、混合铵盐、铜粉、三氯化铁蚀刻液二、条件要求1、碱性、酸性蚀刻废液利用:占地5000平方米;硫酸铜生产电耗20万度/年、水耗6000吨/年、浓硫酸2000吨/年;碱性蚀刻液生产电耗1.52万度/年、无水耗、液氨350吨/年、工业氯化铵400吨/年;铵盐回收电耗5.61万度/年、水耗6000吨/年、柴油580吨/年。
有印制线路板含铜蚀刻废液需要处理的单位,也可以到污水宝项目服务平台咨询具备类似废水处理经验的企业。
2、三氯化铁蚀刻废液利用:占地2000平方米,电耗2.2万度/年、水耗1.38万吨/年、液氯246吨/年、纯铁片415吨/年、柴油40.8吨/年。
主要设备及运行管理一、主要设备1、碱性、酸性蚀刻废液利用:硫酸铜生产线、碱性蚀刻液生产线、混合铵盐生产线。
基于萃取的印制板碱性蚀刻废液中铜的回收

基于萃取的印制板碱性蚀刻废液中铜的回收摘要:PCB电路板具体生产期间会有大量碱性的蚀刻废液产生,所引发的环境污染问题较为严重。
本文主要结合现行主流回收技术,经过长期实践经验积累与综合分析之后,提出了以萃取法为基础下PCB板废液内铜离子的回收处理方法。
对于废液内多数部分均为铜氨溶液,以萃取法为基础原理,萃取剂选用β-二酮类,萃取铜氨废液内铜,获取不同浓度、温度、pH值等条件下对于萃取具体影响情况。
添加H2SO4反萃取经回收后所有溶液,分析不同H2SO4浓度之下对于萃取具体影响情况。
此次试验研究结果均表明了处于pH值9.5、相对比例1:1、25℃条件下,铜萃取的浓度可达最大;当反萃相的H2SO4溶液内氢离子实际浓度约4mol/L 期间,效果为最佳,可达回收再利用PCB板废液效果。
关键词:萃取;印制板;碱性;蚀刻;废液;铜;回收前言:现阶段在生产电子产品期间,对于PCB板加工常运用各种不同加工处理归功于,所获取到废液较为不同。
PCB 覆铜箔的蚀刻工艺当中,常用酸性与碱性的蚀刻液。
但是,实际生产运行期间,往往会因所产生碱性的蚀刻废液,污染到周边的环境,负面影响及企业外部良好形象均会受到不同程度的影响。
在这一背景下,电子产品的生产企业及社会各界对于PCB蚀刻的废液处理及再回收并利用废液关注度逐渐提高。
鉴于此,本文主要针对以萃取为基础印制板内碱性的蚀刻废液当中铜回收处理进行综述分析,望能够为相关专家及学者对这一课题的深入研究提供有价值的参考或者依据。
1.萃取法基本原理萃取法,主要是在蚀刻废液内添加某类或者某种萃取剂,借助铜离子处于不同溶剂内形成不同溶解度这一基本原理,选择性地把废液内铜离子分离的一种处理方法。
一般、需借助电沉积方法提取其中铜离子。
本文所用萃取剂为β-二酮,萃取机理表示即为:经β-二酮的结构内轻基,与二价的铜离子实现交换处理,螯合物便会逐渐形成。
2.试验研究操作2.1 试验材料试验所用原材料主要包括:二水氯化铜、硫酸、氨水、磺化煤油、β-二酮类的萃取剂。
碱性蚀刻子液配方及故障解决+蚀刻液再生回用铜回收设备药水参数要求

一、碱性蚀刻子液的调配(以配制2000L蚀刻子液为例)1、在调配罐中加入640升自来水。
2、加入560 KG蚀板盐并开启搅拌。
3、待蚀板盐大部分溶解时加入800升25%氨水继续搅拌。
4、直到蚀板盐完全溶解,再加入6公斤碱性蚀刻添加剂。
5、搅拌均匀,化验合格即可使用。
(注:配完后一定要化验氯离子和PH,达到贵司所要求参数后才打到楼顶使用。
)二、碱性蚀刻线工作缸蚀刻液药水参数1、CL-:170 g/L ~210 g/L2、Cu2+:120 g/L ~140 g/L3、pH :8.2 ~8.8 (热溶液时的pH)4、比重:1.18 ~1.25 g/cm35、温度:48 ~52℃6、压力 1.5~3.5 kg/m3三、碱性蚀刻线常见故障解决1、含铜量的多寡对线路侧蚀影响是很小的,但PH、温度过高和时间过长,侧蚀会明增加。
2、蚀刻均匀性:蚀刻液蚀刻掉铜的均匀分布能力。
3、蚀刻因子:线侧蚀度和线厚比值。
蚀刻因子愈高则代表侧蚀愈低,若蚀刻因子降低则可能受以下因数影响。
(A)药液问题:①PH>8.6时,蚀刻因子降低,尤其当NH3•H2O含量升高时。
②氯离子过高,蚀刻因子降低。
③温度愈高则侧蚀愈低,温度愈低则侧蚀愈高,但蚀刻速度会降低。
④亚铜离子(一价铜)过多,蚀刻因子降低。
亚铜离子过多的原因可能因O2不足,此时应增加抽风系统的通气量。
⑤铜离子太低,蚀刻因子降低。
(B)机械问题:①上下喷压不均,造成其中一面过蚀。
此时因调整上下压力,使板子出来后蚀刻程度一致。
②喷嘴或滤网阻塞,造成压力不稳定,蚀刻时间难以控制。
③喷嘴摇动角度过大,细线路的走向应尽量与摆动方向平行。
④蚀刻时间过久,造成过蚀现象。
一般认为铜厚的不均而导致所需的蚀刻时间不同。
若将蚀刻控制到100%均一次蚀刻干净,将会造成部分板子有过蚀现象。
4、问题与对策:(一)速度降低(二)蚀刻不均匀(三)沉淀(四)侧蚀大蚀刻过度(五)蚀铜不足(六)蚀刻机结晶过多四、蚀刻机的维护1.检查喷嘴压力:喷嘴压力可通过每只喷管的压力表表现出来。
- 1、下载文档前请自行甄别文档内容的完整性,平台不提供额外的编辑、内容补充、找答案等附加服务。
- 2、"仅部分预览"的文档,不可在线预览部分如存在完整性等问题,可反馈申请退款(可完整预览的文档不适用该条件!)。
- 3、如文档侵犯您的权益,请联系客服反馈,我们会尽快为您处理(人工客服工作时间:9:00-18:30)。
线路板厂碱性蚀刻液铜回收工艺
简介:
碱性蚀刻液是用蚀刻线路板铜的药液,主要成分:氨水+氯化铵+添加剂。
一般生产车间排出的废液含铜量为110~130g/l。
此废液回收价值高,收回方法,其一:萃取电解法。
此法利用萃取剂萃取出铜离子之后,用硫酸铜溶液做电解液进行电解。
其优点在于电解出来的铜纯度高,一般电解出来的铜都可以达到三个九以上。
以下是萃取电解的工艺流程
注明:
1.萃取槽,萃取剂和原液混合萃取,然后分相,上层为含铜萃
液,下层为萃余液。
2.水洗槽1主要是水洗含铜萃液中的氨根离子,称洗氨。
3.反萃槽,是用硫酸溶液将含铜萃液中的铜洗出来,形成硫酸
铜溶液即电解液。
4.水洗槽2,主要是用水洗掉萃取液中残留的硫酸根。
称洗硫。
5.隔油缸,油其实是指残留的萃取剂。
6.本工艺,蚀刻液循环,萃取剂循环,电解液循环。
洗水排出
处理。